CNC Machining Titanium
CNC Machining Titanium
Titanium is a lustrous transition metal with a silver color, low density, and high strength. It is an ideal material for typical applications in aerospace, medical, military, chemical processing, marine industries, and extremely high-temperature environments. Grade 5 titanium is the most popular titanium alloy. Titanium possesses beneficial properties and characteristics, such as good ductility, a high melting point, low thermal conductivity, resistance to corrosion from seawater, chlorine, and other media, exceptional strength with lightweight properties, and non-magnetic nature. Compared to other metals, it is as strong as steel, with higher density and strength than aluminum. All these features enable custom titanium machining parts to have a long service life, even in challenging environments.
The typical processes for CNC machining titaniuminclude titanium CNC milling, titanium lathe turning, titanium CNC turning and milling, and laser cutting titanium.
Titanium Lathe Turning
Turning titanium parts can get a relatively good surface roughness, and work hardening is not severe. However, the cutting temperature is high, and tool wear is rapid. With years of experience in machining titanium components, as a titanium parts manufacturing supplier, Masion can effectively address any issues encountered during titanium machining.

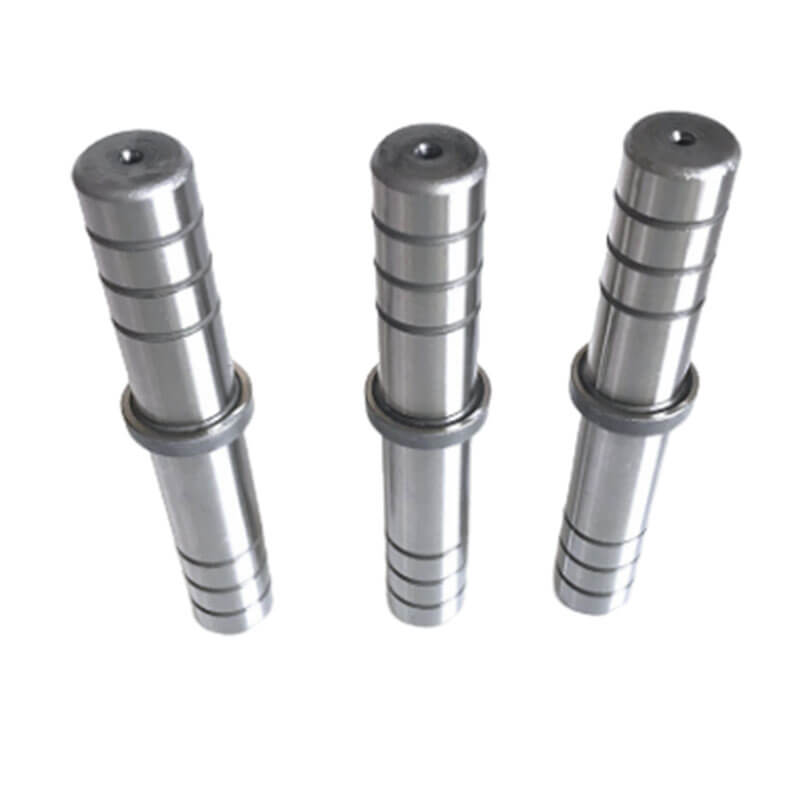
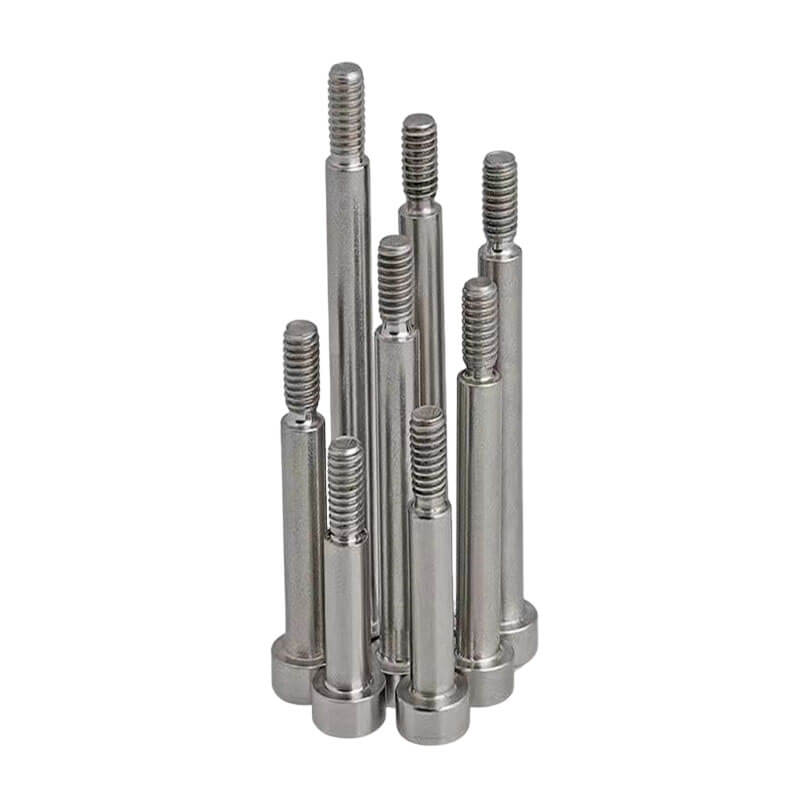
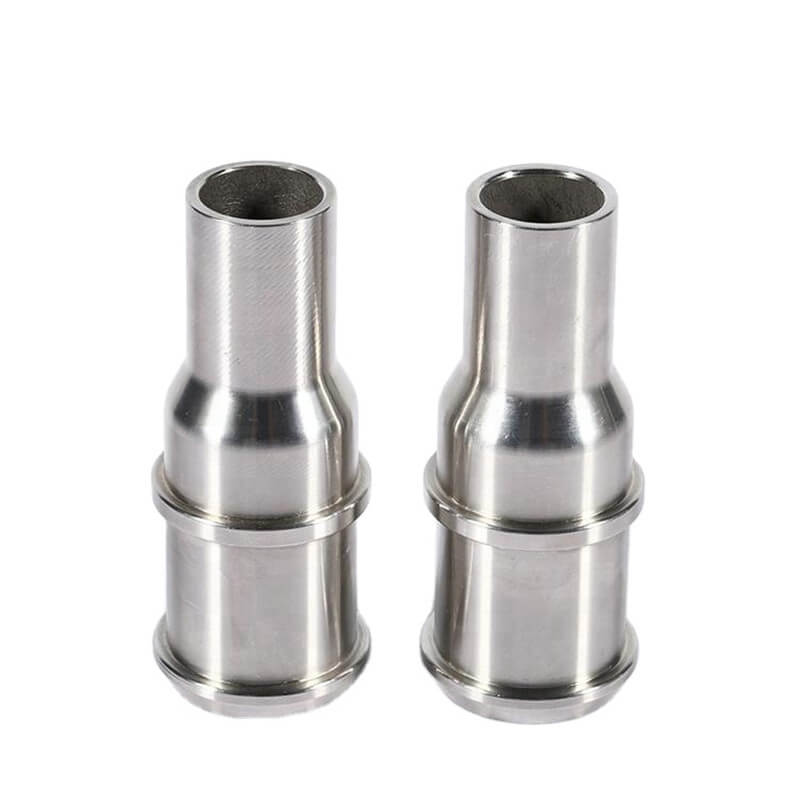
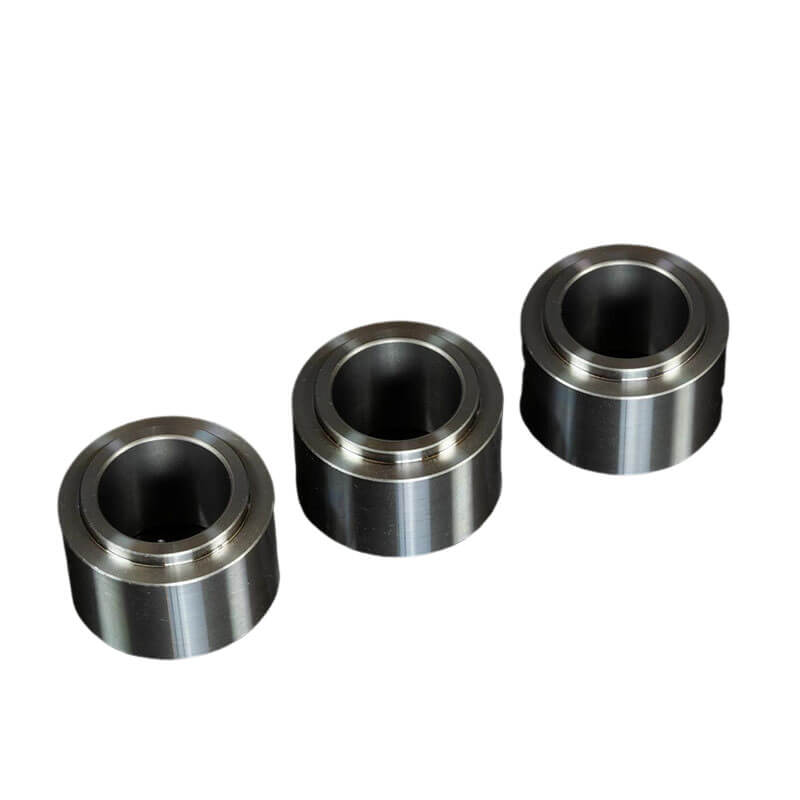
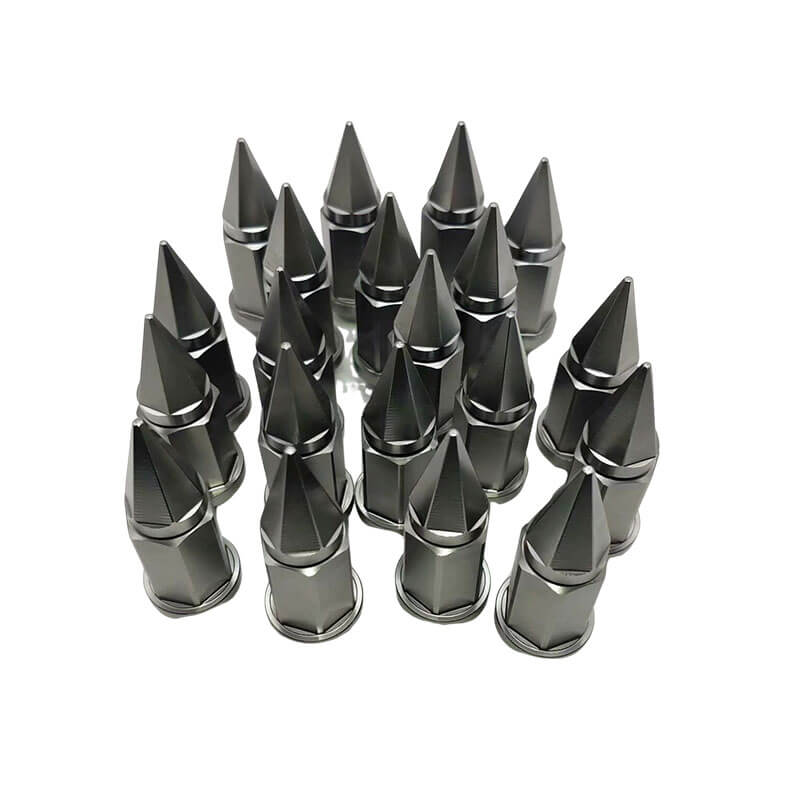
Titanium CNC Milling
Milling titanium parts can be more challenging than turning because milling involves intermittent cutting, and the chips tend to bond with the cutting tool. When the bonded chips re-engage with the workpiece, they can knock off and carry away a small piece of tool material, resulting in tool chipping, significantly reducing tool durability. With years of experience in machining titanium components,as a specialized titanium manufacturers Masion can handle your titanium parts with confidence, and the results will leave you highly satisfied.
