Automatic Machining
Automatic Machining
Automatic lathe machining Services – Precision Automatic lathe machining (turning) Parts Manufacturer & Supplier with 20 sets Automatic lathe machining Machine.
Automatic Lathe Machining Services
We are a professional manufacturer, producer, supplier, and exporter of Automatic lathe machining services, dedicated to the machining of precision Automatic lathe parts and the reduction of the cost of Automatic lathe parts. We have several advanced (Taiwanese-made) Automatic lathes and specialize in producing non-standard screws, copper pillars, injection molding copper nuts, nuts, shaped hexagons, shaped screws, miniature screw copper shafts, copper inserts, motor copper sleeves, copper nozzles, lighting spheres, brass pins, switch pins, thread pins, battery pins, capacitor pins, positioning pins, current pins, directional probes, probes, test pins, test probe, high-frequency pins, and plug hole processing, among others.
Masion provides high-quality Automatic lathe machining services in China and can offer you more competitive prices and faster delivery times. We have high-precision Automatic lathe machining equipment and a clean and tidy production workshop with an ISO9001 quality management system. We have excellent Automatic lathe machining capabilities and are proficient in high-efficiency machining with extremely high accuracy and surface roughness. Whether it’s copper, aluminum, stainless steel, or prototypes, or mass production, we can meet your needs. We have machining capabilities with precision up to 0.005mm and can provide complete inspection reports, so you can trust us with your project.

What We Do

CNC automatic lathes machining materials
Steel, alloy steel, aluminum alloy, titanium alloy, magnesium alloy, zinc alloy, stainless steel, brass, bronze alloy, copper alloy, hard alloy, carbon steel, tungsten steel, plastic parts, etc.

Surface treatment capabilities
Spray painting, baking painting, plastic spraying, sandblasting, shot blasting, anodizing, hard oxidation, micro-arc oxidation, electroplating, electrophoresis, laser engraving, screen printing, wire drawing, mirror polishing, dyeing, blackening, CD pattern, etching, high gloss, corrosion pattern, glue dropping, chromate, PVD plating, laser engraving.

