Copper CNC Machining
Copper CNC Machining
Copper, also known as pure copper, is classified into T1 to T44 based on its purity, with a higher number indicating a higher impurity content. It is also referred to as copper, and these different terms primarily reflect their differences in color and quality. In fact, their color allows for clear identification, as the surface oxidizes to form a layer of reddish cuprous oxide, giving it a purplish-red hue. Copper is slightly harder in material compared to brass, but the difference in net weight is not significant.Due to its lower strength and hardness, copper has some impact on machining processes. However, it possesses excellent electrical conductivity, thermal conductivity, ductility, corrosion resistance, and plasticity.Compared to pure iron, copper has a broader range of applications. Approximately 50% of copper is electrolytically refined into pure copper every year, mainly for the electrical industry.Â
Overall, copper is a high-quality metal material that plays a significant role in many industrial sectors.
Â
Copper CNC machining techniques typically include Copper CNC turning, Copper CNC milling, Copper CNC turning and milling, Copper CNC Swiss machining, CopperCNC laser cutting, and more.
Copper CNC Milling
Although copper is not widely used, it is employed in the machining of precision mechanical components. Copper milling is a machining process where copper is removed using CNC machining centers to shape copper workpieces of various specifications. This method can produce flat surfaces, curved surfaces, and complex shapes of copper workpieces. Copper, due to its good toughness and plasticity, finds widespread application. However, during machining, tool adhesion can occur easily. Therefore, it is essential to choose high-speed sharp copper cutting tool s. The greater the plasticity of the copper material, the higher the spindle speed should be during milling. With many years of experience in machining copper, Masion can effectively address any challenges encountered during copper machining.




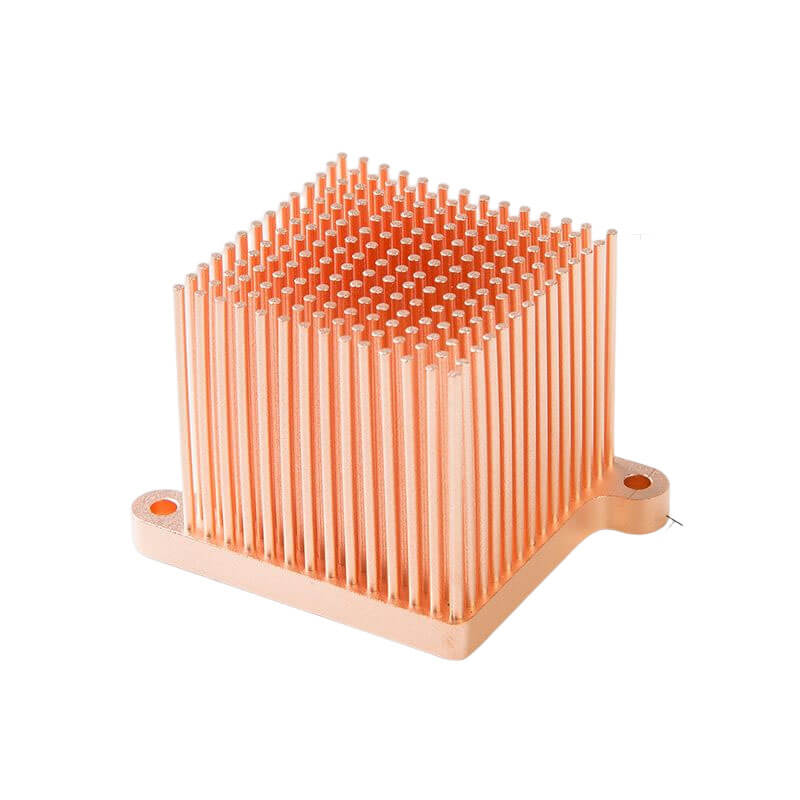

Copper CNC Turning
Copper turning is a high-precision machining technique that utilizes the rotation of tools on a CNC lathe along the axis of the workpiece. Through friction and contact with the workpiece surface, a layer of the copper workpiece’s surface is cut off to achieve precise machining. Generally, copper turning is suitable for cylindrical products, using round bars or pipes as raw materials, and then using programmed instructions to turn the copper workpiece into products of different shapes. Common machining methods include turning, drilling, knurling, tapping, etc. Due to the soft nature of copper, high-speed steel or hard alloy copper cutting tool s must be used during the turning process.
