5 axis CNC machining parts
5 axis CNC machining parts
CNC 5 axis cnc machining parts,5 axis cnc parts manufacturer in China.
MOQ Starts from 1pcs.
As a specialized 5-axis CNC machining part, and 5-axis CNC parts manufacturer, Masion provides high-quality custom 5-axis CNC machining parts services to customers with outstanding production advantages, advanced technological capabilities, and professional solution offerings.
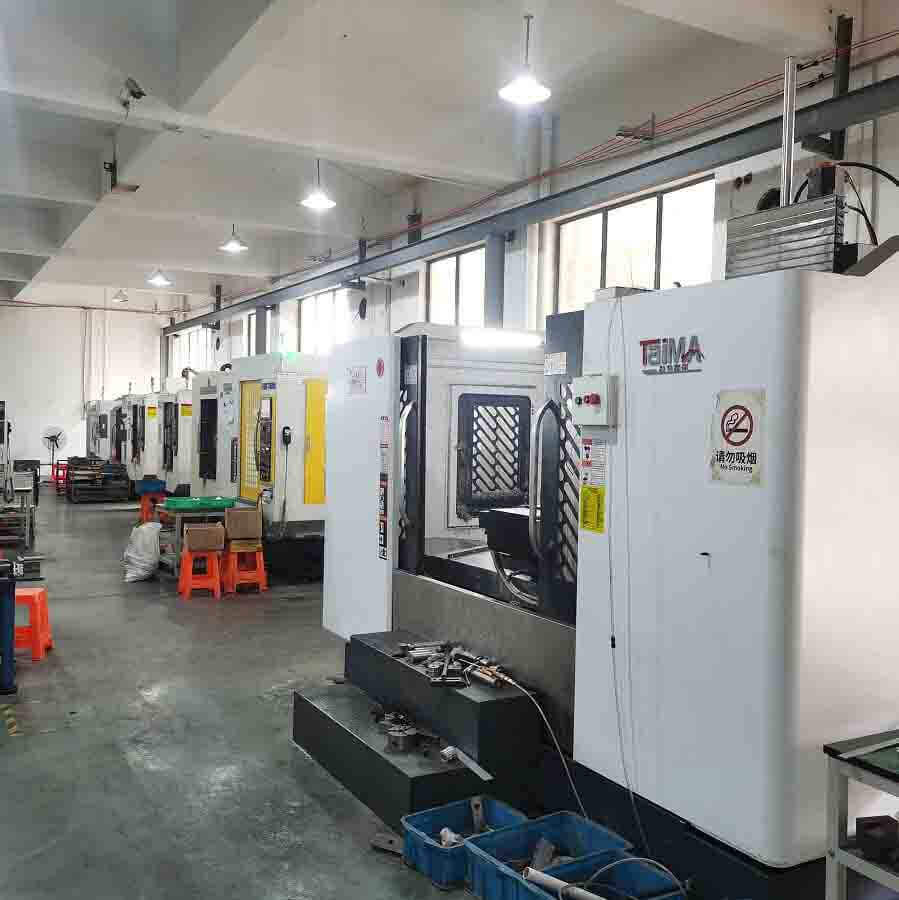
Masion Capability
High Capacity, Proper Price
Free Samples, Low MOQ
Certified Factory, Guaranteed Quality
High precision, Good surface
Our Products
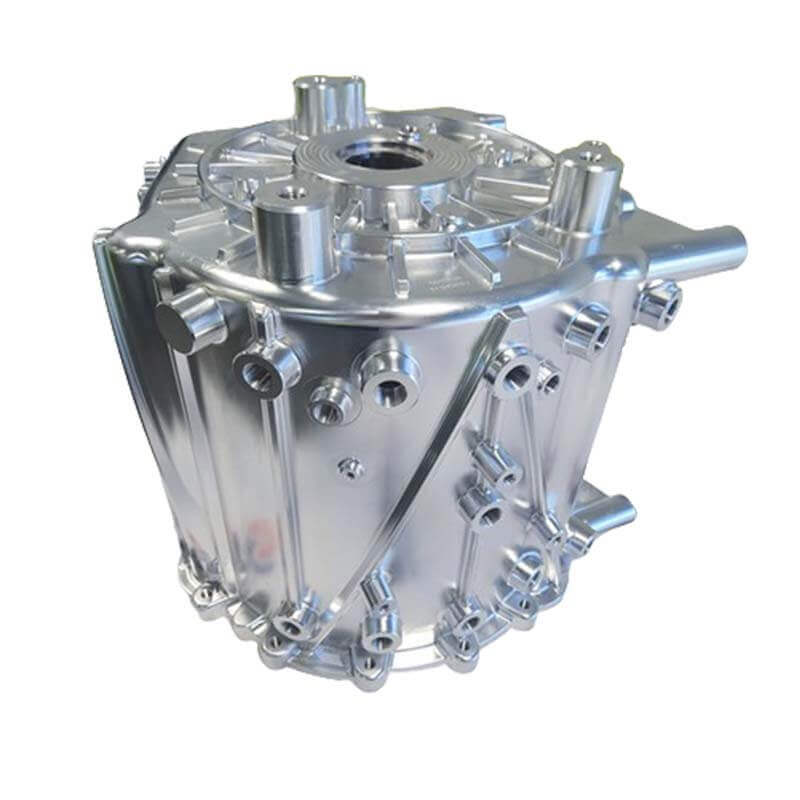
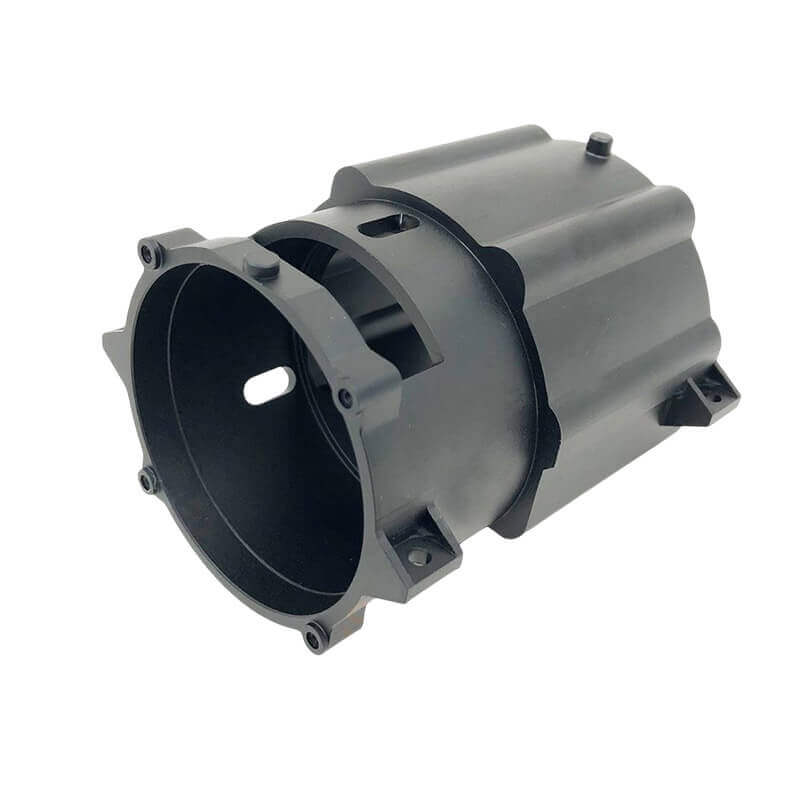
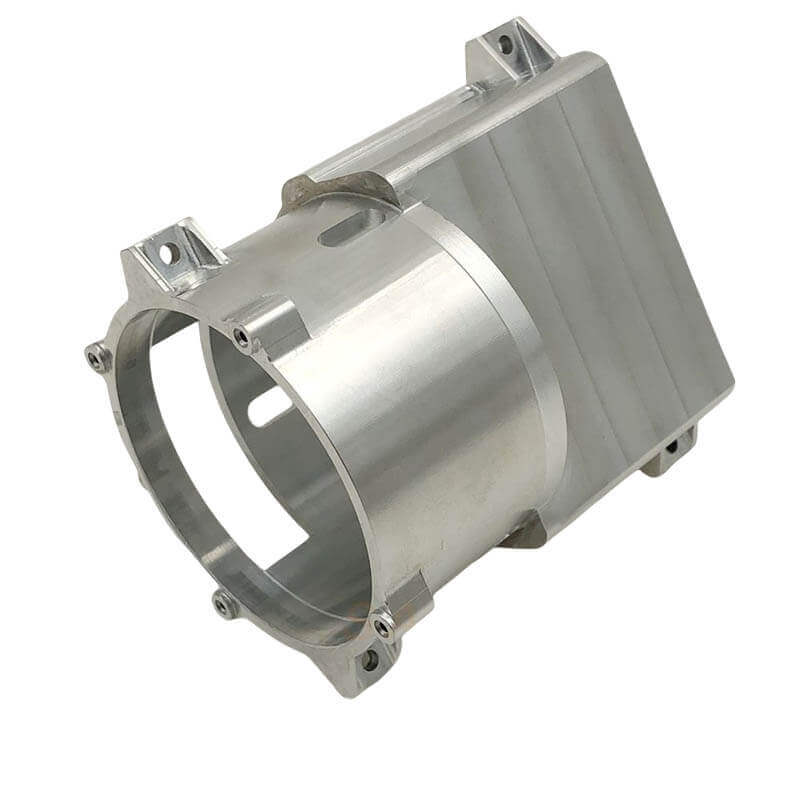
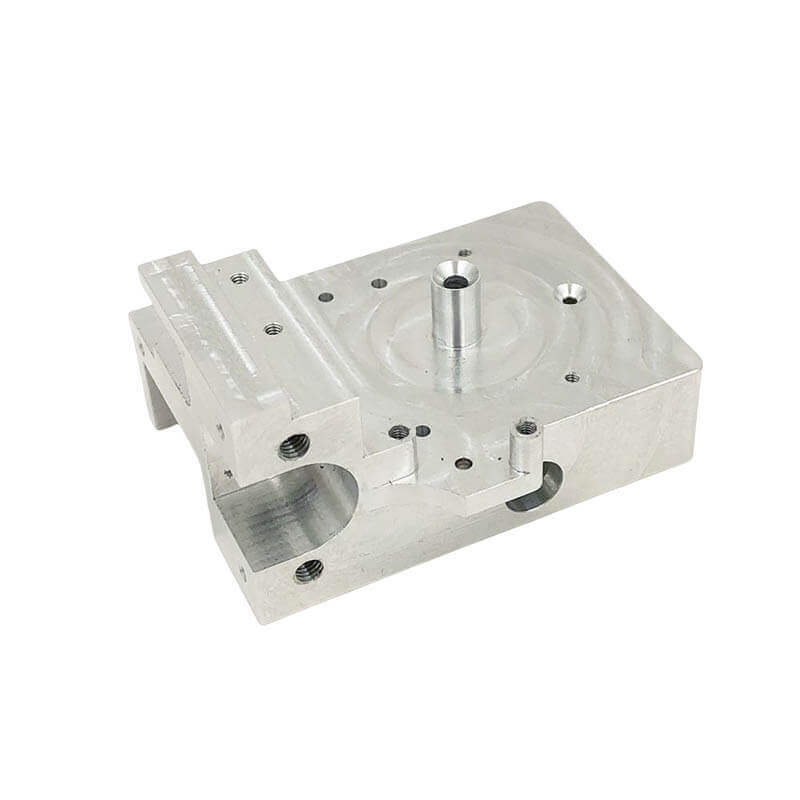
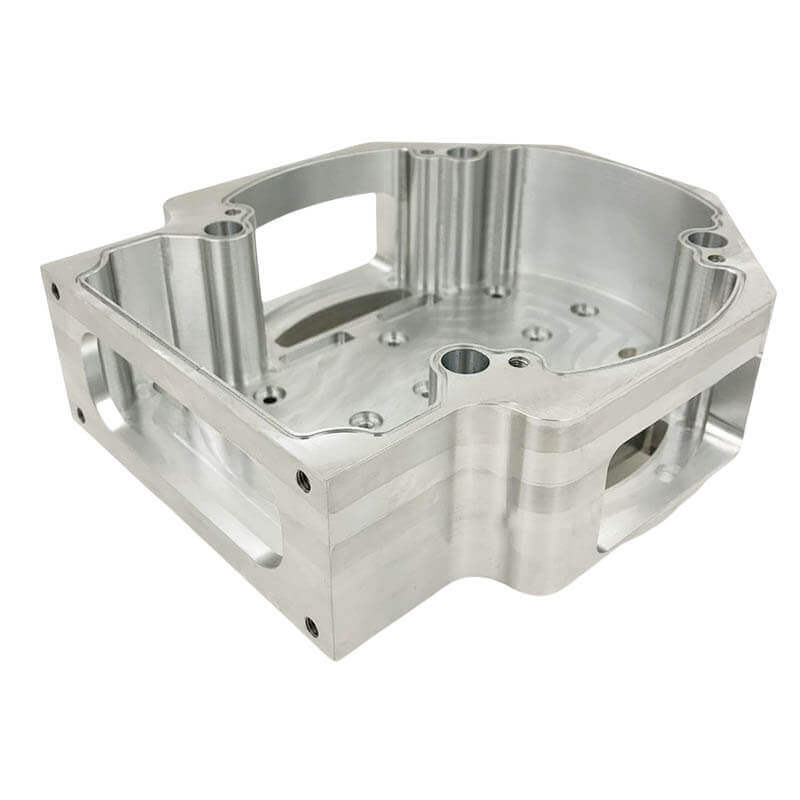

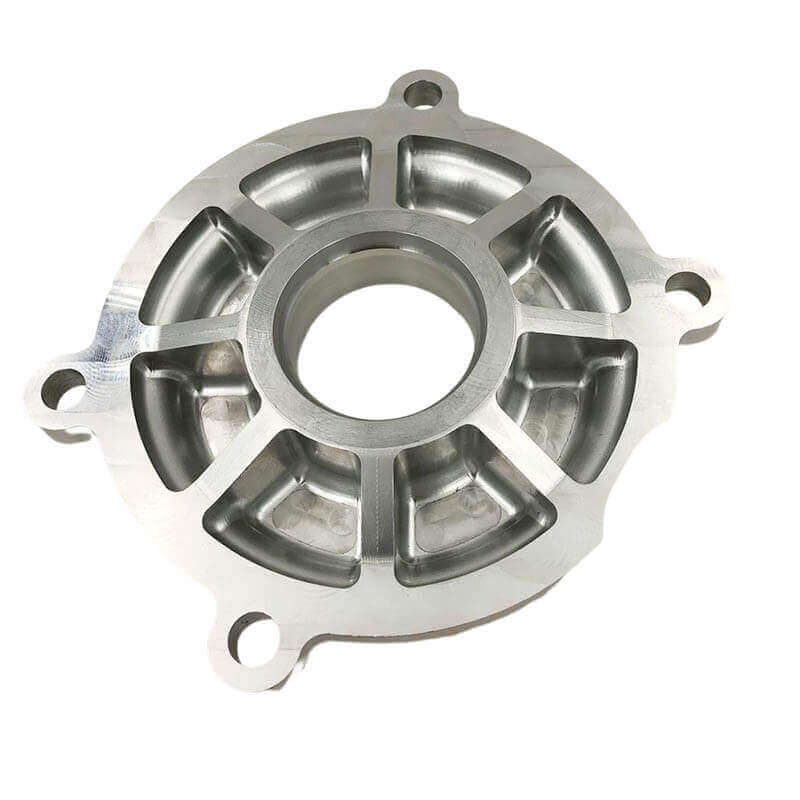
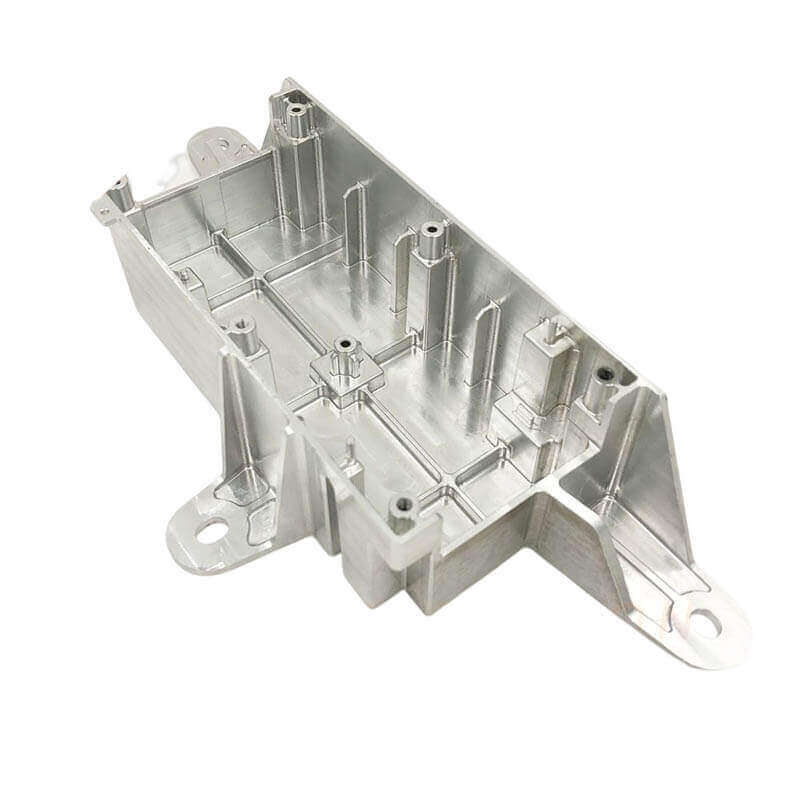
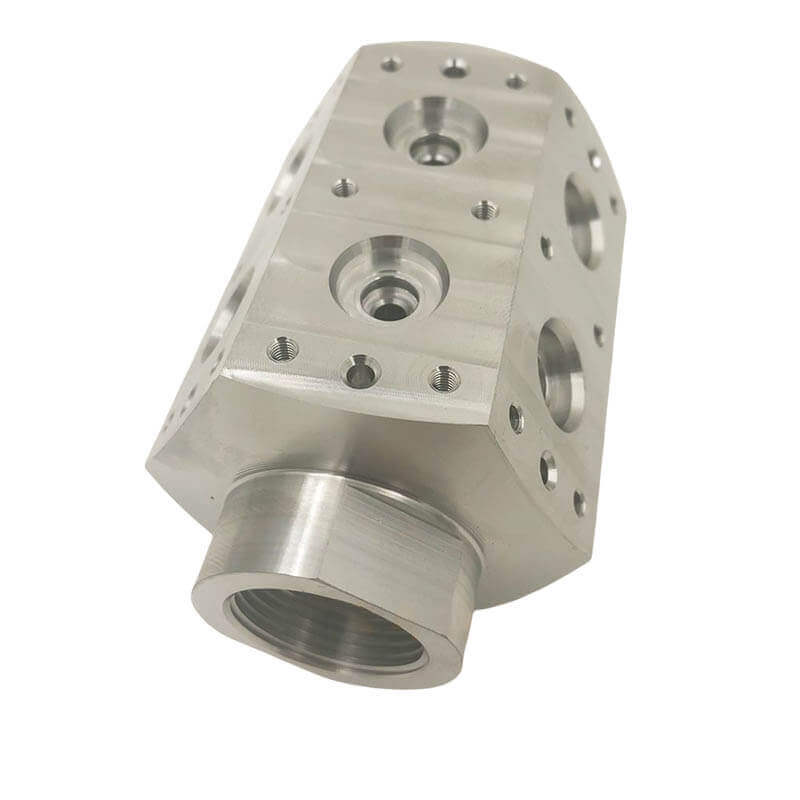
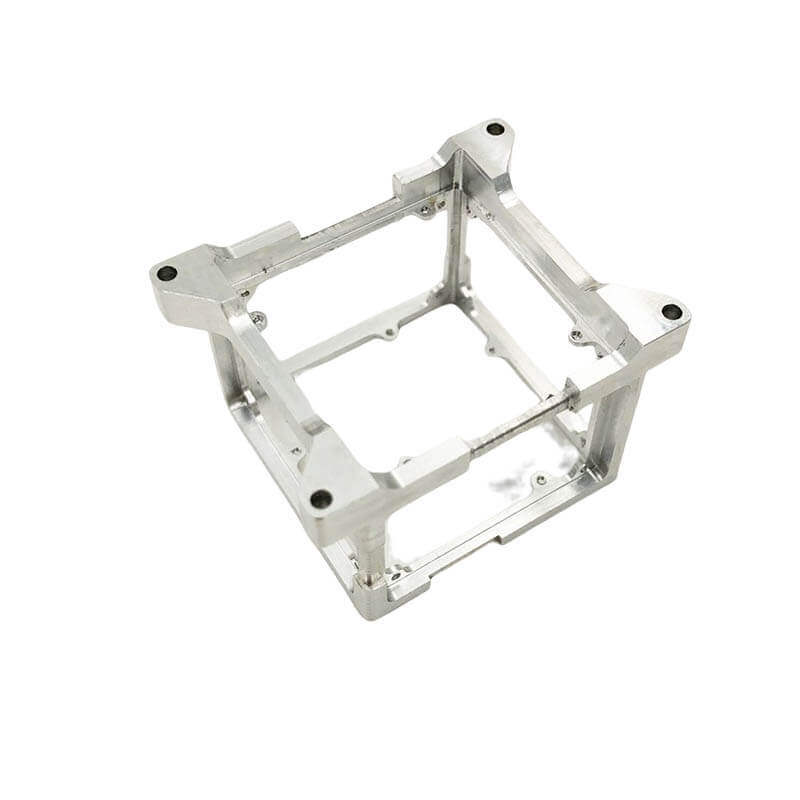
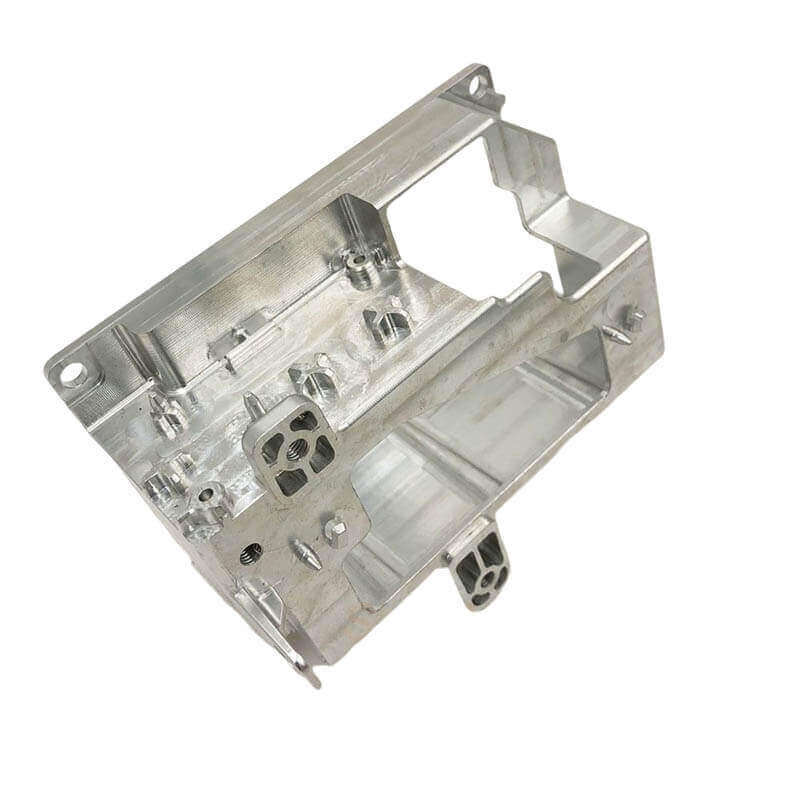

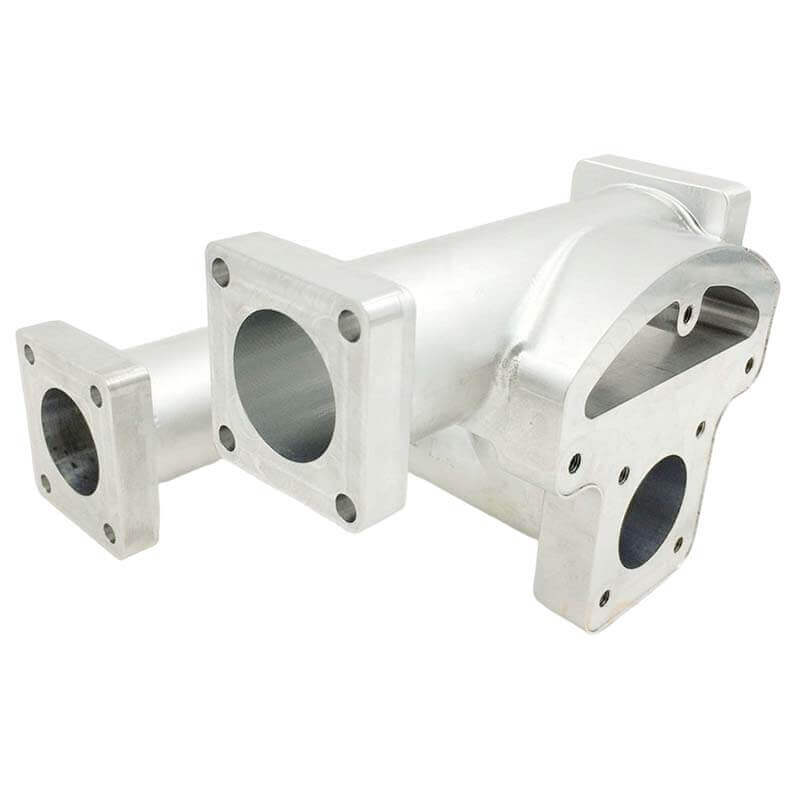
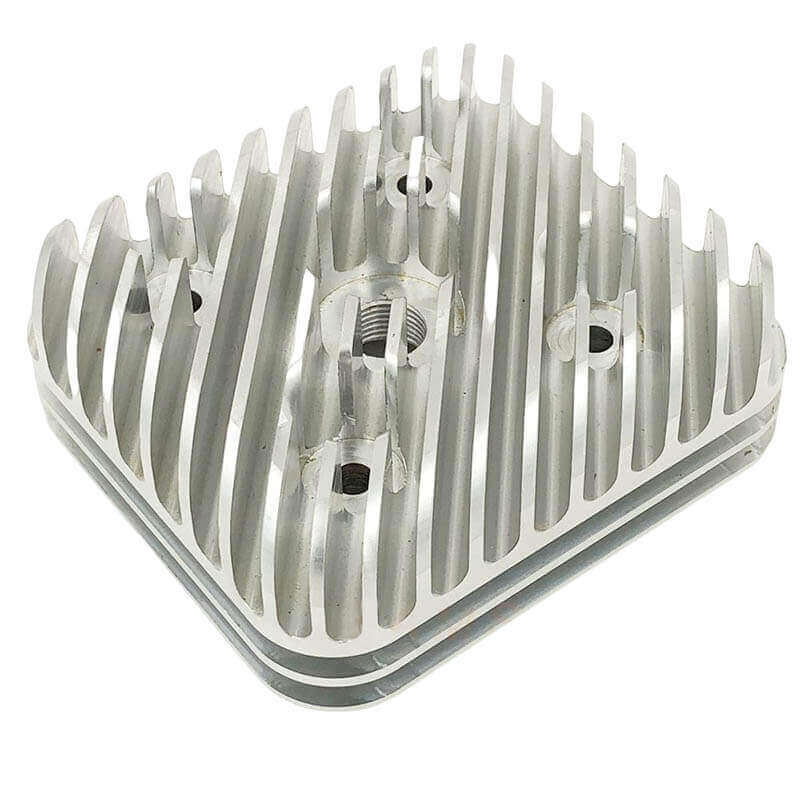
