Stainless Steel Manifold Blocks
Stainless Steel Manifold Blocks
Stainless steel manifold blocks manufacturer in China.
MOQ Starts from 1pcs.
As a specialized stainless steel manifold block manufacturer,Masion provides high-quality custom stainless steel manifold block services to customers with outstanding production advantages, advanced technological capabilities, and professional solution offerings.

Masion Capability
High Capacity, Proper Price
10000pcs production capacity per month make the price lower.
Free Samples, Low MOQ
1pcs MOQ make you order flexibly with one free sample for you testing.
Certified Factory, Guaranteed Quality
ISO9001:2008 and strictly 100% inspection guarantee quality and CMM inspection equipment.
High precision, thick gold
With 0.005mm tolerance and with different surface finishing and different materials.
Our Products

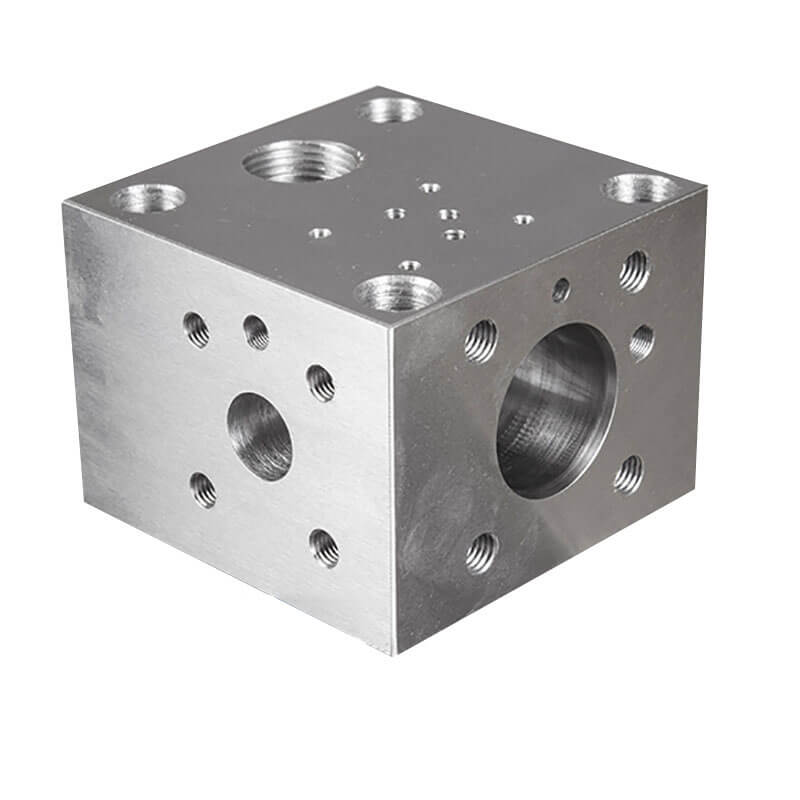

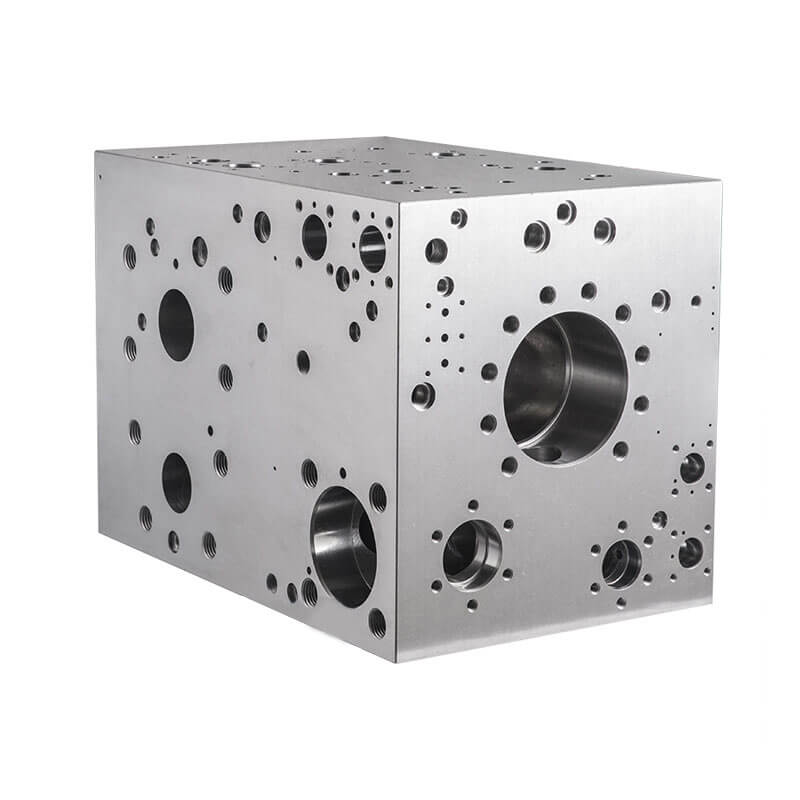
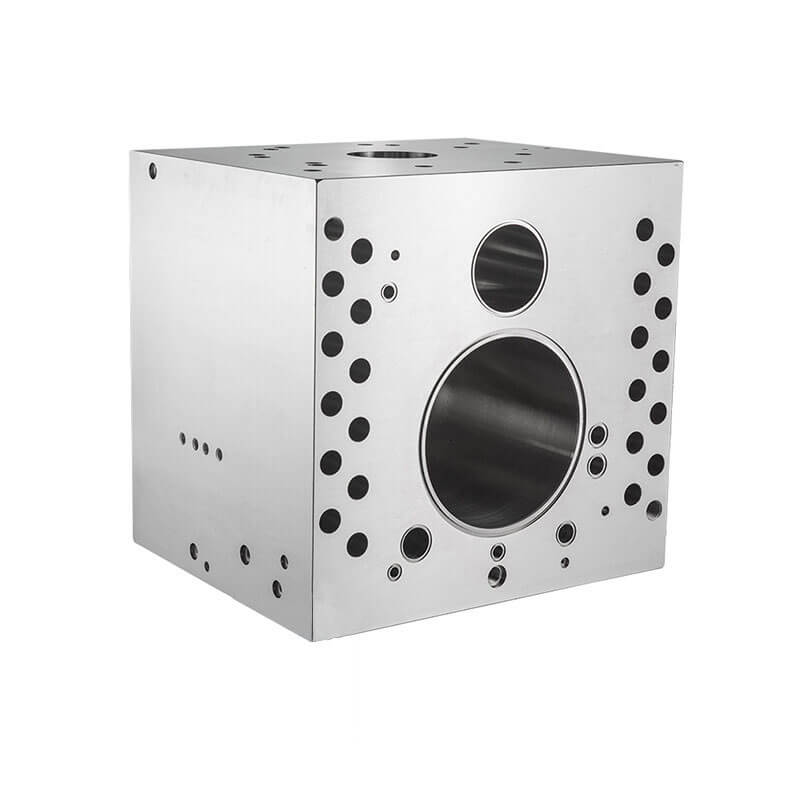


