Aluminum CNC Machining
Aluminum CNC Machining
Aluminium CNC cutting service
Aluminum CNC machining includes CNC milling aluminum, CNC turning aluminum, CNC milling and turning aluminum, CNC Swiss machining aluminum, CNC automatic lathe machining aluminum, CNC stamping aluminum, etc.
CNC Milling Aluminum
Aluminum milling is the machining of cutting aluminum workpieces using tools on a CNC machining center or milling machine to remove aluminum surface material and create shapes such as flat surfaces, grooves, holes, etc. Due to the easy machinability of aluminum, aluminum milling is a relatively straightforward and efficient machining method. Here are some advantages of aluminum milling: The advantages of aluminum milling include ease of machinability, high processing speed, a bright surface finish, corrosion resistance, and mature technology.

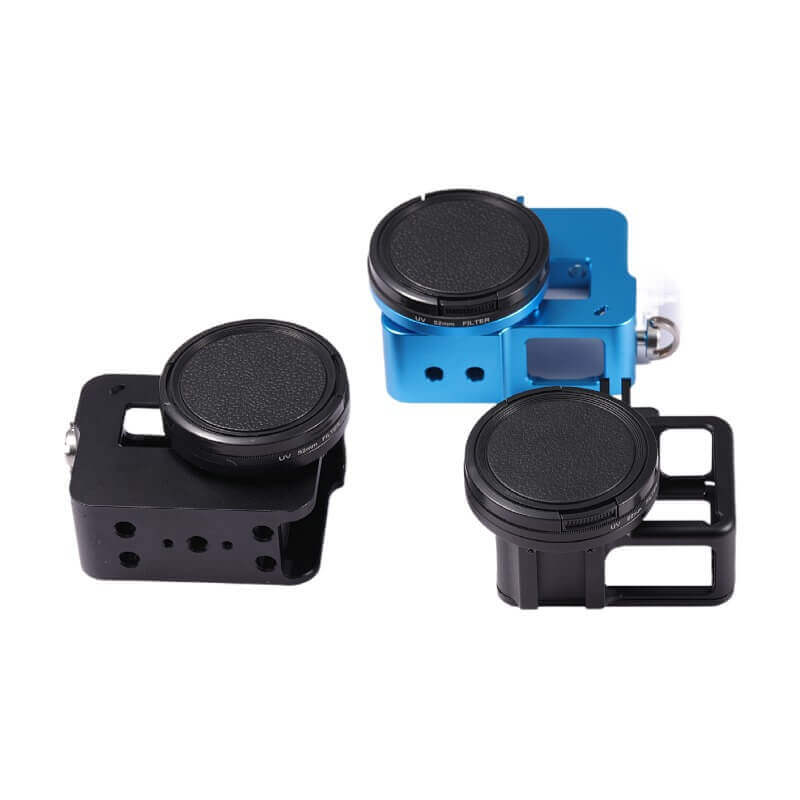




CNC Turning Aluminum






CNC Milling and Turning Aluminum


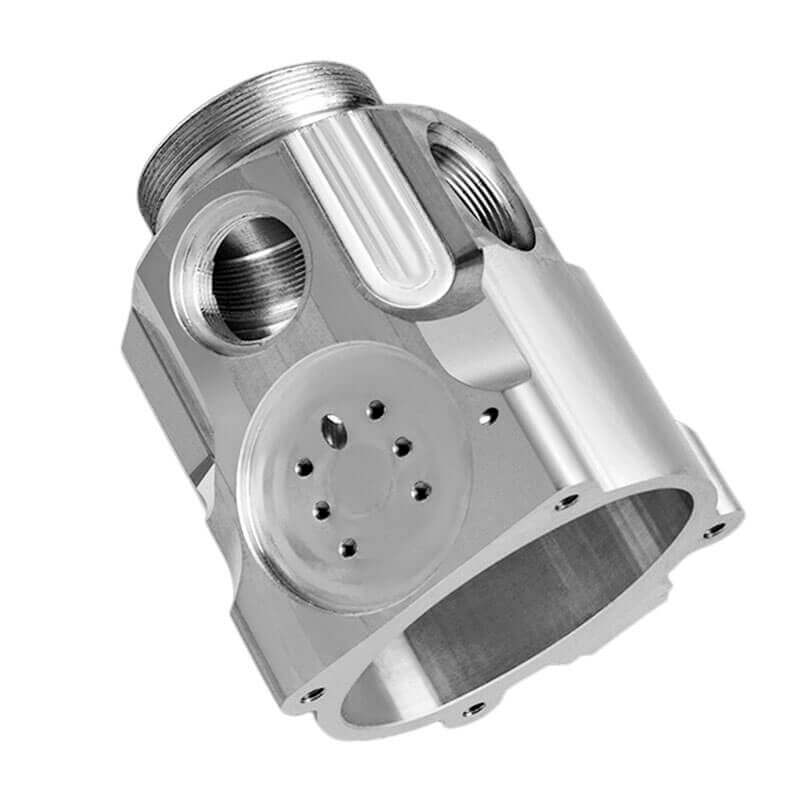



CNC Swiss Machining Aluminum

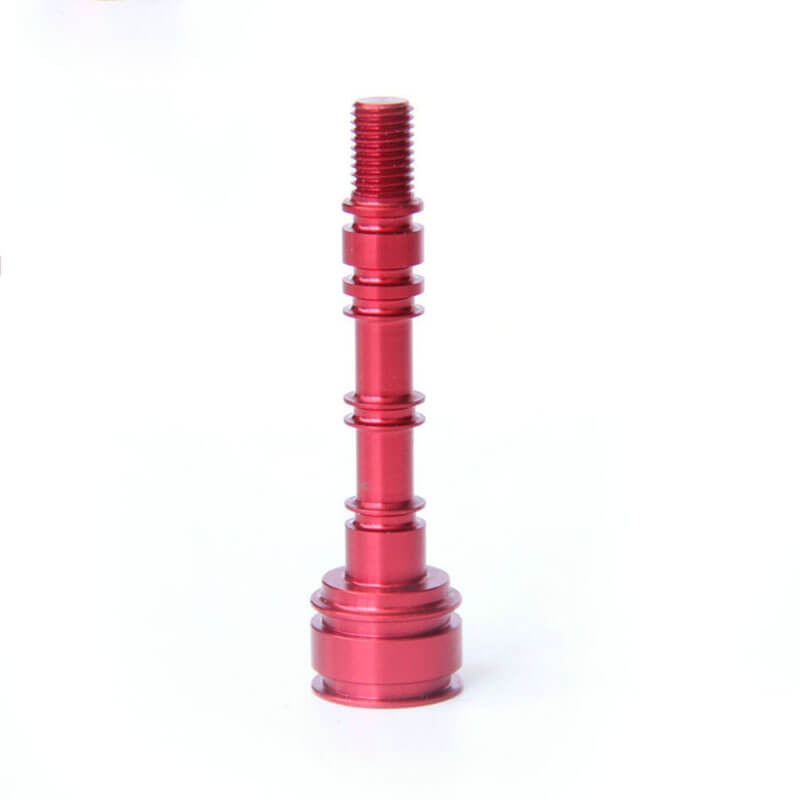
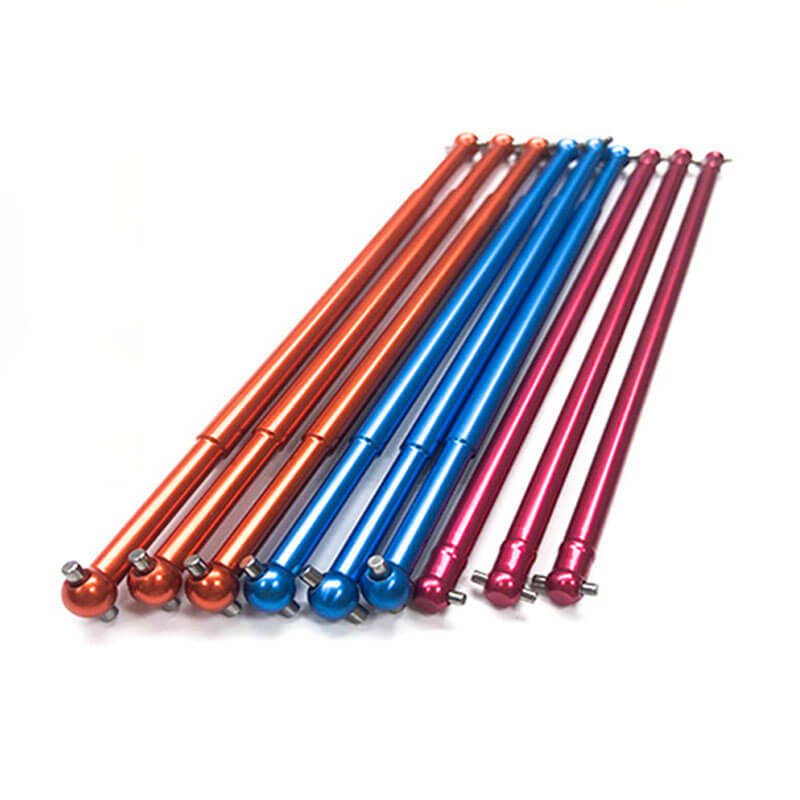
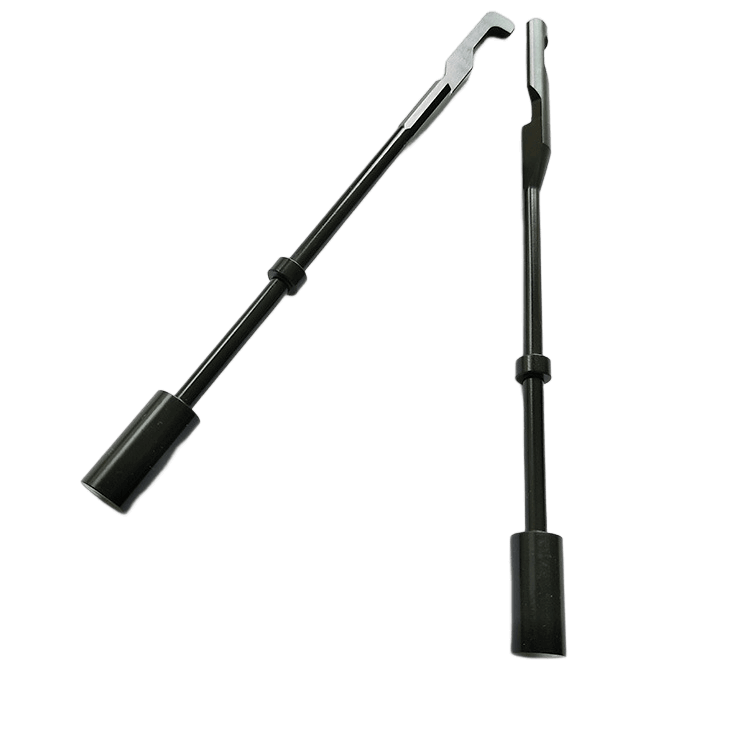

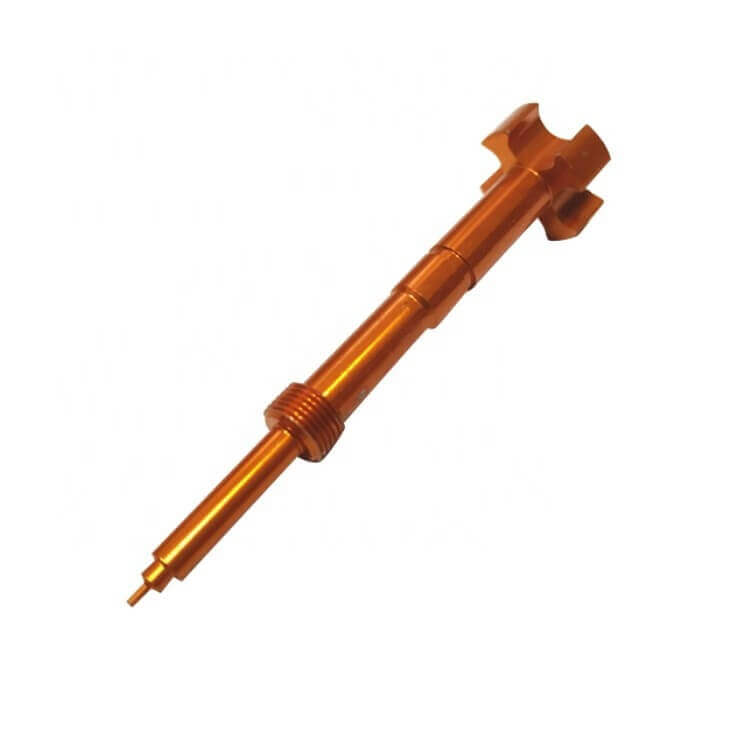
CNC Automatic Lathe Machining Aluminum


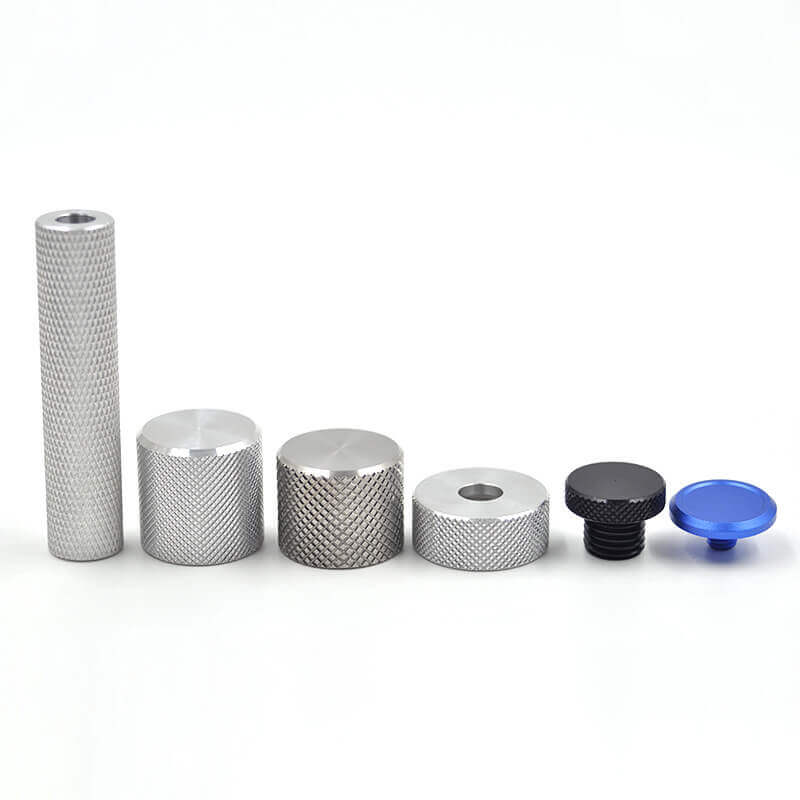



CNC Stamping Aluminum and CNC Laser Cutting






Five Pre-CNC Processing Methods for Aluminum Allow
Picture | Process | Materials | Description | Advantage | Application | If need mold |
---|---|---|---|---|---|---|
![]() | Aluminum casting | ZLD102、ZLD104、ZLD107、A356.etc | Liquid aluminum is poured into the mold cavity, also known as gravity casting | Good flowability, easy to shape, high strength, good corrosion resistance. | Automotive parts, aerospace components, electronic equipment enclosures, etc. | Yes |
