5 axis CNC impeller machining
5 axis CNC impeller machining
CNC Seven-Stage ImpellerVacuum Cleaner Impeller, Stirrer Impeller manufacturer in China.
MOQ Starts from 10pcs.
As a specialized CNC Stirrer Impeller Vacuum Cleaner Impeller,Seven-Stage Impeller,Small Fan Impeller, Hydrogen Energy Impeller, Marine Impeller, Multi-Stage Centrifugal Pump Impeller, Diesel Engine Centrifugal Pump Impeller, Axial Flow Fan Stainless Steel Impeller Machining manufacturer, Masion provides high-quality custom CNC impeller machining services to customers with outstanding production advantages, advanced technological capabilities, and professional solution offerings.
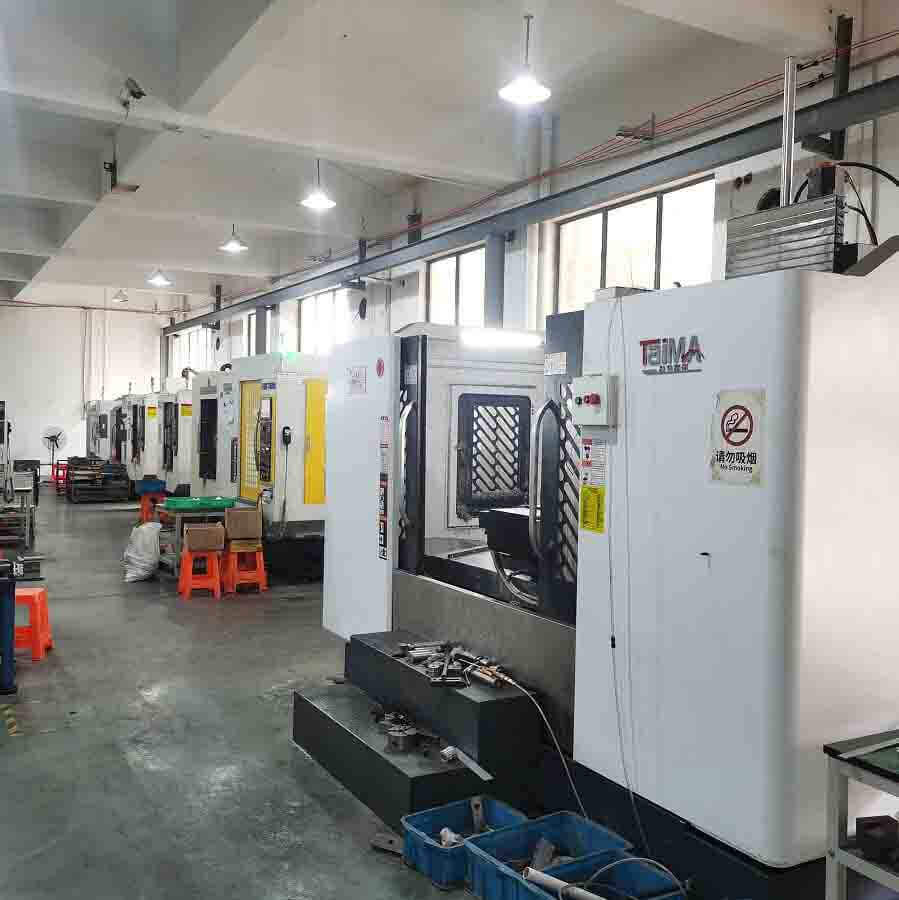
Masion Capability
High Capacity, Proper Price
Free Samples, Low MOQ
Certified Factory, Guaranteed Quality
High precision, thick gold
Our Products
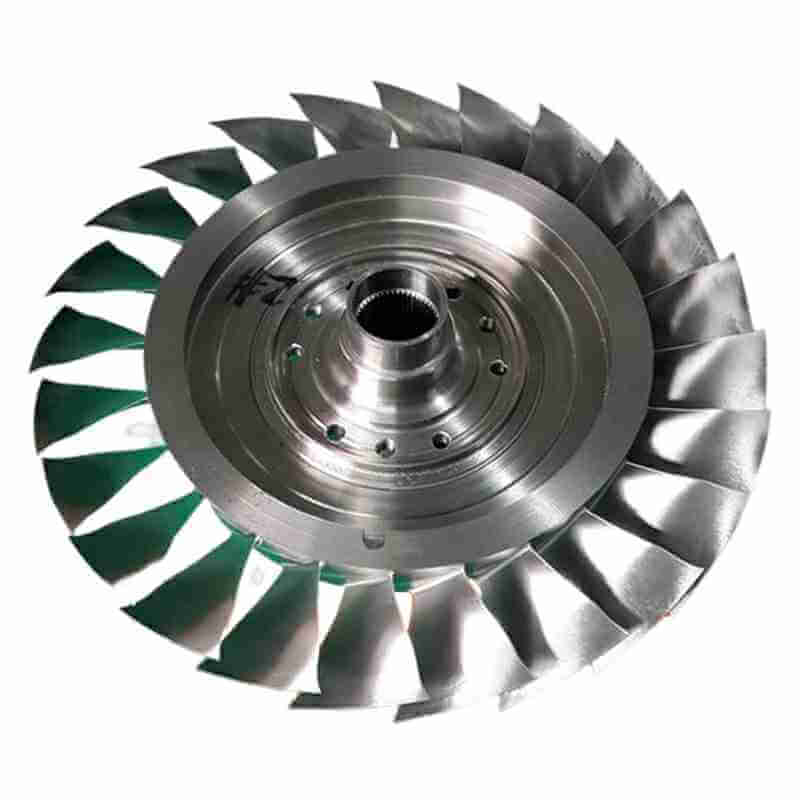