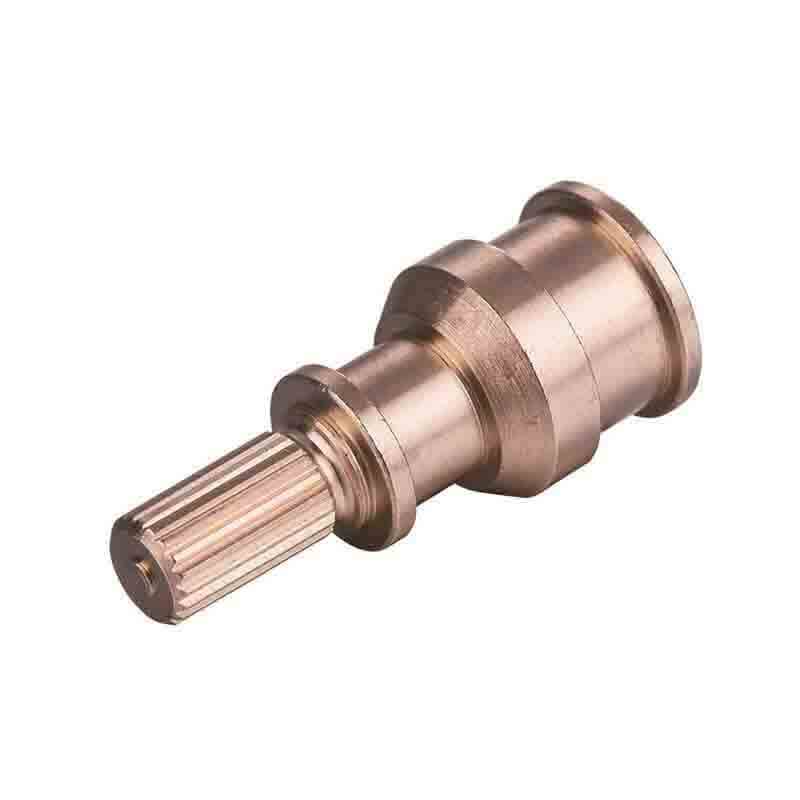





CNC Milling and Turning Copper
Copper turning and milling processing is a combined machining technique that integrates the processes of turning and milling. The principle involves rotating the workpiece during turning while the tool moves to frictionally cut off excess material from the copper workpiece. In the milling stage, the copper workpiece is fixed, and the tool rotates to mill away the excess material. In composite turning and milling, a fast machining approach can be utilized to adjust the spindle speed.





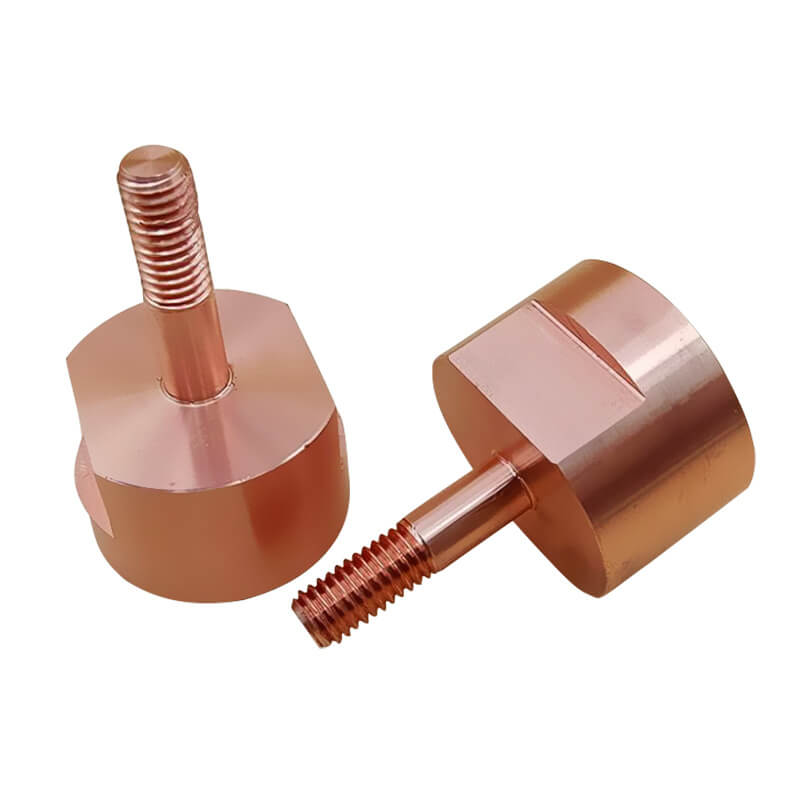
CNC Swiss machining Copper
Copper Swiss-type lathe machining is widely used in the manufacturing of various copper new energy terminals, cutting machine nozzles, new energy charging gun terminals, and other conductive components. The commonly used equipment is the CITIZEN Swiss-type lathe imported from Japan, and copper workpieces are processed using Swiss-type lathe programs. The Swiss-type lathe machining process involves a combination of turning and milling but is limited to copper workpieces with a diameter of less than 32 millimeters. The principle of Swiss-type lathe machining involves rotating the copper workpiece during turning while the tool moves to cut the copper; in the milling stage, the copper workpiece remains stationary, and the tool rotates to cut the copper workpiece, primarily aiming to remove excess material.




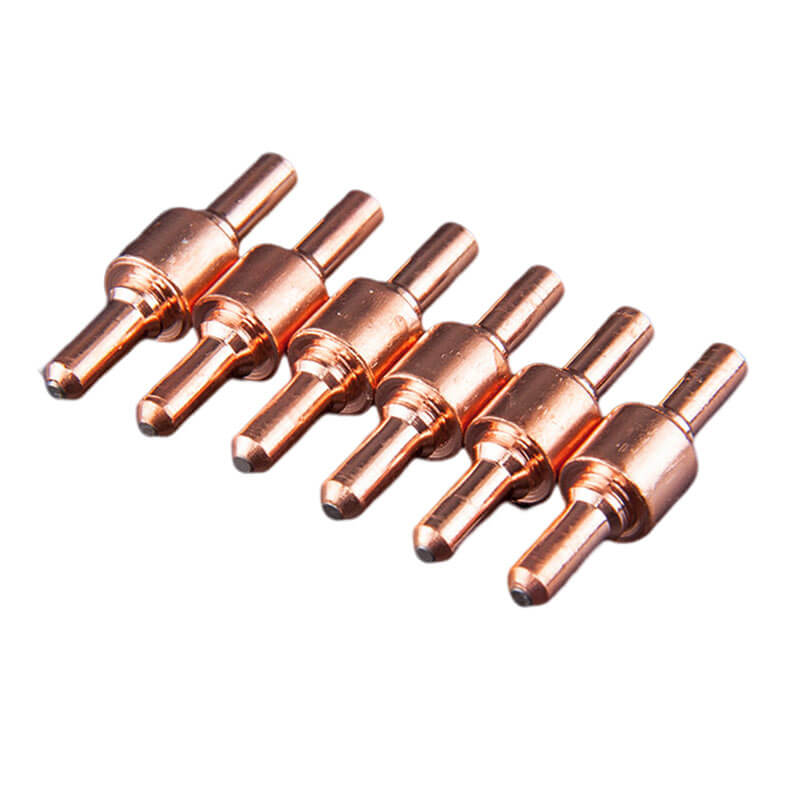
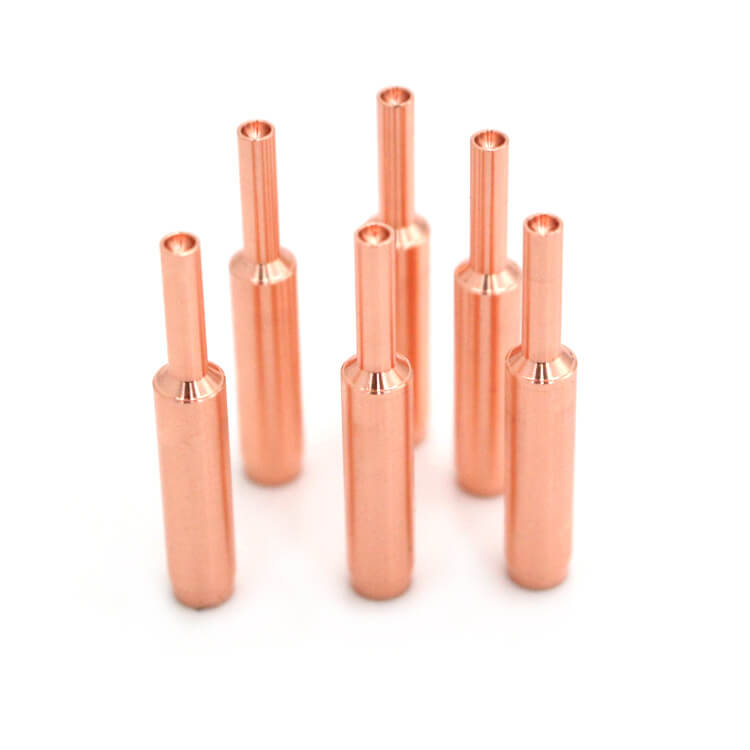
Copper Laser Cutting