One-stop processing
Combined with various processes such as casting, extrusion profiles, casting, hot forging, etc., to save a significant amount of costs.
Products Gallery
Automatic lathe machining contact pins
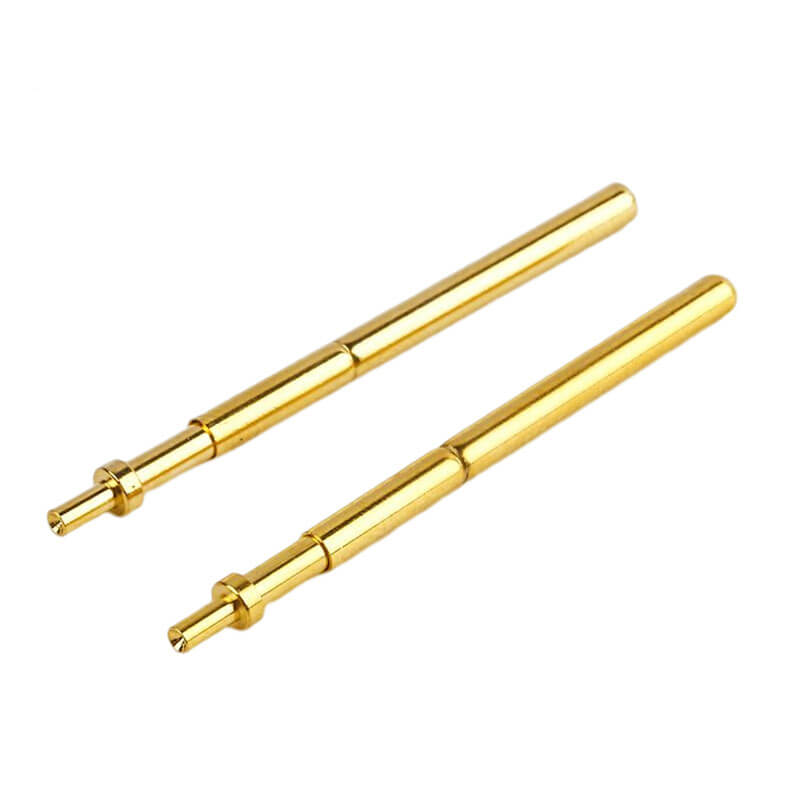
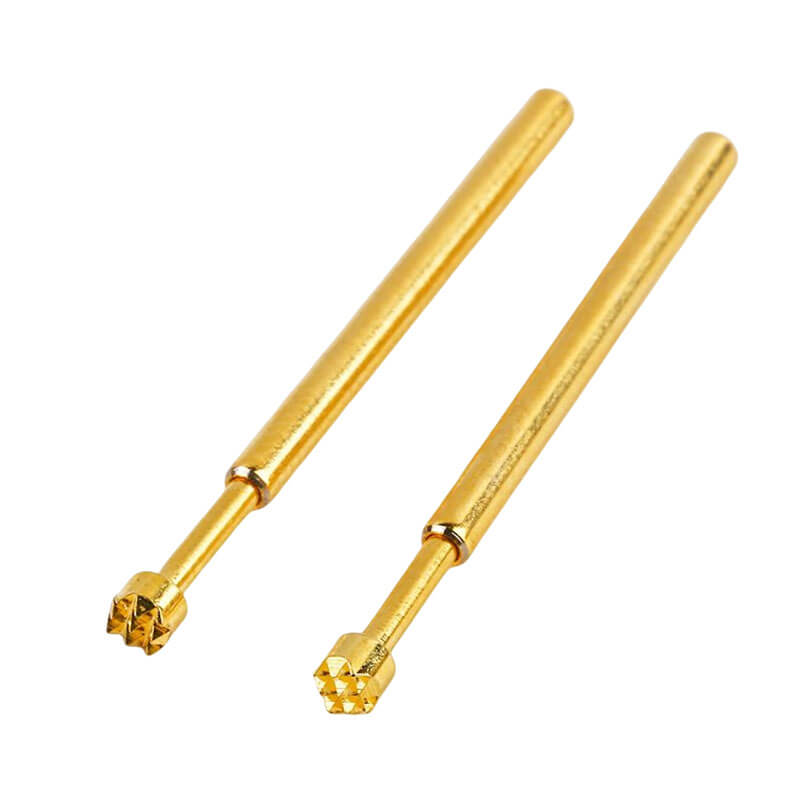
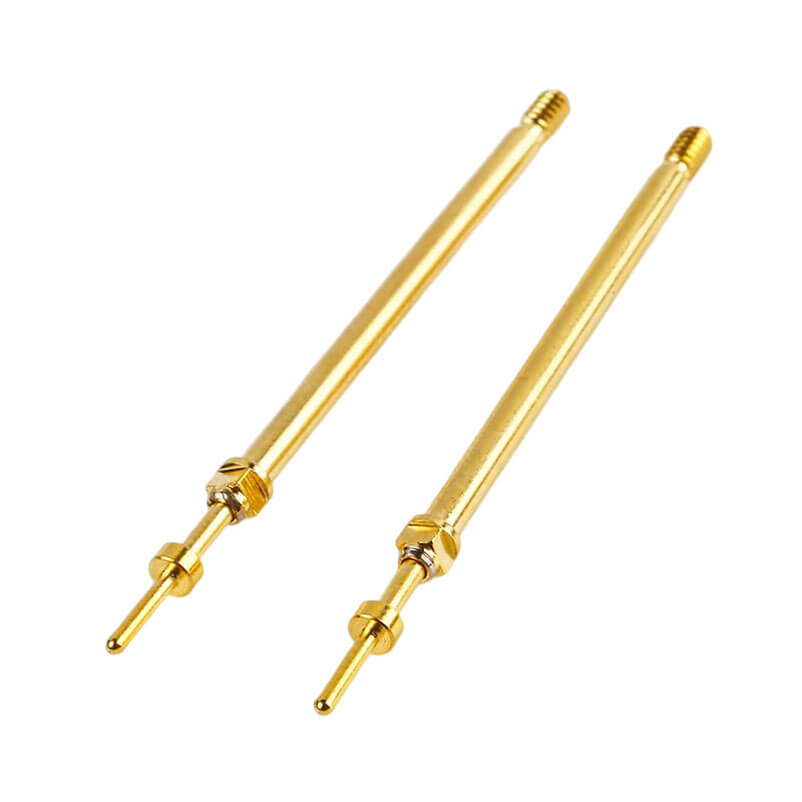
Automatic lathe machining Screw and nut studs
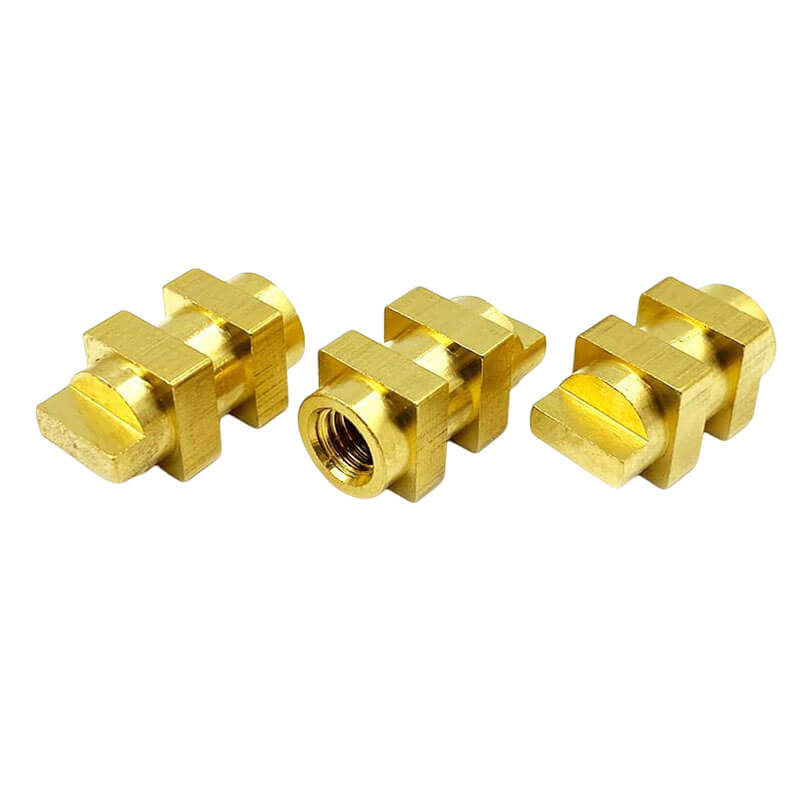