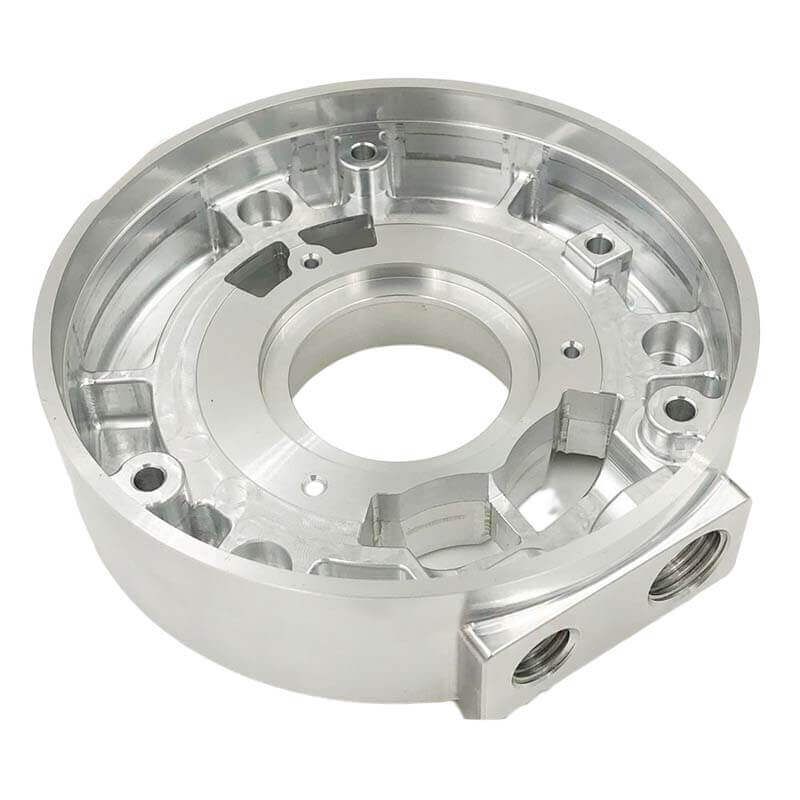
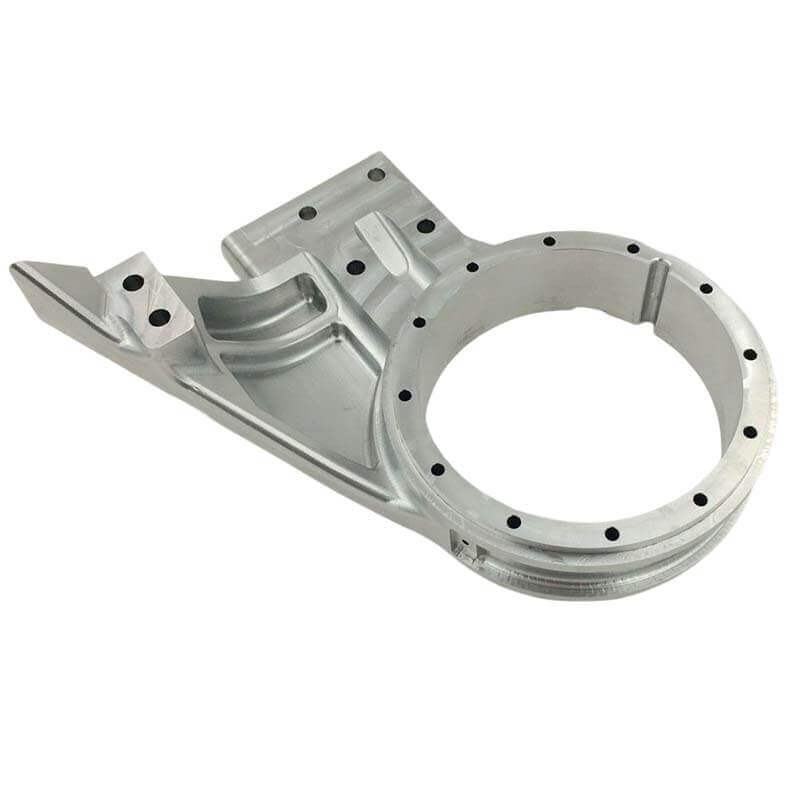
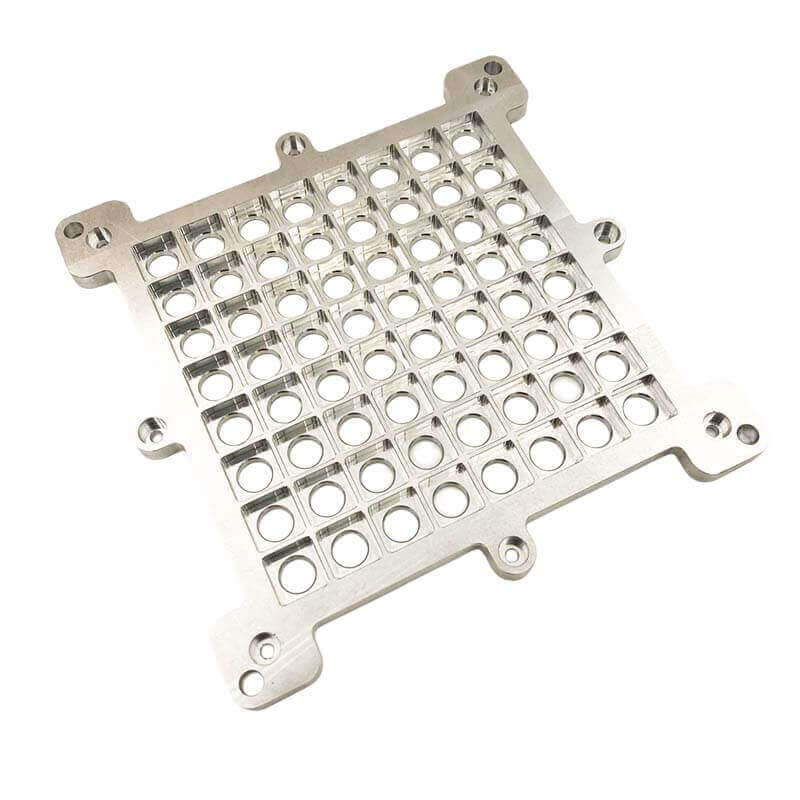
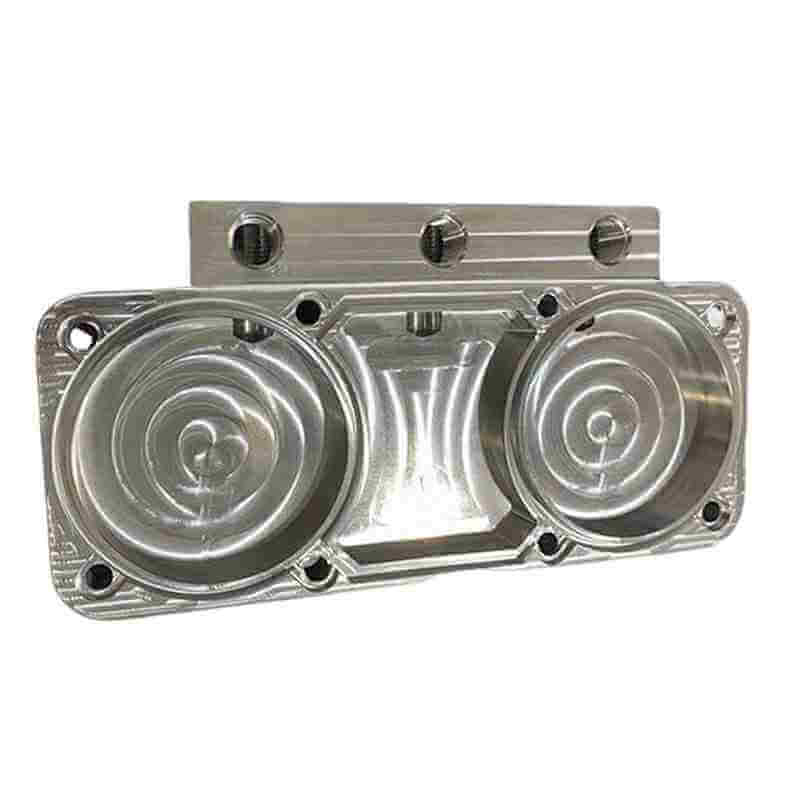
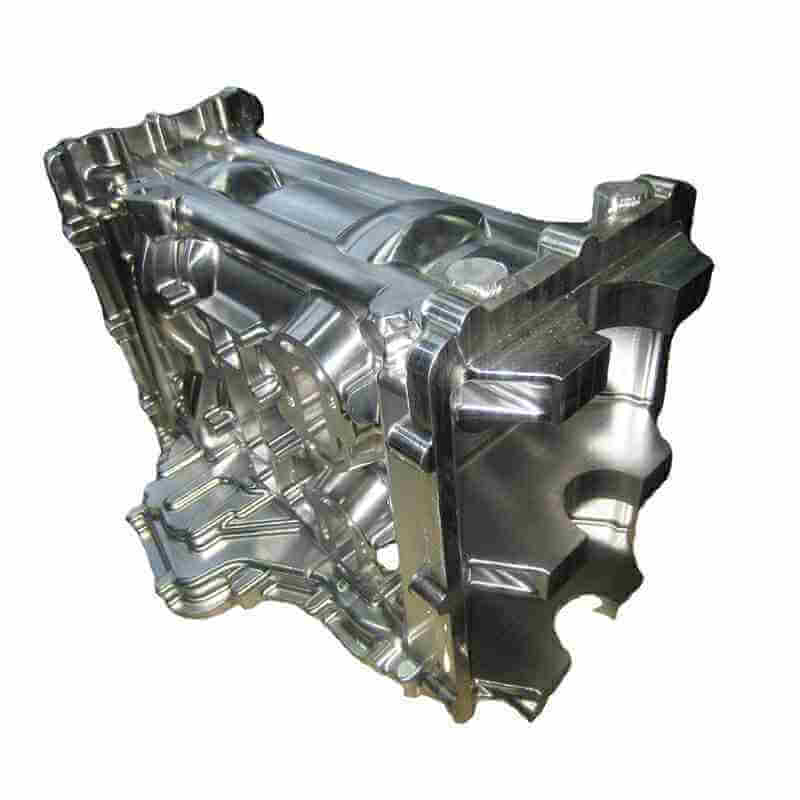
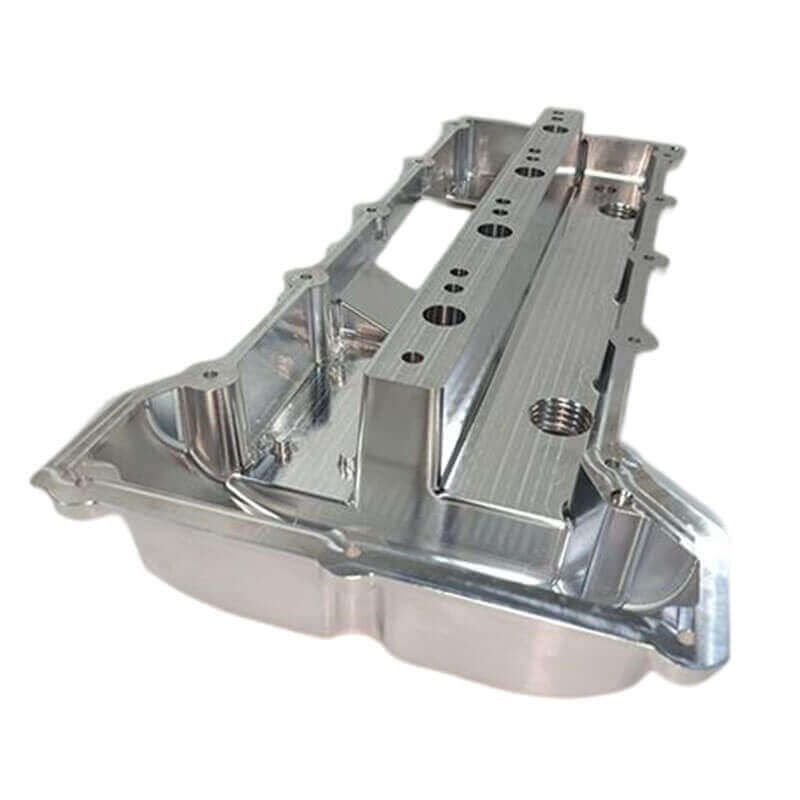
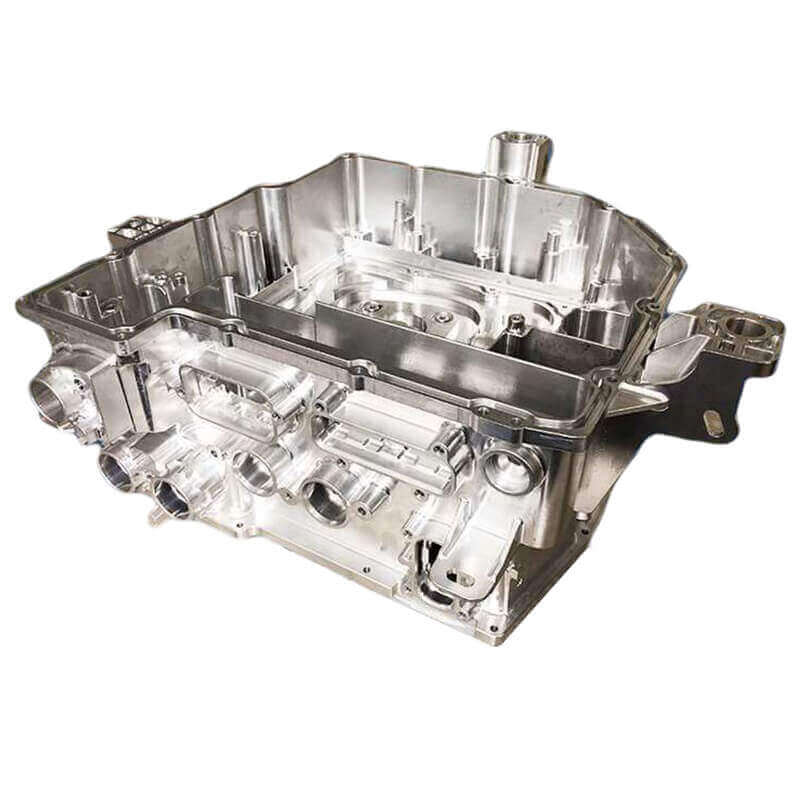
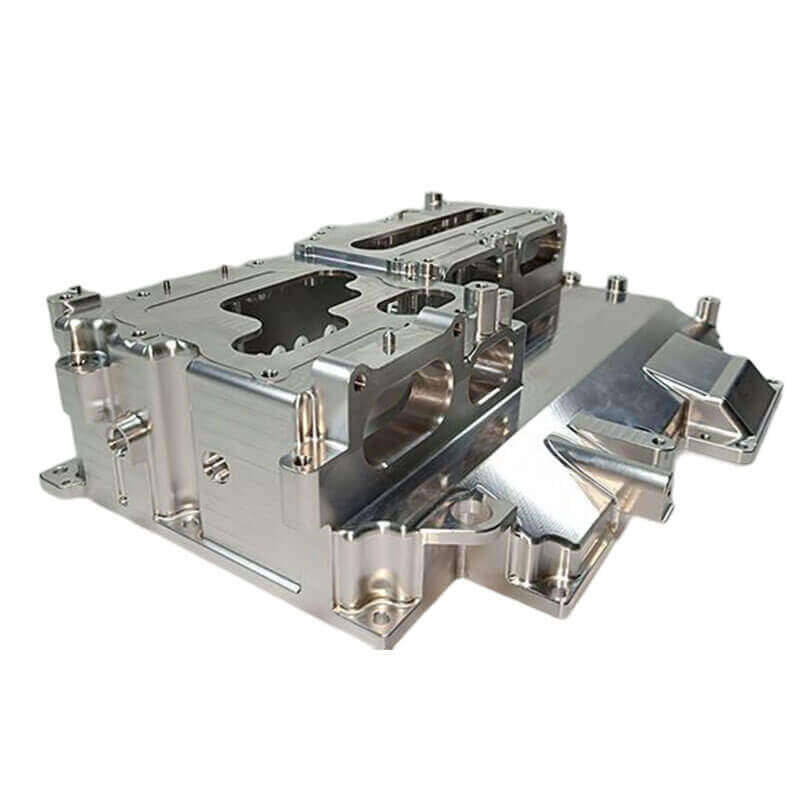
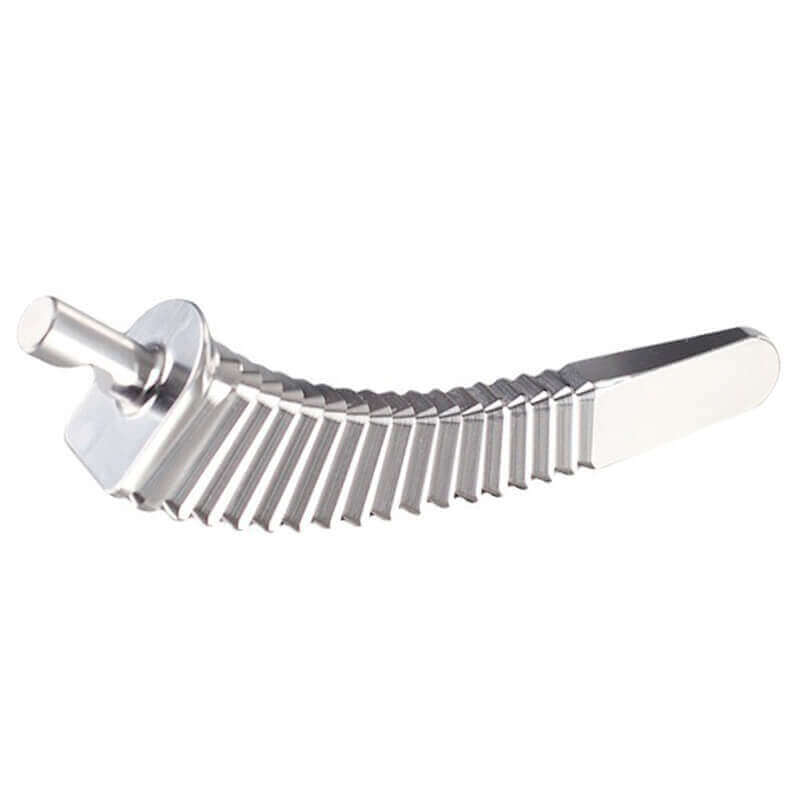
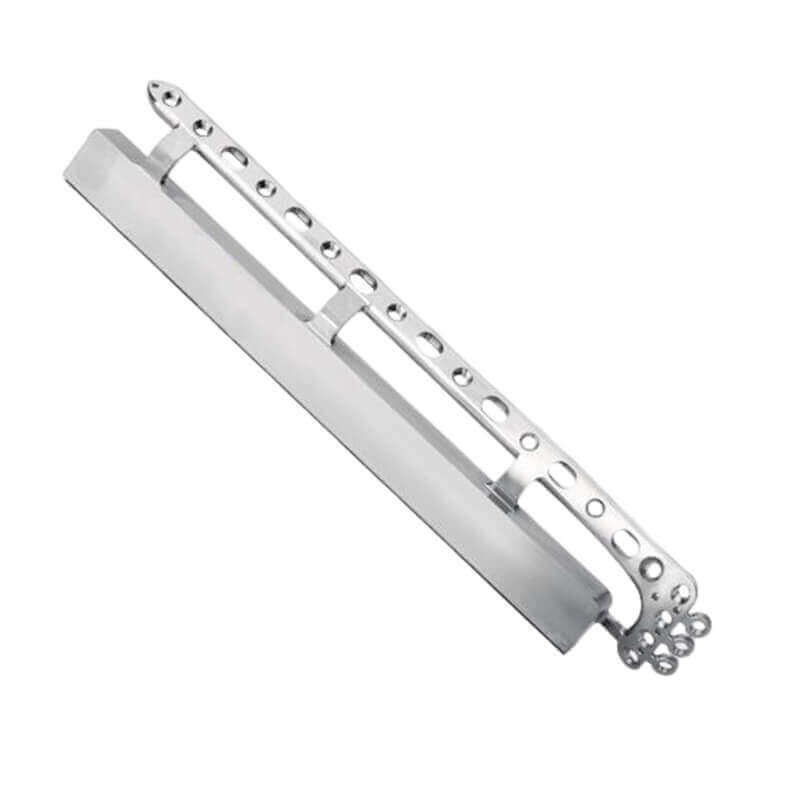
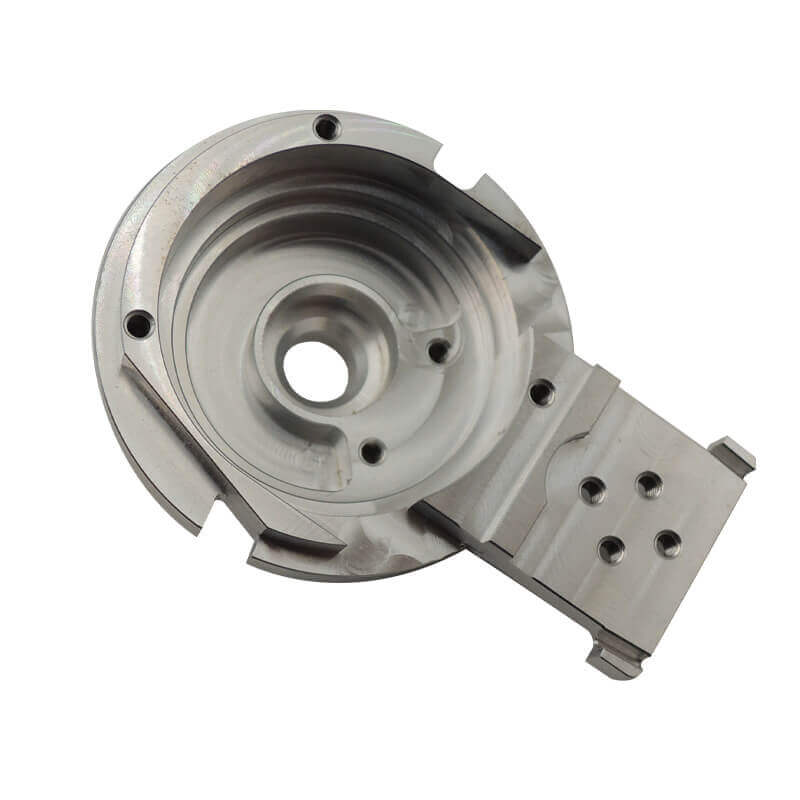
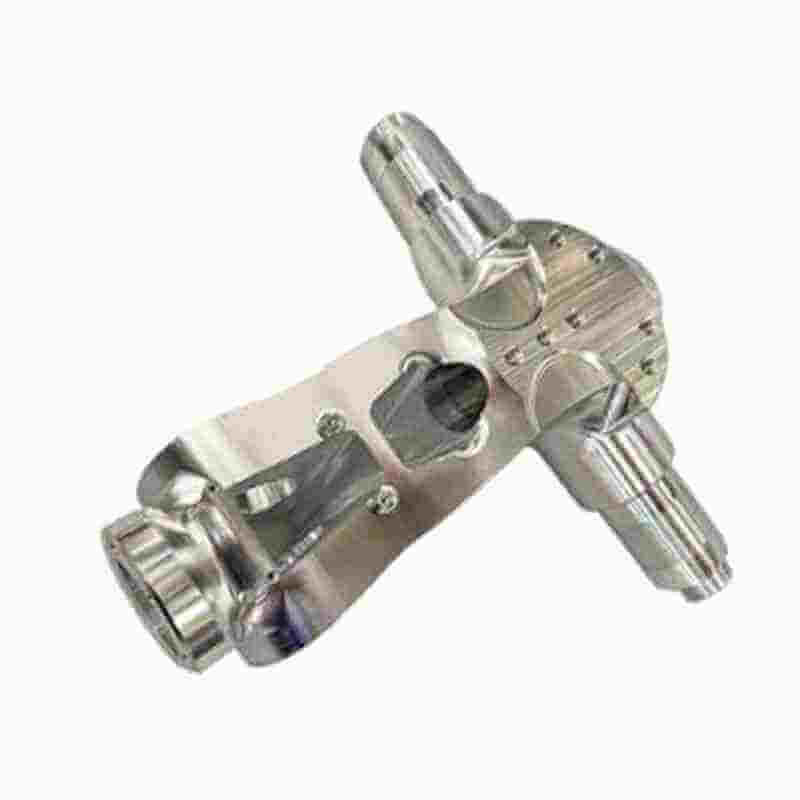
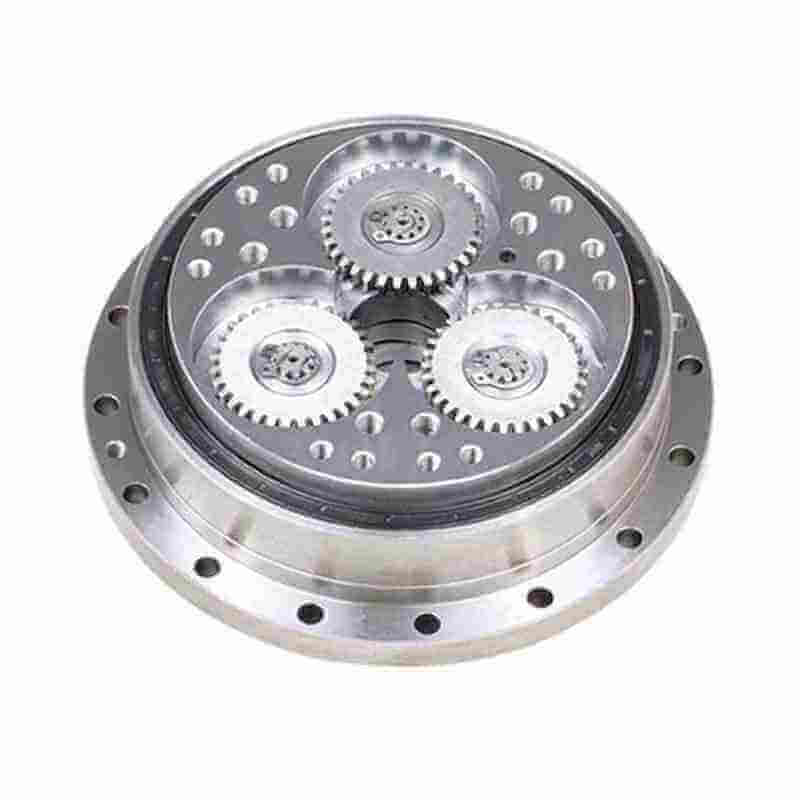
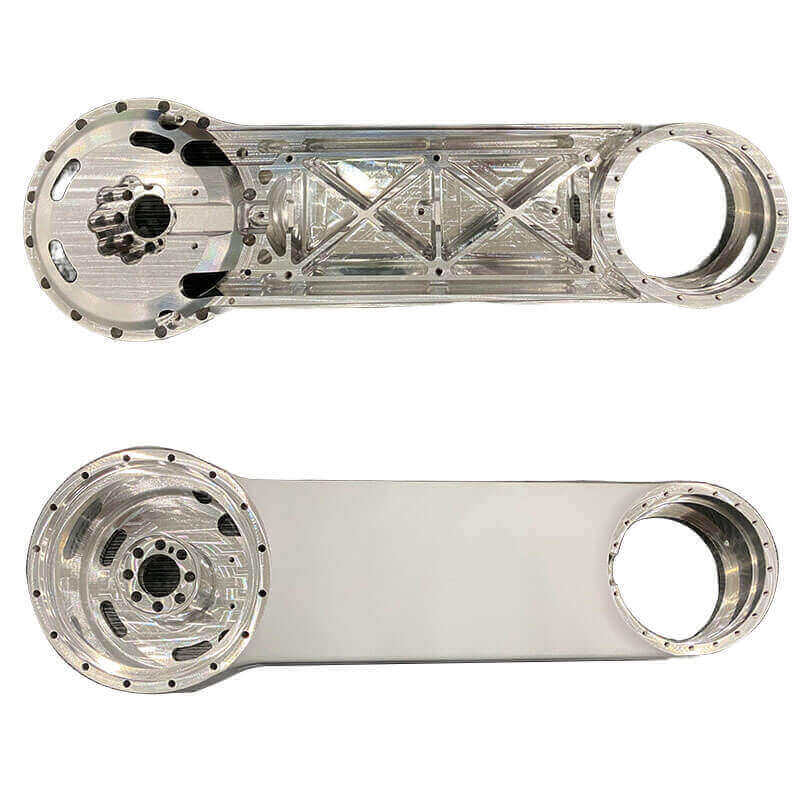
What Sets Us Apart

Strong Experience
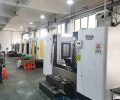
Advanced Machine
30 sets precision CNC 3,4,5 axis machine, with mature and stable manufacturing processes.
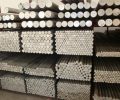
Surprised Price
Stockpiling a large amount of conventional materials and having a mature production process can reduce the overall price by 5%.
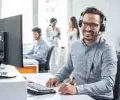
24/7 Engineering Support
Masion offers 24/7 engineering support, design services, cost reduction, quality assurance, and smooth product transitions.