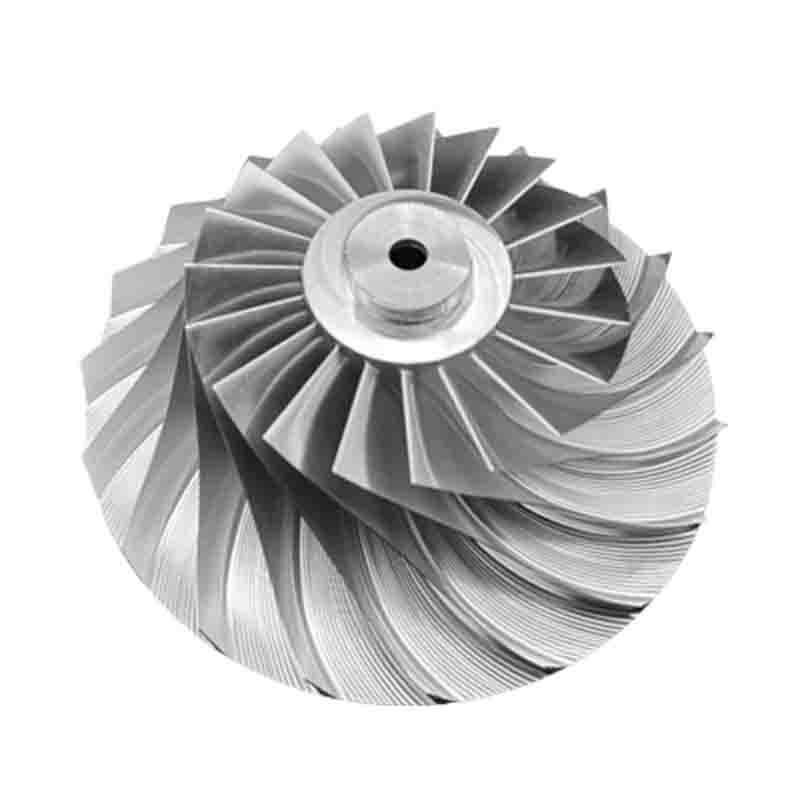
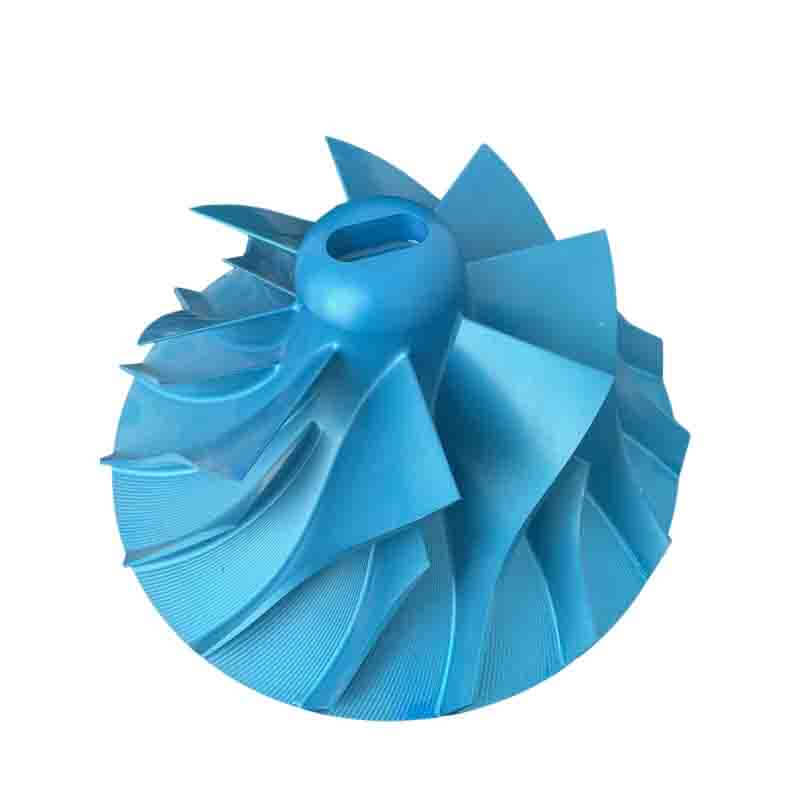
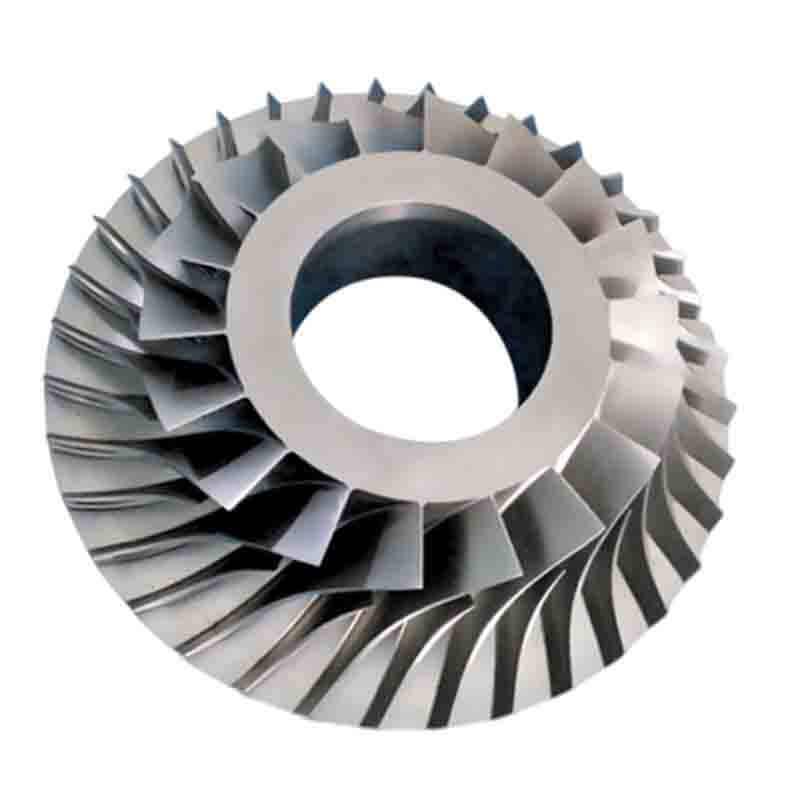
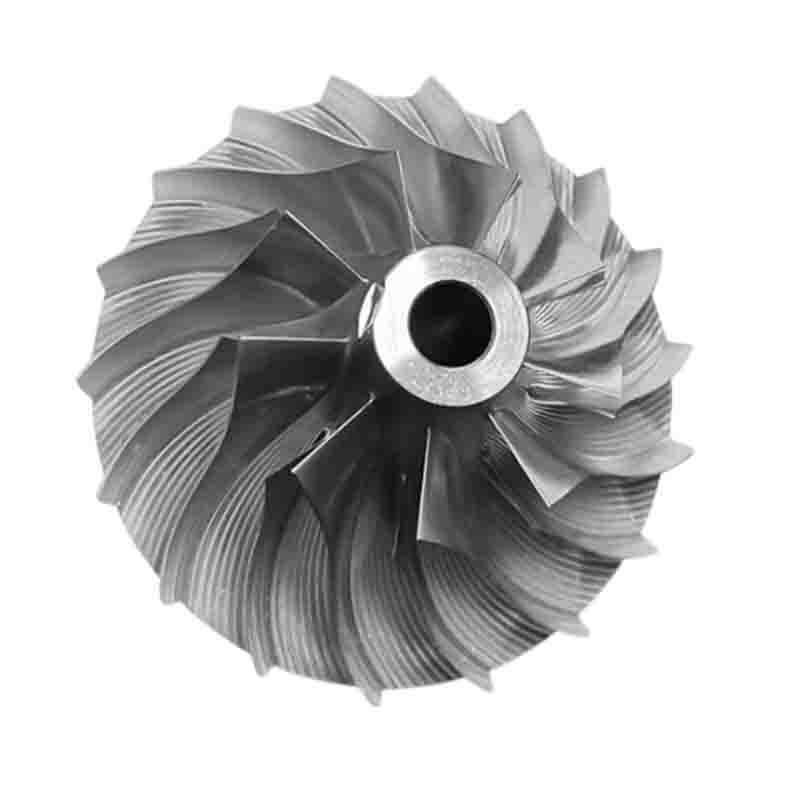

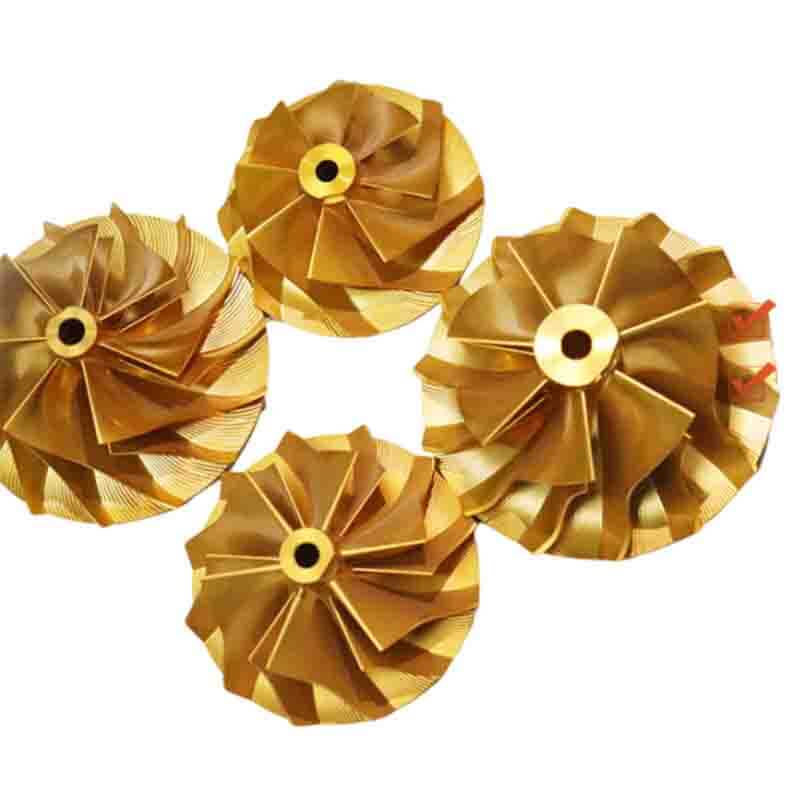
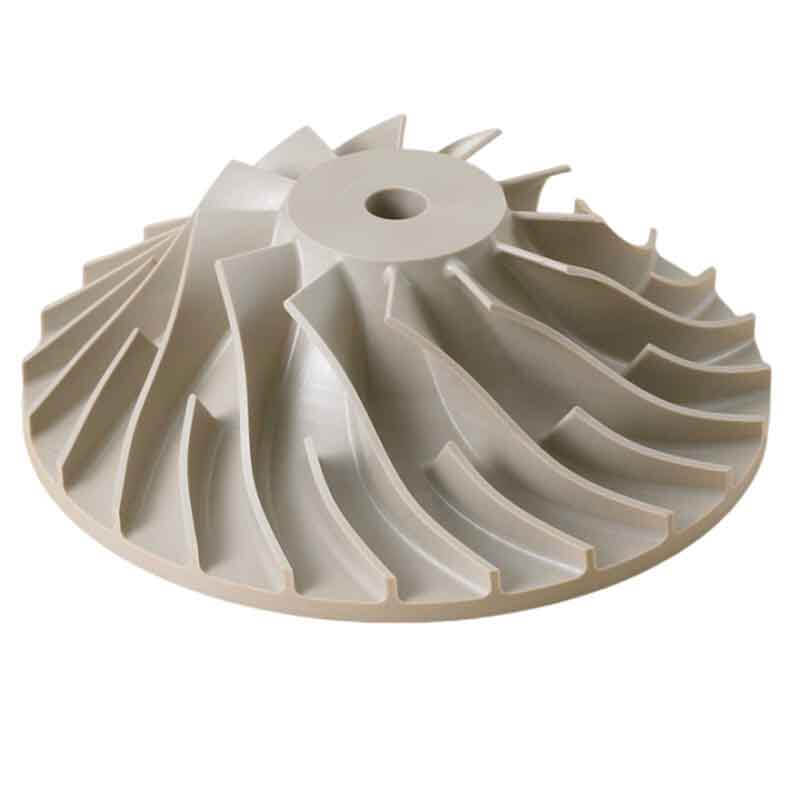
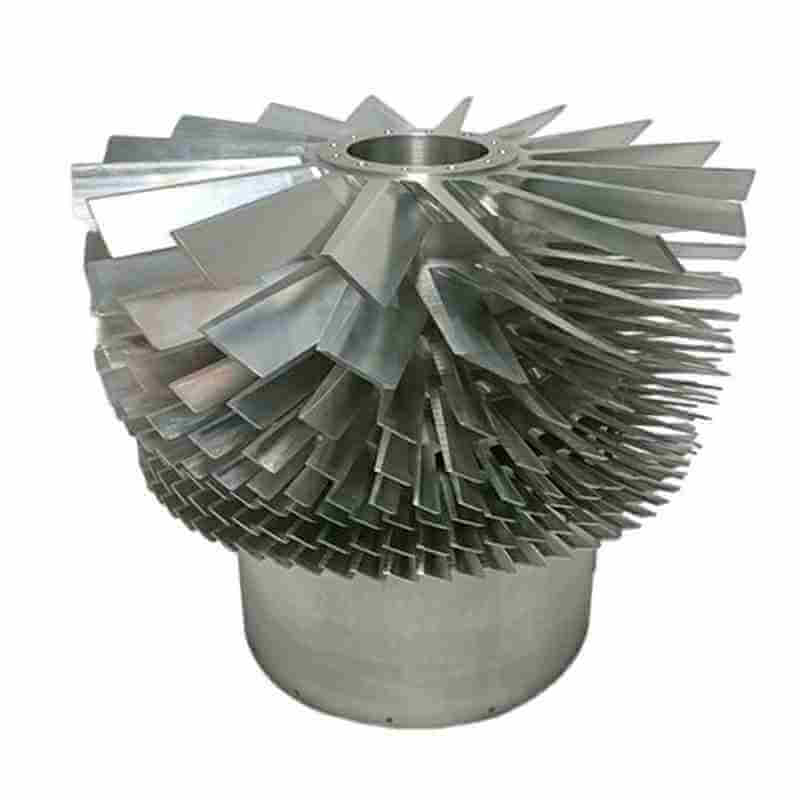
