Gold Plating
24K Gold Plating
24K Gold Plating Processing: Suitable for Appearance Plating of Jewelry, Crafts, and other Decorative Items, as well as Functional Plating with Conductive Performance Requirements
Introduction to "24K Gold Plating" Processing Capability
Applicable Materials
Iron parts, steel parts, stainless steel, copper parts, aluminum alloys, magnesium alloys, titanium alloys, zinc alloys, precious alloys, tungsten steel, ceramics, etc.
Available Plating Types
Water gold plating, real gold plating, bright gold plating, rose gold plating, champagne gold plating, 24K gold plating, matte gold plating, vacuum titanium gold plating, PVD vacuum furnace gold plating, etc.
Available Techniques
Hanging plating, barrel plating, shake plating, selective electroplating, continuous electroplating, spot plating, brush plating, etc.
Available Colors:
Gold, rose gold, champagne gold, titanium gold, etc.
Available Film Thickness
Gold layer thickness ranging from 0.025μm to 3μm.
Maximum Size
850mm.
Introduction to 24K Gold Plating Process
Applicable electroplating techniques for 24K gold plating include hanging plating, barrel plating, shake plating, continuous plating, and vibratory plating. However, it should be noted that the plating accuracy for 24K gold is relatively poor, and it is often difficult to achieve complete plating inside deep or blind holes.
Film thickness for 24K gold plating refers specifically to the thickness of the gold layer. It generally ranges from 0.5 microns (0.125μm) to 120 microns (3μm). Therefore, it is not uncommon for customers to request gold plating with a thickness of several millimeters. To clarify, such requests indicate that the customer is still unfamiliar with gold plating techniques. (Note: 1 millimeter = 100 microns = 1000 micrometers = 40,000 angstroms. Additionally, angstroms are very close to microinches. So, if a drawing specifies a gold layer thickness of 20 microinches, it can be directly expressed as plating with 20 angstroms of gold.)
Overall film thickness for 24K gold plating varies depending on the material of the workpiece. Different pretreatment methods are required during the gold plating process. For example, in the case of aluminum alloy materials, after zinc plating and nickel underplating, gold plating can be applied directly. However, depending on the requirements of the workpiece’s end use, additional processes such as copper/acidity copper/flash copper plating or strike nickel plating may be necessary. Therefore, for precision components with tolerance requirements, consideration should be given to the residual dimensions due to film thickness before gold plating. Generally, the overall film thickness for 24K gold plating ranges from 1 to over 20 microns.
Wear resistance of 24K gold plating: Gold plating with 24K gold does not mean it is immune to wear. However, compared to pure gold or soft gold, the surface hardness of hard gold plating is higher, resulting in greater wear resistance. The surface hardness of hard gold plating is generally around 120 Vickers hardness.
Cost calculation for 24K gold plating primarily depends on the cost of gold consumed, which accounts for approximately 40-50% of the total cost. This cost is mainly determined by the surface area of the workpiece to be gold-plated and the thickness of the gold layer. Additionally, factors such as the material of the workpiece, its shape, size, the complexity of the plating requirements, and the difficulty level of electroplating, as well as the quantity of workpieces in a batch and whether it is a one-time or long-term order, all significantly impact the quotation. Therefore, electroplating quotations are usually subject to negotiation, with a high degree of subjectivity.c chrome in the coating is only 50%-70%, while the rest is chromium oxide. The black chrome coating has a loose crystalline structure with a branching pattern, which allows it to fully absorb light waves and appear black. It has been proven that black chrome coating is the most excellent selective absorber among all black electroplating and coating as solar energy development continues. The ratio of the absorption rate (a) to the reflection rate (y) of black chrome coating can be greater than 10, making it widely used in solar energy collectors, weapons, optical instruments and cameras. In addition, black is relatively solemn, so it is increasingly used in automotive, daily light industry decorative parts, and other fields.
24K Gold Plating Process
Hanging Plating:
- Pre-plating inspection
- Chemical degreasing
- Hot water rinse
- Water rinse
- Acid cleaning
- Water rinse
- The workpieces to be plated are soaked in a very dilute sodium carbonate solution, while the workpieces that do not require immediate plating are passivated and dried
- Hanging the workpieces
- Electrochemical degreasing
- Water rinse
- Activation
- Water rinse
- Pure water rinse
- Nickel plating
- Nickel recovery cleaning
- Water rinse
- Pure water rinse
- Pre-gold plating
- Gold recovery cleaning
- Secondary gold recovery cleaning
- Immersion rinse
- Cascade rinse
- Pure water cascade rinse
- Hot pure water immersion rinse
- Vibrational drying
- Vibrational drying
- Inspection.
Barrel Plating
- Pre-plating inspection
- Chemical degreasing (for heavily contaminated contacts, pre-cleaning with organic solvent degreasing)
- Hot water rinse
- Water rinse
- Acid cleaning
- Water rinse
- The workpieces to be plated are soaked in a very dilute sodium carbonate solution, while the workpieces that do not require immediate plating are passivated and dried
- Placing the workpieces into the barrel
- Electrochemical degreasing
- Water rinse
- Activation
- Water rinse
- Pure water rinse
- Nickel plating
- Nickel recovery cleaning
- Water rinse
- Pure water rinse
- Nickel plating (brass components pre-plated with copper)
- Nickel recovery cleaning
- Water rinse
- Pure water rinse
- Pre-gold plating
- Gold plating (hard gold)
- Secondary gold recovery cleaning
- Water rinse
- Pure water rinse
- Hot pure water rinse
- Drying (temperature not exceeding 120℃)
- Post-plating inspection.
Vibratory Plating
- Pre-plating inspection
- Chemical degreasing (for contacts with deep holes or blind holes, pre-cleaning with organic solvent ultrasonic degreasing)
- Hot water rinse
- Water rinse
- Acid cleaning
- Water rinse
- Passivation and drying
- Placing the workpieces into the vibrating sieve
- Chemical degreasing
- Electrolytic degreasing (can be done in the chemical degreasing tank)
- Immersion rinse
- Cascade rinse
- Activation
- Immersion rinse
- Cascade rinse
- Pure water cascade rinse
- Nickel plating (brass components pre-plated with copper)
- Nickel recovery cleaning
- Immersion rinse
- Cascade rinse
- Pure water cascade rinse
- Pre-gold plating
- Gold recovery cleaning
- Secondary gold recovery cleaning
- Immersion rinse
- Cascade rinse
- Pure water cascade rinse
- Hot pure water immersion rinse
- Vibrational drying
- Inspection.
24K Gold Plating Processing: Production equipment Showcase
Pre-plating inspection station
This station is equipped with tools and instruments for inspecting the workpieces before the plating process. It may include magnifying glasses, measuring devices, and quality control equipment.
Chemical degreasing tank
This tank contains a chemical degreaser solution that is used to remove any grease or contaminants from the surface of the workpieces. It may be equipped with agitators or ultrasonic transducers to enhance the cleaning process.
Hot water rinse station
Workpieces are rinsed with hot water at this station to remove the chemical degreaser and any residual impurities.
Water rinse station
A water rinse is performed to further cleanse the workpieces and ensure they are free from any cleaning solution.
Acid cleaning tank
This tank contains an acid solution that is used to clean the workpiece surfaces, remove oxide layers, and prepare them for plating.
Passivation and drying area
Workpieces that do not require immediate plating are passivated and dried in this area. Passivation helps protect the surfaces and prevent oxidation.
Hanging or barrel plating equipment
Depending on the plating method used, there will be hanging racks or barrel plating equipment where the workpieces are placed for the actual plating process. These equipment ensure proper immersion and contact with the plating solution.
Electrochemical degreasing setup
This setup is used for electrochemical degreasing of the workpieces, which helps remove stubborn contaminants and ensures a clean surface.
Activation station
Workpieces are treated with an activation solution to prepare the surfaces for plating and enhance adhesion.
Nickel plating tank
This tank contains a nickel plating solution. The workpieces, especially brass components pre-plated with copper, undergo nickel plating to provide a base layer.
Nickel recovery cleaning setup
After nickel plating, a cleaning setup is used to recover excess nickel and remove any residual plating solution.
Pre-gold plating station
The workpieces go through preparatory steps before gold plating.
Secondary gold recovery cleaning setup
A cleaning setup is used to recover any excess gold and ensure surface cleanliness.
Rinse stations
Multiple rinse stations, including immersion rinses and cascade rinses, are set up to thoroughly clean the workpieces at various stages of the process.
Hot pure water immersion rinse station
The workpieces undergo a final rinse with hot pure water to ensure complete cleanliness.
Drying equipment
Vibrational drying or other drying methods are employed to remove excess moisture from the plated workpieces without damaging the plating.
Inspection area
The plated workpieces are inspected using visual examination, measurement tools, and other quality control measures to ensure they meet the desired specifications.
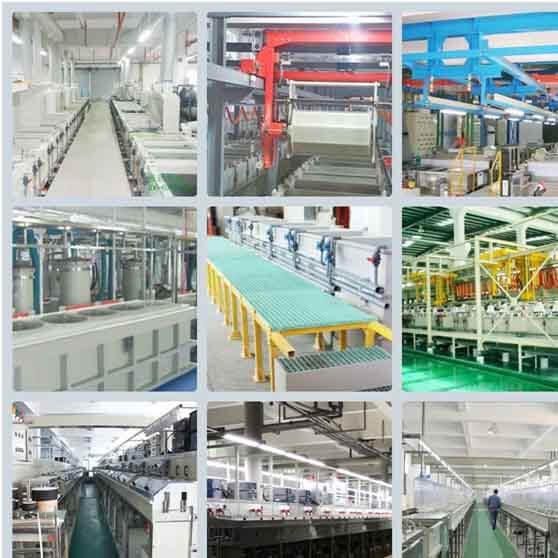
24K Gold Plating Process: Instrument Showcase
Thickness Gauge
This device measures the thickness of the gold layer to ensure it meets the desired specifications. It provides precise readings in micrometers (μm) or millimeters (mm).
Adhesion Tester
The adhesion tester evaluates the bond strength between the gold layer and the substrate. It applies controlled force to determine the coating's resistance to peeling or detachment.
X-ray Fluorescence (XRF) Analyzer
The XRF analyzer is used to determine the elemental composition of the gold plating. It identifies the purity and percentage of gold in the plating layer.
Salt Spray Chamber
This chamber simulates harsh environmental conditions, such as saltwater exposure, to assess the corrosion resistance of the gold plating. It measures the plating's ability to withstand corrosion over time.
Microscope
A microscope with high magnification capabilities is used for visual inspection of the gold plating. It allows for detailed examination of the coating's surface, including its smoothness and uniformity.
Cross-Sectional Analysis Instrument
This instrument enables the examination of a cross-sectional sample of the gold-plated material. It provides insights into the plating thickness, layer structure, and any potential defects or inconsistencies.
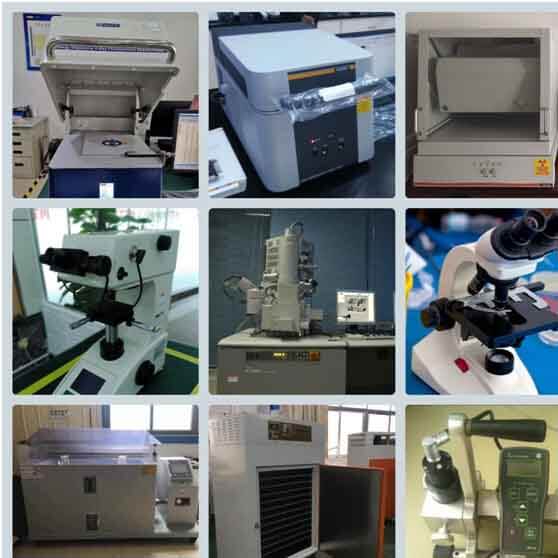
24K Gold Plating Process: Sample Cases
Jewelry
Gold plating is commonly used in the jewelry industry to enhance the appearance of various accessories such as necklaces, bracelets, earrings, and rings. It provides a luxurious and radiant finish, adding value and elegance to the pieces.
Watches
Watchmakers often utilize 24K gold plating to create exquisite timepieces with a timeless appeal. The gold-plated components, such as watch cases, bezels, and dials, exude a sense of luxury and prestige.
Decorative Items
Many decorative items, such as statues, sculptures, and ornaments, can be enhanced with 24K gold plating. The gold layer gives these items a lavish and opulent look, making them stand out as centerpieces or decorative accents.
Electronic Devices
Some electronic devices incorporate 24K gold plating for both aesthetic and functional purposes. Gold-plated connectors and contacts are used in high-end audio instruments, smartphones, and other electronic devices to improve conductivity and resist corrosion.
Automotive Emblems
Luxury car manufacturers often utilize 24K gold plating for their emblems and logos. The gold-plated emblems add a touch of sophistication and exclusivity to the vehicles, enhancing their overall brand image.
Architectural Applications
In architecture and interior design, 24K gold plating can be used to embellish elements like door handles, handrails, decorative accents, and lighting fixtures. It creates a lavish and striking visual impact, adding a touch of grandeur to the space.
These sample cases demonstrate the versatility and aesthetic value of 24K gold plating across various industries and applications.

Brass Gold Plating
Brass H62 hanging gold plating with hard gold/thick gold processing.

