Dacromet Coating
Dacromet Coating
Colorful Dacromet Coating Processing/MAGNI Processing/Geomet/ZINTEK Process Introduction
The surface treatment process of MAGNI has the following characteristics
Advantages of Zintek Processing
No hydrogen embrittlement issues, no need for additional dehydrogenation heat treatment;
Suitable for bolts with high tension (PC 10.9 and above), even thin coatings can provide sufficient corrosion protection (8-12um) (>1000h NSS);
Coating is chromium-free and non-toxic;
Precise control of torque tension characteristics can be achieved by using sealant containing lubricant;
Good chemical stability;
No wastewater treatment issues, a clean production technology;
Low cost (simple process).
Disadvantages of Zintek Processing
Very small parts tend to stick together;
It is difficult to coat for the precise threads;
Surface wear during transportation should be carefully managed as it may cause a decrease in surface appearance and corrosion resistance. The perfect anti-corrosion performance cannot conceal its low hardness and poor abrasion resistance. The advantages and disadvantages of the Dacromet coating process are as follows:
Dacromet Finish Processing Advantages
Superb corrosion resistance: The thickness of the Dacromet coating is only 4-8 μm, but its rust prevention effect is 7-10 times higher than that of traditional electroplating zinc, hot-dip galvanizing, or coating method. Standard parts and pipe fittings treated with Dacromet finish processing have passed the salt spray test for more than 1200 hours without showing red rust.
No hydrogen embrittlement: The Dacromet finish processing technology eliminates hydrogen embrittlement, making it suitable for coating stress parts.
High heat resistance: Dacromet finish can resist high-temperature corrosion, and the heat resistance temperature can reach over 300℃. Traditional galvanizing technology peels and scrapes off at 100℃.
Good adhesion and re-compatibility: The Dacromet coating has excellent adhesion to the metal substrate and strong adhesion to other additional coatings. The treated parts are easy to spray and color, and the adhesion to organic coatings even exceeds that of phosphating films.
Good penetration: Due to the electrostatic shielding effect, it is difficult to electroplate zinc on the deep holes, narrow gaps, and inner walls of pipe fittings. Therefore, these parts cannot be protected by electroplating.
No pollution or public hazards: During the entire production and processing of Dacromet finish, as well as the coating of parts, there is no wastewater or exhaust gas that pollutes the environment. There is no need for waste treatment, reducing the processing cost.
Disadvantages of Dacromet Processing
Some Dacromet coatings contain harmful chromium ions to the environment and human health, especially hexavalent chromium ions that have carcinogenic effects.
Dacromet finish requires high sintering temperatures and long processing times, resulting in high energy consumption.
The surface hardness and wear resistance of Dacromet coatings are not high, and the products are not suitable for contact and connection with copper, magnesium, nickel, and stainless steel components, as they may cause contact corrosion, affecting the surface quality and anti-corrosive performance of the products.
Dacromet coatings have a limited range of surface colors, typically silver-white or silver-gray, which may not meet the personalized needs of the automotive industry. However, post-treatment or composite coatings can be applied to obtain different colors, improving the decorative and matching properties of heavy-duty automotive components.
Dacromet coatings do not exhibit good electrical conductivity, making them unsuitable for use in electrical components, such as grounding bolts.
Common Materials Used for Dacromet Coating
Dacromet coating has a wide range of applications and commonly used substrate materials include steel/stainless steel, iron/ cast iron, aluminum/aluminum alloy, zinc alloy, and other structural components. It can also be used for sintered metals and special surface treatments.
Membrane Thickness and Salt Spray Test of Dacromet Coating
The typical membrane thickness of Dacromet coating is 4-8μm, and it can withstand a neutral salt spray test for over 1200 hours!
The Surface Color of Dacromet Coating
The common colors of Dacromet coating are silver-white and silver-gray; various colored effects such as black, yellow, red, blue, green, etc. can be achieved through special post-treatment.
