Anodizing
Aluminum Anodized Finish (Aluminum Anodizing)
Brief introduction to the aluminum anodizing process
Anodic oxidation, also known as aluminum anodizing, refers to the electrochemical oxidation of metals or alloys. It is a process in which an oxide layer is formed on the surface of the aluminum and its alloys (anodes) under specific electrolyte and process conditions with the application of an external current.
There are three common types of anodizing for aluminum products: sulfuric acid anodizing, chromic acid anodizing, and oxalic acid anodizing. If not specified, sulfuric acid anodizing is usually referred to.
Here is a brief overview of Aluminum anodizing:
Common Substrates for Aluminum Anodizing:
Magnesium alloys: Primarily used for conductive oxidation/chemical oxidation, resulting in colors such as white and yellow.
Titanium alloys: Anodizing titanium alloys can produce various colors, including blue, yellow, green, gold, etc.
The thickness of Aluminum Anodizing:
Functions of Aluminum Anodizing:
- Protective: Increases surface hardness (HV300) and improves wear resistance.
Decorative: Creates various surface colors and effects.
Insulating: The oxide layer is non-conductive and provides insulation.
- Enhances adhesion to organic coatings.
Improves bonding with inorganic coverings.
Colors of Aluminum Anodizing:
Note: The translation provided here is a direct translation of the text. Some terms, such as “ADC10” and “ADC12,” may refer to specific aluminum alloy designations and may vary based on regional standards.
02 | Aluminum Anodizing Process
Aluminum Anodizing Process:
Note 1:
Note 2:
Note 3:
03 | Aluminum Anodizing Production Equipment Showcase
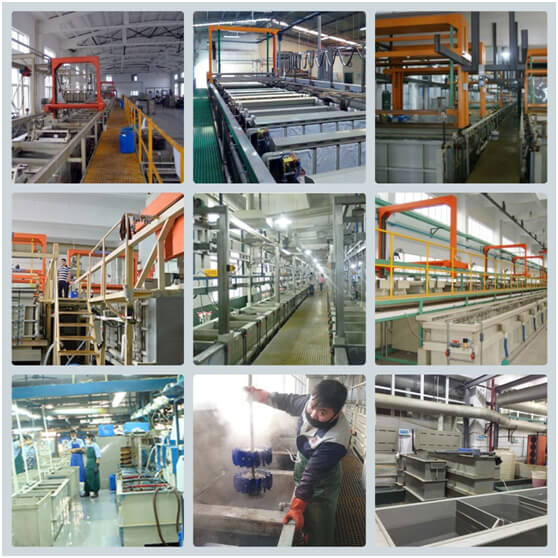
In addition, the supporting facilities include an automatic sandblasting machine station and 15 manual sandblasting machines. There are also resources available for grinding, polishing, and high-gloss outsourcing services. The daily average production capacity exceeds one million units, ensuring sufficient production capacity.
04 | Aluminum Anodizing Display of Inspection Equipment
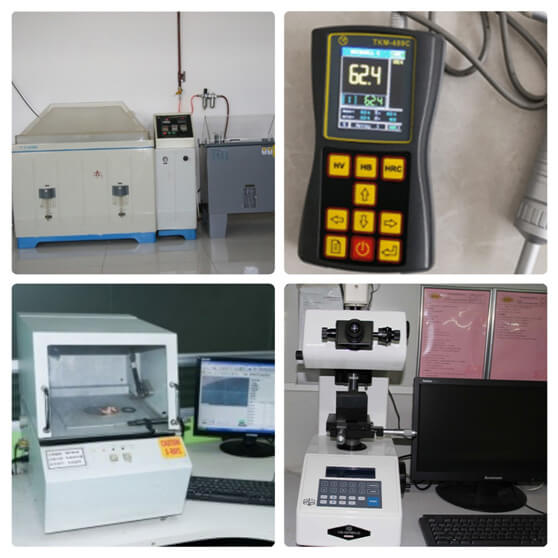
05 | Aluminum anodizing sample cases
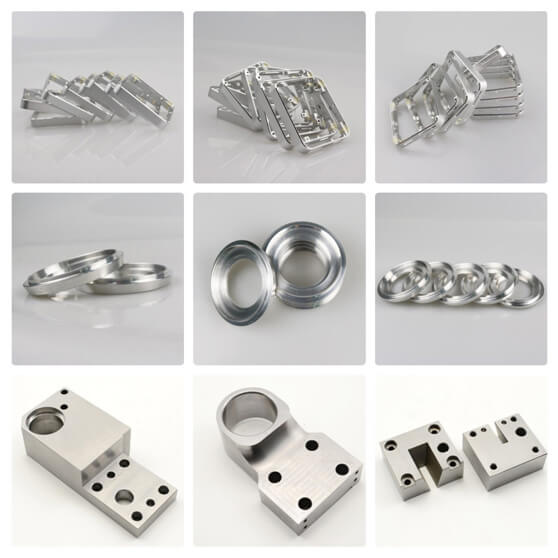
Anodizing die-cast aluminum
Brief Introduction to Anodizing of Die-Cast Aluminum
Anodizing die-cast aluminum
Colors for Die-Cast Aluminum Anodizing
Common Base Materials for Die-Cast Aluminum Anodizing
Cast aluminum series: such as A356, A360, A380, etc.
DM series: such as DM3, DM6, etc.
Thickness of Die-Cast Aluminum Anodizing
Process Flow of Anodizing Die-Cast Aluminum Alloys
General Process Flow of Anodizing Die-Cast Aluminum
Note 1
Note 2
Note 3
Display of Equipment for Anodizing Die-Cast Aluminum
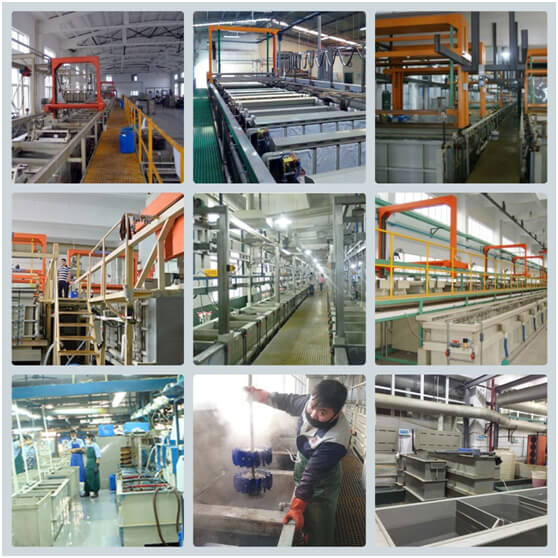
Exhibition of Inspection Equipment for Anodizing Die-Cast Aluminum
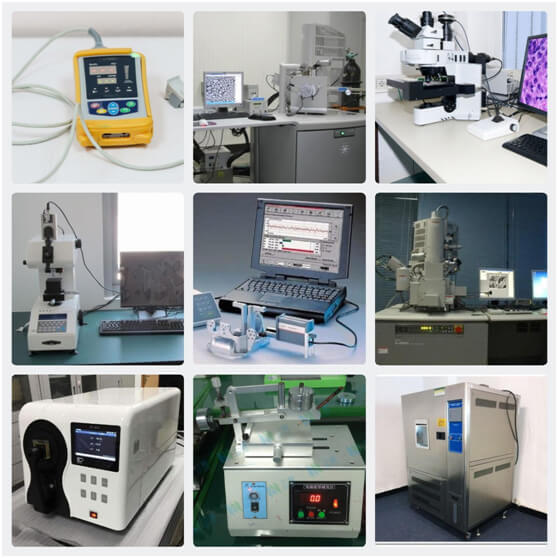
Anodized Die-Cast Aluminum Sample Cases
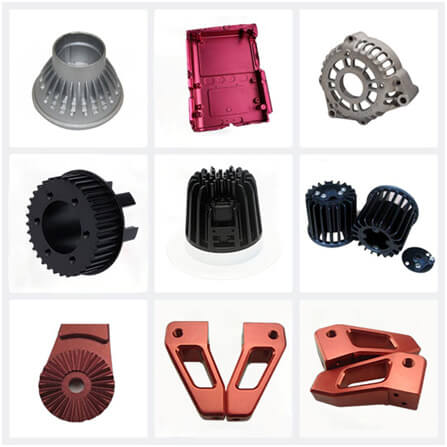
Camouflage Anodizing
Camouflage Anodizing Process Overview
It is said that there is another implementation method, which is to use the masking spraying/dripping method on the basis of anodizing coloring to create a disorderly camouflage pattern of dual or multiple colors on the surface of the workpiece through color adjustment. However, this method is too complicated and has been discontinued.
