5 Axis CNC Machining Services
5 Axis CNC Machining Services
Precision 5 axis cnc machining manufacturer with 30 sets 3.4.5 Axis CNC Machining Center.
5 axis CNC machining service

for turbo molecular pumps, high-pressure water pump impeller machining, air compressor impeller machining, blower impeller machining, vortex disk parts machining, and hairdryer impeller machining. We specialize in providing customized 5-axis complex products for various industries such as medical, aerospace, automotive, electronics, telecommunications, refrigeration, optics, and home appliances. With advanced 5-axis machining equipment and a team of skilled designers, engineers, and machinists, we can effectively address any technical questions you may have regarding complex products.
What We Do

5 axis CNC Milling materials

Surface treatment capacity
Spray paint, Paint, Spray, Sandblasting, Shot blasting, Anodizing, Hard anodizing, Micro arc oxidation, Electroplating, Electrophoresis, Radial carving, Silk screen printing, Wire drawing, Mirror polishing, Dyeing, Blackening, CD pattern, Etching, Highlight, Etching, Glue drop, Chromic salt, PVD plating, Laser engraving, Magnetic polishing.

One-stop 5 axis CNC milling Services
Including Forging, Casting, Extrusion, Stamping, Casting, and Hot Forging, which saves a lot of costs.
Products Gallery
sports, 3C Electronics, Communications, Auto Parts, Aerospace Industry, Medical Equipment, Petrochemical Industry, new energy, and other industries.
5 axis CNC machining of impeller
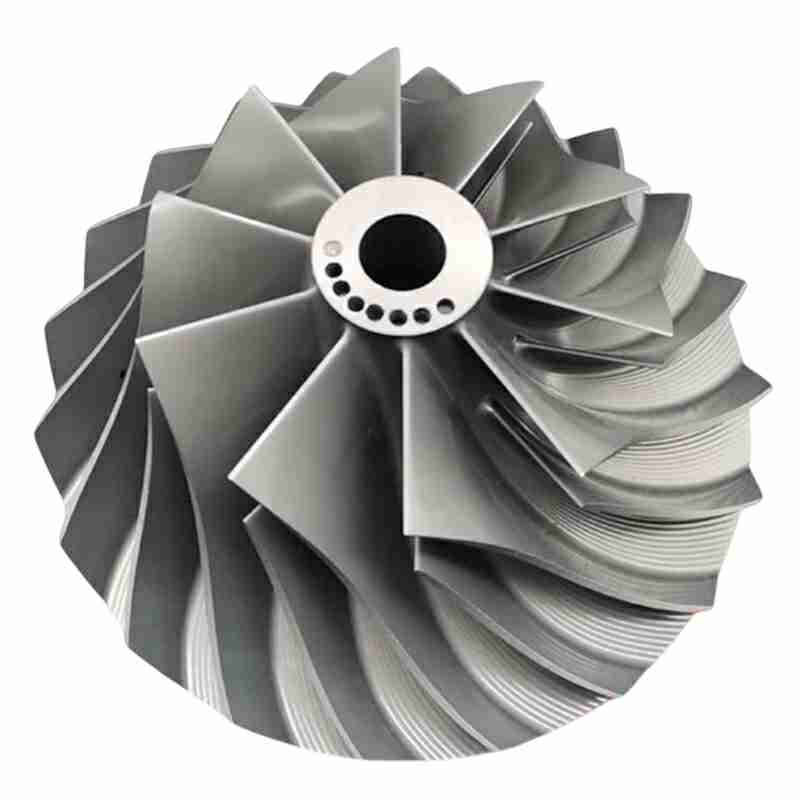
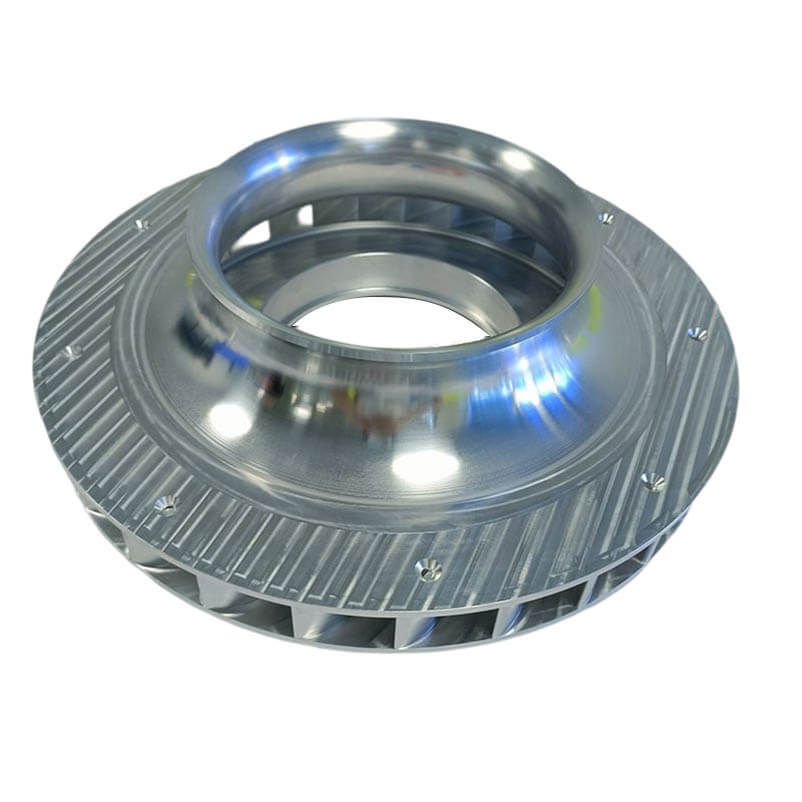