5 axis Manufacturing Process
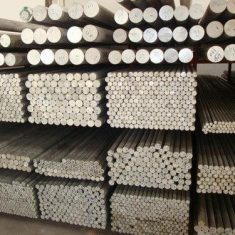
Raw Material
Forging
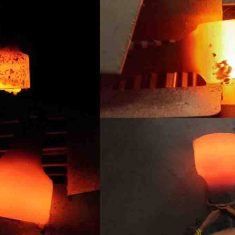
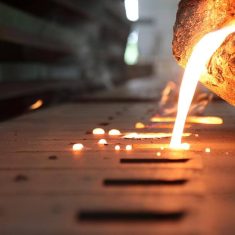
Casting
CNC 5 axis Machining
- Milling
- Turning
- Drilling
- Threading
- Cutting
- Counter Sinking
- Boring
- Knurling
- Grooving
- Taper
- Turning
- Tapping
- Reaming
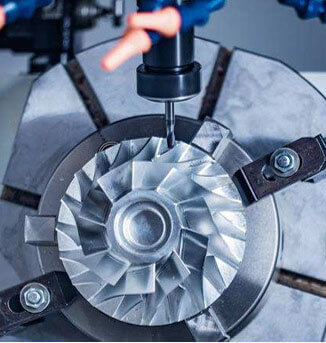
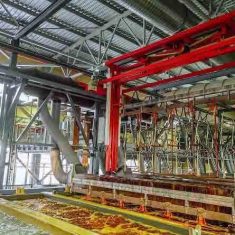
Surface Finish
Packing
- For products with general packaging requirements, we will use cardboard to separate, and then use cartons to pack,
- For products with very high packaging requirements, we will package the products individually, using ziplock bags, or foam bags, or pearl cotton bags, and then separate with cardboard, and finally use carton packaging.
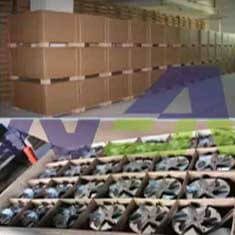
- For some very large products, we generally use wooden cases, first pack the products, and then use wooden cases to pack. Prevent product damage.
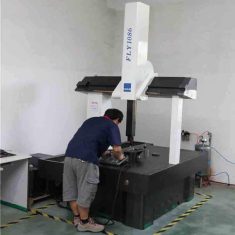
Quality Control (Testing)