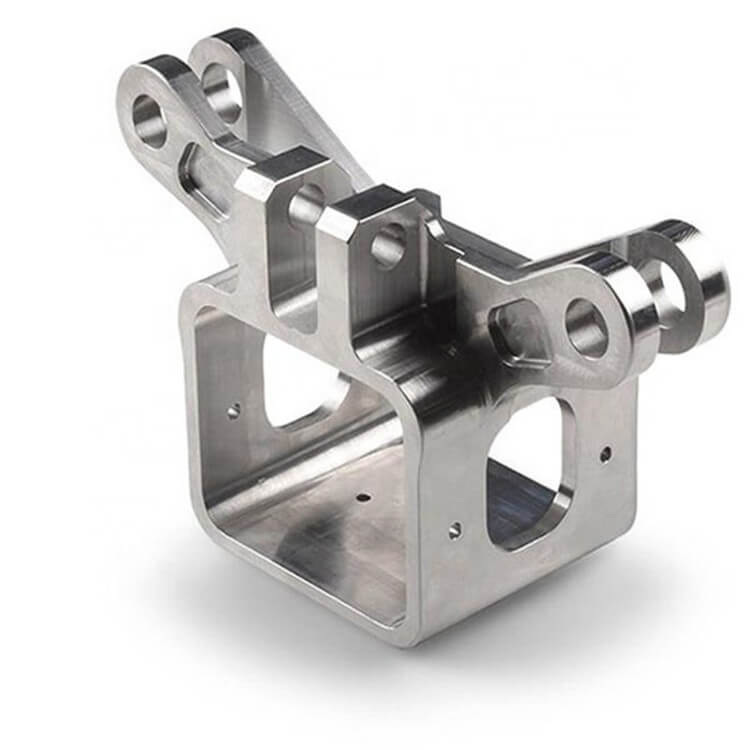
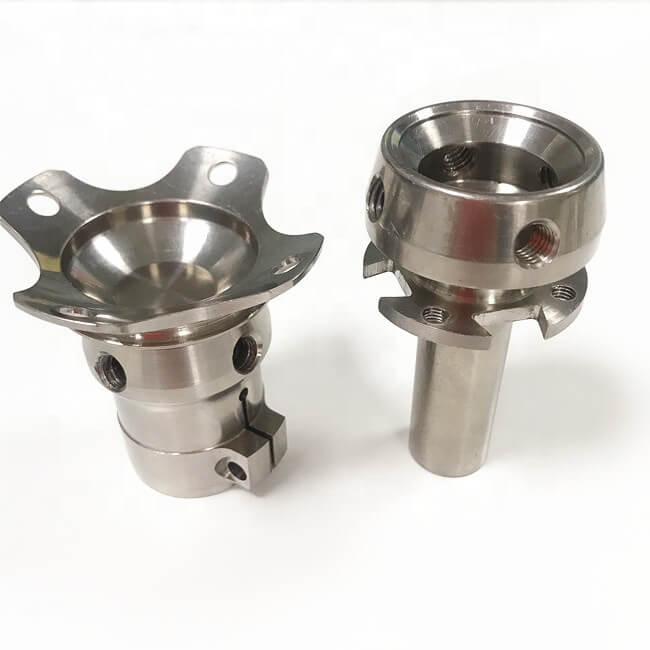
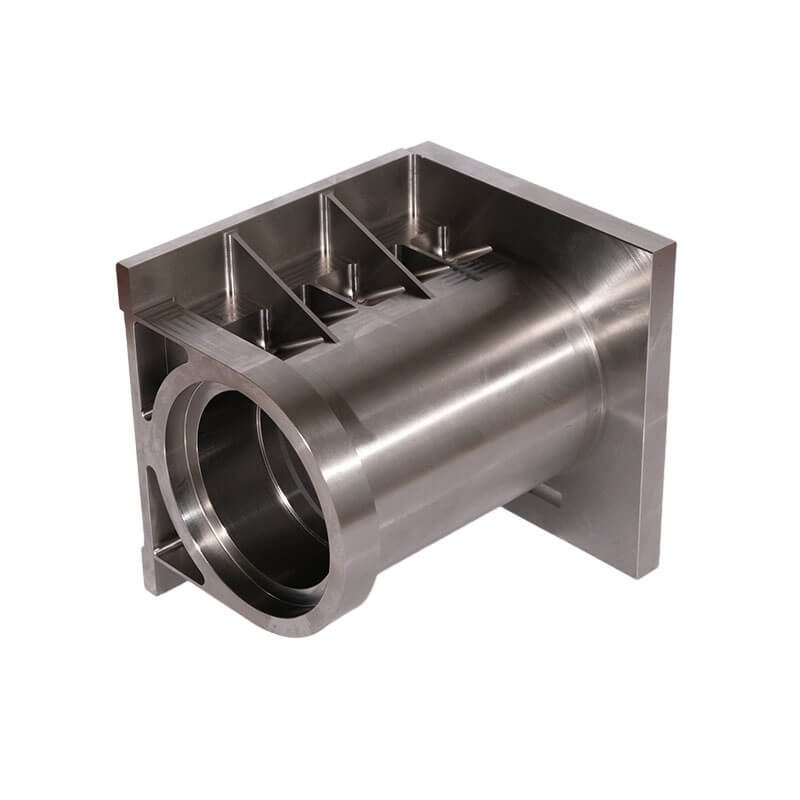
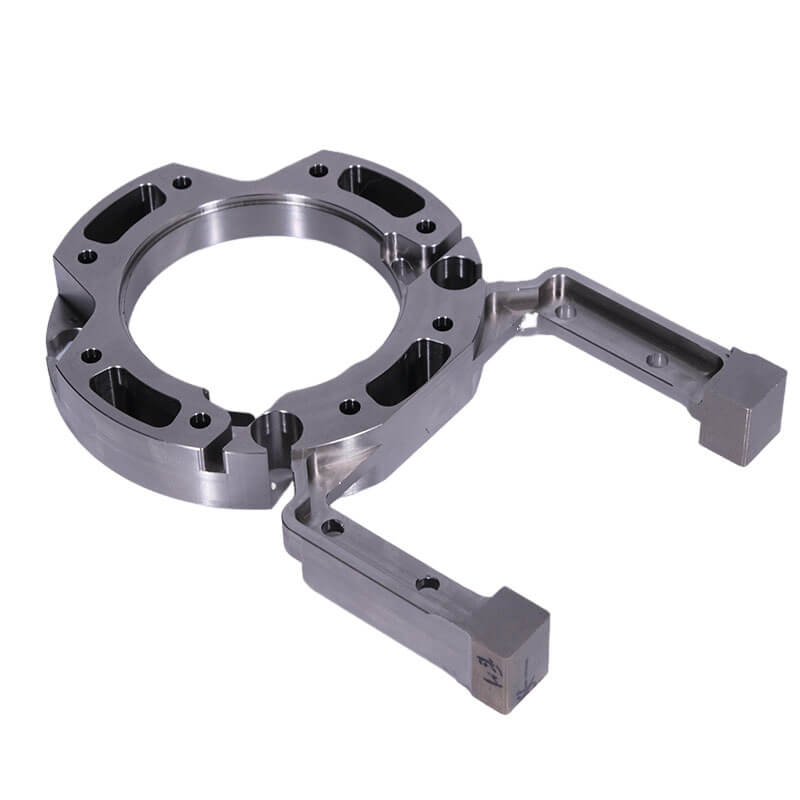
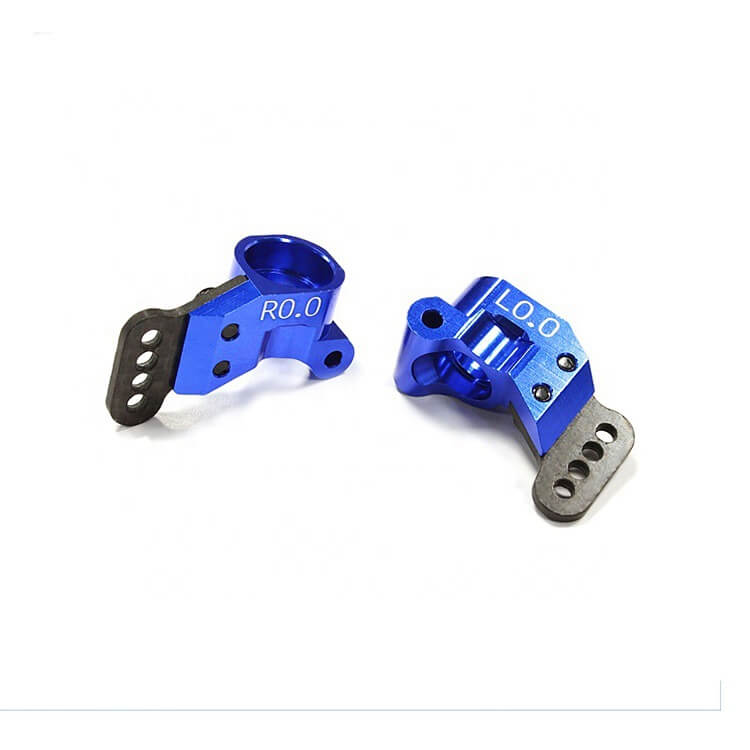
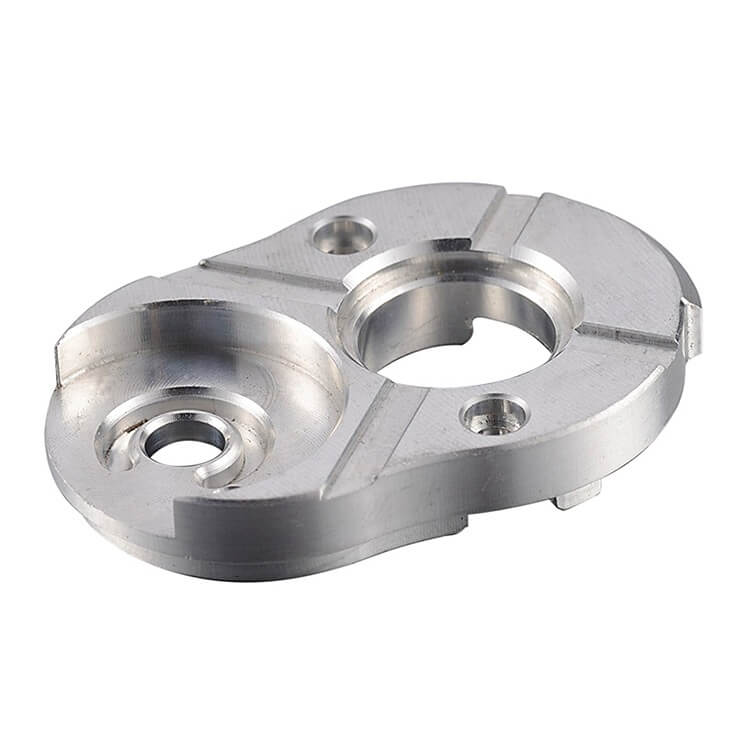
Titanium CNC Turning and Milling
Titanium’s turning and milling processing is the integration of turning and milling processes, used for challenging materials like titanium alloys. Its purpose is to enhance efficiency and precision while reducing