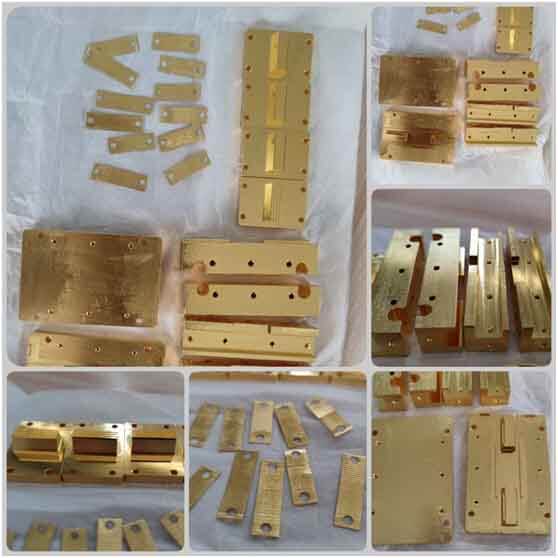
Base material: Brass H62
Plating Type: Gold plating/hard gold plating/gold-cobalt alloy plating/thick gold plating/24K gold plating
Process: Hanging gold plating
Thickness: Ni: 8μm, Au: 20 mar (0.5μm)
Electroplating cost: 30usd/square decimeter
- Pre-plating inspection
- chemical degreasing
- hot water washing
- flowing water cleaning
- acid washing
- flowing water washing
- immerse the plating parts that need to be plated with an extremely dilute solution of sodium carbonate, and the plating parts that are not urgently needed are passivated and dried
- hang the plating parts
- electrochemical degreasing
- flowing water washing
- activation
- flowing water washing
- pure water washing
- electroplating nickel
- nickel recovery and cleaning
- flowing water washing
- pure water washing
- pre-plating gold
- gold recovery and cleaning
- secondary gold recovery and cleaning
- immersion
- rinsing
- pure water rinsing
- hot pure water immersion
- vibration drying
- inspection.
The principle of hard gold plating
add a trace amount of cobalt element (the hardness of gold is 20, and the hardness of cobalt is 125) to the gold salt. Therefore, the commonly used term for hard gold plating in the industry is gold-cobalt alloy plating!
Applicable electroplating processes for hard gold plating
Hanging gold plating, rolling plating, shaking plating, continuous plating, and vibrating plating are all applicable. However, it should be noted that the positioning accuracy of hard gold plating is poor, and it is often difficult to plate the inside of deep holes or blind holes.
The thickness of hard gold plating
It should be noted that the thickness here specifically refers to the thickness of the gold layer. Generally, it is between 0.5 mar (0.125μm) and 120 mar (3μm). Therefore, we often encounter some customers who ask for gold plating of several millimeters. To be honest, we can be sure that this purchase is still at a beginner level in terms of gold plating technology. (PS: 1 millimeter = 100 silk = 1000 micrometers = 40000 mar; in addition, the unit of mar is very close to microinch, so some drawings use microinch as the unit. If the required gold layer thickness is 20 microinches, it can be directly said to plate 20 Mar gold).
Bright Gold Plating
Overview of One-Stop Bright Gold Plating Capability
Available materials
copper/copper alloy, aluminum/aluminum alloy, iron/iron alloy, steel/stainless steel, zinc/zinc alloy, magnesium/magnesium alloy, titanium/titanium alloy, plastic parts, etc. In addition, for materials such as tungsten steel, canna alloy, ceramics, glass, etc., you can also get gold plating processing done in a one-stop-shop by Optimim.
Workpiece size
0.1mm-1000mm (workpieces within 1 meter can be handled)
Salt spray requirements
Different materials have different achievable salt spray durations; requirements for salt spray testing of 100 hours or more can be met.
Electroplating of Bright Gold: Process Overview
The applicable electroplating processes for bright gold are hanging plating, continuous plating, and vibratory plating. Since workpieces with bright gold electroplating generally have high appearance requirements, rolling plating, and shaking plating cannot be used (in any case, these processes will leave some traces on the surface of the workpiece, which will affect the appearance).
The thickness of the gold layer in bright gold electroplating generally ranges from 0.5 microns (0.125μm) to 3 microns (120 Ma). Therefore, it is not uncommon for customers to request a thickness of several millimeters for the gold layer, but such requests indicate a lack of understanding of the electroplating process.
The total thickness of the electroplating for a workpiece of different materials varies, and different pretreatment methods are required during the electroplating process. For example, in the case of aluminum alloy materials, zinc immersion plating is performed twice and then nickel plating is performed as a base layer before the gold plating process. However, depending on the requirements of the workpiece, acid copper/plating or impact nickel plating may also be added. Therefore, for precision parts with dimensional accuracy requirements, the residual size of the thickness of the electroplating needs to be considered before the gold plating process. In general, the total thickness of the electroplating for hard gold is between 1 and 20 microns.
The cost of electroplating for hard gold mainly depends on the cost of the gold consumed (which accounts for about 40-50% of the total cost), which in turn depends on the surface area of the workpiece and the thickness of the gold layer required. In addition, the cost of electroplating depends on factors such as the material of the workpiece, the shape and size of the workpiece, the difficulty of the electroplating process, the quantity of the workpiece in a batch, and whether it is a one-time or long-term order, which greatly affects the quotation. Therefore, electroplating costs are usually negotiated on a case-by-case basis, and subjective factors play a significant role in the pricing.
Bright Gold Plating Process Flow
Hanging plating
- Pre-plating inspection
- Chemical degreasing
- Hot water washing
- Flow washing
- Acid pickling
- Flow washing
- The plating parts that will be electroplated next are soaked in a very dilute solution of sodium carbonate. For the parts that do not need to be electroplated urgently, they are passivated, dried and hung up.
- Electrochemical degreasing
- Flow washing
- Activation
- Flow washing
- Pure water washing
- Nickel plating
- Nickel recovery cleaning
- Flow washing
- Pure water washing
- Pre-gold plating
- Gold plating recovery cleaning
- Secondary gold recovery cleaning
- Immersion
- Rinse
- Pure water rinse
- Hot pure water immersion
- Vibration drying
- Inspection.
Roll plating
- Pre-plating inspection
- Chemical degreasing (for contact bodies with heavy oil pollution, organic solvent degreasing cleaning is used in advance)
- Hot water washing
- Flow washing
- Acid pickling
- Flow washing
- The plating parts that will be electroplated next are soaked in a very dilute solution of sodium carbonate. For the parts that do not need to be electroplated urgently, they are passivated, dried and put into the drum.
- Electrochemical degreasing
- Flow washing
- Activation
- Flow washing
- Pure water washing
- Nickel plating (brass parts are pre-electroplated with copper)
- Nickel recovery cleaning
- Flow washing
- Pure water washing
- Pre-gold plating
- Gold plating (hard gold)
- Secondary gold recovery cleaning
- Flow washing
- Pure water washing
- Hot pure water washing
- Drying (temperature not exceeding 120℃)
- Post-plating inspection.
Vibration plating
- Pre-plating inspection
- Chemical degreasing (for contact bodies with deep or blind holes, organic solvent ultrasonic degreasing cleaning is used in advance)
- Hot water washing
- Flow washing
- Acid pickling
- Flow washing
- Passivation and drying
- The plating parts are loaded into the vibrating screen
- Chemical degreasing
- Electrolytic degreasing (can be carried out in the chemical degreasing tank). Immersion
- Rinse
- Activation
- Immersion
- Rinse
- Pure water rinse
- Nickel plating (brass parts are pre-electroplated with copper)
- Nickel recovery cleaning
- Immersion
- Rinse
- Pure water rinse
- Pre-gold plating
- Gold plating recovery cleaning
- Secondary gold recovery cleaning
- Immersion
- Rinse
- Pure water rinse
- Hot pure water immersion
- Vibration drying
- Inspection.
Display of Production Equipment for Bright Gold Plating Process
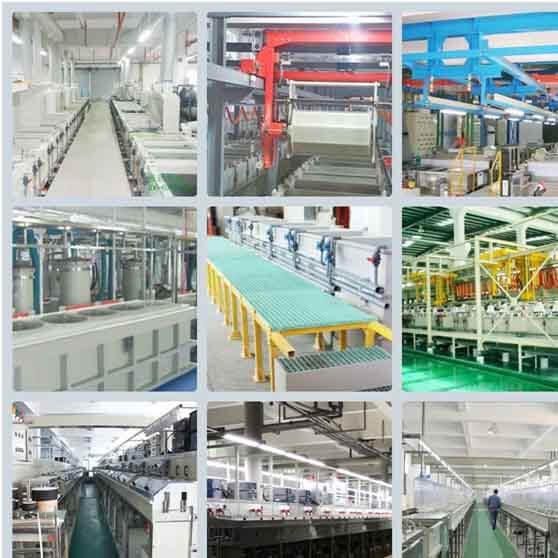
Display of Inspection Equipment for Bright Gold Plating Processing.
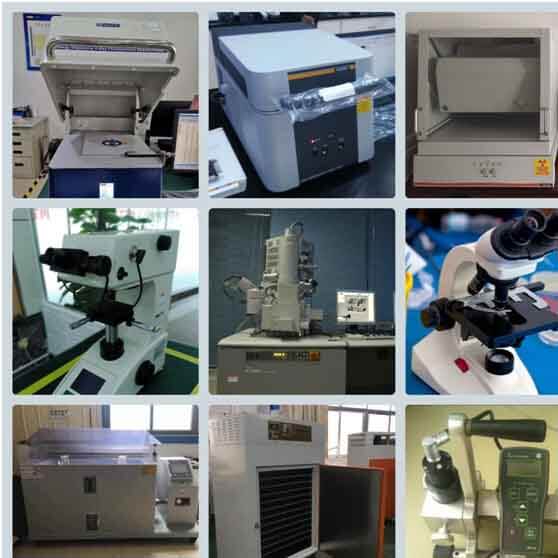
Sample cases of bright gold plating processing
Jewelry
Bright gold plating is commonly used on jewelry to give it a shiny, luxurious appearance. It is applied to items such as necklaces, bracelets, rings, and earrings.
Watch Components
Bright gold plating is used to enhance the appearance of watch components such as watch faces, bezels, and bands. It is also used to protect the watch from corrosion and wear.
Electronic Components
Bright gold plating is used on electronic components such as connectors, switches, and circuit boards. The gold provides a reliable, corrosion-resistant surface that can withstand frequent use and exposure to the environment.
Optical Components
Bright gold plating is used on optical components such as mirrors and lenses. The gold coating enhances the reflective properties of the component and protects it from damage.
Decorative Objects
Bright gold plating is also used on decorative objects such as picture frames, vases, and sculptures. The gold gives these items a sophisticated, high-end appearance.
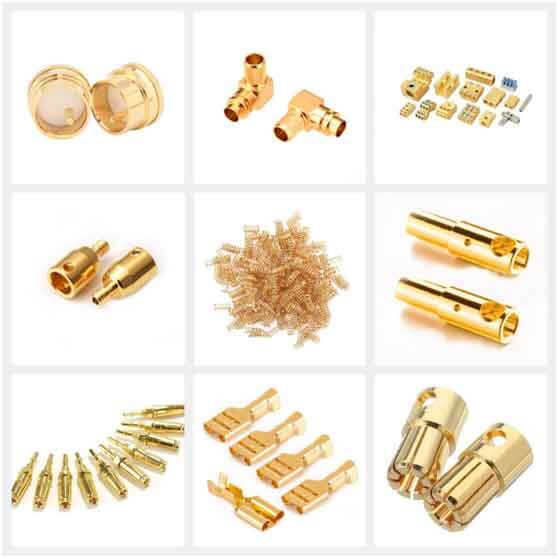
Gold Imitation Plating
Introduction to Gold Imitation Plating Processing Capability
Suitable Materials
We can provide gold imitation plating services for various materials such as iron, steel, stainless steel, copper, aluminum alloy, zinc alloy, brass alloy, tungsten steel, and more.
Plating Options
Our gold imitation plating capabilities include options such as gold imitation plating, copper-zinc alloy plating, copper-tin alloy plating, copper-zinc-tin alloy plating, and gold color electrophoretic coating.
Process Techniques
We offer gold imitation plating using processes such as hanging plating and barrel plating, depending on the specific requirements of the workpieces.
Supporting Processes
Additional processes such as sandblasting and polishing can be provided as complementary services to enhance the surface finish and appearance of the workpieces.
Color Options
Our gold imitation plating can achieve a rich and visually appealing gold color or an 18K gold color, providing a luxurious and elegant appearance.
Thickness Range
We can achieve gold imitation plating with a thickness ranging from 5 to 20 microns, ensuring durability and longevity.
Maximum Size
Our plating capabilities can accommodate workpieces with a maximum size of 600mm, allowing for a wide range of applications. At our supply chain facility, we have the expertise and equipment to deliver high-quality gold imitation plating services tailored to your specific needs.
Introduction to Gold Imitation Plating Process
Commonly used gold imitation coatings are primarily based on brass plating solution, with the 18K gold color being popular. This color is achieved through a copper-zinc binary alloy. People generally favor this color, making it the most common choice for gold imitation plating. Some variations may include the addition of a third metallic element to alter the appearance and color tone. Gold imitation coatings are essentially alloy coatings, typically composed of copper and zinc, with the addition of a third metal element, often tin.
Gold imitation plating process flow
- Pre-plating Inspection
- Chemical Degreasing
- Hot Water Rinse
- Running Water Rinse
- Acid Pickling
- Running Water Rinse
- Immersion in Dilute Sodium Carbonate Solution for the upcoming electroplating items; Passivation and Drying for items that do not require immediate electroplating
- Hanging the workpiece for plating
- Electrochemical Degreasing
- Running Water Rinse
- Activation
- Running Water Rinse
- Distilled Water Rinse
- Nickel Plating
- Nickel Recovery Cleaning
- Running Water Rinse
- Distilled Water Rinse
- Gold Imitation Plating
- Gold Plating Recovery Cleaning
- Immersion
- Dipping Rinse
- Distilled Water Rinse
- Hot Distilled Water Immersion
- Vibrating Drying
- Inspection and Quality Control.
Gold imitation plating production equipment showcase
Plating Tanks
Tanks are used for immersing the workpieces during the plating process. These tanks are typically made of chemically resistant materials such as polypropylene or stainless steel.
Rectifiers
Electrical power supply units that provide the required current for the electroplating process. They control the voltage and current during plating to ensure proper deposition of the gold imitation layer.
