Stainless Steel CNC machining
Stainless Steel CNC machining
Stainless steel is a corrosion-resistant, high-strength, and aesthetically pleasing metal material. Its primary components include iron, chromium, nickel, and other elements. By incorporating different elements and employing various techniques, stainless steel can be manufactured into various types with different properties and applications.
Stainless steel CNC machining is a prevalent and crucial machining method in the current manufacturing industry. Its main characteristic is the control of the tool’s movement by a CNC machine to carry out the machining of workpieces. In CNC machining, it is primarily divided into hard programming and visual programming. The significant difference lies in visual programming, which allows for real-time modifications during the machining process, greatly enhancing efficiency. Stainless steel CNC machining is known for its high precision, speed, and production efficiency.
Stainless steel machining techniques typically include stainless steel CNC milling, stainless steel CNC turning, stainless steel CNC turning-milling combination, stainless steel Swiss machining, stainless steel automatic lathe machining, stainless steel laser cutting, and more.
CNC Stainless Steel Milling
Stainless steel CNC milling is typically performed using a CNC machining center to cut stainless steel. It employs rotating tools within the CNC machining center to carry out the cutting operations, removing unnecessary stainless steel material and achieving the desired shapes, such as flat surfaces, curved surfaces, and complex profiles. When milling stainless steel, it’s essential that the milling tools are sharp and impact-resistant, and the chip grooves are sufficiently large.
Milling stainless steel presents certain challenges: stainless steel is highly ductile, has high toughness, and consumes a significant amount of energy during milling, resulting in elevated temperatures. Stainless steel has low thermal conductivity, which can lead to poor heat dissipation and high tool temperatures. Stainless steel also exhibits strong adhesion and built-up edge formation during milling, and it tends to work-harden, forming a hardened layer on the machined surface. Stainless steel chips are less prone to breaking, which can lead to chip clogging during milling and impact the surface finish.