5 axis CNC machining of aerospace parts



5 axis CNC machining of medical parts
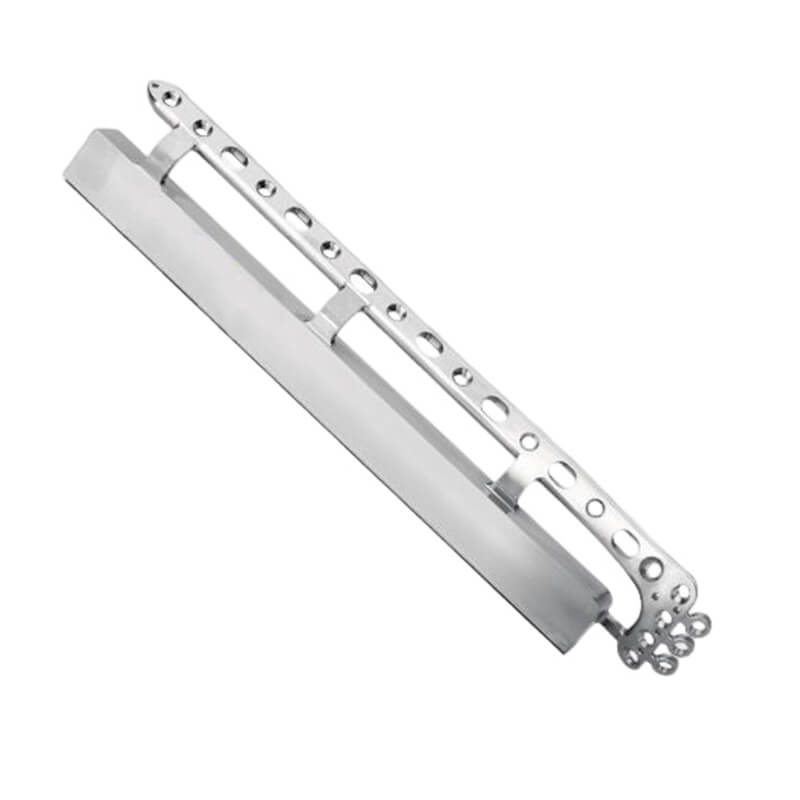

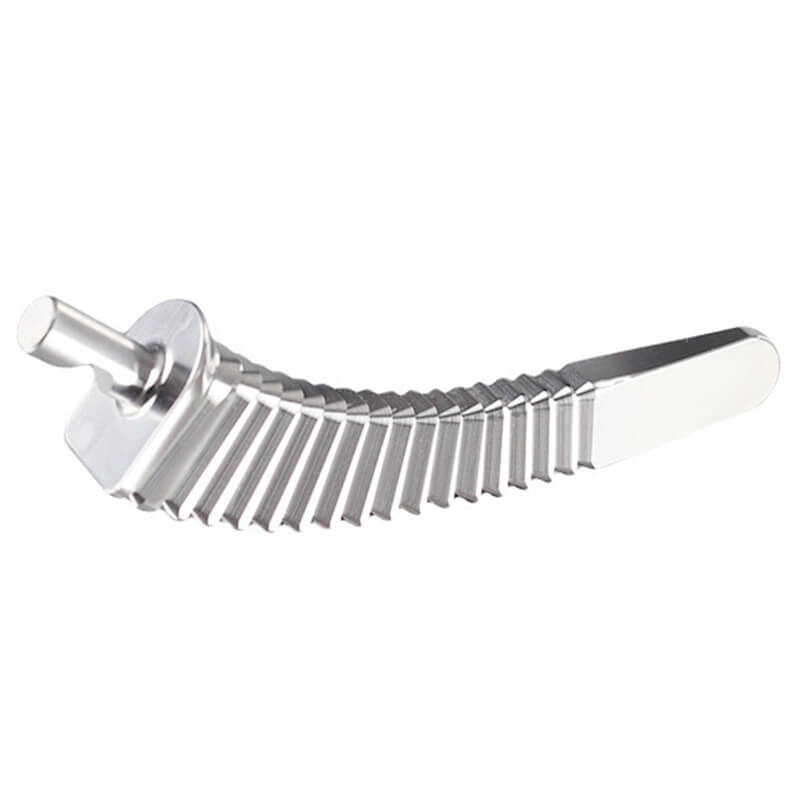
5 axis CNC machining of automotive components





