Brass Turned Components
Brass Turned Components
Brass Turned Components Manufacturer in China.
MOQ Starts from 1pcs.
As a specialized brass turned components manufacturers,Masion provides high-quality customdifferent brass turned components services to customers with outstanding production advantages, advanced technological capabilities, and professional solution offerings.
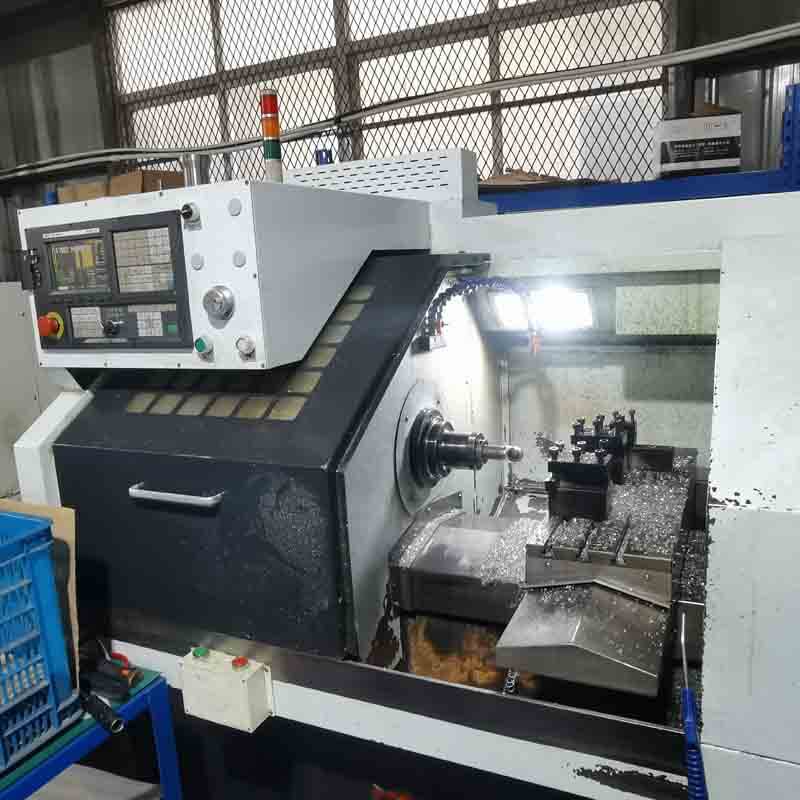
Masion Capability
High Capacity, Proper Price
10000pcs production capacity per month make the price lower.
Free Samples, Low MOQ
1pcs MOQ make you order flexibly with one free sample for you testing.
