CNC Turning Services
CNC Turning Services
As a professional CNC turning manufacturer, supplier, and factory, Masionis dedicated to delivering high-precision CNC turning parts with a strong focus on cost-effectiveness. With our advanced CNC lathes, we have the capability to manufacture a wide range of CNC turning parts, including rope skipping handles, tattoo pen shells, pet ash boxes, flashlights, motorcycle fuel filters, golf drive shaft sleeves, wall pendants, stainless steel gaskets, knobs, screws, locking sleeves, ear temperature gun probes, precision shafts, optical instrument objective rings, and various other rotating components.
At Masion, we take pride in providing top-quality CNC turning services in China at a more competitive price and with faster delivery times. Our production shop is clean, organized, and operates in accordance with the ISO 9001 quality management system.
At Masion, with our experienced team, we excel in efficiently machining CNC turning parts with high accuracy and excellent surface roughness, regardless of the material used, whether it’s metal or plastic, and whether it’s a prototype or a mass production project.
We offer comprehensive testing reports and can achieve a maximum precision of ±0.005mm. You can trust us with your projects, and we will ensure that your requirements are met to the highest standards.

What We Do

CNC Turning materials
Steel, Aluminum, Titanium, Magnesium, Stainless steel, Brass, Bronze, Copper, Hard alloy, Carbon steel,Tungsten steel, Plastic parts, etc.

Surface treatment capacity
Spray paint, Sandblasting, Anodizing, Electroplating, Electrophoresis, Silk screen printing, Mirror polishing, Blackening, PVD plating, Laser engraving, Powder Coating

One-stop Service
Including Forging, Casting, Extrusion, Stamping, Casting, and Hot Forging, which saves a lot of costs.
Products Gallery
Masion’s CNC turning expertise extends to various industries, including outdoor sports equipment, medical devices, automobiles, beauty products, etc.
Outdoor Sports CNC turning Parts




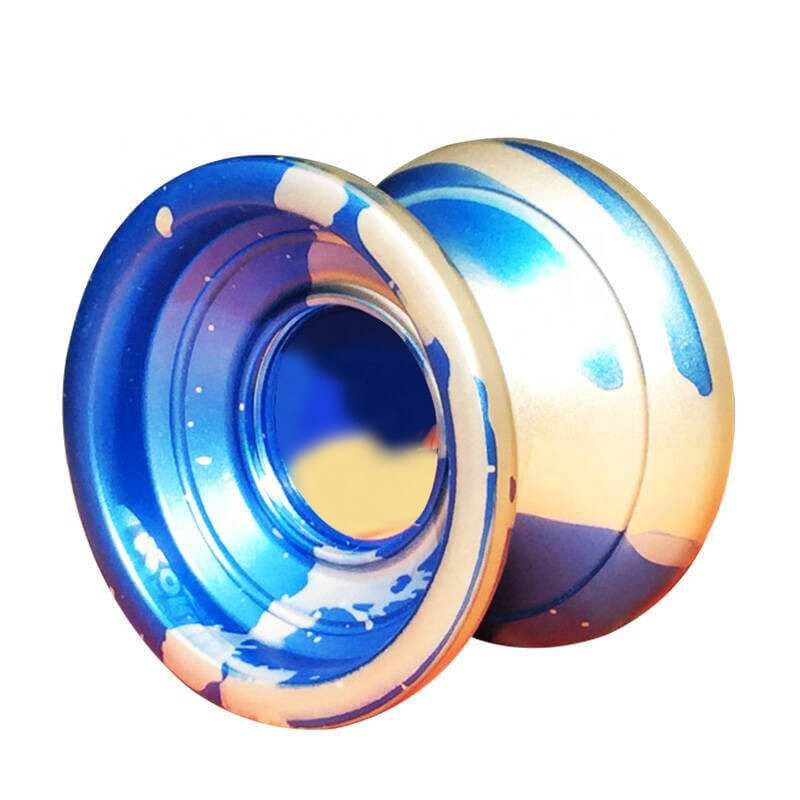
Other CNC Turning Parts
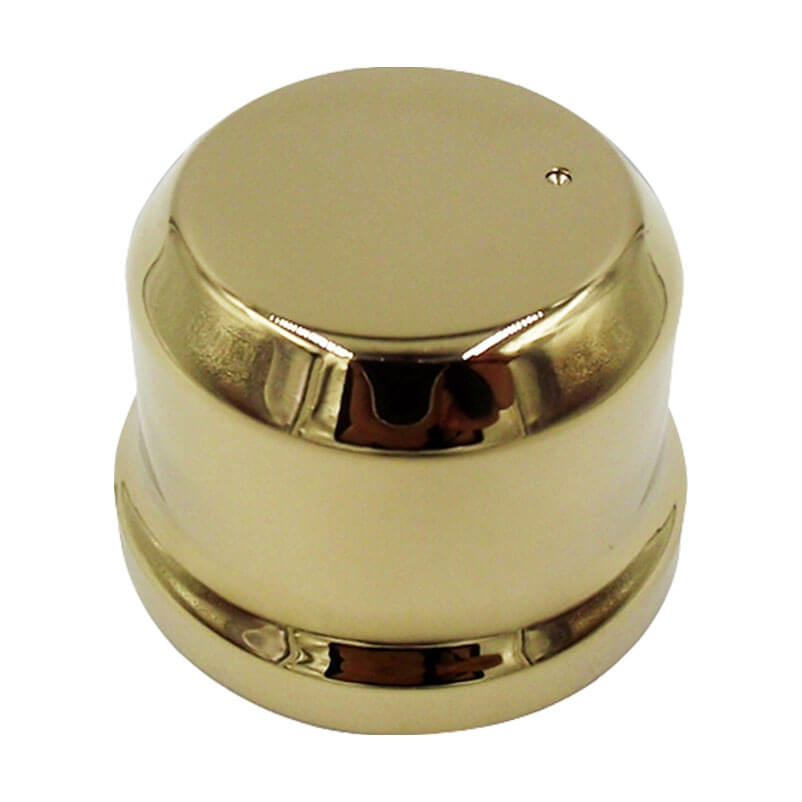