Masion has many years of experience in stainless steel machining, making it well-equipped to handle any challenges encountered during the stainless steel machining process.


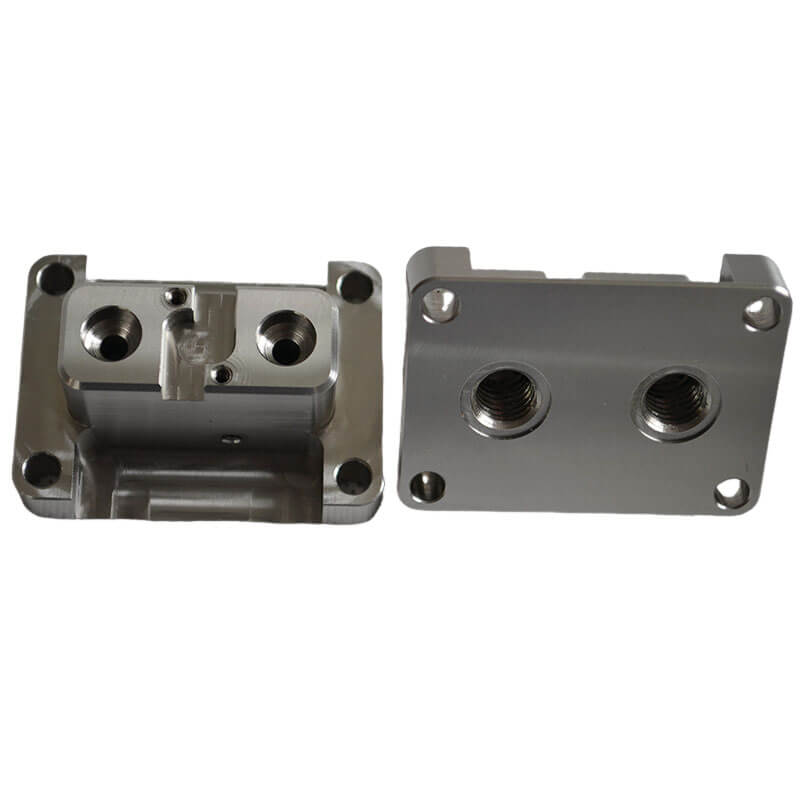
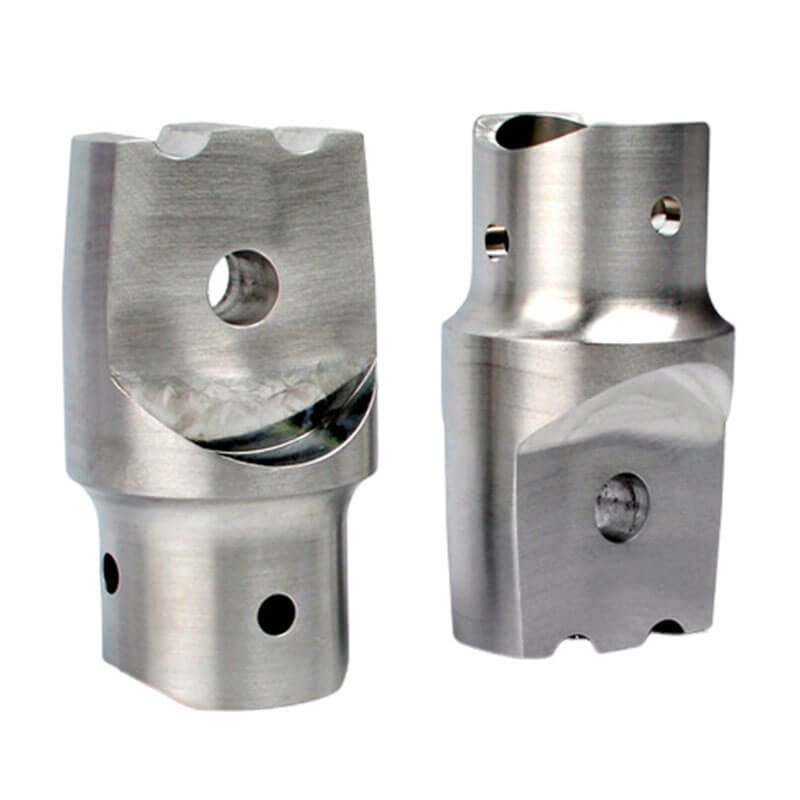
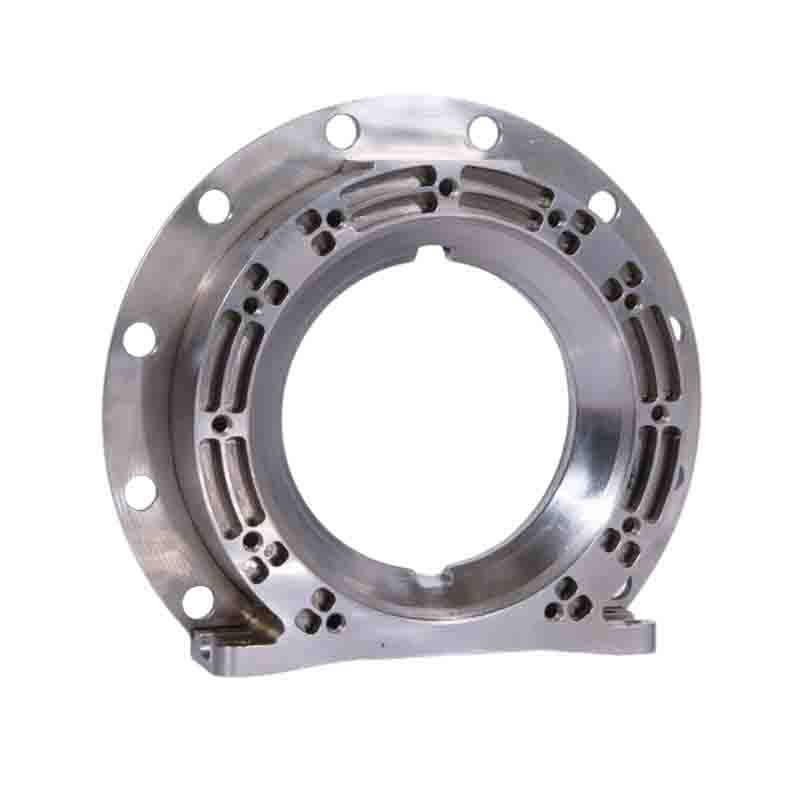
CNC Stainless Steel Turning
Stainless steel turning is a highly demanding machining method because stainless steel, being a material with high hardness, is difficult to machine and prone to scratching. It may also undergo deformation during heat treatment. The interaction with cutting tools can often result in significant tool wear. The principle of this machining method is to use high-quality, high-precision, and high-rigidity CNC machine tools. The stainless steel workpiece is securely clamped, and through continuous rotation and the use of cutting tools on the tool holder, friction is generated by the movement of the tool holder and the rotation of the stainless steel workpiece. This gradually removes excess surface material and shapes the workpiece into the desired design, primarily used for producing cylindrical products. In stainless steel turning, tool materials such as hard alloys, high-speed steel, and cutting tools with advanced coatings are commonly chosen.


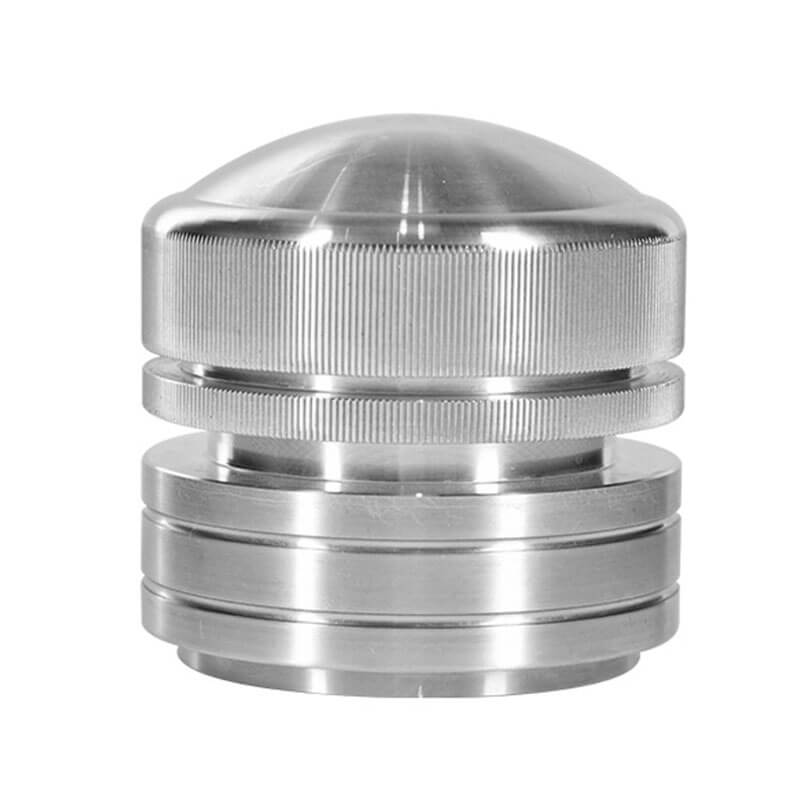


CNC Milling and Turning Stainless Steel
Stainless steel turning-milling composite machining combines turning and milling processes, typically used for challenging materials like stainless steel. Its aim is to enhance efficiency and precision while reducing the number of steps and improving material utilization. It involves roughing and contouring with turning first, followed by a switch to milling for more intricate operations such as grooving, hole drilling, and surface finishing. This approach leverages the strengths of both methods, avoiding the limitations of a single machining process. Material selection and tool geometry are critical in effectively cutting stainless steel while minimizing tool damage. Machine tool stability and rigidity also impact the quality of machining.