Certified Factory, Guaranteed Quality
ISO9001:2008 and strictly 100% inspection guarantee quality and CMM inspection equipment.
High precision, thick gold
With 0.002mm tolerance and with different surface finishing and different materials.
Our Products
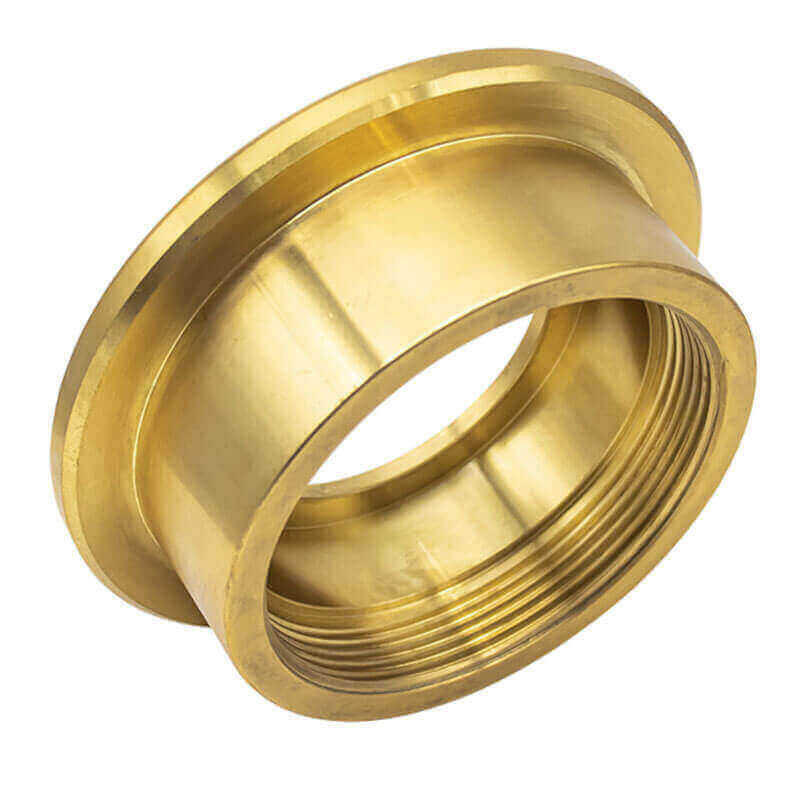
