CNC Machine Shop
All you need to know about CNC machine shops is here.Top 11 tips about CNC machining shop.
Abstract:When I mention “CNC machine shop,” you might think we are a CNC machining ‘store ’selling CNC equipment. If I use different terms like “CNC machining workshop,” “CNC workshop,” or “CNC machining manufacturer,” you would quickly understand that we are a CNC manufacturing facility. In the following text, I will provide detailed information and considerations about the workshop and share tips on how to choose a local CNC machine shop. Let’s start the introduction to a CNC machine shop!
Definition: What is CNC Machine Shop?
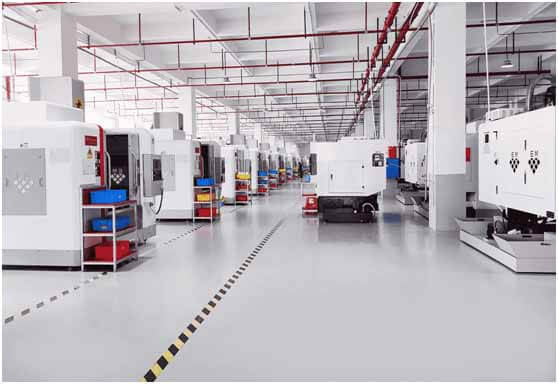
What is the Brief History of CNC Machine Shop?
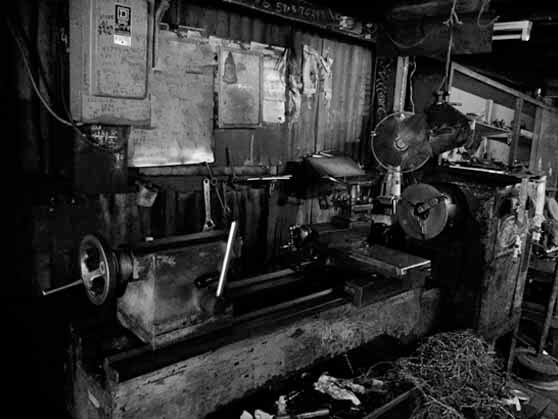
What Does a CNC Machine Shop Do?
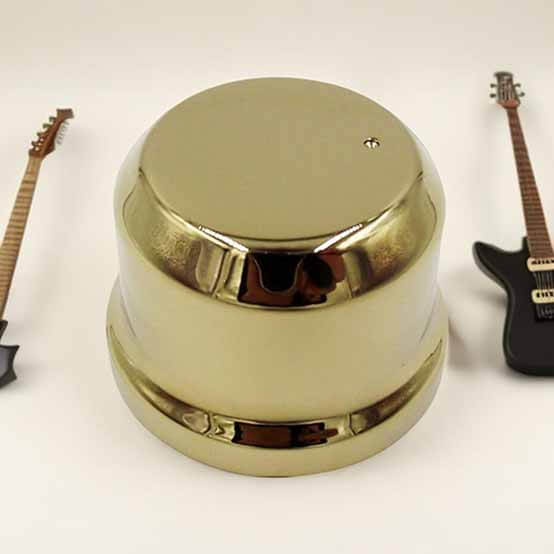
What Does the CNC Machine Shop Consist of?
The composition of a machine shop is generally determined based on factors such as the type of production and the technological characteristics of the products. The composition can vary depending on the type of workshop. Generally, a machine shop consists of two main parts:
Production Department:
Auxiliary Department:
CNC machines
Cutting tools
Workholding devices
Inspection and measurement equipment
Skilled personnel
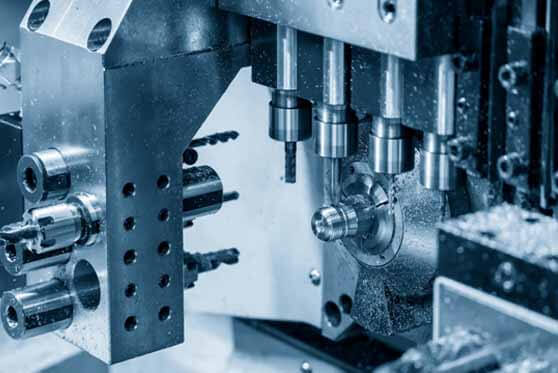
How Many Types of Shops are there in CNC Machine Shops?