- Masion conduct material inspections to ensure their correctness.
- Masion perform initial inspections on the first samples; production proceeds only if the dimensional inspection is passed, with adjustments made if necessary for non-compliance.
- Masion conduct sample inspections on the manufactured products to ensure compliance with the dimensional requirements specified in the drawings.
Application Area
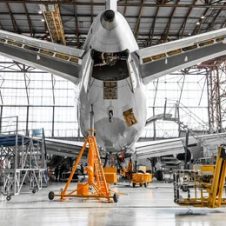
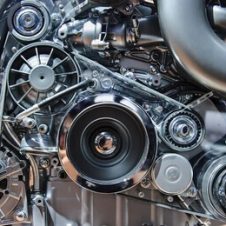
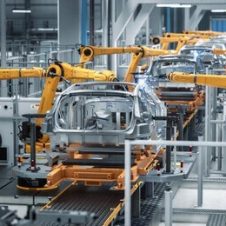
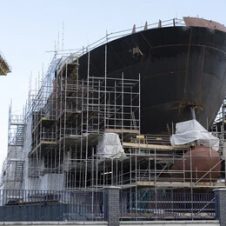
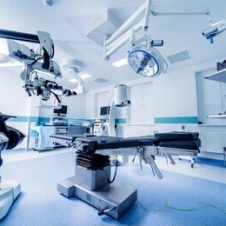

5 axis CNC Machining FAQs
Generally, there are two types of five-axis machining centers: 3+2 and simultaneous five-axis. A 3+2 five-axis machining center consists of three linear axes (X, Y, Z) and two rotational axes (A, B). On the other hand, simultaneous five-axis refers to the capability of all five axes (X, Y, Z, A, B) to move simultaneously in a coordinated manner.
3+2 machining primarily relies on the rotation of two axes on the worktable, allowing the tool to perform multi-sided machining along the rotating surfaces of the product.
