Brass Turning Parts
Brass Turning Parts
Brass turned partsmanufacturer in China.
MOQ Starts from 100pcs.
As a specialized brass turned parts manufacturer, Masion provides high-quality custom different automatic brass turned parts services to customers with outstanding production advantages, advanced technological capabilities, and professional solution offerings.
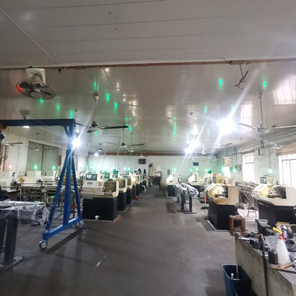
Masion Capability
High Capacity, Proper Price
100000pcs production capacity per day make the price lower.
Free Samples, Low MOQ
100pcs MOQ make you order flexibly with free sample for you testing.
Certified Factory, Guaranteed Quality
ISO9001:2008 and strictly 100% inspection guarantee quality.
High precision, Good surface
With 0.05mm tolerance and with different surface finishing.
Our Products


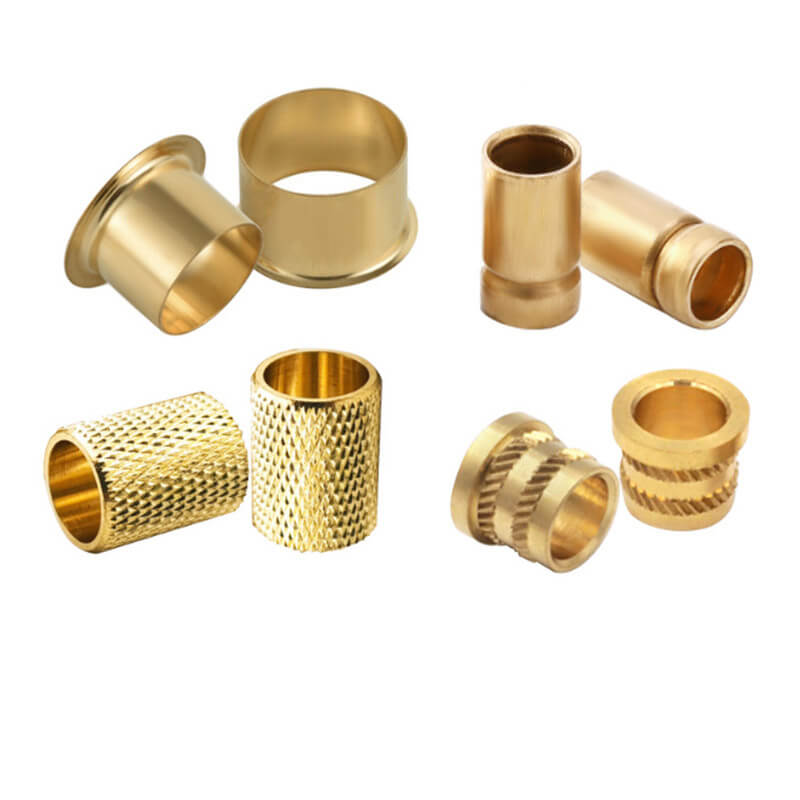

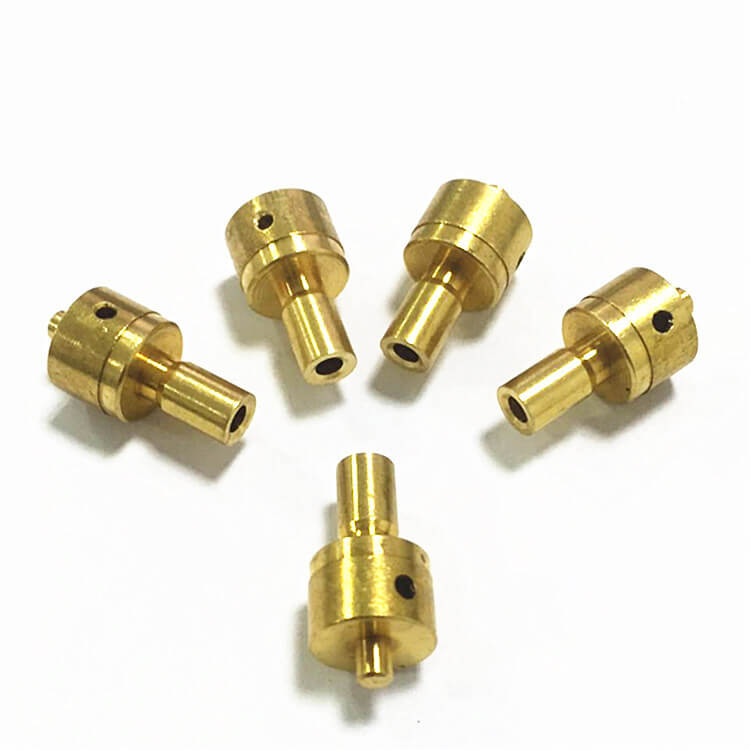
