PEEK CNC machining
PEEK CNC machining
Polyetheretherketone (PEEK) is a special type of high-performance polymer material known for its high mechanical strength, resistance to high temperatures, impact resistance, flame retardancy, acid and alkali resistance, hydrolysis resistance, wear resistance, fatigue resistance, radiation resistance, and excellent electrical properties. This material finds extensive applications in the aerospace, medical devices (such as artificial bone repair for bone defects), and industrial sectors.
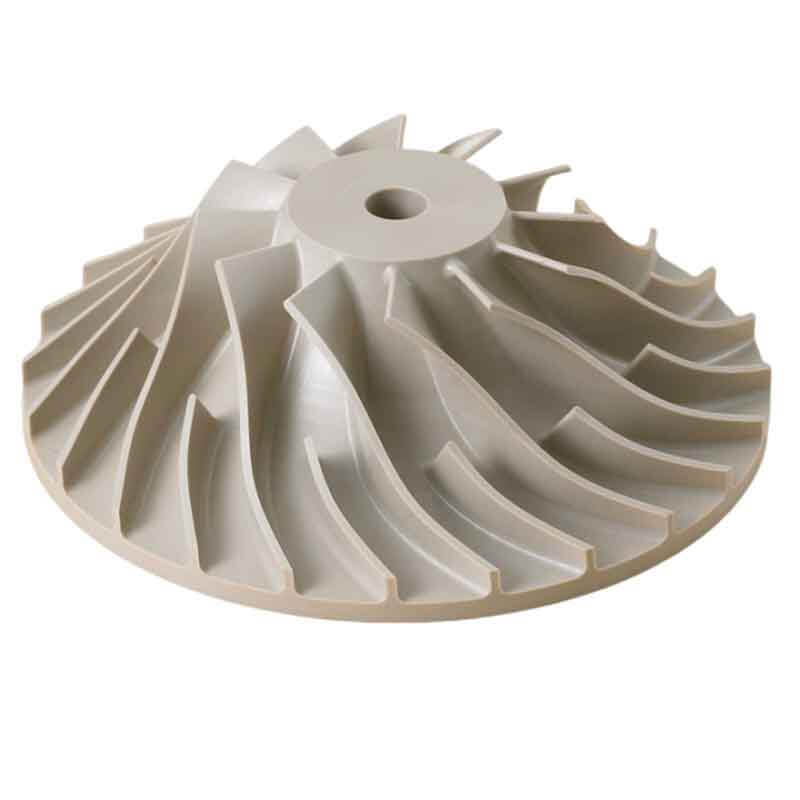
Some Picture of PEEK CNC machining Parts
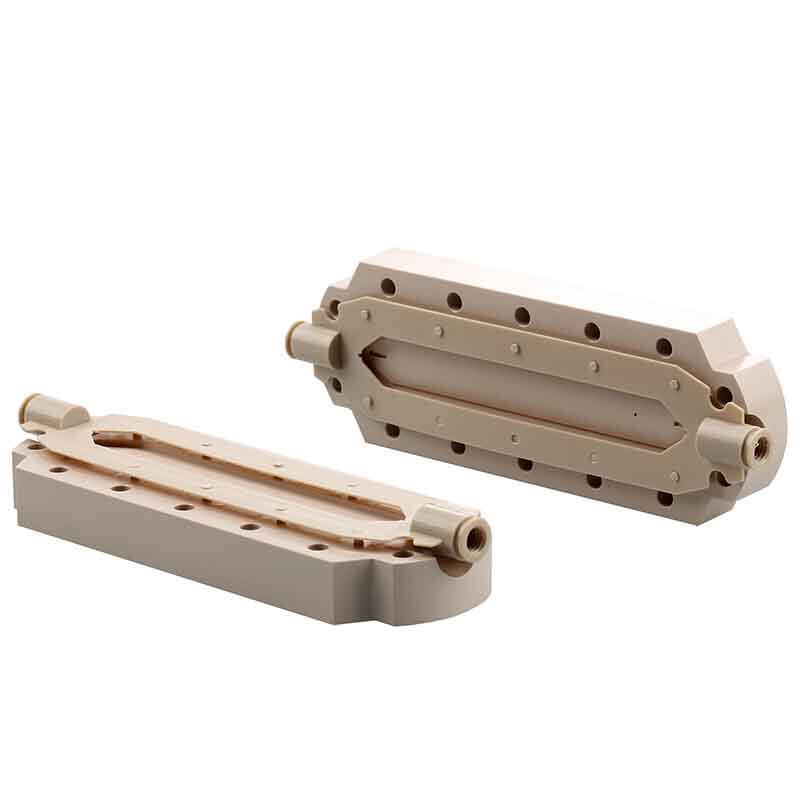
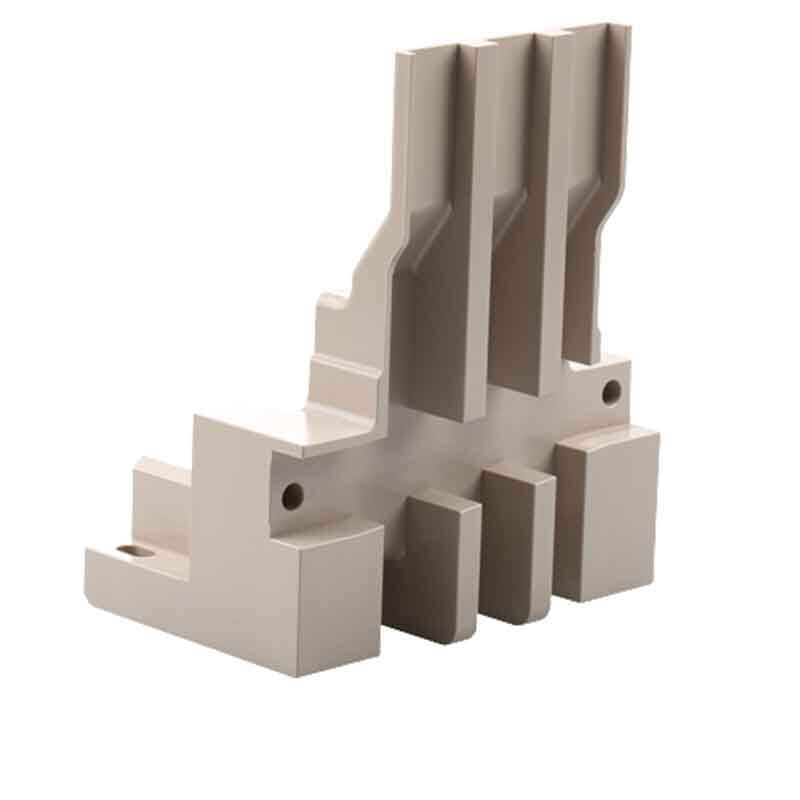

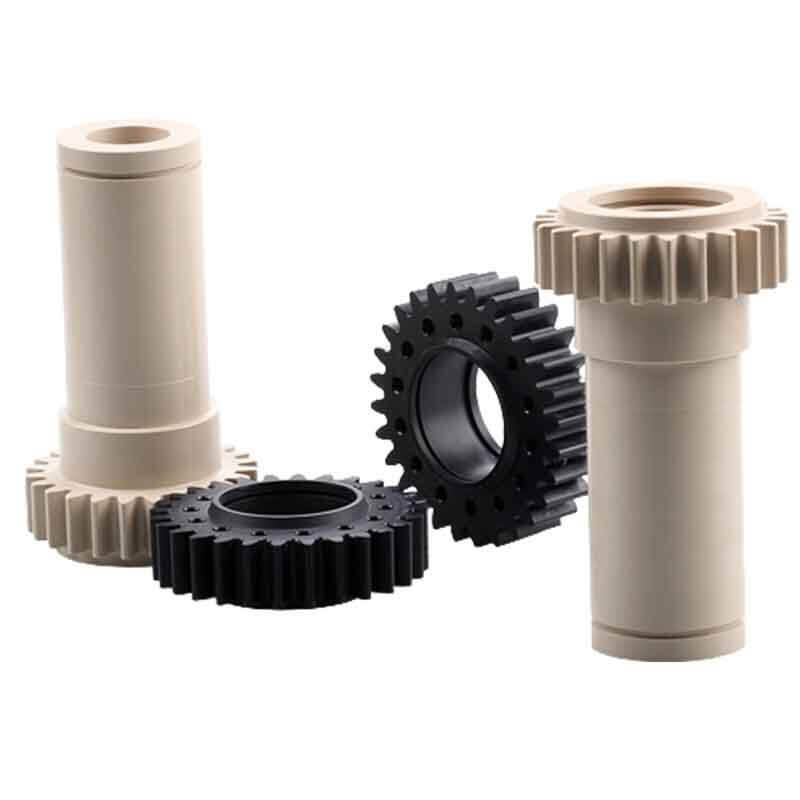
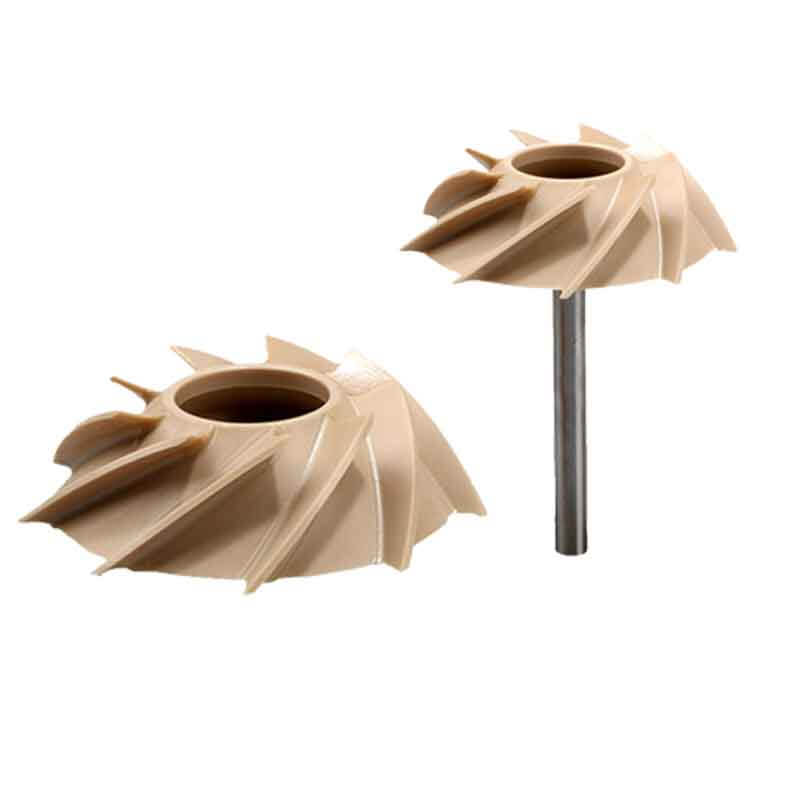

PEEK CNC machining FAQs
PEEK plastic, also known as polyetheretherketone, is a semi-crystalline, high-performance thermoplastic material. PEEK CNC machining involves using computer-controlled lathes or machining centers to perform a series of operations on PEEK, such as turning, milling, drilling, and more. CNC machining doesn’t require molds, thus reducing setup time and costs. CNC plastic machining is particularly suitable for components larger than 600 millimeters. It involves precise tool control to achieve the desired shape and dimensions.