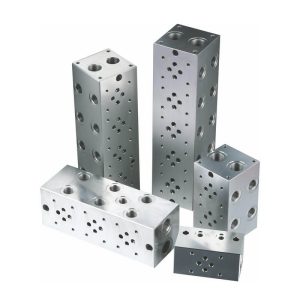
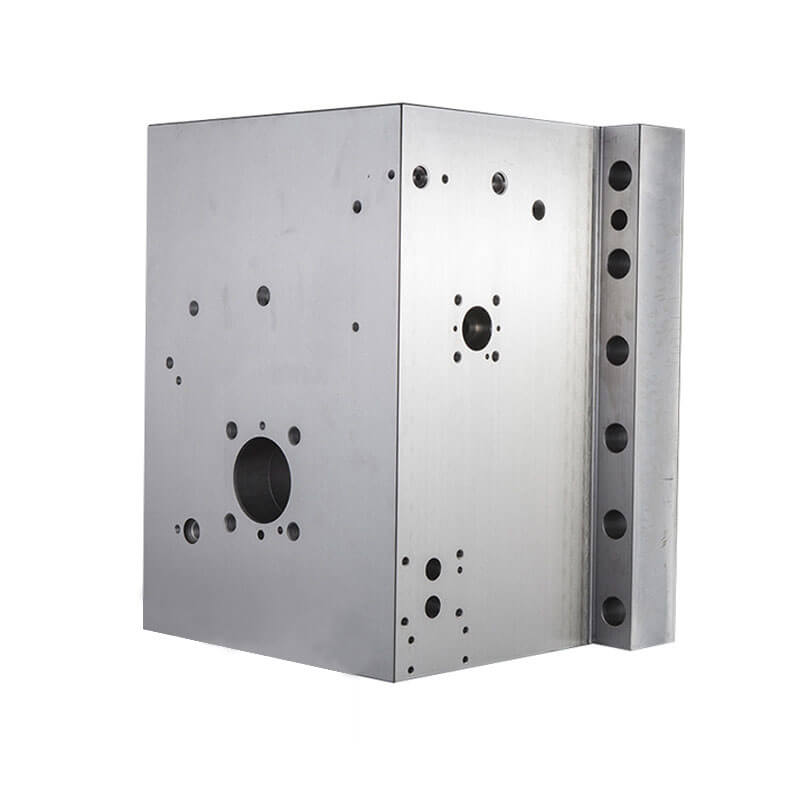
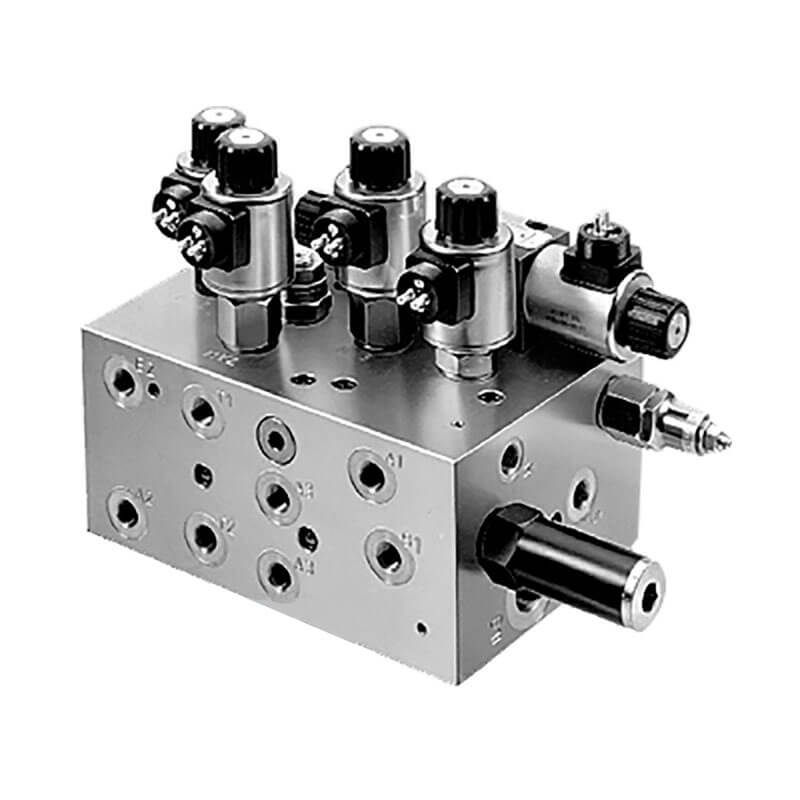


What Sets Us Apart
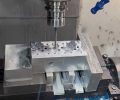
Strong Experience
With 16 years of stainless steel manifold blocks machining expertise, we focus on high-quality, customized solutions for different hydraulic block manifold demands.

Advanced Machine
30 sets precision 3,4,5 axis CNC machining center with mature and stable manufacturing processes with technical machinist and engineer.

Surprised Price
Stockpiling a large amount of conventional materials and having a mature production process can reduce the overall price by 5%.
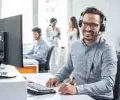
24/7 Engineering Support
Masion is specializing in offering 24/7 engineering support, design services, cost reduction, quality assurance, and smooth product transitionsunparalleled excellence etc.
Stainless Steel Manifold Blocks Manufacturing Process

Raw Material
In the preparation stage of stainless steel manifold blocksmaterials, it is typically required that the materials conform to specified model requirements and meet standard performance criteria. Additionally, we maintain a regular inventory of product materials to address any issues related to insufficient delivery time.
Hydraulic block manifold Machining
- Milling
- Drilling
- Threading
- Cutting
- Counter Sinking
- Boring
- Tapping
- Reaming


Surface Finish
- The stainless steel manifold blocks
can undergo an PVD process to alter its appearance, achieving various colors such as black, blue, red, gold, green, and more. PVD treatment enhances the aesthetic appeal, wear resistance, and corrosion resistance of the hydraulic
Packing
- For stainless steel manifold blocks. with extremely high requirements, we pack the part one by one with PC bag, or blister bag etc.
- For stainless steel manifold blocks. with moderate requirements, we also perform packing the bag as clients need.