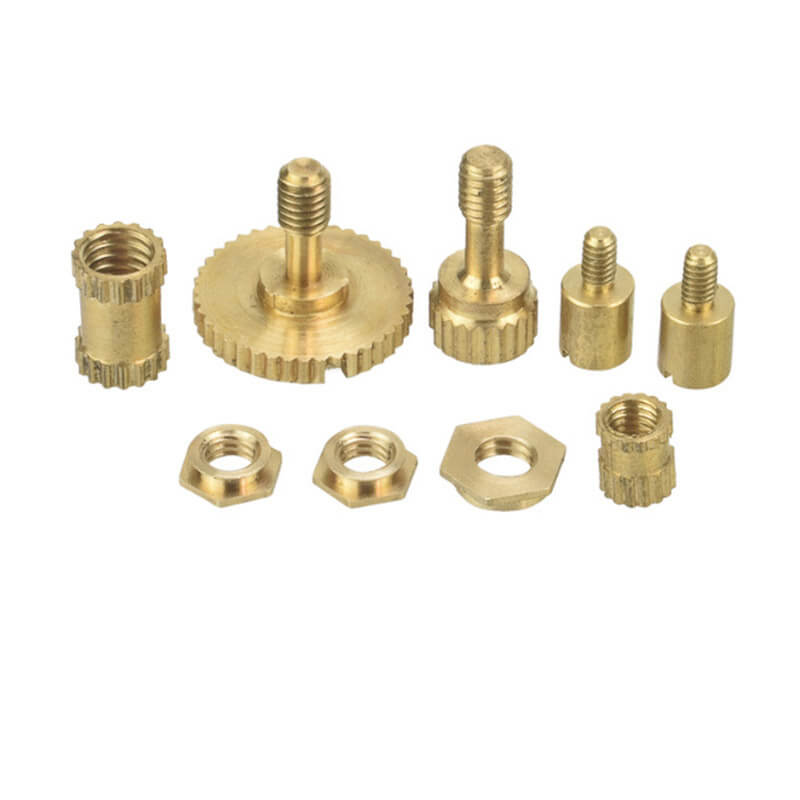

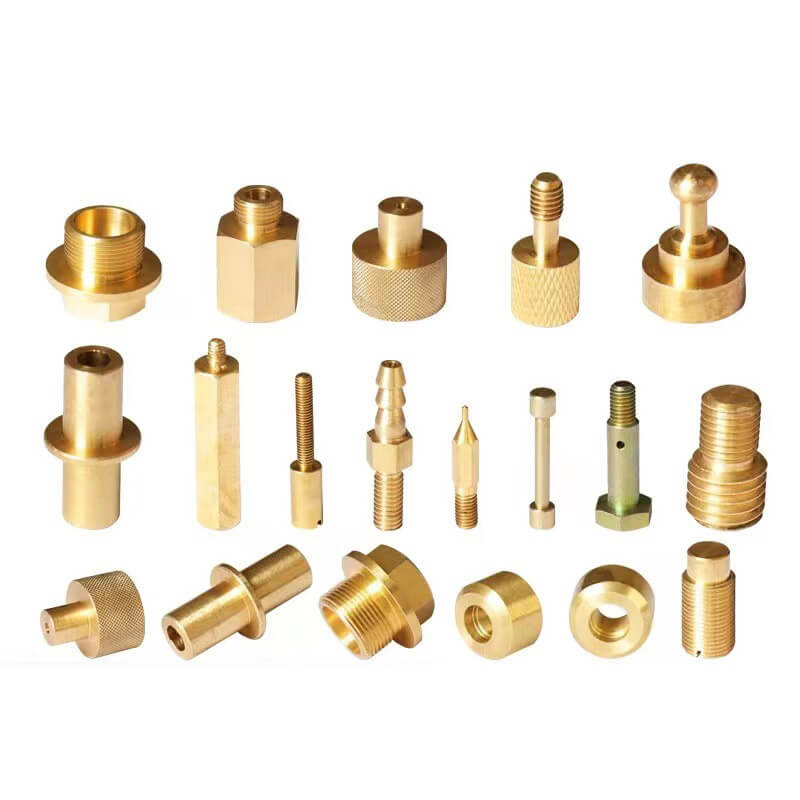
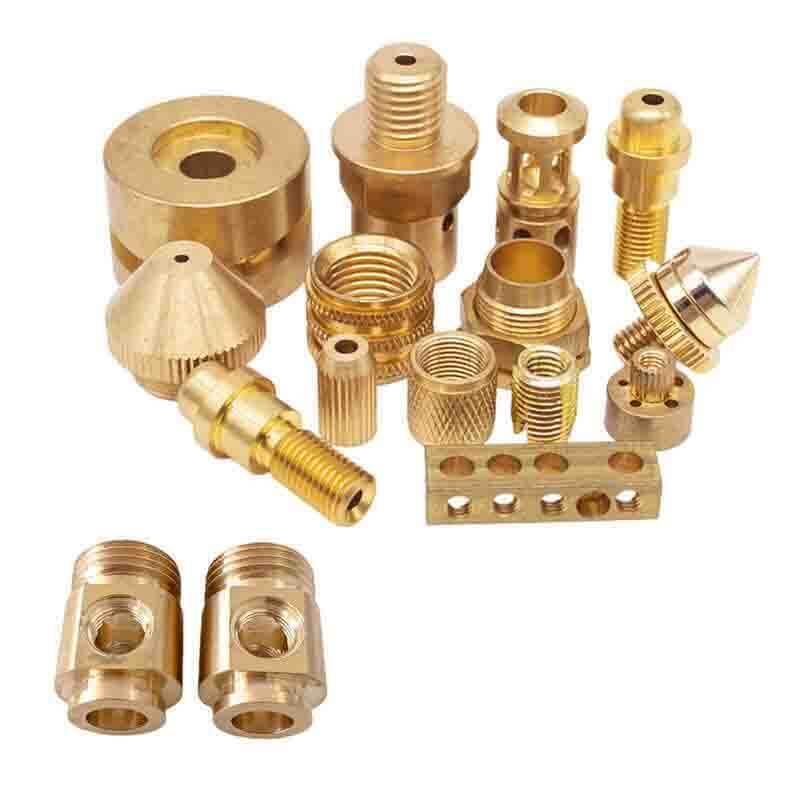
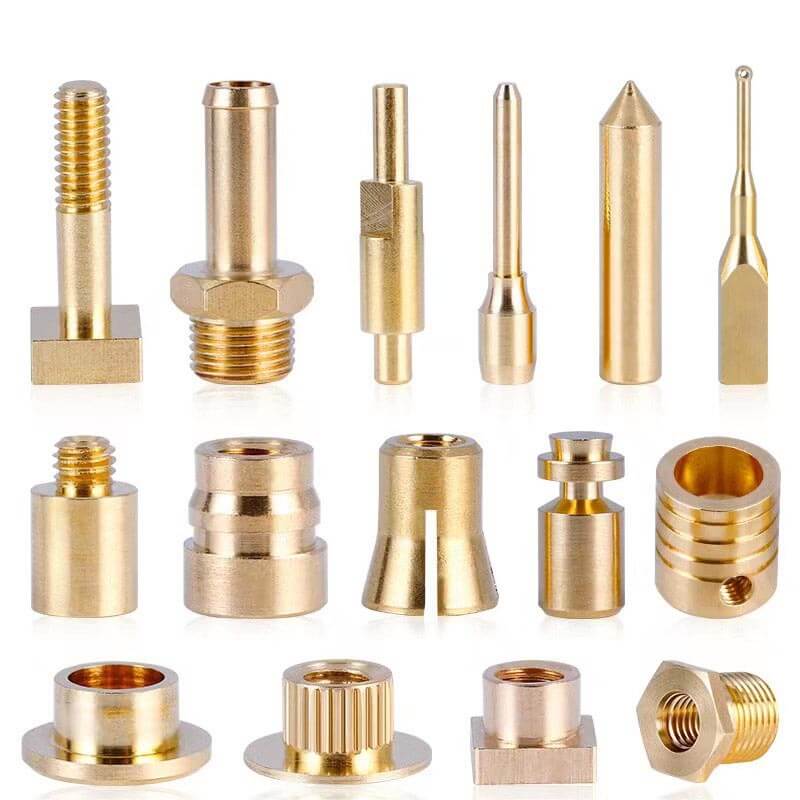
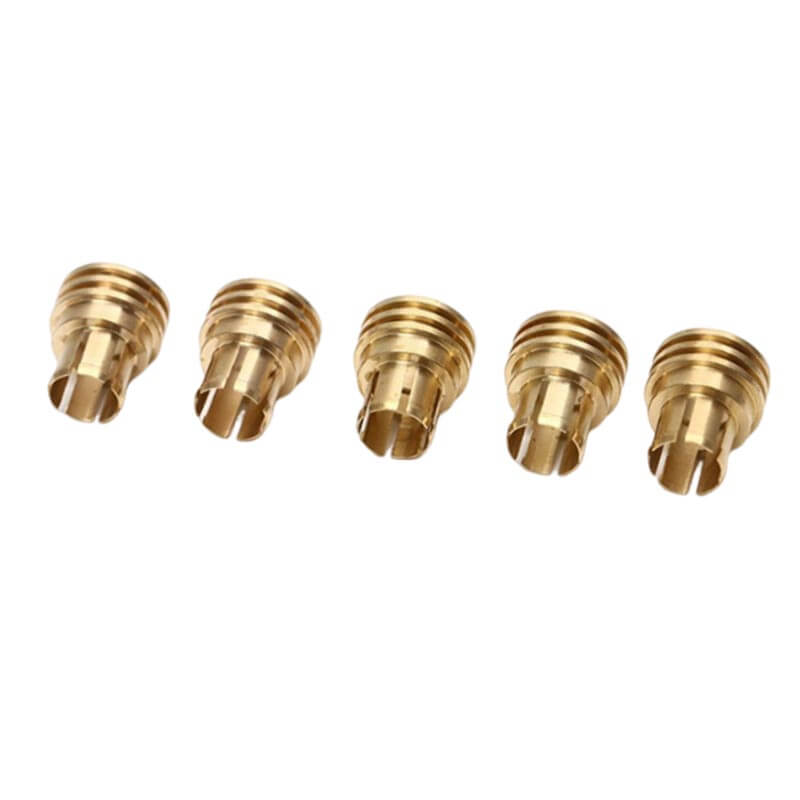
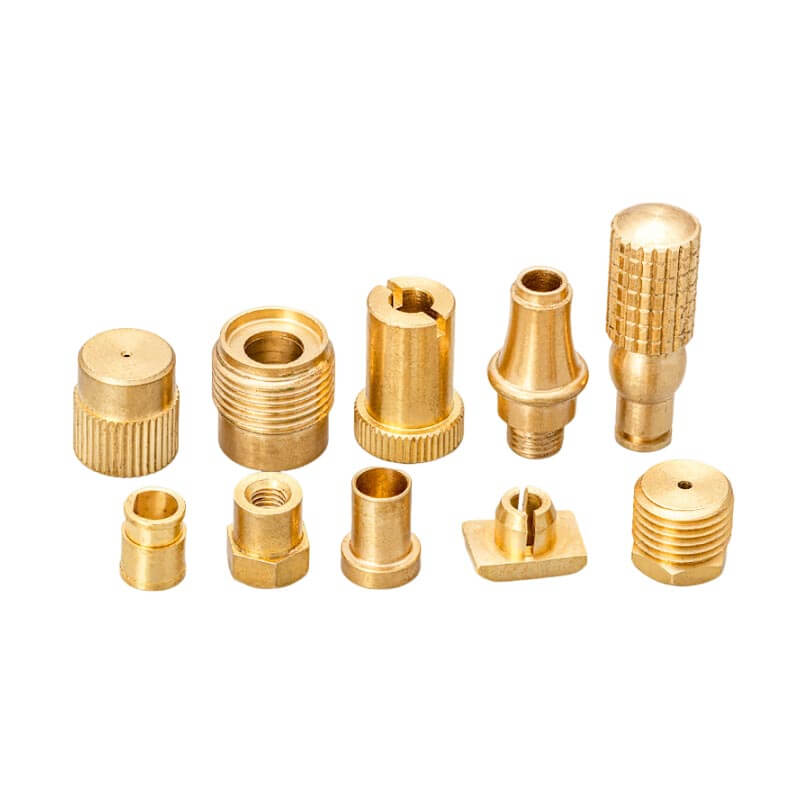
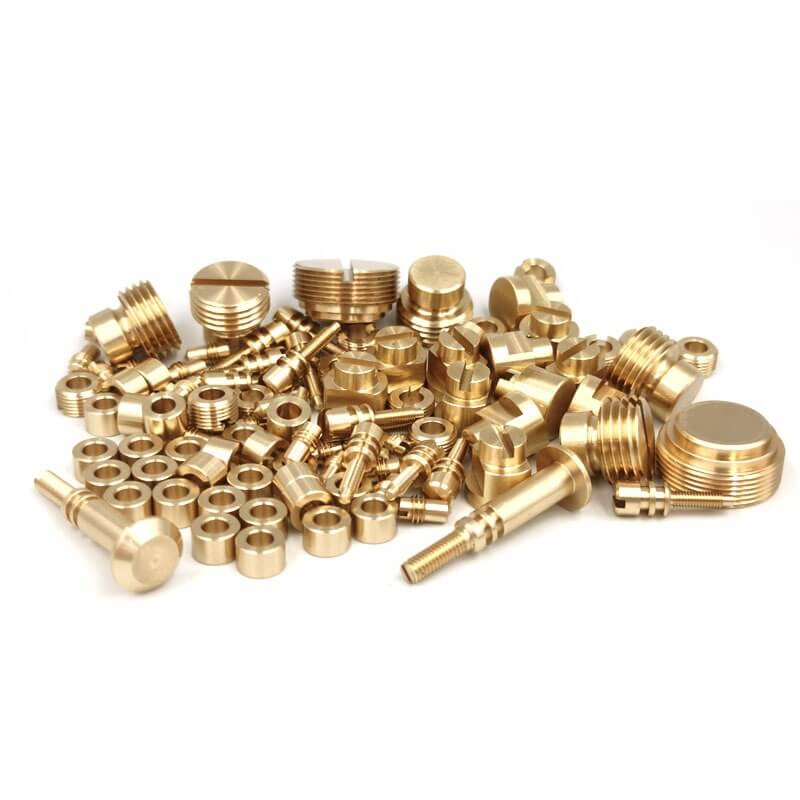
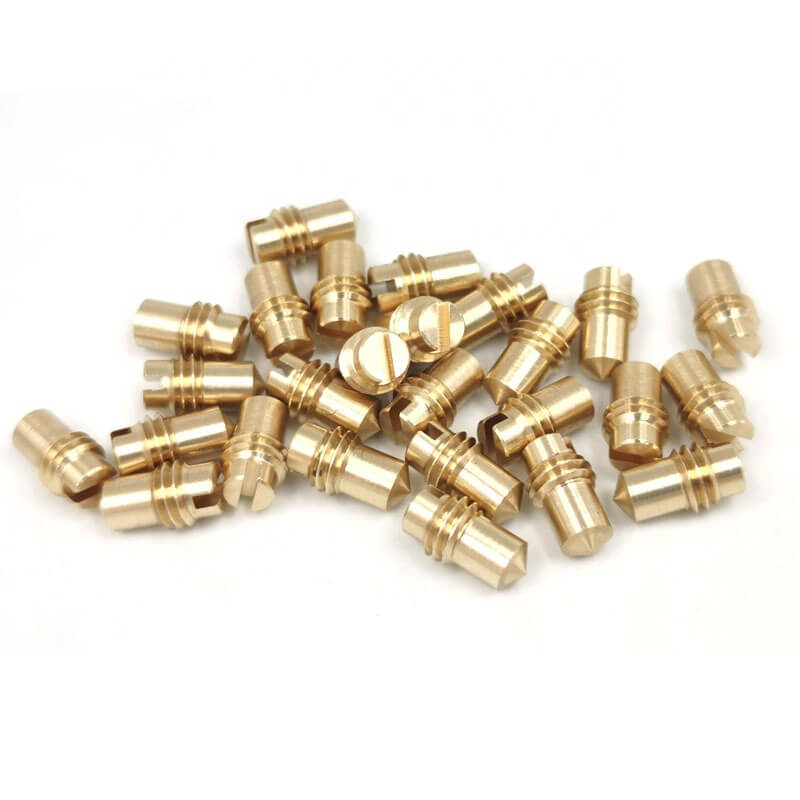