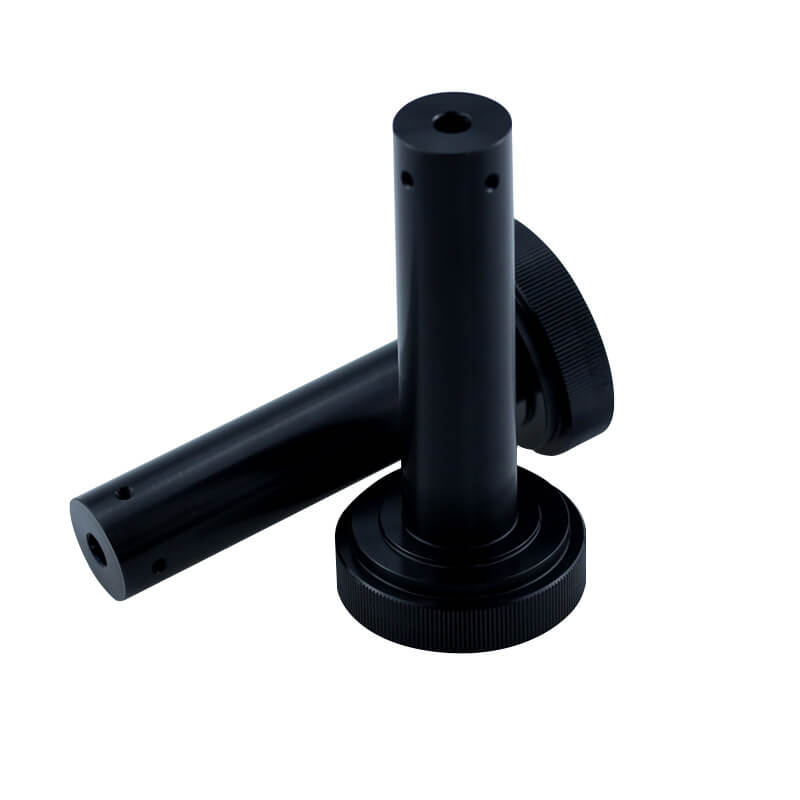
Medical CNC Turning Parts
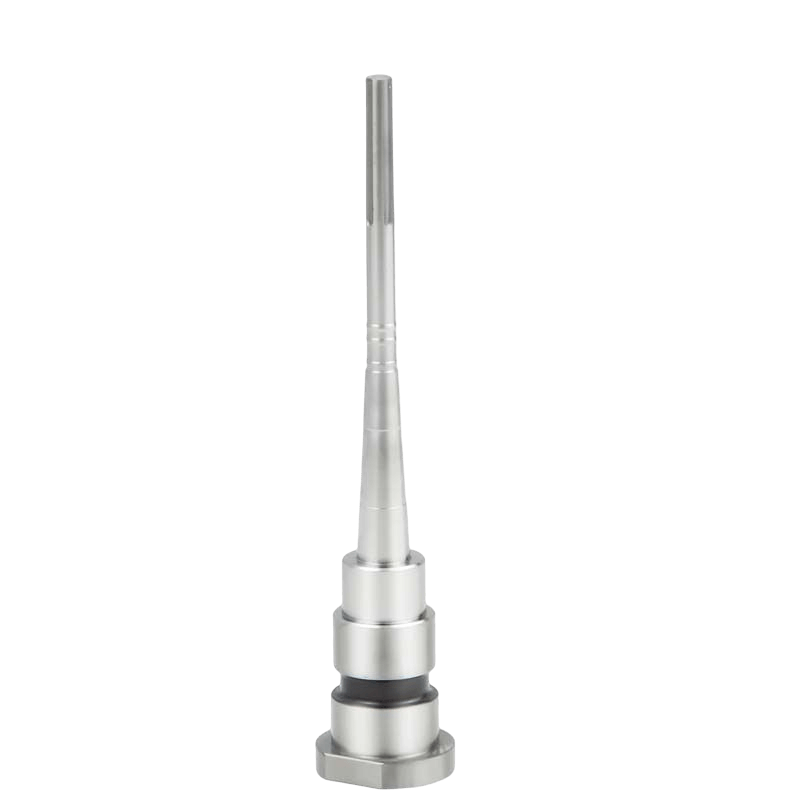