Camouflage anodizing of aluminum parts is now widely used in the electronic industry, such as electronic cigarettes, fidget spinners, beauty pens, and other fields.
Camouflage Anodizing Process Flow
- Cleaning: use a cleaning agent to remove impurities from the metal surface to ensure that the surface is free of contaminants.
Acid washing: immerse the metal in an appropriate acid solution to corrode the metal surface and prepare it for surface oxidation.
Heat treatment: place the metal in a high-temperature environment to form a layer of oxide film on the surface, creating camouflage.
Polishing: polish the surface of the oxide film to make it smooth and shiny, achieving the camouflage effect.
Protection: apply a coating to the surface of the oxide film to increase its corrosion resistance and wear resistance and extend its service life.
Camouflage anodizing production equipment display.
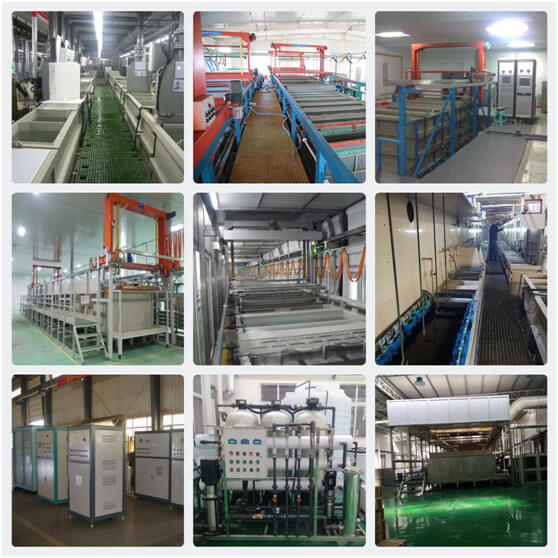
Camouflage Anodizing Testing Equipment Display
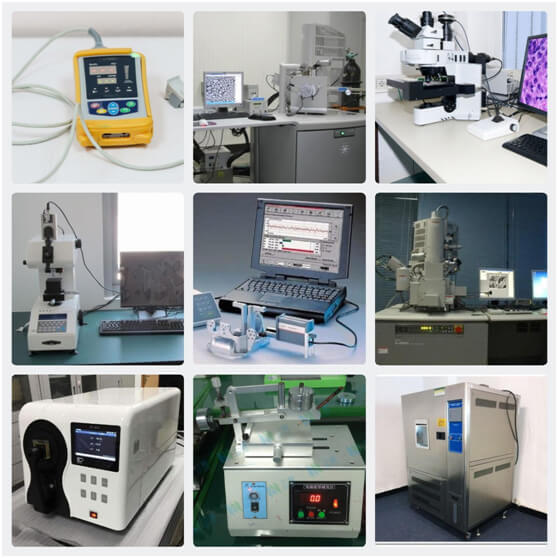
Sample Cases of Camouflage Anodizing
Camouflage anodized aluminum electronic cigarette
Camouflage anodized aluminum spinner
Camouflage anodized aluminum pen
Camouflage anodized aluminum flashlight
Camouflage anodized aluminum rifle parts
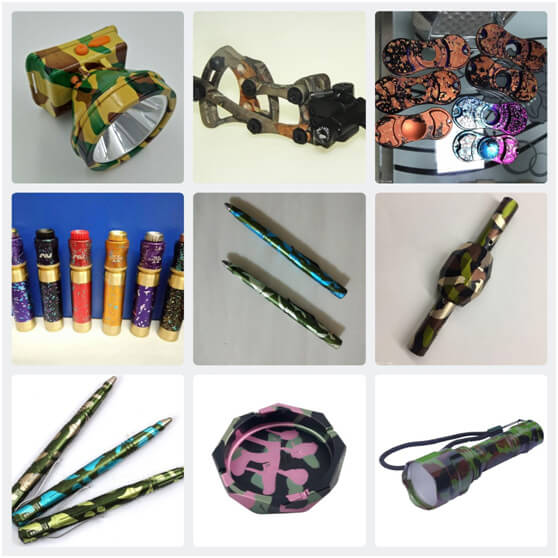
Color Anodizing
Brief Introduction to Color Anodizing Process
Color anodizing is a process that uses electrolysis to produce a decorative and protective oxide coating on the surface of metal substrates, typically aluminum. The anodizing process involves immersing the metal substrate in an electrolyte solution and passing an electric current through it, which causes the surface to oxidize and form a layer of aluminum oxide. The thickness of the oxide layer can be controlled through the voltage and duration of the process, which is important for achieving consistent coloration. In the case of color anodizing, dyes or pigments are added to the electrolyte solution to impart a desired color to the oxide layer. The type and concentration of the dye or pigment will affect the resulting color, and multiple colors can be achieved by either masking or patterning the metal substrate prior to anodizing. Once the desired color is achieved, the oxide layer is sealed to improve its corrosion resistance and durability.
The anodizing of aluminum products can usually be divided into three types: sulfuric acid anodizing, chromic acid anodizing, and oxalic acid anodizing. If not specifically stated, it usually refers to sulfuric acid anodizing.
Common Substrates for Color Anodizing
Die-cast aluminum alloys: Usually, when die-casting aluminum alloys are anodized, only the natural color (gray) or black can be achieved. However, there are also a few anodizing plants that can achieve color anodizing on die-cast aluminum alloys.
Magnesium alloys: Mainly used for conductive oxidation/chemical oxidation, with colors such as white and yellow. Titanium alloys: Color anodizing of titanium alloys can achieve various colors, such as blue, yellow, green, gold, etc.
Thickness of Color Anodized Film:
The Function of Color Anodizing:
- Protective: increase surface hardness (HV300) and enhance wear resistance and corrosion resistance;
Decorative: can create various colors and surface effects;
Insulating: the oxide film is non-conductive and can act as an insulator;
Can improve the adhesion between parts and organic coatings;
Can improve the adhesion between parts and inorganic coatings.
Different Colors of Color Anodizing
Dyeing involves adsorbing pigments into the gaps of the oxide film and achieving different colors through subsequent sealing treatment. Dyeing has the advantages of fast coloring, bright color, and simple operation. In addition, it is common for customers to provide a Pantone color code for specified colors, and some anodizing plants claim to be able to customize colors for customers. Although theoretically, anodizing plants can achieve any color, it is not cost-effective for both the plant and the customer to do so without a large volume of goods. If custom color matching is necessary, the starting price for the entire process is around 500USD.
Currently, anodizing plants can meet more than 99% of users’ demands for personalized colors through color matching. Therefore, the best way to achieve color anodizing that is fast, good, and cheap is to find an anodizing plant that can achieve the desired colors.
Dyeing: Natural, white, black, bright silver, gray, matte white, matte black, bright black, red, purple, yellow, green, gold, rose gold, champagne gold…almost all colors can be done!
Electrolytic coloring: Based on the transparent oxide film generated in the first electrolysis, the secondary electrolysis film is generated in a solution containing a metal salt by using an alternating current. The weather resistance, light resistance, wear resistance, etc. of the oxide film generated by electrolytic coloring are much better than those of the dyeing film, but the obvious limitation of electrolytic coloring is that the color is monotonous. Currently, the most commonly used electrolytic coloring is black, and a few other colors such as antique copper, golden yellow, and jujube red can also be produced. However, the overall color and glossiness are far inferior to those of the dyeing film.