steps and improving material utilization. It begins with turning for rough and contour machining and then transitions to milling for finer operations such as slotting, hole drilling, and surface finishing.
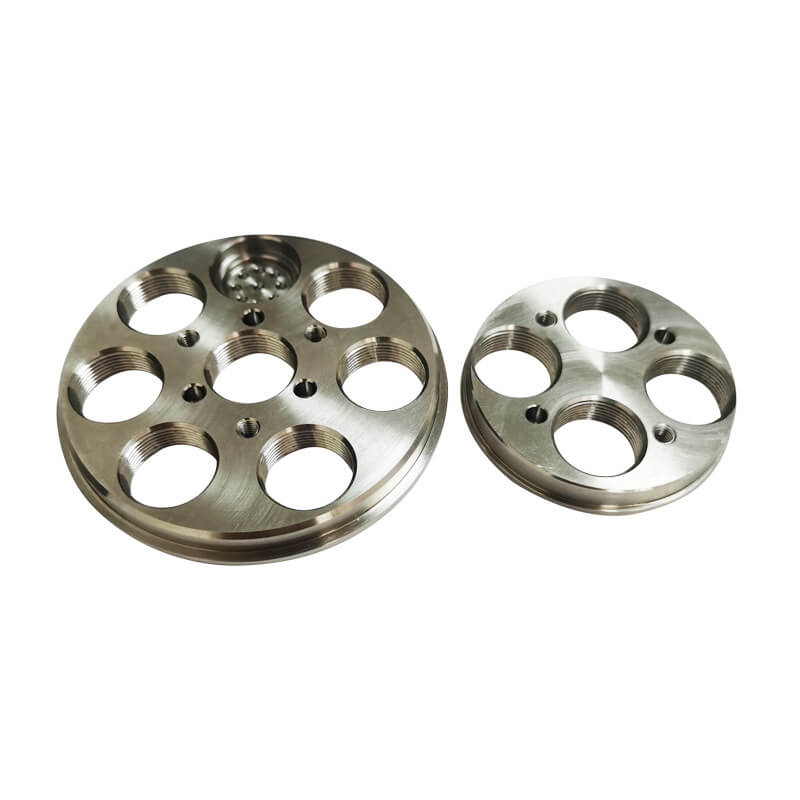
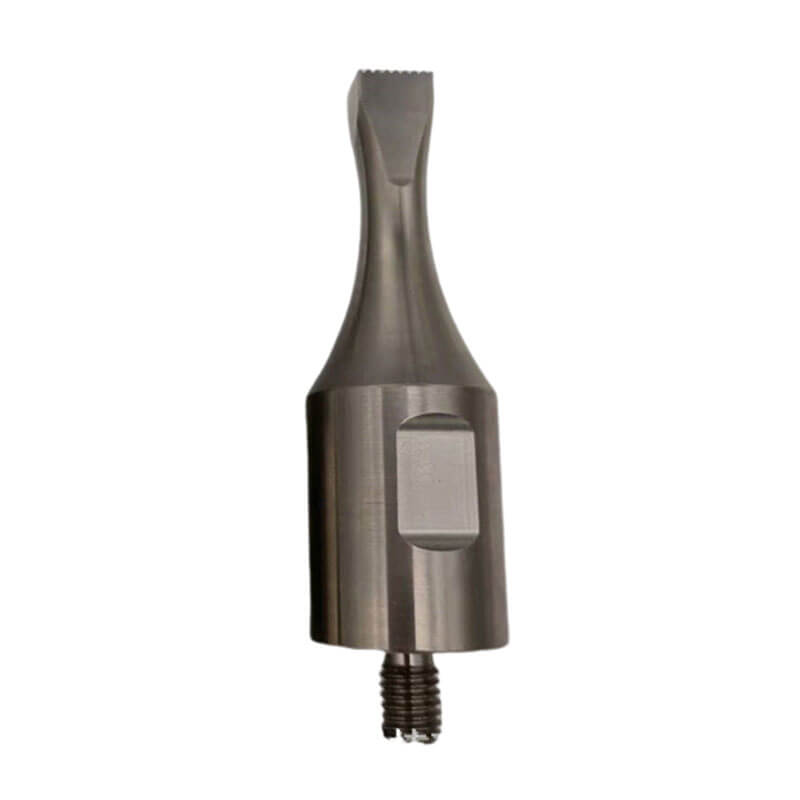
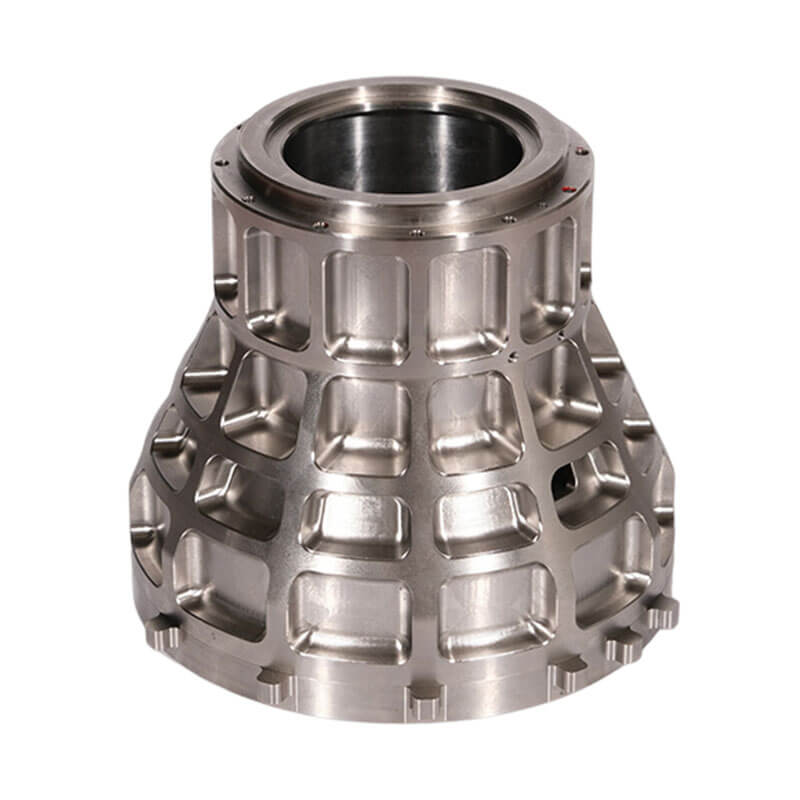
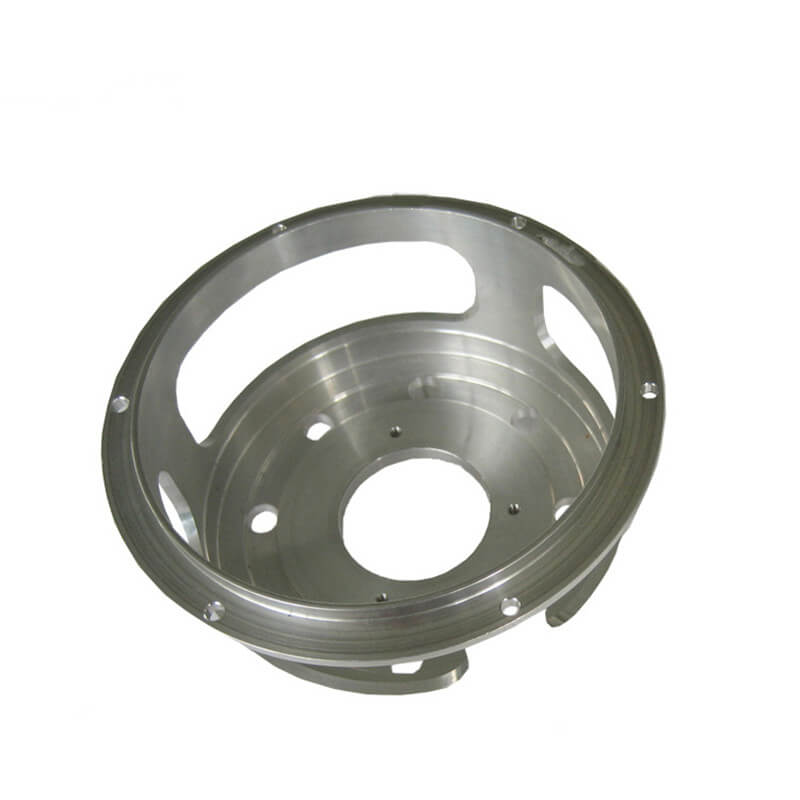
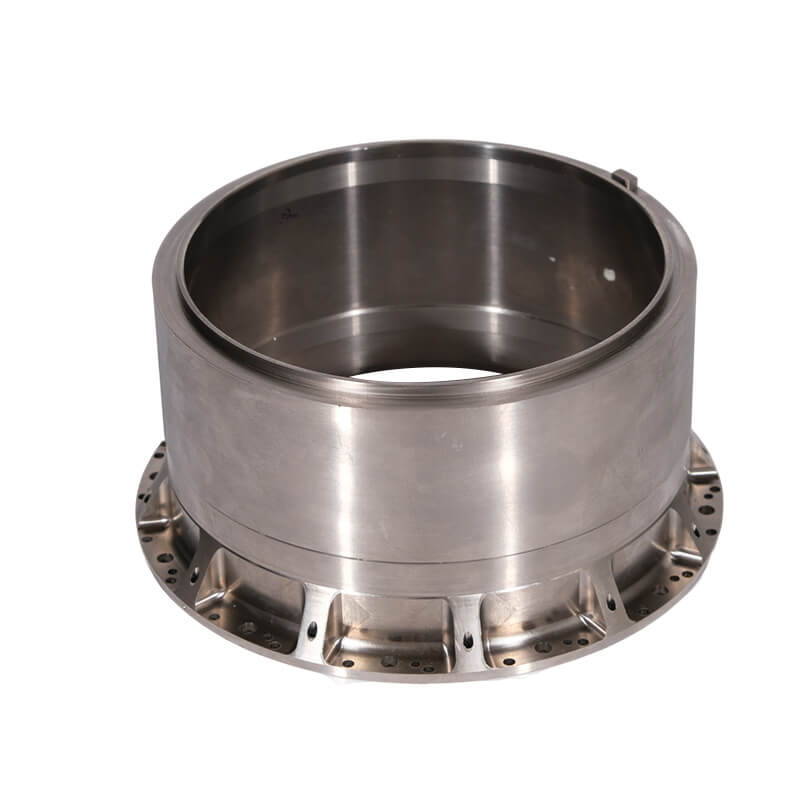
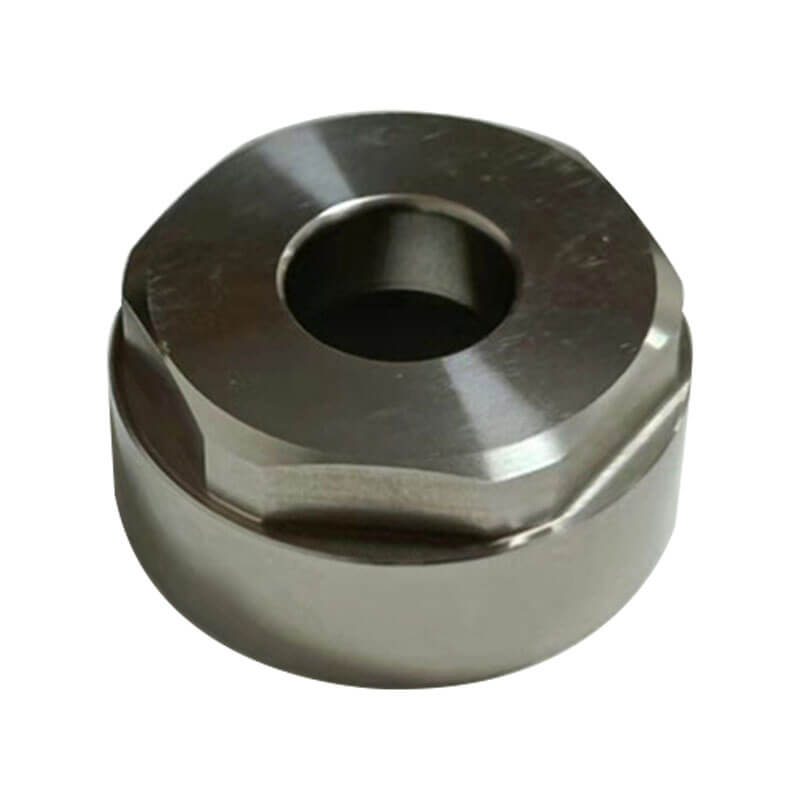
CNC Swiss Machining Brass