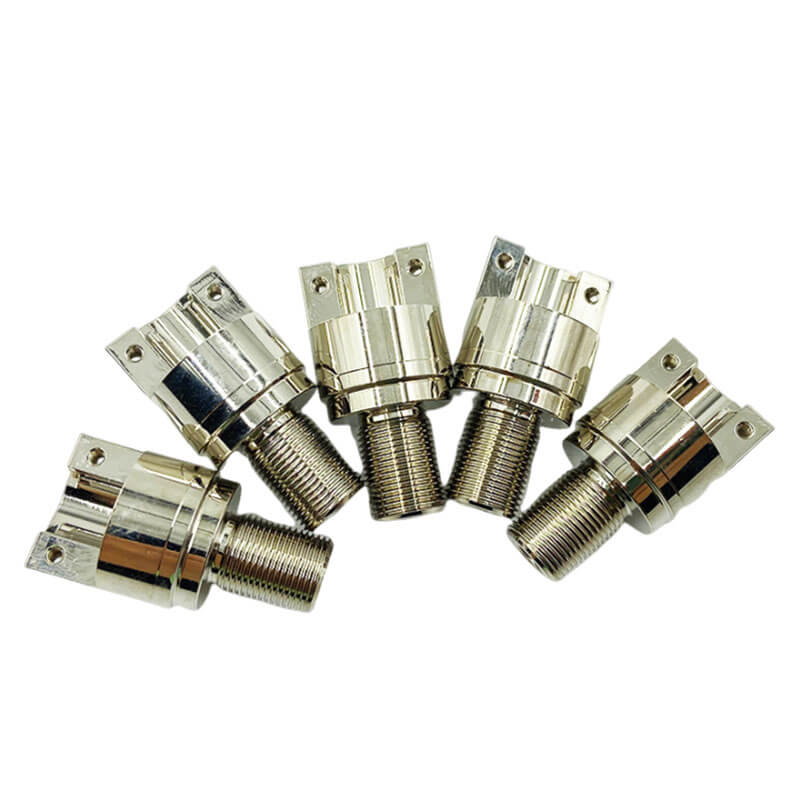
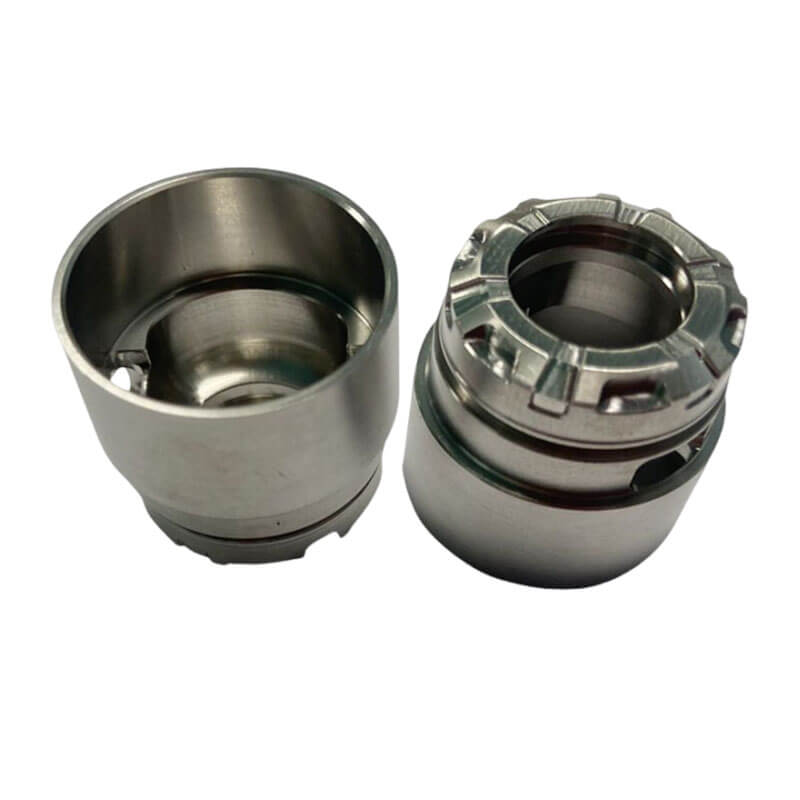
CNC Swiss Machining Brass
Masion utilizes precision Japanese-imported CITIZEN Swiss-type lathes for machining various stainless steel shafts. They are equipped with appropriate tools, cutting parameters, and coolant. By adjusting parameters such as cutting speed, feed rate, and cutting depth in the lathe’s program, they efficiently process stainless steel workpieces.
This Swiss-type lathe machining process combines turning and milling techniques and, with the use of an automatic feeding mechanism, effectively enhances the speed and efficiency of stainless steel machining. This approach not only reduces processing time but also lowers the machining costs.


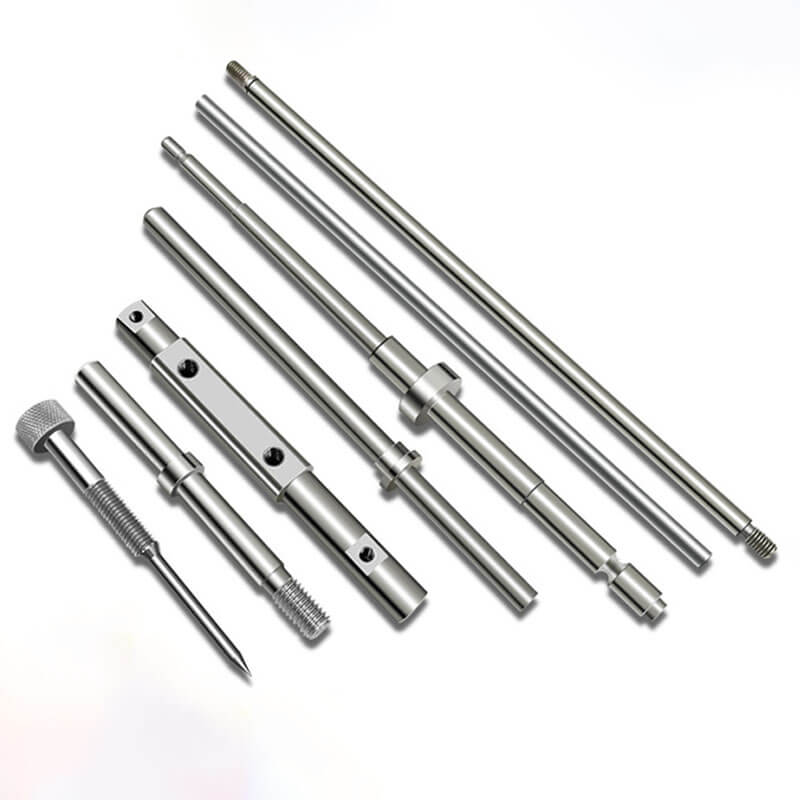


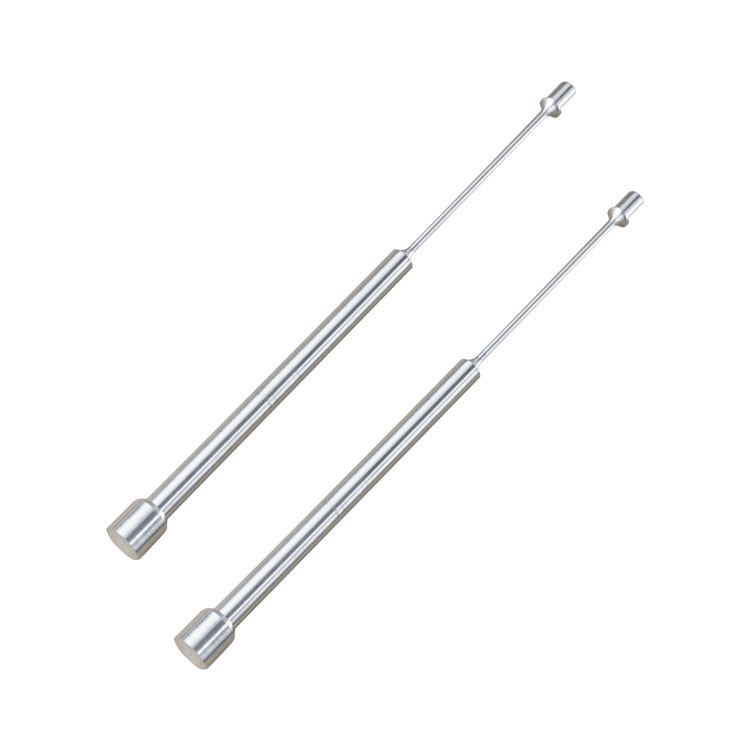
CNC Automatic Lathe Machining Stainless Steel
The automatic lathe machining of stainless steel materials is primarily focused on small part processing. This method involves driving the stainless steel workpiece to rotate through the rotation of a cam, while the cutting tools on the tool holder move along a predefined path to achieve the turning operation on the stainless steel workpiece.