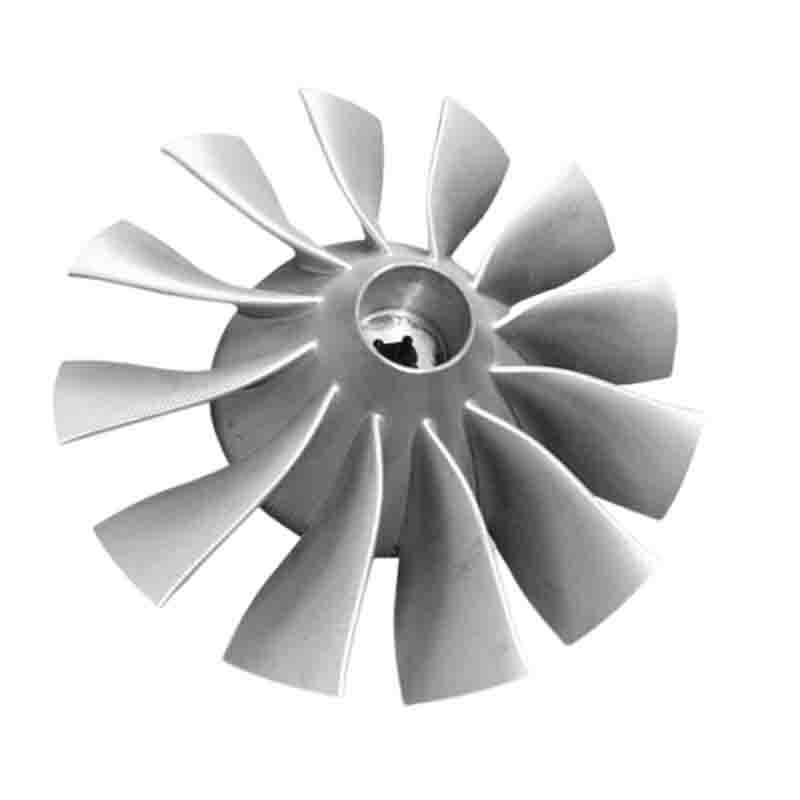
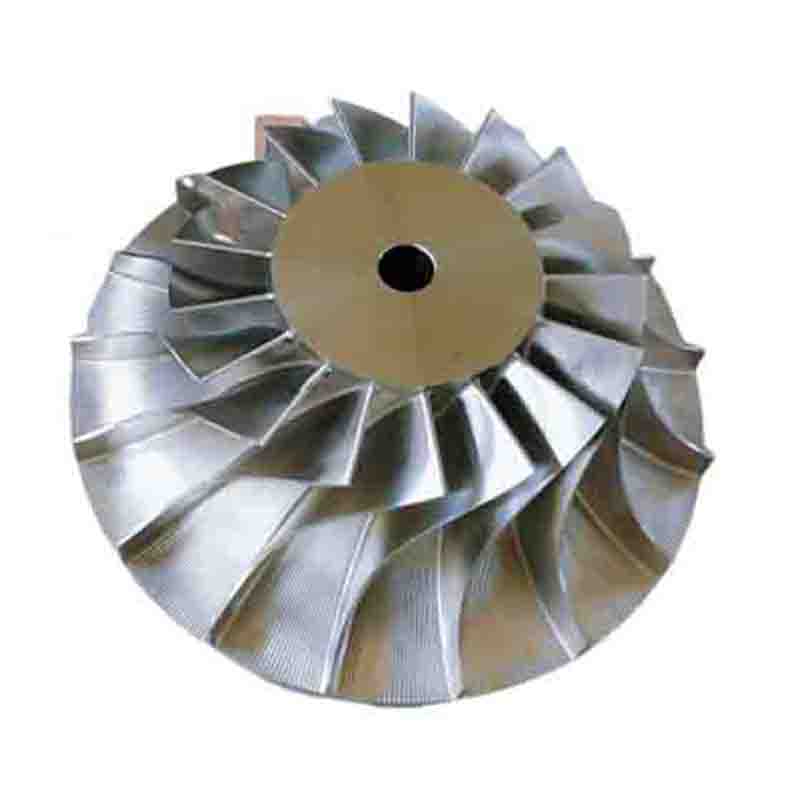
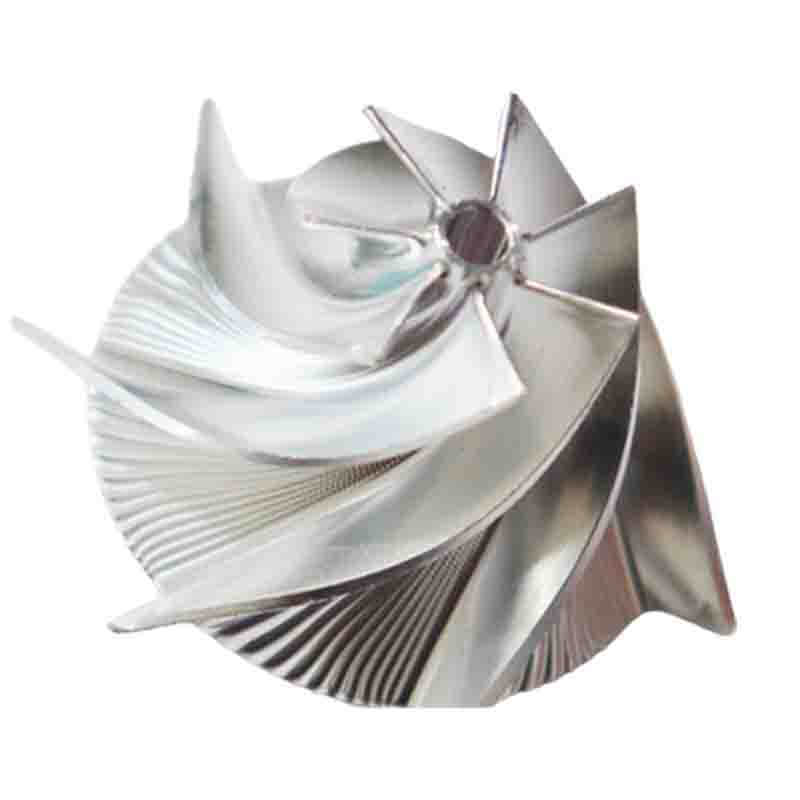
What Sets Us Apart

Strong Experience
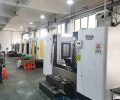
Advanced Machine
30 sets precision CNC 3,4,5 axis machine, with mature and stable manufacturing processes.