CNC milling workshop:
5-axis CNC machine workshops
CNC cutting workshop
Large CNC machining workshop
Precision CNC machine workshop
CNC Grinding Workshop
CNC boring machine
Honing machine
CNC Swiss Lathe Machining Workshop Link to CNC Swiss lathe machining service)
CNC Turning-Milling Workshop Link to CNC turning-milling service
Another CNC machine workshop:
CNC drilling machine: CNC Drilling Machine is primarily used for drilling, reaming, tapping, and other hole machining operations. It is a digitally controlled machine tool primarily designed for hole processing with drilling as the main operation.It is more powerful and stable than a handheld drilling machine and can be used for various manufacturing tasks.
CNC boring machine:One method of mechanical machining using a boring tool on a CNC boring machine is CNC boring and milling. CNC boring and milling mainly involve flat milling, and contour milling, as well as drilling, reaming, countersinking, boring, tapping, and thread machining of the workpiece.
CNC punching machine: Also known as a numerical control punching machine, it is an automated machine tool equipped with a programmable control system. The control system can logically process programs specified by control codes or other symbolic instructions and decode them to initiate the punching machine’s actions and process the parts.
EDM (Electrical Discharge Machining) machine: Electrical discharge machining (EDM) refers to a specialized machining method that utilizes electrical and thermal energy to generate pulsed electrical discharges in a specific medium between the tool and the workpiece. These discharges create localized, momentary high temperatures, gradually eroding the metal material. The process is called electrical discharge machining due to the visible sparks generated during the discharges. It is widely used in the manufacturing of metal molds and mechanical equipment. It is also known as electrical discharge machining or EDM.
Electrochemical machining (ECM): A method of machining metal materials using electrochemical reactions (or electrochemical corrosion).Unlike CNC machining, electrochemical machining (ECM) is a specialized machining method that utilizes the principle of electrochemical anodic dissolution of metal in an electrolyte to shape the workpiece. It is capable of processing materials of any hardness. Common electrochemical machining methods include electrochemical machining, electro-grinding, electrochemical polishing, electroplating, electrochemical etching, and electrolytic refining.
3D printer: We usually called it 3D printing or additive manufacturing, it is a technology that constructs objects layer by layer using digital model files as a basis and adhesive materials such as powdered metal or plastic.
Laser marking machine: Laser marking technology is one of the major applications of laser processing. It uses high-energy-density lasers to locally irradiate the workpiece, causing vaporization or color change reactions on the surface layer materials, leaving a permanent mark. Laser marking can create various characters, symbols, patterns, etc., with character sizes ranging from millimeters to micrometers, which is particularly significant for product anti-counterfeiting.
Surface processing tools: Various equipment is used for grinding, polishing, sandblasting, and coloring as most parts require some form of surface treatment.
Sandblasting machine: A sandblasting machine is a device that uses compressed air as power to create a high-speed jet to propel abrasive materials (such as glass beads, steel shot, steel grit, quartz sand, garnet, iron sand, or sea sand) onto the surface of the workpiece to be treated. Its main purpose is to impact the surface of the object through high-speed abrasive particle projection, achieving the removal of surface dirt, oxide layers, scratches, coatings, and rust.
Vibratory finishing machine: Through the action of the vibratory motor rotating at high speed and the effect of the spring, the grinding stones, water, and grinding fluid in the grinding groove undergo regular relative motion with the processed parts. This results in the removal of burrs or oxide layers protruding from the surface of the parts, as well as the rounding of sharp corners and polishing.
Ultrasonic cleaning machine: Ultrasonic cleaning utilizes the cavitation, acceleration, and direct flow effects of ultrasonic waves in a liquid to directly or indirectly act on the liquid and dirt. This disperses, emulsifies, and removes the dirt layer, achieving the purpose of cleaning. Currently used ultrasonic cleaning machines mostly apply the cavitation effect and direct flow effect.
Polishing machine:A polishing machine is an electric tool used for the processing and modification of the surface of workpieces through the use of flexible polishing tools and abrasive particles or other polishing media. The working principle involves the high-speed rotation of a sponge or wool polishing pad driven by an electric motor. The polishing pad and polishing compound work together to create friction with the surface to remove paint contaminants, oxide layers, and shallow scratches.
Inspection equipment
Coordinate measuring machine (CMM): A Coordinate Measuring Machine (CMM) refers to an instrument capable of measuring geometric shapes, lengths, and circularity within the spatial range of a hexahedron. CMMs are helpful in ensuring accuracy and quality.
3D projector: A device used for 3D projection, which allows for the visualization of objects in three dimensions.
3D scanner: A device used to capture the three-dimensional shape and structure of an object, creating a digital representation of the object.
Vernier caliper: A measuring instrument with a scale and a sliding jaw used to measure dimensions with high precision.
Micrometer caliper: Also known as a micrometer, it is a measuring instrument used for precise measurement of small distances or thicknesses.