One of the key advantages of automatic lathe machining for small stainless steel parts is the high level of precision control. Typically, the machining precision can reach an astonishing +/- 0.005 millimeters, which means that the manufactured parts exhibit a high degree of consistency and accuracy. This high-precision machining is crucial for the production of components that require zero error and precise fits. By combining mechanical rotation and cutting, it can achieve excellent machining quality and precise control of part dimensions, even on challenging stainless steel materials.
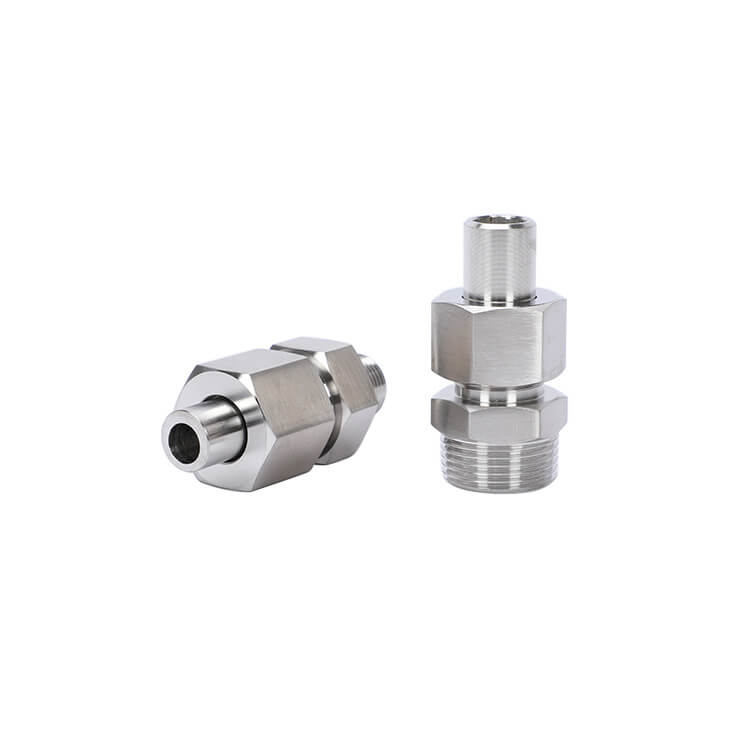
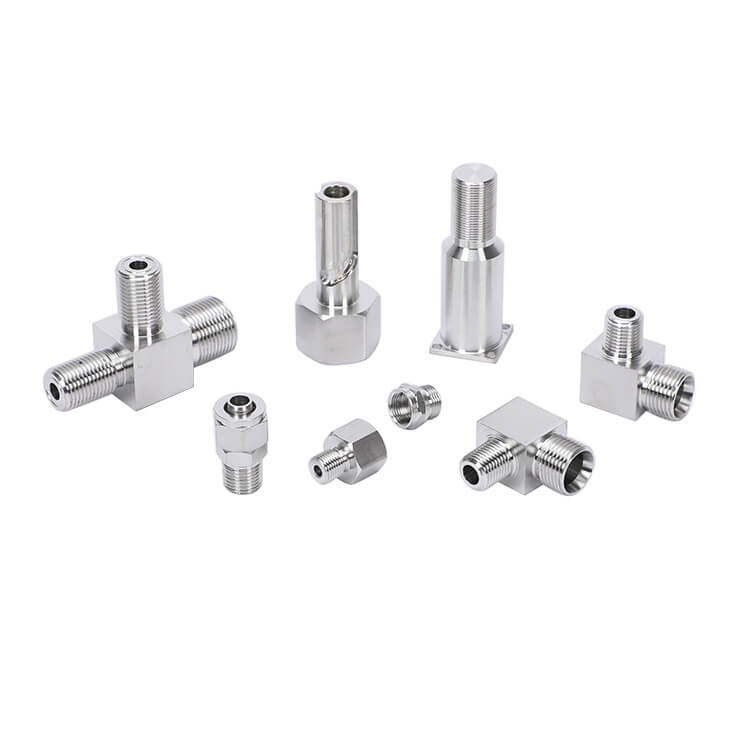
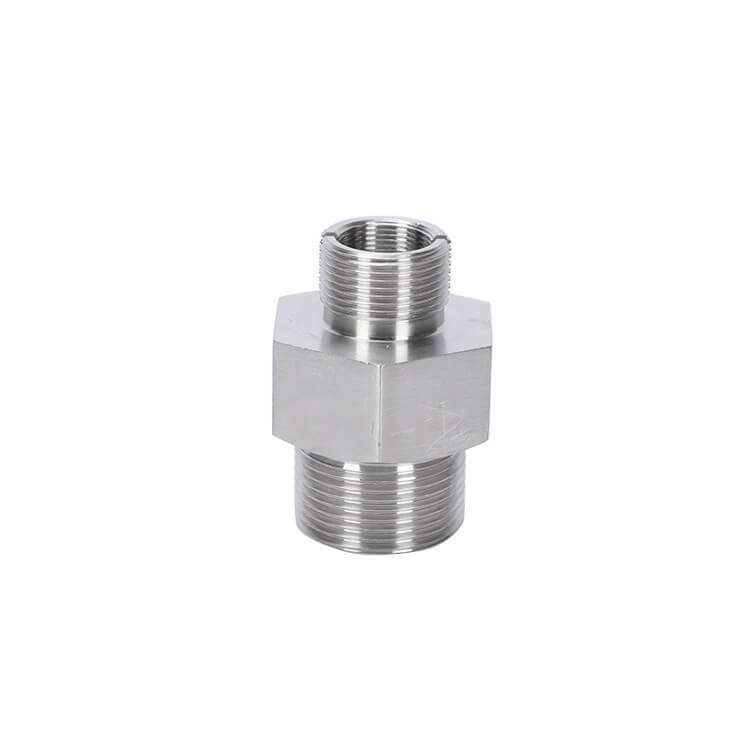


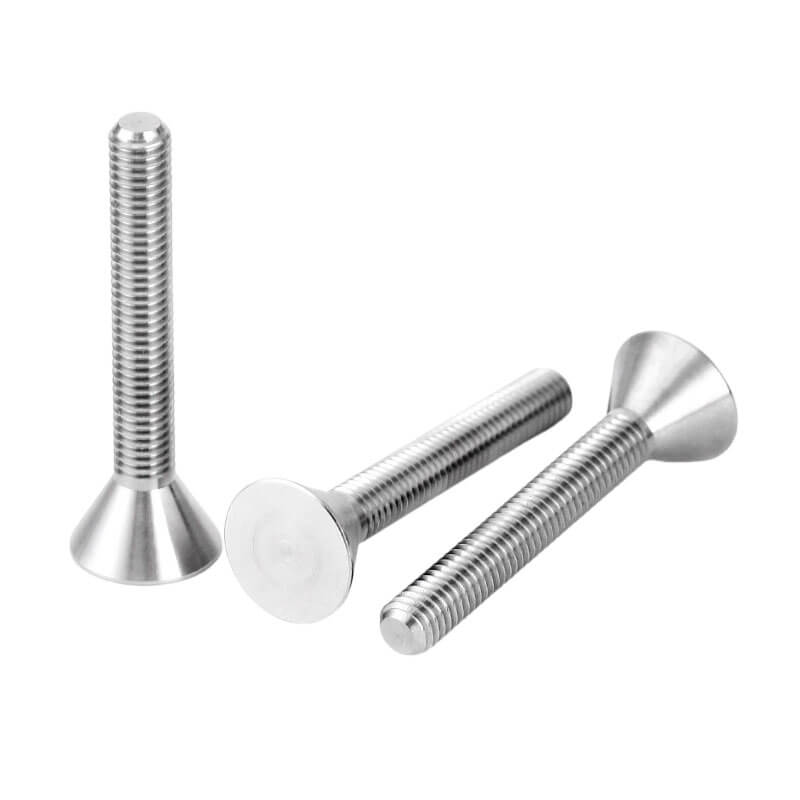
Stainless Steel Laser Cutting
Stainless steel laser cutting is a metal cutting method specifically designed for cutting materials like stainless steel. For stainless steel materials, particularly suitable is the use of a YAG (Yttrium Aluminum Garnet) crystal rod laser, as stainless steel exhibits good absorption characteristics for this type of laser. This method utilizes a high-energy density laser beam to rapidly heat and melt the stainless steel material, and then uses auxiliary gases to blow away the molten material, achieving the cutting process.
Stainless steel laser cutting offers several advantages. Firstly, it achieves high-precision cutting with dimensional accuracy at a high level. Secondly, laser cutting is a non-contact process, which doesn’t introduce mechanical stress, thus avoiding deformation and quality issues in the cutting area. Additionally, laser cutting is fast, making it suitable for efficient large-scale production.
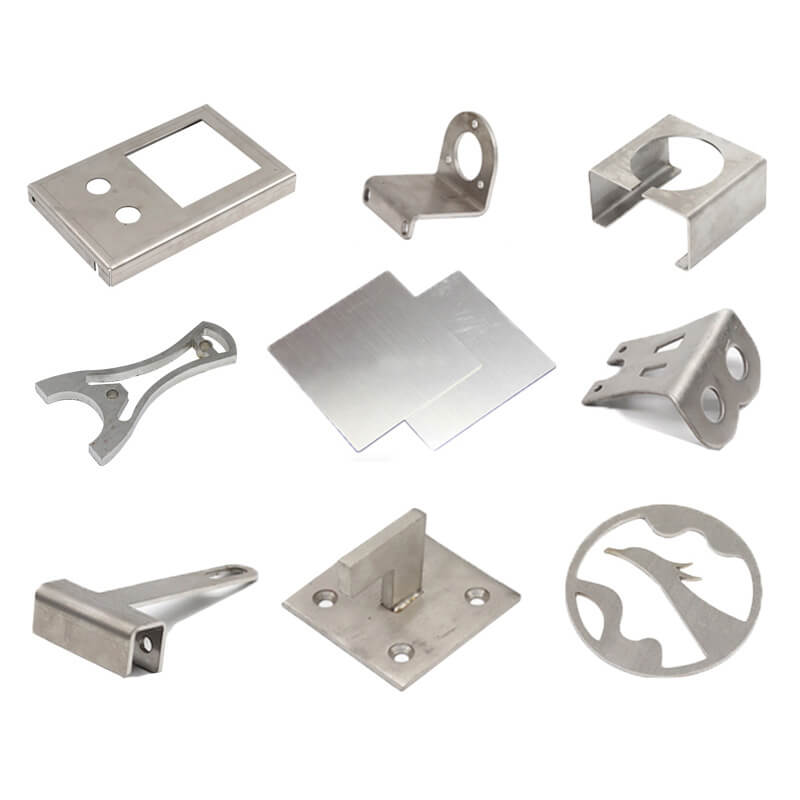
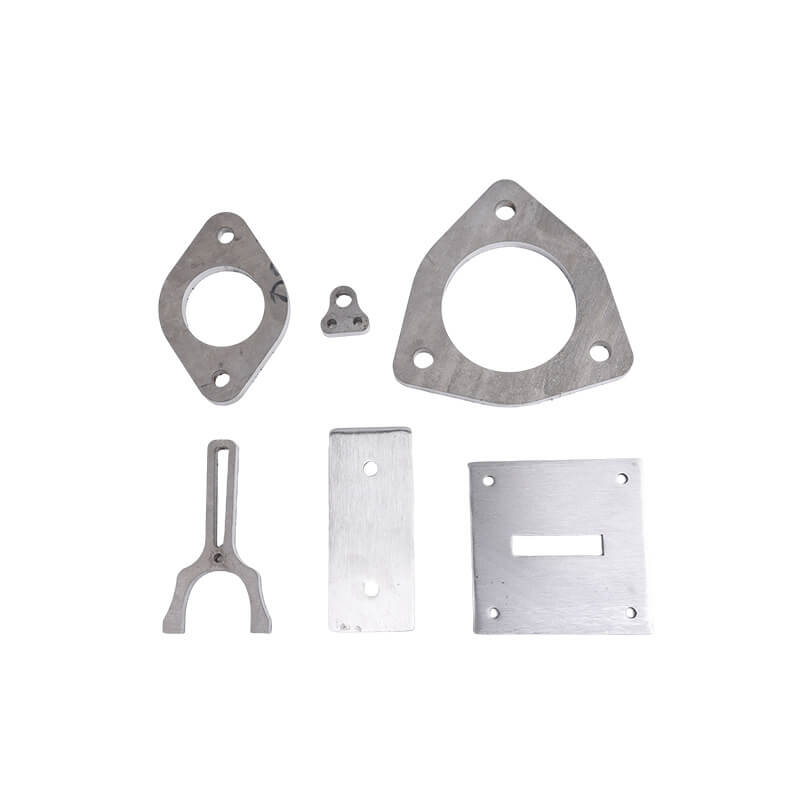
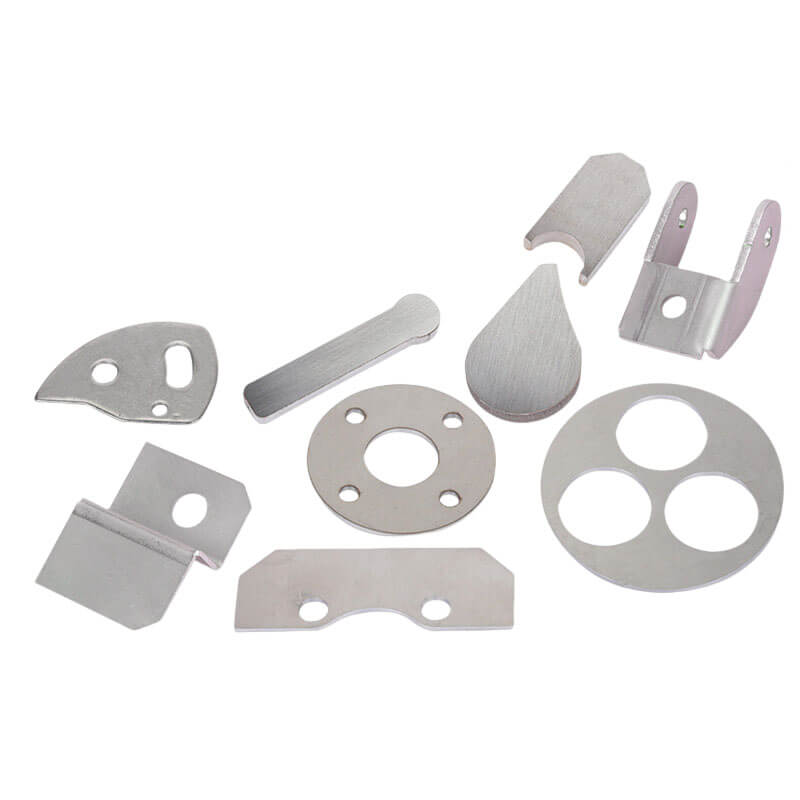


What are the Processes for Stainless Steel Material Treatment?
In the field of stainless steel processing, a series of methods such as forging, casting, cold drawing, hot rolling, extrusion, stretching, and more play essential roles. These methods lay the foundation for subsequent CNC stainless steel processing. In the initial stage, product shapes that meet design requirements can be easily formed by developing molds. Then, in the subsequent CNC processing, by removing excess material, the workpiece is precisely machined to meet the strict requirements of the design drawings, thus achieving an efficient and precise machining process.
Stainless steel is a metal material known for its high corrosion resistance and aesthetic appeal, and it is widely used in various fields such as industry, construction, and home applications. There are many different methods for the production of stainless steel, including forging, casting, extrusion, stretching, hot rolling, cold drawing, and more. Among these, forging is a common method for producing stainless steel.
Picture | Manufacturing Method | Advantages | Disadvantages | Applications | Manufacturing Process | Materials Processed | Applicable Stainless Steel Grades |
---|---|---|---|---|---|---|---|
