Magnesium CNC Machining
Magnesium CNC Machining
Magnesium alloy materials are primarily composed of magnesium, supplemented by other elements such as aluminum, zinc, manganese, cerium, and thorium, forming magnesium alloys. Magnesium alloys are often chosen as materials for CNC machining due to several advantages: lightweight, high strength, excellent heat dissipation, and outstanding shock absorption. They can withstand larger impact forces compared to aluminum alloys, making them suitable for applications in new energy vehicles, aerospace, rockets, and more. A commonly used alloy by Masion is aluminum-magnesium alloy. In addition to this, other magnesium alloys such as magnesium-manganese alloy and magnesium-zinc-zirconium alloy can also be chosen.
- CNC machining magnesiumof common manufacturing processes are included milling and turning,
CNC Magnesium Milling
Magnesium alloy milling is a method of material removal in manufacturing. It involves securing the magnesium alloy workpiece in a CNC machining center and then programming the CNC machining center with G-code based on the product drawing dimensions. Excess material is quickly milled to achieve the desired shape and dimensions of the product.
The advantages of magnesium alloy milling include reduced milling resistance, leading to a reduction in machining time and improved tool life. The process is efficient, with excellent performance, ease of machining, low cost, and minimal usage of cutting fluid.


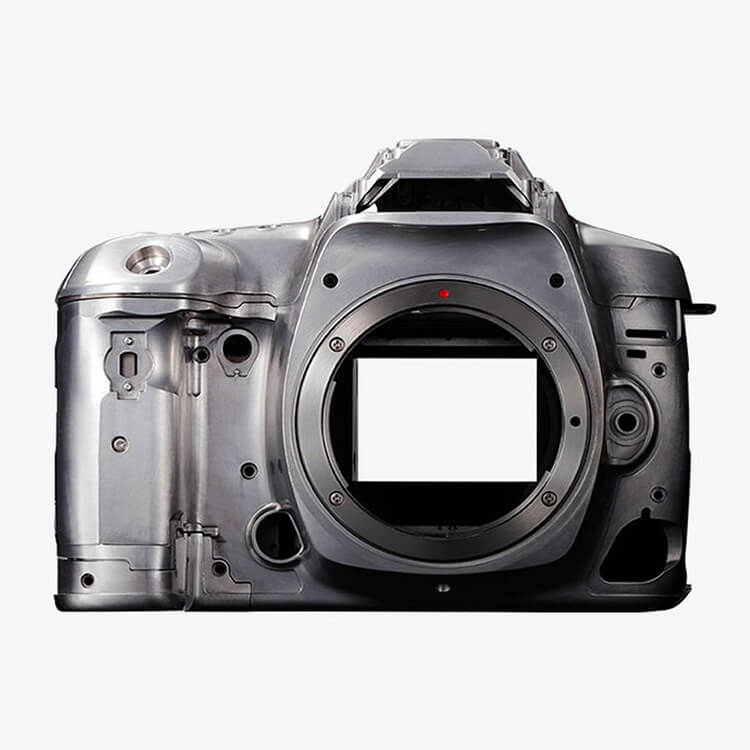

CNC Magnesium Turning
Magnesium alloy turning is a simple machining process suitable for magnesium-aluminum alloy materials. This method utilizes the rotation of the magnesium alloy workpiece, shaping the desired form through the movement of the lathe tool and friction with the magnesium alloy workpiece, resulting in the ideal shape of a rotated magnesium alloy body. As magnesium alloy is easily machinable, high-speed machining techniques can be employed during turning, along with the use of specialized cutting fluids to enhance surface finishing.