Process Flow of Color Anodizing
Anodizing process for color anodized aluminum:
Display of color anodizing production equipment
Hanging Equipment
Degreasing Machine
Acid Etching Tank
Anodizing Tank
Quality Inspection Equipment
Dyeing Tank
Sealing Tank
Auxiliary Equipment
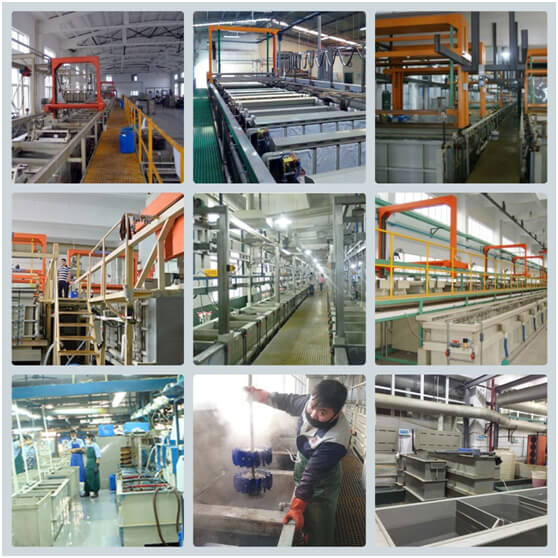
Color anodizing production line
Display of Production Equipment for Color Anodizing
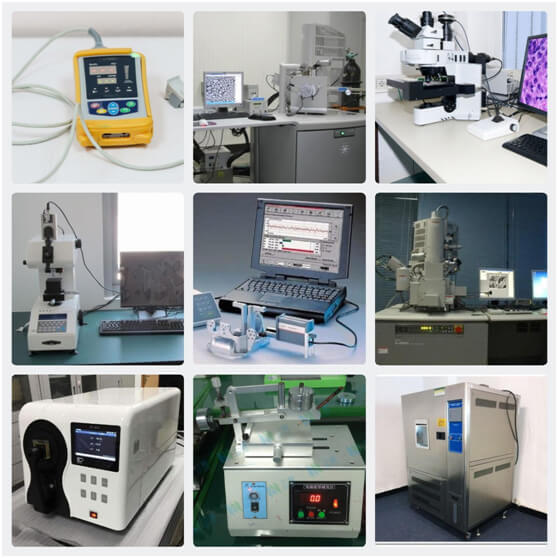
Sample Cases of Colored Anodizing
Color Aluminum Anodizing doors and windows
Color Aluminum Anodizing automotive parts
Color Aluminum Anodizing household items
Color Aluminum Anodizing electronic product casings
Color Aluminum Anodizing aerospace components
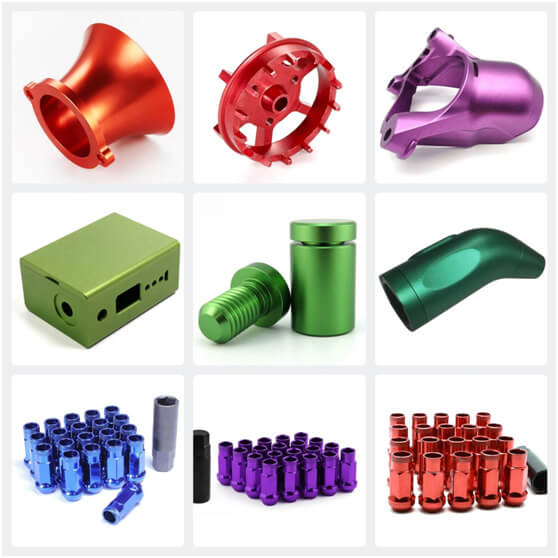
Conductive oxidation(Anodizing)
Brief introduction of the conductive oxidation process
After undergoing conductive oxidation, aluminum workpieces acquire certain corrosion resistance properties while retaining their surface conductivity. Additionally, conductive oxidation effectively prevents interference from electromagnetic signals.
Common Substrates for Color Anodizing
Die-cast aluminum alloys: Usually, when die-casting aluminum alloys are anodized, only the natural color (gray) or black can be achieved. However, there are also a few anodizing plants that can achieve color anodizing on die-cast aluminum alloys.
Magnesium alloys: Mainly used for conductive oxidation/chemical oxidation, with colors such as white and yellow. Titanium alloys: Color anodizing of titanium alloys can achieve various colors, such as blue, yellow, green, gold, etc.
Thickness of Conductive Oxide Film
Common substrates for conductive oxidation
Magnesium alloys are usually subjected to anodizing treatment, which involves conducting oxidation.
Functions of Conductive Oxidation
2. Wear Resistance: It possesses certain wear-resistant properties. (However, it is advised not to test it by scratching with hard objects.)
3. Corrosion Resistance: It has a certain level of corrosion resistance.
4. Protection against Electromagnetic Signal Interference.
Colors of Conductive Oxide
- Colorless transparent oxide film, with a thin film thickness of approximately 0.3-0.5 μm, exhibits good conductivity. It is primarily used for deformed aluminum electrical components.
- With a film thickness of around 0.5 μm, it ranges from colorless to rainbow or deep brown. It has good corrosion resistance and fewer pores. It is applied to larger components or assemblies unsuitable for anodizing.
- The oxide film is gold and rainbow in color, with better corrosion resistance. It is suitable for localized oxidation of aluminum alloy welding components.
- The oxide film is rainbow-colored, thin, and exhibits better conductivity than the formula mentioned in No. 2. It is suitable for components that require certain conductivity.
- After conductive oxidation, the oxide film needs to undergo post-treatment filling. The post-treatment formula is 30-50 g/L K2Cr2O7 (or Na2Cr2O7) (CP grade) at 90-95°C for 5-10 minutes. This is commonly used as an underlying layer for spray painting or electrophoretic coating processes.
Conductive Oxidation Process Flow
General Process Flow of Conductive Oxidation
- Aluminum workpiece
- Hanging Fixture
- Degreasing/Deoiling
- Water Rinse
- Alkaline Etching
- Water Rinse
- Brightening
- Water Rinse
- Oxidation
- Continuous Water Rinse
- Hot Water Rinse
- Hot Air Blow Dry
- Baking and Drying at 40 degrees Celsius (Aging Treatment)
- Unhanging Fixture
- Quality Inspection
- Packaging
- Shipment.
Prepare the aluminum workpiece
Mounting on fixtures
Degreasing/Deoiling
Water rinse
Alkaline etching
Water rinse
Brightening
Water rinse
Oxidation
Continuous water rinse
Hot water rinse
Hot air blow dry
Baking and drying at 40 degrees Celsius (Aging treatment):
Unmounting fixtures
Quality inspection
Packaging
Shipment
Note 1
Note 2
Note 3
Conductive Oxidation Production Equipment Showcase
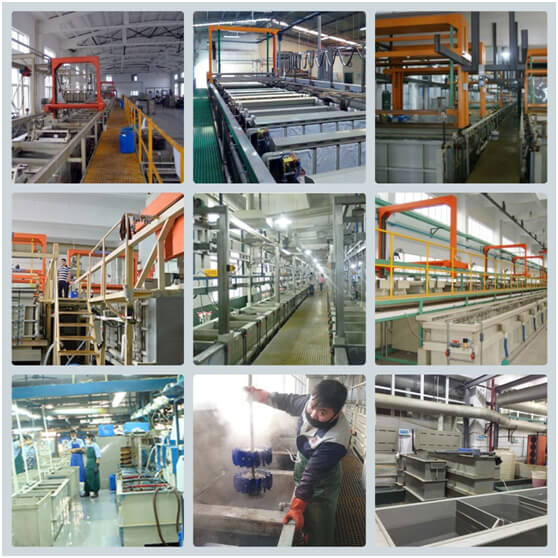
Conductive Oxidation Testing Equipment Showcase
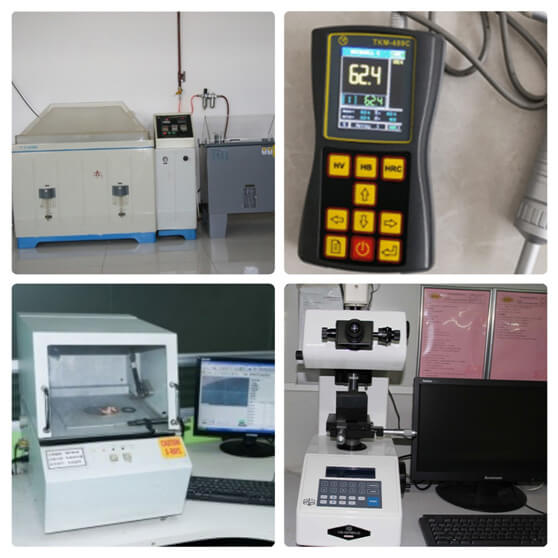
Conductive Oxidation Sample Cases
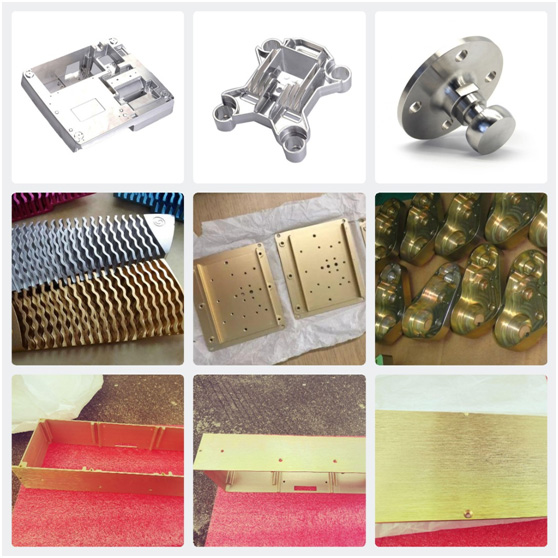
Electrolytic Coloring of Anodized Aluminum
Brief Introduction tothe process of coloring aluminum electrolytic.
