QPQ Coating
Black Phosphate Coating
black phosphate coating process introduction
The thickness of the phosphating film is about 3-20 microns, and it is gray or dark gray in color. It has good adhesion to the metal substrate and is stable under atmospheric conditions. The corrosion resistance of phosphating and metal oxides in acidic and alkaline environments is not good, and it is important to note that the corrosion resistance of phosphating film is about 2-10 times higher than that of oxide film.
QPQ Coating
What is qpq coating?QPQ Treatment Process Introduction
Hot-dip nitriding of steel parts (QPQ treatment) is a surface hardening method that involves immersing steel parts into a nitriding solution and allowing nitrogen atoms to penetrate the surface of the steel parts at high temperatures. This results in a hard, low-friction, and wear-resistant surface layer, as well as an internal nitrided layer, which increases the strength and wear resistance of the entire steel part. QPQ treatment can also improve the corrosion resistance of steel parts while reducing deformation and discoloration.
The characteristics of the QPQ treatment process are
Excellent Wear Resistance and Fatigue Resistance
QPQ can greatly improve the surface hardness and wear resistance of various black metal parts, as well as reduce friction coefficients. After being treated with QPQ, the wear resistance is more than 16 times higher than conventional quenching and high-frequency quenching, more than 9 times higher than 20 copper carburizing quenching, and more than 2 times higher than hard chrome plating and ion nitriding. Fatigue tests show that QPQ can increase the fatigue strength of medium carbon steel by more than 40%, which is better than the effects of high-temperature nitriding and gas nitriding. QPQ technology is especially suitable for complex-shaped parts, solving the problem of deformation.
Excellent Corrosion Resistance
Under the same test conditions, samples of different materials and process treatments were subjected to continuous spray tests according to the ASTM B117 standard. The salt spray test temperature was 35+2℃, the relative humidity was >95%, and the 5% NaCl solution was sprayed. The test results showed that the corrosion resistance of parts treated with QPQ was 5 times that of 1Cr18Ni9Ti stainless steel, 70 times that of hard chrome plating, and 280 times that of blackening. After being treated with QPQ, some materials can achieve a neutral salt spray test of 100-300 hours.
Small Deformation After Product Treatment
The workpiece hardly deforms after being treated with QPQ, effectively solving the problem of hardening deformation that is difficult to solve with conventional heat treatment methods. For example, after QPQ treatment, the surface hardness of a 2Cr13 stainless steel thin plate with a size of 510*460>1.5mm is greater than HRC60, and the unevenness is less than 0.5mm. Currently, QPQ technology has been applied very successfully to many types of shaft parts and slender rod parts, effectively solving the contradiction of hardening and product deformation that has existed for a long time.
Can Replace Multiple Heat Treatment and Corrosion Protection Processes, Short Time Period
After being treated with QPQ, the workpiece has improved hardness and wear resistance, increased corrosion resistance, and a black, beautiful appearance. It can replace multiple processes such as conventional quenching, tempering, and blackening (chromium plating), shortening the production cycle and reducing production costs. A large amount of production data shows that compared with carburizing quenching, QPQ treatment can save 50% of energy, and compared with hard chrome plating, it can save 30% of costs, with high-cost performance.
The commonly used substrates for QPQ treatment
Various structural steels
Mild steel, Q235, 20, 20Cr, 20CrMnTi, 20CrNiMo, 35CrMo, 42CrMo, 45, 40Cr, 50CrV, 65Mn, and 38CrMoAl.
Various tool sheets of steel
T7~T12, 5CrMnMo, 5CrNiMo, 3Cr2W8V, GCrl5, HI3 (0.35% C, 1.5% Mo, 5% Cr, 1% Si, 1% V), Cr12MoV, and various high-speed sheets of steel.
Various stainless steels
0Cr3~4Crl3, 201, 301, 304, 316, 1Cr18Ni9Ti, 0Crl8Nil2MoTi, 4Cr9Si2, and 5Cr21Mn9Ni4N.
Various cast irons
Gray iron, malleable iron, ductile iron, and wear-resistant alloy cast iron.
Various iron-based powder metallurgy components.