Racks and Hooks
These are used to hang and suspend the workpieces in the plating tanks, allowing for even immersion and consistent plating results.
Chemical Degreasing Equipment
Equipment such as immersion tanks, spray systems, or ultrasonic cleaners used for the chemical degreasing process to remove grease and contaminants from the workpiece surface.
Rinse Stations
Stations equipped with running water or spray systems for rinsing the workpieces between different process steps to remove residual chemicals and ensure cleanliness.
Acid Pickling Tanks
Tanks containing acid solutions used for the pickling process, where the workpieces are immersed to remove impurities and provide surface activation.
Rectifiers
Gold Imitation Plating Tanks: Tanks are specifically designed for the gold imitation plating process, equipped with the necessary plating solutions and electrodes to achieve the desired color and appearance.
Distilled Water Rinse System
A system that provides distilled water for the final rinsing of the workpieces, ensuring a clean surface free from impurities.
Drying Equipment
Equipment such as vibrating dryers, hot air dryers, or drying ovens are used to remove moisture from the plated workpieces after rinsing.
Quality Control Tools
Instruments and devices for inspecting the plating quality, such as thickness testers, color measurement devices, and visual inspection tools.
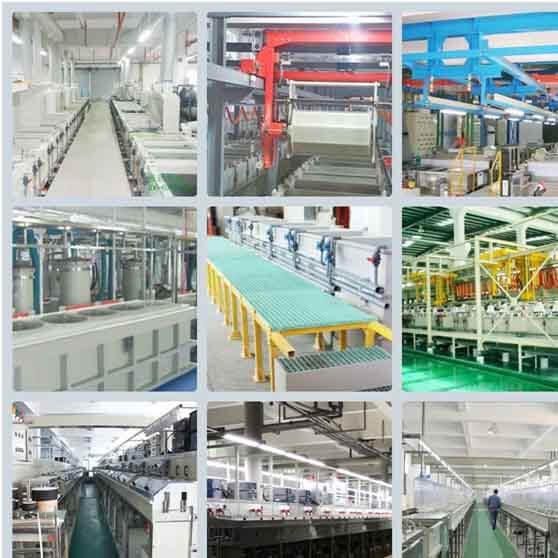
Exhibition of Testing Instruments for Imitation Gold Plating Process
Thickness Measurement
Coating Thickness Gauge
Used to measure the thickness of the gold plating layer.
Micrometer
Used to measure the overall thickness of the workpiece. Adhesion Testing:
Cross-Cut Adhesion Tester
Evaluates the adhesion strength of the gold plating layer by making cuts in a grid pattern and applying tape to assess coating adhesion.
Surface Quality Assessment
Visual Inspection Tools
Magnifying glasses, microscopes, or inspection lamps are used to visually assess the surface quality, including smoothness, uniformity, and absence of defects.
Gloss Meter
Measures the glossiness of the plated surface.
Surface Quality Assessment
Salt Spray Test Chamber
Subjects the plated workpieces to a corrosive environment to evaluate their resistance to corrosion.
Humidity Chamber
Simulates high humidity conditions to assess the corrosion resistance of the plated layer.
Color Evaluation
Colorimeter
Measures and quantifies the color properties of the gold plating layer, including hue, saturation, and brightness. Plating Thickness Distribution:
X-ray Fluorescence (XRF) Analyzer
Determines the distribution of plating thickness across the workpiece by analyzing the elemental composition. These testing instruments are utilized to ensure the quality, durability, and adherence of the imitation gold plating layer, as well as to assess the overall appearance and performance of the plated workpieces.
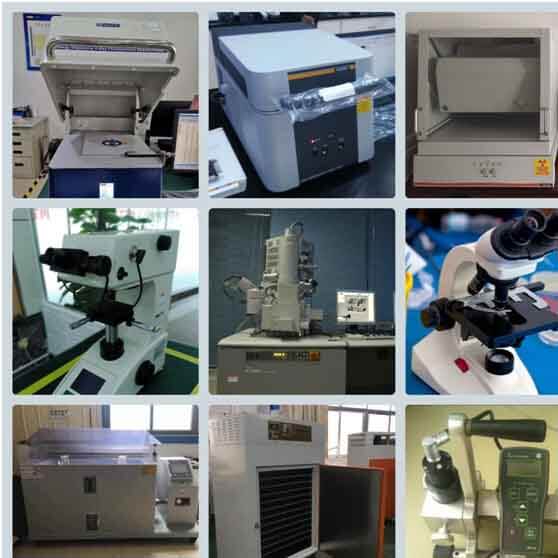
Sample Cases of Imitation Gold Plating Process
Decorative Artware
Various art pieces, such as sculptures, figurines, and ornaments, can be finished with an imitation gold plating layer to enhance their aesthetic appeal and create a luxurious appearance.
Jewelry and Accessories
Imitation gold plating is commonly used in the production of costume jewelry, fashion accessories, and decorative components like pendants, earrings, bracelets, and belt buckles. It provides an affordable alternative to solid gold while maintaining a similar visual effect.
Interior Decor Items
Items used for interior decoration, such as lamp bases, handles, knobs, and decorative hardware, can be coated with an imitation gold layer to add a touch of elegance and sophistication to furniture, lighting fixtures, and home decor.
Electronic Devices
Some electronic devices, such as smartphones, tablets, and laptops, may feature imitation gold plating on certain components or accents, giving them a premium and stylish appearance.
Automotive Trim
Imitation gold plating can be applied to automotive trim elements, such as emblems, grilles, badges, and decorative trims, to create a luxurious and eye-catching look for vehicles.
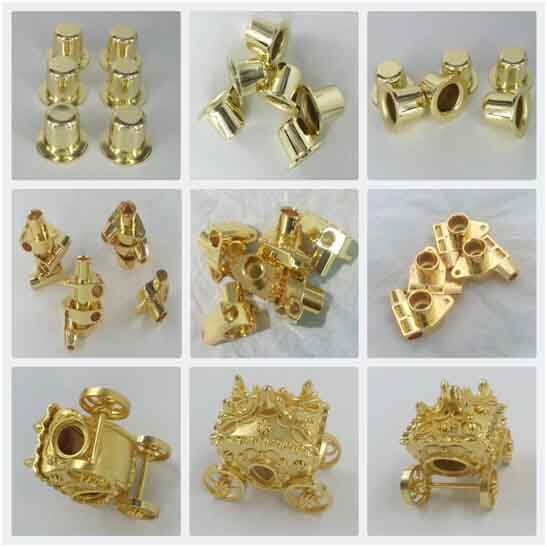
Gold Plated Tungsten
Hard Gold plated tungsten probe by water immersion / local gold plating processing.
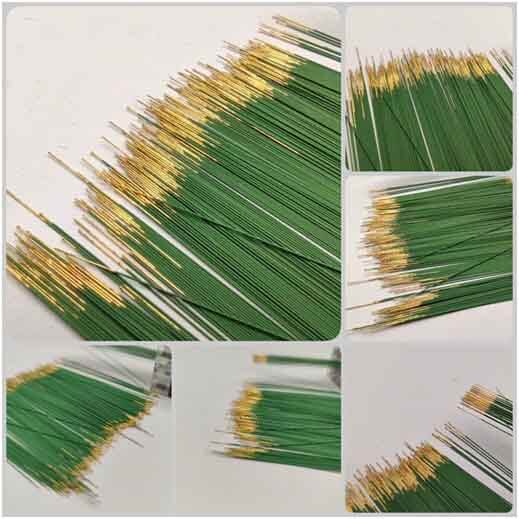
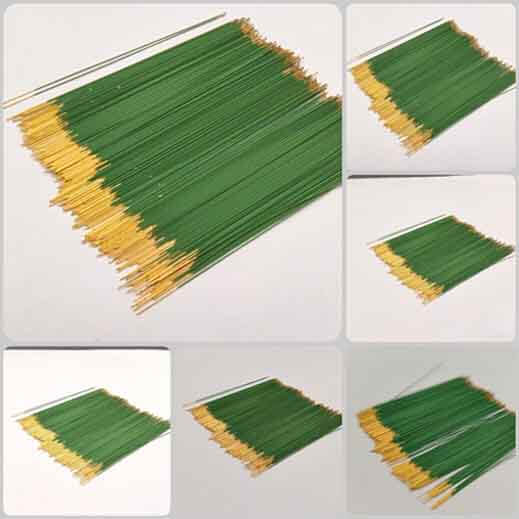
Substrate: tungsten steel
Plating Type: hard gold plating / 24K gold plating/electroplating gold
Process: hanging plating
Film thickness: 5μm thickness on one side, gold layer thickness of 8 Ma (0.2μm)
Electroplating cost: 0.3 USD/piece
Benefits of gold plating on test probes
The gold plating layer has good ductility, easy to polish, high temperature resistance, and good anti-discoloration performance. Gold plating on silver can prevent the silver from discoloring; gold alloy plating can show various color tones and is often used as a decorative plating layer, such as for jewelry, clock parts, and artwork. Gold plating has low contact resistance, good conductivity, easy to weld, strong corrosion resistance, and has certain wear resistance (referring to hard gold), so it has a wide range of applications in precision instruments, printed circuit boards, integrated circuits, tube shells, electrical contacts, etc.
The benefits of re-gold plating on test probes after pre-gold plating treatment
Ensure the adhesion of the gold plating layer. Reduce the possibility of contamination of the positive gold plating bath. Economical and practical, cost-effective. Can improve the density of the gold plating layer.
Is gold plating the only process for test probe gold plating?
As we all know, gold plating is, as the name suggests, to the plate with gold. Actually, what we call gold plating is not only for gold plating the probes. Before gold plating, we will first plate a layer of nickel. The cost of nickel plating for test probes is much lower than that of gold plating, and nickel plating can also achieve the effects of antioxidation and wear resistance, but its conductivity is not as good as gold plating. Good conductivity is very important in the electronic hardware industry and the probing industry, so gold plating is more frequently used. Finally, let's consider why a layer of nickel is plated on the test probe before gold plating. The reason is that copper and gold elements are not so easy to bond. After gold plating, the gold may come off, which will affect the use of the probe. Plating a layer of nickel before gold plating can solve this problem very well.
Gold Plating of Plastic Parts
Note: The term “10å”›” (10 microns) is a unit of thickness commonly used in the electroplating industry in China.
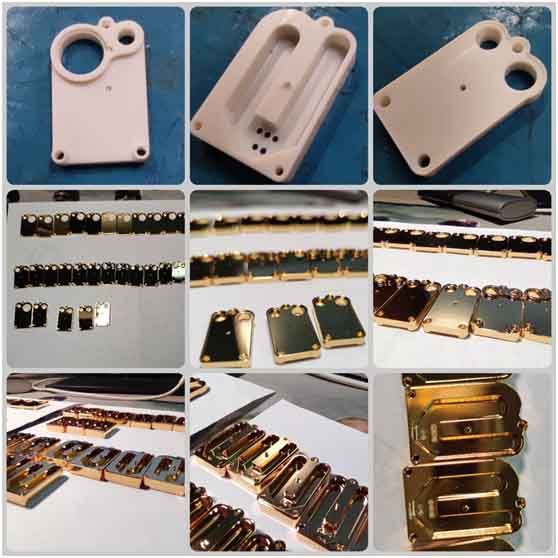
Substrate: ABS (Taiwan Chi Mei 711, electroplating grade ABS)
Plating types: acid copper plating, chemical nickel plating / electroless nickel plating, thick gold plating / 24K gold plating
Process: hanging plating
Auxiliary process: mechanical polishing
Film thickness: single side film thickness of 15μm, gold layer thickness of 10μm / 0.25μm;
Electroplating price: 3 USD / piece;
There are many special design requirements for plastic electroplating parts,
The substrate is best made of ABS material. The adhesion of the film after electroplating ABS is good, and the price is relatively cheap.
The surface quality of the plastic parts must be very good. Electroplating cannot cover up some of the defects in injection molding and usually makes these defects more obvious.
In structural design, attention should be paid to the following points to ensure that the shape is suitable for electroplating treatment:
1)
The surface protrusions should be controlled at 0.1~0.15mm/cm, and sharp edges should be avoided as much as possible.
2)
If there is a blind hole design, the depth of the blind hole should not exceed half of the aperture, and there should be no requirement for the color of the bottom of the hole.
3)
Suitable wall thickness should be used to prevent deformation. It is best to be above 1.5mm and below 4mm. If it needs to be made very thin, a reinforced structure should be added at the corresponding position to ensure that the deformation of electroplating is within a controllable range.
4)
The design should consider the needs of the electroplating process. Since the working conditions of electroplating are generally in the temperature range of 60 to 70 degrees Celsius, under the condition of hanging, the unreasonable structure will inevitably cause deformation, so attention should be paid to the position of the water outlet in the design of plastic parts, and there should be a suitable hanging position to prevent damage to the required surface during hanging. For example, in the design below, the square hole in the middle is specially designed for hanging.
5)
It is also best not to have metal inserts in plastic parts. Due to the different expansion coefficients of the two, when the temperature rises, the plating liquid will seep into the gap, causing a certain impact on the structure of the plastic part.
Gold Plating Titanium
Overview of Gold Plating Titanium Capability:
Available Materials: Titanium Alloys – TA1, TA2, TA3, TA4, TC4, etc.
Available Plating Types: Water Gold Plating, Real Gold Plating, Bright Gold Plating, Rose Gold Plating, Champagne Gold Plating, 24K Gold Plating, Matte Gold Plating, Vacuum Titanium Gold Plating, PVD Vacuum Furnace Gold Plating…
Available Processes: Rack Plating, Barrel Plating, Shake Plating, Selective Plating, Multicolor Plating…
Supporting Processes: Sandblasting, Mechanical Polishing, Electrolytic Polishing…
Available Colors: Gold, Rose Gold, Champagne Gold, Titanium Gold, etc.