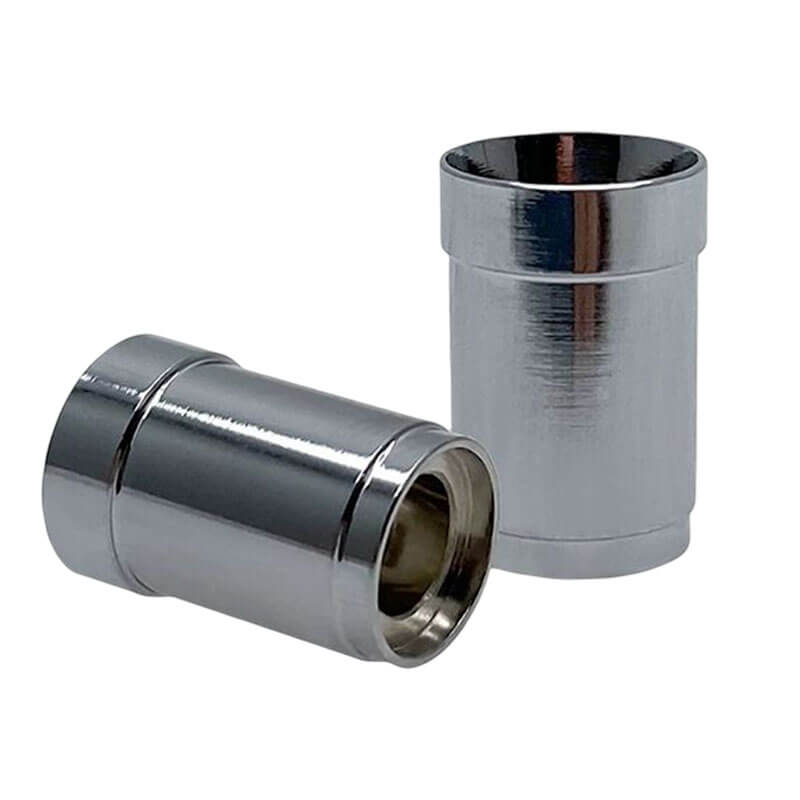
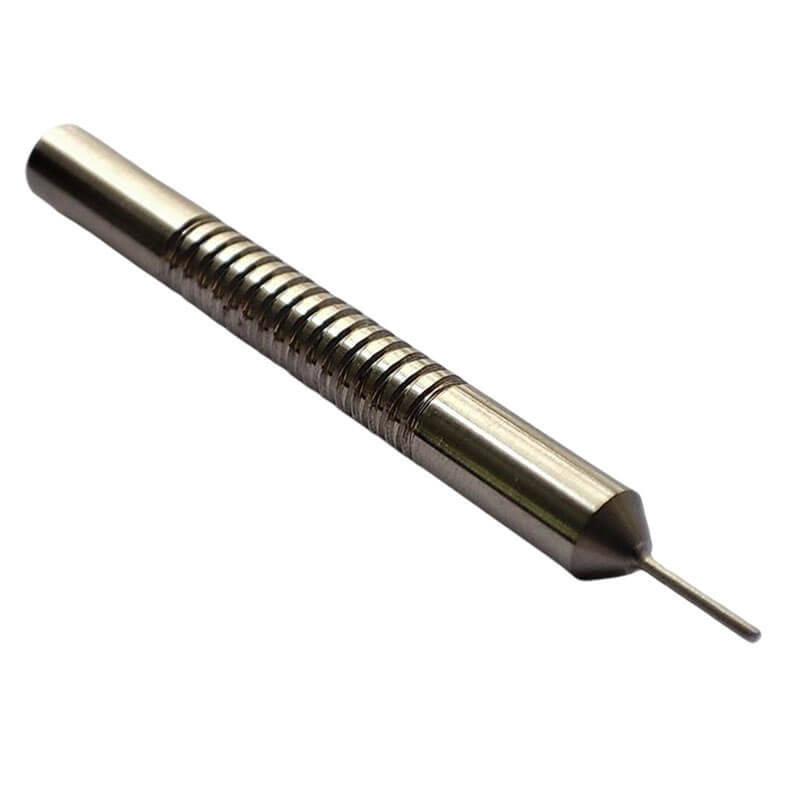