Due to the high reflectivity of pure copper (also known as copper), CO2 laser beams cannot be used for cutting it. Accordingly, a fiber laser cutting machine with resistance to high reflectivity must be used for cutting copper. When using a fiber laser cutting machine to cut copper, the following points should be noted: Firstly, copper is a good conductor of electricity and absorbs a lot of energy from the laser, so it is necessary to choose a laser cutting machine with a higher power. Secondly, copper has a low melting point, requiring the laser cutting machine to have good energy and flow control capabilities to ensure the stability and efficiency of the cutting process. Additionally, for high-precision cutting and engraving of copper, the laser cutting machine needs to have high precision and control accuracy to ensure the accuracy of surface quality and cutting effects. The fiber laser cutting machine is an advanced equipment that converts optical energy into thermal energy, causing localized melting or vaporization of the material, thereby achieving the cutting purpose.






Copper CNC Machining Method
What are the Copper CNC Machining Material Processing Techniques?
Copper CNC machining typically involves the use of copper rods; however, for certain specialized products with irregular shapes that require CNC machining, molds need to be fabricated in advance to shape the copper workpieces into specific forms. Subsequently, in the subsequent CNC machining process, excess material is cut based on specific dimensions. This approach effectively reduces the manufacturing cost of copper components and shortens CNC machining time for rapid delivery. Here are commonly used copper material processing techniques: forging, casting, and cold extrusion.