Available Coating Thickness: Gold layer thickness ranging from 0.025μm to 3μm.
Maximum Size: 600mm.
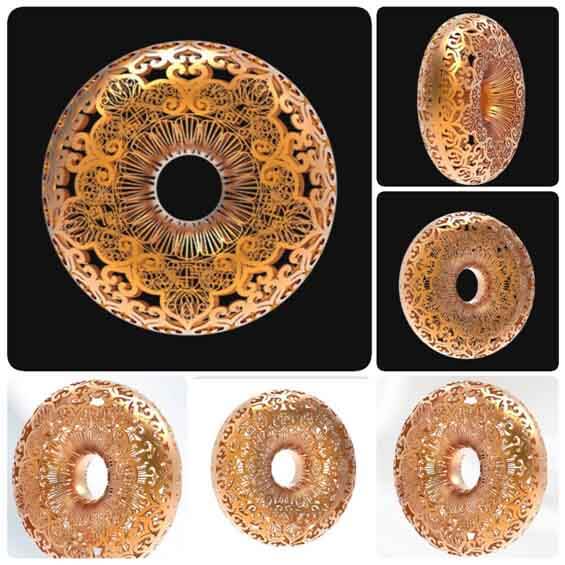
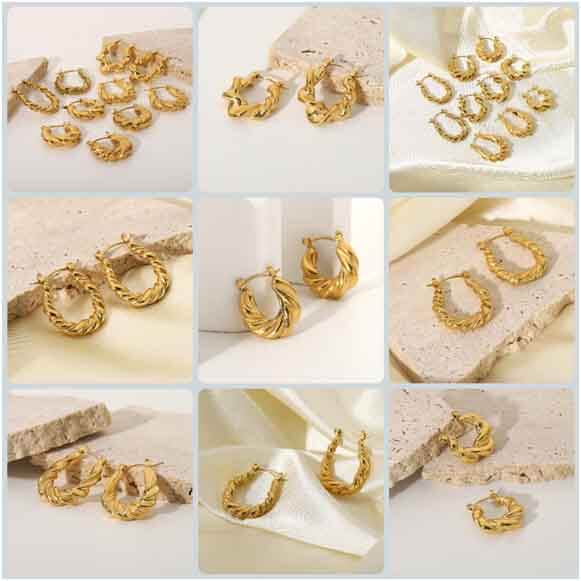
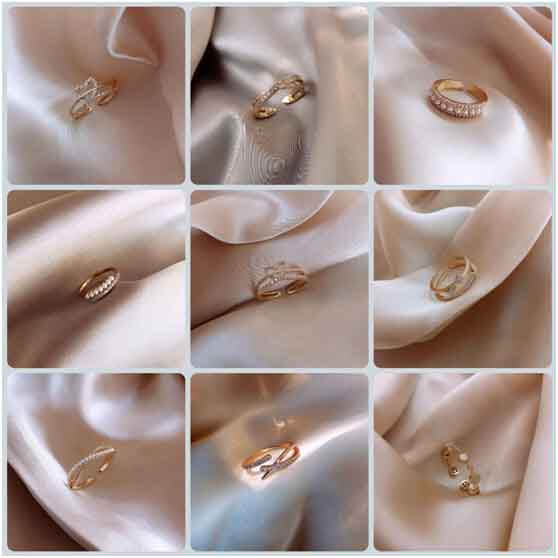
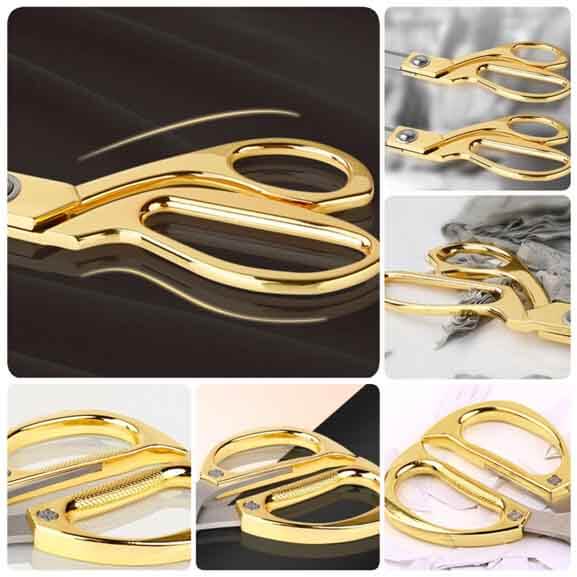
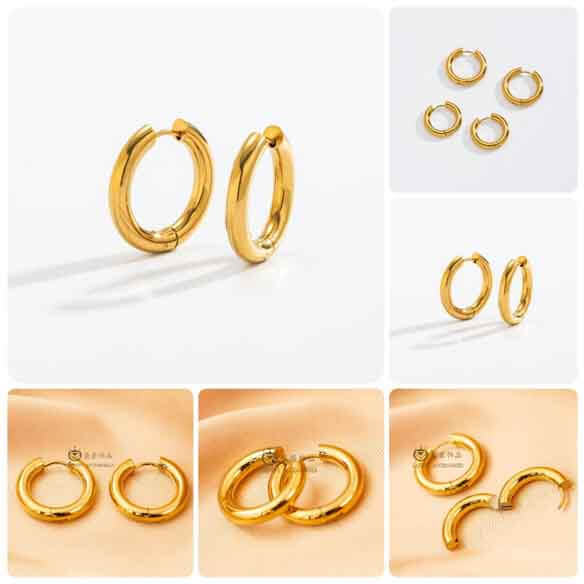
Analysis of Challenges in the Titanium Alloy Electroplating Process
Properties of Titanium and Titanium Alloys
Main Solutions to Problems in Titanium and Titanium Alloy Electroplating Processes
The first solution is the conversion film approach, where an additional layer is applied during the electroplating process to remove the oxide film from the titanium or titanium alloy surface. This additional layer should have good adhesion to the substrate, higher activity, and should not affect the adhesion between the electroplated layer and the metal. Electroplating is then performed on this film layer to achieve better adhesion with other metals.
The second solution is the avoidance of oxygen medium. This method involves conducting electroplating in an oxygen-isolated environment to prevent the formation of the oxide film. This approach is mainly used in processes such as molten salt plating and vacuum deposition. Before electroplating, the titanium substrate surface needs to be etched to increase the surface area between the plating and the substrate, thus enhancing the adhesion. After electroplating, the temperature needs to be controlled within an appropriate range for further treatment.
The third solution is the metal underlayer approach, which involves removing the oxide film from the surface of titanium metal and depositing a metal underlayer before applying the desired metal plating layer. Currently, to achieve better electroplating results on titanium and titanium alloys, a combination of the above three methods is often employed in practical operations, followed by further treatment.
Hard Gold Plating
Summary of Hard Gold Plating Processing Capability
Materials
copper/copper alloy, aluminum/aluminum alloy, iron/iron alloy, steel/stainless steel, zinc/zinc alloy, magnesium/magnesium alloy, titanium/titanium alloy, plastic parts, etc. In addition, for materials such as tungsten steel, Kovar alloy, ceramics, glass, etc., one-stop gold plating processing can also be done.
Workpiece size
0.1mm-1000mm (workpieces within 1 meter can be handled).
Salt spray requirement
Different materials can achieve different salt spray durations; salt spray testing requirements of 100 hours or more can be achieved.
Brief Introduction to Hard Gold Plating Process
Various electroplating processes can be used for hard gold plating, including hanging plating, rolling plating, shaking plating, continuous plating, and vibrating plating. However, it should be noted that hard gold plating has poor positional accuracy and it is difficult to plate deep or blind holes.
When discussing the thickness of hard gold plating, it is important to note that this refers specifically to the thickness of the gold layer, which is typically between 0.5 micrometers (0.125 microns) and 3 micrometers (120 microinches). It is common for customers to request gold plating with thicknesses of several millimeters, but such requests demonstrate a lack of understanding of the gold plating process.
The total thickness of hard gold plating varies depending on the material of the workpiece. Different pre-treatment methods are needed for different materials. For example, in the case of aluminum alloy materials, a second zinc immersion and nickel plating are typically performed before gold plating. Depending on the requirements of the workpiece, additional steps such as copper or nickel plating may be added. For precision parts with tolerance requirements, it is necessary to consider the residual size of the thickness before gold plating. Generally, the total thickness of hard gold plating ranges from 1 to 20 micrometers.
It should be noted that hard gold plating does not mean that the workpiece will never wear out. While the surface hardness of hard gold plating is higher and more wear-resistant than that of pure gold or soft gold, it is not completely immune to wear and tear. The surface hardness of hard gold plating is generally around 120 on the Vickers hardness scale.
The cost of hard gold plating is mainly determined by the cost of the gold consumed (which accounts for about 40-50% of the total cost), as well as the surface area of the workpiece and the thickness of the gold layer. Other factors that affect the cost include the material of the workpiece, the shape and size of the workpiece, the difficulty of electroplating, the quantity of workpieces in each batch, and whether the order is a one-time order or a long-term contract. Therefore, the pricing of electroplating is usually negotiated on a case-by-case basis and is highly subjective.
Process Flow of Hard Gold Plating
Rack plating
- Pre-plating inspection
- chemical degreasing
- hot water rinse
- flowing water rinse
- acid pickling
- flowing water rinse
- immerse the parts to be plated next in a very dilute sodium carbonate solution, and passivate and dry the parts that do not require urgent plating
- hanging the parts for plating
- electrochemical degreasing
- flowing water rinse
- activation
- flowing water rinse
- pure water rinse
- nickel plating
- nickel recovery and cleaning
- flowing water rinse
- pure water rinse
- pre-gold plating
- gold recovery and cleaning
- secondary gold recovery and cleaning
- immersion rinse
- drip rinse
- pure water rinse
- hot pure water immersion rinse
- vibration drying
- inspection.
Barrel Plating:
- Pre-plating inspection
- chemical degreasing (for contact bodies with heavy oil pollution, organic solvent degreasing is used in advance)
- hot water rinse
- flowing water rinse
- acid pickling
- flowing water rinse
- immerse the parts to be plated next in a very dilute sodium carbonate solution, and passivate and dry the parts that do not require urgent plating
- pour the parts into the barrel
- electrochemical degreasing
- flowing water rinse
- activation
- flowing water rinse
- pure water rinse
- nickel plating (brass parts are pre-electroplated with copper)
- nickel recovery and cleaning
- flowing water rinse
- pure water rinse
- pre-gold plating
- gold plating with increased thickness (hard gold)
- secondary gold recovery and cleaning
- flowing water rinse
- pure water rinse
- hot pure water rinse
- drying (temperature not exceeding 120℃) → post-plating inspection.
Vibratory Plating:
- Pre-plating inspection
- chemical degreasing (for contact bodies with deep or blind holes, organic solvent ultrasonic degreasing is used in advance)
- hot water rinse
- flowing water rinse
- acid pickling
- flowing water rinse
- passivate and dry the parts
- load the parts into the vibrating screen
- chemical degreasing
- electrochemical degreasing (can be performed in the chemical degreasing tank)
- immersion rinse
- drip rinse
- activation
- immersion rinse
- drip rinse
- pure water rinse
- nickel plating (brass parts are pre-electroplated with copper)
- nickel recovery and cleaning
- immersion rinse
- drip rinse
- pure water rinse
- pre-gold plating
- gold recovery and cleaning
- secondary gold recovery and cleaning
- immersion rinse
- drip rinse
- pure water rinse
- hot pure water immersion rinse
- vibration drying
- inspection.
Display of production equipment for hard gold plating processing.
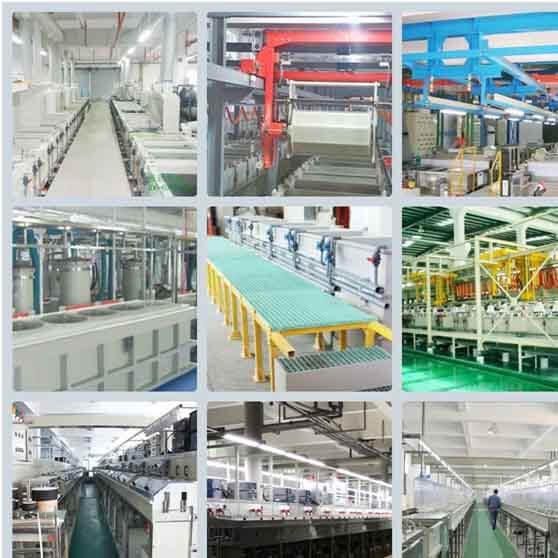
Display of Inspection Equipment for Hard Gold Plating Processing.
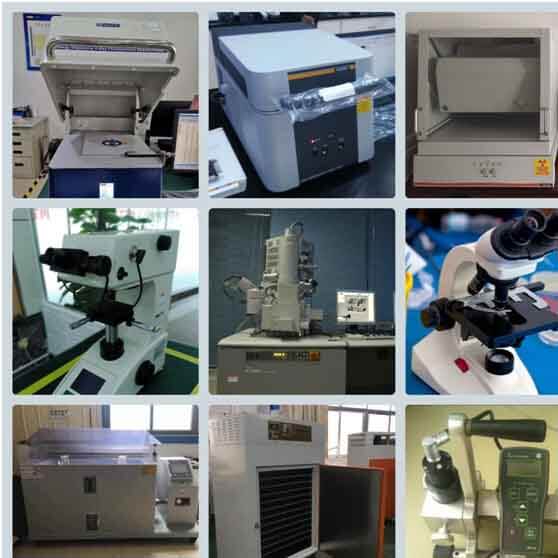
Sample Cases of Hard Gold Plating Processing

Matte Gold Plating
Introduction to the capabilities of matte gold plating:
Applicable materials
iron, steel, stainless steel, copper, aluminum alloy, magnesium alloy, titanium alloy, zinc alloy, Kovar alloy, tungsten steel, ceramics, etc.