![]() | Stainless Steel Forging | 1. Deformation at high temperatures. 2. Can be divided into hot forging and cold forging. | 1. High-temperature process. 2. Different grades of stainless steel may have different forging requirements. | Various components, parts, structural elements, etc. | Plastic deformation at high temperatures. | Stainless steel blanks | Applicable to various stainless steel grades. |
![]() | Casting | 1. Suitable for mass production. 2. Relatively low cost. | 1. Material strength and wear resistance may be compromised. 2. Potential for defects like porosity and inclusions. | Construction, automotive, machinery, etc. | Melting the material and forming it in molds. | Molten metal materials | Applicable to various stainless steel grades. |
![]() | Cold Drawing | 1. Manufactures various specifications of stainless steel materials. 2. High strength.Corrosion resistance, no deformation | 1. High energy and material costs. | Wires, ropes, metal rods, steel wires, etc. | Deformation through tension and stretching. | Stainless steel blanks | Applicable to various stainless steel grades. |
![]() | Cold-Rolled Stainless Steel | 1. Excellent surface quality. 2. High dimensional accuracy. 3. Corrosion resistance. 4.High hardness and strength. | 1. Energy-intensive process. | Construction, automotive, electronics, etc. | Shaping into sheets at room temperature, multiple rolling passes, and quenching treatment. | Stainless steel raw materials | Applicable to various stainless steel grades. |
What is the Surface Treatment of Stainless Steel
Picture | Surface Treatment Type | Principle | Process | Materials | Advantages and Disadvantages | Cost | Applications | Learn More |
---|---|---|---|---|---|---|---|---|
![]() | PVD Process | Transfer of special performance particles to the substrate using physical vapor deposition | Physical vapor deposition, such as vacuum evaporation, sputtering, etc. | Stainless steel and other metals | Advantages: Improved performance; Disadvantages: Higher cost | High | Jewelry, tools, etc. | Learn More |
![]() | Sandblasting (Shot Blasting) | High-speed spraying of abrasive materials (e.g., copper ore sand, quartz sand, emery, iron sand) using compressed air | Sandblasting with various abrasive materials | Stainless steel and other metals | Advantages: Uniform and efficient; Disadvantages: Noisy | Moderate | Surface treatment, cleaning | Learn More |
![]() | Chemical Treatment(electroplate) | Formation of stable compounds on stainless steel surfaces using chemical or electrochemical methods | Chemical treatment(electroplate), electrochemical treatment | Stainless steel and other metals | Advantages: Can achieve complex patterns; Disadvantages: Complex | Moderate | Decorations, electronic products | Learn More |
![]() | Mirror Finish | Polishing stainless steel surfaces | Physical and chemical polishing | Stainless steel and other metals | Advantages: High-end, futuristic look | Low | Furniture, architecture | Learn More |
![]() | Surface Coloring | Dyeing stainless steel using chemical or electrochemical methods | Chemical or electrochemical coloring | Stainless steel | Advantages: Adding colors, improving wear resistance; Disadvantages: May damage the oxide layer | Low | Decorations, signage | Learn More |