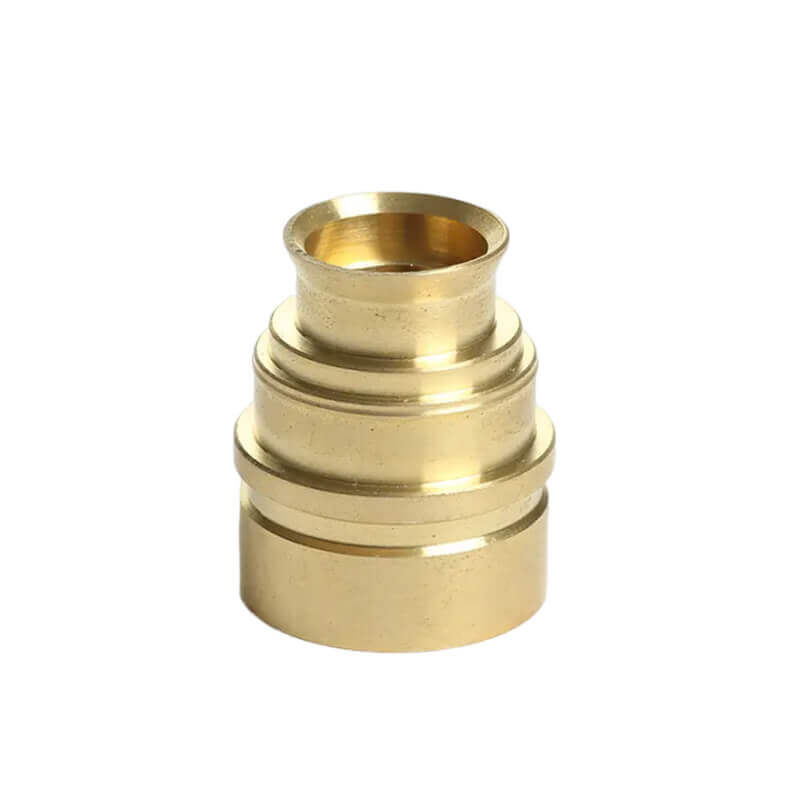
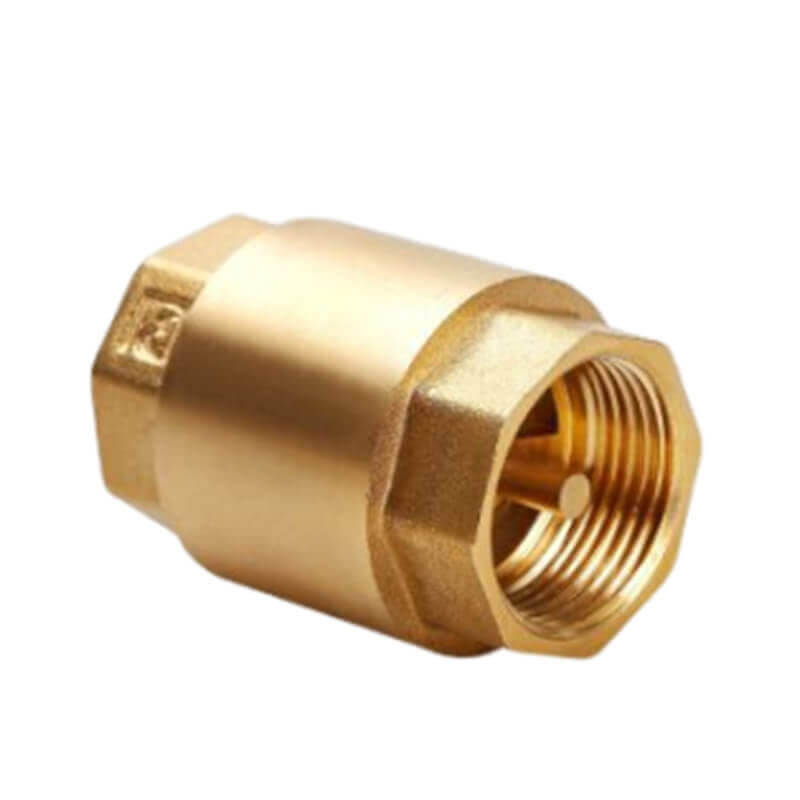

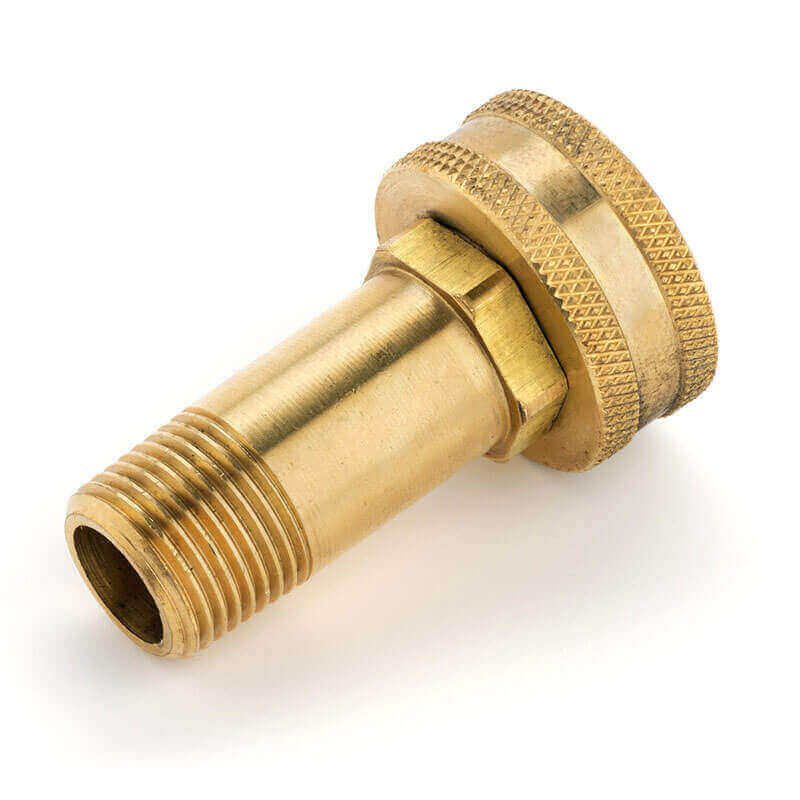
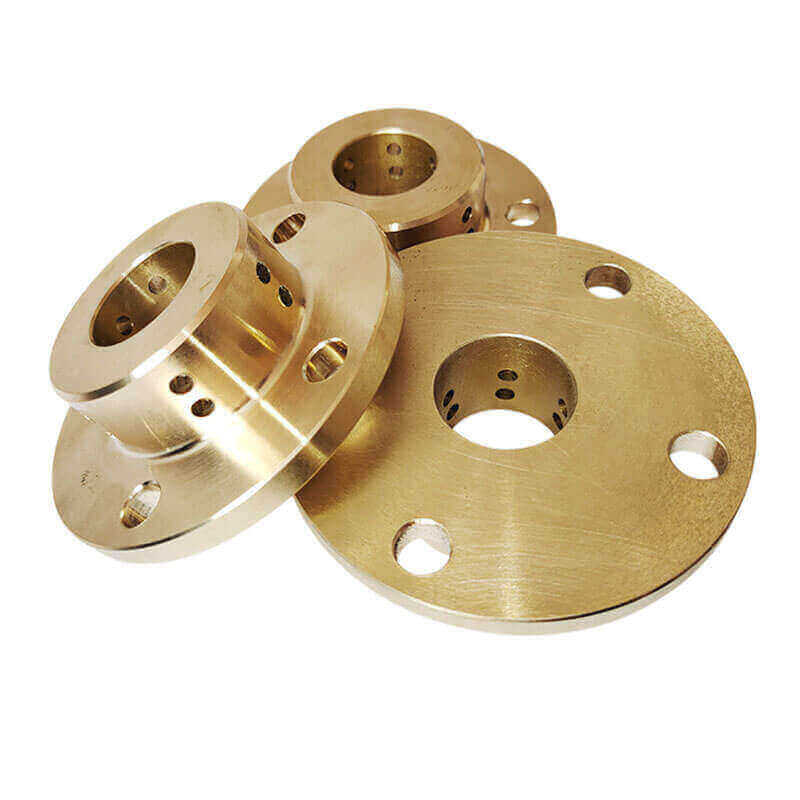
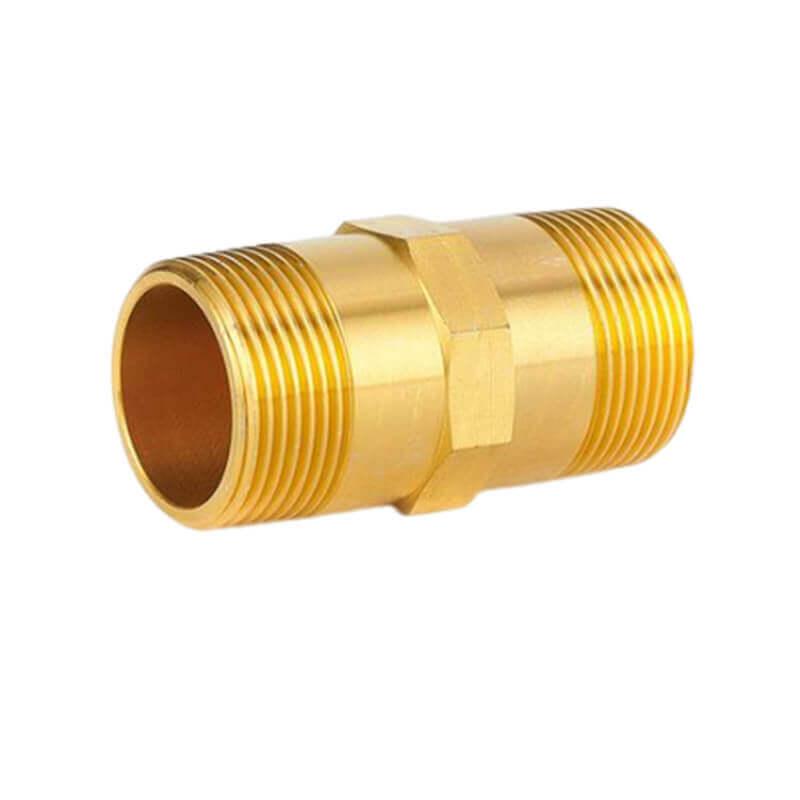


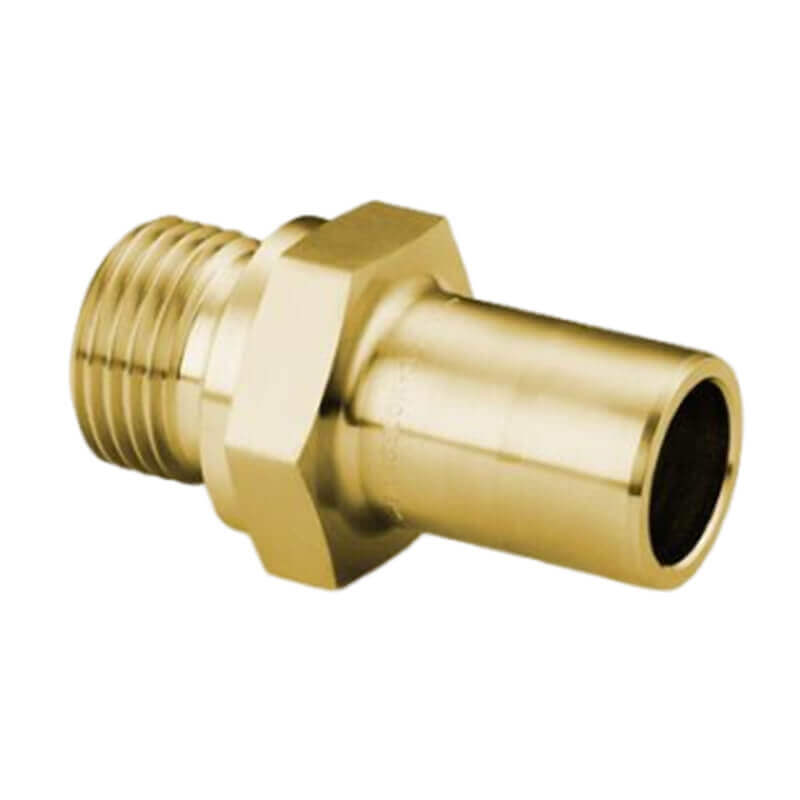
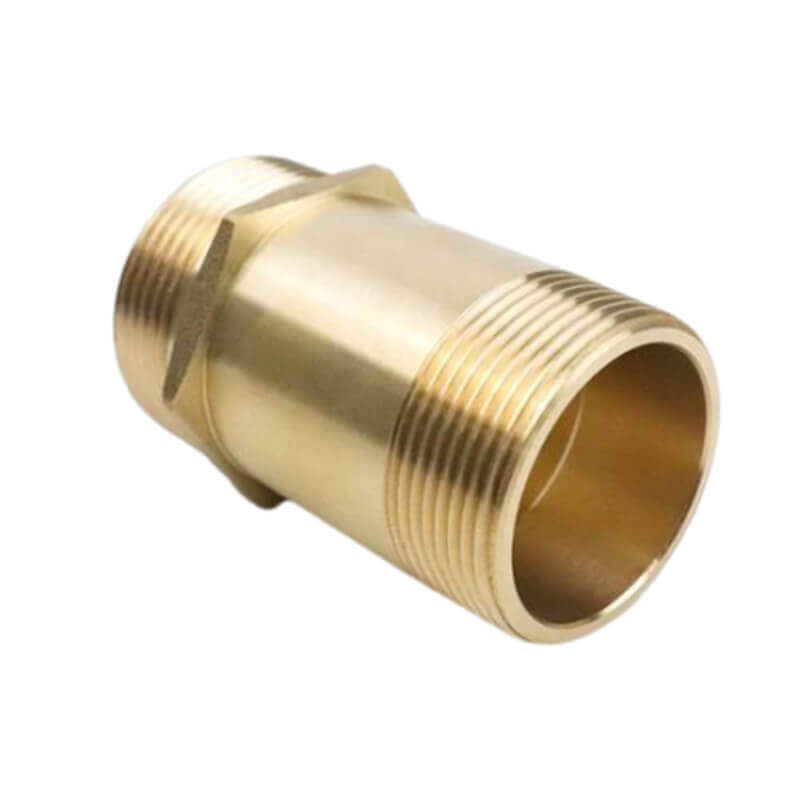
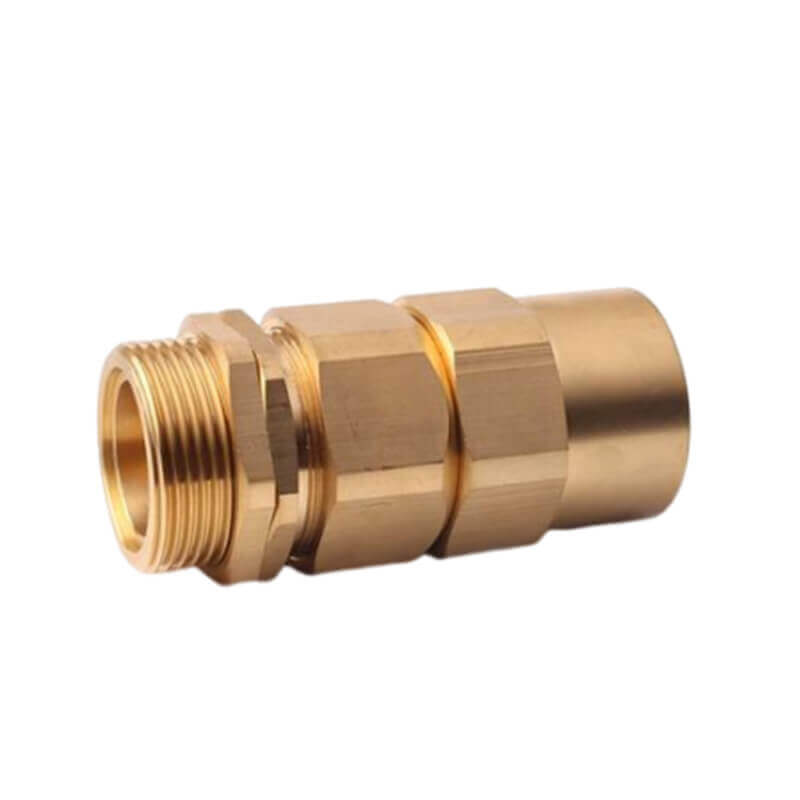