Applicable plating types
matte gold plating, thick gold plating, hard gold plating, gold-cobalt alloy plating, etc.
Applicable processes
hanging plating, barrel plating, agitation plating, selective plating.
Supporting process:
sandblasting
Available colors:
gold, rose gold, champagne gold, titanium gold, etc.
Available film thickness
0.025μm-3μm gold layer thickness.
Maximum size
850mm.
Introduction to the Process of Matte Gold Plating
The applicable electroplating processes for matte gold plating include rack plating, barrel plating, continuous plating, and vibratory plating.
The thickness of the matte gold plating layer needs to be clarified. Generally, it ranges from 0.5 microns (0.125 μm) to 120 microns (3 μm). Therefore, it is not uncommon for customers to request gold plating thickness in millimeters, but this is a sign of being a novice in the field of gold plating. (PS: 1 millimeter = 100 microns = 40000 gauge; in addition, the gauge is very close to the microinch. So, for some drawings that use microinch as the unit, if a gold layer thickness of 20 micro inches is required, it can be directly expressed as a plating of 20 gauge gold.)
The total thickness of matte gold plating varies for different materials of workpieces. For example, for aluminum alloy materials, it is usually required to perform secondary zinc immersion plating, followed by nickel plating, and then gold plating. Depending on the usage requirements of the workpiece, copper or nickel strike, or electroless nickel plating may also be added. Therefore, for precision parts with tolerance requirements, the remaining size of the plating thickness needs to be considered before gold plating. Generally, the total thickness of hard gold plating ranges from 1 to more than 20 microns.
The cost calculation of matte gold plating mainly depends on the cost of the gold consumed, which accounts for about 40-50% of the total cost. This cost is mainly determined by the surface area of the workpiece that needs to be gold-plated and the thickness of the gold layer. In addition, the cost of gold plating is affected by different materials, the shape and size of the workpiece, the difficulty of electroplating, the quantity of single-batch workpieces, and whether it is a one-time order or a long-term order. Therefore, usually, the price of electroplating is negotiable, and the subjective proportion is very high.
Process Flow for Matte Gold Plating
Hanging Plating
- Sandblasting
- Pre-plating inspection
- Chemical degreasing
- Hot water washing
- Running water cleaning
- Acid washing
- Running water washing
- Immerse the plating parts that need to be electroplated in an extremely dilute sodium carbonate solution; passivation and drying for plating parts that do not need to be electroplated
- Hang the plating parts
- Electrochemical degreasing
- Running water washing
- Activation
- Running water washing
- Pure water washing
- Pre-gold plating
- Gold recovery cleaning
- Secondary gold recovery cleaning
- Immersion
- Rinse
- Pure water rinse
- Hot pure water immersion
- Vibration drying
- Inspection.
Roll Plating
- Sandblasting
- Pre-plating inspection
- Chemical degreasing (for contacting bodies with heavy oil pollution, organic solvents are used for degreasing and cleaning)
- Hot water washing
- Running water cleaning
- Acid washing
- Running water washing
- Immerse the plating parts that need to be electroplated in an extremely dilute sodium carbonate solution; passivation and drying for plating parts that do not need to be electroplated
- Pour the plating parts into the roller
- Electrochemical degreasing
- Running water washing
- Activation
- Running water washing
- Pure water washing
- Electroplating nickel (copper plating is performed in advance for brass parts)
- Nickel recovery cleaning
- Running water washing
- Pure water washing
- Pre-gold plating
- Thick gold plating (hard gold plating)
- Secondary gold recovery cleaning
- Running water washing
- Pure water washing
- Hot pure water washing
- Drying (temperature not exceeding 120℃)
- Post-plating inspection.
Vibratory Plating:
- Sandblasting
- Pre-plating inspection
- Chemical degreasing (organic solvents and ultrasonic cleaning are used for pre-cleaning bodies with deep holes or blind holes)
- Hot water washing
- Running water cleaning
- Acid washing
- Running water washing
- Passivation and drying
- Load the plating parts into the vibrating screen
- Chemical degreasing
- Electrolytic degreasing (can be carried out in the chemical degreasing tank)
- Immersion
- Rinse
- Activation
- Immersion
- Rinse
- Pure water rinse
- Nickel plating in the plating tank (copper plating is performed in advance for brass parts)
- Nickel recovery cleaning
- Immersion
- Rinse
- Pure water rinse
- Pre-gold plating
- Gold recovery cleaning
- Secondary gold recovery cleaning
- Immersion
- Rinse
- Pure water rinse
- Hot pure water immersion
- Vibration drying
- inspection.
Display of Production Equipment for Matte Gold Plating Processing
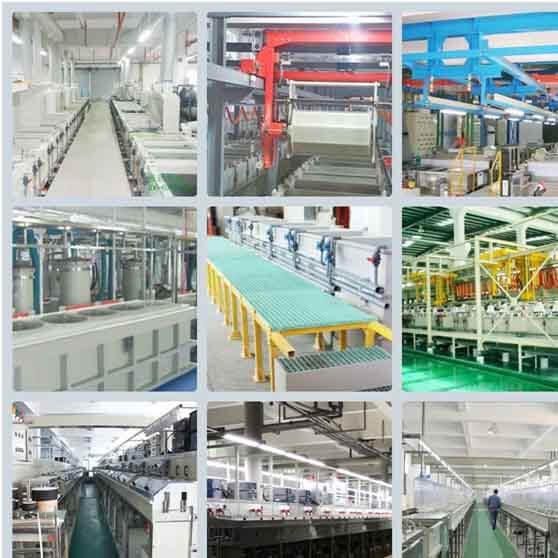
Display of inspection equipment for dull gold plating processing.
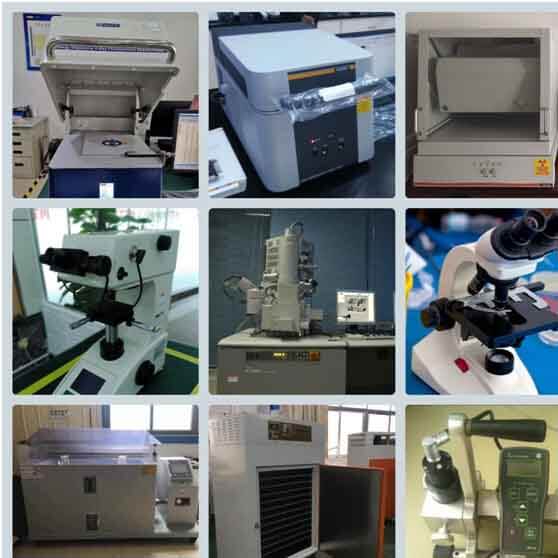
Sample Cases of Matte Gold Plating Processing
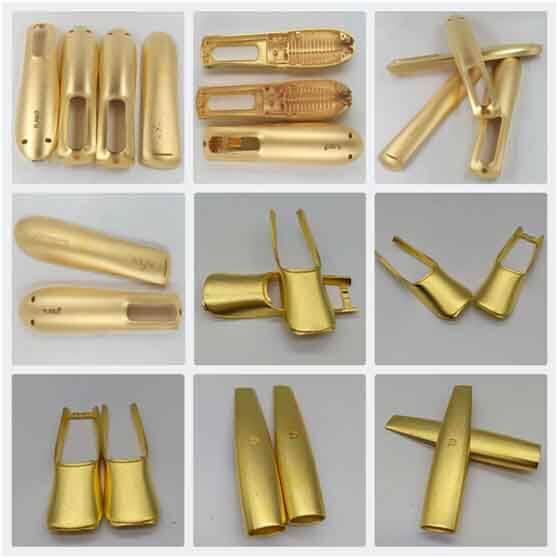
Palladium Plating
Introduction to Palladium Plating | Palladium Gold Plating | Palladium Nickel Plating | Nickel Palladium Gold Plating | Electroplating Palladium Process
Palladium alloy coatings are more resistant to organic pollution than pure palladium, and other properties are also superior to pure palladium coatings. The main properties of palladium-nickel alloy coatings with a palladium content of around 80% are resistance to sulfidation, creep corrosion, and bending extension, with hardness superior to hard gold coatings (the surface hardness of hard gold plating is about HV120, while the surface hardness of palladium plating can reach HV450).
Palladium and palladium alloy electroplating solutions mainly include the ammonia chloride system, amino sulfonic acid system, and amine chloride system. Among them, the ammonia chloride system plating solution (mainly containing dichlorodiammine palladium 10 to 40 g/L, ammonium chloride 10 g/L, ammonium sulfate 25 g/L, solution pH value 8.5 to 9) has simple operation and is suitable for palladium and palladium-nickel alloy plating of electrical contact elements. The chemical palladium plating solution contains dichlorodiammine palladium 7.5 g/L, ethylenediaminetetraacetic acid (EDTA) 8 g/L, and hydrazine 1 mol/L. The resulting palladium coating has a purity of 99.4%, a Vickers hardness of 150 to 350, and a gray-white color.
Palladium Plating Process | Palladium Plating | Palladium-Nickel Plating | Nickel-Palladium-Gold Plating | Electroplating Palladium Process
Steel parts plating palladium process flow
- Pre-treatment before electroplating
- copper plating or silver plating
- cleaning
- polishing
- organic solvent cleaning
- electrochemical degreasing
- cleaning
- activation
- cleaning
- palladium plating
- cleaning
- polishing
- cleaning
- drying
- hanging fixture
- inspection packaging;
Copper and copper alloy parts plating palladium process flow
- Polishing
- organic solvent cleaning
- silver plating
- cleaning
- polishing
- electrochemical degreasing
- cleaning
- activation
- cleaning
- palladium plating
- cleaning
- polishing
- cleaning
- drying
- hanging fixture
- inspection packaging.
Palladium Plating | Gold Palladium Plating | Palladium Nickel Plating | Nickel Palladium Gold Plating | Electroplating Palladium Pricing:(The following prices are for reference only)
Minimum expenditure
The minimum expenditure for palladium plating is generally between 100-120 USD.
Charged by surface area
When the workpiece is large or the batch size is large, the cost of palladium plating will eventually be calculated based on the surface area! The two main factors that determine the cost of a single batch of palladium plating are as follows:
Thickness of the palladium layer
The thicker the palladium layer, the higher the cost of palladium consumption, and therefore, the overall cost of palladium plating increases almost proportionally; the calculation method is usually to calculate the cost of palladium consumption, and then calculate the total cost based on the proportion of palladium cost, which is usually between 50-70%.
Quantity of single batch processing
A principle is that the smaller the quantity, the higher the unit price; for example, if there is only one small piece, then it will cost around 100-120 USD. For the same piece, if there are 1000 pieces, it is possible to achieve 0.1 USD/piece.
Pd Plating | Pd-Au | Pd-Ni | Ni-Pd-Au | Electroplating Pd | Production Instrument Display
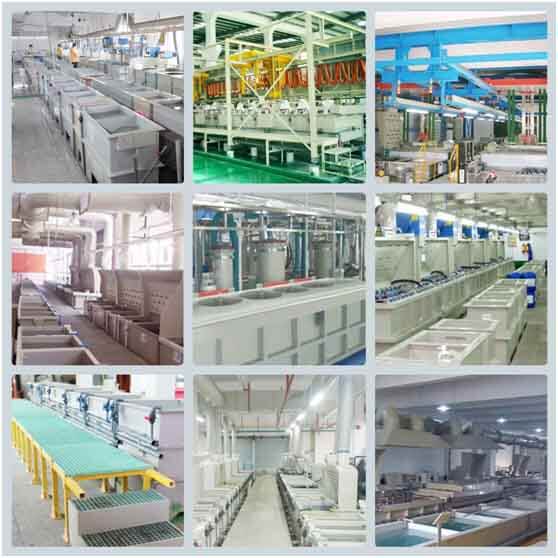
Commentary: Due to the small size of the workpieces that are plated with palladium (or very small), and the market demand is not large, so far, there has been no large-scale automatic production line for palladium plating processing. All are manually operated lines.
Hanging plating
suitable for larger workpieces that require a thicker coating. The advantage is that the plating speed is fast, and the surface appearance of the plated workpiece is relatively better! The disadvantage is that the cost is high (mainly labor costs, hanging and taking off are manually operated).
Rolling plating
suitable for small workpieces that are not angular, heavy, and not afraid of collision. The advantages are high production efficiency and low cost. And because the plating speed is slow, the control of the film thickness can be more precise.
Shake plating
a process derived from rolling plating, suitable for ultra-small, ultra-fine, ultra-thin, and easily deformed workpieces.
Palladium plating processing | Palladium gold plating | Palladium nickel plating | Nickel palladium gold plating | Palladium electroplating | Display of testing instrument for palladium plating processing.
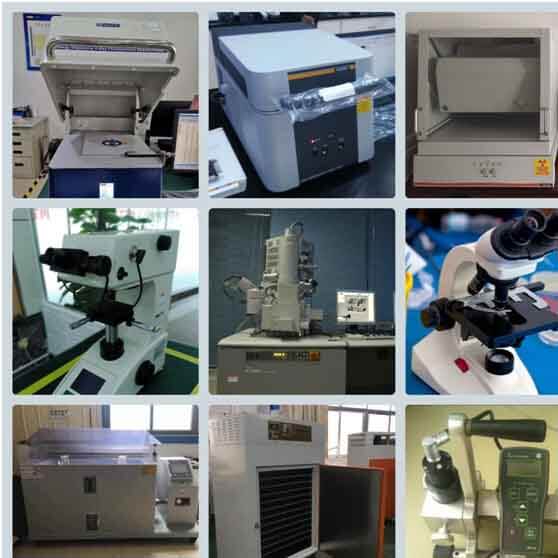
Palladium plating processing | Palladium gold plating | Palladium nickel plating | Nickel palladium gold plating | Palladium electroplating | Sample cases
Jewelry
Palladium gold plating can be used to provide a durable and corrosion-resistant coating on jewelry items such as rings, necklaces, and bracelets.