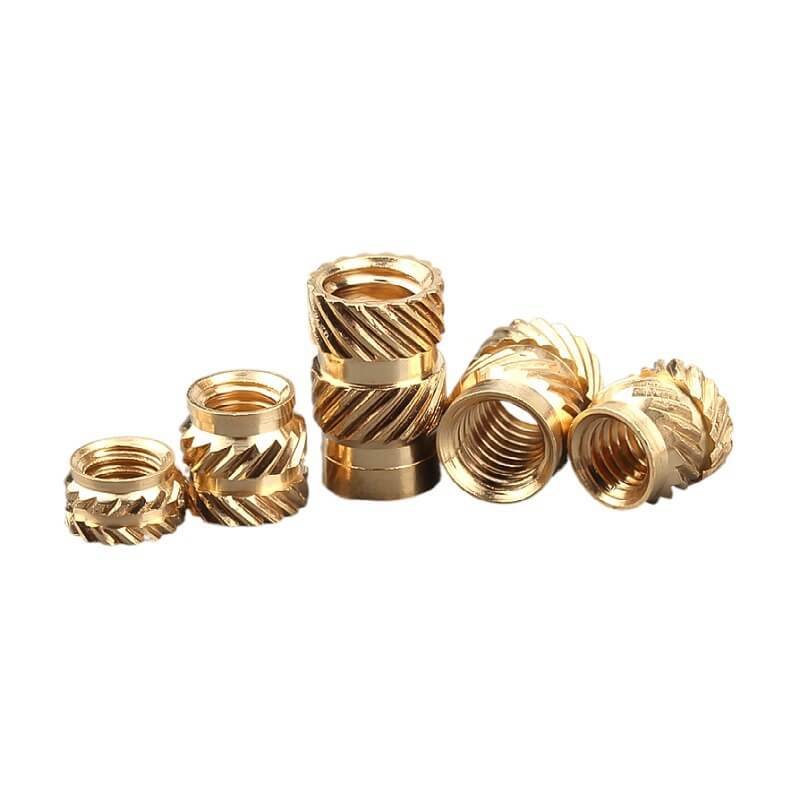
Automatic lathe machining instrument accessories




Why Choose Masion
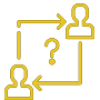
Rich Experience
Masion currently has production experience in automatic lathe machining parts for industries such as automotive parts, electronics, and communication.