Masionemploys precision Japanese-imported CITIZEN Swiss-type lathes for the machining of various titanium parts. They are equipped with suitable tooling, cutting parameters, and coolant. By adjusting parameters such as cutting speed, feed rate, and cutting depth within the lathe program, they efficiently machining titanium parts.
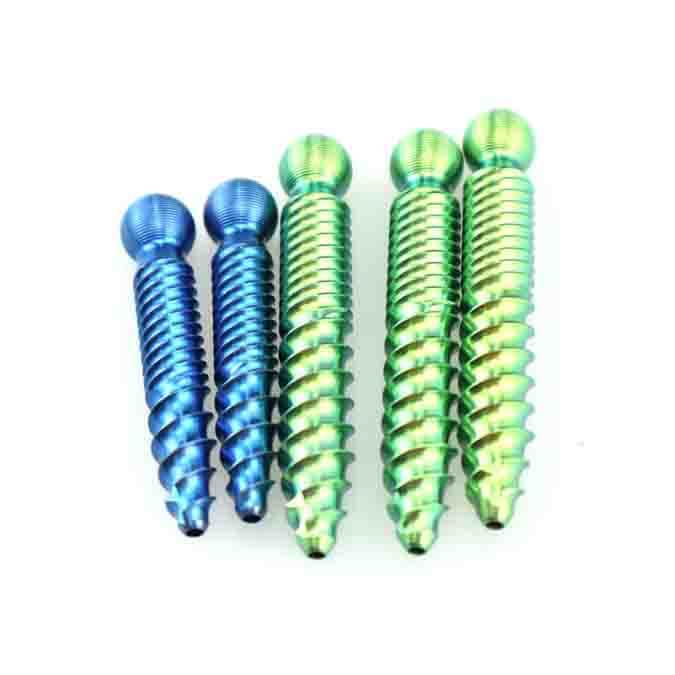
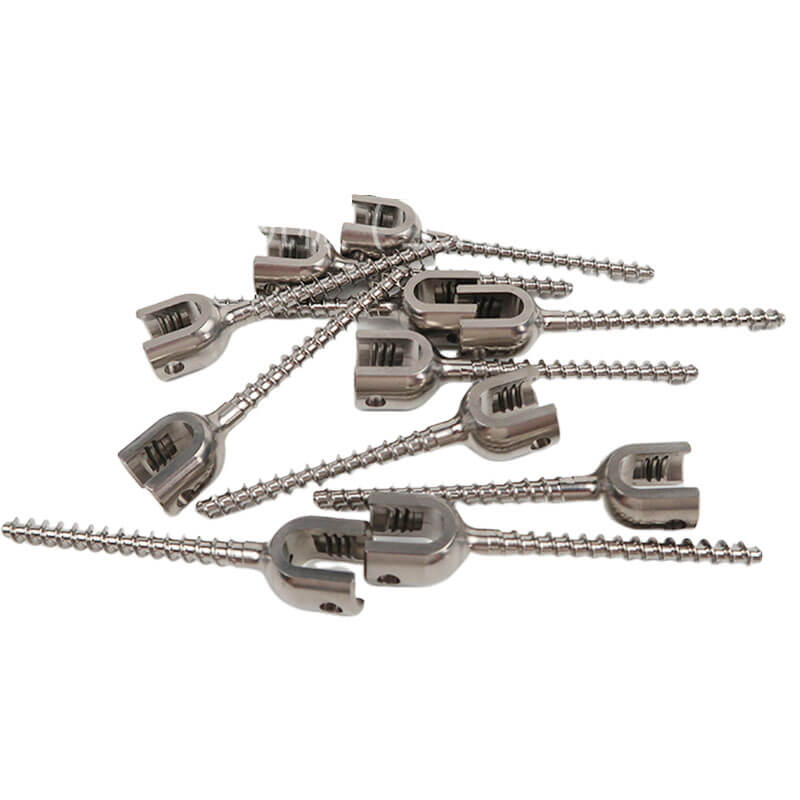
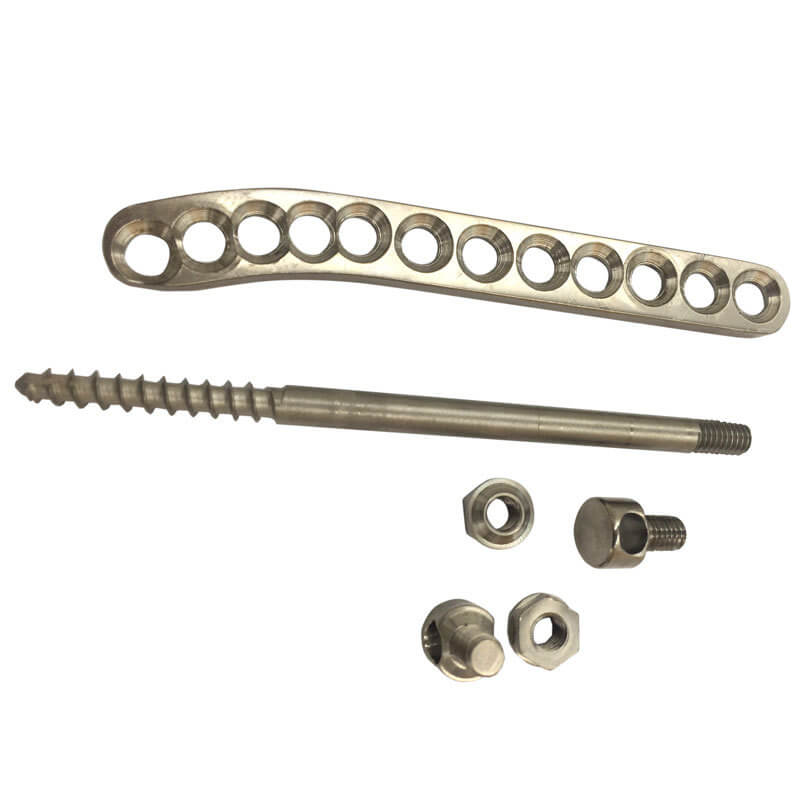
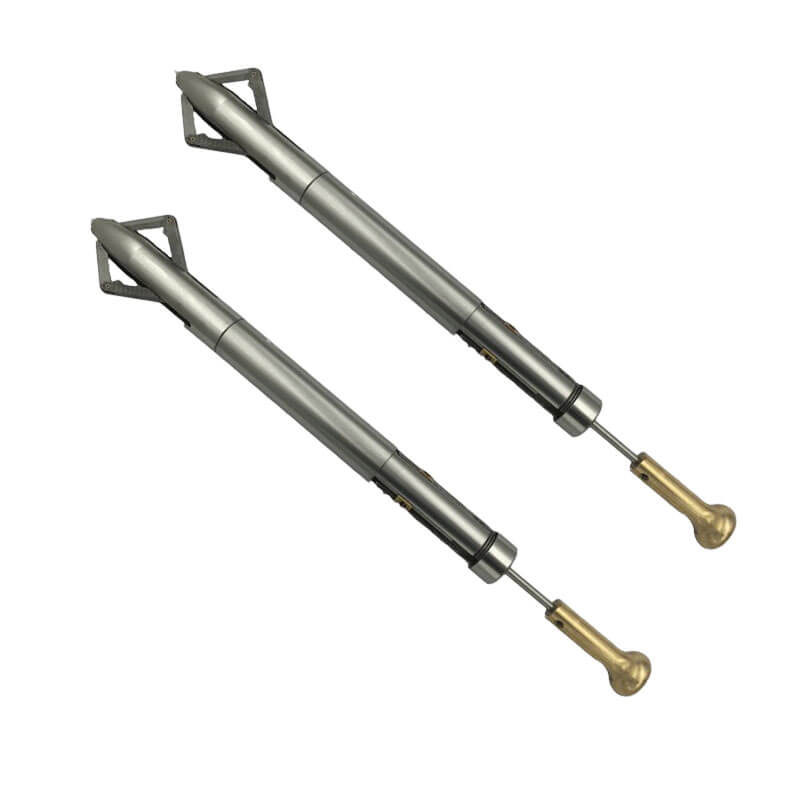