Five-axis machining centers are equipped with two additional rotational axes, allowing the worktable to rotate simultaneously. As a result, both the tool and the worktable can rotate at the same time, enabling the machining of different surfaces of complex workpieces.
It also utilizes computer-controlled tool movements along five different axes, enabling extremely precise cutting and machining in three-dimensional space.
Typically, the applications of five-axis machining include components such asimplantable medical devices, surgical robots, surgical instruments, turbocharger impeller machining, secondary impeller machining, 7-stage impeller machining for turbo molecular pumps, high-pressure water pump impeller machining, air compressor impeller machining, blower impeller machining and diesel engine crankshafts.
Different axes:The tool of the three-axis machining center can move along three directions, which is what we call the three axes (X,Y,Z).This means that the workpiece often needs to be repositioned and re-clamped multiple times to complete complex machining processes. Four-axis machining adds an additional rotational axis (usually A or B axis) to provide an additional cutting direction, reducing the need for re-clamping. However, there are still geometric limitations that cannot be fully addressed. The “3+2” design of a five-axis machining center typically involves adding an additional rotational axis (usually called the C-axis) to the three-axis setup. This design enables simultaneous rotation of the tool and workpiece through the rotational axis, allowing for synchronous machining of complex cuts on different surfaces. As a result, five-axis machining centers can quickly and efficiently cut complex workpieces, minimizing the need for re-clamping and repositioning. This design significantly improves both the efficiency and precision of the machining process. Compared to three-axis and four-axis machining centers, five-axis machining centers have superior capabilities in processing complex geometries and intricate surfaces, resulting in a several-fold increase in processing efficiency.