Picture | Type | Manufacturing Method | Advantages | Applications | Manufacturing Process | Processing Materials | Applicable Brass Alloy Grades |
---|---|---|---|---|---|---|---|
![]() | Copper Forging | Material selection and heating | High precision, suitable for mass production | Electrical appliances, construction, chemicals, circuit boards, electromagnetic switches, roof panels,etc. | Forging machine, forging or pressure | High-quality copper material | C10100 C11000 C14500 |
![]() | Copper Casting | Pressure casting | High precision, suitable for mass production | Large, complex parts, small-batch large castings, high-precision components | Die Casting | Liquid or semi-liquid copper | C10100 C11000 C14500 C10200 C12000 |
![]() | Copper Cold Extrusion | Cold extrusion | Excellent electrical conductivity and corrosion resistance | Electronics, aerospace, automotive, construction, instruments, etc. | Cold extrusion, surface treatment | Pure copper or copper alloy | C10100 C11000 C14500 C10200 C12000 |
Surface finish
There are several surface treatments for copper:
Surface treatment for copper refers to a process of treating the surface of copper material. Copper is a high-quality conductive material widely used in electronics, electrical appliances, communication, and other fields. However, the surface of copper is susceptible to oxidation, corrosion, and other influences, affecting its conductivity and service life. Therefore, surface treatment of copper can enhance its corrosion resistance and conductivity, extending its service life.