Dacromet/Geomet Coating Process
- Degreasing with neutral cleaning agent
- Surface oxide layer treatment by shot blasting machine (shot blasting and rust removal)
- Multi-element alloy co-perfusion furnace co-perfusion
- Cooling
- Shot blasting
- Passivation
- Immersion or spraying with Dacromet finish solution
- Sintering and curing oxidation reduction at around 300℃
- Cooling
- Pre-plating alkaline copper
- Acid bright copper (optional)
- Bright nickel
- Chrome plating
- Degreasing and cleaning
- Shot blasting and rust removal
- Immersion coating
- Film formation by baking
- Cooling
- Second immersion coating
- Baking cycle
- Cooling
Note 1
The rust removal process in the Dacromet finish pretreatment is different from the general pretreatment method for painting, which uses acid pickling for rust removal. This is because most of the parts treated with Dacromet are high-strength bolts, nuts, and high-strength stamped parts, and hydrogen embrittlement will occur after acid pickling, which will affect the product quality. (Note: In the case of not considering hydrogen embrittlement, acid pickling is also used for the Dacromet pretreatment, especially for cabinets, control cabinet panels, etc., but special attention should be paid to not bringing the acid pickling residue into the coating tank to avoid damaging the Dacromet solution.)
Note 2
General phosphating cannot be used as the substrate treatment for Dacromet because the Dacromet coating needs to be cured at a high temperature of 300℃ for a long time, and the crystal water in the phosphating film will evaporate, causing the Dacromet coating to crack and affecting the adhesion and corrosion resistance of the coating. Therefore, mechanical shot blasting is usually used for rust removal in the Dacromet pretreatment before coating.
Note 3
The Dacromet coating method adopts different coating methods according to the different requirements of the workpiece and product quality, generally divided into three methods: immersion coating, spray coating, and brush coating.
Note 4
The baking and curing of Dacromet are generally divided into two stages: the pre-baking zone and the sintering zone. The pre-baking zone is generally around 10 minutes, and the temperature is controlled at 100-150℃. If the temperature is too low, the volatilization of moisture is insufficient, which will affect the regular arrangement of the zinc and aluminum layers of the workpiece in the high-temperature zone, affecting the appearance, adhesion, and corrosion resistance of the final coating. If the temperature is too high, the volatilization of moisture is too fast, which is not conducive to the leveling of the coating, affecting the uniformity and adhesion of the coating. The baking zone is generally around 20 minutes, and the temperature is controlled at 300-340℃. If the temperature is too low, the conversion of hexavalent chromium in the coating to trivalent chromium is insufficient, the trivalent chromium mesh structure between the zinc and aluminum layers is poor, the carbonization of organic components is insufficient, and the trivalent chromium mesh structure is unreasonable, resulting in poor adhesion of the coating. Moreover, hexavalent chromium is prone to lose under the condition of water, and the self-repairing ability of the coating is reduced, leading to a decline in corrosion resistance. If the temperature is too high, too much hexavalent chromium in the coating will be converted to trivalent chromium, and the content of soluble hexavalent chromium in the coating will decrease, which also affects the corrosion resistance of the coating.
Dacromet Processing Fee Explanation
Dacromet Finish Processing Production Equipment Showcase
Dip tanks
Dip tanks are used to immerse the material in a solution of zinc and aluminum-based coatings. The material is submerged into the solution, and the coating is applied evenly across the surface of the material.
Spraying equipment
Spraying equipment can be used to apply the Dacromet coating to the surface of the material. This method is often used for smaller parts or for areas that are difficult to reach with dip tanks.
Drying ovens
After the material has been coated with Dacromet met, it needs to be cured at a specific temperature to ensure that the coating adheres properly to the surface of the material. Drying ovens are used to control the temperature and humidity of the curing process.
Testing equipment
Quality control is critical in the production of Dacromet coatings. Testing equipment, such as salt spray testers, can be used to evaluate the effectiveness of the coating in preventing corrosion.
Handling equipment
Dacromet met-coated materials can be heavy and bulky, so handling equipment such as cranes, hoists, and conveyors are often used to move the material through the production process.