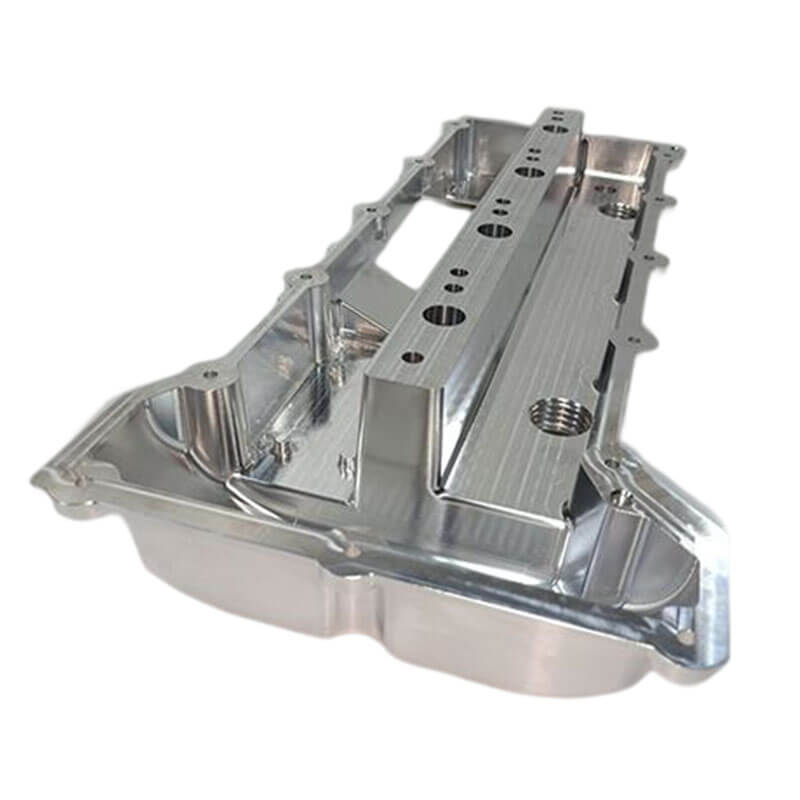

5 axis CNC machining of robot components
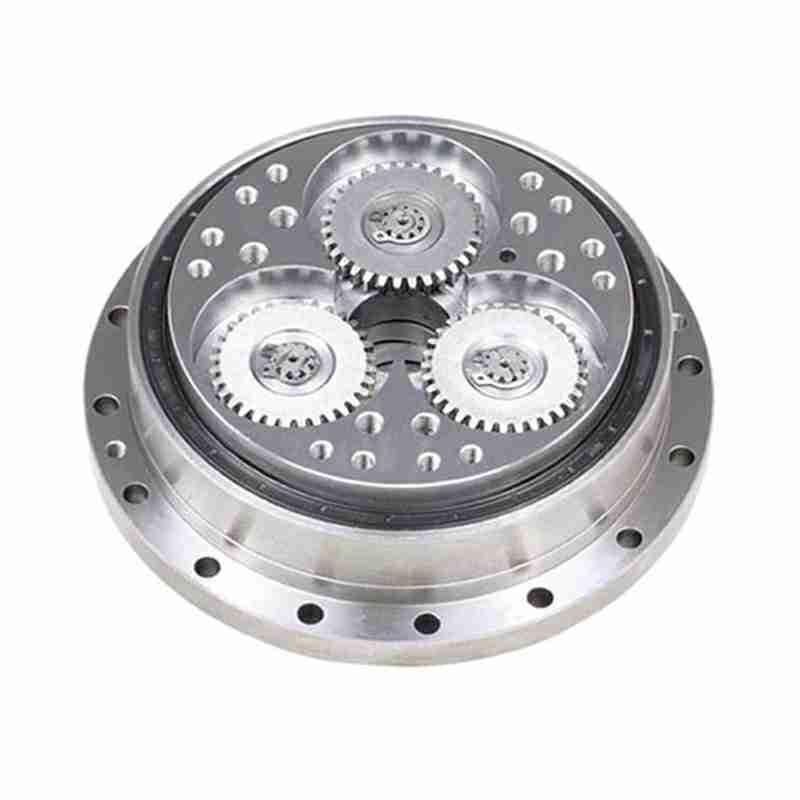