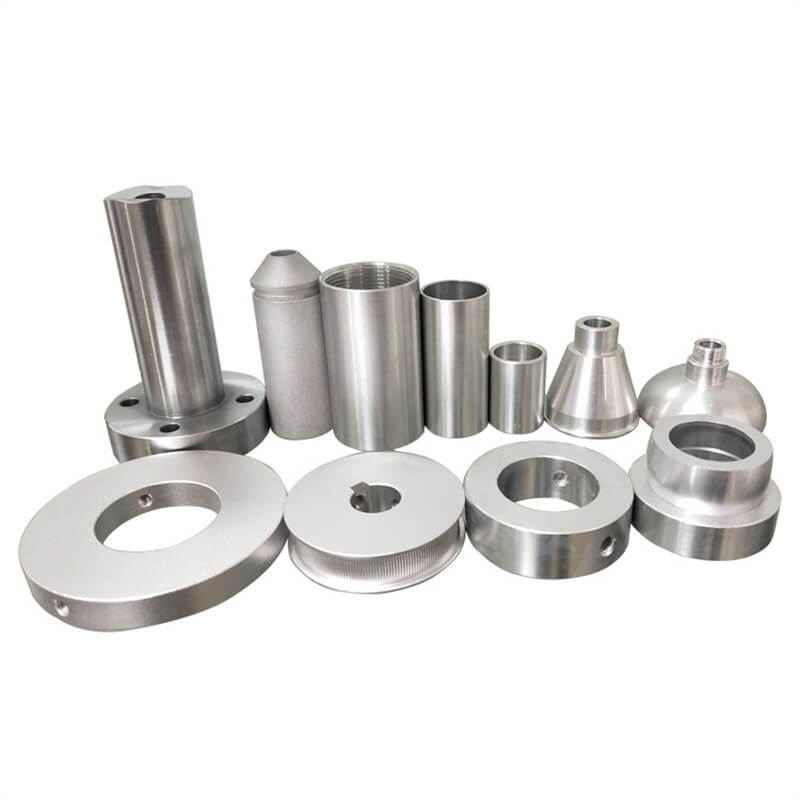
Common Machining Methods for Magnesium Materials (Pre-CNC Processing)
Typically, prior to CNC machining of magnesium alloys, we select the appropriate material based on the dimensions and shape indicated in the drawings. For products with rotational geometry, we opt for magnesium alloy bars or tubes for CNC machining. For products with square dimensions, magnesium alloy sheets are usually chosen. For other non-standard dimensions requiring CNC machining, we select casting, forging, or other appropriate manufacturing methods based on the shape.
Forming Processes for Magnesium Alloys:
Liquid State Forming Processes:
Gravity Casting
Magnesium alloy castings are manufactured using various methods such as sand casting, investment casting, and die casting. The use of self-hardening resin sand and investment casting methods can improve casting quality, simplify the process, enable automated production, and reduce harmful gas emissions.
Low-Pressure Casting
Low-pressure casting technology is employed to produce high-quality magnesium alloy castings, avoiding casting defects such as cracks and uneven filling.
Die Casting
Magnesium alloys are suitable for die casting, although conventional die casting does not allow for heat treatment. Vacuum die casting, oxygen-enhanced die casting, and semi-solid die casting technologies can address this issue, enhancing casting quality and mechanical properties.
Semi-Solid Casting
Semi-solid forming is a new process that refines grain structure, reduces porosity, and improves casting quality. Semi-solid thixoforming is a mature method used in magnesium alloy production.
Solid State Forming Processes:
Extrusion
Magnesium alloys are suitable for extrusion forming, allowing for refined grain structure, improved strength, good surface quality, and dimensional accuracy through warm and hot extrusion.
Forging
Free forging and die forging are common forging methods for magnesium alloys, and forging temperature influences mechanical properties. Precision forging is suitable for high-precision, complex-shaped forgings, offering advantages such as high production efficiency and low cost.
Rolling
Magnesium alloy strips and sheets can be produced through rolling, and the rolling process can improve the microstructure and mechanical properties. Rolling temperature is a critical parameter, and deviations can result in issues.
Various common surface treatments for magnesium alloys:
4.2 Post-Surface Rust Prevention Treatment for Parts:
(1) Surface Pre-Cleaning (Pre-treatment): Magnesium alloy products, after processes like die casting or forging, can have contaminants such as oxides, lubricants, and oils on the surface. Therefore, pre-treatment aims to clean the magnesium alloy surface for subsequent processing. Two main methods are used for cleaning: mechanical cleaning, using different abrasion, rough polishing, dry, and wet abrasive blasting to achieve the required surface roughness for magnesium alloy; chemical cleaning, using solvent, alkali washing, acid washing, to achieve different surface conditions for magnesium alloy.
(2) Passivation Treatment: Passivation treatment involves a non-electrolytic chemical reaction between the magnesium alloy surface and a solution, creating an insoluble inorganic salt surface film. Besides improving corrosion resistance, the passivation film can serve as a base for coatings, enhancing adhesion for magnesium alloy coatings.
(3) Anodizing Treatment: Anodizing treatment forms an anodized oxide film on the magnesium alloy surface, significantly enhancing corrosion resistance. It also imparts a metallic luster, serving decorative purposes. The oxide film can act as a base for subsequent coatings, improving coating adhesion. A well-sealed dense oxide layer can enhance surface hardness and corrosion resistance.
(4) Electroplating Treatment: Electroplating technology is used to alter the surface color and appearance of magnesium alloy materials to achieve the desired functionality and decorative purposes. Typically, several pre-plating pretreatments such as zinc displacement, copper displacement, or electroless nickel are performed to enhance adhesion before electroplating when considering improving adhesion of the electroplated layer.