Excellent Quality Service
Masion communicates with customers in time on production progress, 3+1 service, on-time delivery, and customer satisfaction are the standards for testing product quality.
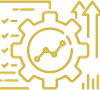
Quality Control
Masion has professional automatic lathes that control the quality of the production process. Professional mechanics and programmers ensure quality control. The professional inspection team controls product quality before shipment, ensuring a high yield of good-quality products. 100% inspection before shipment guarantees worry-free quality.
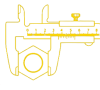
Machining precision
Masion’s Automatic Turning machining accuracy can reach ±0.005mm, with a surface roughness of Rα0.04-0.08μm.

Technical Strength
Masion adheres to Taiwan’s strong managerial experiencesand mature experience, strictly following precision-level manufacturing and machining techniques.

Fast Delivery
Masion has more than 20 advanced automatic lathes, samples can be delivered within 7 days, and each lathe can produce 2000 products per day. Large quantities of goods can be delivered within 10-15 days, and there is a sufficient inventory of conventional materials. The production runs 24Hrs*7 days.
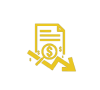
Reducing Costs
Masion often prepares Regular-size materials in stock to reduce costs through bulk purchasing. Automatic loading racks reduce labor costs by minimizing manual operations. Optimizing production processes reduces the occurrence of defective products and ultimately reduces production costs.

High product yield rate
Through material testing, precise equipment control, professional quality inspection processes, and attention to quality details, Masion ensures that the product yield rate reaches 99%.

Production Capacity
Masion is a manufacturer of automatic lathes parts with 15 years of experience, advanced automatic lathes, experienced designers, mechanics, engineers, and experience in processing tens of thousands of product cases.
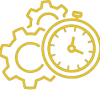
Rapid Production
Prompt collaboration with customers for structural and visual verification.
How do we guaranty the quality?
Man
Masion is equipped with excellent production and management talents, including programming masters and process engineers with more than 10 years of experience, skilled operators, and experienced production managers who are rigorous in their management and aim to deliver high-quality products on time.
Machine
Masion has high-precision automatic lathe machining with a dimensional accuracy of ±0.005mm and surface roughness of Rα0.04-0.08μm. Automatic lathe: Taiwanese machine, professional automatic lathe with cam, equipped with automatic feeding system to improve production efficiency and product accuracy, and avoid manual operation errors.
Environment
A clean and tidy machining workshop further ensures the precision of automatic lathe machining.