The principle of aluminum electrolytic coloring involves the use of a physical method where, in the presence of an electric current, metal ions are reduced and deposited as colloidal particles in the pores of the oxide film. It is based on the transparent oxide film formed during the initial electrolysis and involves secondary electrolysis using alternating current in a solution containing metal salts to generate a secondary electrolytic film. The oxide film produced by aluminum electrolytic coloring exhibits improved weather resistance, lightfastness, and abrasion resistance compared to dyed films. However, aluminum electrolytic coloring has a noticeable limitation, which is the monotonous color range. Currently, the most commonly used color achieved through electrolytic coloring is black. A few other colors such as antique bronze, golden yellow, and dark red can also be achieved, but the overall color and glossiness are far inferior to dyed films.
The process flow of Aluminum electrolytic coloring
Aluminum Electrolytic Coloring Process:
- Aluminum workpiece
- Hanging fixture
- Degreasing
- Water rinsing
- Alkali etching
- Water rinsing
- Polishing
- Water rinsing
- Anodizing
- Water rinsing
- Deionized water rinsing
- Aluminum Electrolytic coloring
- Water rinsing
- Deionized water rinsing
- Sealing
- Water rinsing
- Air blowing
- Drying
- Unhanging fixture
- Quality inspection
- Packaging
- Shipment.
Aluminum Electrolytic Coloring Production Equipment Display
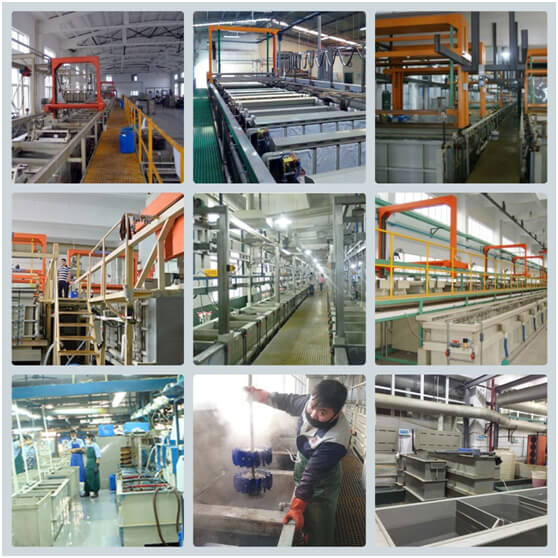
Aluminum Electrolytic Coloring Inspection Equipment Display
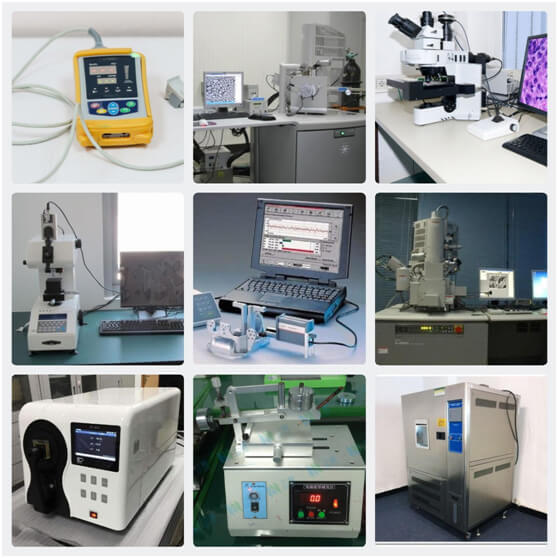
Aluminum Electrolytic Coloring Sample Cases
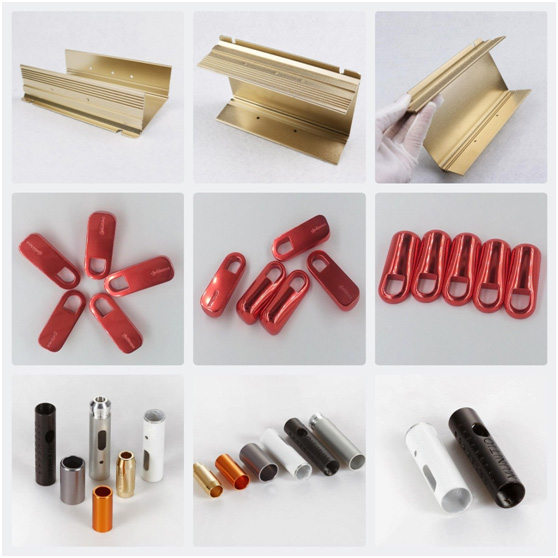
Exposure Developing Anodized Oxidation
Brief introduction to Exposure developing anodized oxidation
Ink protection with two dyeing steps: After polishing the workpiece, the logo area is protected with ink during exposure development. Then, sandblasting is performed, followed by the first round of anodizing, dyeing, and sealing. The logo protection ink is cleaned, and the second round of oxidation and dyeing is carried out (if the logo area requires color), followed by sealing. Two rounds of anodizing and dyeing: After the first round of anodizing, dyeing, and sealing, the oxide and dye film layer is removed through CNC machining, and then the second round of anodizing and dyeing is performed to achieve a two-color effect. Currently, the first method is commonly used.
Exposure development anodizing process flow
- Workpiece polishing to a mirror finish
- Spray photosensitive ink
- Exposure development
- Removal of ink from non-protected areas
- Sandblasting
- First round of anodizing
- Laser engraving of conductive areas
- CNC machining of areas requiring a second round of anodizing
- Second round of anodizing.
- Workpiece polishing to a mirror finish
- Grinding
- Screen printing
- UV ink spraying
- Sandblasting
- First round of anodizing
- Ink removal
- Second round of oxidation.
For the second round of anodizing process:
- Cleaning
- Nitric acid neutralization
- Triple water rinse
- Anodizing
- Water rinse
- Nitric acid neutralization
- Double water rinse
- Dyeing
- Double water rinse
- Sealing
- Double distilled water rinse
- Drying
- Double distilled water rinse
- Drying
- Hanging Down.
Exhibition of exposure development anodizing production equipment
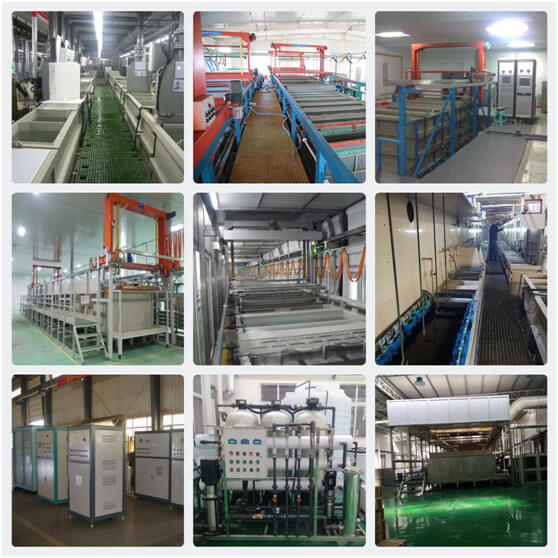
Detection equipment display for exposure development anodizing.
