Our Quality Control
Our Quality Control
Design of CNC Machining Plan
CNC programming during CNC machining.
Simulation inspection process in CNC machining
Methods and Tools for Quality Control in CNC Machining
Quality Inspection:
1. Incoming Inspection:
Generally, the raw materials we purchase come with material reports, but there is still a certain degree of risk. Therefore, we conduct self-inspection based on the materials and use material testing instruments to ensure the accuracy of the materials. If materials are used incorrectly, it will be fatal for us and our customers. We will not only fail to meet the delivery deadline but also lose a significant amount of costs. Therefore, we will prevent such incidents from happening at this point.
2. In-process Inspection:
Self-inspection should be carried out promptly after rough processing to adjust data with errors in time. The content of self-inspection mainly includes the positional size of the processing part.
1) Whether the workpiece is loose;
2) Whether the workpiece is correctly centered;
3) Whether the size of the CNC machining parts at the processing position to the reference edge (reference point) meets the requirements of the drawing:
4) The positional size of the CNC processing part to each other. After checking the positional size, measure the shape size of the rough processing (excluding the arc).
The machinist completes a self-inspection of the workpiece and confirms that it complies with the drawing and process requirements before removing the workpiece for inspection by the inspector.
Inspection will inspect semi-finished products during machining to ensure product accuracy and sustainable processing.
Here the machinist and inspector will use calipers or micrometers to test the part dimension
Pre-shipment Inspection
2) According to the product shape and tolerance requirements, precision instruments such as the 3 Coordinate Measuring Machine, project meter, height gauge, and micrometer are selected to measure all dimensions of the product to ensure that the product dimensions meet the customer’s drawing requirements.
3) 3.For products with strict tolerance requirements for anodizing and electroplating, there is a tolerance of 0.01mm, while for powder coating and painting, there is a tolerance of about 0.05mm. Therefore, we will conduct a second measurement of all surface-treated products to ensure that the size after surface treatment is within the precision range required by the customer. A comprehensive inspection of customer logos, product labels, and packaging to ensure they meet customer requirements.

X-ray Material Tester
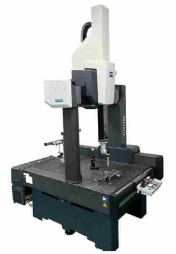
Coordinate measuring equipment
A three-coordinate measuring machine uses a guiding mechanism, measuring element, and digital display device to measure the coordinates of a point on a workpiece. The machine has a table on which the workpiece is placed, and a probe that can be manually or automatically moved to the measuring point. The measuring process is carried out by the probe, which is equipped with a grating ruler and reading head along the X, Y, and Z axes. When the probe touches the workpiece and sends a signal, the control system collects the coordinate values of the three axes relative to the machine tool’s origin. The data is then processed by the computer system to determine the coordinate values of the measured point. The measuring machine is capable of measuring points of varying sizes and can handle large workpieces as well.
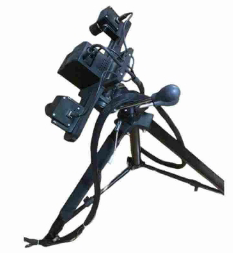
3D Scanner
n cases where 3D CAD data cannot be used, the data generated by 3D scanning can be used to build and improve product designs using real models created by rapid prototyping. The data can also be utilized in various applications, such as reverse engineering, detection and comparison, and 3D visualization.
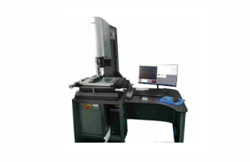
Project Meter
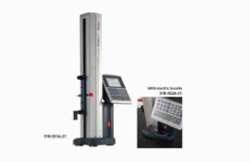
Mitutoyo Digital height micrometer
Test Equipment
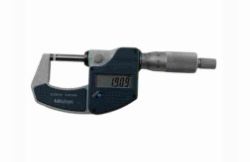
Digital Outside Mierometer
The Outside Micrometer, commonly known as the Spiral Micrometer, is often simply referred to as the "micrometer." It is a highly precise measuring instrument used for measuring the diameter of an object.