![]() | Aluminum die Casting | ADC12、A380、ZLD102、ZLD104,etc | Die casting is a high-pressure casting process using cold chamber die-casting machines for aluminum alloy | 1. Low Density and High Strength-to-Weight Ratio. 2. Excellent Mechanical Properties 3. Outstanding Electrical and Thermal Conductivity 4. Good Corrosion Resistance 5. Favorable Surface Properties | Electronics, automotive, motors, household appliances, and some communication industries. | Yes |
![]() | Aluminum forging | 2024 7075 6061 2025 7475 2011 6063 ,.etc | Aluminum forging shapes heated aluminum using pressure and molds for the desired profiles or shapes at 400°C to 500°C. | High strength, good formability, excellent fatigue resistance. | Aircraft components, automotive parts, sporting equipment, and so on. | Yes |
![]() | Aluminum Extrusion | 5052 5083 6061 6063 6082 7075,.etc | Aluminum extrusion molds shape heated aluminum rods through hot extrusion, creating extruded profiles or shaped workpiece. | High customizability, lightweight, high strength, good thermal conductivity | Window frames, pipes, structural frameworks, etc. | Yes |
![]() | Aluminum laser cutting. | 1060 1100 3003 5052 5082 6061 6063 7075,.etc | Aluminum laser cutting involves using a laser cutting machine to cut various aluminum sheets into different shapes and profiles. | High-precision cutting, fast, low deformation, suitable for intricate design cuts. | Automotive parts, aerospace components, decorative materials, etc. | No |
There are several surface treatment methods for aluminum alloy
Picture | Process | Machining principle | Machining material | Advantage | Application | Remark | Learn More |