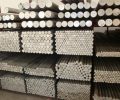
Surprised Price
Stockpiling a large amount of conventional materials and having a mature production process can reduce the overall price by 5%.
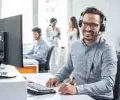
24/7 Engineering Support
Masion offers 24/7 engineering support, design services, cost reduction, quality assurance, and smooth product transitions.
CNC impeller Manufacturing Process
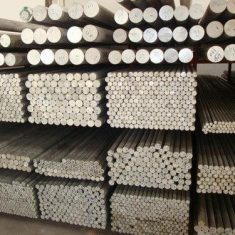
Raw Material
Forging
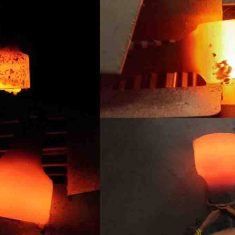
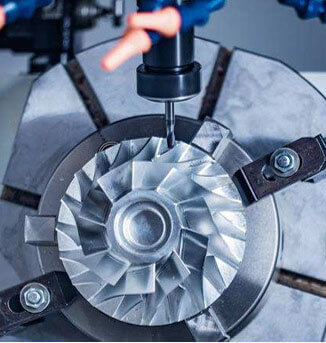
CNC 5 axis Machining
- Milling
- Turning
- Drilling
- Threading
- Cutting
- Counter Sinking
- Boring
- Knurling
- Grooving
- Taper
- Turning
- Tapping
- Reaming
Surface Finish
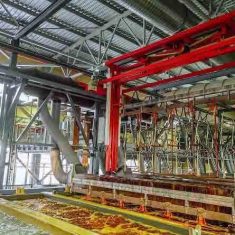
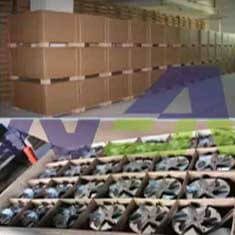
Packing
- For small-sized impellers, we individually package them with bubble wrap before placing them in cardboard boxes.
- As for large-sized impellers, we utilize wooden crate packaging, with additional isolation measures to prevent any damage to the impellers during transportation.
Quality Control (Testing)
- Masion conduct material inspections to ensure their correctness.
- Masion perform initial inspections on the first samples; production proceeds only if the dimensional inspection is passed, with adjustments made if necessary for non-compliance.

- Masion conduct sample inspections on the manufactured products to ensure compliance with the dimensional requirements specified in the drawings.
Application Area
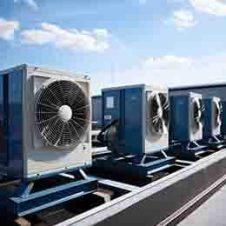
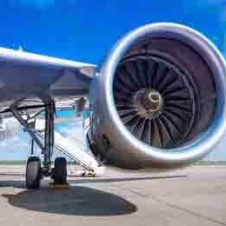

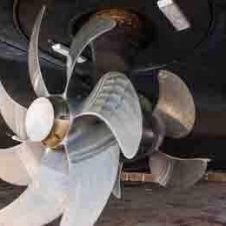
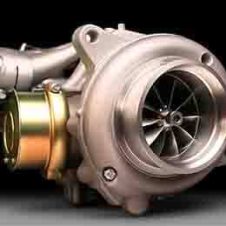
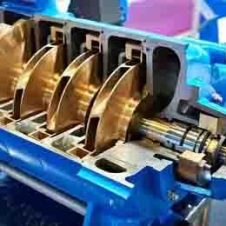
5 axis CNC Impeller machining FAQs
Manufacturing Process:
Forged Impellers: Impellers Forging is a traditional metalworking method involving heating metal to a plastic state and forming the desired shape through hammering or pressing. This method is typically used for producing impellers with high strength and for high-temperature materials.
CNC Machined Impellers: CNC impellers machining employs computer-programmed machine tools to control the movement, cutting, and shaping of the workpiece. In the context of impellers, 5-axis CNC machining provides greater design flexibility for producing complex geometries.
Applicable Materials:
Forged Impellers: Impellers Forging is typically employed with high-strength metals like steel, aluminum alloys, or nickel-based alloys. This makes it an ideal choice for demanding working environments, such as aircraft engines or automotive turbos.
CNC Machined Impellers: CNC impellers machining can accommodate various materials, including metals, plastics, and composite materials like PEEK. This versatility makes CNC suitable for a broader range of applications.
Production Efficiency:
Forged Impellers: Forged impellers are well-suited for mass production, especially for relatively simple geometric shapes. Once appropriate molds are established, large quantities of similar impellers can be produced in a short time.