Electronic components:
Palladium nickel plating can be used to protect electronic components from corrosion and wear, making them more reliable and long-lasting.
Aerospace components
Palladium electroplating can provide high-quality surface protection for aerospace components, such as turbine blades and engine parts.
Medical implants
Palladium plating can be used to coat medical implants, such as pacemakers, to provide a biocompatible and corrosion-resistant surface.
Automotive parts
Nickel palladium gold plating can be used to provide a decorative and durable finish on automotive parts such as rims, emblems, and trim.
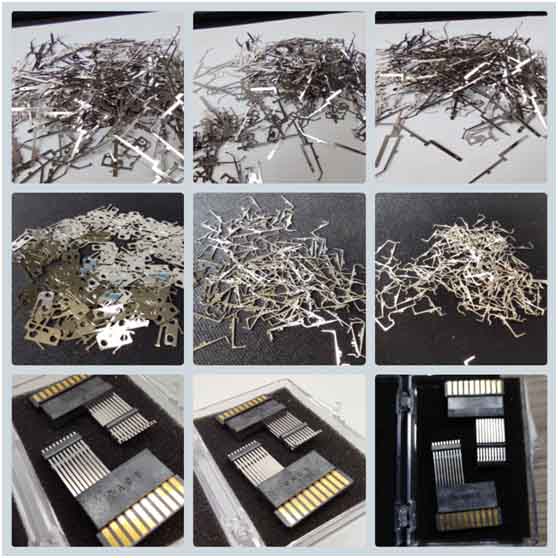
Pearl Gold Plating
Introduction to the Process of Pearl Gold Plating
In the pre-processing stage of pearl gold plating, sandblasting or pearl nickel plating is usually used as the base. In addition, the brightness needs to be controlled during the gold plating process.
The applicable electroplating processes for pearl gold plating include hanging plating, rolling plating, and shaking plating.
The film thickness of pearl gold plating refers specifically to the thickness of the gold layer and is generally between 0.5 microns (0.125μm) and 120 microns (3μm). Therefore, it is not uncommon to encounter customers who ask for gold plating thickness in millimeters, which indicates a lack of understanding of the gold plating process. (PS: 1 millimeter = 100 silk = 1000 microns = 40000 gauges; the gauge unit is very close to microinches, so if a drawing requires a gold layer thickness of 20 microinches, it can be directly stated as 20 gauges of gold).
The overall film thickness of pearl gold plating depends on the material of the workpiece and requires different pre-treatment methods. For example, for aluminum alloy materials, it is usually necessary to perform secondary zinc immersion and nickel plating before gold plating. Depending on the usage requirements of the workpiece, copper acid/copper alkali/copper pyrophosphate plating, or impact nickel plating may be required. Therefore, for precision parts with tolerance requirements, the residual size of the film thickness needs to be considered before gold plating. Generally, the overall film thickness of hard gold plating is between 1-20 microns.
The cost calculation of pearl gold plating mainly depends on the cost of the gold consumed (which accounts for about 40-50% of the total cost), which in turn depends mainly on the surface area of the workpiece and the thickness of the gold layer required for plating. In addition, the cost of gold plating varies depending on the material, shape, and size of the workpiece, the difficulty of electroplating, the quantity of single batch workpieces, and whether it is a one-time or long-term order. Therefore, the quotation for electroplating is usually negotiated on a case-by-case basis, and the subjective proportion is very high!
Process of Pearl Gold Plating
Hanging Plating
- Sandblasting
- pre-plating inspection
- chemical degreasing
- hot water washing
- flowing water cleaning
- acid washing
- flowing water washing
- immerse the plating parts that will be electroplated in a very dilute solution of sodium carbonate, and those parts that do not need urgent electroplating should be passivated and dried
- hang the plating parts
- electrochemical degreasing
- flowing water washing
- activation
- flowing water washing
- pure water washing
- pearl nickel plating
- nickel recovery cleaning
- flowing water washing
- pure water washing
- pre-gold plating
- gold recovery cleaning
- second gold recovery cleaning
- immersion washing
- dripping washing
- pure water dripping washing
- hot pure water immersion washing
- vibration drying
- inspection.
Roll Plating
- Sandblasting
- pre-plating inspection
- chemical degreasing (for contact parts with heavy oil pollution, use organic solvent degreasing cleaning)
- hot water washing
- flowing water cleaning
- acid washing
- flowing water washing
- immerse the plating parts that will be electroplated in a very dilute solution of sodium carbonate, and those parts that do not need urgent electroplating should be passivated and dried
- pour the plating parts into the drum
- electrochemical degreasing
- flowing water washing
- activation
- flowing water washing
- pure water washing
- pearl nickel plating (copper-plated in advance for brass parts)
- nickel recovery cleaning
- flowing water washing
- pure water washing
- pre-gold plating
- thick gold plating (hard gold plating)
- second gold recovery cleaning
- flowing water washing
- pure water washing
- hot pure water washing
- drying (temperature not exceeding 120℃)
- post-plating inspection.
Display of Production Equipment for Pearl Gold Plating Processing
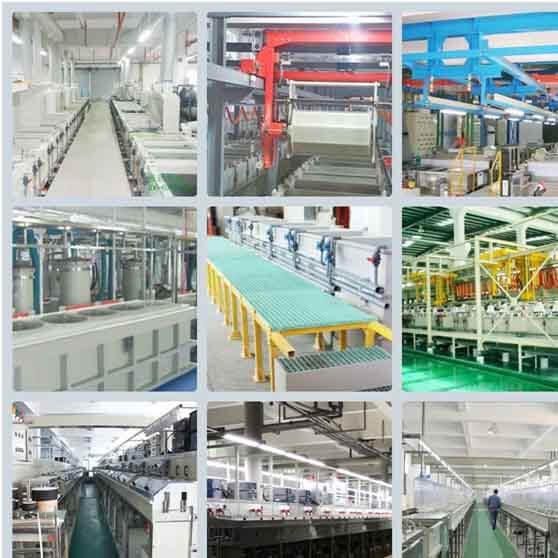
Display of Inspection Equipment for Pearl Gold Plating Processing.
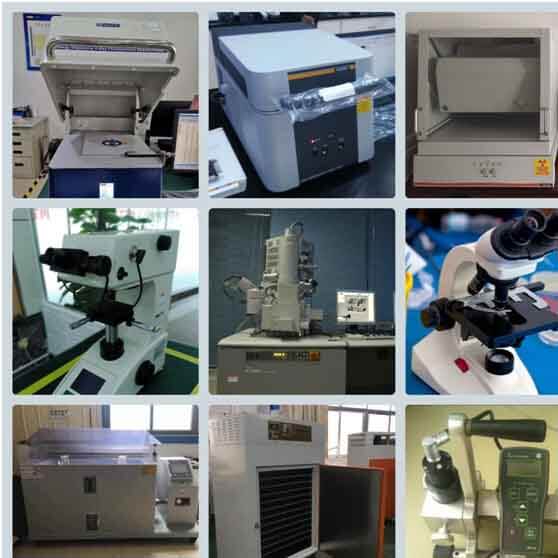
Pearl Gold Plating Process Sample Cases
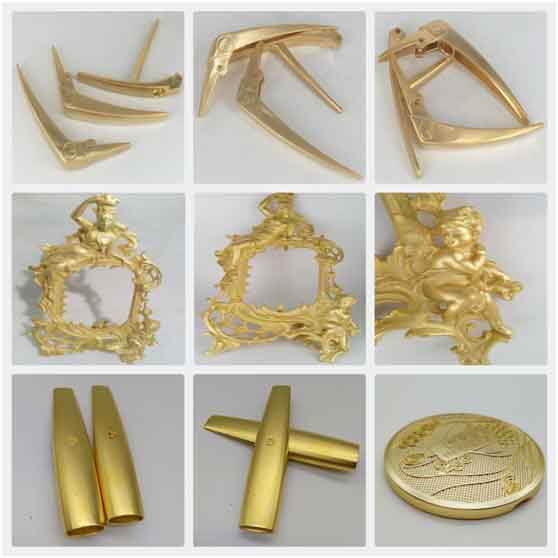
Real Gold plating
Overview of One-Stop Real Gold Plating Capabilities:
Suitable Materials: Copper/copper alloys, aluminum/aluminum alloys, iron/iron alloys, steel/stainless steel, zinc/zinc alloys, magnesium/magnesium alloys, titanium/titanium alloys, plastic parts, etc. Additionally, for materials such as tungsten steel, precious alloys, ceramics, glass, etc., Opti-Plating can also provide one-stop Real Gold plating services.
Workpiece Size: 0.1mm-1000mm (Workpieces within 1 meter can be handled). Salt Spray Requirements: Different materials have different achievable salt spray durations. OptiPlating can meet salt spray testing requirements of 100 hours or more.
Real Gold plating/Real Gold plating Process Introduction
Principle of Real Gold plating: A trace amount of cobalt element is added to the gold salt (gold has a hardness of 20, while cobalt has a hardness of 125). Therefore, the industry term for hard Real Gold plating is often referred to as gold-cobalt alloy plating.
Applicable electroplating processes for Real Gold plating: Hanging plating, barrel plating, agitation plating, continuous plating, and vibratory plating can all be used. However, it should be noted that hard Real Gold plating has poor coverage, making it difficult to achieve plating inside deep holes or blind holes.
Gold layer thickness: It is important to clarify that the term “thickness” here specifically refers to the thickness of the gold layer. Generally, it ranges from 0.5 μm to 120 μm (0.5 mu to 120 mu). Therefore, it is common to encounter customers who request Real Gold plating with a thickness of several millimeters. In reality, it can be assured that such a request indicates a lack of understanding of the Real Gold plating process. (Note: 1 millimeter = 100 microinches = 40000 mu; additionally, the unit “mu” is very close to microinch. Thus, for some drawings that use micro inches as the unit, if a gold layer thickness of 20 micro inches is required, it can be directly stated as Real Gold plating with a thickness of 20 mu.)
Overall plating thickness: Different materials of the workpiece require different pretreatment methods during the Real Gold plating process. For example, in the case of aluminum alloy materials, it is common to perform zinc immersion after nickel plating and then proceed with Real Gold plating. However, depending on the usage requirements of the workpiece, additional processes such as copper acid plating/alkaline plating/pyrophosphate plating or strike nickel plating may be necessary. Therefore, for precision parts with tolerance requirements, the residual dimension for plating thickness needs to be considered before Real Gold plating. Generally, the overall plating thickness for hard Real Gold plating ranges from 1 μm to over 20 μm.
Wear resistance of Real Gold plating: Hard Real Gold plating does not mean it is immune to wear. It simply has a higher surface hardness compared to pure gold or soft gold, making it more resistant to wear. The surface hardness of hard Real Gold plating is generally around 120 Vickers hardness.
Cost calculation for Real Gold plating: The cost of hard Real Gold plating mainly depends on the cost of the gold consumed (which accounts for approximately 40-50% of the total cost), which, in turn, depends on the surface area of the workpiece and the thickness of the gold layer needed. Additionally, the cost of Real Gold plating is influenced by factors such as the material, shape, and size of the workpiece, the difficulty of electroplating, the quantity of batched workpieces, and whether it is a one-time order or a long-term order. Consequently, electroplating pricing is typically negotiated on a case-by-case basis, and subjective factors play a significant role in determining the final quote.
Real Gold plating/Real Gold plating Process Flow
Rack Plating
- Pre-plating inspection
- Chemical degreasing
- Hot water rinse
- Flow rinse
- Acid etching
- Flow rinse
- Immerse the parts to be plated in a very dilute sodium carbonate solution for the subsequent plating; for parts that do not require immediate plating, passivation and drying are performed
- Hang the parts for electrochemical degreasing
- Flow rinse
- Activation
- Flow rinse
- DI water rinse
- Nickel plating
- Nickel recovery cleaning
- Flow rinse
- DI water rinse
- Pre-Real Gold plating
- Real Gold plating recovery cleaning
- Secondary gold recovery cleaning
- Immersion rinse
- Cascade rinse
- DI water cascade rinse
- Hot DI water immersion rinse
- Vibrational drying
- Inspection.
Barrel Plating
- Pre-plating inspection
- Chemical degreasing (for parts with heavy oil contamination, pre-clean with organic solvent)
- Hot water rinse
- Flow rinse
- Acid etching
- Flow rinse
- Immerse the parts to be plated in a very dilute sodium carbonate solution for the subsequent plating; for parts that do not require immediate plating, passivation and drying are performed
- Transfer the parts into the barrel
- Electrochemical degreasing
- Flow rinse
- Activation
- Flow rinse
- DI water rinse
- Nickel plating (brass parts pre-plated with copper)
- Nickel recovery cleaning
- Flow rinse
- DI water rinse
- Pre-Real Gold plating
- Thick gold (hard gold) plating
- Secondary gold recovery cleaning
- Flow rinse
- DI water rinse
- Hot DI water rinse
- Drying (temperature not exceeding 120°C)
- Post-plating inspection.
Vibration Plating
- Pre-plating inspection
- Chemical degreasing (for parts with deep or blind holes, pre-clean with organic solvent and ultrasonic cleaning)
- Hot water rinse
- Flow rinse
- Acid etching
- Flow rinse
- Passivation and drying
- Place the parts in a vibrating sieve
- Chemical degreasing
- Electrolytic degreasing (can be done in the chemical degreasing tank)
- Immersion rinse
- Cascade rinse
- Activation
- Immersion rinse
- Cascade rinse
- DI water cascade rinse
- Nickel plating (brass parts pre-plated with copper)
- Nickel recovery cleaning
- Immersion rinse
- Cascade rinse
- DI water cascade rinse
- Pre-Real Gold plating
- Real Gold plating recovery cleaning
- Secondary gold recovery cleaning
- Immersion rinse
- Cascade rinse
- DI water cascade rinse
- Hot DI water immersion rinse
- Vibrational drying
- Inspection.