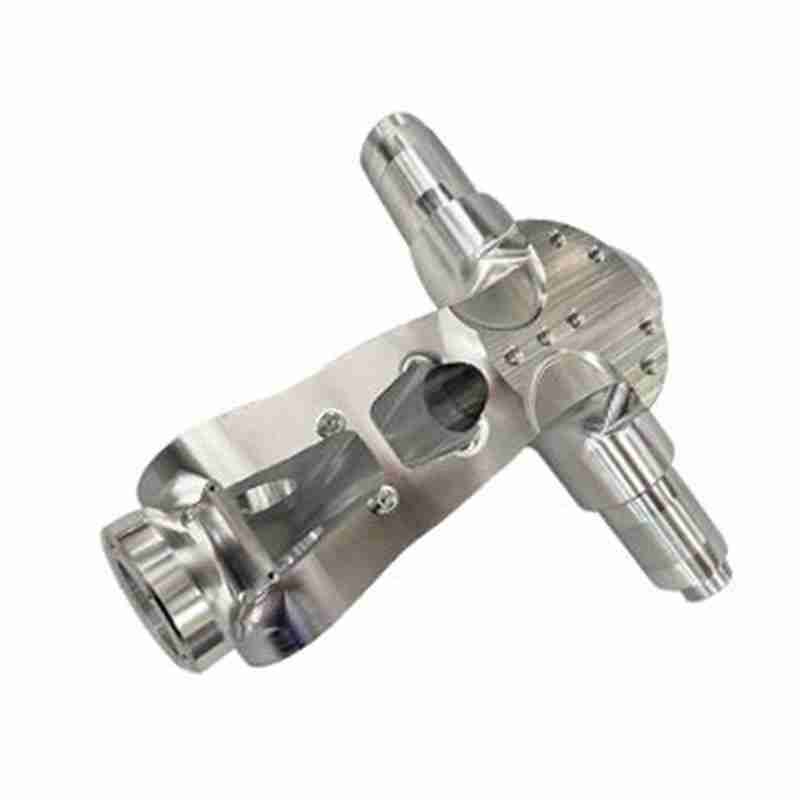
Why Choose Masion
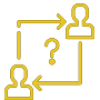
Rich Experience
Currently, Masion has experience in 5 axis CNC machining products for various industries, including aerospace, medical, automotive, electronics, robots, navigation, communications, and more.

Excellent Quality Service
Masion communicates with customers in time on production progress, 3+1 service, on-time delivery, and customer satisfaction are the standards for testing product quality.
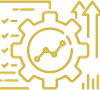
Quality Control
Dedicated inspection team ensuring product quality and on-time delivery. We have a measurement laboratory equipped with high-precision inspection instruments including Coordinate Measuring Machines (CMMs), project meters, scanners, etc. We guarantee 100% inspection and shipment of all products, providing worry-free quality assurance.
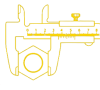
Machining Accuracy
5-axis machining with an accuracy of up to ±0.01mm and surface roughness of SA<0.05um.

Strong Technology
Adhering to Taiwan’s CNC machining and mature experience, strictly following precision manufacturing and processing techniques.

Fast Delivery
With over 30 equipment units, we can provide samples within 7 days and deliver small batches within 10-15 days. We maintain sufficient inventory of conventional materials and operate on a 7×24 production schedule
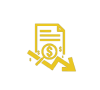
Reducing Costs
Free optimization and Design for Manufacturability (DFM) analysis to reduce costs, minimizing exceptions before mass production, and providing quick response to any issues.

High product yield rate
10-step quality inspection processes, ensuring a product yield rate of 99% through strict control at every stage.

Production Capacity
With 15 years of experience as a CNC machining manufacturer and 5 years of expertise in 5-axis CNC machining, we have processed thousands of product cases. Our team comprises experienced designers, machinists, engineers, and more.
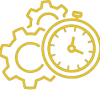
Rapid Production
Quick collaboration with customers for structural and visual verification.
Superior Service – Timely communication of production progress to customers, offering 3+1 service, punctual delivery, and customer satisfaction as the standard for evaluating product quality.
How do we guaranty the quality?
Man
Excellent production and management personnel equipped with 5-axis machining. Experienced programming masters, process engineers, and skilled operators with over 10 years of experience. The production manager is a former engineer from a Taiwanese company, bringing extensive experience and rigorous management to ensure on-time delivery of high-quality products.
Machine
High-precision 5-axis CNC machining with 0.1um feed, 1um cutting, nanometre-level surface roughness, and ±0.05um dimensional accuracy. Software for 5-axis CNC machining: Professional 5-axis precision machining CAM software with 5-axis process development, in-machine measurement, logical judgment, and control plan planning functions. Stable achievement of "0.1um feed, 1um cutting, nm-level surface roughness, and ±0.05um dimensional accuracy" machining. One-click output of NC programs to avoid manual operation errors.
Environment
A clean and orderly machining workshop further ensures the precision of 5 axis cnc machine parts.