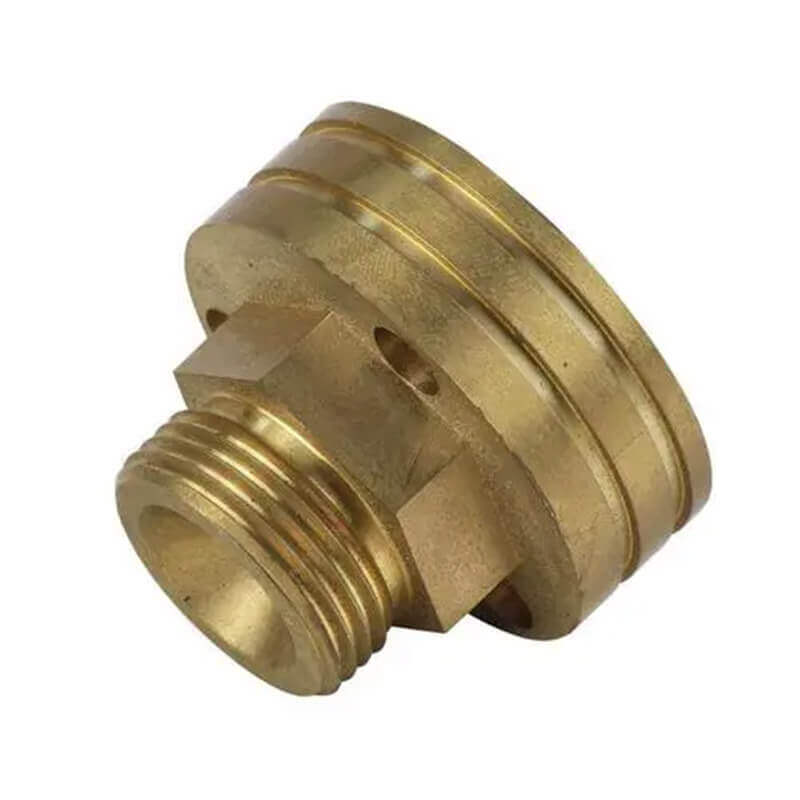
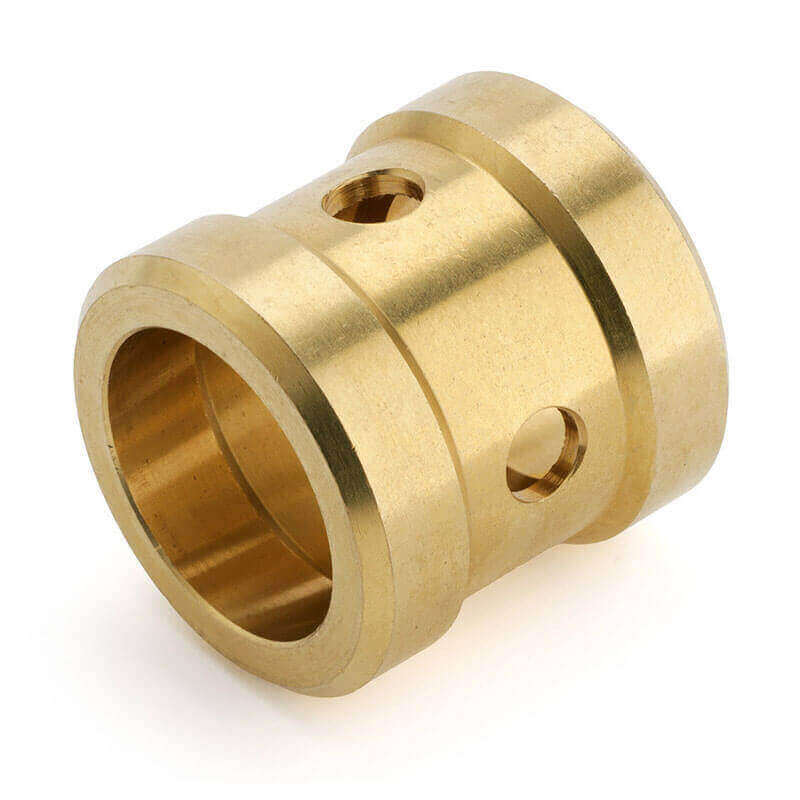
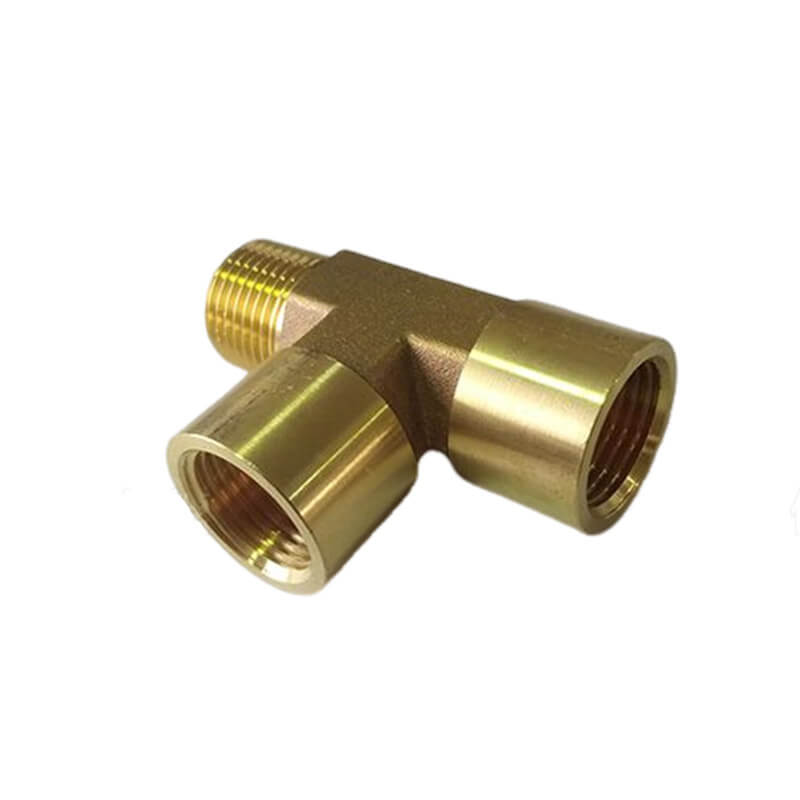
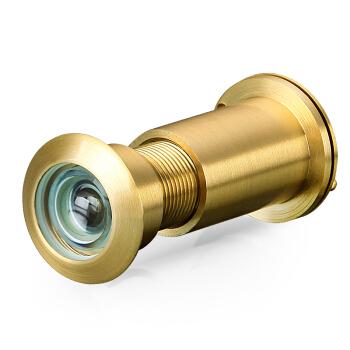
What Sets Us Apart
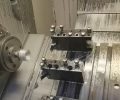
Strong Experience
With 16 years of turning brass parts machining expertise, we focus on high-quality, customized solutions for different turning brass parts demands.
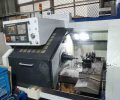
Advanced Machine
30 sets precision imported Japanese Citizen Swiss CNC Lathe with mature and stable manufacturing processes with technical machinist and engineer.