Automobile CNC Turning Parts
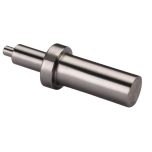




Beauty CNC Turning Parts




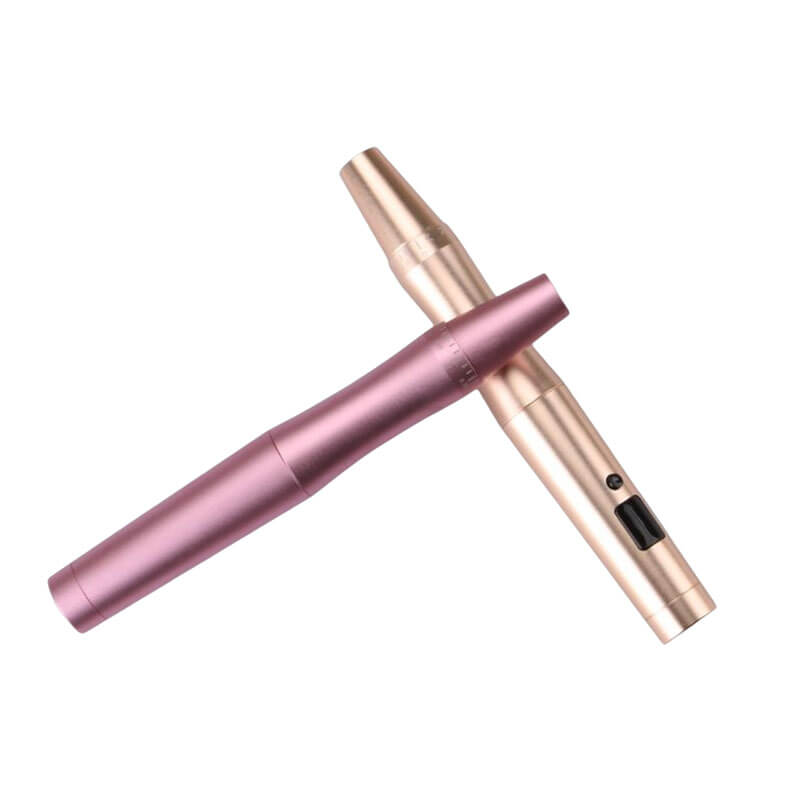
Why Choose Us
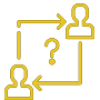
Rich Experience
Masion specializes in CNC turning machining parts. Our expertise ensures precise and reliable solutions for your specific needs.

Excellent Service
We prioritize effective communication with you, Additionally, we offer a 3+1 service, guaranteeing on-time delivery of their CNC-turning products.
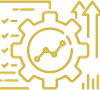
Quality Control
Masion has a dedicated inspection team to ensure high product yield and on-time delivery. We conduct inspections before shipment.
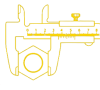
Machining Accuracy
We achieve machining accuracy levels of ±0.005mm, and our surface roughness ranges from Rα0.04 to 0.01μm.

Strong Technology
Our CNC machining parts meet the highest standards of accuracy, reliability, and performance to satisfy diverse customer needs.

Fast Delivery
Masion delivers samples within 7 days and small batches within 10-15 days. We maintain sufficient materials and manufacture in 7*24 hours.
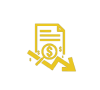
Cost Reduction
Masion offers CNC turning solutions to reduce costs. We reduce costs through a high yield of good parts and respond quickly to abnormal situations.

High Product Yield
Masion has ten quality control processes for control, layer upon layer, ensuring a 99% product quality rate.

Production Strength
With over 15 years of experience in CNC turning, we boast an advanced CNC lathe and a team of skilled designers, mechanics, and engineers.
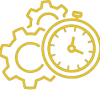
Rapid Production
Masion is efficiently working with customers to verify the structure and appearance of CNC parts, ensuring timely feedback throughout the order.
CNC Turning Tolerance
Threaded Hole
Radius
Minimum Hole
• Minimum Radial: 0.08 inches (0.5 mm), 0.04 inches (0.5 mm) for aluminum and brass.
Groove
• Minimum Outer Diameter (OD) groove width for aluminum and brass: 0.02 inches (0.5 mm)
• Maximum OD groove depth: 1.00 inches (25.4 mm) — varies with groove width.
Linear Dimension
Hole (not reamed)
Axial Diameter
How do We Guaranty the Quality?
Man
Masion has a group of exceptional production and management personnel, with over 10 years of extensive experience in CNC turning, which aims to deliver high-quality products on time. The team comprises a proficient programming master, an experienced process engineer, and skilled operators. The production manager, a former engineer from a Taiwanese company, brings a wealth of experience and strict management practices to the table.
Machine
Masion’s CNC turning process is highly precise, with a dimensional accuracy of ±0.005 and a finish of Rα0.04 -- 0.01μm. Our turning CNC machining software includes professional CAM software for precision turning machining that enables the development of turning processes and generates CNC programs with a single key, reducing the possibility of manual errors.
Environment
Masion’s machining workshop is clean and organized, which enhances the accuracy of CNC turning machining.