Materials
Incoming spectral inspection, no mixing of materials, ensuring the physical properties of customer-customized 5 axis cnc machine parts. By inspecting the material dimensions, material composition reports, and other factors during material intake, the authenticity of the materials can be quickly determined.
Method
Strict adherence to the ISO9001:2015 quality management system to ensure that every 5 axis CNC machine parts meets the requirements. In-machine process inspection and coordinate measuring machine (CMM) inspection of finished products to meet the quality standards for shipment.
CNC 5 Axis Machining Materials
Picture | Material | Brief Introduction | Material Trademark | Surface Finish | More |
---|---|---|---|---|---|
![]() | Aluminum Alloy | Aluminum alloy: Low density, high strength, ductility, corrosion resistance, easy to strengthen and surface treat, good conductivity, recyclable, and cost-effective. | AL5052-T651, AL6061-T651, AL 7075-T651, AL6082-T651 etc | A. Polishing, B. Grinding, C. Radium carving, D. Bead Blasting, E. Painting, F. Coating, G. Anodizing, H. Hard anodizing, I. Teflon Coating, J. Laser marking, K. Silk printing, L. Silk transfer printing | Learn more |
![]() | Brass | Brass is an alloy composed of copper and zinc. High strength, good ductility, excellent mechanical properties, high wear resistance, good corrosion resistance, and lower price. | H58 H59、H62、HA177-2、HMn58-2、HPb59-1、HSn62-1 | A. Polishing, B. Grinding, C. Brushing, D. Laser marking, E. Screen printing, F. Transfer. | Learn More |
![]() | Copper | High copper content, ranging from 99.5% to 99.95%. High density, melting point, excellent electrical conductivity, thermal conductivity, ductility, and corrosion resistance. | T1、T2、T3、TU1、TU2b | A. Polishing, B. Grinding, C. Brushing, D. Laser marking, E. Screen printing, F. Transfer. | Learn More |
![]() | Stainless Steel | Low chromium content, 10.5%, high carbon content, 1.2%. High hardness, wear resistance, and high corrosion resistance. | 201、303、304、316、410、420、17-4PH | A. Polishing, B. Grinding, C. Vacuum heat treatment, D. Bead Blasting, E. Painting, F. Nitriding, G. Passivation, H. Zinc plating,J. Teflon, K. Titanium Coating, L. Laser marking, M. screen printing, N. transfer printing。 | Learn More |
![]() | Plastic | Plastics have poor thermal conductivity, low coefficient of thermal expansion, and low elastic modulus. | POM PEEK HDPE PET Nylon PTFE PVC PP ABS PC PMMA | Painting, F. radium carving, L. chrome plating, R. laser marking, S. silk screen, T. Transfer printing | Learn More |
![]() | Plastic | Plastics have poor thermal conductivity, low coefficient of thermal expansion, and low elastic modulus. | POM PEEK HDPE PET Nylon PTFE PVC PP ABS PC PMMA | Painting, F. radium carving, L. chrome plating, R. laser marking, S. silk screen, T. Transfer printing | Learn More |
![]() | Plastic | Plastics have poor thermal conductivity, low coefficient of thermal expansion, and low elastic modulus. | POM PEEK HDPE PET Nylon PTFE PVC PP ABS PC PMMA | Painting, F. radium carving, L. chrome plating, R. laser marking, S. silk screen, T. Transfer printing | Learn More |
![]() | Plastic | Plastics have poor thermal conductivity, low coefficient of thermal expansion, and low elastic modulus. | POM PEEK HDPE PET Nylon PTFE PVC PP ABS PC PMMA | Painting, F. radium carving, L. chrome plating, R. laser marking, S. silk screen, T. Transfer printing | Learn More |
![]() | Plastic | Plastics have poor thermal conductivity, low coefficient of thermal expansion, and low elastic modulus. | POM PEEK HDPE PET Nylon PTFE PVC PP ABS PC PMMA | Painting, F. radium carving, L. chrome plating, R. laser marking, S. silk screen, T. Transfer printing | Learn More |
Surface Finish of 5 Axis CNC Machining Parts
Picture | Process | Spec | Material | Colors | Appearance | More |
---|---|---|---|---|---|---|
![]() | Electrophoresis | Electrophoresis coats workpiece surface with colored paint film for corrosion resistance, wear resistance, aesthetics, or special functions. | Aluminum, steel, stainless steel, Magnesium alloy, zinc alloy, etc. | Red, green, blue, purple, white, black, etc. | Glossy or Matte | Learn more |
![]() | Electroplating | Electroplating utilizes electrolytic principles to apply a thin metal layer for oxidation prevention, wear resistance, conductivity, reflectivity, and corrosion resistance. | Copper, cast iron, steel and stainless steel, aluminum, ABS plastics, polypropylene, polysulfone and phenolic plastics, etc. | Red, yellow, gold, green, blue, purple, rose gold, titanium, white, black, etc. | Glossy or Matte | Learn More |
![]() | Polishing | Polishing reduces surface roughness through mechanical, chemical, or electrochemical action, resulting in a smooth and lustrous finish, eliminating imperfections and enhancing paint appearance. | Copper, cast iron, steel and stainless steel, aluminum, magnesium alloy, titanium alloy, etc. | N/A | Glossy | Learn More |
![]() | Anodizing | Anodizing is an electrochemical process forming oxide film on metals like aluminum, improving corrosion resistance, wear resistance, hardness, and surface appearance. | Aluminum alloy, magnesium alloy, titanium alloy, etc., | Clear, black, grey, red, blue, gold,yellow, violet, double colors, camouflage color, etc. | Matte, Semi-glossy, glossy | Learn More |
![]() | Bead Blasting | Compressed air propels abrasive materials to remove rust, stains, and paint from metal surfaces, achieving a renovated appearance by grinding burrs and scars. | Cast iron, steel, stainless steel, aluminum alloy, magnesium alloy, titanium alloy, ABS, etc. | N/A | Matte | Learn More |
![]() | Powder Coating | Plastic spraying electrostatically applies powder coating to metal surfaces, forming a protective film for corrosion resistance, improved appearance, and color options. | Cast iron, steel, aluminum alloy, magnesium alloy, ABS and various plastics, etc. | Black, white, blue, green, yellow, purple, all the colors on the Pantone color card | Matte or glossy | Learn More |