(5) Metal Coating: Metal coatings can further prevent corrosion and increase the mechanical properties and hardness of the magnesium alloy surface, ultimately aiming to achieve lightweight magnesium alloy selection under specific environmental conditions.
Common Grades of Magnesium Alloys:
AZ91D: Belongs to the cast magnesium alloy category, primarily processed using pressure die casting with subsequent machining. Surface appearance can be altered using methods such as electrophoresis. It exhibits higher strength and corrosion resistance compared to pure magnesium and is used for electrical product casings, small-sized thin or irregular brackets, etc. ‘A’ represents aluminum (Al), ‘Z’ represents zinc (Zn), ‘9’ indicates an aluminum content of 9%, ‘1’ indicates a zinc content of 1%, and ‘D’ is the identification code.
AZ31B: AZ31B magnesium alloy is a deformable magnesium alloy with good mechanical properties, primarily used for automotive parts, machine casings, communication equipment, etc. Cast magnesium alloy AZ31B has high vibration resistance and heat absorption properties, making it an ideal material for manufacturing aircraft hubs.
AZ40: Applications of AZ40 magnesium alloy include engine gearboxes, oil pumps and pipes, dashboards, gearbox bodies, crankshaft boxes, engine front covers, cylinder heads, air conditioner casings, etc.
AZ41: AZ41 magnesium alloy possesses high strength, hardness, electrical conductivity, thermal conductivity, good wear resistance, and anti-friction properties. After aging treatment, the hardness, strength, electrical conductivity, and thermal conductivity significantly improve, and it is easily weldable.
AM60B: AM60B has high elongation and impact resistance, mainly used for steering wheels and seats in automobiles.
AM50A: AM50A has high elongation and impact resistance, mainly used for steering wheels and seats in automobiles.
MB8: Typically manufactured into sheets, strips, or stamped parts, used for parts bearing medium loads.
MB1: Commonly made into sheets, rods, strips, and forgings, used for aerospace components with low stress but high ductility, weldability, and resistance to ignition.
Magnesium Aluminum Zinc Alloys: AZ31B, AZ40M, AZ61M, AZ91D, etc.
Magnesium Manganese Alloys: M2M, etc.
Magnesium Zinc Zirconium Alloys: ZK61M, ZK61S, etc.
Magnesium CNC machining FAQs
Low weight
Compared to aluminum alloys, magnesium alloys not only have a lighter weight but also possess higher strength and superior rigidity. The stiffness of magnesium alloys increases cubically with thickness, making them favorable for the design of structural components.
Machinability: Magnesium alloys have low cutting resistance, approximately one-tenth that of steel and one-third that of aluminum, resulting in shorter cutting times and longer tool life. Their machining performance is excellent, leading to low machining costs and minimal energy consumption.
Corrosion Resistance: Magnesium exhibits good corrosion resistance in atmospheric conditions, surpassing that of iron. High-purity magnesium alloy AZ91D has significantly better corrosion resistance than low-carbon steel and even exceeds cast aluminum alloy A380. The presence of beryllium and calcium in magnesium alloys can enhance their corrosion resistance, while the presence of iron, cobalt, nickel, and copper significantly reduces the alloy’s corrosion resistance.
Damping Capacity: Magnesium alloys have excellent damping capacity compared to other metals. Even though the Young’s modulus of magnesium is low, it serves as an excellent damping material. Using magnesium alloy materials in automotive structural components can significantly reduce noise and vibration during vehicle operation.
Dimensional Stability: Magnesium alloys can maintain their dimensional stability over extended periods, with virtually no observable changes in the working dimensions.
Impact Resistance: When magnesium die-cast components are subjected to impact, they produce smaller surface scars compared to iron and aluminum components.
Abundant Resources: China is a major source of magnesium resources, with abundant reserves of high-quality magnesium refining materials, including magnesite, dolomite, and salt lake magnesium resources.
Magnesium is one of the easiest materials to CNC machining. It is easily machined at high speeds, far exceeding the maximum speeds achievable with cast iron and steel. Furthermore, it can achieve excellent surface quality.
During dry machining of magnesium alloys, there is no need for coolant, which can reduce machining costs and resource consumption.
However, due to the low heat capacity and relatively high thermal expansion of magnesium alloys, the chips produced during machining are prone to ignition. Moreover, during machining, the relatively large linear coefficient of thermal expansion of magnesium alloys can cause workpiece deformation, resulting in reduced machining precision. When machining magnesium alloys, cutting fluid is used to cool the workpiece, reducing the likelihood of part distortion and chip ignition. Therefore, in the machining of magnesium alloy components, cutting fluid is often referred to as coolant and is one of the factors that extend the tool life.