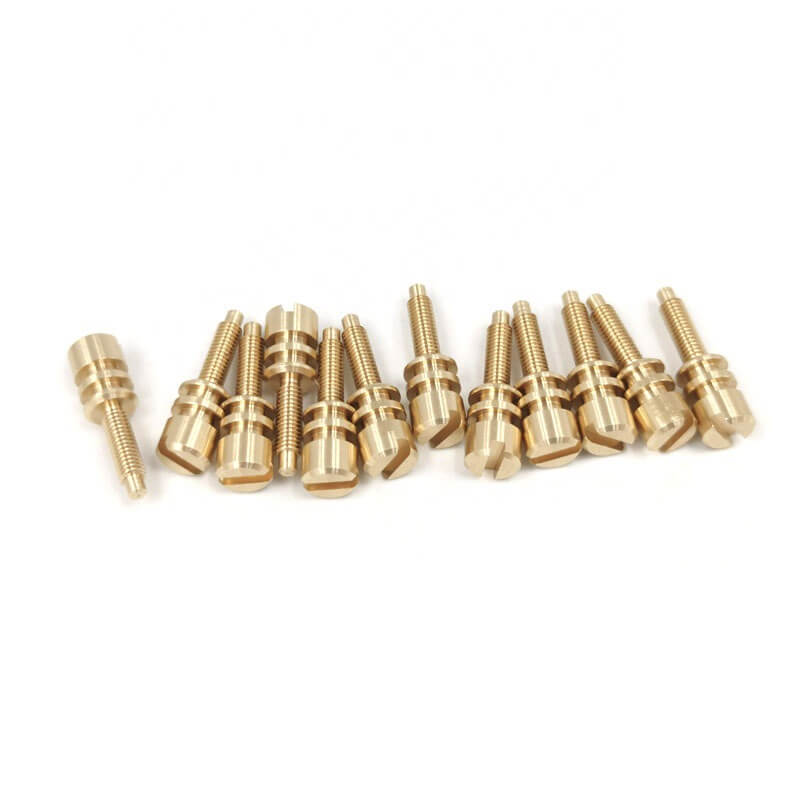
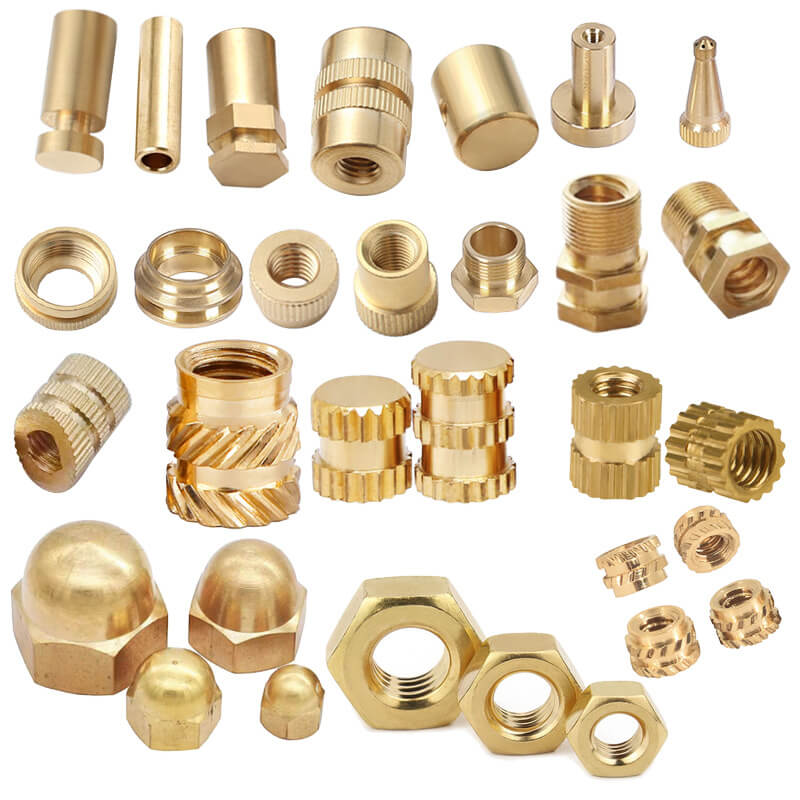
What Sets Us Apart
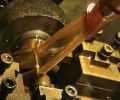
Strong Experience
With 16 years of CNC machiningbrass turned parts expertise, we focus on high-quality, customized solutions for screw demands.