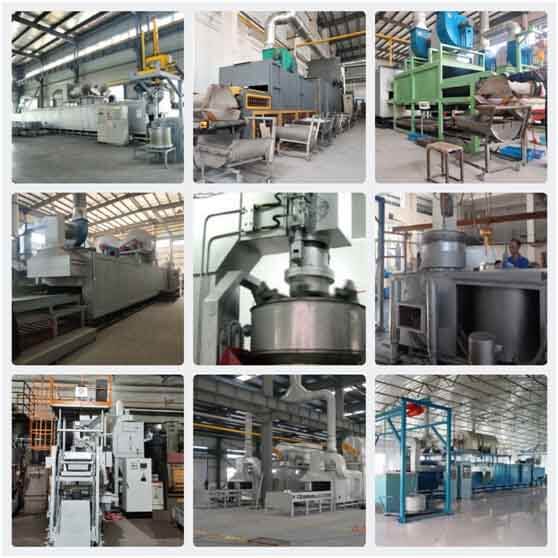
DacrometCoating DetectingInstrument
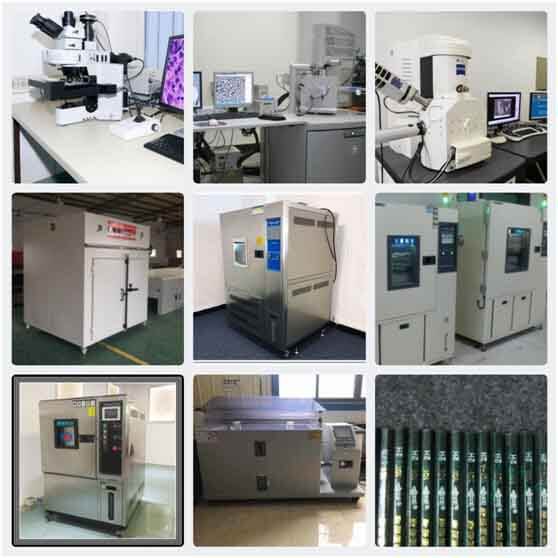
Surface Inspection
Place the coated sample under sunlight. A properly coated Dakro coating should appear gray in color, and the surface should be free from any protrusions, bubbles, or cracks, and should have a smooth texture. The surface coating should be uniform without any localized thickening. Additionally, the coating should not change color, or have any missing areas, pitting, or impurities.
Resistance to ammonia water of the coating
Determine the curing of the coating during the production process; select the workpiece that has just come out of the production line at room temperature, drip 1 to 4 drops of concentrated ammonia water on the coating, and keep it for 15-30 minutes. If a yellow color appears, it is qualified, indicating that it has been baked thoroughly. However, it should be noted that when the workpiece is over-baked, yellowing may also occur during the ammonia water test, so the test should be analyzed and judged in combination with the baking and curing of the workpiece, and cannot be used as the only basis for judging product quality.
Coating hardness
Hardness is one of the important mechanical properties of the coating, which involves the wear resistance and service life of the coated workpiece in use. Since the hardness of the Dacromet coating is very low, the pencil hardness test method is used, and the hardness is between 1H and 3H. Some manufacturers claim to provide 5H.
Coating Weight and Coating Thickness Testing:
This is mainly for checking the quality of the coating on the workpiece and for cost accounting purposes. Generally, the thickness of the coating is tested using the metallographic microscope method according to the requirements of GB T6462. Dacromet testing standards classify different grades based on the weight and thickness of the surface coating. Two commonly used test methods are as follows:
Solution Weight Method:
Select a sample with a weight greater than 50g (with a surface coating) and use a high-precision electronic balance or weighing scale (1mg accuracy) to weigh the sample. Record the weight as W1 (in milligrams). Then place the sample in an aqueous solution with a 20% NaOH content and heat the solution to 70-80°C. Leave it for approximately 10 minutes to dissolve the surface coating (zinc-chromium coating). After the coating has dissolved, remove the sample, rinse it thoroughly with water, allow it to air dry, and then weigh it again. This will give you the weight of the sample without the coating, denoted as W2 (in milligrams). Measure the surface area of the workpiece, denoted as S (in square decimeters). Then use the following formula to calculate the coating weight (in milligrams per square decimeter): Coating Weight (Wmg/dm2) = (Weight 1 - Weight 2) / S
Metallographic Microscopy Method
Metallographic microscopy method is one of the physical methods. It involves using conventional metallographic techniques to prepare cross-sectional samples of the tested coating. The cross-sectional image of the tested coating is then observed under a metallographic microscope equipped with a measuring microscope, allowing for direct measurement of the average thickness of the coating at specific locations. This method offers high measurement accuracy, a sufficient basis for analysis, and intuitive judgment based on directly measuring the profile thickness of the coating at a certain magnification. However, this method is more complex in sample preparation and is generally used for verifying and arbitrating coatings with strict thickness requirements or when there are disputes over the results obtained from other thickness measurement methods.
Method Principle
The metallographic method for thickness measurement involves observing and measuring the cross-sectional thickness of the tested coating using a metallographic microscope with a specific magnification and a measuring microscope. In order to meet the requirements of metallographic microscope examination, the tested coating should be cut, edge-protected, embedded, ground, polished, and chemically etched prior to thickness measurement. The following steps are involved:
Cut a section of the coating perpendicular to the substrate using a blade.