Real Gold plating/Real Gold plating Process Instrument Showcase
Ultrasonic Cleaning Machine
Used for thorough cleaning of workpieces to remove dirt and contaminants.
Electrocleaning Tank
Utilized for electrolytic cleaning to remove residual contaminants and prepare the surface for plating.
Real Gold Plating Tank
Contains the Real Gold plating bath with a gold-containing electrolyte solution.
Nickel Plating Tank
Used for nickel plating as an intermediate layer before
Other Plating Tanks
Depending on specific requirements, additional tanks may be present for pre-plating processes such as copper plating or post-plating processes for rinsing and cleaning.
DC Power Supply
Provides the direct current necessary for the electroplating process.
Drying Oven
Used for drying the workpieces after various rinsing and cleaning stages.
Vibrational Dryer
Enables rapid drying of the plated workpieces using vibrations.
Polishing/Buffing Machines
Employed for post-plating surface finishing to achieve desired shine and smoothness.
Inspection Tools
Various tools and instruments for quality control and inspection of the plated workpieces.
Ventilation Systems
Ensure proper air circulation and removal of fumes and gases generated during the plating process.
Personal Protective Instrument (PPE)
Includes gloves, goggles, and protective clothing to ensure operator safety.
Temperature Controllers
Monitor and regulate the temperature of plating baths.
pH Meters
Measure and control the acidity or alkalinity of plating solutions. Thickness Measurement Tools: Used to measure the thickness of the gold layer on the plated workpieces.
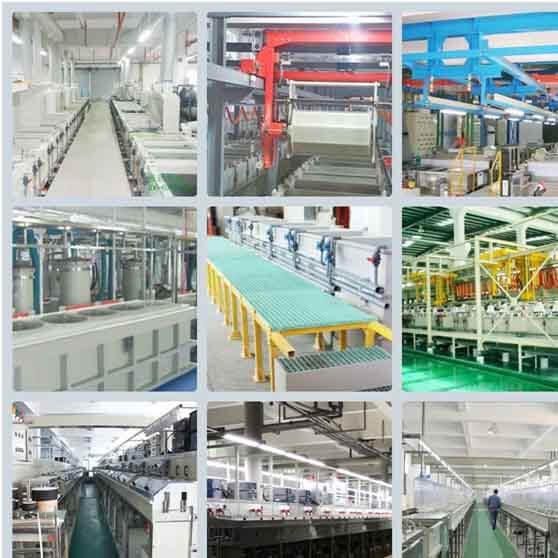
Real Gold plating/Real Gold plating Process Inspection Instrument Showcase
X-ray Fluorescence (XRF) Analyzer
Utilized for non-destructive measurement of the thickness of the gold layer on the plated workpieces.
Eddy Current Tester
Measures the thickness of non-magnetic coatings, including gold, on conductive substrates.
Pull-Off Adhesion Tester
Determines the adhesion strength of the gold layer by applying a controlled force to pull it off the substrate.
Cross-Cut Tester
Evaluates the adhesion of the gold layer by making precise cuts and examining the coating's integrity.
Scanning Electron Microscope (SEM)
Provides high-resolution imaging and analysis of the gold-plated surface for quality inspection and defect identification.
Optical Microscope
Used for visual examination and magnification of the plated surface to detect any irregularities or imperfections.
Salt Spray Test Chamber
Conducts accelerated corrosion testing by subjecting the plated workpieces to a salt fog environment to evaluate their resistance to corrosion.
Humidity Chamber
Simulates high humidity conditions to assess the corrosion resistance of the gold-plated surface.
Four-Point Probe
Measures the electrical resistance of the gold layer to determine its conductivity and ensure proper plating quality.
Profilometer
Evaluates the roughness of the gold-plated surface by measuring the height variations across the surface.
Magnifying Glass/Loupe
Used for detailed visual inspection of the plated surface to identify any defects, scratches, or inconsistencies.
Light Box
Provides uniform and controlled lighting conditions for enhanced visual examination of the plated workpieces.
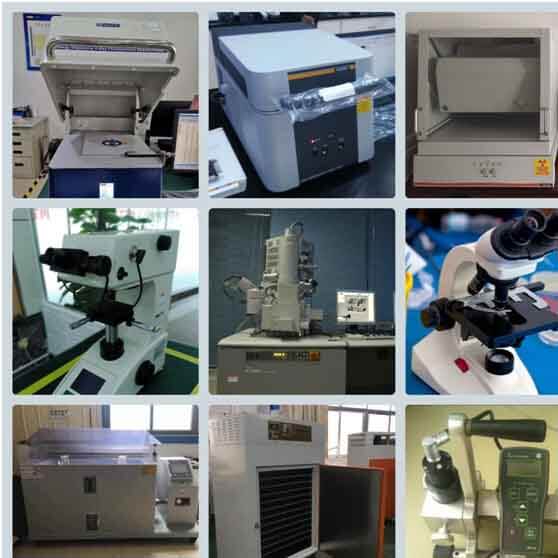
Real Gold plating/Real Gold plating Process Sample Cases
Gold-plated Necklaces
Elegant necklaces with intricate designs, where the base material is typically copper or brass, and the Real Gold plating provides a luxurious and durable finish.
Gold-plated Rings
Stunning rings featuring gemstones or unique patterns, with a gold-plated surface that enhances their beauty and adds a touch of luxury.
Gold-plated Bracelets
Stylish bracelets made from various materials such as stainless steel or silver, enhanced with a layer of Real Gold plating for an exquisite appearance.
Gold-plated Statues
Artistic sculptures or figurines with detailed craftsmanship, where the Real Gold plating accentuates the intricate details and adds a regal touch.
Gold-plated Picture Frames
Ornate frames with a gold-plated surface, elevating the presentation of cherished photographs or artwork.
Gold-plated Vases
Elegant vases with a gold-plated finish, enhancing their aesthetic appeal and making them an eye-catching centerpiece.
Gold-plated Connectors
Electrical connectors, commonly used in electronic devices and instrument, featuring Real Gold plating to ensure reliable conductivity and corrosion resistance.
Gold-plated PCBs (Printed Circuit Boards)
PCBs used in high-end electronics, where Real Gold plating on certain contact areas provides excellent electrical performance and long-term durability.
Gold-plated Watch Cases
Watch cases made from stainless steel or other materials, coated with a layer of Real Gold plating to achieve a luxurious and timeless appearance.
Gold-plated Watch Hands and Hour Markers
Delicate watch hands and hour markers featuring Real Gold plating, enhancing readability and adding a touch of elegance to timepieces.
Gold-plated Emblems and Badges
Decorative emblems and badges on vehicles, coated with Real Gold plating for a sophisticated and distinctive look.
Gold-plated Interior Trim
Interior accents and trim pieces, such as buttons, knobs, or dashboard details, with a gold-plated surface, elevating the interior aesthetics of automobiles.

Rolled gold plating
Overview of Maine’s one-stop thick gold plating capabilities
Materials that can be processed: copper/copper alloy, aluminum/aluminum alloy, iron/iron alloy, steel/stainless steel, zinc/zinc alloy, magnesium/magnesium alloy, titanium/titanium alloy, plastic parts, etc. In addition, tungsten steel, can-forest alloy, ceramics, glass, and other materials can also be processed with one-stop gold plating.
Workpiece size: 0.1mm-1000mm (workpieces within 1 meter can be processed).
Gold layer thickness: 1 mark (0.025μm) – 120 marks (3μm).
Salt spray requirements: Different materials can achieve different salt spray durations; salt spray testing requirements of more than 100 hours can be achieved.
Introduction to the Process of Rolled gold Plating
The process characteristics of rolled gold plating are as follows
The current for roll plating is transmitted directly.
Roll plating is the process of collecting scattered small parts inside the rolling drum.
Advantages and disadvantages of rolled gold plating (compared to hanging plating gold):
Uniformity of gold plating layer
The thickness of the gold plating layer is relatively uniform with little fluctuation.
The appearance of the gold plating layer
In the roll plating process, the workpieces will constantly collide with each other, leaving some collision marks on the surface of the workpiece. Therefore, the surface of rolled gold plating is often not as smooth and bright as hanging plating gold.
Production efficiency
Rolled gold plating only requires the workpieces to be poured into the rolling drum, saving a lot of time for hanging and removing the workpieces. At the same time, rolled gold plating is not limited by the capacity of hanging tools. For a large number of small parts, several thousand or tens of thousands of parts can be processed at once, making the efficiency of roll plating much higher than hanging plating.
Price and cost
Rolled gold plating saves a lot of labor and greatly improves production efficiency. Therefore, overall, rolled gold plating is cheaper than hanging plating gold. In general, for the same workpiece, the cost of roll plating is about 80%-90% of that of hanging plating.
Rolled gold plating Processing, Process Flow
- Pre-plating inspection
- Chemical degreasing (organic solvent cleaning is used for contact parts with heavy oil contamination)
- Hot water rinse
- Water rinse
- Acid pickling
- Water rinse
- For the parts to be plated next, soak them in a very dilute sodium carbonate solution. For the parts that do not require immediate plating, passivate and dry them
- Pour the parts into the drum
- Electrochemical degreasing
- Water rinse
- Activation
- Water rinse
- Pure water rinse
- Electroless nickel plating (copper plating is used as a pre-plating process for brass parts)
- Nickel recovery cleaning
- Water rinse
- Pure water rinse
- Pre-gold plating
- Thick gold plating (hard gold)
- Second gold recovery cleaning
- Water rinse
- Pure water rinse
- Hot pure water rinse
- Drying (temperature not exceeding 120℃)
- Post-plating inspection.
Display of Production Equipment for Gold Roll Plating Processing.
Chemical Degreasing Equipment
This equipment is used for removing grease and contaminants from the workpieces before plating. It may include ultrasonic tanks, spray systems, or immersion tanks.
Hot Water Rinse Equipment
This equipment provides a controlled supply of hot water for rinsing the workpieces and removing cleaning solutions effectively. It can include hot water rinse tanks or spray systems.
Acid Cleaning Equipment
Acid cleaning tanks or systems are used for the removal of oxide layers, scale, and surface impurities from the workpieces. These tanks are equipped with appropriate safety measures for handling acid solutions.
Sodium Carbonate Solution Soaking Equipment
Workpieces requiring sodium carbonate soaking are typically immersed in tanks or containers with a controlled dilute solution of sodium carbonate. These containers may have agitation mechanisms for proper soaking.
Drum or Barrel Plating Equipment
The workpieces are placed into a rotating drum or barrel for the plating process. This equipment ensures proper immersion and contact with plating solutions. The drum may have adjustable speed controls and agitation mechanisms for uniform plating.
Electrochemical Degreasing Equipment
Electrochemical degreasing is often performed inside the drum or barrel. This equipment utilizes an electrolyte solution and electrodes to remove remaining grease and contaminants from the workpieces.
Activation Equipment
Activation tanks or systems are used for applying activation solutions to the workpieces, preparing the surfaces for plating. The equipment may include tanks, dip systems, or spray systems.
Electroless Nickel Plating Equipment
For electroless nickel plating, dedicated plating tanks or systems are used. These systems provide controlled deposition of nickel onto the workpiece surfaces.
Gold Plating Equipment
Gold plating tanks or systems are used for applying a thick layer of gold onto the surfaces of the workpieces. These tanks may include agitation mechanisms, temperature controls, and precise deposition controls.
Cleaning and Rinsing Equipment
After plating, cleaning and rinsing equipment is used for recovery cleaning and rinsing steps. It may include tanks, spray systems, or cascade rinsing systems for thorough cleansing.
Drying Equipment
Drying equipment such as drying ovens, hot air blowers, or vibrational dryers are used to remove moisture from the plated workpieces. This equipment ensures proper drying without damaging the plated surfaces.
Inspection Equipment:
Inspection stations are set up with visual examination tools, measuring instruments, and quality control measures to inspect the plated workpieces for adherence, thickness, and overall quality.
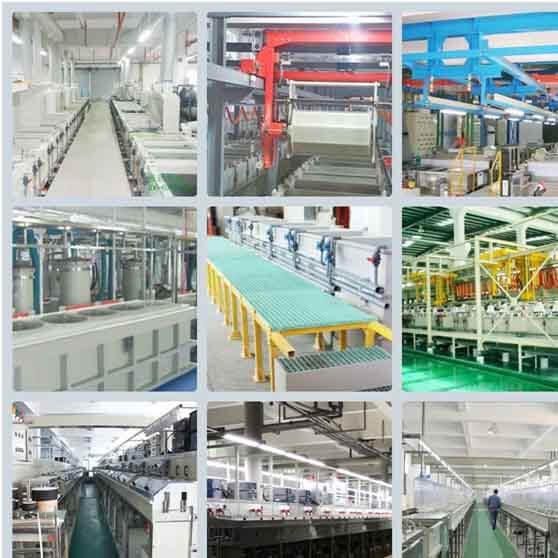
Display of Testing Equipment for Roller Gold Plating Process.
