CNC Turning
Something you could know about the CNC turning and CNC turning parts.
How to Describe CNC Turning? What is Meaning?
CNC turning is a production technique that uses an lathe to cutting rotary workpieces. It involves securing a rod material in a fixture and rotating it, while using a cutting tool to move back and forth, left and right to cut the rod material, as a result, removing material to create the desired shape as per the design.
CNC turning will use CAM programming to generate G-code to control the forward, left, and right of the tool on the tool holder for cutting, which is also called subtractive manufacturing. This is because it is necessary to remove material in order to achieve the desired design of the part.
The cutting tool, typically a single-point cutting tool, is guided by a computer program that determines the movement of the tool and the speed at which it rotates. The computer program takes into account a variety of factors, such as the material being machined, the size and shape of the final product, and the desired level of precision, to generate a cutting path for the tool. The tool then moves along this path, removing material as it rotates, until the final product is formed.
CNC turning is widely used, and we can often see it in automotive parts, agricultural parts, communication parts, electronic equipment parts, medical equipment parts, and aerospace components. These parts are highly precise and of high quality, and they are closely related to our daily lives. Therefore, it is an indispensable production technology.
The process provides a high degree of accuracy, repeatability, and consistency, making it well-suited for large-scale production runs. Additionally, the use of computer control allows for the automation of many aspects of the machining process, making it more efficient and cost-effective than manual machining methods.
CNC turning involves the use of numerical control (CNC) lathe to produce rotary components such as golf tees, rope handles, Stethoscope Chestpiece, Tattoo Eyebrow Housing, and all cylindrical housing. The process involves rotating the workpiece and using a turning tool to shape it into the desired form. CNC lathes have diverse production capabilities and can be equipped with different cutting tools to perform machining operations such as turning, drilling, tapping, reaming, knurling, grooving, and cutting on workpieces. CNC turning can improve production efficiency, reduce machining time, and enhance product accuracy, enabling mass production of various equipment components, making it a highly favored machining method.
The use of computer control in CNC turning allows for the automation of many aspects of the machining process, making it more efficient and cost-effective compared to traditional manual methods.
Masion is a company that excels in CNC turning, offering efficient and precise machining of turning components. The company’s CNC turning capabilities allow it to produce parts with high accuracy and surface roughness.
Masion’s expertise in CNC turning makes it a reliable partner for various industries that require high-quality turned parts. With the use of advanced computer control systems and cutting-edge machinery, the company can achieve precise and consistent results, meeting even the most demanding requirements of its customers.
Masion’s commitment to providing top-notch CNC turning services is reflected in its use of the latest technology and its investment in the training and development of its employees. The company’s expertise in CNC turning, combined with its focus on quality and customer satisfaction, sets it apart in the industry.
In conclusion, if you’re looking for a company that can provide high-precision and efficient CNC turning services, look no further than Maison. With its cutting-edge technology, skilled workforce, and commitment to quality, Maison is well-equipped to meet all your turning parts needs.
What are the Different Types of CNC Turning?
Lathe turning: This is the most traditional type of CNC turning and involves the use of a lathe to create rotational parts by removing material from a workpiece.
Swiss turning, named for its use in machining Swiss watches, is known for its high efficiency, high precision, and suitability for machining large quantities of small-volume parts. It is primarily used for machining high-precision small parts. SWISS lathe has 3, 4, and 5-axis functionality and can carry out the turning and milling at the same time. CNC turning and milling:The turning and milling machine combines all the functions and features of a CNC lathe and a CNC milling machine. It can perform multiple machining operations such as turning, milling, drilling, and boring, while also reducing the number of tool changes and fixture changes, completing the machining of complex parts at a time, and ensuring high precision and good surface finish.
Chucking turning: Chucking turning is used for larger parts and involves clamping the workpiece in a chuck and using a tool to remove material. Bar turning: Bar turning is a type of CNC turning that involves feeding a bar stock into a turning machine, where it is machined into a finished part. The lathe: also referred to as the Microcomputer lathe, is a high-tech machine that combines electrical and hydraulic systems. It is mainly used for the lathing and shaping of motor shafts, hexagons, screwdriver toolbars, crosses, plum shapes, and other hardware products.
Depending on the size of the product, design shape, cost analysis, and precision requirements, different machining processes need to be selected in order to manufacture the parts that meet cost, precision, and quality requirements.
What Components are Ideal for CNC Turning Processes?
Parts with good surface roughness requirements
Parts with complex surface shapes
Parts with special threads
High-precision rotary parts: CNC lathes are known for their rigidity, precision, and accuracy. They can be adjusted manually or automatically, making them ideal for machining high-precision parts.
Good surface roughness rotary parts: CNC lathes have a constant linear speed cutting function, which produces parts with small and uniform surface roughness. Different surface roughness requirements can also be met by adjusting the feed speed.