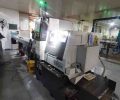
Advanced Imported Machine
40 sets precision CNC automatic lathes, imported Japanese

Surprised Price
Stockpiling a large amount of conventional materials and mature production process can reduce the overall price by 5%.
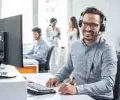
24/7 Engineering Support
Masion offers 24/7 engineering support, design services, cost reduction, quality assurance, smooth product transitions and fast action.
Brass turning parts Manufacturing Process
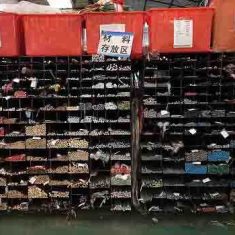
Material Preparation
During the brass materials preparation stage, it is typically required for the materials to have good smoothness and high concentricity, facilitating smooth usage on the automatic lathe feeding rack. Additionally, we offer a regular product material inventory to address any issues related to insufficient delivery lead times.
CNC Automatic Machining
- Milling
- Turning
- Drilling
- Threading
- Cutting
- Counter Sinking
- Boring
- Knurling
- Grooving
- Taper
- Turning
- Tapping
- Reaming

Packing Requirement
- For Brass turning parts with extremely high requirements, we pack the part one by one with PC bag, or blister bag etc.
- For Brass turning parts with moderate requirements, we also perform packing the bag as clients need.
- For Brass turning parts with no packaging requirements, we will arrange the products neatly and separate them with cardboard.

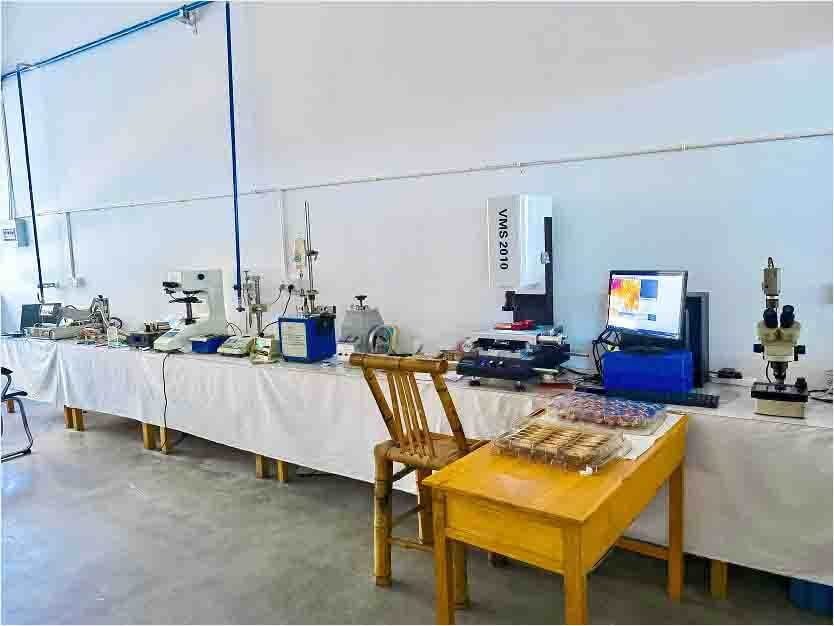
Quality Control (Testing)
- We conduct material inspections to ensure their correctness.
- We perform initial inspections on the first samples; production proceeds only if the dimensional inspection is passed, with adjustments made if necessary for non-compliance.
- We conduct sample inspections on the manufactured products to ensure compliance with the dimensional requirements specified in the drawings.
Application Area
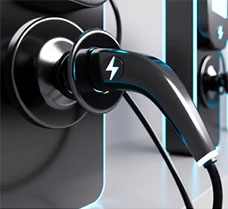
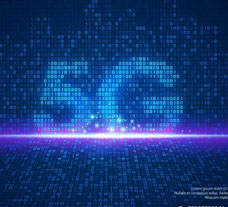
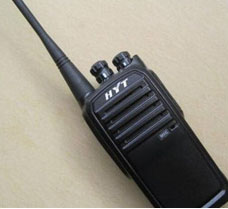
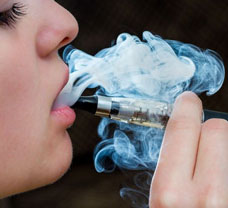
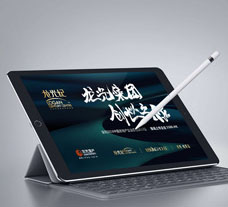

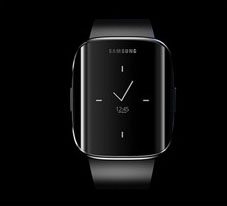

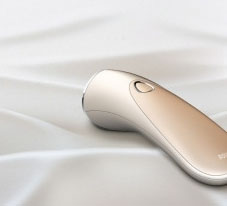
Brass turning parts FAQs
The advantages of brass turning parts are diverse, making them highly favored in various industrial applications:
Â
Excellent machinability: Brass possesses outstanding machinability, facilitating efficient turning, milling, and cutting processes in the production of brass parts.
Â
Superior conductivity: Due to its excellent electrical conductivity, brass turning parts are commonly used in the manufacturing of electrical and electronic devices. Connectors, sockets, and other electrical components often utilize brass materials to ensure optimal electrical conductivity.