- For stainless steel manifold

Quality Control(Testing)
- Masion conduct material inspections to ensure the parts correctness.
- Masion perform initial inspections on the first samples; production proceeds only if the dimensional inspection is passed, with adjustments made if necessary for non-compliance.
- Masion conduct sample inspections on the manufactured products to ensure compliance with the dimensional requirements specified in the drawings.
Application Area



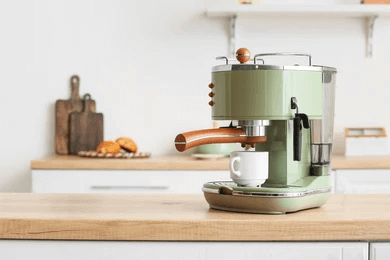


Stainless steel manifold blocks FAQs
A hydraulic manifold block is a component in hydraulic systems that serves as a central distribution point for hydraulic fluid. It typically contains channels, ports, and valves to control the flow of hydraulic fluid between various components such as pumps, valves, and actuators.
A hydraulic manifold block is a crucial component in hydraulic systems, designed to regulate fluid flow between pumps and actuators, such as hydraulic cylinders and motors, and other system components. It acts as a control center by directing fluid to different parts of the hydraulic system, ensuring efficient and accurate operations.
Integration of Hydraulic Components: The manifold block consolidates various hydraulic components such as valves, pumps, and actuators into a single, compact unit. This integration simplifies the hydraulic circuit and reduces the need for numerous hoses and connectors, which can be potential leak points.
Channeling Fluid Flow: Inside the manifold block are drilled channels and passages. These channels are strategically designed to direct hydraulic fluid to and from different components within the system.
Valve Incorporation: Valves are often integrated into the manifold block. These valves, which can include directional control valves, pressure relief valves, and check valves, regulate the flow and pressure of the hydraulic fluid. By controlling these valves, the manifold can direct fluid flow in a specific sequence or path, manage the pressure within the system, and control the speed and force of actuators.
Operation of Actuators: The fluid’s flow from the manifold block to various actuators (like hydraulic cylinders or motors) enables the actuators to perform their intended actions, such as lifting, pressing, or turning. The precise control of fluid flow and pressure ensures that these actions are carried out efficiently and accurately.
Heat Dissipation and Filtration: Some manifold blocks are also designed to help dissipate heat and may include provisions for fluid filtration, further contributing to the overall efficiency and longevity of the hydraulic system.
Customization for Specific Applications: Manifold blocks can be custom designed for specific applications, taking into account factors like the type of fluid used, operating pressure, flow rate, and environmental conditions.
Hydraulic manifold blocks, which are essential components in hydraulic systems, are typically made from a variety of materials. The choice of material usually depends on the application’s specific requirements, such as pressure ratings, environmental conditions, system pressure, fluid compatibility, and application requirements and cost constraints. Common materials used include:
Steel: Often used for high-pressure applications due to its strength and durability. Steel manifold blocks can withstand significant pressure and are resistant to wear and tear.
Aluminum: Popular for its lightweight properties, aluminum is used in applications where weight is a critical factor, such as in aerospace or mobile hydraulics. It’s also easier to machine than steel, but it has a lower pressure rating.
Ductile Iron: This material offers good strength and durability, similar to steel, but at a lower cost. Ductile iron is often used in medium to high-pressure applications.
Stainless Steel: Chosen for its corrosion resistance, stainless steel is ideal for harsh environments or applications where the fluid being used might corrode other materials.
Brass: Sometimes used for lower pressure applications or in environments where corrosion resistance is important but stainless steel is not necessary.
Composite Materials: In some specialized applications, composites may be used for their unique properties like corrosion resistance, lightweight, or thermal insulation.
Yes, hydraulic manifold blocks are often designed with modularity and customization in mind. This allows for the integration of specific valves, ports, and features tailored to the requirements of a particular hydraulic system.
Specific Flow Paths and Circuitry: Custom manifold blocks can be designed with specific internal flow paths and circuitry to match the unique requirements of the hydraulic system. This includes determining the size and placement of channels and ports to facilitate the desired fluid flow and pressure.
Material Selection: Depending on the application, manifold blocks can be made from different materials such as aluminum, steel, stainless steel, or ductile iron, each offering different benefits in terms of strength, weight, and corrosion resistance.
Integration of Valves and Components: Custom manifolds can incorporate various valves (like relief valves, check valves, directional control valves) and other components in specific configurations to suit the application’s needs.