![]() | PVD(Physical Vapour Deposition) | PVD vaporizes source materials and deposits functional films onto substrates, enhancing appearance, hardness, wear resistance, corrosion resistance, and service life. | Iron, stainless steel, aluminum alloy, titanium alloy, copper, ceramics, tungsten steel, zinc alloy, ABS and various plastics | Gold, gun black, coffee, purple, heptagon, royal blue, azure blue, black, titanium gray, so why bowl, rose gold, gold, champagne gold, etc. | Glossy | Learn More |
5 axis CNC machining service FAQs
Generally, there are two types of five-axis machining centers: 3+2 and simultaneous five-axis. A 3+2 five-axis machining center consists of three linear axes (X, Y, Z) and two rotational axes (A, B). On the other hand, simultaneous five-axis refers to the capability of all five axes (X, Y, Z, A, B) to move simultaneously in a coordinated manner.
3+2 machining primarily relies on the rotation of two axes on the worktable, allowing the tool to perform multi-sided machining along the rotating surfaces of the product.
Five-axis machining centers are equipped with two additional rotational axes, allowing the worktable to rotate simultaneously. As a result, both the tool and the worktable can rotate at the same time, enabling the machining of different surfaces of complex workpieces.
It also utilizes computer-controlled tool movements along five different axes, enabling extremely precise cutting and machining in three-dimensional space.
Typically, the applications of five-axis machining include components such asimplantable medical devices, surgical robots, surgical instruments, turbocharger impeller machining, secondary impeller machining, 7-stage impeller machining for turbo molecular pumps, high-pressure water pump impeller machining, air compressor impeller machining, blower impeller machining and diesel engine crankshafts.
Different axes:The tool of the three-axis machining center can move along three directions, which is what we call the three axes (X,Y,Z).This means that the workpiece often needs to be repositioned and re-clamped multiple times to complete complex machining processes. Four-axis machining adds an additional rotational axis (usually A or B axis) to provide an additional cutting direction, reducing the need for re-clamping. However, there are still geometric limitations that cannot be fully addressed. The “3+2” design of a five-axis machining center typically involves adding an additional rotational axis (usually called the C-axis) to the three-axis setup. This design enables simultaneous rotation of the tool and workpiece through the rotational axis, allowing for synchronous machining of complex cuts on different surfaces. As a result, five-axis machining centers can quickly and efficiently cut complex workpieces, minimizing the need for re-clamping and repositioning. This design significantly improves both the efficiency and precision of the machining process. Compared to three-axis and four-axis machining centers, five-axis machining centers have superior capabilities in processing complex geometries and intricate surfaces, resulting in a several-fold increase in processing efficiency.
Different machine prices: Three-axis machining centers are the most commonly used and generally satisfy simple milling operations, so the equipment prices are relatively lower, typically around 29000usd to 36000usd. Four-axis machining centers, with an added rotational axis to the three axes, incur additional costs ranging from 7500usd to 15000usd. Five-axis machining centers have higher prices, generally ranging from 75000usd to 230000usd.
Machining characteristics: In three-axis machining, the tool direction remains constant throughout the cutting path. The cutting condition of the tool tip cannot be perfectly optimized in real-time. During five-axis machining, we can consider improving the cutting direction of the tool to ensure the optimal path of tool movement throughout the entire machining process. Additionally, in five-axis machining of workpieces, the tool can maintain a simultaneous linear movement direction, resulting in the best cutting performance. Compared to four-axis machining, where an additional rotational axis is added to a three-axis machining center, the rotational axis is limited to a 360° rotation in the horizontal plane and cannot achieve high-speed rotation.
This characteristic is suitable for machining some box-type parts.
Different machining costs: The average cost for three-axis machining is generally around 9-10usd per hour, four-axis machining is around 15-25usd per hour, and five-axis machining costs around 60-75usd per hour. It can be seen that the investment and output of five-axis machining equipment are proportional, and the machining difficulty is high, typically requiring experienced and skilled technicians to operate.
With the continuous development and advancement of technology and the manufacturing industry, the widespread application of high-end complex products has driven the development of 5-axis machining technology. The demand for complex components with high precision and intricate surfaces has made 5-axis machining centers the preferred choice for customers. Of course, customers also consider the machining cost of 5-axis machining centers as a necessary factor to consider.
The pricing for five-axis machining centers can vary among suppliers and is typically determined by several factors. Here are some common cost factors:
Material cost: The type and quality of materials used in five-axis machining centers will impact the cost. High-performance metals and advanced composite materials can result in higher costs, and material selection depends on the customer’s design requirements, with different materials varying in performance and price.