---|---|---|---|---|---|---|---|
![]() | Aluminum Sandblasting | Sandblasting is a process that utilizes air generated by a compressed air machine to rapidly spray sand particles onto the surface of aluminum workpieces, creating a sandy appearance. | Glass beads, tungsten sand, alumina, aluminum oxide, steel shot, steel grit, quartz sand, silicon carbide, etc. | Sandblasting can increase surface roughness, enhance adhesion, address and conceal certain defects generated during aluminum alloy machining processes, and meet specific appearance requirements from customers. | Aerospace, automotive parts, lighting fixtures, electronic devices, construction, industrial, furniture, etc. | The commonly used sandblasting particle diameters 0.15mm(#100)、0.125mm(#120)、0.106mm(#150)、0.088mm(#180)、0.074mm(#200)、0.065mm(#250)、0.05mm(#300)etc. | Learn More |
![]() | Aluminum passivation | Aluminum passivation is a method in which the workpiece machined by aluminum CNC machining is immersed in a passivation solution to form a protective film on the aluminum surface, slowing down metal corrosion. | Passivation Dip(solution) | The white protective film generated by aluminum passivation makes it less prone to oxidation, providing strong corrosion resistance, an attractive appearance, and long-lasting gloss. It is environmentally friendly and does not contain cadmium ions or other harmful substances. | Aluminum alloy materials, automotive components, aerospace components, building materials | 1. Ensure passivation thickness > 8 micrometers. 1. Prioritize pre-brightening and contamination-free surface. 2. Precisely manage passivation time. 3. Maintain solution concentration, adjust time per temp. Avoid excessive passivation. | Learn More |