Â
The main copper surface treatment processes include the following:
Picture | Surface Finishing | Principle | Process | Materials | Advantage | Disadvantages | Cost | Application | Learn More |
---|---|---|---|---|---|---|---|---|---|
![]() | Copper Chemical Polishing | Chemical reaction to remove oxides and dirt | Chemical polishing with polishing solution | Copper materials | Improves surface smoothness and conductivity | May require specific equipment, relatively high cost | Moderate | Electronics, electrical, communications, etc. | Learn More |
![]() | Copper Mechanical Polishing | Mechanical force to remove oxides and dirt | Mechanical polishing using polishing machinery | Copper materials | Improves surface smoothness and conductivity | Potential material wear, relatively complex operation | Moderate | Electronics, electrical, communications, etc. | Learn More |
![]() | Copper Electroplating (Copper-Silver Plating) | Electrochemical process | Electrochemical immersion with silver salt reaction | Copper components | Enhances conductivity, corrosion resistance, and aesthetics | Silver plating may peel off, requires prior nickel plating | High | Electronics, electrical, decorative items, etc. | Learn More |
![]() | Copper Tin Plating | Prevents copper from turning green due to moisture, inhibits oxidation/sulfidation | Electrochemical immersion, reaction of tin with copper | Copper components | Prolongs lifespan, improves electrical contacts | Requires specific equipment, relatively high cost | Moderate | Electronics, electrical, communications, etc. | Learn More |
Surface treatment processes for copper can enhance its corrosion resistance and conductivity, extending its service life. In practical applications, appropriate surface treatment processes should be chosen based on specific circumstances to achieve the best results.
What are the Copper Grades and their Applications?
Named for its purple-red color, copper rods possess excellent electrical conductivity, thermal conductivity, corrosion resistance, and workability. They can be welded and brazed. However, it can cause “hydrogen embrittlement,” so it is not suitable for processing (annealing, welding, etc.) Copper rods are used more extensively than pure iron.  Minute impurities, especially phosphorus, arsenic, aluminum, etc., Copper refined in this manner can reach a purity of 99.99%.
Characteristics
High purity, fine structure, extremely low oxygen content. No pores, blowholes, looseness. Excellent electrical conductivity, high surface precision of the electrodes eroded, suitable for precision and fine machining. It has good thermal conductivity, workability, ductility, corrosion resistance, and weather resistance.
Â
In China, copper is categorized into three grades: T1, T2, and T3, with T2 copper being widely used. T1, T2, and T3 copper are classified based on different chemical compositions as follows:
Â
T1 copper has a copper content of over 99.95%, with a total impurity content not exceeding 0.05%.
T2 copper has a copper content of over 99.90%, with a total impurity content not exceeding 0.1%.
T3 copper has a copper content of over 99.7%, with a total impurity content not exceeding 0.3%.
Copper possesses excellent electrical conductivity, thermal conductivity, good corrosion resistance, and workability. It can be molten welded and brazed. T1 and T2 copper are mainly used for conductive, thermal, and corrosion-resistant components, such as wires, cables, conductive screws, casings, and various conduits. T3 copper is primarily used as structural materials for making electrical switches, washers, rivets, nozzles, and various conduits.
Copper Grade Comparison Table
Here is a comparison table listing different grades of copper (also known as copper) and their corresponding designations in China, Japan, Germany, the United States, and the United Kingdom. The grades vary based on oxygen content and the presence of other elements like phosphorus.