Proper Proportion of Magnesium Alloy Cutting Fluid: During the machining of magnesium alloys, phenomena such as atomization, splashing, and evaporation can occur. Therefore, it is essential to pay attention to the proper mixing ratio of the magnesium alloy cutting fluid. On one hand, the effectiveness of the cutting fluid may decrease due to some physical changes, and on the other hand, insufficient cutting fluid performance can affect the quality of magnesium alloy machining.
Flow Rate of Magnesium Alloy Cutting Fluid: In the process of machining magnesium alloys, a higher flow rate and pressure can help wash away the chips, keeping the cutting area clean. This contributes to an improvement in the precision of magnesium alloy machining. If the flow rate of the cutting fluid is too low and its performance is inadequate, it can result in rough machining of magnesium alloy products, leading to material and resource wastage, and increased costs for the company.
Effective Cooling: Magnesium alloys have a relatively low melting point. In high-speed and high-pressure machining scenarios, excessive heat can cause workpiece temperatures to rise significantly, leading to deformation of the magnesium alloy workpiece. To prevent such occurrences, it is important that the cutting fluid provides effective cooling, which can effectively reduce the temperature of magnesium alloy workpieces and enhance product quality.
Use of Dedicated Magnesium Alloy Cutting Fluid: It is necessary to use cutting fluid specifically designed for magnesium alloys. General-purpose cutting fluids can easily oxidize, releasing magnesium ions into the cutting fluid. The introduction of magnesium ions disrupts the internal stability of the cutting fluid, leading to stratification. This happens as the concentration of magnesium ions increases over time, ultimately resulting in an uncontrollable situation. Special additives in magnesium alloy-specific cutting fluids effectively prevent the oxidation of magnesium ions.
Additionally, it’s important to be cautious about magnesium alloy swarf (chips) because they can easily ignite when exposed to sparks.
Please note that while this is a translation, it is essential to follow specific safety guidelines and recommendations for handling cutting fluids and machining magnesium alloys to ensure a safe and efficient machining process.
Cutting fluids serve two major functions: cooling and lubrication. Therefore, cutting fluids are often not required when machining magnesium alloys, especially in small-batch production or simple machining processes where dry machining can be more cost-effective and cleaner.
The use of cutting fluid for lubrication may be necessary when deep-hole boring, when feed and cutting speeds are very high, or during large-batch production to provide cooling. In large production batches, cutting fluid is one of the factors that extend tool life.
(1) Measures in Daily Management:
When processing magnesium alloy parts in designated areas, the work site should be clean, well-lit, and well-ventilated. It is essential to promptly clean up magnesium chips from the work area. Magnesium chips should not be piled up near the machine tools; instead, a designated container should be placed outside the workshop for chip disposal. Each machine tool should be equipped with dry powder fire extinguishers or fire-fighting sand.
(2) Technical Specification Measures:
Choose appropriate cutting parameters and tool geometry to minimize depths of cut smaller than 0.05mm. Maintain sharp tools and ensure continuous cutting to avoid generating thin ribbon-like chips.
(3) Equipment and Environmental Measures:
Whenever possible, employ dry high-speed cutting, avoiding the use of cutting fluids. Allow natural air cooling and provide chip evacuation equipment. Since magnesium alloy powder can produce hydrogen when it comes into contact with water, use mineral oil (acidic cutting agents are strictly prohibited) during production and processing. Machine tools using oil-based cutting fluids should have leak-proof designs. Furthermore, when removing magnesium chips, avoid contact with water as much as possible.
Free Sample
Explore Other Materials
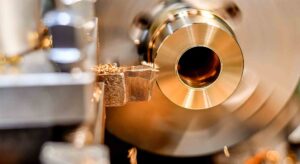
CNC Machining Bronze
There are many types of bronze, with commonly used ones including phosphor bronze, tin bronze, and aluminum bronze. Additionally, there are less commonly used types like beryllium bronze, silicon bronze,

ABS CNC Machining
Acrylonitrile Butadiene Styrene (ABS) is a thermoplastic polymer known for its excellent balance of material properties. It exhibits good toughness and chemical resistance, along with a range of other customizable
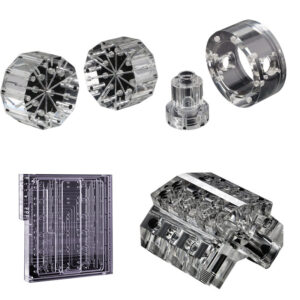
CNC PMMA Machining
PMMA is a material with high mechanical strength, strong dimensional stability, and excellent resistance to creep. PMMA sheet is a high-performance acrylic glass widely used in applications such as construction,