Materials
Masion conducts strict inspections of incoming materials to ensure the physical properties of customized turning CNC machining parts. We determine the authenticity of raw materials quickly through composition, size, and material report testing.
Method
Masion strictly implements the ISO9001:2015 quality management system to ensure the quality of each CNC turning part. We perform Coordinate Measuring Machine product testing and project meter testing before shipment to meet quality requirements.
CNC Turning Materials
Picture | Material | Brief Introduction | Material Trademark | Surface Finish | More |
---|---|---|---|---|---|
![]() | Aluminum Alloy | Aluminum alloy: Low density, high strength, high ductility, corrosion resistance, easy to strengthen and treat, good conductivity, recyclable, and cost-effective. | AL5052-T651, AL6061-T651, AL 7075-T651, AL6082-T651 etc | A. Polishing, B. Grinding, C. Radium carving, D. Bead Blasting, E. Painting, F. Coating, G. Anodizing, H. Hard anodizing, I. Teflon Coating, J. Laser marking, K. Silk printing, L. Silk transfer printing | Learn more |
![]() | Brass | Brass is an alloy composed of copper and zinc. High strength, good ductility, excellent mechanical properties, high wear resistance, good corrosion resistance, and lower price. | H58 H59、H62、HA177-2、HMn58-2、HPb59-1、HSn62-1 | A. Polishing, B. Grinding, C. Brushing, D. Laser marking, E. Screen printing, F. Transfer. | Learn more |
![]() | Bronze | Bronze: Copper alloy with tin (3-14%) and lead. Low melting point, high strength, excellent castability, chemical stability, ductility, wear resistance, corrosion resistance, vibrant color. | QSn-6-6-3 SAE660 | A. Polishing, B. Grinding, C. Brushing, D. Laser marking, E. Screen printing, F. Transfer. | Learn more |
![]() | Copper | High copper content, ranging from 99.5% to 99.95%. High density, melting point, excellent electrical conductivity, thermal conductivity, ductility, and corrosion resistance. | T1、T2、T3、TU1、TU2b | A. Polishing, B. Grinding, C. Brushing, D. Laser marking, E. Screen printing, F. Transfer. | Learn more |
![]() | Magnesium alloy | Magnesium alloy: High strength, low density (approx. 1.8g/cm3), large elastic modulus, excellent heat dissipation, remarkable impact resistance. | AZ31、AZ41、AZ61 | A. Polishing, B. Grinding, C. Brushing, D. Laser marking, E. Screen printing, F. Transfer. A. Polishing, B. Brushing, C. Bead Blasting, D. Micro-arc oxidation | Learn more |
![]() | Stainless Steel | Low chromium content, 10.5%, high carbon content, 1.2%. High hardness, wear resistance, and high corrosion resistance | 201、303、304、316、410、420、17-4PH | A. Polishing, B. Grinding, C. Vacuum heat treatment, D. Bead Blasting, E. Painting, F. Nitriding, G. Passivation, H. Zinc plating,J. Teflon, K. Titanium Coating, L. Laser marking, M. screen printing, N. transfer printing。 | Learn more |
![]() | Titanium alloy | Titanium alloy is an alloy made from multiple types of titanium and other metals. Excellent strength, corrosion resistance, and heat resistance. | 1,2,3,4,5 Grade | A. Polishing, B. Grinding, C. Brushing, D. beadblasting, E. Laser marking, F. Screen printing, G. Transfer printing. | Learn more |
![]() | ABS | Plastics have poor thermal conductivity, low coefficient of thermal expansion, and low elastic modulus. | ABS-GF30 AG15A1-H | Painting, F. radium carving, L. chrome plating, R. laser marking, S. silk screen, T. Transfer printing | Learn more |
![]() | PTFE | Plastics have poor thermal conductivity, low coefficient of thermal expansion, and low elastic modulus. | 008 1700 | Painting, F. radium carving, L. chrome plating, R. laser marking, S. silk screen, T. Transfer printing | Learn more |
![]() | POM | Plastics have poor thermal conductivity, low coefficient of thermal expansion, and low elastic modulus. | POM-C POM-H | Painting, F. radium carving, L. chrome plating, R. laser marking, S. silk screen, T. Transfer printing | Learn more |
![]() | PEEK | Plastics have poor thermal conductivity, low coefficient of thermal expansion, and low elastic modulus. | 8200 PEEK, PEEK 4500G, PEEK 1000 | Painting, F. radium carving, L. chrome plating, R. laser marking, S. silk screen, T. Transfer printing | Learn more |
![]() | PMMA | Plastics have poor thermal conductivity, low coefficient of thermal expansion, and low elastic modulus. | Altuglas V825T、Altuglas V825、Altuglas V920 | Painting, F. radium carving, L. chrome plating, R. laser marking, S. silk screen, T. Transfer printing | Learn more |
![]() | Steel | Carbon steel: Steel with carbon content below 1.7%. Ultra-high-strength steels: High strength, toughness, good hardenability. | 45#、40Cr、42CrMo、42CrMoB7 | A. Polishing, B. Grinding, C. Nitriding, D. Bead Blasting, E. Painting, F. Radium carving, H. Hard anodizing, I. Passivation, J. Galvanizing, K. Electroless nickel plating, L. Chrome plating, M. blackened/oxidized black, O. Teflon, P. Titanium coating, Q.LC coating, R. Laser marking, S. Silkscreen, T. Transfer Printing | Learn more |
Surface Finish of CNC Turning Parts
Product surface finish can be highly specific to meet different customer demands. We provide various surface finish options to improve product quality, appearance, and market competitiveness. The surface finish for CNC turning parts is intended to enhance their appearance, surface hardness, roughness, chemical resistance, and corrosion resistance. Below are several common surface finish choices available, If you want to know more about surface finish. Please Learn More.(Link to surface finish )
Picture | Process | Spec | Material | Colors | Appearance | More |
---|---|---|---|---|---|---|
![]() | Dacromet | Dacromet is a corrosion-resistant coating with zinc, aluminum, chromic acid, and water, enhancing product quality and longevity. | Iron and steel and non-ferrous metals such as aluminum, magnesium and another alloy, copper, nickel, zinc and etc. | Red, silver, white, black, blue, green, yellow, etc. | Matte, Glossy or semi-glossy | Learn more |