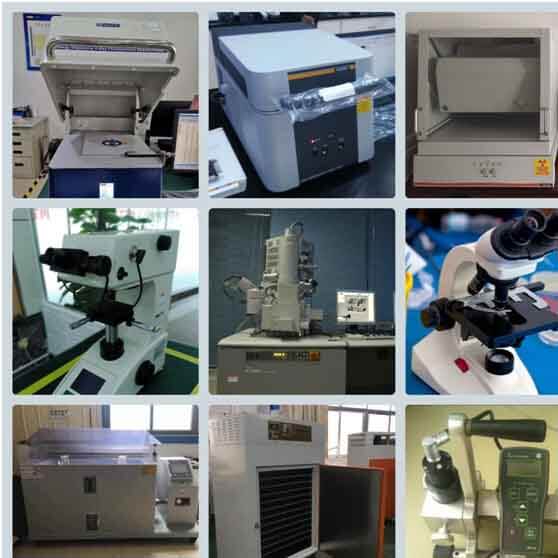
Sample cases of roller gold plating processing
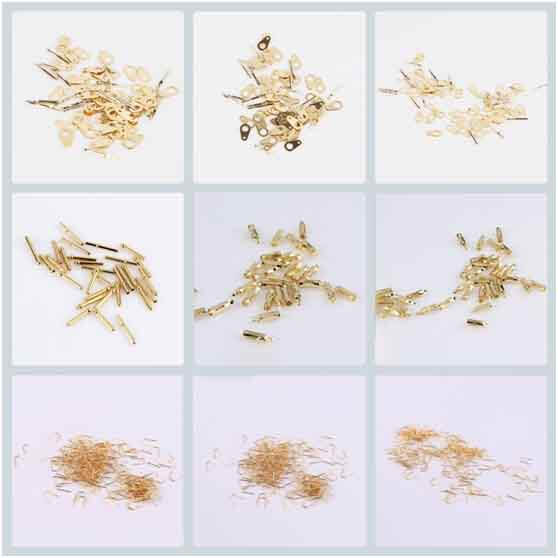
Thick Brass Gold Plating
Sample cases of roller gold plating processing
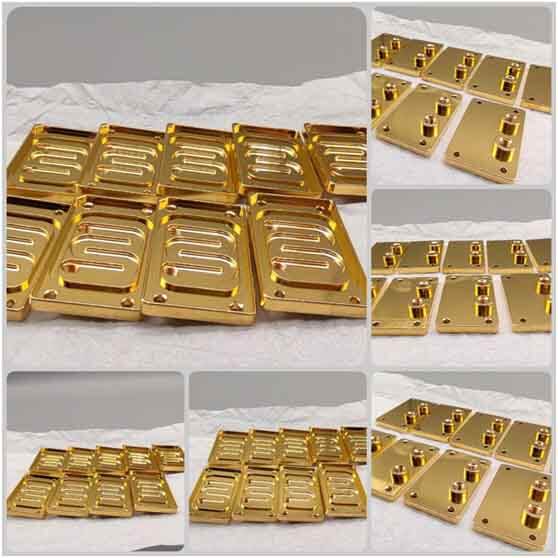
Base material: Brass
Plating Type: Gold plating/hard gold plating/thick gold plating/genuine gold plating
Process: Hanging plating
Thickness: Ni: 10μm; Au: 20 M (0.5μm)
Requirement: Neutral salt spray test for 48 hours;
Electroplating cost: 35 USD/square decimeter
Process flow
- Pre-plating inspection
- Chemical degreasing
- Hot water washing
- Flow washing
- Acid washing
- Flow washing
- Soak the plating parts to be electroplated next in a very dilute sodium carbonate solution. For the plating parts that are not urgently needed, passivation and drying after pickling
- Hang the plating parts
- Electrochemical degreasing
- Flow washing
- Activation
- Flow washing
- Pure water washing
- Electroplating nickel
- Nickel recovery and cleaning
- Flow washing
- Pure water washing
- Pre-plating gold
- Gold recovery and cleaning
- Secondary gold recovery and cleaning
- Immersion
- Rinse
- Pure water rinse
- Hot pure water immersion
- Vibration drying
- Inspection.
The principle of hard gold plating
Adding a trace amount of cobalt element to the gold salt (the hardness of gold is 20, and the hardness of cobalt is 125). Therefore, hard gold plating is commonly referred to as gold-cobalt alloy in the industry!
Applicable electroplating processes for hard gold plating
Hanging plating, rolling plating, shaking plating, continuous plating, vibrating plating, etc. However, it should be noted that the positioning accuracy of hard gold plating is poor. For parts with deep holes or blind holes, it is often difficult to plate inside the holes.
Thickness of hard gold plating
It should be noted that the thickness here specifically refers to the thickness of the gold layer! Generally between 0.5 M (0.125μm) -120 M (3μm); Therefore, you will often encounter some customers who say they want to gold plate a few millimeters thick, to be honest, it can be confirmed that they are still in the early stage of gold plating technology. (PS: 1 millimeter = 100 silk = 1000 micrometers = 40000 M; In addition, the unit M is very close to microinch, so for some drawings that use microinch as the unit, if the requirement for gold layer thickness is 20 microinch, it can be directly said to gold plate 20 M.)
Thick gold plating
Overview of one-stop thick gold plating processing capabilities
Materials that can be processed include copper/copper alloy, aluminum/aluminum alloy, iron/iron alloy, steel/stainless steel, zinc/zinc alloy, magnesium/magnesium alloy, titanium/titanium alloy, plastic parts, etc. In addition, for materials such as tungsten steel, Kovar alloy, ceramics, glass, etc., Youdianet can also provide one-stop gold plating processing.
Workpiece size: 0.1mm-1000mm (workpieces within 1 meter can be processed)
Gold layer thickness: 1 mu (0.025μm) – 120 mu (3μm)
Salt spray requirements: Different materials have different achievable salt spray durations; it can achieve salt spray test requirements of over 100 hours.
Introduction to Thick Gold PlatingProcess
The principle of gold plating is to add a trace amount of cobalt element (the hardness of gold is 20, and the hardness of cobalt is 125) to the gold salt. Therefore, the industry term for hard gold plating is gold-cobalt alloy plating.
The applicable electroplating processes for gold plating include hanging plating, barrel plating, shake plating, continuous plating, and vibration plating. However, it should be noted that the positioning accuracy of hard gold plating is relatively poor, and it is often difficult to plate the inner holes of workpieces with deep or blind holes.
The thickness of gold plating: It should be noted that the thickness here refers specifically to the thickness of the gold layer, which is generally between 0.5 microns (0.125μm) and 120 microns (3μm). Therefore, customers who ask for gold plating in millimeters are often not very familiar with the gold plating process. (PS: 1 millimeter = 100 microns = 40000 Ma; in addition, the unit “Ma” is very close to microinch, so some drawings may use microinch as the unit, for example, if the gold layer thickness is required to be 20 microinches, it can be directly said to plate 20 Ma of gold).
The overall thickness of gold plating
In the process of gold plating, different materials of workpieces require different pre-treatment methods. For example, for aluminum alloy materials, after the second zinc plating, nickel plating is done, and then gold plating can be directly performed. However, depending on the usage requirements of the workpiece, additional plating of acid copper/alkaline copper/flashing copper, or impact nickel plating, may be necessary. Therefore, for precision parts with tolerance requirements, the remaining thickness of the coating should be considered before gold plating. Generally speaking, the overall thick gold plating is between 1-20 micrometers.
Wear resistance of gold plating
Hard gold plating does not mean it will not wear out. It only means that the surface hardness of hard gold plating is higher and more wear-resistant than pure gold or soft gold. The surface hardness of hard gold plating is generally around 120 Vickers hardness.
Cost accounting of gold plating
The cost of hard gold plating mainly depends on the cost of the consumed gold (which accounts for about 40-50% of the total cost), which in turn depends on the surface area of the workpiece and the thickness of the gold layer. In addition, the cost of gold plating is greatly affected by the material of the workpiece, the shape and size of the workpiece, the difficulty of electroplating, the quantity of the workpieces in a batch, and whether it is a one-time or long-term order. Therefore, the quotation for electroplating is usually a case-by-case negotiation, and the subjective proportion is very high.
Thick Gold Plating Process
The conventional process for thick gold plating is as follows: (taking the commonly used copper part chemical nickel-gold plating process as an example)
- Hanging
- acid washing and degreasing
- two-stage water washing
- micro-etching
- acid washing
- water washing
- pre-dip
- activation/catalysis
- post-dip
- chemical nickel plating
- two-stage water washing
- dip gold plating
- gold recovery solution
- water washing
- unhanging
Degreasing
Remove slight oxidation and impurities on the surface of the copper part, reduce the surface tension of the liquid, eliminate the air adsorbed on the copper surface, and allow the solution to spread on the surface to achieve a wetting effect.
Micro-etching
Remove the oxide on the copper surface, make the surface slightly rough, and provide a good combination for the remaining chemical nickel layer.
Acid washing
Remove the oxide on the copper surface after micro-etching, and present a fresh copper surface; clean the remaining liquid on the surface after micro-etching.
Pre-dip
Remove the oxide on the copper surface after micro-etching, and ensure that the copper surface enters the catalytic tank in a fresh state (without oxide), mainly to maintain the acidity of the catalytic tank and extend the life of the catalytic tank.
Catalysis
Through displacement reaction, a layer of palladium is produced on the copper surface, providing a self-catalytic surface for chemical nickel deposition.
Post-dip
Remove the ion palladium that may be adsorbed on the substrate or solder resist film to prevent permeation in the chemical nickel.
Chemical nickel plating
Provide a metal diffusion barrier layer between copper and gold; provide a corrosion-resistant layer and a weldable surface.
Production Equipment Showcase for Thick Gold Plating Processing
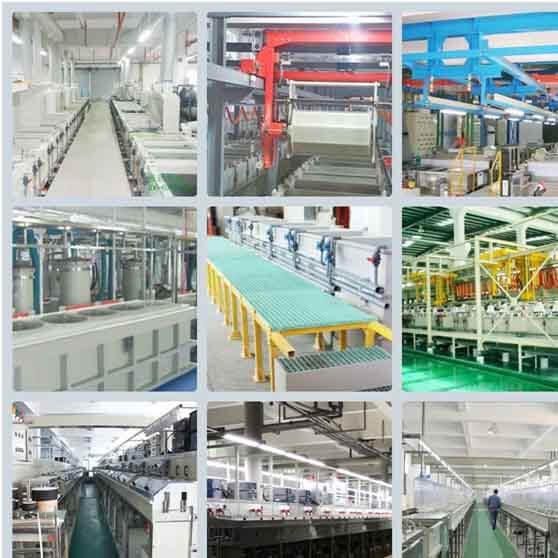
Display of Inspection Equipment for Thick Gold Plating Processing
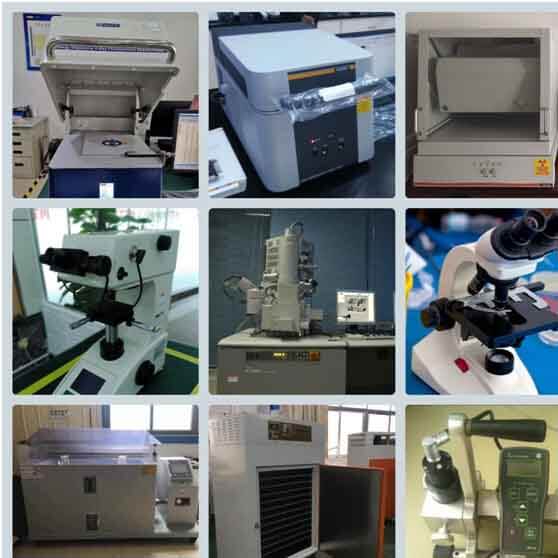
Sample cases of thick gold plating processing.
High-end jewelry
Some high-end jewelry appears luxurious, but what many people don't know is that it is actually made using a thick gold plating technique.
Electronic components
Thick gold plating is commonly used on electronic components such as connectors, switches, and printed circuit boards to improve conductivity and prevent corrosion.
Watchmaking
Thick gold plating is also used on the cases and straps of high-end watches to enhance their appearance and durability.
Automotive components
Thick gold plating can be used on automotive components such as emblems and trim to give them a high-end appearance and prevent corrosion.
Decorative items
Thick gold plating is often used on decorative items such as picture frames and figurines to give them a luxurious appearance.
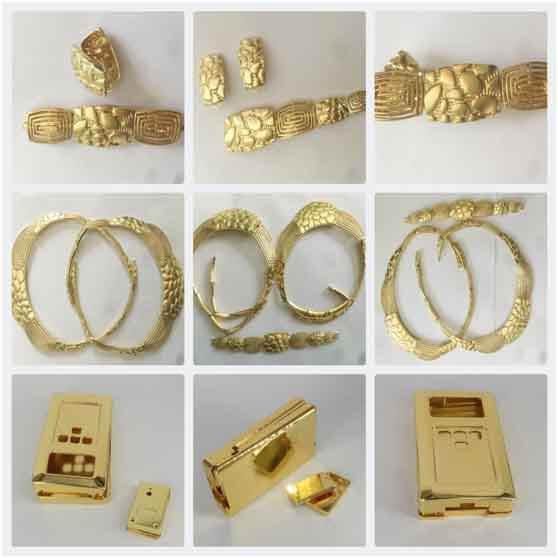
Free Sample
Explore Other Surface Finish
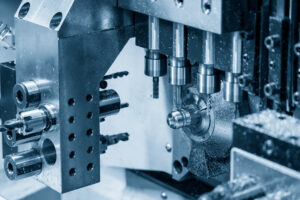
Swiss Turn Machining
Swiss Turn machining is one of the most common modern machining techniques. Its advantages of speed, convenience, and high precision make it highly favored by customers, leading to its widespread
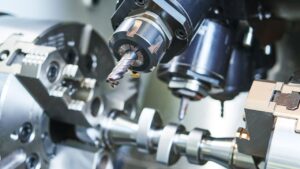
CNC Turning Services 101 – Know the Every Unknown
Get a detailed overview of CNC turning services. Explore the benefits, types, and materials involved in creating high-precision parts for various industries.
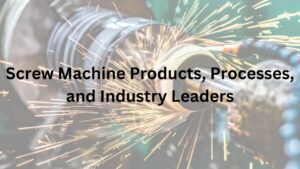
Screw Machine Products, Processes, and Industry Leaders
Explore comprehensive Swiss Machine Products guide covering tools, techniques, and top manufacturers. Master the art of precision manufacturing for optimal results.