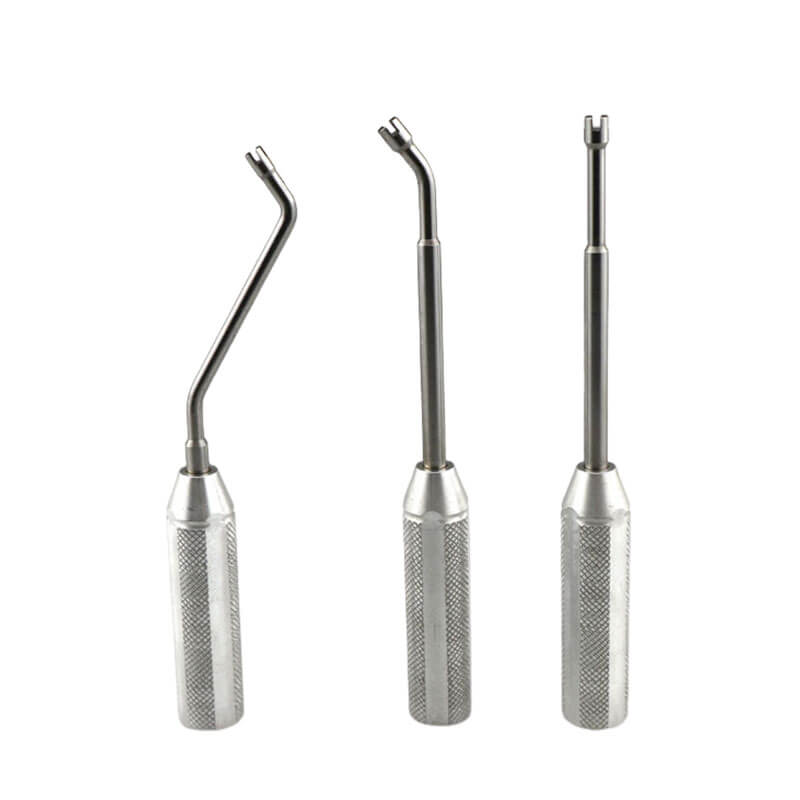
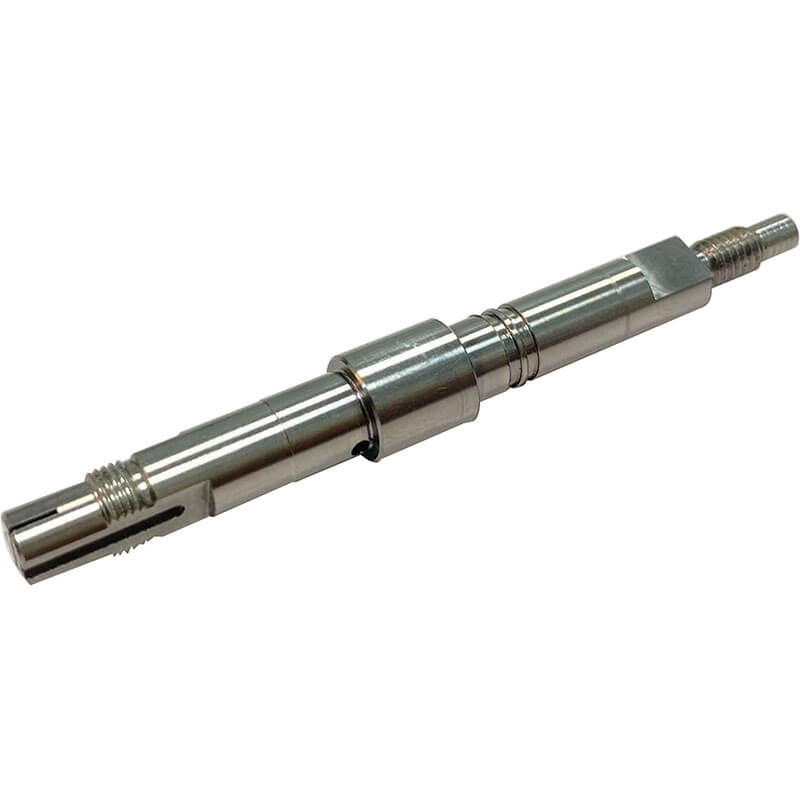
CNC Automatic Lathe Machining Titanium
Automatic lathe machining of titanium parts is primarily utilized in the manufacturing of small-scale components. This machining method involves rotating a cam to drive the rotation of titanium parts, while the tools on the tool post move along predetermined paths to perform turning operations on the titanium parts. The main products in this context are primarily titanium screws.