Immerse the coating section in a special resin.
After the coating is dried, perform edge trimming.
Observe and take photographs under a microscope.
Take measurements and determine the coating thickness from the photographs.
Convert the measured thickness to the actual coating thickness based on the magnification used.
Coating Adhesion Test
According to the Chinese standard GB/TS 270-1985, the adhesion of the coating can be tested using a tape adhesion test. This test method applies a vertical and uniform tensile force to the bond surface of the specimen at a specified speed to determine the force required to cause adhesion failure between coatings or between the coating and the substrate. Adhesion is typically expressed as the force per unit area. The test results require that the coating should not be peeled off or expose the substrate after the test. However, within the allowable range, discoloration and adhesion of zinc-aluminum powder may occur.
Rapid detection of the ammonium nitrate method for the coating
commonly used in production, the coating quality can be quickly tested by this method in three hours, which is equivalent to 1000 hours of salt spray test.
Coating Water Resistance Test:
To perform the coating water resistance test, first prepare deionized water at a temperature of 40°C±1°C. Then immerse the test samples in the deionized water continuously for 240 hours. After 240 hours, remove the samples and allow them to air dry at ambient temperature, then conduct the adhesion strength test. The test results must meet the requirements of the adhesion strength test data. Subsequently, perform the adhesion test by removing the samples from the deionized water and allowing them to stand for 2 hours before conducting the experiment. Finally, the requirement for the water resistance test is that the coating should not be peeled off, and the substrate should not be exposed.
Coating Humidity Resistance Test
To conduct the humidity resistance test, a humidity test chamber must be equipped, as the test conditions have specific requirements for the temperature and humidity of the test chamber. The standard test method is as follows: Set the temperature of the humidity test chamber to 40°C±2°C and the relative humidity to 95%±3%. Then vertically fix the samples in the fixture and suspend them inside the humidity test chamber. If testing multiple samples, they should not come into contact with each other. Once the temperature and humidity in the humidity test chamber reach the set values, start the timer. Conduct a test every 48 hours, with an additional test every 72 hours after two checks, and the samples should be repositioned after each check. After 240 hours, perform a final check. Conduct the test continuously for 240 hours, with no red rust, blistering, or coating detachment during this period. Based on the standard requirements, the humidity resistance test should only be conducted on Dacromet coatings that have achieved grade 3 or 4, and after the Dacromet coating has undergone a 240-hour test, there should be no red rust spots on the surface.
Test for Heat Corrosion Resistance of Coatings
The Dacromet sample is placed in a high-temperature oven at 300°C for a certain period, and then compared with a standard sample to observe the changes in the coating to judge its heat corrosion resistance. This test is only conducted when users request heat resistance performance of coatings.
Test for Mechanical Friction Resistance of Coatings
The requirement is that the Dacromet coating still has good corrosion resistance after several loading and unloading cycles. The operating method is to randomly select several sets of bolts and nuts, screw the nut onto the bolt and then unscrew it, repeating this process ten times. Then immerse the nuts and bolts in a 3% sodium chloride solution and observe the changes in the mechanically rubbed coating. Normally, the coating will not change until ten days after the test.
Test for Salt Spray Resistance of Coatings
The test equipment should meet the standard requirements.Prepare a sodium chloride solution with a concentration of 50±5g/L using distilled water. Measure the pH value of the test solution between 6.5 and 7.2 at 25°C. Start the equipment and begin the experiment after 20 minutes. The temperature inside the spray chamber should be maintained at 35±2°C. Spray for 15 minutes at 45-minute intervals. Conduct a visual inspection of the equipment every 48 hours to check for normal operation. If everything is normal, conduct inspections at 240, 360, and 480-hour intervals. It is important to note that the test samples should be placed at an incline of 60 to 75 degrees from the horizontal line, without touching each other. Additionally, the solution dripping from above should not fall from one component to another.
After undergoing rigorous salt spray testing, the appearance of red rust on the surface coating must be recorded for DACROMET coatings. Typically, a record sheet is used to document the experimental data ranging from 120 to 1000 hours. The results obtained can be classified into four levels to assess the severity of the red rust appearance after different durations of salt spray testing.