![]() | Surface Brushing | Brushing stainless steel surfaces | Brushing | Stainless steel | Advantages: Good tactile feel, wear-resistant, textured effect | Moderate | Electronics, kitchen appliances | Learn More |
![]() | Painting | Applying paint to stainless steel for color or texture change | Coating | Stainless steel | Advantages: Simple process, diverse color options; Disadvantages: May damage the oxide layer | Low | Furniture, product branding | Learn More |
![]() | QPQ Blackening | Formation of wear-resistant, dense layers on stainless steel through QPQ treatment | QPQ treatment | Stainless steel | Advantages: Improved wear resistance, corrosion resistance; Disadvantages: Higher cost | High | Mechanical parts, automotive components | Learn More |
Introduction to Stainless Steel Materials
Stainless steel is a corrosion-resistant, high-strength, and aesthetically pleasing metal material. It primarily consists of iron, chromium, nickel, and other elements. By adding different elements and employing various processes, various stainless steel types with distinct properties and applications can be produced. Common stainless steel materials include:
201 Stainless Steel
Gravity Casting
A relatively newer stainless steel material known for its corrosion resistance, strong formability, low density, and good workability. It is often used in the production of kitchenware and toys.
302 Stainless Steel
302 is a stainless steel grade with corrosion resistance similar to 304, but it has a relatively higher carbon content, resulting in better strength. The corrosion resistance of stainless steel is mainly determined by its carbon content, with higher carbon content leading to better corrosion resistance. The superior corrosion resistance of 302 stainless steel effectively prevents corrosion while maintaining stainless steel’s strength and corrosion resistance.
303 Stainless Steel
Grade 303 is a stainless steel type with added sulfur and phosphorus, making it easier to machine. This characteristic enhances stability during machining, increasing cutting efficiency. Sulfur and phosphorus are common additives that increase stainless steel’s hardness and corrosion resistance, making it suitable for use in specific environments.
304 Stainless Steel
304 stainless steel is the most common stainless steel material. It is commonly used to manufacture household items, kitchen utensils, sinks, and more.
316 Stainless Steel
316 stainless steel is a high-quality stainless steel type commonly used in applications requiring corrosion resistance, such as marine engineering, chemical equipment, and textile machinery. It consists of aluminum-containing variants, providing superior corrosion resistance.
321 Stainless Steel
321 stainless steel is known for its excellent high-temperature performance and is used in applications like heat exchangers, heat treatment furnaces, and automotive exhaust systems.
Characteristics and Applications of Stainless Steel Materials
Different stainless steel materials have unique characteristics and are suitable for various fields and applications. Here are the characteristics and application ranges of various stainless steel materials:
304 Stainless Steel: Known for its good corrosion resistance, ductility, and toughness. Commonly used in products with moderate corrosion resistance requirements or high abrasion performance requirements.
316 Stainless Steel: Offers higher corrosion resistance and superior mechanical properties. Commonly used in equipment and tools in industries like chemistry, textiles, paper-making, and marine applications.
430 Stainless Steel: Known for its good corrosion resistance and high-temperature strength. Frequently used in the production of furniture, appliances, and everyday items.
201 Stainless Steel: Characterized by low density, low strength, and high formability. Commonly used in the manufacturing of kitchenware, sinks, range hoods, and more.
In summary, the choice of stainless steel material should be based on specific use conditions and requirements to fully utilize their respective performance and characteristics, achieving the best results.
Stainless Steel CNC Machining FAQs
There is a common misconception that products made from stainless steel don’t rust. However, stainless steel can indeed rust, although it is relatively resistant to rusting in ordinary environments. It has a thin and tightly adhering oxide layer on its surface, which acts as a protective film, preventing oxygen atoms and external corrosive factors from affecting the inner surface for a certain period. This maintains a state of relative resistance to oxidation and rust.
Nevertheless, when the protective film on the surface of stainless steel is continually damaged, oxygen atoms from the air or liquids can infiltrate, and iron atoms from the metal can leach out, leading to chemical reactions that form a loose, iron oxide layer (rust). Over time, this corrosion process results in rust on the surface of stainless steel.
During the CNC machining of stainless steel, the surface may accumulate dust and particles of other metal elements or environmental contaminants. In a humid environment, this can lead to electrochemical reactions on the stainless steel surface, breaking down the original protective film. This is known as electrochemical corrosion and is one of the factors that cause stainless steel to rust.
If the environment in which stainless steel is machined, stored, or transported contains a significant amount of sulfides, chlorides, or other acidic ions and comes into contact with humid air or moisture, it can create an acidic liquid. Over time, this can also cause chemical corrosion of the stainless steel, leading to rust.
To prevent stainless steel from rusting, manufacturers and storage facilities should take effective preventive measures, which may include the following suggestions (for reference only):
During the machining of stainless steel, avoid using the same machining equipment for other metal materials to prevent contamination from metal dust.
Before surface treatment, clean the finished stainless steel products to remove dust, dirt, oil stains, and rust spots from the surface.
If there are rust spots or traces on the surface of stainless steel materials before machining, perform rust removal (recommended environmentally friendly rust remover that does not corrode the stainless steel surface, such as VCI-708 organic acid-based rust remover).