0Cr3~4Crl3, aTypical applications of QPQ treatment include engine valves, crankshafts, cylinder liners, gears, camshafts, bearings, spindles, sliders, steering arms, windshield wiper ball joint shafts, guide rails, hydraulic cylinders, universal joints, connecting pins, various molds, pistons, threaded screws, bolts and nuts, pump bodies, high-speed steel drill bits, gun barrels, various cutting tools, flanges, keys, gaskets, housings, and so on.201, 301, 304, 316, 1Cr18Ni9Ti, 0Crl8Nil2MoTi, 4Cr9Si2, and 5Cr21Mn9Ni4N.
Surface hardness and case depth comparison of conventional materials after QPQ treatment:
Material Type | Representative Steel Grade | Prior Treatment | Nitriding Temperature (℃) | Nitriding Time (h) | (μm)Compound Layer (μm) | Total Diffusion Layer (mm) |
---|---|---|---|---|---|---|
Medium Carbon Steel | 45# | Not treated or normalized | 565 | 1.5 | 17 | 0.3-0.5 |
Medium Carbon Steel | 40Cr | Not treated or normalized | 565 | 1.5 | 15 | 0.2-0.4 |
Cold Work Die Steel | Cr12MnMo | High-temperature quenching | 540 | 2.5 | 10 | 0.15-0.2 |
NitridingSteel | 38CrMoAl | Normalization | 570 | 2 | 12 | 0.25-0.4 |
Casting Die Steel | 3Cr2W8V | Quenching and high-temperature tempering | 570 | 2.5 | 11 | 0.15-0.3 |
Hot Work Die Steel | H13 | Normalization | 565 | 3 | 11 | 0.15-0.3 |
Hot Work Die Steel | 5CrMnMo | Quenching | 570 | 3 | 11 | 0.15-0.3 |
High Speed Steel | W6Mo5Cr4V2 | (Tool) Quenching | 550 | 0.25 | 2 | 0.05-0.1 |
High Speed Steel | W6Mo5Cr4V2 | (Tool) Quenching | 550 | 2.5 | 11 | 0.15-0.3 |
Stainless Steel | 1Cr13;4Cr13 | Quenching | 570 | 2.5 | 10 | 0.1-0.2 |
Stainless Steel | 1 Cr18Ni9Ti | Quenching | 570 | 2.5 | 10 | 0.1-0.2 |
Stainless Steel | OCr18Ni12Mo2Ti | Quenching | 570 | 2.5 | 8 | 0.1-0.2 |
Carbon Structural Steel | 08;10;10F | Annealing | 570 | 2.5 | 15 | 0.3-0.5 |
Carbon Structural Steel | 35;40 | Not treated or normalized | 570 | 2.5 | 15 | 0.3-0.5 |
Bearing Steel | G Cr15 | Quenching and annealing | 565 | 2 | 10 | 0.15-0.3 |
Alloy Structural Steel | 50 Mn | Annealing | 520 | 2 | 12 | 0.2-0.4 |
Alloy Structural Steel | 30CrMo-35CrMo | Quenching and annealing | 565 | 2 | 15 | 0.25-0.4 |
Alloy Structural Steel | 38CrMoAlA- | Quenching and annealing | 570 | 12 | 0.25-0.4 | |
38CrWVAlA | ||||||
Alloy Structural Steel | 38CrAlA- | Quenching and annealing | 570 | 2 | 12 | 0.25-0.4 |
40CrNiMoA | ||||||
gray cast iron | HT200 | Quenching and annealing | 570 | 3 | 15 | 0.15-0.3 |
Ductile Iron | QT20-60 | Not treated | 570 | 3 | 15 | 0.15-0.3 |
Note 1: Prior to undergoing the QPQ salt bath composite process, complex parts need to undergo tempering treatment at a temperature of at least 580℃, followed by slow cooling. To compensate for the slight expansion after the process, precision parts should have a machining allowance of 10±2μm in diameter before treatment.
QPQ process flow
- Load basket
- Remove oil and clean
- Rinse
- Preheat
- Nitriding
- Air-cooling
- Oxidizing
- Hot water cleaning
- Clean water rinsing
- Dehydration and drying
- Rough polishing
- Fine polishing
- Load basket
- Preheat oxidation
- Hot water cleaning
- Clean water rinsing
- Dehydration and drying
- Fine polishing
- Dip in hot rust preventive oil or emulsion rust preventive oil
- Wipe off the oil.