PEEK is preferred for CNC machining due to its excellent mechanical properties, such as high strength, resistance to high temperatures, and chemical resistance. It is also a high-performance polymer with good electrical insulation properties.
PEEK can be challenging to machine because it is a high-temperature polymer, and excessive heat generated during machining can lead to material degradation. Proper tooling, cooling, and cutting parameters are essential to achieve high-quality results.
CNC mills and lathes equipped with the appropriate tooling, such as carbide or PCD (Polycrystalline Diamond) cutters, are commonly used for PEEK machining. High-speed machining centers may be preferred for precision work.
Yes, safety precautions are important when machining PEEK. Proper ventilation and dust extraction systems should be in place to control potentially harmful fumes and dust. Personal protective equipment, like respiratory protection and eye protection, is recommended.
Tolerances in Peek cnc machining can vary depending on the specific equipment and techniques used. However, precision tolerances in the range of ±0.005 mm (0.0002 inches) or better can often be achieved.
Yes, CNC machining allows for the creation of intricate and complex shapes in PEEK, making it a versatile choice for various engineering applications.
Depending on the application, some CNC machined PEEK parts may require post-processing, such as surface finishing or deburring, to meet specific requirements.
Proper disposal of PEEK machining waste and adhering to environmental regulations is important, as PEEK is a polymer and should be handled and disposed of responsibly.
Free Sample
Explore More Plastic Materials
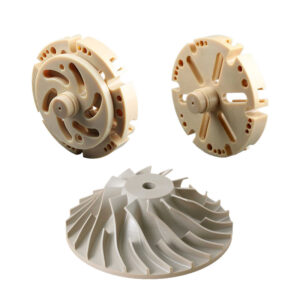
PEEK CNC machining
Polyetheretherketone (PEEK) is a special type of high-performance polymer material known for its high mechanical strength, resistance to high temperatures, impact resistance, flame retardancy, acid and alkali resistance, hydrolysis resistance,

CNC Machining Titanium
Titanium is a lustrous transition metal with a silver color, low density, and high strength. It is an ideal material for typical applications in aerospace, medical, military, chemical processing, marine
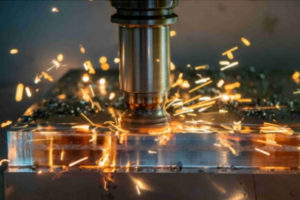
Aluminum CNC Machining
Aluminum alloy is a widely used material in various fields, known for its excellent strength, lightweight properties, good thermal conductivity, corrosion resistance, cost-effectiveness, blade-friendly nature, and ease of processing. It