Â
Exceptional thermal conductivity: In addition to its electrical conductivity, brass exhibits excellent thermal conductivity. As a result, brass parts are frequently used in the fabrication of radiators, coolers, and other equipment requiring efficient heat conduction.
Â
Good corrosion resistance: Brass features corrosion resistance and durability, making it well-suited for applications in humid environments or those subject to significant humidity variations. This characteristic ensures the stability of brass turning parts outdoors and in certain chemical environments.
Â
Elegant appearance: Brass, with its golden color, is a widely used material in architectural decoration and precision instruments. Its elegant appearance, combined with ease of machining, makes it suitable for manufacturing various exquisite parts.
Ensuring the precision and quality of brass turned parts is a crucial aspect of the production process. Here are some key steps and measures:
Â
High-Precision Machinery: Masion utilizes advanced automatic lathes imported from Taiwan and Swiss lathefrom Japan Citizen for turning operations. These machines provide more accurate and stable processing, ensuring that the parts meet design specifications.
Â
Strict Process Control: Masion implements a rigorous production process control flow, ensuring that each manufacturing step adheres to specifications. This includes material preparation, turning processes, heat treatment (if required), surface treatment, etc.
Â
Precision Measurement Instruments: Masion employs high-precision measuring instruments such as coordinate measuring machines, projectors, and micrometers to accurately measure the dimensions of each part. This helps identify and correct any dimensional deviations promptly.
Â
Quality Control Inspections: Masion conducts comprehensive quality control inspections, including testing material properties, hardness, appearance, and geometric shapes. This ensures that each part complies with design requirements and quality standards.
Â
Material Selection and Quality Monitoring: Masion selects high-quality brass materials and monitors the quality of raw materials. This ensures that raw materials meet specifications, and their performance remains consistent throughout the entire production process.
Â
Continuous Improvement and Feedback: Masion establishes a feedback mechanism to continuously improve the production process. Regularly reviewing quality data and optimizing manufacturing processes based on experience and lessons learned helps enhance product quality.
Â
Training and Certification: Masion provides training for production operators to ensure they master operational skills. Additionally, certification based on international or industry standards is obtained to ensure that the production process complies with regulations and standards.
Yes, customizing brass turned parts is entirely feasible. Here are our capabilities and advantages in customizing brass turned parts:
Â
Adaptation to Special Design Requirements: We typically assist clients in completing design drawings, either based on samples or sketches, in formats such as STEP, STP, or CAD. This allows for precise negotiation of geometric shapes, dimensions, hole positions, surface treatments, etc., meeting the specific design requirements of the client.
Â
Flexibility and Personalization: The production process for custom brass turned parts at Masion is highly flexible, allowing adjustments based on the client’s personalized requirements. This flexibility enables Masion to provide various types of parts tailored to individual needs.
Â
Material Selection: Clients can choose different types and grades of brass materials to meet specific performance and environmental requirements. This includes various alloy compositions and specific material treatments. CNC turning can be performed on the different materials chosen by the client.
Â
Special Surface Treatments: If clients require special surface treatments such as electroplating, coating, or polishing, we can customize these according to their specifications to achieve the desired appearance and performance.
Â
Quality Control and Testing: Customized brass turned parts still undergo rigorous quality control and testing procedures to ensure they meet design specifications and quality standards.
Â
Quick Response and Delivery: Customized services often involve close collaboration with clients to ensure their needs are met. We strive to provide a quick response and timely delivery.
Â
Therefore, we excel in providing customized services to meet specific client requirements. Whether it’s unique shapes, specific dimensions, or special surface treatment requirements, we are committed to delivering custom brass turned parts that fulfill unique design and functional needs. If you have specific requirements, feel free to contact us, and we will be happy to provide support.
The manufacturing process for brass turned parts involves several steps. Here is a general overview of the manufacturing process:
Â
Design and Engineering: Initially, based on customer requirements and design drawings, the part is designed and engineered. This includes specifying geometric shapes, dimensions, materials, and surface treatment requirements.
Â
Material Preparation: Select appropriate brass material, usually based on specific alloy requirements. The material may be provided in the form of bars or tubes. Material grades such as H58, H59, H62, H65, H68, etc., are chosen to ensure material quality and compliance with relevant standards.
Â
CNC Turning: Employ CNC lathes for turning operations. CNC lathes automatically control the movement of the tool, handle automatic loading, and cut the brass material according to predetermined trajectories, forming the geometric shape of the part. Once the automated machining program is coded, the entire process requires no manual intervention.
Â
Selection of Cutting Parameters: Choose appropriate cutting speeds, feed rates, and cutting depths to ensure precision and surface quality. Adjustments may be necessary based on testing and optimization.
Â
Heat Treatment (Optional): In some applications, brass turned parts may undergo heat treatment processes to improve mechanical properties, hardness, or other characteristics. This step is usually determined based on specific requirements.
Â
Surface Treatment: Conduct surface treatments such as polishing, electroplating, oxidation, etc., as required by design specifications. This enhances the appearance and corrosion resistance of the parts.
Â
Quality Control: Implement quality control measures throughout the production process. Use measuring instruments to inspect dimensions, shapes, and surface smoothness, ensuring each part meets design specifications.
Â
Packaging and Delivery: Finally, after passing quality inspections, the finished brass turned parts undergo appropriate packaging and are delivered according to customer requirements.