![]() | Aluminum Anodizing | Using acidic electrolyte, aluminum serves as the anode, and through the action of electric current and the electrolyte, a protective oxide film forms on the surface of the aluminum. | Electrolyte, electric current | To enhance aesthetics, various colors can be achieved through oxidation, providing cost-effectiveness. This process improves corrosion resistance and increases the hardness of aluminum components. , | Aerospace, automotive, electronics, construction, furniture, daily necessities, beauty products, etc. | Use sulfuric, chromic, acetic, or boric acid at 5-25 volts, <25°C. Post-anodizing steps: 1. Hot water rinse (40-50°C, 0.5-1 min). 2. Age (40-50°C, 10-15 min). 3. Dry. For blind holes, blow out debris before oxidation.. | Learn More |
![]() | Aluminum Powder Coating | Applying a plastic coating through surface spray enhances aesthetics and corrosion resistance. | Plastic Powder | Enhancing aesthetics, improving corrosion resistance, commonly used for exterior decoration. | - | 1. Ensure that the workpiece is clean, oil-free, and free from contamination before powder coating. 2. Choose appropriate paint for spraying. 3. Control the coating thickness well. 4. Control the spraying time properly. 5. Finally, dry and cure the coating. | Learn More |
![]() | Aluminum Electroplating | Apply a chromium coating on the surface of the aluminum alloy to enhance heat resistance and corrosion resistance. | .Chromium sulfate | High heat resistance, resistant to discoloration, stable chemical properties, and excellent appearance. | Aluminum alloy plating is widely used in automotive, electronics, furniture, and