Thread gauge: A tool used to measure the pitch or size of threads on screws or bolts.
Go-No Go Gages: A measuring instrument used to determine the depth of holes, slots, or other features in a workpiece.
How is the CNC Machine Shop Layout
Division and Layout of the Mechanical Machining Workshop
The following principles should be followed when formulating the workshop zoning:
Principle of minimum transport distance: The workshop zoning should minimize the distance for material transportation and flow during the production process.
Process principle: Equipment should be arranged according to the sequence of production processes to determine the positions of various departments.
Space utilization principle: When arranging the workshop, attention should be given to effective space utilization, and measures such as basements or platforms can be taken to save floor space for facilities and departments.
Principle of convenience and safety for workers’ work: Ensure that workers can work conveniently and safely.
Principle of future development and flexibility for adjustments.
Principles of Workshop Equipment Layout Design
Principle of process specialization
However, process-specialized production units cannot independently complete all machining tasks for a product (part). Each product must pass through multiple production units before completion, which has the following drawbacks:
Principle of object specialization
Object specialization involves setting up production units based on products (components). Within object-specialized production units, various types of production equipment and workers with different skills required for manufacturing the product are concentrated. Each production unit can independently complete most or all of the process for the product without assistance from other units. This approach is commonly used in workshops such as engine workshops or chassis workshops in automobile manufacturing plants.Organizing production units according to the specialization of objects has the following advantages:
The disadvantages are as follows:
Hybrid Principle
Workshop Equipment Layout Design Forms
Content of Workshop Equipment Plan Layout
Forms of Workshop Equipment Layout
Based on the principles of workshop equipment layout and the division of production lines and part processing flows, there are generally several forms:
The U-shaped layout has the following characteristics:
The U-shaped layout has the following advantages:
Spacing between Machine Tools
How to Manager CNC Machine Shop?
Workshop Site health management
Timely clean the public areas according to the hygiene zones.
Workpiece Placement Management
Workstation Site Management
Process Management
Quality Management
Equipment Maintenance and Management
Safety Management
How to diversify the functions of a CNC machining workshop?
One-stop service:
Surface treatment:
Sandblasting machine:
Vibratory deburring machine:
Ultrasonic cleaning:
Polishing machine:
Laser marking:
Quality control process:
Incoming inspection
In-process inspection:
100% inspection before packaging:
Qualified technicians with technical expertise:
A professional technician should possess the following skills:
How to Keep CNC Machining Shop Safe?
Ensuring machine shop safety is crucial due to the presence of various hazards in the workshop. Here are some tips to keep workers safe when they are working in the CNC machining shop.
For moremachine shop safety rules please go to
Seven Tips to Know the Capabilities ofReliable and Qualified CNC Machining Shop?
When developing a new project and searching for a matching CNC machining shop, it’s important to have a precise understanding of the capabilities offered by the shop. Choosing a small shop CNC can be beneficial in saving time. Here we list some tips for your reference in making a better choice.
Supplier's capabilities:
Supplier's materials:
Supplier's methods:
Supplier's qualities:
Supplier's reputation:
Supplier's certifications:
Supplier's after-sales support:
WhatOur CNC Machine Shop Could Serve for You?
The professional design team for creating 2D or 3D CAD models:
Competitive pricing:
Quality assurance:
One-stop service:
Free samples:
No minimum order quantity:
Quick response service:
Conclusion:
Free Sample
Explore Other Guide and resource
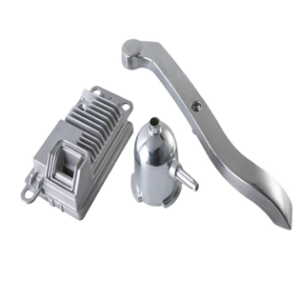
Aluminium Passivation
Aluminium is a non-ferrous light metal. Aluminium and Aluminium alloys have the characteristics of high specific strength, excellent plasticity, excellent electrical and thermal conductivity, and good processing performance and corrosion

Automatic Lathe Machining
An automatic lathe is a highly capable and precise machine that can continuously and repetitively be machining a variety of materials, including aluminum, iron, copper, zinc alloy, and plastic, among
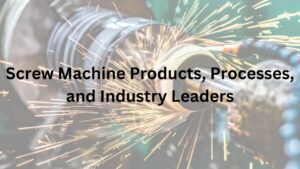
Screw Machine Products, Processes, and Industry Leaders
Explore comprehensive Swiss Machine Products guide covering tools, techniques, and top manufacturers. Master the art of precision manufacturing for optimal results.