Process and parameter requirements:
Preheating
Nitriding
Pre-cooling
Oxidation
QPQ Treatment Production Equipment Display
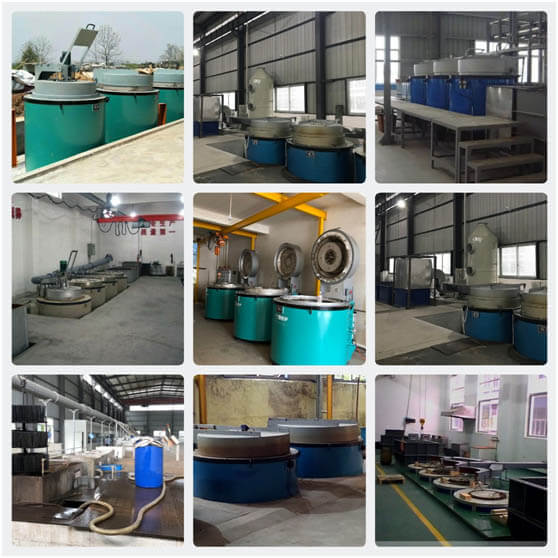
QPQ Treatment Testing Equipment Display
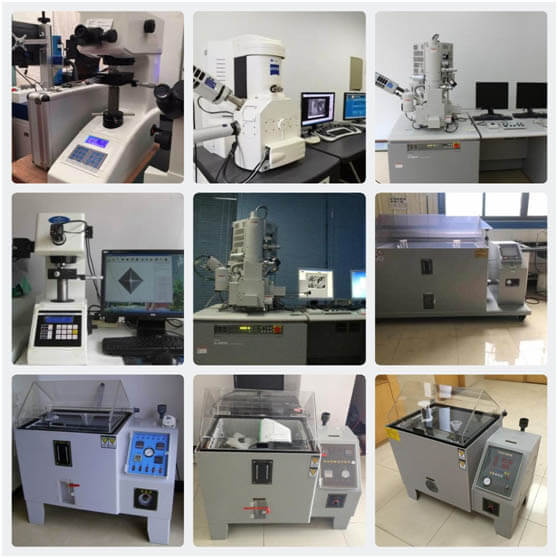
Appearance Inspection
Salt Spray Test
Wear Resistance Test
Case Depth Hardness Test
QPQ Processing Sample Cases
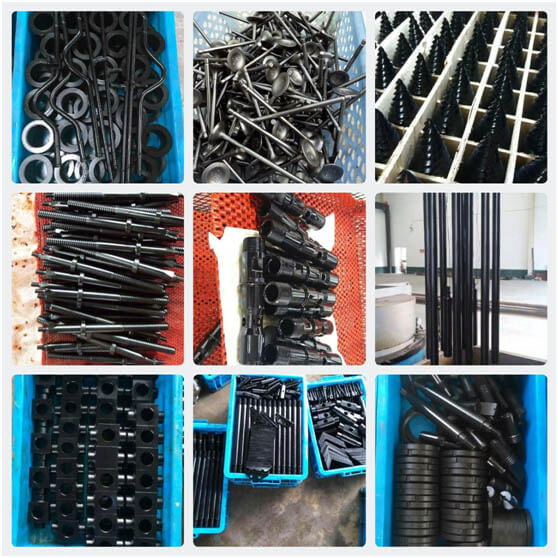
Free Sample
Explore Other Surface Finish

Electrophoretic Coating
Bead Blasting, also known as abrasive blasting or sandblasting,typically involves the use of compressed air to propel abrasive particles from a nozzle and direct them onto the surface to be
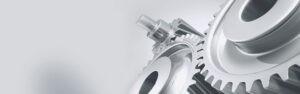
Dacromet Coating
Colorful Dacromet coating processing refers to a special post-treatment process after conventional Dacromet coating processing, which enables the Dacromet coating to exhibit various desired colors such as black, red, blue,
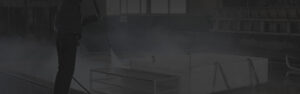
Metal Passivation
Passivation refers to the process of treating the metal with a strong oxidant or electrochemical method to oxidize its surface, making it passive, i.e., transforming the metal surface into a