Complex surface shape rotary parts: CNC lathes have the capability of linear and circular interpolation, enabling them to process any rotary part with complex surface shapes.
Special threads rotary parts: Unlike conventional lathes that can only turn limited threads, CNC lathes can turn any type of thread, including equal lead straight, conical, and increasing/decreasing lead threads. When equipped with precision thread cutting functions, NC lathes can produce threads with high precision and low surface roughness.
Hardened workpieces: In large-scale die machining, some parts can undergo large deformation after the heat finish, making it challenging to grind. If it is a hardened workpiece, it can be machined using hard alloy tools, ceramic tools, cubic boron nitride tools, and other CNC turning methods. For high-hardness quenched and tempered hardened steel, hard alloy tools are unable to machine the workpiece as they either experience severe wear or are unable to machine it at all. Ceramic tools are suitable for precision machining processes, small feed machining of workpieces, and avoiding intermittent cutting. However, for large workpieces with a precision machining allowance of more than 2mm and significant deformation after quenching, ceramic tools are not recommended. Cubic boron nitride tools have higher hardness and better wear resistance compared to hard alloy and ceramic tools and are currently the most suitable tools for machining quenched and tempered hardened steel components.
What are the Different Types of CNC Turning Processes?
Cylindrical Turning: This involves clamping the workpiece in a chuck for rotational motion, while the turning tool is mounted on the tool holder for longitudinal feeding. This is the most common turning process and mode of operation.
Facing: Facing refers to the process of turning the end face of a workpiece with a 90° offset tool, a 75° external turning tool, or a 45° elbow turning tool. The workpiece rotates as the main movement, while the turning tool moves transversely, perpendicular to the axis of the workpiece.
Hole Turning: Hole turning involves turning a blank hole (such as a casting or forging hole) or a drilled hole into a turning hole using an inner hole turning tool on a lathe.
Knurling: Knurling machining involves using an extrusion method to deform the surface of a part, creating a raised pattern.
Grooving: Grooving refers to creating a groove on the surface of a workpiece. There are different types of grooves, including outer grooves, inner grooves, and 45° end grooves.
Cutting or Parting: Cutting or Parting refers to the process of cutting a rod or workpiece into two or more sections along a specified path. This is typically done using a forward-cutting method, where the lathe spindle rotates forward, and the turning tool moves transversely for turning.
Taper Turning: Taper turning is a machining process that forms a conical surface by the tool following a path along the tool tip trajectory and the axis of the workpiece, forming an angle between them. This method of machining can be used to create a conical shape on the surface or inside of a workpiece. Taper turning is generally divided into two types: internal taper turning and external taper turning, which refer to the conical shape formed on the inner and outer surfaces of the workpiece, respectively. There are four main methods of taper turning: wide blade tool turning, offset sliding plate method, offset tail seat method, and copying (using a mold).
Form Turning Surface: Form turning surface refers to the surface of a workpiece turned by a forming tool, forming method, or copying method. The formed surface processed on a lathe is a plain line curve of the rotary surface. Common forming surfaces include spherical and olive-shaped surfaces.
Turning Threads: Refers to a machining method where specialized thread-cutting tools are used to cut continuous protrusions and grooves with the same profile and specified tooth shape along a helix on a cylindrical or conical surface, forming a thread tooth shape. Typically, turning threads can be divided into two types: internal threads and external threads.The appropriate gear fit is selected based on the tooth pitch, and the cutting amount is adjusted based on the size of the thread. Threads can be either cylindrical or conical and come in different types, including triangular, trapezoidal, square, internal, and external.
Tapping: Tapping refers to the process of machining threads inside a workpiece. Specifically, the workpiece rotates, and the cutting tool moves along the internal axis of the workpiece by one pitch. The movement of the tool creates the thread machining process on the surface of the workpiece’s threads.
Reaming: On the lathe, a specialized cutting tool (reamer) is used to slightly remove a thin layer of material from a previously drilled or bored hole, usually with a thickness of only a few microns. This is a method used for the precision machining of cylindrical or tapered holes, which can improve the accuracy of the product and reduce surface roughness. Due to the large number of cutting edges on the reamer, the cutting allowance is small, the cutting resistance is low, and it has good guidance and rigidity. Therefore, the dimensional accuracy of the machined hole can reach IT9IT7 and the surface roughness can reach Ra3.20.8μm. The machining range for precision cylindrical and conical holes is generally from 3 to 100 mm.
Drilling: Drilling is a machining method that uses a fixed twist drill on a lathe. By rotating the workpiece and gradually moving the twist drill closer to the workpiece to perform the cutting action, the hole formed is called a drilled hole. Lathe drilling involves rotating the workpiece and fixing the twist drill, making it suitable for drilling single holes with rotary bodies.