Surprised Price
Stockpiling a large amount of conventional materials and having a mature production process can reduce the overall price by 5%.
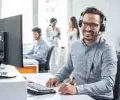
24/7 Engineering Support
Masion is specializing in offering 24/7 engineering support, design services, cost reduction, quality assurance, and smooth product transition sun paralleled excellence etc.
Brass turned components Manufacturing Process

Raw Material
Brass turned components Machining
- Milling
- Turning
- Drilling
- Threading
- Cutting
- Counter Sinking
- Boring
- Knurling
- Grooving
- Taper
- Tapping
- Reaming
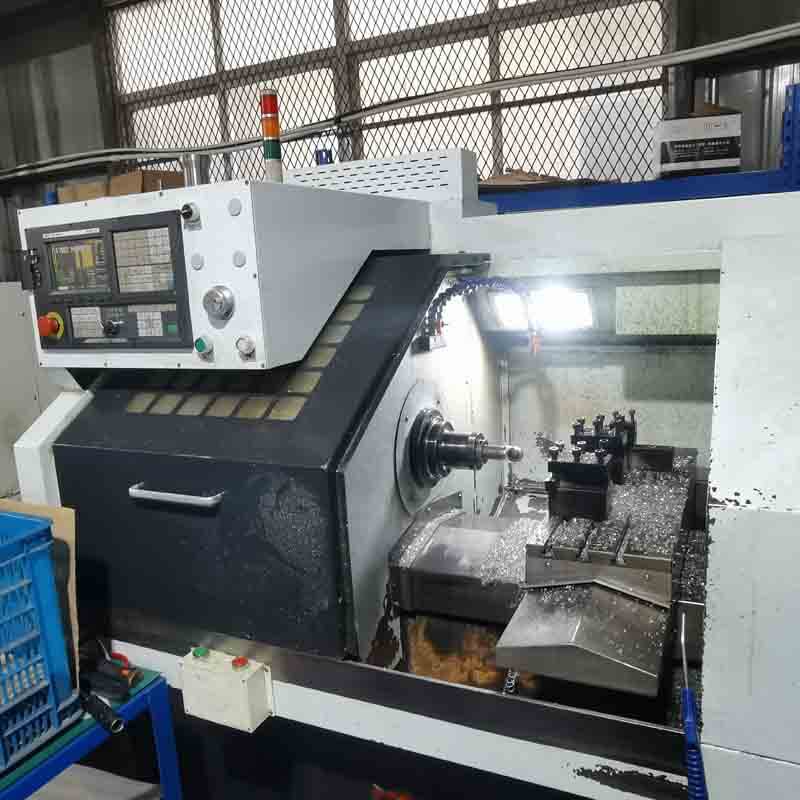
Packing
- For brass turned components. with extremely high requirements, we pack the part one by one with PC bag, or blister bag etc.
- For brass turned components. with moderate requirements, we also perform packing the bag as clients need.

- For brass turned components. with no packaging requirements, we will arrange the products neatly and separate them with cardboard.

Quality Control(Testing)
- Masion conduct material inspections to ensure the partss correctness.
- Masion perform initial inspections on the first samples; production proceeds only if the dimensional inspection is passed, with adjustments made if necessary for non-compliance.
- Masion conduct sample inspections on the manufactured products to ensure compliance with the dimensional requirements specified in the drawings.
Application Area



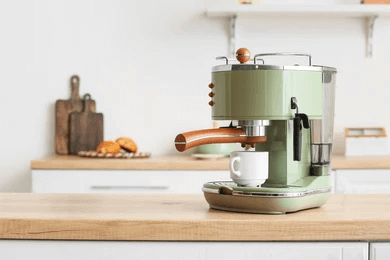


Brass turned components FAQs
Turning:
Description: Turning is the fundamental machining process used for brass turned components. It involves rotating a workpiece on a lathe while a cutting tool removes material to achieve the desired shape.
Purpose: Turning is used to create cylindrical shapes, contours, and profiles. It is the primary process for brass components that have rotational symmetry.
Drilling:
Description: Drilling is a machining process that creates holes in the brass material using a rotating cutting tool.
Purpose:
Brass turned components often require holes for fasteners, connectors, or other purposes. Drilling is employed to achieve precise hole sizes and depths.
Milling:
Description: Milling involves removing material from the brass workpiece using a rotating cutter. This process can create a variety of shapes, slots, and features.
Purpose:
Milling is used when components require flat surfaces, pockets, or intricate geometries that cannot be achieved through turning alone.
Threading:
Description:
Threading is a process used to cut threads onto the surface of the brass turned component, creating helical grooves.
Purpose:
Threads are essential for components that need to be connected or screwed into other parts. Threading can be done internally (tapping) or externally (die cutting).