![]() | Electrophoresis | Electrophoresis forms a colored paint film layer on the workpiece surface, providing corrosion resistance, wear resistance, decoration, and special functions. | Aluminum, steel, stainless steel, Magnesium alloy, zinc alloy, etc. | Red, green, blue, purple, white, black, etc. | Glossy or Matte | Learn more |
![]() | Electroplating | Electroplating applies a thin metal layer using electrolytic principles to prevent oxidation and enhance wear resistance, conductivity, reflectivity, corrosion resistance, and appearance. Common processes include chromium, nickel, gold, silver, and tin plating. | Copper, cast iron, steel and stainless steel, aluminum, ABS plastics, polypropylene, polysulfone, phenolic plastics, etc. | Red, yellow, gold, green, blue, purple, rose gold, titanium, white, black, etc. | Glossy or Matte | Learn more |
![]() | Polishing | Polishing reduces surface roughness, achieving a smooth and bright finish through mechanical, chemical, or electrochemical methods. It removes imperfections, such as oxidation and scratches, enhancing the paint's appearance. | Copper, cast iron, steel and stainless steel, aluminum, magnesium alloy, titanium alloy, etc. | N/A | Glossy | Learn more |
![]() | Anodizing | Anodizing is an electrochemical process for metals like aluminum and titanium, forming an oxide film layer on the surface. It improves corrosion resistance, wear resistance, hardness, decoration, and surface protection. | Aluminum alloy, magnesium alloy, titanium alloy, etc., | Clear, black, grey, red, blue, gold,yellow, violet, double colors, camouflage color, etc. | Matte, glossy, semi-glossy | Learn more |
![]() | Bead Blasting | Compressed air propels sand materials at high velocities to remove rust, stains, and paint from metal surfaces, achieving a renewed appearance by grinding down burrs and scars. | Cast iron, steel, stainless steel, aluminum alloy, magnesium alloy, titanium alloy, ABS, etc. | N/A | Matte | Learn more |
![]() | Powder Coating | Plastic spraying electrostatically applies powder coating to metal surfaces, forming a protective film against corrosion and wear while improving appearance with various colors. | Cast iron, steel, aluminum alloy, magnesium alloy, ABS, and various plastics. | Black, white, blue, green, yellow, purple, all the colors on the Pantone color card | Matte or glossy | Learn more |
![]() | PVD(Physical Vapour Deposition) | PVD vaporizes material into gas and deposits functional films on substrates, enhancing appearance, hardness, and durability. | Iron, stainless steel, aluminum alloy, titanium alloy, copper, ceramics, tungsten steel, zinc alloy, ABS, and various plastics | Gold, gun black, coffee, purple, heptagon, royal blue, azure blue, black, titanium gray, so why bowl, rose gold, gold, champagne gold, etc. | Glossy | Learn more |
CNC Turning Service FAQs
Precision and Accuracy: Masion CNC turning services utilize advanced computer-controlled machinery to ensure a high level of precision and accuracy in the manufacturing process. Usually it is +-0.005mm. CNC (Computer Numerical Control) machines can perform complex operations and achieve consistent results, reducing human errors and achieving tight tolerances.
Small Batch Orders: We welcome small batch orders (5-100pcs) and work closely with our customers to gradually increase the order volume and achieve mutual growth. Establishing long-term partnerships with our customers is crucial, and we provide expertise, efficient supply chain management, and flexible production capabilities to meet their needs. We look forward to building solid partnerships with our customers for shared success.
Free Samples: For simple turning parts, Masion offers free samples, with customers only responsible for the shipping costs. For larger turning parts, Masion will initially charge for the samples, and once the sample quality is confirmed by the customer, we will gradually waive the sample fees within the subsequent orders, thus providing samples for free. Masion is committed to ensuring sample quality, and in case of any non-compliance, we will refund the sample fees.
Fast Delivery Capability: We highly value fast delivery capability, and partnering with Masion enables us to provide samples quickly and shorten delivery times for batch orders. Time is critical, and the ability to deliver quickly is essential for market dominance. Through collaboration with Masion, we ensure timely provision of samples and meet project delivery timelines. Regardless of project scale, we are dedicated to efficient supply chain management and production processes to meet time-sensitive requirements. We look forward to collaborating with you and contributing our fast delivery capability to your success.
Complex Design: Masion CNC turning services excel in producing parts with intricate designs and complex geometries. By programming and controlling the motion of cutting tools, complex shapes and contours can be created, which are difficult or impossible to achieve manually. This opens up new possibilities for product design and enables the production of highly intricate and complex components.
Cost-effectiveness: While the initial investment in CNC turning equipment may be significant, the long-term cost-effectiveness of Masion services is evident. CNC machines can operate continuously with minimal supervision, reducing labor costs. Additionally, the precision and efficiency of CNC turning services minimize material waste and rework, resulting in overall cost savings.
Quality Control and Inspection: Masion CNC turning services incorporate quality control measures throughout the manufacturing process. CNC machines can be equipped with sensors and probes for in-process detection, ensuring that part dimensions and specifications remain within the required tolerances. This real-time quality monitoring helps identify and rectify any issues promptly, thereby improving overall product quality.