Materials
Masion performs a rigorous incoming material inspection to ensure that the physical properties of the customized automatic lathe machining parts are not affected by mixed materials. The authenticity of the materials is quickly identified by checking the material dimensions, material composition reports, and other material components during raw material feeding.
Method
Masion strictly complies with the ISO9001:2015 quality management system, and every automatic lathe machining part is ensured to be qualified. Inspection methods such as Vernier calipers, three-coordinate measuring machines, and two-dimensional inspections are used to ensure that the shipped products meet the quality requirements.
Automatic lathe machining Materials
Picture | Material | Brief Introduction | Material Trademark | Surface Finish | More |
---|---|---|---|---|---|
![]() | Aluminum Alloy | Aluminum alloy combines low density, high strength, high ductility, corrosion resistance, easy strengthening, surface treatment, good conductivity, recyclability, and low cost. | AL5052-T651, AL6061-T651, AL 7075-T651, AL6082-T651 etc | A. Polishing, B. Grinding, C. Radium carving, D. Bead Blasting, E. Painting, F. Coating, G. Anodizing, H. Hard anodizing, I. Teflon Coating, J. Laser marking, K. Silk printing, L. Silk transfer printing | Learn more |
![]() | Brass | Brass is an alloy composed of copper and zinc. High strength, good ductility, excellent mechanical properties, high wear resistance, good corrosion resistance, and lower price. | H58 H59、H62、HA177-2、HMn58-2、HPb59-1、HSn62-1 | A. Polishing, B. Grinding, C. Brushing, D. Laser marking, E. Screen printing, F. Transfer. | Learn more |
![]() | Stainless Steel | Low chromium content, 10.5%, high carbon content, 1.2%. High hardness, wear resistance, and high corrosion resistance. | 201、303、304、316、410、420、17-4PH | A. Polishing, B. Grinding, C. Vacuum heat treatment, D. Bead Blasting, E. Painting, F. Nitriding, G. Passivation, H. Zinc plating,J. Teflon, K. Titanium Coating, L. Laser marking, M. screen printing, N. transfer printing。 | Learn more |
Surface Finish of Automatic Turning Parts
Picture | Process | Brief Introduction | Materials | Colors | Texture | More |
---|---|---|---|---|---|---|
![]() | Electroplating(GOLDEN PLATING) | Electroplating is electrolytic deposition of thin metal layers to improve properties such as corrosion resistance and appearance. | Copper, cast iron, steel and stainless steel, aluminum, ABS plastics, polypropylene, polysulfone, and phenolic plastics, etc. | Red, yellow, gold, green, blue, purple, rose gold, titanium, white, black, etc. | Glossy or Matte | Learn more |
![]() | Polishing | Polishing is a surface machining method that smoothens and enhances the appearance of a workpiece through mechanical or chemical action. | Copper, cast iron, steel and stainless steel, aluminum, magnesium alloy, titanium alloy, etc. | N/A | Glossy | Learn more |
![]() | Anodizing | Anodizing is an electrochemical process that forms an oxide film layer on metal surfaces, enhancing corrosion resistance and surface properties. | Aluminum alloy, magnesium alloy, titanium alloy, etc., | Clear, black, grey, red, blue, gold,yellow, violet, double colors, camouflage color, etc. | Matte, semi-glossy, glossy | Learn more |
CNC Milling and Turning Service FAQs
Automatic lathes are commonly used in mass production environments where large quantities of small, precision parts need to be manufactured efficiently. These machines are capable of producing components with high accuracy and repeatability.
In automatic lathe machining, the workpiece is held in a collet or chuck and rotated at high speeds. The cutting tool, which is mounted on a tool turret, is programmed to move in a specific pattern dictated by the cam mechanisms or computer numerical control (CNC) system.
The automatic lathe’s cam-driven fixtures control the movement of the cutting tool, determining the depth, speed, and direction of the cuts. The tool can move along the X-axis (forward and backward), Z-axis (left and right), and sometimes the Y-axis (up and down) to perform various operations such as turning, facing, boring, drilling, threading, and grooving.
Automatic lathes can be classified into two main types: single-spindle and multi-spindle. Single-spindle automatic lathes have one spindle that can hold and work on a single workpiece at a time. Multi-spindle automatic lathes, on the other hand, have multiple spindles that can simultaneously work on several workpieces, significantly increasing production rates.
Advancements in technology have led to the development of CNC automatic lathes, which use computerized controls to precisely control the movement of the cutting tool. CNC automatic lathes offer greater flexibility, faster setup times, and the ability to produce more complex components compared to cam-driven automatic lathes.
Automatic lathe machining refers to the process of using an automatic lathe to manufacture small components or parts through automated machining techniques. This process involves setting up the automatic lathe with the appropriate tooling, programming the machine to execute the desired operations, and then allowing the machine to automatically perform the machining tasks.
Overall, automatic lathe machining plays a crucial role in the efficient production of small, intricate parts used in industries such as automotive, aerospace, electronics, and medical equipment manufacturing.
An automatic lathe is capable of machining a wide range of workpieces, including:
Shafts: Small cylindrical components used in various applications.
Screws: Threaded fasteners used for joining parts together.