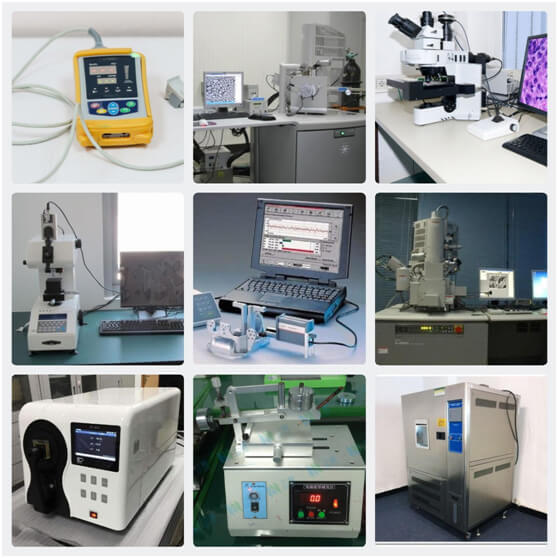
Exposure development anodizing sample cases.
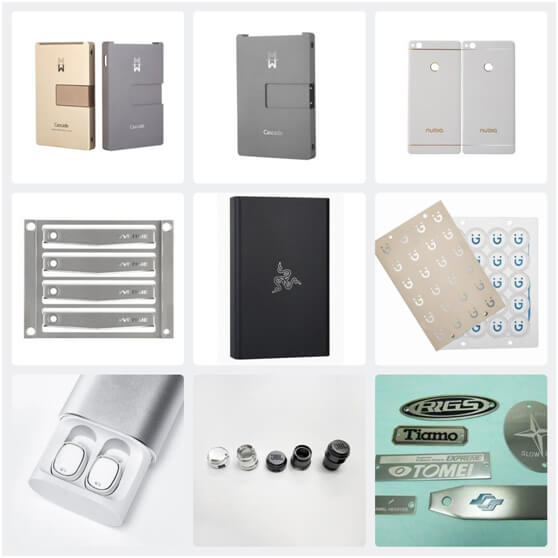
Hard Anodizing.
Brief Introduction to Hard Anodizing Process
Sulfuric Acid Hard Anodizing: This method uses sulfuric acid as the electrolyte to produce a hard and durable oxide film on the surface of the workpiece. It is the most commonly used and referred to method when talking about Hard Anodizing unless otherwise specified. Oxalic Acid Hard Anodizing: In this method, oxalic acid is used as the electrolyte to achieve a hard anodized coating with enhanced wear resistance. Mixed Acid Hard Anodizing: This method involves the use of a mixture of acids, such as sulfuric acid and oxalic acid, to achieve the desired hardness and wear resistance of the anodized coating.
These different methods of Hard Anodizing are employed based on specific requirements and considerations for the workpiece and its intended application. However, unless otherwise specified, the term “Hard Anodizing” typically refers to the sulfuric acid hard anodizing method.
Common Base Materials for Hard Anodizing:
For deformable aluminum alloys with a copper content greater than 5% or a silicon content greater than 8%, as well as high-silicon die-cast aluminum alloys, special measures need to be taken during hard anodizing. For example, to prevent burn damage to aluminum alloys during the anodizing process, an electrolyte solution containing 385 g/L sulfuric acid and 15 g/L oxalic acid can be used, and the current density should be increased to 2.5 A/dm² or higher for 2XXX series aluminum alloys.
Thickness of Hard Anodized Coating:
It should also be noted that since the hard anodized coating is a two-sided growth process, achieving a 100 μm coating thickness actually means adding 50 μm to each side.
Furthermore, it should be noted that the thicker the hard anodized coating, the lower the microhardness of the outer layer (the oxide layer becomes more brittle), and the roughness of the coating surface increases.
Functions of Hard Anodizing:
Excellent thermal insulation coating: Melting point is 2050°C, with poor thermal conductivity.
Good insulation properties: High resistance, with breakdown voltage of up to 2000V.
Strong adhesion of the coating: Approximately 50% of the generated oxide film penetrates into the aluminum alloy, and the remaining 50% adheres to the surface of the aluminum alloy.
Extremely high corrosion resistance: It exhibits excellent corrosion resistance in industrial and marine climates.
Colors of Hard Anodized Coatings:
Conductive Oxidation Process Flow
Hard Anodizing Process Flow
- Aluminum Workpiece
- Hanging Fixture
- Degreasing/Chemical Oil Removal
- Cold Water Rinse
- Alkali Etching
- Water Rinse
- Polishing/Electrolytic Polishing
- Water Rinse
- Hard Anodizing
- Hot Water Rinse
- Deionized Water Rinse
- Dyeing or Electrolytic Coloring
- Water Rinse
- Deionized Water Rinse
- Sealing
- Cold Water Rinse
- Remove Hanging Fixture
- Air Blow
- Drying
- Quality Inspection
- Lubrication
- Packaging
- Shipping;
Note 3
A common issue that arises during the production of the darkest black hard anodizing is the presence of water spots. This is caused by residual moisture in some through-holes or blind holes of the workpiece that was not completely blown dry (usually due to impatience and inadequate drying). Therefore, when producing the darkest black anodizing, it is important to ensure that the moisture is completely removed by thorough blowing and, if possible, additional drying in an oven. Once water spots remain, they cannot be easily removed after some time, resulting in the need for rework, which may affect the dimensional tolerances of the workpiece and should be avoided if possible.
Note 1
Note 2
Display of Equipment for Hard Anodizing Production
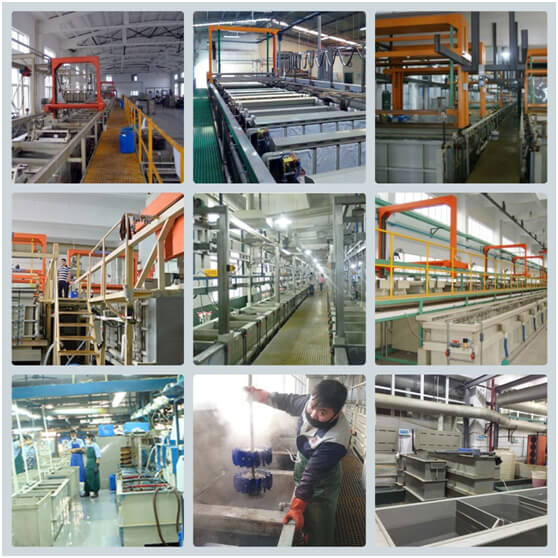
In addition, the supporting facilities include an automatic sandblasting machine and 15 manual sandblasting machines. There are also resources available for grinding, brushing, and high-polishing processes through outsourcing. The daily average production capacity exceeds one million units, ensuring abundant production capacity.
Display of Equipment for Hard Anodizing Inspection
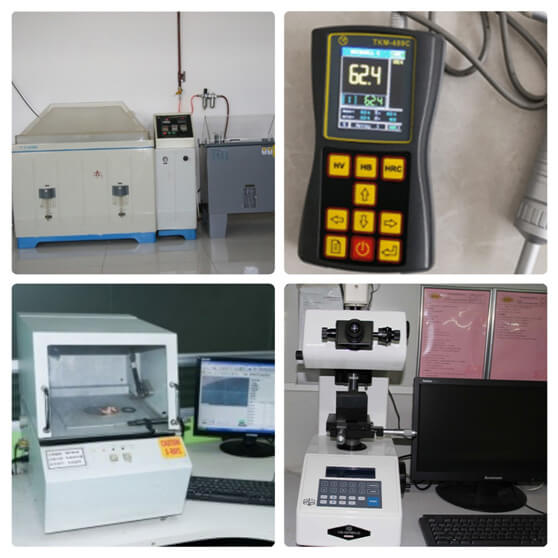
- Portable Coating Thickness Gauge: A handheld coating thickness gauge is used to measure the thickness of the anodized layer. It provides quick and non-destructive measurements, allowing for on-site inspection and verification of coating thickness.
- X-ray Coating Thickness Gauge: An X-ray coating thickness gauge utilizes X-ray fluorescence (XRF) technology to measure the thickness of the anodized layer. It offers high precision and accuracy, particularly for thicker coatings.
- Salt Spray Testing Machine: A salt spray testing machine, also known as a salt fog chamber, is employed to simulate corrosive environments. It exposes the anodized parts to a saltwater mist, assessing their resistance to corrosion over a specified period.
- Hardness Tester: A hardness tester measures the hardness of the anodized surface. Various methods, such as Rockwell or Vickers hardness testing, can be utilized to evaluate the coating’s hardness and mechanical properties.