CNC Machined Impellers: CNC impellers machining offers greater flexibility, as it doesn’t require specialized molds. This is advantageous for small-batch production or situations requiring frequent design changes.
Design Freedom:
Forged Impellers: Forged impellers are typically suitable for relatively simple geometric shapes, as complex shapes may necessitate more intricate molds and processes.
CNC Machined Impellers: 5-axis CNC impellers machining provides greater design freedom, making it easier to manufacture impellers with complex shapes. This is particularly crucial in some high-performance applications.
Cost:
Forged Impellers: Manufacturing forged impellers typically involves higher initial costs, especially in mold production. However, in large-scale production, the cost per impeller may be lower.
CNC Machined Impellers: The initial costs of CNC impellers machining are relatively lower, especially for small-batch production. However, for complex impeller designs, longer machining times may lead to higher production costs.
Quality Control:
Forged Impellers: The forging impellers process is intricate, and defects in molds or uneven equipment pressure can impact quality. Casting defects may include gating inclusions, porosity, uneven surfaces, sand inclusions, cracks, and shrinkage.
CNC Machined Impellers: CNC impellers machining helps avoid many of the issues associated with forging, ensuring impellers meet performance indicators such as density, hardness, and wear resistance.
- Optimization of Machining Parameters:
- axis CNC machining of impellers necessitates the optimization of machining parameters. This includes the selection and adjustment of tooling, cutting speeds, feed rates, cutting depths, etc., ensuring the quality and efficiency of impeller machining.
- Planning of Machining Paths:
Planning the machining paths is crucial for 5-axis CNC impeller machining. This involves the mapping of tool entry and exit points, cutting directions, cutting trajectories, and other factors to ensure precision and surface quality in the machining process.
- Design and Manufacturing of Tools:
Specialized tools are required for 5-axis CNC impeller machining, demanding characteristics such as high strength, hardness, and wear resistance. Factors like tool shape and size also need to be considered in the design and manufacturing of these tools.
- Monitoring and Control of Machining Process:
Real-time monitoring and control of the machining process are essential for 5-axis CNC impeller machining. This includes tracking tool wear, ensuring machining quality, monitoring efficiency, and other aspects to guarantee the overall quality and efficiency of impeller machining.
- Surface Treatment After CNC Machining of Impellers:
Following 5-axis CNC machining, impellers require additional surface treatments such as polishing, sandblasting, electroplating, etc. These treatments aim to enhance the surface quality and corrosion resistance of the impellers.
Establish Detailed Impeller Process Flow and Standards:
Develop clear impeller process flows and quality standards to ensure adherence to specified procedures throughout all production stages, encompassing material procurement, machining, heat treatment, surface treatment, and more.
Enforce Stringent Material Control:
Conduct thorough inspections and validation of impeller raw materials, ensuring compliance with design requirements and standards. Material quality is crucial for the final product’s performance.
Utilize Advanced Machining Equipment:
Opt for high-performance CNC machine tools and cutting tools to guarantee precise machining. 5-axis CNC machining offers increased flexibility and the ability to handle more complex geometric shapes.
Implement Appropriate Tool Management:
Regularly inspect and replace tools to maintain sharpness and proper working conditions. Proper tooling significantly influences machining quality.
Regularly Calibrate and Maintain Equipment:
Periodically calibrate and maintain machining equipment to ensure working accuracy and stability, preventing quality variations due to equipment issues.
Implement Well-Defined Cutting Parameters:
Optimize cutting parameters, including cutting speed, feed rate, and cutting depth. This helps avoid excessive wear and enhances surface quality.
Adopt High-Precision Measurement Tools:
Use high-precision measurement tools such as coordinate measuring machines to perform detailed dimensional measurements on impellers, ensuring compliance with design specifications.
Implement Process Controls:
Real-time monitoring during the production process, detecting and correcting any changes that could lead to quality issues. This may involve monitoring temperature, pressure, and other critical process parameters.
Establish a Traceability System:
Set up a traceability system to track the production process of each impeller, including material sources, processing parameters, and inspection records.
Train and Certify Personnel:
Provide training for operators to ensure their understanding of correct processes and operating procedures. Where applicable, ensure employees obtain relevant quality certifications.
Continuous Improvement:
Regularly assess the effectiveness of quality control procedures and make improvements. Continuously optimize the machining process based on feedback to adapt to changing demands and technological advancements.
By integrating these control measures, you can ensure effective management and control of quality throughout the impeller machining process.
In five-axis CNC impeller machining, if blade breakage occurs, it needs to be addressed to ensure machining precision and overall effectiveness. Here are some possible causes and corresponding solutions:
Thin Blade Thickness or Selection of Too Hard and Brittle Grade during Rough Machining:
Issue: The blade may break due to inadequate thickness or the use of excessively hard and brittle grades during rough machining.
Solution: Increase the blade thickness or use a tougher and more resilient grade. Consider adopting a more suitable grade with higher bending strength.
Incorrect Welding Process for the Blade:
Issue: Incorrect welding processes may lead to excessive welding stress or welding cracks.
Solution: Avoid using a three-sided enclosed blade slot structure. Preferably, use a mechanically clamped structure to reduce welding stress and minimize the risk of cracks.
Improper Blade Grinding Methods:
Issue: Inappropriate blade grinding methods can result in grinding-induced stress and cracks.