The main difference between CNC turning and CNC milling lies in the movement of the workpiece and cutting tool. In CNC turning, the workpiece rotates against a stationary cutting tool, whereas in CNC milling, the cutting tool rotates while the workpiece remains stationary. CNC turning is typically used for cylindrical shapes and external features, while CNC milling is better suited for complex geometries and internal features.
Masion can accommodate workpieces with a maximum machining diameter of 630mm and a maximum machining length of 1400mm.
Masion’s CNC turning machines can achieve a tolerance of +-0.005mm for CNC turning parts.
Typically, Masion can complete a CNC turning project within 10-15 days for simple CNC turning parts and around 25-30 days for more complex CNC turning parts. This timeframe takes into account our extensive experience and the availability of over 50 sets of turning machines.
Yes, Masion specializes in working with custom designs in CNC turning services. Our team includes three designers who can create 2D or 3D CAD models based on client specifications. They will analyze the CNC turning process based on the customer’s drawings and develop the corresponding CNC turning process flow.They can then program the CNC machines to produce the desired cylindrical parts according to the custom design.
Common file formats used for CNC turning projects include .PDF, .STL, .STEP, .IGES, and .DWG. These formats contain the necessary 3D model data that CNC machines use to interpret and execute the turning process.
Masion support one stop CNC turning services and consider to deduct the service cost.So we will use the lowest CNC turning process to work with our clients to decrease the cost. However, clients should know the cost of CNC turning services depends on factors such as the complexity of the part, the material, the machine setup time, and the desired quantity. We often provide quotes based on these factors.
While CNC turning excels at machining cylindrical shapes, it may have limitations when it comes to extremely complex geometries that include non-cylindrical features. To address this, CNC turning and milling can be employed for complex cylindrical products, allowing the workpiece to be machined in a single operation and overcoming the challenges associated with intricate components.
Yes, CNC turning services can provide a range of surface finishes and textures according to the project’s requirements. Masion offers various options for surface treatments in CNC turning services. This can include smooth finishes, knurling, grooves, Vibration grinding, Satin,bead blasting, and other specific surface treatments including:
(1) Mechanical surface treatment: sandblasting, shot blasting, polishing, rolling, powder coating, brushing, spraying, painting, oiling.
(2) Chemical surface treatment: blue and black, phosphating, pickling, electroless plating of various metals and alloys, TD treatment, QPQ treatment, chemical oxidation.
(3) Electrochemical surface treatment: anodization, electrochemical polishing, electroplating.
(4) Modern surface treatment: chemical vapor deposition CVD, physical vapor deposition PVD, ion implantation, ion plating, laser surface treatment.
These surface treatments can be used to achieve different finishes, textures, and desired properties on the machined parts.
To ensure quality control in CNC turning services, we employ several measures. Firstly, we maintain strict compliance with the ISO 9001 quality management system standards throughout our production process. Secondly, we have implemented a comprehensive inspection process consisting of multiple stages, including initial sample inspection, in-process inspection, and pre-shipment inspection. Our inspection tools encompass advanced precision testing equipment like CMM (Coordinate Measuring Machine) and project meters, in addition to commonly used measuring tools like micrometers and calipers. These measures enable us to uphold rigorous quality control standards.
- Drawing Analysis: The provided drawings from the customer need to be analyzed to determine the machining processes and paths for each dimension. Firstly, the specifications, performance, and functions of the CNC lathe should be compared with the geometric shapes and dimensions of the parts to determine if they meet the requirements.
- Process Analysis: Next, a process analysis should be carried out. Due to the inability of CNC lathes to be manually adjusted during the machining process like conventional machine tools, an economically reasonable process plan must be established in advance. This includes determining the part’s positioning and fixtures, machining sequence, tool paths, tools, cutting parameters, heat treatment methods, as well as calibration and auxiliary processes.
- Selection of Suitable Tools: Based on the characteristics of the product such as outer diameter, inner diameter, holes, slots, etc., suitable tools like external cutting tools, internal cutting tools, drills, groove cutters, etc., should be selected. Additionally, suitable fixtures should be chosen based on the workpiece’s outer diameter. The tools and fixtures should then be installed in the designated positions according to the product’s requirements, which may require adjustments.
- Documentation or Programming: Prior to machining, the machining program for the workpiece needs to be developed. If the program is lengthy or complex, it is preferable to perform programming off the machine using a programming machine or manual programming to avoid occupying the machine’s time. For shorter programs, they should also be recorded on a program sheet.
- Machine Startup: Before commencing machining, it is generally necessary to start up the machine tool followed by the system. In some cases, the machine tool and system are interlocked, meaning the machine tool must be powered on to display information on the CRT.