The standard also specifies the method of extracting samples:
For each type of test, three random samples should be taken from the same batch of products for testing. If any of the samples fail the test, another three samples should be randomly selected and tested again. If any of these samples fail, the batch of products is considered to be disqualified.
For components or parts with a weight exceeding 150 grams, a portion of the workpiece should be cut and used as a sample for testing. To prevent the exposed steel substrate at the cutting edge from affecting the test results, protective coatings such as paint, wax or tape should be applied. The same method can also be used to prepare samples for parts with complex shapes where the surface area is difficult to determine.
In addition to the five coating tests mentioned in the above standards, in actual production, other tests such as ammonia testing, conductivity testing, coating hardness testing, and porosity testing are usually conducted.
Colorful Dacromet Coating Processing Sample Case
Dacromet is a coating process that provides corrosion resistance to metal surfaces. Here are some sample cases showcasing the use of Dacromet met
Automotive Parts
Dacromet coating is used in various automotive parts such as brake components, clutch parts, and suspension parts to protect them from corrosion and increase their longevity.
Fasteners
Dacromet met-coated fasteners are used in various industries such as construction, machinery, and electronics to protect them from corrosion and rust.
Marine Parts
Dacromet is used in various marine applications such as boat trailers, anchors, and propellers to protect them from the corrosive effects of saltwater.
Electrical Components
Dacromet met-coated electrical components are used in various industries such as aerospace and telecommunications to protect them from corrosion and improve their durability.
Agricultural Equipment
Dacromet is used in various agricultural applications such as tractors, combines, and other equipment to protect them from the harsh outdoor environment and increase their lifespan.
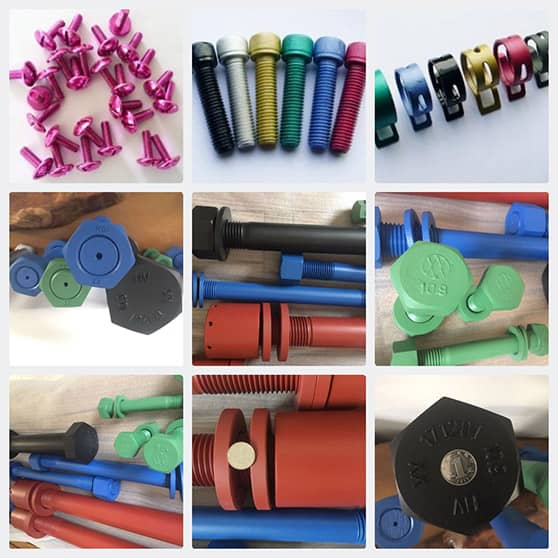

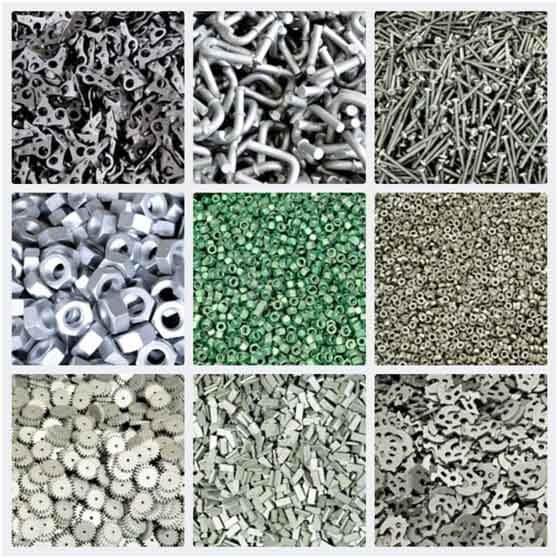
Free Sample
Explore Other Surface Finish
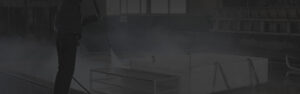
Metal Passivation
Passivation refers to the process of treating the metal with a strong oxidant or electrochemical method to oxidize its surface, making it passive, i.e., transforming the metal surface into a

Anodizing
Aluminum Anodized Finish (Aluminum Anodizing) Brief introduction to the aluminum anodizing process Anodic oxidation, also known as aluminum anodizing, refers to the electrochemical oxidation of metals or alloys. It is
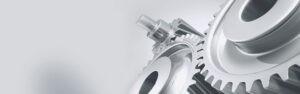
Dacromet Coating
Colorful Dacromet coating processing refers to a special post-treatment process after conventional Dacromet coating processing, which enables the Dacromet coating to exhibit various desired colors such as black, red, blue,