Name | Name Chinese Grade | Japanese Grade | German Grade | US Grade | British Grade | |
---|---|---|---|---|---|---|
Oxygen-free copper | TU0 | -- | C10100 | C110 | Zero oxygen free copper | |
Oxygen-free copper | TU1 | C1020 | OF-Cu | C10200 | C103 | Oxygen-free copper I |
Oxygen-free copper | TU2 | C1020 | OF-Cu | C10200 | C103 | Oxygen-free copper II |
Copper | T1 | C1020 | OF-Cu | C10200 | C103 | Copper I |
Copper | T2 | C1100 | SE-Cu | C11000 | C101 | Copper II |
Copper | T3 | C1221 | -- | -- | -- | Copper III |
Phosphorized copper | TP1 | C1201 | SW-Cu | C12000 | -- | Deoxidized copper phosphor I |
Phosphorized copper | TP2 | C1220 | SF-Cu | C12000 | -- | Phosphodeoxy copper II |
Copper CNC Machining FAQs
When turning copper on a lathe, it is important to grind the copper cutting tool properly. Considering that copper tends to stick to the tool during processing, a crucial aspect of the machining process is to ensure a large front angle and a chip groove greater than 5mm, with a depth ideally between 2mm to 3mm. This approach minimizes heat generation during the machining of copper, resulting in smooth and polished surfaces.
Copper is highly prone to oxidation and discoloration. Using common cutting fluids can lead to a chemical reaction with copper, resulting in greenish discoloration and black spots on the surface. To prevent this, it is recommended to use cutting fluids specifically designed for copper, containing anti-oxidation and anti-rust properties to prevent oxidation during and after the machining process.
Products processed from copper include CNC milling and engraving machines, CNC lathes, core-walking machines, automatic lathes, turning, stamping, stretching, tubing, shafts, axles, copper and iron sleeves, aluminum sleeves, copper columns, copper needles, probes, rivets, pins, threaded inserts, nuts, threaded rods, nozzles, spray nozzles, oil nozzles, wind nozzles, air nozzles, connector shaft bases, ball joints, shaft connectors, spring-tipped positioning pins, adjusting rods, flange covers, rivet cones, brackets, pin connector nut, copper nut, non-standard custom hardware parts.
Recently, many online discussions have taken place regarding the raw material for copper flexible connections, specifically copper, also known as T2 copper. Surprisingly, there are several types of T2 copper. T1, T2, and T3 are the three grades of copper, which appear similar and cannot be distinguished with the naked eye; professional testing equipment is required for differentiation.
Â
These three types of materials have different copper contents, which is the fundamental distinction:
Â
T1: Copper content is 99.95%
T2: Copper content is 99.90%
T3: Copper content is 99.70%
Their melting points slightly differ, and their electrical conductivity and resistivity also vary. T1 has the highest copper content, while T3 has the lowest. The choice of which type to use depends on the specific application and requirement.
Â
When grinding your own tools for machining copper, it’s beneficial to have a larger back angle to enhance tool sharpness. Polishing of the front cutting surface is essential. For pointed ends, a slightly smaller point angle is preferred for better machining results.
The characteristic of long and unbroken chips in copper requires a smooth front cutting surface on the machining tool to reduce friction between the chips and the tool. This is crucial for improving tool life and machining quality.
In machining copper using a CNC engraving machine, the cutting line speed does not significantly impact tool life. Thus, the spindle speed can be adjusted within a considerable range. Generally, a flat-bottomed cutter is used at a spindle speed of around 14,000 (rpm).
The length of the tool protruding should be kept as short as possible, or a thicker tool holder can be used to increase tool strength and reduce deformation during machining, which significantly affects the surface finish of the workpiece.
For precision machining with a ball-end cutter, the intersection of the two edges of the cutter should be thin to ensure sharpness and reduce friction during machining, especially in areas with small curvature for better results.