- Reference Point Return: For machine tools with incremental control systems, it is essential to first execute the reference point return operation to establish the movement standards for the machine tool’s coordinates.
- Program Editing Input: If modifications are required for the input program, the programming mode selector switch should be set to the EDIT position, and the edit keys can be used for adding, deleting, or modifying operations.
- Machine Tool Locking: Prior to checking the program, the machine tool needs to be locked, and then the program can be run. If any errors are found, it is necessary to re-edit the program.
- Program Verification and Trial Cutting: Generally, the tool path is checked during the simulation process, followed by observing the tool movement during idle rotation. Finally, the workpiece is clamped for trial cutting.
- Proceed with workpiece setup, alignment, and tool setting. This can be achieved through manual incremental movements, continuous movements, or manual playback disc movements on the lathe. Align the tool with the program’s starting point and adjust the tool’s reference.
- Start coordinate feed and begin continuous machining. Usually, machining is performed using programs stored in the memory, which has a lower failure rate compared to using programs on paper tape. The feed rate during machining can be adjusted using the feed rate multiplier switch. The feed motion can be temporarily paused for observation or manual measurements by pressing the feed hold button (FEEDHOLD). To resume machining, press the CYCLE START button. To ensure the program’s correctness, a final check should be conducted before machining. For turning operations, a pencil can be used to draw the workpiece profile on paper as a visual aid. If the system has tool path simulation functionality, it can be used to verify the program’s correctness.
- Utilize various CRT screens to display the position of the worktable or tool, program information, and the machine tool’s status, enabling the operator to monitor the machining process.
- After the program is completed, if it needs to be saved, it can be stored in the memory of the CNC system. If the program is too long, it can be output to an external device for preservation.
- In the case where the workpiece is still clamped in the fixture, perform dimensional inspection of the workpiece. If the dimensions do not meet the requirements, appropriate tool compensation should be applied, and re-machining should be performed until the dimensions are within the specified range before removing the workpiece.
- Lastly, the machine tool should be powered off first, followed by shutting down the system.
- Post-Processing: Conduct a comprehensive inspection of the finished workpieces and perform special measurements on critical dimensions. Then, carry out surface treatments as required, such as oxidation, plating, PVD coating, spray coating, painting, electrophoresis, etc.
- Perform visual inspections and dimensional measurements on the workpieces after surface treatments to ensure they meet the required quality standards.
Finally, package the workpieces and ensure that all aspects related to the external packaging, including external box dimensions, weight, labels, logos, etc., comply with the specified requirements.
Absolutely! CNC turning services are an excellent choice for rapid prototyping. Although primarily used for cylindrical parts, they offer a swift and precise method for prototyping specific components. Hence, Masion gladly accept small-batch rapid prototyping orders, including 5-10 units. Our efficient production process ensures quick delivery to customers, significantly reducing waiting times.
Yes, Masion provides a one-stop service that includes not only CNC turning services but also a comprehensive range of options for surface treatments (such as oxidation, plating, Dacromet, tin plating, QPQ, etc.), assembly, packaging, and shipping for various products. Masion is committed to assisting customers with any service they require and strives to meet their needs to the fullest extent possible. Customer satisfaction is Masion’s ultimate goal and driving force.
When selecting a CNC machining service provider, the following factors should be considered:
- Does the factory have sufficient production capacity and necessary machines and facilities to support production?
- Does the factory have experience in producing similar products?
- Does the factory have advanced inspection devices to ensure product quality?
- Do the factory’s machinists follow standardized operating procedures and meet quality management standards?
- Are the lead times for sample production and large-scale production short?
- Does the factory’s pricing meet customer expectations?
- Can the communication personnel quickly understand customer requirements and provide solutions?
- Does the sample production meet the dimensional tolerances specified in the drawings?
Note: It’s worth mentioning that while the translation provided here is accurate, it is always recommended to review and proofread translations for the specific context or audience.
Free Sample
Explore Other Services

CNC Turning Services
https://youtu.be/TfLpTK81Lw0 As a professional CNC turning manufacturer, supplier, and factory, Masionis dedicated to delivering high-precision CNC turning parts with a strong focus on cost-effectiveness. With our advanced CNC lathes, we

Precision Machining Services
Precision Machining Services–Ultra Precision Machining Manufacturer If your product requires a very high level of dimensional tolerance that cannot be achieved through CNC machining alone, the best solution would be

5 Axis CNC Machining Services
Precision 5 axis cnc machining manufacturer with 30 sets 3.4.5 Axis CNC Machining Center. Traditional CNC machining centers typically have three axes: X, Y, and Z. A five-axis CNC machining