Ensure that the cutting fluids, mechanical oil, human sweat, and airborne dust on the stainless steel surface are thoroughly cleaned to avoid affecting subsequent surface treatments and maintain cleanliness for storage and transportation (recommended VCI-600E biodegradable and environmentally friendly cleaning agent, a water-based product with plant-based components, safe and effective for cleaning surfaces below 200μm).
For stainless steel storage and transportation, use rust-proof packaging and add desiccants inside the packaging. This helps prevent the formation of condensation on the stainless steel surface, reducing the risk of corrosion in a closed environment for an extended period (recommended VCI-2000 rust-proof bags and VCI desiccants).
Milling stainless steel typically requires a spindle speed ranging from 200 to 1000 RPM. In general, the specific required spindle speed typically depends on different materials ofcutting tool, the dimensions of the workpiece, and the machining requirements.
The feed rate for milling stainless steel should be between 0.05 to 0.2 mm per tooth of the cutter. The exact value depends on the required surface roughness, spindle speed, and the material of the cutting tool.
Characteristics of Milling Stainless Steel:
Stainless steel is a common material with a high level of machining difficulty. It has strong adhesion and melting characteristics, causing chips to adhere to the cutter’s teeth, which deteriorates the cutting conditions. During up-milling, cutter teeth initially slide on the hardened surface, increasing the tendency for work-hardening, leading to more significant impacts and vibrations during milling, making the cutter teeth more prone to wear.
Milling Stainless Steel Techniques:
When milling stainless steel using a machining center, the selected milling cutter’s blade should be extremely sharp to better withstand the impact forces generated during milling. Additionally, the chip groove of the milling cutter should be wide. When machining stainless steel, you can choose a vertical milling cutter, cylindrical milling cutter, or helical milling cutter. The helix angle of the cutter can be set to 45°. Moreover, the rake angle of the milling cutter should be adjusted to reach 27° or more.
CNC Machining Precautions:
When aligning the workpiece, use hand rotation of the chuck or low speed to align; avoid high-speed alignment.
When changing the spindle’s rotation direction, stop the spindle first before changing the direction suddenly.
When mounting or dismounting the chuck, only use hand rotation to drive the spindle’s rotation; do not forcibly loosen or tighten directly, and place a wooden block on the bed surface to prevent accidents.
Tool installation should not extend too far, and shims should be flat, with a width matching the cutter’s bottom width.
Do not use reverse turning of the spindle to brake during work.
The significant price difference between Stainless steel 304 and Stainless steel 201 can be attributed to three main factors:
Nickel Content: 304 stainless steel contains a higher proportion of nickel, typically ranging from 8% to 10.5%, whereas 201 stainless steel contains only 3.50% to 5.50% nickel. Nickel content directly affects a material’s corrosion resistance. Thus, 304 stainless steel exhibits superior corrosion resistance and oxidation resistance.
Ductility: 201 stainless steel has a higher carbon content, around 0.15%, while 304 stainless steel has a carbon content of approximately 0.07%. This makes 201 stainless steel relatively harder, while 304 stainless steel is more ductile. Scratches on 201 stainless steel surfaces tend to be more noticeable compared to 304 stainless steel.
Brightness: 201 stainless steel contains a higher manganese content, around 5.5% to 7.5%, while 304 stainless steel has lower manganese content, not exceeding 2%. In terms of appearance, 201 stainless steel tends to have a darker color, while 304 stainless steel is brighter. This difference in brightness is one of the factors contributing to the higher price of 304 stainless steel.
For improved machining performance, 303F stainless steel is a good choice. It offers excellent machining properties and can help address various machining challenges. If you are working with materials that are too hard or have poor machinability, it can lead to issues such as reduced product quality and increased costs. 303F stainless steel is the solution because it features a higher sulfur content, enhancing its machining performance. It reduces burrs and other issues during machining, leading to higher production efficiency and better product quality. Whether you’re machining bolts or nuts on automatic lathes, 303F stainless steel’s advantages will shine.
440C stainless steel is favored for its wide range of applications. It offers excellent dimensional stability at high temperatures, making it suitable for high-temperature bearing steel. Its excellent straightness, down to around 0.005mm, ensures precision and stability in products. Moreover, 440C stainless steel can be used to manufacture high-quality cutting tools, such as medical scalpels, scissors, nozzles, bearings, and more. It possesses good hardness and wear resistance, making it a reliable choice for various tasks.
430F stainless steel is an excellent choice for automatic lathe machining. It offers outstanding high-temperature dimensional stability and is ideal for machining bolts and nuts. With excellent straightness, it ensures high precision and surface finish. The 430F stainless steel’s machining performance is superb, making it a reliable choice for applications that demand high precision, straightness, and surface finish.
In engineering design, both 303 and 304 stainless steel, which belong to the austenitic stainless steel 300 series, are commonly used. However, there are significant differences between them. 303 stainless steel contains added sulfur, reducing its corrosion resistance. In terms of machinability, 303 stainless steel is favored for its excellent performance and is used in parts that require extensive machining. It has better machinability and is easier to work with. On the other hand, 304 stainless steel is more challenging to machine but offers superior overall mechanical properties. Thus, 304 stainless steel is more suitable for applications that demand high surface finish and cutting requirements. In terms of corrosion resistance, 304 stainless steel generally outperforms 303 stainless steel. Its lack of sulfur makes it more resistant to corrosion, especially in harsh environments like seawater and chloride exposure.
Free Sample
Explore Other Materials
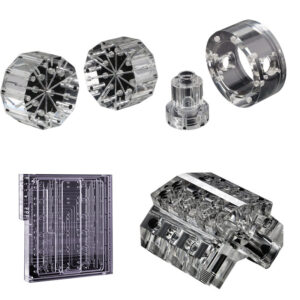
CNC PMMA Machining
PMMA is a material with high mechanical strength, strong dimensional stability, and excellent resistance to creep. PMMA sheet is a high-performance acrylic glass widely used in applications such as construction,
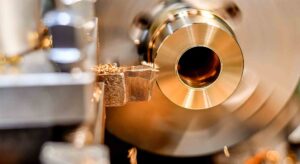
CNC Machining Bronze
There are many types of bronze, with commonly used ones including phosphor bronze, tin bronze, and aluminum bronze. Additionally, there are less commonly used types like beryllium bronze, silicon bronze,

CNC FR4 Machining
FR4 boards, made from a composite of glass fiber cloth and epoxy resin (with “FR4” denoting the cloth specification), come in common thicknesses of 1.6mm and 1.2mm. They are also