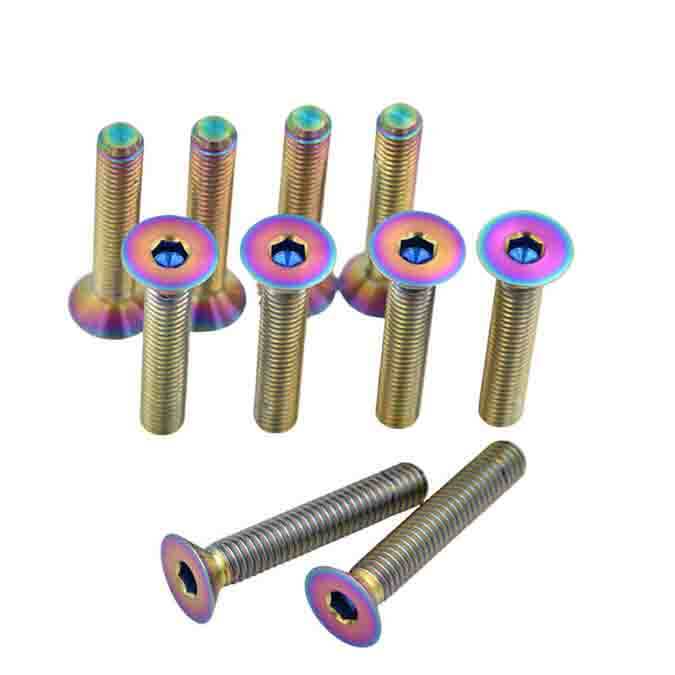

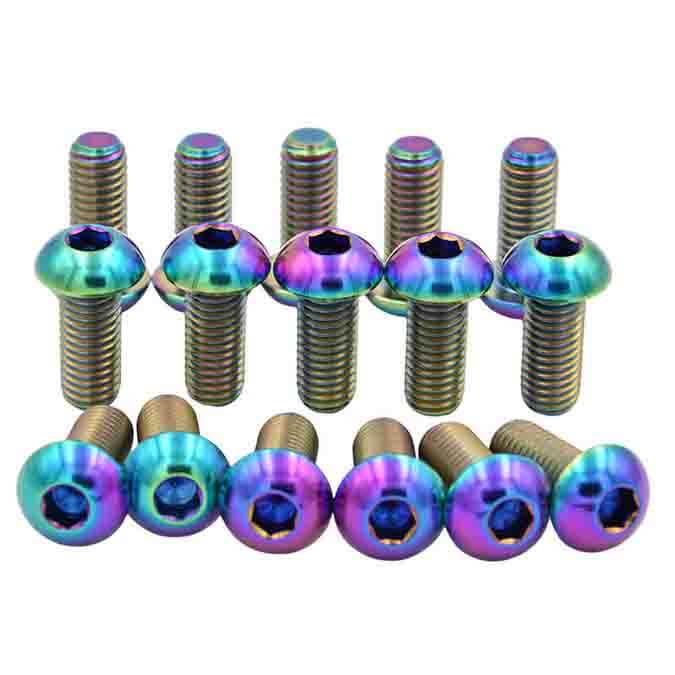
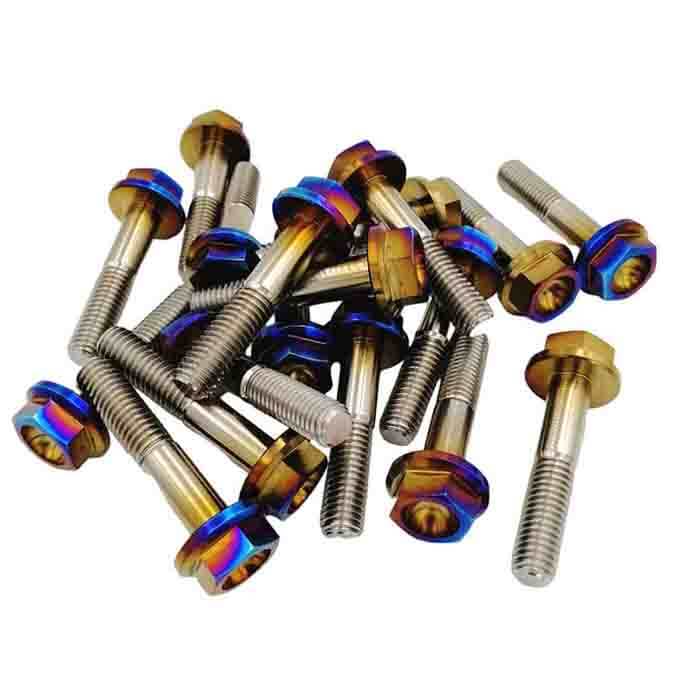
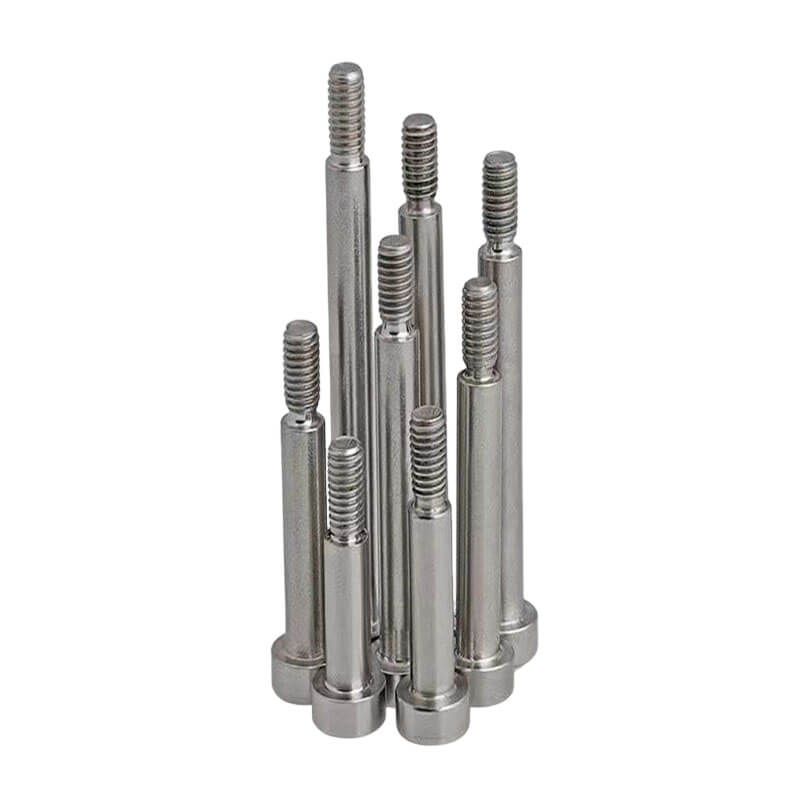
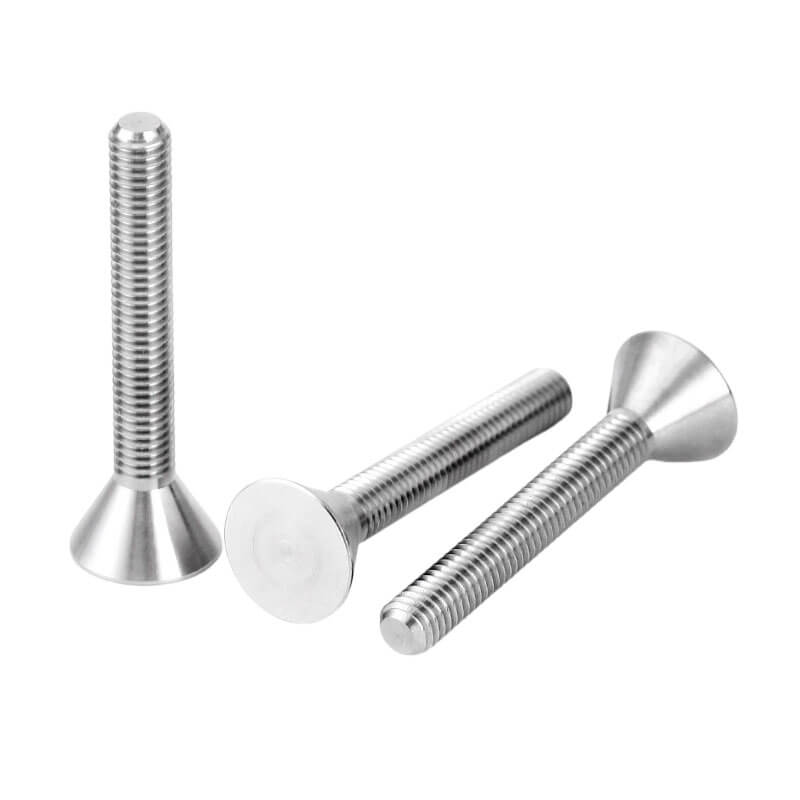
CNC Titanium Springs Winding
There are many types of springs, and titanium springs are just a small part of them. Due to titanium’s characteristics of lightweight, high strength, and excellent corrosion resistance, titanium springs are widely used in various fields, including chemical industry, marine engineering, and automotive manufacturing. Titanium springs come in various types, such as titanium tension springs, titanium compression springs, and titanium torsion springs. The manufacturing methods for titanium springs can be broadly categorized into cold rolling and hot rolling. Titanium springs are primarily made from titanium wire, with cold rolling typically used for wire diameters less than 8mm and hot rolling for diameters greater than 8mm. The heat treatment of titanium springs can be annealed and acid washed as per customer requirements.