Sample Cases of Hard Anodizing
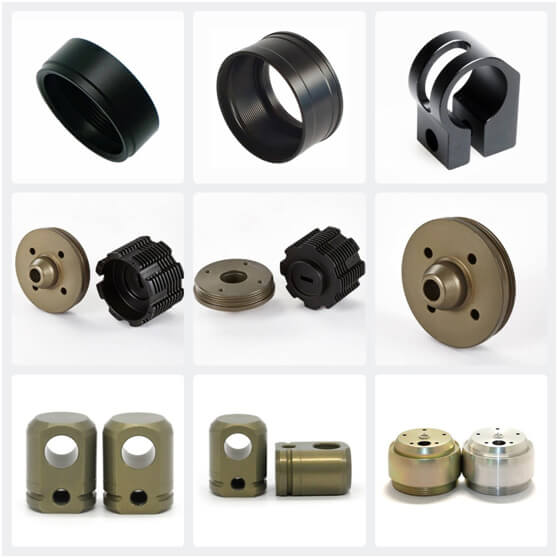
Anodizing Large Parts
Brief Introduction to the Process of Anodizing Large Parts
The functions of anodizing large parts are as follows:
The common base materials for anodizing large parts:
Film thickness for anodizing large parts:
Colors for anodizing large parts:
Process Flow for Anodizing Large Parts.
The process flow of color anodization:
- Aluminum workpiece
- Hanging fixture installation
- Degreasing
- Rinsing
- Alkali Etching
- Alkaline etching
- Rinsing
- Polishing
- Rinsing
- Anodizing
- Rinsing
- Deionized water rinse
- Rinsing
- Air blowing
- Drying
- Fixture removal
- Quality inspection
- Packaging
- Shipment.
Display of Production Equipment for Anodizing Large Parts
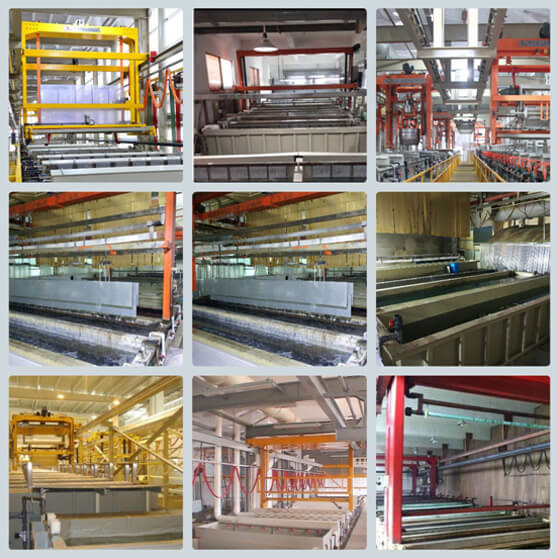
Display of Inspection Equipment for Anodizing Large Parts.
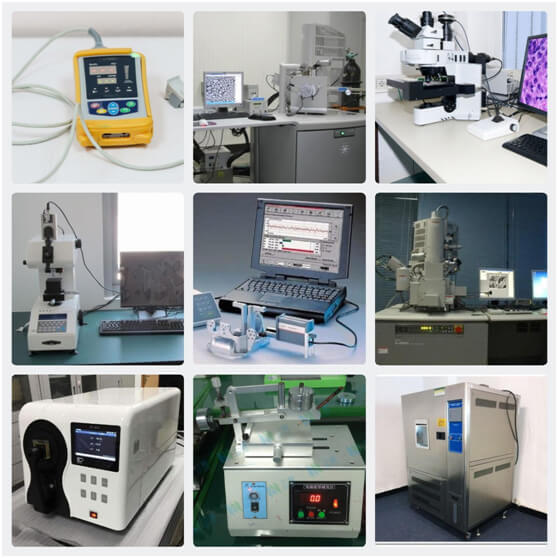
Sample Cases of Anodizing Large Parts.
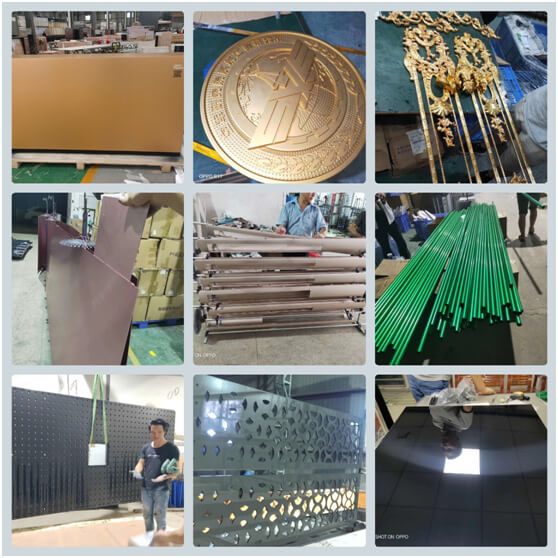
Microarc Oxidation
Brief Introduction to Microarc Oxidation Process
Workpieces treated with micro-arc oxidation exhibit significantly improved corrosion resistance and wear resistance compared to traditional anodized coatings, making them widely used in marine vessels, aerospace components, and other applications.
Common Substrates for Microarc Oxidation:
Thickness of Microarc Oxidation Coatings:
Microarc Oxidation Colors:
Effects of Microarc Oxidation:
Significantly increased surface hardness of materials, with microhardness ranging from 1000 to 2000 HV and up to 3000 HV, comparable to hard alloys and much higher than the hardness of high-carbon steel, high-alloy steel, and high-speed tool steel after heat treatment.
Good wear resistance.
Excellent heat resistance and corrosion resistance. This fundamentally overcomes the shortcomings of aluminum, magnesium, and titanium alloy materials and thus has broad application prospects.
Good insulation properties, with insulation resistance up to 100 MΩ.
Environmentally friendly electrolyte solution that meets environmental emission requirements.
Stable and reliable process with simple equipment.
The reaction takes place at room temperature, making it convenient to operate and easy to master.
The ceramic coating grows in situ on the substrate, ensuring strong adhesion and a uniform and dense ceramic layer.
Microarc Oxidation (MAO) Process Flow
- Workpiece
- Hanging Fixture
- Water Rinse
- Degreasing/Deoiling
- Hot Water Rinse
- Microarc Oxidation (MAO)
- Pure Water Rinse
- Air Blow
- Drying
- Unhanging Fixture
- Quality Inspection
- Packaging
- Shipping;
Note 1
Note 2
Note 3
Microarc Oxidation (MAO) Production Equipment Showcase
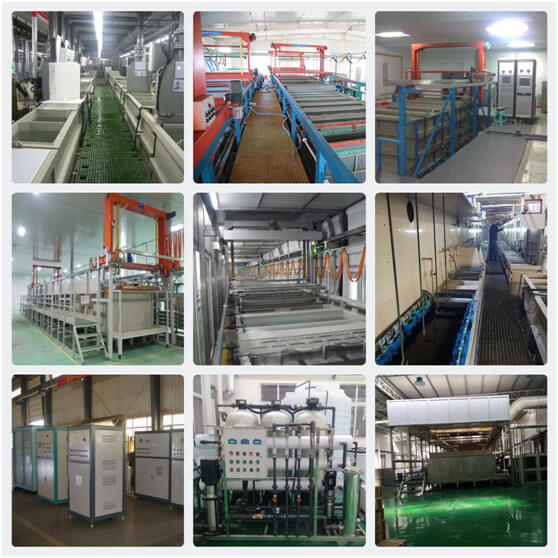
The micro-arc oxidation production line showcases the capability to perform micro-arc oxidation on materials such as aluminum alloys, magnesium alloys, titanium alloys, etc., producing gray, brown, black, and coffee-colored coatings.
Microarc Oxidation Testing Equipment Showcase
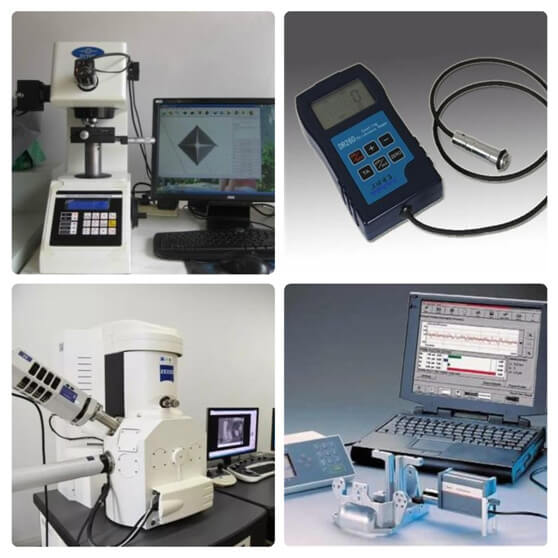
To measure the thickness of the oxide ceramic coatings, a German handheld thickness gauge (such as HUATEC) is used for precise thickness characterization. For the measurement of surface microhardness, a microhardness tester is employed to assess the hardness of the coating surface.