Different machine prices: Three-axis machining centers are the most commonly used and generally satisfy simple milling operations, so the equipment prices are relatively lower, typically around 29000usd to 36000usd. Four-axis machining centers, with an added rotational axis to the three axes, incur additional costs ranging from 7500usd to 15000usd. Five-axis machining centers have higher prices, generally ranging from 75000usd to 230000usd.
Machining characteristics: In three-axis machining, the tool direction remains constant throughout the cutting path. The cutting condition of the tool tip cannot be perfectly optimized in real-time. During five-axis machining, we can consider improving the cutting direction of the tool to ensure the optimal path of tool movement throughout the entire machining process. Additionally, in five-axis machining of workpieces, the tool can maintain a simultaneous linear movement direction, resulting in the best cutting performance. Compared to four-axis machining, where an additional rotational axis is added to a three-axis machining center, the rotational axis is limited to a 360° rotation in the horizontal plane and cannot achieve high-speed rotation.
This characteristic is suitable for machining some box-type parts.
Different machining costs: The average cost for three-axis machining is generally around 9-10usd per hour, four-axis machining is around 15-25usd per hour, and five-axis machining costs around 60-75usd per hour. It can be seen that the investment and output of five-axis machining equipment are proportional, and the machining difficulty is high, typically requiring experienced and skilled technicians to operate.
With the continuous development and advancement of technology and the manufacturing industry, the widespread application of high-end complex products has driven the development of 5-axis machining technology. The demand for complex components with high precision and intricate surfaces has made 5-axis machining centers the preferred choice for customers. Of course, customers also consider the machining cost of 5-axis machining centers as a necessary factor to consider.
The pricing for five-axis machining centers can vary among suppliers and is typically determined by several factors. Here are some common cost factors:
Material cost: The type and quality of materials used in five-axis machining centers will impact the cost. High-performance metals and advanced composite materials can result in higher costs, and material selection depends on the customer’s design requirements, with different materials varying in performance and price.
Equipment and energy cost: The usage of equipment and energy, as well as the electricity rate from the power supplier, will determine the hardware cost of the five-axis machining center. Some suppliers may charge additional equipment usage fees based on the size and complexity of the workpiece.
Difficulty and cycle of machining: The difficulty and cycle time of the five-axis machining center are key factors influencing the cost. More complex workpieces require more machining steps and time, which can increase the cost. Therefore, cost-effectiveness should be considered during the design phase.
Software and labor cost: The software licensing and labor operation of the five-axis machining center are also cost factors. Some suppliers may charge labor operation fees based on the quantity of workpieces or the complexity of the process.
Quantity of workpieces: Typically, the machining cost for small batch production is higher compared to large batch production since suppliers prefer larger orders to optimize time and resources. However, Masion welcomes small batch orders and provides corresponding discounts.
In addition to the above factors, there may be additional costs related to special packaging, transportation, or other requirements based on customer requests.
The pricing structure for five-axis machining centers is a complex issue. Different suppliers of five-axis machining may have different pricing structures, and customers should choose the appropriate five-axis machining supplier based on their specific needs. Prior to selecting a five-axis machining supplier, customers should consider factors such as the technical expertise of their engineers, service quality, and reputation to ensure they receive the best value.
Regarding specific five-axis machining costs, prices in the market are typically around 50usd per hour. For a workpiece with dimensions of 1000×1000, the price may be around 80usd per hour. Masion provides five-axis machining services and offers reasonable quotes based on your workpiece, with competitive pricing and high quality assurance.
5-axis machining centers have diverse functionalities and powerful processing capabilities, enabling them to process various different materials. These machines offer enhanced flexibility and precision compared to traditional 3-axis machines. Here are some common types of materials that can be machined using 5-axis CNC machines:
Metals: 5-axis CNC machines are widely used for machining various types of metals, including aluminum, steel, stainless steel, brass, copper, titanium, and alloys etc. They are capable of producing complex shapes, intricate patterns, and precise details on metal parts.
Plastics: Different types of plastics, such as ABS, acrylic, polycarbonate, nylon, polypropylene, and PVC, can be machined using 5-axis CNC machines. These machines can create intricate designs and smooth finishes on plastic components.
Composites: 5-axis CNC machines are suitable for machining composite materials, which are combinations of different materials like carbon fibers, fiberglass, Kevlar, or other reinforcing fibers embedded in a matrix material. They are commonly used in aerospace, automotive, and marine industries.
Wood: CNC machines are widely used in woodworking, and 5-axis CNC machines can handle complex wood machining tasks. They can carve intricate designs, create curved surfaces, and produce high-quality wooden furniture, decorative items, and architectural components.
Foam: 5-axis CNC machines are used for machining foam materials, such as expanded polystyrene (EPS) and polyurethane (PU) foam. They are commonly employed in the production of molds, prototypes, architectural models, and packaging inserts.
The accuracy of five-axis machining centers varies among different brands. Generally, German brands have the highest precision, followed by brands from Japan and the United States. For example, the repeatability of positioning accuracy of the five-axis machining center used by Masion can reach 0.001 millimeters, while the machining accuracy is within the range of ±0.01 millimeters. (0.0004 inch) Such precision levels typically meet the tolerance requirements for most complex workpieces.
Maximum workpiece size: 2600×700 mm
Maximum travel: 2000x610x630 mm
A-axis swing angle: 360°
Maximum swing angle of B-axis: ±100°
Maximum workpiece weight: 1000 kg
Positioning accuracy: <6μm
Repeatability: <4μm
Maximum center coolant pressure: 150 Pa
Maximum spindle speed: 20000 rpm
Five-axis linkage: X, Y, Z, A, B.
We usually understand the time that affects the production of five-axis machining from the following factors.
Complexity of the part design: If a customer’s product design is highly complex with multiple surfaces and holes to be machined, it will take more time to produce the product.
Choice of material grade: Generally, aluminum is easier to machine compared to other metal materials, resulting in relatively shorter processing time. However, if the material to be machined using five-axis technology is a harder material like stainless steel, titanium alloy, etc., the machining time will be longer, and the tools may be more prone to wear and damage.
Surface finish requirements: Five-axis machining typically involves rough machining and finishing stages. For parts requiring extremely smooth surface finishes, an additional process step may be needed. If only general surface finish requirements are necessary, the machining time will be relatively shorter.
Surface treatment requirements: Some customers may require post-machining surface treatments such as oxidation, plating, etc. This will increase production time, and there is a possibility of product damage during intermediate processes, leading to higher scrap rates.
Production scheduling: If it is a reorder of existing products, the speed will be faster, usually around 3-4 days. However, as material procurement, CNC machining, and other processes all require time, any delays in these stages can affect the overall production schedule.
Quantity considerations: For some precision parts requiring five-axis machining, if the order quantity does not meet the minimum requirements, additional processes such as wire cutting or laser cutting may be needed, which will consume more time and effort. This is especially true for customized high-precision precision components with small volumes and an imperfect supply chain, making it prone to supplier delivery delays.
After sample development, when moving to mass production of precision components, there may be process factors that are not conducive to large-scale production. For example, there may be no issues during CNC machining, but in mass production, it is found that some precision parts are not easily oxidized, requiring fixture treatments, etc.
Unexpected events involving skilled personnel in precision part manufacturing facilities. If there is a situation where there are no qualified substitute personnel, it will lead to a decrease in production capacity, especially for processes with a high level of technical dependence, which may result in delivery delays.
Other uncontrollable factors such as power outages, equipment failures, and other unforeseen circumstances. Companies should have contingency plans in place to deal with such situations to avoid being at a loss.
Overall, taking into account the above factors, the typical production time for sample five-axis machining at Masion is around 5-10 days, for small orders it is generally 10-15 days, and for large orders it is usually 30-35 days.
Yes, you mentioned the advantages of 5-axis CNC machines. They are highly useful in mold machining and prototype design, especially in the early stages of complex workpieces that require validation. By using 5-axis machining centers, validation time can be reduced, market acceptance can be improved, and faster product development cycles can be achieved.
These machines offer great flexibility and can produce complex prototypes as well as batch or high-volume products. In general, a 5-axis machining center is often the optimal choice for machining workpieces. It can handle complex components with diverse shapes and surfaces, while ensuring high precision and superior quality of the workpieces. As a result, 5-axis machining is widely applied and considered the best solution in many industrial manufacturing sectors.
By using 5-axis CNC machines, the need to transfer workpieces between different machines is reduced, thereby minimizing the risk of human error. Additionally, these machines often have high-speed cutting capabilities, which can enhance production efficiency and reduce machining time.
In conclusion, the versatility, flexibility, and high precision of 5-axis CNC machines make them indispensable tools in mold machining and prototype design. They can accelerate the product development process, improve product quality, and provide a competitive advantage for businesses in batch production of complex work pieces.
When choosing a qualified 5-axis machining center supplier, you should pay attention to the following details:
Determine if the supplier has its own 5-axis machining center rather than relying on outsourcing. You can directly inquire with the supplier or visit their machining facility to ensure they can perform 5-axis machining tasks directly.
Confirm if the supplier has experience in machining complex components. You can request the supplier to showcase photos or samples of previously machined complex parts to verify their experience and capabilities.
Verify if the supplier has a design team and can provide design support for the components. Correct design is crucial for machining complex parts, and discussing and optimizing the design with the supplier can ensure a smooth machining process.
Evaluate the professionalism of the supplier’s communication personnel. For machining complex parts, strict requirements regarding dimensions, tolerances, surface roughness, etc., exist. The supplier’s communication personnel need to possess professional knowledge, effectively communicate with the customer, understand and fulfill their requirements, and minimize time costs.
Compare the machining prices offered by different suppliers. Machining complex components typically incurs higher costs, and there may be variations in the quotations provided by different suppliers. Customers can choose a suitable price based on their own situation and ensure that the pricing from the selected supplier is reasonable.
Confirm if the supplier has samples or case studies of complex components available for reference to evaluate their machining quality and capabilities.
Verify if the supplier has a strict quality management system in place to ensure the quality of complex components.
Confirm if the supplier is equipped with high-quality inspection equipment such as coordinate measuring machines, project meters, surface roughness testers, etc., and understand their inspection procedures and standards.
Considering these factors comprehensively, choosing a reliable 5-axis CNC machining service provider can ensure high-quality machining results and a smooth production process.