Equipment and energy cost: The usage of equipment and energy, as well as the electricity rate from the power supplier, will determine the hardware cost of the five-axis machining center. Some suppliers may charge additional equipment usage fees based on the size and complexity of the workpiece.
Difficulty and cycle of machining: The difficulty and cycle time of the five-axis machining center are key factors influencing the cost. More complex workpieces require more machining steps and time, which can increase the cost. Therefore, cost-effectiveness should be considered during the design phase.
Software and labor cost: The software licensing and labor operation of the five-axis machining center are also cost factors. Some suppliers may charge labor operation fees based on the quantity of workpieces or the complexity of the process.
Quantity of workpieces: Typically, the machining cost for small batch production is higher compared to large batch production since suppliers prefer larger orders to optimize time and resources. However, Masion welcomes small batch orders and provides corresponding discounts.
In addition to the above factors, there may be additional costs related to special packaging, transportation, or other requirements based on customer requests.
The pricing structure for five-axis machining centers is a complex issue. Different suppliers of five-axis machining may have different pricing structures, and customers should choose the appropriate five-axis machining supplier based on their specific needs. Prior to selecting a five-axis machining supplier, customers should consider factors such as the technical expertise of their engineers, service quality, and reputation to ensure they receive the best value.
Regarding specific five-axis machining costs, prices in the market are typically around 50usd per hour. For a workpiece with dimensions of 1000×1000, the price may be around 80usd per hour. Masion provides five-axis machining services and offers reasonable quotes based on your workpiece, with competitive pricing and high quality assurance.
5-axis machining centers have diverse functionalities and powerful processing capabilities, enabling them to process various different materials. These machines offer enhanced flexibility and precision compared to traditional 3-axis machines. Here are some common types of materials that can be machined using 5-axis CNC machines:
Metals: 5-axis CNC machines are widely used for machining various types of metals, including aluminum, steel, stainless steel, brass, copper, titanium, and alloys etc. They are capable of producing complex shapes, intricate patterns, and precise details on metal parts.
Plastics: Different types of plastics, such as ABS, acrylic, polycarbonate, nylon, polypropylene, and PVC, can be machined using 5-axis CNC machines. These machines can create intricate designs and smooth finishes on plastic components.
Composites: 5-axis CNC machines are suitable for machining composite materials, which are combinations of different materials like carbon fibers, fiberglass, Kevlar, or other reinforcing fibers embedded in a matrix material. They are commonly used in aerospace, automotive, and marine industries.
Wood: CNC machines are widely used in woodworking, and 5-axis CNC machines can handle complex wood machining tasks. They can carve intricate designs, create curved surfaces, and produce high-quality wooden furniture, decorative items, and architectural components.
Foam: 5-axis CNC machines are used for machining foam materials, such as expanded polystyrene (EPS) and polyurethane (PU) foam. They are commonly employed in the production of molds, prototypes, architectural models, and packaging inserts.
The accuracy of five-axis machining centers varies among different brands. Generally, German brands have the highest precision, followed by brands from Japan and the United States. For example, the repeatability of positioning accuracy of the five-axis machining center used by Masion can reach 0.001 millimeters, while the machining accuracy is within the range of ±0.01 millimeters. (0.0004 inch) Such precision levels typically meet the tolerance requirements for most complex workpieces.
Maximum workpiece size: 2600×700 mm
Maximum travel: 2000x610x630 mm
A-axis swing angle: 360°
Maximum swing angle of B-axis: ±100°
Maximum workpiece weight: 1000 kg
Positioning accuracy: <6μm
Repeatability: <4μm
Maximum center coolant pressure: 150 Pa
Maximum spindle speed: 20000 rpm
Five-axis linkage: X, Y, Z, A, B.
We usually understand the time that affects the production of five-axis machining from the following factors.
Complexity of the part design: If a customer’s product design is highly complex with multiple surfaces and holes to be machined, it will take more time to produce the product.
Choice of material grade: Generally, aluminum is easier to machine compared to other metal materials, resulting in relatively shorter processing time. However, if the material to be machined using five-axis technology is a harder material like stainless steel, titanium alloy, etc., the machining time will be longer, and the tools may be more prone to wear and damage.
Surface finish requirements: Five-axis machining typically involves rough machining and finishing stages. For parts requiring extremely smooth surface finishes, an additional process step may be needed. If only general surface finish requirements are necessary, the machining time will be relatively shorter.
Surface treatment requirements: Some customers may require post-machining surface treatments such as oxidation, plating, etc. This will increase production time, and there is a possibility of product damage during intermediate processes, leading to higher scrap rates.
Production scheduling: If it is a reorder of existing products, the speed will be faster, usually around 3-4 days. However, as material procurement, CNC machining, and other processes all require time, any delays in these stages can affect the overall production schedule.