For turning copper on a CNC lathe, suitable copper cutting tool s include hard alloy (carbide) tools, high-speed steel (HSS) tools, tungsten steel tools, vertical tools, multi-blade tools, and PVD-coated tools. The choice of tool depends on factors such as turning process, cutting speed, processing conditions, workpiece shape, and machining accuracy requirements. Hard alloy tools are recommended for efficient and high-speed, deep-cut, and high-feed turning processes. High-speed steel tools, although less expensive, are suitable for small-batch, medium-low-speed, and small-feed turning processes. Tungsten steel tools are ideal for high-hardness metal materials like copper, providing fast cutting speed and longer tool life, though they are relatively more expensive. Vertical tools are versatile for various metal materials, including copper. Multi-blade tools are commonly used for turning copper, enabling multiple different types of machining processes in a single cut and improving processing efficiency. PVD-coated tools are prepared using physical vapor deposition technology, forming a thin film on the tool surface, providing excellent wear resistance and anti-oxidation performance, enhancing cutting speed and tool life, suitable for high-precision and high-speed machining. Nickel-based alloy tools have high hardness and excellent wear resistance, capable of withstanding high temperatures, making them suitable for cutting difficult-to-cut metals like copper. Apart from choosing the appropriate tool, other methods can make copper easier to cut, such as using a lubricant during cutting to reduce friction and heat and improve cutting efficiency and tool life. In summary, the choice of tool should be based on a specific analysis of the actual situation. Hard alloy tools are suitable for high-efficiency, high-speed, deep-cut, and high-feed turning processes, while high-speed steel tools are suitable for low-efficiency, medium-low-speed, and small-feed turning processes. Select the appropriate tool according to the actual situation to improve processing efficiency, machining accuracy, and reduce the number of tool changes and costs.
Copper has low strength and hardness, resulting in a low cutting load during turning, allowing for sharper copper cutting tool s. However, due to its high plasticity and toughness, the chips are not easily broken, resulting in chip lumps during turning, intensifying tool wear and affecting the surface quality of the workpiece. Additionally, copper has a high linear expansion coefficient, and the workpiece undergoes thermal effects during turning.
The main reasons include improper tool selection, unreasonable setting of processing parameters, and inadequate operational skills. Therefore, extra care and precision are required when turning copper.
Attention should be paid to proper tool selection and assembly, reasonable setting of processing parameters, stable clamping of the workpiece, and maintenance of the machining environment. Regular equipment maintenance and upkeep are also necessary to ensure machining accuracy and stability.
Standards for copper products include:
Â
Seamless copper tubes for air conditioning and refrigeration equipment (GB/T 17791-2007)
Seamless copper tubes for cables (GB/T 19849-2005)
Seamless round copper tubes for conductivity (GB/T 19850-2005)
Oxygen-free copper tubes for magnetrons (GB/T 20301-2006)
Seamless internally threaded copper tubes (GB/T 20928-2007)
Laser cutting of copper is an efficient and precise processing method that can complete complex cutting tasks in a short time. However, to achieve the best cutting results, it is essential to set the cutting parameters appropriately.
Â
Based on information about laser cutting parameters, the parameters for laser cutting copper include laser power, cutting speed, gas flow rate, and focal length. For most copper materials, the recommended laser power range is 1500-3000 watts. The cutting speed for copper is suitable between 1-2m/min. The focal length, if too large or too small, can affect the cutting quality, and the gas flow rate, if too large or too small, can also affect the cutting effect. Therefore, adjustments should be made based on specific circumstances.
Â
Copper is industrial-grade copper with a melting point of 1083°C, no allotropic transformation, a relative density of 8.9, and a density five times that of magnesium.
Free Sample
Explore Other Materials

PC CNC Machining
PC sheets, also known as polycarbonate sheets or polyester sheets, are characterized by high transparency, lightweight, impact resistance, sound insulation, heat insulation, flame resistance, and resistance to aging. They are
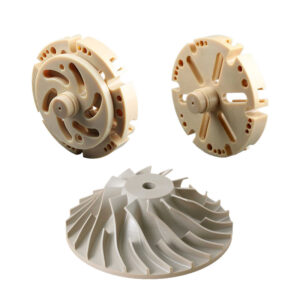
PEEK CNC machining
Polyetheretherketone (PEEK) is a special type of high-performance polymer material known for its high mechanical strength, resistance to high temperatures, impact resistance, flame retardancy, acid and alkali resistance, hydrolysis resistance,

CNC POM Machining
POM (Polyoxymethylene) is an important semi-crystalline thermoplastic engineering plastic known for its impact resistance and wear resistance. It is widely used in industries such as automotive, electronics, and machinery and