Knurling:
Description:
Knurling is a process that involves impressing a pattern onto the surface of the brass component to improve grip or provide a decorative finish.
Purpose:
Knurling is commonly used on components like knobs, handles, or other parts where a textured surface is desirable.
Deburring:
Description:
Deburring is the removal of sharp edges or burrs left on the brass turned component during machining.
Purpose:
Deburring improves the component’s safety, appearance, and functionality by eliminating rough edges that could cause injury or interfere with assembly.
Finishing:
Description:
Finishing processes include polishing, plating, or coating the brass turned components to enhance their appearance, durability, or corrosion resistance. Purpose: Finishing processes are applied based on the specific requirements of the application and the desired final appearance of the components.
components:
Polishing:
Description:
Polishing involves smoothing the surface of the brass turned component to achieve a reflective or mirror-like finish.
Purpose:
Polishing enhances the aesthetic appeal of the component, providing a shiny and attractive appearance.
Nickel Plating:
Description: Nickel plating is a process where a thin layer of nickel is electroplated onto the surface of the brass turned component.
Purpose:
Nickel plating enhances corrosion resistance, provides a silver-colored finish, and can improve wear resistance.
Chrome Plating:
Description:
Chrome plating involves depositing a layer of chromium onto the brass turned component.
Purpose:
Chrome plating offers a bright, reflective surface with excellent corrosion resistance. It is often used for decorative purposes.
Electroless Nickel Plating:
Description:
Electroless nickel plating is a process where a layer of nickel-phosphorus alloy is deposited onto the component without the need for an electric current.
Purpose:
Electroless nickel plating provides corrosion resistance, hardness, and a uniform coating, making it suitable for various applications. Antique or Aged Finishes:
Description:
Antique finishes involve treating the brass to create an aged or weathered appearance. Purpose: Antique finishes are used for decorative purposes, giving brass turned components a vintage or rustic look. Clear Coating:
Description:
Clear coating involves applying a transparent protective layer to the brass turned component. Purpose: Clear coatings protect against tarnishing and oxidation while preserving the natural appearance of the brass. Lacquering:
Description:
Lacquering involves applying a clear or tinted lacquer to the brass surface.
Purpose:
Lacquering provides a protective barrier against oxidation and maintains the component’s appearance over time.
Chemical Patina:
Description:
Chemical patina involves treating the brass with chemicals to induce a controlled oxidation, creating unique and artistic colorations. Purpose: Chemical patinas are often used for artistic or decorative purposes, offering a customized and visually appealing finish. Powder Coating:
Description:
Powder coating involves applying a dry powder to the brass component and curing it through heat.
Purpose:
Powder coating provides a durable, protective layer that can be customized in terms of color and texture.
Complexity of Components:
More complex brass turned components with intricate designs or tight tolerances may require additional time for machining and inspection.
Quantity of the Order:
Larger orders may take longer to fulfill due to increased machining time, setup requirements, and the need for comprehensive quality control measures. Material Availability:
The availability of brass raw materials can affect lead time. If specific alloys or grades are in high demand or limited supply, it may impact production schedules.
Machining Processes:
The choice of machining processes and the required precision can influence lead time. For example, additional processes such as threading, milling, or complex surface finishes may extend production time.
Finishing Requirements:
Certain finishes, such as plating or coating, may add time to the production process. Each additional step in finishing requires its own set of processes and drying/curing times.
Tooling and Setup:
The time required for tooling and setup on machining equipment is a consideration. This includes the preparation and calibration of machines before production begins. Supplier and Manufacturer
Capacity:
The capacity of the manufacturing facility and the availability of skilled labor can impact lead time. High-demand periods or capacity constraints may extend production schedules.
Quality Control Procedures:
Stringent quality control procedures, while essential, may add time to the overall lead time. Thorough inspections at various stages contribute to the reliability and quality of the final components.
Shipping and Logistics:
The time required for shipping and logistics, especially for international orders, should be factored into the overall lead time. Communication and Approval
Processes:
Timely communication between the customer and the manufacturer, as well as the approval of design specifications and samples, can affect lead time.
Free Sample
Explore Other Products

Automatic Lathe
Test Pin and other Automatic Lathing Machining Parts such as screws,copper pillar, knob, etc.

CNC Milling
CNC Milling Aluminum different automobile hub, and different 3-axis, 4-axis,5 axis CNC machining parts.
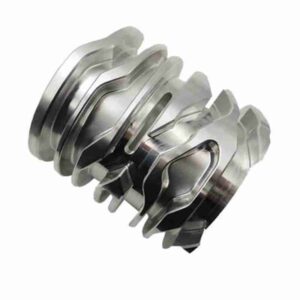
CNC Milling & Turning Combination
Roller shaft,Turn-milling composite processing, 7075 aluminum machining, and another turning and milling CNC machining parts.