Quantity considerations: For some precision parts requiring five-axis machining, if the order quantity does not meet the minimum requirements, additional processes such as wire cutting or laser cutting may be needed, which will consume more time and effort. This is especially true for customized high-precision precision components with small volumes and an imperfect supply chain, making it prone to supplier delivery delays.
After sample development, when moving to mass production of precision components, there may be process factors that are not conducive to large-scale production. For example, there may be no issues during CNC machining, but in mass production, it is found that some precision parts are not easily oxidized, requiring fixture treatments, etc.
Unexpected events involving skilled personnel in precision part manufacturing facilities. If there is a situation where there are no qualified substitute personnel, it will lead to a decrease in production capacity, especially for processes with a high level of technical dependence, which may result in delivery delays.
Other uncontrollable factors such as power outages, equipment failures, and other unforeseen circumstances. Companies should have contingency plans in place to deal with such situations to avoid being at a loss.
Overall, taking into account the above factors, the typical production time for sample five-axis machining at Masion is around 5-10 days, for small orders it is generally 10-15 days, and for large orders it is usually 30-35 days.
Yes, you mentioned the advantages of 5-axis CNC machines. They are highly useful in mold machining and prototype design, especially in the early stages of complex workpieces that require validation. By using 5-axis machining centers, validation time can be reduced, market acceptance can be improved, and faster product development cycles can be achieved.
These machines offer great flexibility and can produce complex prototypes as well as batch or high-volume products. In general, a 5-axis machining center is often the optimal choice for machining workpieces. It can handle complex components with diverse shapes and surfaces, while ensuring high precision and superior quality of the workpieces. As a result, 5-axis machining is widely applied and considered the best solution in many industrial manufacturing sectors.
By using 5-axis CNC machines, the need to transfer workpieces between different machines is reduced, thereby minimizing the risk of human error. Additionally, these machines often have high-speed cutting capabilities, which can enhance production efficiency and reduce machining time.
In conclusion, the versatility, flexibility, and high precision of 5-axis CNC machines make them indispensable tools in mold machining and prototype design. They can accelerate the product development process, improve product quality, and provide a competitive advantage for businesses in batch production of complex workpieces.
When choosing a qualified 5-axis machining center supplier, you should pay attention to the following details:
Determine if the supplier has its own 5-axis machining center rather than relying on outsourcing. You can directly inquire with the supplier or visit their machining facility to ensure they can perform 5-axis machining tasks directly.
Confirm if the supplier has experience in machining complex components. You can request the supplier to showcase photos or samples of previously machined complex parts to verify their experience and capabilities.
Verify if the supplier has a design team and can provide design support for the components. Correct design is crucial for machining complex parts, and discussing and optimizing the design with the supplier can ensure a smooth machining process.
Evaluate the professionalism of the supplier’s communication personnel. For machining complex parts, strict requirements regarding dimensions, tolerances, surface roughness, etc., exist. The supplier’s communication personnel need to possess professional knowledge, effectively communicate with the customer, understand and fulfill their requirements, and minimize time costs.
Compare the machining prices offered by different suppliers. Machining complex components typically incurs higher costs, and there may be variations in the quotations provided by different suppliers. Customers can choose a suitable price based on their own situation and ensure that the pricing from the selected supplier is reasonable.
Confirm if the supplier has samples or case studies of complex components available for reference to evaluate their machining quality and capabilities.
Verify if the supplier has a strict quality management system in place to ensure the quality of complex components.
Confirm if the supplier is equipped with high-quality inspection equipment such as coordinate measuring machines, project meters, surface roughness testers, etc., and understand their inspection procedures and standards.
Considering these factors comprehensively, choosing a reliable 5-axis CNC machining service provider can ensure high-quality machining results and a smooth production process.
Free Sample
Explore Other Services
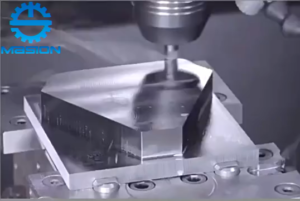
CNC Milling Services
Masion provides CNC Milling Services, specializing in the manufacturing of various CNC Milling parts, ensuring quality and quantity assurance.

CNC Milling and Turning Services
CNC Milling and Turning Services –China CNC Turning Milling Parts Manufacturer. CNC milling and turning is one of the advanced manufacturing technologies in the international mechanical processing industry. It integrates

Rapid Prototyping Manufacturing Services
China Rapid Prototyping Manufacturing Services-Your Trusted CNC and 3D Rapid Prototyping Manufacturer. I understand that you are looking for a suitable manufacturer for rapid prototyping (3D printing, rapid CNC machining,