The surface, cross-section morphology, and microstructure of the micro-arc oxidation ceramic coatings are examined using an environmental scanning electron microscope (SEM). This technique allows for detailed inspection and characterization of the coating’s surface features and microstructure.
These testing equipment and techniques provide valuable information regarding the thickness, hardness, morphology, composition, and surface roughness of micro-arc oxidation coatings. They help ensure the quality and performance of the coatings and assist in meeting the required specifications for different applications.
Microarc Oxidation Sample Cases
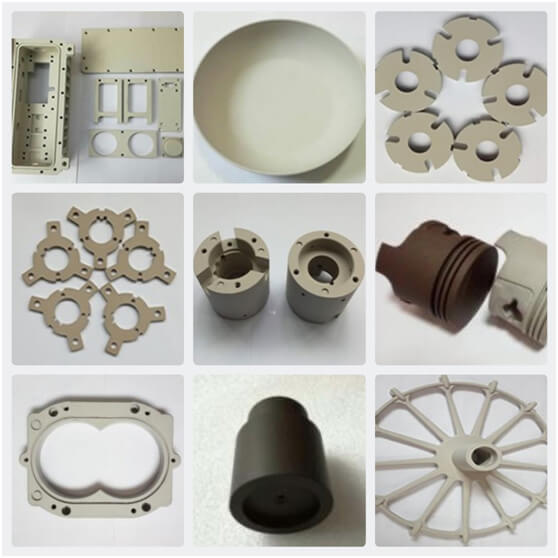
Aluminum Alloy: A6061-T6
Surface Finish: Smooth
The thickness of Ceramic Coating: 25 μm
Performance: Enhanced hardness, wear resistance, and corrosion resistance
Magnesium Alloy: AZ91D
Surface Finish: Textured
The thickness of Ceramic Coating: 30 μm
Performance: Improved surface hardness, wear resistance, and anti-corrosion properties
Titanium Alloy: Ti6Al4V
Color: Black
The thickness of Ceramic Coating: 35 μm
Performance: Increased surface hardness, wear resistance, and high-temperature resistance
Aluminum Alloy: AA7075
Surface Finish: Fine grain
The thickness of Ceramic Coating: 28 μm
Performance: Enhanced hardness, wear resistance, and corrosion resistance
Precision Anodizing
Brief Introduction of the precision anodizing process
When conducting precision anodizing, it is essential to consider the allowance dimensions of the workpiece. Additionally, careful consideration should be given to the impact of rework and de-anodizing on the dimensional integrity of the workpiece.
Precision anodizing process.
- Aluminum workpiece
- Hanging fixture installation
- Degreasing
- Rinsing
- Alkali etching
- Rinsing
- Polishing
- Rinsing
- Anodizing
- Rinsing
- Deionized water rinsing
- Dyeing or electrolytic coloring
- Rinsing
- Deionized water rinsing
- Sealing
- Rinsing
- Removal from hanging fixture
- Drying
- Inspection
- Inspection
- Packaging
- Shipment.
Precision anodizing production equipment showcase.
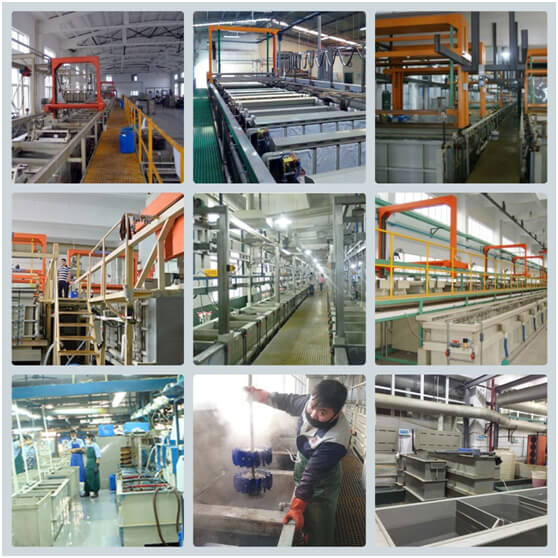
Precision anodizing production equipment display.
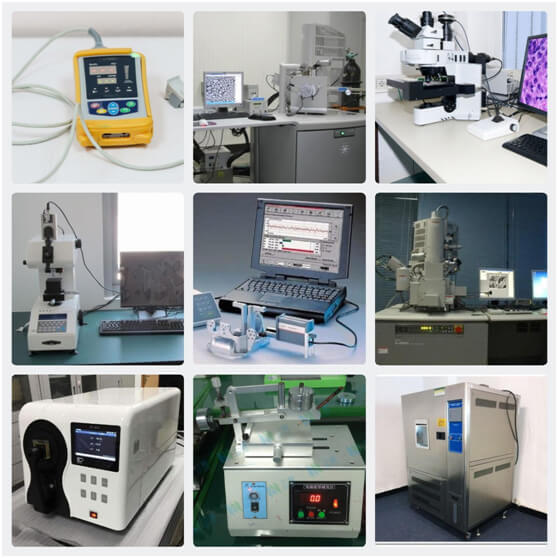
Precision anodizing sample cases.
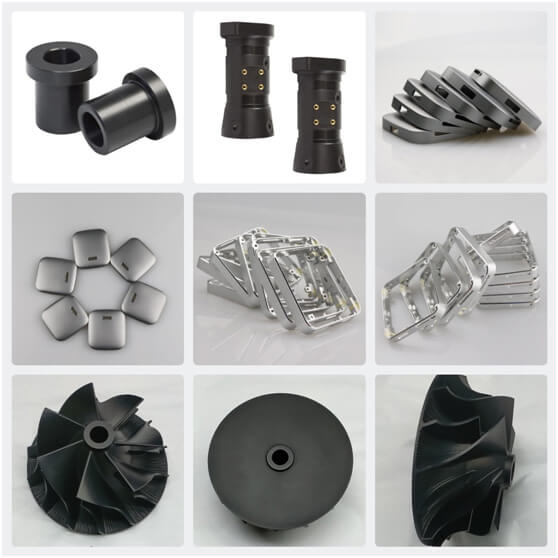
Titanium anodizing
Brief Introduction to the Titanium Anodizing Process
What colors can be achieved through titanium anodizing?

Titanium anodizing process
- Degreasing (with strong alkaline degreaser)
- Water rinsing
- Initial acid etching (hydrofluoric acid solution)
- Water rinsing
- Secondary acid etching (hydrofluoric acid + hydrogen peroxide solution)
- Water rinsing
- Anodizing (constant voltage electrolysis in phosphoric acid solution)
- Water rinsing
- Sealing
- Drying.
Degreasing
Initial acid etching
Secondary acid etching
Anodizing
Sealing
Drying
Exhibition of Production Equipment for Titanium anodizing
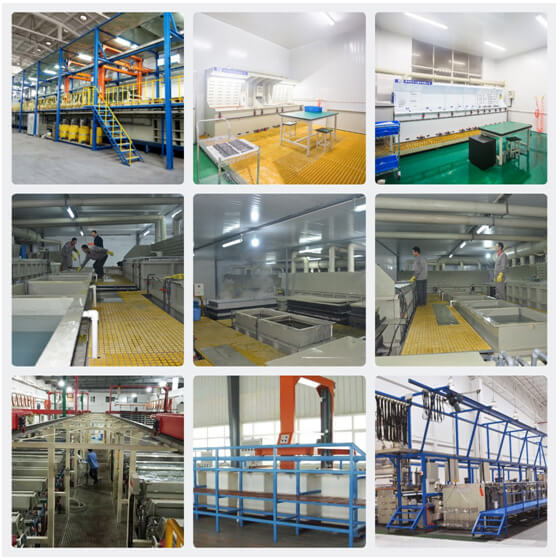
Titanium Anodizing Detection Equipment Show.