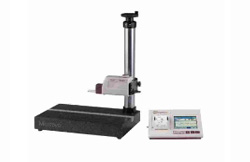
Mitutoyo Roughness Tester
Roller shaft,Turn-milling composite processing, 7075 aluminum machining, and another turning and milling CNC machining parts.
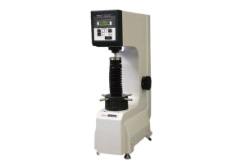
Mitutoyo Hardness Tester
A hardness tester is a specialized tool used to measure the surface hardness of coatings. It has the capability to convert between six different hardness scales, which include HL, HRB, HRC, HB, HV, and HS.
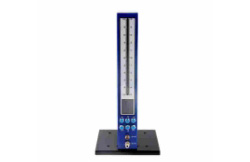
Pneumatic Measuring Instrument
A pneumatic momentum meter is a new type of measurement tool used to convert changes in the dimensions of a workpiece into variations in compressed air flow or pressure, which are then displayed through an indicator.
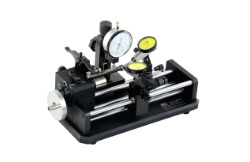
Concentricity Tester
The concentricity tester is primarily used for precision measurements of roundness, concentricity, circular runout, and cross-section variations of shaft components. It provides high accuracy, with measurements reaching up to 0.005mm, allowing for precise and reliable results.
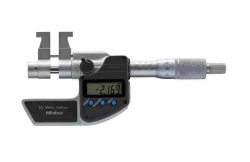
Digital Inside Mierometer
INSIDE MICROMETER, as known a mechanical instrument used for precise measurement of internal dimensions. It can read up to the third decimal point (thousandth). This extreme level of precision is why it is called the "micrometer."

Pin Gauges
The pin plug gauge measures the inner diameter of a round hole. It is primarily utilized for measuring the inner diameter of small round holes that range between 0-10mm and requires a high level of precision.
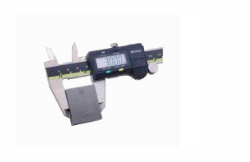
Digital Caliper
A digital caliper consists of a main ruler and a vernier. It is used to measure length, inside and outside diameter, and depth. The resolution for digital calipers is 0.01mm. It allows an error of ±0.03mm/150mm.
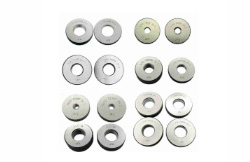
Thread Ring Gagues
The purpose of a thread ring gauge is to verify the accuracy of the external thread's dimensions. The specifications of thread ring gauges are categorized into three types: coarse teeth, fine teeth, and pipe thread.
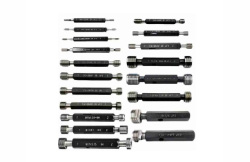
Thread Plug Gagues
The thread plug gauge is a measuring tool that is used to determine the precision of the internal thread's size. This gauge can be categorized into three types: ordinary coarse teeth, fine teeth, and pipe thread.
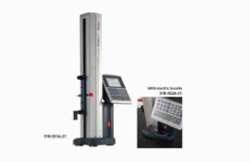
Mitutoyo Digital Height Micrometer
The pin plug gauge measures the inner diameter of a round hole. It is primarily utilized for measuring the inner diameter of small round holes that range between 0-10mm and requires a high level of precision.
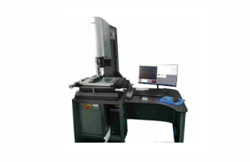
Project Meter
A digital caliper consists of a main ruler and a vernier. It is used to measure length, inside and outside diameter, and depth. The resolution for digital calipers is 0.01mm. It allows an error of ±0.03mm/150mm.