Bolts: Threaded fasteners with a head designed for assembly and disassembly.
Nuts: Components with a threaded hole that pairs with screws or bolts.
Threaded rods: Long rods with continuous threading used for fastening or supporting applications.
Musical instrument components: Various parts used in musical instruments, such as bass volume knob potentiometer cap, string plate lifting screw, bass open string knob θ14 wire wheel post, string code, guitar screw knob, Guitar & Gear Accessories, guitar metal slide, guitar strap buckle,.etc.
Contact pins(probes): Brass or metal pins used for electrical connections in various devices and equipment.
Switch pins: Pins used in switches for electrical circuits.
Battery pins: Pins used for connecting batteries in electronic devices.
Capacitor pins: Pins used for connecting capacitors in electronic circuits.
Positioning pins: Pins used for precise alignment or location purposes.
Probes: Pins used for testing or probing electrical circuits or components.
High-frequency pins: Pins designed for transmitting or receiving high-frequency signals.
Plug socket pins: Pins used in plug sockets for electrical connections.
Directional probes: are specialized contact pins used in various testing and measurement applications.
Test pins, also known as test probes or test pins, are specialized tools used for electrical testing and measurement purposes.
These are just a few examples, and the versatility of automatic lathes allows for machining a wide variety of other small components and parts with precision and efficiency.
Automatic lathe machining is commonly used for manufacturing small shafts, screws, bolts, nuts, threaded rods, and various musical instrument components such as bass volume knob potentiometer cap, string plate lifting screw, bass open string knob θ14 wire wheel post, string code, guitar screw knob, Guitar & Gear Accessories, guitar metal slide, guitar strap buckle,and different contact pin such as brass pins, switch pins, threaded pins, battery pins, capacitor pins, positioning pins, current pins, directional probes, probes, test pins, high-frequency pins, and plug socket pin.
Automatic lathes can machine a wide range of materials, including metals (such as steel, aluminum, brass, and titanium), plastics, and even certain types of wood.
Automatic lathes are capable of achieving high precision levels, typically within micrometer tolerances. The exact precision level can vary depending on factors such as the specific machine used, the quality of the cutting tools, and the programming of the machining operations.
In general, modern automatic lathes are designed to provide precise and accurate machining results. Masion could achieve tolerances in the range of +-0.005mm (5 micrometers). However, it’s important to note that the actual precision achieved may vary depending on the specific requirements of the workpiece, the material being machined, and other factors.
Many manufacturers and machining service providers, including Masion strive to meet clients’ demands for precise components. We often have quality control measures in place to ensure the accuracy and consistency of the machined parts. This may involve regular calibration of the machines, rigorous inspection processes, and continuous improvement initiatives.
It’s worth noting that achieving high precision in automatic lathe machining also requires attention to factors such as tool selection, tool wear monitoring, machine stability, and proper setup. By considering these factors and employing best practices, automatic lathe machining can consistently deliver parts with the desired precision level for a wide range of applications.
Yes, we can. We have already helped customers manufacture products of the same quality as Feinmetall, meeting their requirements in terms of precision and quality.
The maximum size of the workpiece that can be machined with an automatic lathe (turning) usually is 32mm.
The cost of automatic lathe machining parts can vary depending on factors such as the complexity of the part, material selection, quantity ordered, and the specific machining services.
For simpler parts such as screws, bolts, threaded rods, and nuts, the choice of material often depends on the pricing. Stainless steel and copper tend to be relatively expensive, while aluminum is usually more affordable. As a rough estimate, aluminum parts can be priced at around 0.005 USD per piece, while copper and stainless steel parts can range from 0.01 to 0.1 USD per piece.
On the other hand, more complex parts like contact probes require higher precision and may need additional surface treatments, such as gold-plating. As a result, the unit price for contact probes is generally higher, ranging from 0.1 to 0.5 USD per piece.
Free Sample
Explore Other Services

Wire Edm Machining
What is EDM Machining – Electrical Discharge Machining Definition https://cncmasion.com/wp-content/uploads/2023/11/390137809503.mp4 Electrical discharge machining or EDM, also known as spark machining or spark eroding, is a metal fabrication process and non-traditional
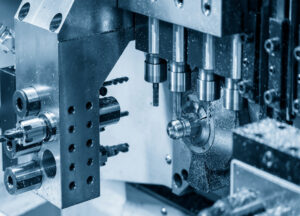
Automatic Machining
Automatic lathe machining Services – Precision Automatic lathe machining (turning) Parts Manufacturer & Supplier with 20 sets Automatic lathe machining Machine. Automatic Lathe Machining Services We are a professional manufacturer,

CNC Milling and Turning Services
CNC Milling and Turning Services –China CNC Turning Milling Parts Manufacturer. CNC milling and turning is one of the advanced manufacturing technologies in the international mechanical processing industry. It integrates