decorative items. | 1. Prioritize clean, oil-free, and corrosion-free workpieces pre-plating. Select appropriate aluminum plating solution (e.g., aluminum sulfate or acidic aluminum chloride). Manage parameters: solution temp, current density | Learn More |
![]() | Aluminum PVD Coating | Depositing a thin film on the surface of aluminum under vacuum conditions to enhance corrosion resistance. | PVDcoating, Titanium nitride, titanium carbide,Alumina, silicon nitride | Offering various colors, enhancing corrosion resistance, and considering the adhesion of the coating. | Automobiles, new energy, precision machinery manufacturing, medical, industrial components, consumer electronics, beverage equipment, and so on | Before PVD vacuum deposition for aluminum, surface chrome plating is required for the workpiece. | Learn More |
![]() | Chemical Polishing of Aluminum | Utilize the selective self-dissolution effect of acidic or alkaline solutions to achieve smooth polishing of the aluminum surface | Acidic or alkaline solutions | Significantly improve the surface quality of aluminum, adjusting surface properties such as gloss and pH value. | Electronic Industry Aerospace Industry New Energy Industry - Industrial Equipment Manufacturing. Medical Equipment Manufacturing | 1. Sulfuric Acid: Removes aluminum oxide and contaminants. 2. Nitric Acid: Rapidly removes oxide with high corrosiveness. 3. Sodium Hydroxide: Dissolves oxide at high temps (alkaline polish). 4. Potassium Hydroxide: Alkaline polish, like sodium hydroxide. | Learn More |
Aluminum CNC Machining FAQs
Different alloy element content. 6061 aluminum alloy has a higher alloy element content compared to 6063 aluminum alloy.