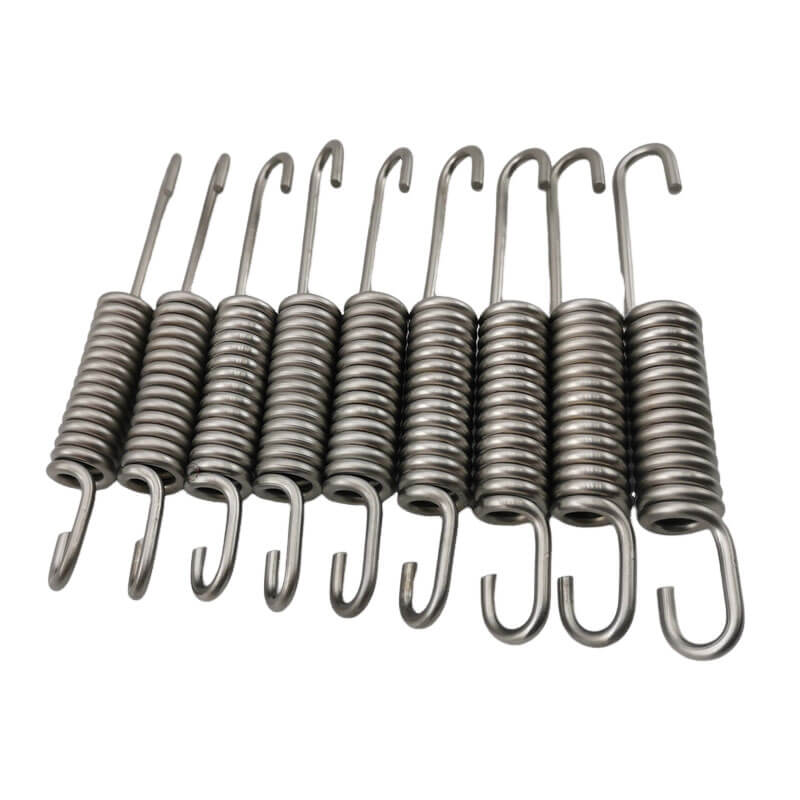
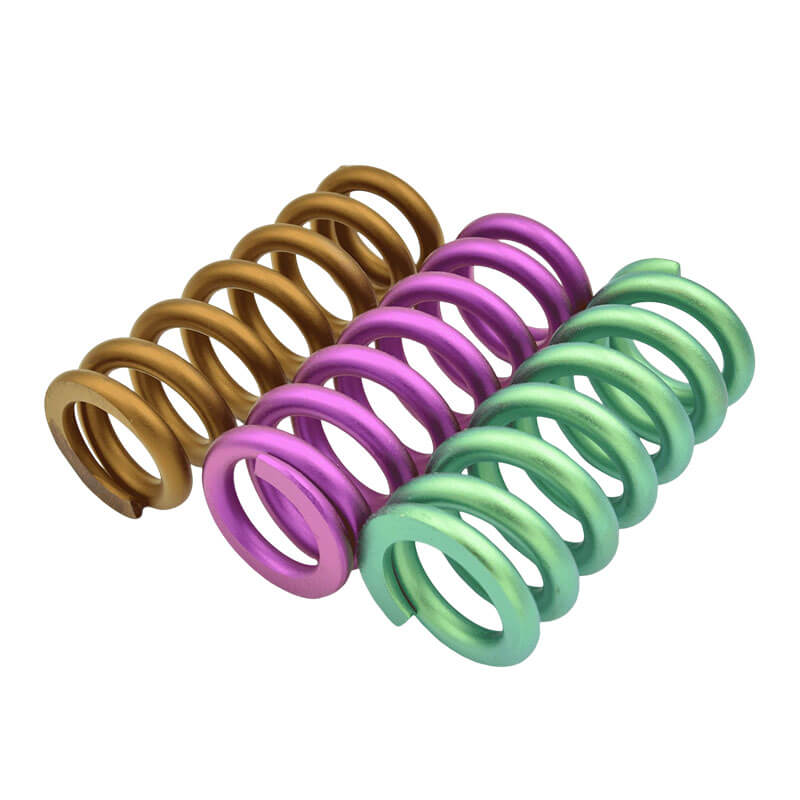
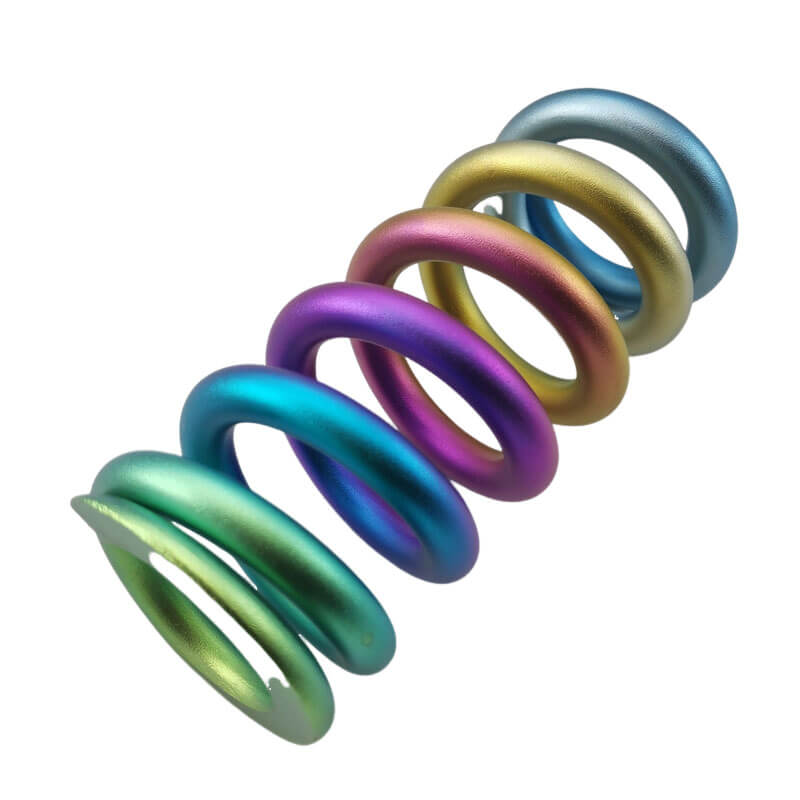
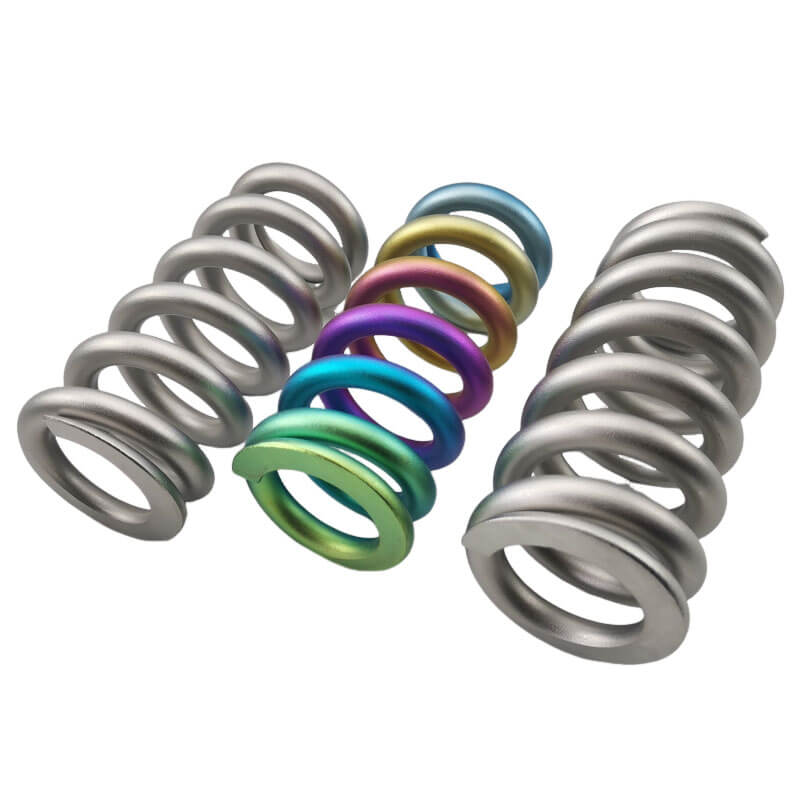
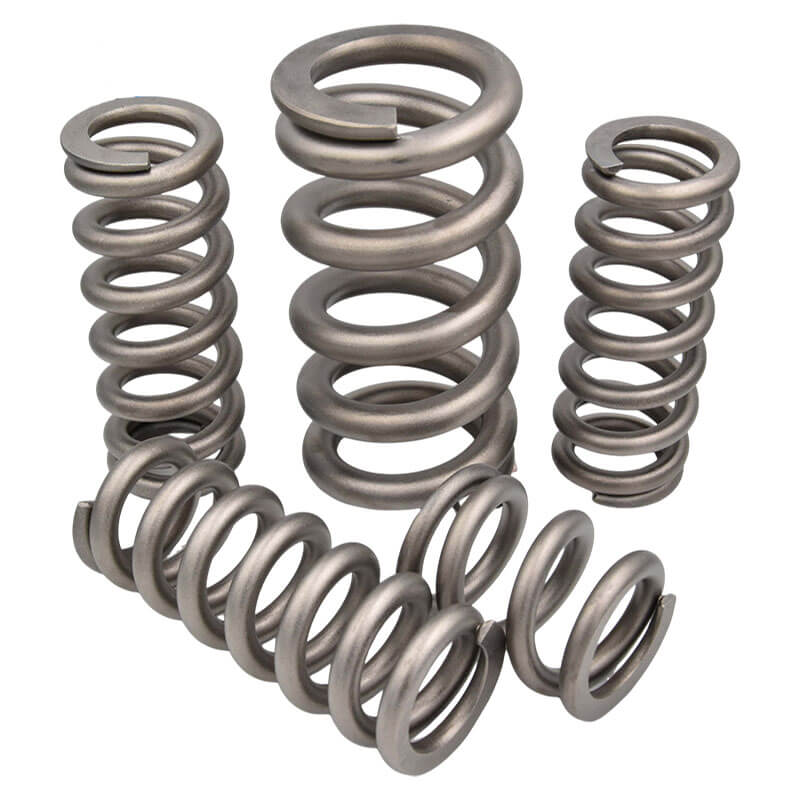
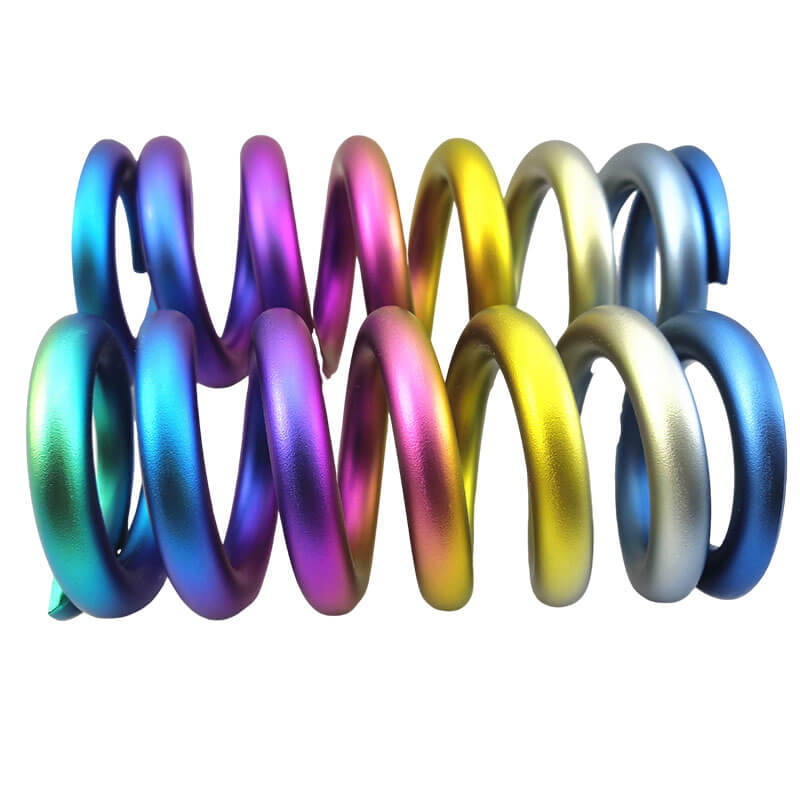
Titanium Parts Machining Methods
What are the processing methods for titanium parts material?