Solution: Choose a relatively soft grinding wheel and regularly maintain its sharpness. In five-axis CNC machining, pay attention to the quality of grinding and strictly control the oscillation of milling cutter teeth.
Excessive Tool Wear:
Issue: Overly worn tools can directly impact overall process performance.
Solution: Replace the tool or cutting edge promptly to prevent a decline in machining quality. Regularly monitor tool wear and change tools as needed.
It’s essential to address these issues promptly to maintain the desired machining precision and ensure the effectiveness of the overall process.
Selecting the material for an impeller is a crucial engineering decision as the material’s performance directly impacts the impeller’s lifespan, durability, and overall performance. Here are some general considerations to make informed decisions when choosing impeller materials:
Operating Environment and Application:
Consider the specific operating environment and application for which the impeller will be used. Factors such as high temperature, high speed, corrosive environments, or high-pressure applications will influence material selection.
Mechanical Properties:
Ensure that the chosen material possesses adequate mechanical properties, including strength, toughness, hardness, and fatigue resistance. These properties directly affect the impeller’s load-bearing capacity and durability.
Wear Resistance:
For applications like pumps or turbines, wear resistance is crucial. Selecting a material with good wear resistance can extend the impeller’s lifespan.
Corrosion Resistance:
If the impeller will operate in a corrosive environment, choosing a material that can resist corrosion is essential. This may involve selecting corrosion-resistant alloys or special coatings.
Thermal Conductivity:
Some applications require materials with excellent thermal conductivity to better disperse or conduct heat, particularly in high-temperature applications.
Density and Weight:
Density and weight are critical considerations for certain applications. Lightweight materials can reduce inertia forces, aiding in lowering the impeller’s load and energy consumption.
Temperature Stability:
Consider the temperature range the impeller will experience during operation. The material should maintain stable performance within this range without significant deformation or damage.
Magnetic Properties:
In certain applications such as motors or generators, avoiding the use of magnetic materials may be crucial to prevent interference with equipment.
Cost:
Material cost is also an important consideration. Balancing performance requirements with an acceptable cost range is necessary.
Machinability:
The machinability of the material is a crucial factor. Some materials may be easier to machine into complex geometric shapes, which could be a key consideration in impeller design.
Making thoughtful decisions based on these considerations will contribute to selecting the most suitable material for the impeller, ensuring optimal performance and longevity.
When selecting materials for CNC machining of impellers, several factors need to be considered, including the working environment, mechanical properties, thermal conductivity, wear resistance, machinability, and cost. Here are some common material options and their characteristics:
Stainless Steel:
Characteristics: Good corrosion resistance, stable mechanical performance, suitable for a wide temperature range.
Applications: General industrial applications, especially where corrosion resistance is essential.
Aluminum Alloy:
Characteristics: Lightweight, good thermal conductivity, suitable for high-speed applications but relatively soft.
Applications: Low-load, high-speed, or weight-sensitive applications.
Nickel-Based Alloys:
Characteristics: Excellent high-temperature performance, corrosion resistance, and strength, suitable for high-temperature and high-load environments.Nickel-based alloy refers to a class of alloys with high strength and certain antioxidant corrosion resistance at 650 ~ 1000℃
Applications: Aerospace, gas turbine, and other high-temperature, high-performance applications.
Titanium Alloy:
Characteristics: Excellent strength, corrosion resistance, and lightweight.
Applications: Aerospace, medical devices, and applications requiring both lightweight and corrosion resistance.
Plastics and Composite Materials:
Characteristics: Lightweight, corrosion-resistant, good mechanical properties for specific applications.
Applications: Low-load, low-speed applications, or situations where overall weight reduction is crucial.
High-Temperature Alloys:
Characteristics: Outstanding high-temperature strength and oxidation resistance.
Applications: Suitable for applications requiring operation in extremely high-temperature environments, such as aerospace and energy fields.
Ceramics:
Characteristics: Extremely high hardness and wear resistance but brittle.
Applications: Suitable for specialized applications with high requirements for hardness and wear resistance, such as high-speed cutting.
It’s important to carefully consider the specific requirements of the impeller application and weigh factors such as material properties, environmental conditions, and cost when making a selection.
Free Sample
Explore Other Products
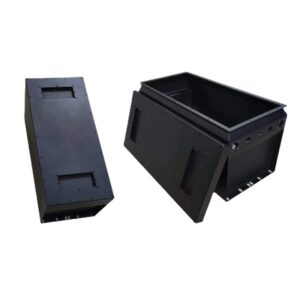
Sheet Metal Fabrication
New Energy Battery Casing and other differentSheet Metal Fabrication parts such as Housing, Case,Enclosure, etc.
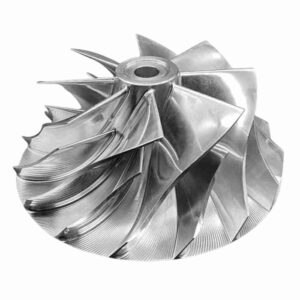
Aluminum Boat Impeller
Five-axis simultaneous complex parts machining, aluminum boat impeller, watercraft impeller, compressor impeller, turbocharger impeller,and another different 5-axis CNC parts etc.

Automatic Lathe
Test Pin and other Automatic Lathing Machining Parts such as screws,copper pillar, knob, etc.