The production cycle for brass turned parts depends on several factors, such as:
Â
Complexity of the Part: More complex brass turned parts typically require additional time for machining and adjustments. Parts with intricate geometric shapes or special requirements may necessitate more engineering and production time.
Â
Size and Quantity: The size and production quantity of brass turned parts impact the production cycle. Larger or smaller parts may require different equipment and processes, and high-volume production of brass turned parts is generally more efficient.
Â
Special Machining and Surface Treatments: If brass turned parts require special machining steps or surface treatments, such as heat treatment, electroplating, or polishing, this may extend the overall production cycle.
Â
Customization Requirements: Customized brass turned parts may require more engineering and adjustments as manufacturers strive to meet specific design specifications and requirements.
Â
Production Equipment and Technology: The use of advanced automatic lathes or Swiss-style CNC machines for machining brass turned parts can potentially shorten the production cycle, while older or less efficient equipment may require more time.
Â
Quality Control Steps: Strict quality control steps may add extra time to the process, but they are crucial for ensuring that brass turned parts meet design specifications and quality standards.
Â
Therefore, please contact us and provide the design drawings for your brass turned parts. We can then provide a more specific lead time based on your requirements.
In general, brass materials, with common varieties such as H59 and H62, are often chosen for metal processing on automatic lathes. The selection of brass is due to its advantages, including resistance to rust, corrosion, excellent thermal and electrical conductivity. Brass is commonly applied in environments requiring rust resistance, high temperature tolerance, as well as good electrical and thermal conductivity, such as in faucets, valves, electrical switches, and more.
Â
While using iron as a material for processing is also an option, it typically requires electroplating afterward to prevent rusting. Stainless steel is another material option, and while it doesn’t require electroplating, its higher hardness can result in relatively slower production processing speeds.
Â
Therefore, the choice of brass, especially on automatic lathes, is often driven by the specific advantages it offers, making it suitable for applications where rust resistance, high-temperature tolerance, and good electrical and thermal conductivity are crucial, such as in the production of faucets, valves, electrical switches, and similar components.
Burring in copper parts during processing on an automatic lathe is often a result of tool wear and slow turning speeds. To address burrs on workpieces after lathe machining, the following steps can be taken:
Â
1.Check whether the cutting tool is worn and in need of replacement.
2.Increase the back rake angle and side rake angle appropriately, ensuring a smooth transition edge.
3.Use an oilstone to grind the cutting tool to achieve a smoother cutting edge.
4.Ensure proper alignment of the cutting tool on the spindle centerline.
5.Apply chamfering to all edges, unless there are specific requirements.
Â
These measures help minimize tool wear and optimize cutting conditions, contributing to the reduction or elimination of burrs on copper parts during automatic lathe processing.
The reasons for the unsuitability of products produced through copper turning part machining are as follows:
Â
1.Design Reasons: Some shortcomings resulting from improper automatic lathe machining are closely related to the design of the parts, such as certain defects during heat treatment. Design flaws, both in shape and structure, can lead to heat treatment issues such as deformation or cracking. Examples include having an unreasonable design with stress concentration areas, such as sharp corners, notches, or insufficient transition radii. Additionally, estimating the working conditions of the parts inaccurately, such as underestimating potential overloads, can result in insufficient load-bearing capacity.
Â
2.Processing-related Reasons: Poor control of the copper turning part machining process can lead to various defects and subsequent product failures. Examples include inadequate control of heat treatment processes leading to issues like overheating, decarburization, or insufficient tempering. Suboptimal forging processes may result in a banded microstructure or phenomena like overheating or burning. Inadequate cold working processes can cause low surface finish, excessive tool marks, and grinding cracks, all of which can contribute to the failure of copper turning parts.
The maximum size for brass turning parts processed on automatic lathes and Swiss-type CNC machines is 32mm, while the minimum size is 0.3mm.
Free Sample
Explore Other Products
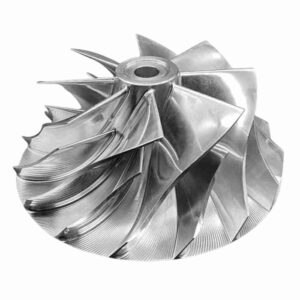
Aluminum Boat Impeller
Five-axis simultaneous complex parts machining, aluminum boat impeller, watercraft impeller, compressor impeller, turbocharger impeller,and another different 5-axis CNC parts etc.
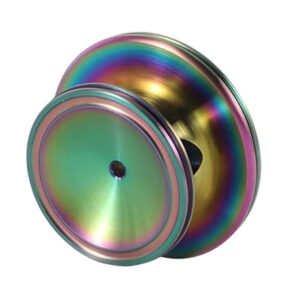
CNC Turning
Stainless Steel stethoscope Chestpiece and another different CNC turning Parts.
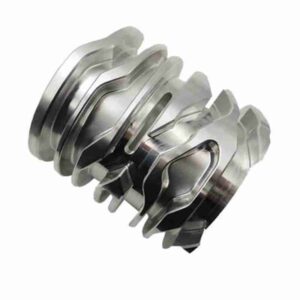
CNC Milling & Turning Combination
Roller shaft,Turn-milling composite processing, 7075 aluminum machining, and another turning and milling CNC machining parts.