In the field of titanium parts material processing, there are various methods to choose from. These methods lay the foundation for subsequent CNC titanium machining. In the initial stages, it is possible to easily shape products that meet design requirements through mold development. Subsequently, in the CNC machining process, excess material can be removed to precisely machine the work piece to meet the strict requirements of the design drawings, thus achieving an efficient and precise machining process. These methods include forging, casting, cold drawing, laser cutting, and they all play important roles in processing titanium materials.
Picture | Process | Materials | Description | Advantage | Application | If need mold |
---|---|---|---|---|---|---|
![]() | Titanium casting | ZTi1 ZTi2 ZTi3 ZTiAl4 ZTiAl5Sn2.5 ZTiAl6V4 ZTiMo32 ZTiAlbSn4.5Nb2Mo1.5 | TitaniumCasting is a commonly used forming process that involves melting titanium alloys and pouring them into molds to solidify and obtain components with the desired shape. | Good fluidity, ease of forming, high strength, and excellent corrosion resistance. | Aerospace, medical devices, automotive parts, construction machinery, and other applications. | Yes |
![]() | Titanium forging | 1. TC4(Ti-6Al-4V) 2. TC6(Ti-5Al-2.5Sn 3.TC11(Ti-6.5Al-3.5Mo-1.5Zr-0.3Si 4.TC17(Ti-5Al-5Mo-5V-3Cr) 5. Ti-15V-3Cr-3Sn-3Al | TitaniumForging is a commonly used forming process that involves heating titanium to a certain temperature and then subjecting them to directional deformation to change their shape, structure, and properties. | High strength, good formability, excellent fatigue resistance. | Aerospace, marine, sports equipment, military equipment, etc. | Yes |
![]() | Titanium Extrusion | TC1 -TC26 TA1、TA2、TA3-TA21 TB2-TB10 | By heating titanium to high temperatures and then extruding them through molds to form the desired cross-sectional shape. | It offers strong customizability, lightweight properties, high strength, and excellent thermal conductivity. | aerospace, medical devices, automotive manufacturing, construction,sports equipment, and more. | Yes |
![]() | Titanium laser cutting. | TC1 -TC26 TA1、TA2、TA3-TA21 TB2-TB10 | Titanium laser cutting involves using a laser cutting machine to cut various Titanium sheets into different shapes and profiles. | High-precision cutting, fast, low deformation, suitable for cutting complex designs. | aerospace, medical devices, automotive parts, construction machinery, and more. | No |
There are several surface treatment methods for Titanium
In the field of titanium parts material processing, there are various methods to choose from. These methods lay the foundation for subsequent CNC titanium machining. In the initial stages, it is possible to easily shape products that meet design requirements through mold development. Subsequently, in the CNC machining process, excess material can be removed to precisely machine the work piece to meet the strict requirements of the design drawings, thus achieving an efficient and precise machining process. These methods include forging, casting, cold drawing, laser cutting, and they all play important roles in processing titanium materials.
Picture | Process | Machining principle | Machining material | Advantage | Application | Remark | Learn More |
---|---|---|---|---|---|---|---|
![]() | Titanium Sandblasting | Learn More | |||||
![]() | Titanium Anodizing | Forming an oxide layer on the surface of titanium alloys through an electrolytic process. | Electrolyte, electric current | Increasing surface hardness, improving corrosion resistance, and aesthetics. | Titanium alloy jewelry, aerospace components, medical devices. | Different colors of oxide layers can be achieved under various electrolytic conditions. | Learn More |
![]() | Titanium Polishing | By polishing to eliminate surface roughness and imperfections, the titanium surface becomes as shiny as a mirror. | .Hemp wheel or wool wheel ,Cotton wheel,Roving wheelwith special permanent luminous titanium wax. | Enhance surface smoothness and improve aesthetics. | Titanium jewelry, aerospace components, medical devices | It requires professional polishing equipment and operational skills. | Learn More |
![]() | Titanium PVD Coating | Forming thin films or coatings through evaporation and material deposition. | PVD coating, Titanium nitride, titanium carbide, Alumina, silicon nitride | Improve hardness, wear resistance, reduce friction, and enhance corrosion resistance. | Tools, cutting tools, jewelry, medical equipment, aerospace components. | It can achieve coatings of various colors and properties. | Learn More |
Titanium CNC Machining FAQs
Titanium alloys are widely used in fields such as aerospace, medical devices, automotive, construction, sports equipment, and more. Their characteristics include low density, high strength-to-weight ratio, low coefficient of thermal expansion, excellent thermal conductivity, high-temperature and low-temperature strength, corrosion resistance, non-magnetic properties, biocompatibility, and some special alloys with memory functions. In the future, titanium alloys are expected to replace traditional materials in more fields.
Titanium alloys are divided into different grades, mainly categorized into three series: TA (pure titanium and alpha-type alloys), TB (beta-type alloys), and TC (alpha+beta-type alloys). According to the Chinese standard GB/T 3620.1-2016, there are approximately 99 different grades of titanium alloys. The American standard uses “grade” to represent different levels, and there are about 34 different grades.
A-titanium, B-titanium, and AB-titanium are commonly used terms to distinguish different characteristics of titanium alloys. Grade titanium typically refers to titanium materials categorized into different grades based on their intended use and performance requirements. Medical-grade titanium is a high-purity titanium alloy used for manufacturing medical devices and implants. Regarding surface treatment, titanium alloys can undergo various processes such as anodization and micro-arc oxidation to improve hardness and wear resistance. Different processes require specific process conditions and safety measures.
Titanium alloys have significant differences in machinability compared to stainless steel. Due to their low thermal conductivity and tendency to stick to cutting tools, machining titanium alloys is notably different from machining stainless steel. Processing titanium alloys typically requires specialized tooling and cutting fluids to reduce friction and heat, and tool selection and cooling need to consider the characteristics of titanium alloys.
General cutting fluids can be used as coolants for titanium alloy turning and milling, and there are no special requirements. Titanium alloys are flammable, but the primary source of ignition is the chips, so measures to reduce flammability risk include reducing the depth of cut, ensuring adequate cooling, maintaining good ventilation, and avoiding open flames. In case of open flames, water should not be used directly to extinguish the fire; dry sand is a better option.
When machining titanium alloys, it’s recommended to use cutting tools with high-temperature hardness, wear resistance, compressive strength, bending strength, and impact toughness. Commonly used hard alloy cutting tools include YG8, YG6, and YW2. YG8 and YG6 contain cobalt and exhibit good wear resistance, while YW2 contains tungsten, tantalum (niobium), and cobalt, providing high bending strength. Proper tool selection and suitable cutting fluids can improve the machinability of titanium alloys.
The two primary processing methods for titanium screws are cold heading and machining. Cold heading is often used with TC2 titanium, which is relatively soft and exhibits good ductility. Machining is commonly used with TC4 titanium, which has higher hardness and better overall mechanical properties. The two methods differ in material and processing techniques. Machined titanium screws are typically more refined, with higher precision and can achieve tolerances of 0.01mm.
For processing titanium alloy threads, a cutting tap is a better choice. Due to the characteristics of titanium alloys, internal thread tapping can be a challenging process, especially for small hole threads. Cutting taps are more suitable than roll taps because roll taps tend to produce higher torque when used on titanium alloys, approximately twice that of steel. The teeth of roll taps are prone to wear, chipping, and even breakage. This is primarily due to the relatively low modulus of elasticity of titanium alloys, which results in significant springback after internal thread tapping, leading to high friction torque. Additionally, factors such as high temperatures, chip adhesion, and difficulties in providing cutting fluid to the cutting zone can contribute to the challenges of machining titanium alloys. To address these issues, it’s essential to optimize the geometry parameters of titanium alloy internal thread taps and select the appropriate tap based on the form of the hole, accuracy requirements, and machine conditions.
Titanium springs are typically manufactured using TC4 titanium alloy, known for its low elastic modulus and high fatigue strength, making it suitable for spring production. There are several main types of titanium springs, including tension springs, compression springs, and torsion springs. These titanium springs have various applications, including but not limited to:
Chemical Industry: Titanium springs are used in chemical equipment such as pumps and valves due to titanium’s corrosion resistance and chemical stability.
Marine Engineering: Titanium’s corrosion resistance is advantageous in seawater environments, making titanium springs suitable for underwater equipment and diving apparatus.
Automotive Manufacturing: Titanium springs can be used in vehicle suspension systems to reduce weight and improve fuel efficiency, thanks to titanium’s lightweight and high strength properties.
Aerospace: In the aerospace field, where lightweight, high-strength components are essential, titanium springs find applications in various aerospace components and systems.
Free Sample
Explore Other Materials
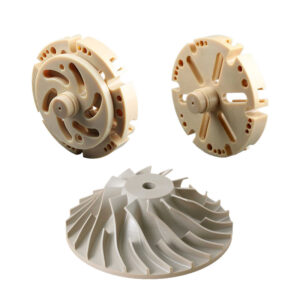
PEEK CNC machining
Polyetheretherketone (PEEK) is a special type of high-performance polymer material known for its high mechanical strength, resistance to high temperatures, impact resistance, flame retardancy, acid and alkali resistance, hydrolysis resistance,
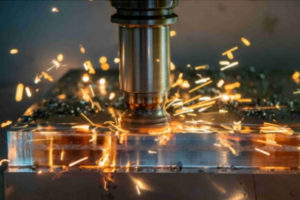
Aluminum CNC Machining
Aluminum alloy is a widely used material in various fields, known for its excellent strength, lightweight properties, good thermal conductivity, corrosion resistance, cost-effectiveness, blade-friendly nature, and ease of processing. It

PTFE CNC machining
Polytetrafluoroethylene (PTFE), commonly referred to as PTFE, possesses outstanding characteristics. It can endure an extreme temperature range from -200°C to 260°C for extended periods, displaying exceptional resistance to various chemicals