Different alloy elements. The main alloying elements in 6063 aluminum alloy are magnesium and silicon, providing excellent machinability, weldability, extrudability, electroplating capability, corrosion resistance, and toughness. It can be easily polished, coated, and exhibits excellent anodizing effects, making it a typical extrusion alloy. On the other hand, 6061 aluminum alloy also contains magnesium and silicon, forming Mg2Si phase.
Different performance. 6061 aluminum alloy is suitable for industrial structural components that require certain strength, weldability, and high corrosion resistance. 6063 aluminum alloy is suitable for various industrial structural applications that require a certain strength, weldability, and corrosion resistance, such as manufacturing trucks, tower structures, ships, trams, furniture, mechanical parts, precision machining, etc.
Different oxidation performance. 6061 aluminum alloy has moderate oxidation performance, while 6063 aluminum alloy exhibits better oxidation performance. For customers who prefer a bright oxidation surface, 6063 material is preferable as it results in a brighter oxidation surface and better film adhesion.
Different plasticity. 6061 aluminum alloy has moderate plasticity, while 6063 aluminum alloy has better plasticity.
Hence, for many profile processing applications like radiators, power bank casings, power charging casings, cylinder casings, and chassis casings, etc., the choice of aluminum alloy depends on the specific requirements and use cases.
Machine tool condition: The stability of processing largely depends on the condition of the machine tool itself. A new machine tool may not be calibrated properly, and specifications may vary. In such cases, it’s important to inspect components like servo motors, lead screws, nuts, etc., and calibrate the machine tool.
Material cooling: Deformation may occur in the workpiece after cooling. This is often unavoidable. Therefore, careful attention should be given to the use of coolant. During on-site measurements, the possibility of material deformation should also be considered.
Machining technique: Improper machining techniques can result in defects in the workpiece. While adhering to the basic machining techniques for CNC milling (such as “roughing before finishing, face before hole, large surface before small surface” or using fixtures with strategies like “reduce the number of fixings, opt for combined fixtures”), efforts should be made to minimize machining errors caused by aluminum chips on the workpiece.
Parameter settings: Cutting speed, feed rate, cutting depth, and tool compensation all affect machining stability. Hence, special attention is needed in setting these parameters.
Tool selection: When machining aluminum, specialized tools should be used whenever possible for better precision. For instance, dedicated end mills for aluminum usually have larger rake and helix angles, with sharper cutting edges, which is beneficial for machining aluminum (preventing chip formation). This results in improved surface quality after machining.
Clamping pressure: Aluminum is relatively soft, so clamping strength needs to be carefully considered. In general, smaller companies with limited resources and less precision-demanding machining tasks might use a vise to clamp the workpiece. For thin-walled parts, to minimize deformation and ensure machining precision, these small companies may resort to using a vise or adhesive like AB glue. On the other hand, well-funded companies can utilize high-end equipment like vacuum milling chucks. Additionally, adjusting features like convexities and edges in the process can meet the requirements. During the machining process, allowing the aluminum material to rest for a while after roughing, and then proceeding to the next step, helps to eliminate stress. Alternatively, using spectrum analysis to select five frequencies with a multi-mode processing method for stress relief can achieve the goal. This equipment can be used for workpieces of all shapes and sizes. Attaching the exciter to the workpiece and applying vibration can eliminate stress effectively.
Achieving a high level of surface polish is crucial when machining high-precision aluminum alloy components or large aluminum alloy parts, as it directly impacts the product’s performance and value. To achieve a high gloss finish, there are several key points to consider. Firstly, opt to use cutting oil instead of cutting fluid as the lubricant for the machine. Compared to cutting fluid, cutting oil provides better lubrication, although it has a poorer cooling effect. For products aiming for a high gloss effect, a cutting oil suitable for aluminum alloy cutting is usually chosen to ensure lubrication during the cutting process. Secondly, when selecting tools, consider using specialized tools designed for high gloss machining of aluminum alloys. The material of high gloss tools differs from tungsten steel tools and is better suited for achieving the desired surface gloss and cutting requirements of aluminum alloys. During the machining process on the machine tool, ensuring alignment between the machine tool oil pipe and the tool is crucial. This ensures that the cutting oil is adequately lubricating during the cutting process and effectively washes away most of the aluminum slag produced during cutting, reducing the occurrence of chip entrapment. To avoid affecting the product’s glossiness, it’s essential to regularly use an air gun to remove debris that cannot be removed through regular cleaning methods. Lastly, determining the most appropriate machining parameters such as speed and feed based on the tool’s length is essential for achieving the desired surface gloss. Speed and feed are critical factors in determining the product’s surface gloss.