Deep Hole Drilling: Generally, a cylindrical hole with a depth exceeding five times its diameter is called a deep hole, with L/D > 5, which is considered a general deep hole. It is often machined using extended twist drills on a drilling machine or lathe. A hole with L/D = 20-30 is considered a medium-deep hole, and is often machined on a lathe.
Boring: This process involves enlarging an existing hole to a specific size or shape.
Counterboring: This process involves enlarging the top portion of a hole to a larger diameter, creating a flat bottom surface.
Countersinking: This process involves creating a conical recess in the surface of a workpiece to accommodate a screw head.
What are Some Ways to Lower the Cost of CNC-turned Parts?
1. Material – As we all know, in CNC turning, the material is the largest component of the entire workpiece. To reduce the cost of the product, we can consider using forging, casting, or forging processes through the design of product drawings. This is because, for some structurally complex products, direct CNC turning will waste a lot of material. In addition, if we use round tubes for CNC turning, we should choose existing round tubes with diameters and outer diameters close to the product’s inner and outer diameters to ensure the minimum waste of materials and thus reduce the cost of material usage.
2. Quantity – The number of units produced in CNC machine machining affects the cost per unit. Generally, the more units made, the lower the cost per unit.
3. Design – The geometric shape, specifications, and parameters of the parts determine the type and number of required machining machines, which then affects the cost of CNC machining.
4. Machining time – Machining time is a crucial factor and has a direct impact on the cost. Usually, as we know, cost accounting is calculated based on the equipment processing time, so the shorter the processing time, the lower the cost.
1) Selecting the right and best material
Extra machining steps, safety measures, or other resources will increase production costs. Aluminum is generally cheaper than other metals such as brass, copper, stainless steel, and bronze. Brass C360 and aluminum alloy are easy to process, POM is the easiest plastic to process, and ABS is a cost-effective material with good processability.
Choosing profile materials or hot forging, and casting materials can also reduce the cost of CNC machining as many shapes can be formed through molding, but it also involves the cost of mold opening.
For aluminum cutting CNC machining, choose materials with the closest outer diameter to minimize material waste. The smoothness requirement will determine the material for the outer diameter.
2) Reasonable allocation of machining amount
3) Consider all aspects of the design process
Unless necessary, do not specify tolerances as they increase costs. Standard tolerances (±0.125mm or higher) are sufficient for most non-critical features.
Avoid complicated geometric figures as they are more difficult to process, requiring multiple tools, procedures, programming, settings, and longer time. Consider splitting a complex part into multiple independent assemblies that can be connected after machining.
Avoid small parts as they lead to poor surface cleanliness on CNC-cut parts and result in slower machining and rough surfaces. The minimum radius should be 0.4mm or higher.
Minimize surface finish as it adds additional machining, especially for multiple finishes of the same parts. Carefully evaluate the design to reduce multiple surface finishes and avoid unnecessary finishes.
Avoid deep cavities: as they require a long machining time, result in material waste, and are difficult to clean up. Use a shallow cavity design to reduce machining time and waste.
Select the Inner Corner of the Rounded Corner: During CNC machining, a rounded corner can be created with the tool. The larger the radius, the less material needs to be removed, thus saving time for changing tools and machining. It is recommended to use a length-to-diameter ratio of 3:1 or a smaller inner angle radius.
Pay Attention to Drill Size: It is important to be careful when selecting the size of the drill.
Simple Machine Settings and Functions: Keeping machine settings and functions simply can also contribute to reducing machining costs.
4) High-Quality CNC Turning Tools:
5) Equipment Costs:
6) Outsourcing:
7) Workholding:

Free Sample
Explore Other Guide and resource

CNC Turning
Dive into the world of CNC turning with our comprehensive guide, exploring the meaning, types, and processes involved. Uncover the versatility of CNC lathes and their applications in automotive, agriculture,
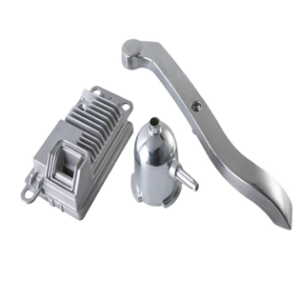
Passivation of Aluminum and Aluminum Alloys
For aluminum and aluminum alloy workpieces, whether obtained through chemical oxidation or anodization, the resulting oxide film is porous, prone to contamination, and has poor corrosion resistance. Even after coloration
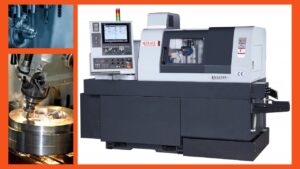
Swiss Machining 101: Purpose, Process, Applications and More
Wondering about Swiss Machining? Unveil every single fact on concept, process, tools, materials, applications, and more. Let’s dive in!