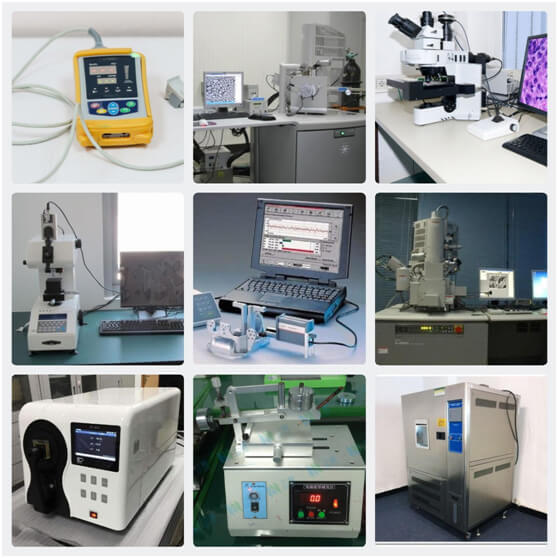
Titanium anodized sample case
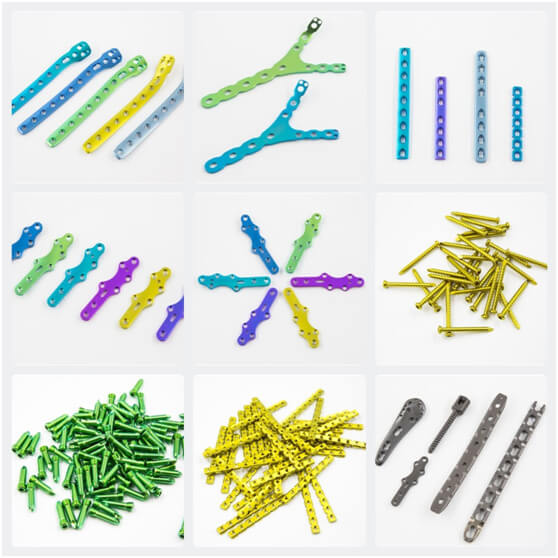
Two-tone anodizing/Secondary anodizing
Introduction to Two-Tone Anodizing Process
The process typically involves two main steps. Firstly, the workpiece undergoes the primary anodizing process, where a protective oxide layer is formed on its surface through an electrolytic reaction. This primary anodizing step provides a base layer of uniform and corrosion-resistant oxide.
After the primary anodizing, the workpiece is prepared for the secondary anodizing and coloring step. There are two common methods used to achieve the two-tone effect.
The first method involves mechanical polishing. Areas of the workpiece that require a different color are carefully polished using CNC or other computer-controlled tools to remove the primary oxide layer. This creates a clean surface for the subsequent anodizing and coloring process. The polished areas are then subjected to a secondary anodizing step, where a new oxide layer is formed. This second oxide layer is porous and provides a suitable base for dyeing or electrolytic coloring. Different dyes or coloring agents are applied to the porous oxide, resulting in the desired two-tone appearance.
The second method involves masking. Specific areas of the workpiece that need a different color are masked or covered before the primary anodizing process. The masked areas remain unoxidized during the primary anodizing step. Afterward, the masking is removed, and the entire workpiece undergoes a secondary anodizing process. The previously masked areas now develop a new oxide layer during the secondary anodizing. These areas are then dyed or colored separately, resulting in the desired two-tone effect.
It is important to note that achieving a consistent texture and surface finish between the two colors can be challenging, especially on complex 3D structures. Additionally, the masking method may result in jagged edges or serrations along the masked boundaries, which can affect the overall appearance. Two-tone anodizing finds applications in various industries, including architecture, automotive, electronics, and fashion, where both functionality and aesthetics are essential.
Two-Tone Anodizing Process Flow
- Aluminum Workpiece
- Hanging Fixture
- Degreasing
- Rinse
- Alkaline Etching
- Rinse
- Brightening
- Rinse
- Primary Anodizing
- Rinse
- Deionized Water Rinse
- Primary Dyeing or Electrolytic Coloring
- Rinse
- Deionized Water Rinse
- Sealing
- Masking
- Curing
- Deoxidation
- Chemical Polishing
- Secondary Anodizing
- Rinse
- Secondary Dyeing or Electrolytic Coloring
- Rinse
- Sealing
- Ink Removal
- Rinse
- Blow Dry
- Drying Oven
- Unhanging Fixture
- Blow Dry
- Drying Oven
- Quality Inspection
- Packaging
- Shipping.
Display of Two-Tone Anodizing Production Equipment
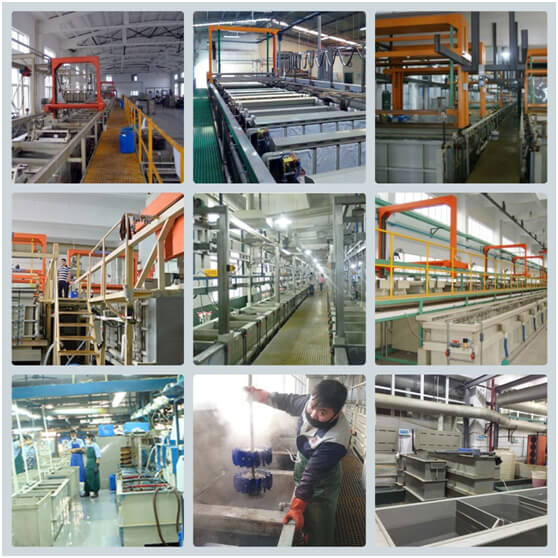
Two-Tone Anodizing Production Line
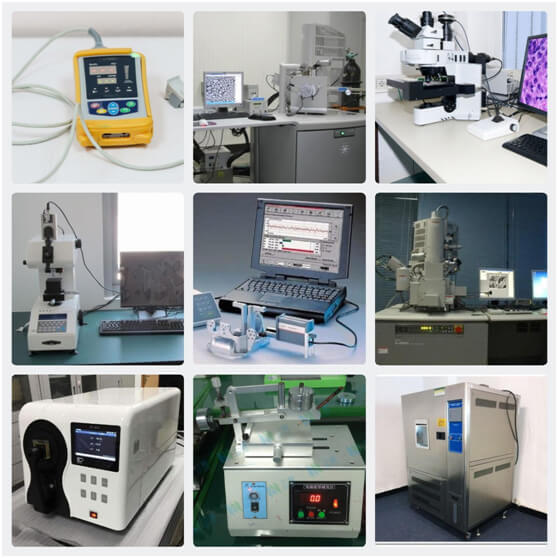
The inspection equipment used for two-tone anodizing primarily includes:
Oxide layer thickness gauge
Colorimeter
Gloss meter
Roughness tester
Pencil hardness tester
UV tester
Constant temperature and humidity chamber
High-low temperature tester
Salt spray chamber
Vibration and wear resistance tester
Examples of Two-Tone Anodizing Sample Cases
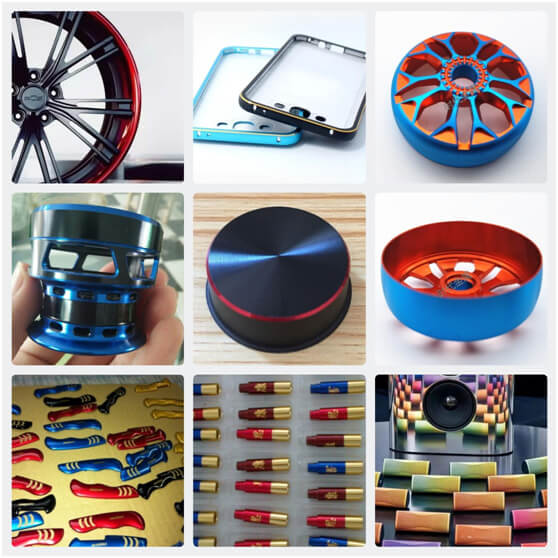
Free Sample
Explore Other Services

QPQ Coating
Phosphating is a process in which a workpiece is treated in a phosphoric acid salt solution containing manganese, iron, and zinc to form a layer of insoluble phosphate film on

Gold Plating
Bead Blasting, also known as abrasive blasting or sandblasting,typically involves the use of compressed air to propel abrasive particles from a nozzle and direct them onto the surface to be

Anodizing
Aluminum Anodized Finish (Aluminum Anodizing) Brief introduction to the aluminum anodizing process Anodic oxidation, also known as aluminum anodizing, refers to the electrochemical oxidation of metals or alloys. It is