When machining aluminum alloys, several common types of cutting fluids are used, including:
Synthetic Cutting Fluid: Synthetic cutting fluid consists of synthetic base oils and additives, offering excellent cooling and lubrication performance. It is suitable for high-speed cutting and heavy-duty machining.
Solvent-Based Cutting Fluid: Solvent-based cutting fluid is based on solvents and provides good cooling and lubrication properties. It is suitable for high-speed cutting and heavy-duty machining.
Water-Soluble Cutting Fluid: Water-soluble cutting fluid is formed by adding cutting fluid to water, creating an emulsion. It offers good cooling and lubrication performance and is suitable for general machining.
Coating-Type Cutting Fluid: Coating-type cutting fluid is a thin-film cutting fluid that can form a protective film during machining, reducing friction and wear. It is suitable for high-speed cutting and heavy-duty machining.
When selecting a cutting fluid, factors such as the machining process, cutting speed, and workpiece material should be considered. Choose the appropriate cutting fluid based on specific requirements. Additionally, pay attention to the quality and stability of the cutting fluid to ensure machining quality and a safe working environment.
Carbide Cutting Tools
Carbide is a highly suitable material for machining aluminum alloys. Carbide cutting tools demonstrate excellent wear resistance and cutting performance during aluminum alloy cutting processes, allowing for high cutting speeds and efficient machining.
Carbide cutting tools are suitable for rough and precision machining and are commonly used in various aluminum alloy milling processes, such as turning, end milling, boring, threading, drilling, etc. Different tool shapes can be selected based on specific machining requirements.
High-Speed Steel Cutting Tools
High-speed steel cutting tools are also commonly used for machining aluminum alloys. They offer good machining efficiency and cutting power at a relatively lower cost, making them ideal for machining small to medium batches of aluminum alloy components.
High-speed steel cutting tools are applicable for milling, turning, thread processing, drilling, and more. However, it’s important to select appropriate cooling fluids and adjust parameters like cutting speed and feed rate to achieve optimal machining results.
PCBN Cutting Tools
PCBN (Polycrystalline Cubic Boron Nitride) cutting tools are among the most ideal tools for machining aluminum alloys. PCBN cutting tools possess extremely high hardness and wear resistance, enabling high-speed cutting and a longer tool lifespan.
PCBN cutting tools are suitable for high-speed cutting and precision machining, making them an ideal choice for processing high-precision aluminum alloy components. However, due to the high cost of PCBN, corresponding cutting tools are relatively expensive, making them suitable for handling larger production batch sizes.
Multi-Flute Milling Cutters
Multi-flute milling cutters are tools suitable for machining aluminum alloys, precision castings, copper alloys, and other materials.
Multi-flute milling cutters feature a wider tool width and a higher number of teeth, effectively enhancing cutting rates while reducing cutting resistance and temperature, thus improving machining efficiency and cutting quality.
Free Sample
Explore Other Materials

Copper CNC Machining
Copper, also known as pure copper, is classified into T1 to T44 based on its purity, with a higher number indicating a higher impurity content. It is also referred to

ABS CNC Machining
Acrylonitrile Butadiene Styrene (ABS) is a thermoplastic polymer known for its excellent balance of material properties. It exhibits good toughness and chemical resistance, along with a range of other customizable
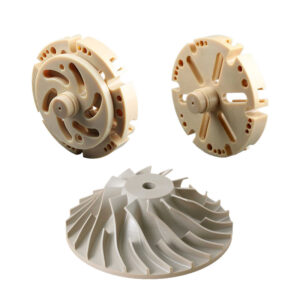
PEEK CNC machining
Polyetheretherketone (PEEK) is a special type of high-performance polymer material known for its high mechanical strength, resistance to high temperatures, impact resistance, flame retardancy, acid and alkali resistance, hydrolysis resistance,