Five-axis machining of stainless steel parts can significantly improve machining accuracy and quality. Compared to traditional four-axis machining, five-axis machining allows for control of the tool in multiple directions, ensuring better dimensional accuracy and geometric tolerances in the machined areas. This superiority is particularly evident in the machining of complex parts. Five-axis machining of stainless steel parts is a high-precision machining method, and the common problems and solutions are as follows:
Tool Wear in Five-Axis Machining of Stainless Steel Parts
Tool wear is a common problem in five-axis machining of stainless steel parts. Solutions include using high-performance tool materials and coatings to enhance tool wear resistance and lifespan. Selecting cutting parameters reasonably to avoid excessive cutting and wear. Regularly inspecting and replacing tools to maintain sharpness and precision. Implementing cooling and lubrication measures to reduce tool wear and heat accumulation.
Workpiece Deformation in Five-Axis Machining of Stainless Steel Parts
Workpiece deformation is another common issue in five-axis machining of stainless steel parts. Solutions include planning machining sequences reasonably to avoid excessive cutting and heat accumulation. Implementing cooling and lubrication measures to reduce cutting forces and heat accumulation. Using methods such as segmented machining and symmetrical machining to balance workpiece stress. Improving workpiece hardness and stability through heat treatment and stress relief measures.
Measurement Errors in Five-Axis Machining of Stainless Steel Parts
Measurement errors are also common in five-axis machining of stainless steel parts. Solutions include using high-precision measuring instruments and equipment to ensure measurement accuracy. Regularly inspecting and calibrating measuring instruments and equipment to avoid error accumulation. Employing methods such as comparative measurement and statistical analysis to identify and address measurement errors. Enhancing the skills and qualifications of measurement personnel to ensure measurement quality and accuracy.
Equipment Failures in Five-Axis Machining of Stainless Steel Parts
Equipment failures are common issues in five-axis machining of stainless steel parts. Solutions include regularly inspecting and maintaining equipment to ensure it is in good condition. Strengthening training and management of equipment operators to avoid errors and accidents. Establishing an equipment maintenance and upkeep system, regularly replacing vulnerable parts, and repairing equipment. Using backup equipment and operating modes to minimize the impact of equipment failures on production.
Common problems in five-axis machining of stainless steel parts include tool wear, workpiece deformation, measurement errors, and equipment failures. Solutions include using high-performance tool materials and coatings, selecting cutting parameters reasonably, implementing cooling and lubrication measures, regularly inspecting and replacing tools, planning machining sequences reasonably, using high-precision measuring instruments and equipment, regularly inspecting and calibrating measuring instruments and equipment, improving the skills and qualifications of measurement personnel, regularly inspecting and maintaining equipment, strengthening training and management of equipment operators, establishing an equipment maintenance and upkeep system, and using backup equipment and operating modes. By implementing these measures, the efficiency and precision of five-axis machining of stainless steel parts can be improved, production costs can be reduced, and product quality can be enhanced.
Five-axis machining technology in the production of sports equipment parts excels in processing efficiency, precision, consistency, and stability compared to conventional CNC machine tools. It is a modern and advanced mechanical machining technology widely applied in the manufacturing of sports equipment components. However, in practical applications, five-axis machining may encounter some common problems. The following are common problems and solutions in five-axis machining of sports equipment:
Short Tool Life in Five-Axis Machining of Sports Equipment
Short tool life is a common issue in five-axis machining. The main reason is that during the five-axis machining process, the tool needs to withstand more force and pressure, leading to faster tool wear.
Solutions:
- Optimize cutting parameters by adjusting feed rates, cutting speeds, cutting depths, etc., according to different materials and part characteristics to reduce tool loads and extend tool life.
- Choose high-quality, high-hardness tools to enhance tool wear resistance and heat resistance, improving cutting efficiency.
Poor Surface Quality of Sports Equipment Components in Five-Axis Machining
Five-axis machining can easily result in surface defects such as tool marks and burrs, affecting the appearance and quality of components.
Solutions:
- Use high-quality tools and cutting fluids to minimize the marks left on the surface during cutting.
- For critical components, perform subsequent polishing or other coating processes to improve the surface quality and appearance of the components.
Insufficient Operator Skill Level
Five-axis machining technology requires a higher skill level from operators. Therefore, inadequate operator skills can easily lead to poor machining of components.
Solutions:
- Establish a comprehensive training system, strengthen operator training, and improve the skills and capabilities of operators.
- Enhance equipment management to ensure that the equipment is in optimal condition, avoiding the impact of machine failures on machining quality.
Five-axis machining technology for sports equipment is a relatively stable modern machining technology. However, it still faces various challenges in practical applications. Only by strengthening technical research, skill training, and establishing scientifically reasonable machining processes and management systems can we better address these issues and enhance production efficiency and product quality.
In today’s manufacturing industry, Five-Axis CNC machining is widely utilized for its efficiency, high precision, and flexibility. This article will explore how to control the precision of Five-Axis CNC machining and ensure machining quality.
Factors Affecting Precision in Five-Axis CNC Machining
Equipment Precision: The accuracy of Five-Axis CNC equipment directly influences the precision of machined parts. Mechanical accuracy, electrical accuracy, and software algorithms of the equipment all impact the machining results.
Workpiece Clamping: The clamping method and position of the workpiece have a significant impact on machining precision. Incorrect clamping may lead to issues such as vibration and deformation during the machining process, affecting precision.
Tool Wear: The degree of tool wear has a considerable impact on machining precision. Tool wear can cause changes in cutting forces, affecting the surface roughness and dimensional accuracy of the cut.
Programming Errors: Programming errors include calculation errors and interpolation errors. Calculation errors result from limitations in the mathematical model and rounding errors, while interpolation errors occur in curve or surface machining due to improper interpolation methods or parameter selection.
Methods for Precision Control in Five-Axis CNC Machining
Select High-Precision Equipment: When choosing Five-Axis CNC equipment, prioritize devices with high precision and stability. Such equipment can better ensure machining accuracy.
Optimize Clamping Solutions: Design rational clamping solutions based on the shape and size of the workpiece. Ensure stability during the machining process, reducing vibration and deformation.
Choose Tools Wisely: Select appropriate tool materials and models based on machining requirements. Also, ensure the sharpness and durability of the tools to minimize the impact of tool wear on machining precision.
Accurate Programming: Use advanced programming software and conduct thorough validation and test cuts. Ensure programming errors are within an acceptable range to enhance machining precision.
Temperature Control: Changes in temperature can affect equipment precision. By controlling the environmental temperature and equipment cooling system, maintaining the equipment at an optimal working temperature helps improve machining precision.
Quality Assurance Measures in Five-Axis CNC Machining
Strictly Control Raw Material Quality: Ensure that raw materials meet machining requirements, reducing errors caused by material issues.
Enhance Process Monitoring: Implement real-time monitoring during the machining process to promptly identify and address potential quality issues.
With the rapid advancement of technology, Drone(UAV)s have become an indispensable part of modern society. Whether in aerial photography, agriculture, rescue operations, or other fields, the applications of Drone(UAV)s are becoming increasingly widespread. In the manufacturing of Drone(UAV)s, five-axis machining technology has emerged as a crucial processing method, playing a key role, particularly in the production of Drone(UAV) components. This article will delve into the application and practical aspects of five-axis machining for Drone(UAV) components in the field of Drone(UAV) manufacturing.
Five-axis machining technology is an advanced CNC processing technique that allows for the machining of multiple surfaces in a single setup. Compared to traditional three-axis machining, five-axis machining technology offers higher efficiency and precision. The primary advantage of five-axis machining lies in reducing the number of setups, thereby improving processing efficiency and preventing errors caused by multiple setups, further enhancing machining precision.
In the field of Drone(UAV) manufacturing, five-axis machining technology finds widespread applications in the following areas:
Drone(UAV) Body Machining: Drone(UAV) bodies are typically made of lightweight materials such as aluminum alloy or carbon fiber. Five-axis machining technology can efficiently handle the machining of multiple surfaces of the Drone(UAV) body, improving precision and overall quality.
Machining Drone(UAV) Components: Drone(UAV) components encompass a diverse range, including wings, landing gear, engines, and more. These components often require high precision and efficiency in machining. Five-axis machining technology can meet these requirements, achieving efficient and high-precision machining.
Drone(UAV) Mold Machining: The precision and quality of Drone(UAV) molds significantly impact the production process and product quality. Five-axis machining technology can efficiently and precisely machine molds, enhancing mold quality and production efficiency.
A certain Drone(UAV) manufacturing company has adopted five-axis machining technology for producing Drone(UAV) components. Through the use of five-axis machining technology, the company successfully increased processing efficiency and precision, shortened production cycles, and simultaneously reduced manufacturing costs. Additionally, the company utilized five-axis machining technology to produce high-quality Drone(UAV) components, thereby improving the overall performance and reliability of the Drone(UAV)s.
The application and practice of five-axis machining for Drone(UAV) components in the field of Drone(UAV) manufacturing demonstrate that this technology can enhance processing efficiency and precision, reduce production cycles, lower manufacturing costs, and improve the overall performance and reliability of Drone(UAV)s. With the continuous development of technology, there is reason to believe that five-axis machining technology will play an increasingly important role in the future of Drone(UAV) manufacturing.
Free Sample
Explore Other Products
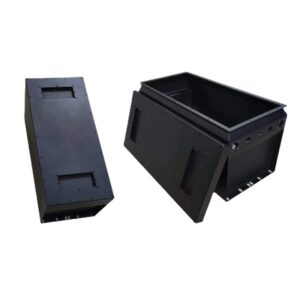
Sheet Metal Fabrication
New Energy Battery Casing and other differentSheet Metal Fabrication parts such as Housing, Case,Enclosure, etc.
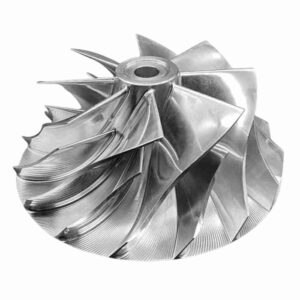
Aluminum Boat Impeller
Five-axis simultaneous complex parts machining, aluminum boat impeller, watercraft impeller, compressor impeller, turbocharger impeller,and another different 5-axis CNC parts etc.
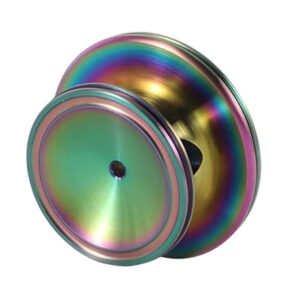
CNC Turning
Stainless Steel stethoscope Chestpiece and another different CNC turning Parts.