Size and Shape: The physical dimensions and shape of the manifold can be tailored to fit into specific spaces within a machine or system, accommodating size constraints and integration with other components.
Pressure and Temperature Ratings: Based on the operational requirements, custom manifolds are designed to withstand specific pressure ranges and temperatures.
Port Sizes and Types: Customization allows for specific port sizes and types to be incorporated, ensuring compatibility with other components in the hydraulic system.
Surface Treatment: Depending on the environment in which the manifold will operate, it can receive various surface treatments for corrosion resistance or enhanced durability.
Additional Features: Features like built-in sensors for pressure or temperature monitoring, or provisions for heat dissipation, can be included in the design.
For manufacturing hydraulic manifold blocks, certain types of stainless steel are preferred due to their specific properties like strength, corrosion resistance, and machinability. The most suitable grades of stainless steel for this application include:
304 Stainless Steel: One of the most common and versatile types of stainless steel, 304 offers excellent corrosion resistance and good machinability. It’s widely used in a variety of industrial applications, including hydraulic systems. However, it’s important to note that while 304 is highly corrosion-resistant, it may not be the best choice in environments where there is a high risk of chloride-induced corrosion.
316 Stainless Steel: This grade is known for its superior corrosion resistance compared to 304, especially in terms of resistance to chlorides and other harsh chemicals. 316 stainless steel is an ideal choice for hydraulic manifold blocks used in marine environments, chemical processing, or other applications where higher corrosion resistance is required.
316L Stainless Steel: The ‘L’ stands for ‘low carbon’ in 316L, which offers even better corrosion resistance than standard 316, particularly against weld decay. This grade is preferred in applications where welding is involved and in highly corrosive environments.
17-4 PH Stainless Steel: This is a precipitation-hardening stainless steel that combines high strength and hardness with excellent corrosion resistance. It’s particularly useful in applications where both high strength and good corrosion resistance are required. The ability to adjust the material’s properties through heat treatment makes it versatile for various hydraulic applications.
Duplex Stainless Steels (like 2205): Duplex stainless steels combine the qualities of austenitic (like 304 and 316) and ferritic stainless steels. They offer excellent corrosion resistance (superior to 316) and high strength. These steels are beneficial in challenging environments, such as high chloride and corrosive settings, and where strength and durability are critical.
410 Stainless Steel: This is a martensitic stainless steel that provides good corrosion resistance and high strength, but it’s less resistant to corrosion compared to the austenitic grades like 304 and 316. It’s used in applications where strength is more critical than corrosion resistance.
When choosing the appropriate grade of stainless steel for a hydraulic manifold block, factors like the specific environmental conditions (e.g., exposure to corrosive substances, temperature extremes), mechanical requirements (e.g., pressure ratings, strength), and cost considerations should be taken into account. The choice will often be a balance between corrosion resistance, strength, machinability, and cost.
Stainless steel is a popular material choice for hydraulic manifold blocks due to its unique set of characteristics that make it suitable for a wide range of applications, especially in demanding environments. Here are some key characteristics of stainless steel materials used for hydraulic manifold blocks:
Corrosion Resistance: Stainless steel is highly resistant to corrosion, making it ideal for use in environments that are prone to rust and corrosion, such as marine, chemical processing, or outdoor applications. This property extends the lifespan of the manifold block and reduces maintenance requirements.
Strength and Durability: Stainless steel offers high strength and durability, which is crucial for withstanding the high pressures typical in hydraulic systems. This makes it a reliable material for manifold blocks in industrial and heavy-duty applications.
Heat Resistance: Stainless steel can maintain its strength and structural integrity at high temperatures, making it suitable for applications where the hydraulic system might be exposed to elevated temperatures.
Cleanliness and Hygienic Properties: The non-porous surface of stainless steel makes it easy to clean and sanitize, which is essential in industries like food processing, pharmaceuticals, and medical equipment where hygiene is a priority.
Aesthetic Appearance: Stainless steel has a modern, clean appearance which is often desirable for visible parts in machinery and equipment. It maintains its luster and finish over time, even in harsh environments.
Weldability and Machinability: While generally not as easy to machine as materials like aluminum, certain grades of stainless steel can be effectively machined and welded, allowing for the creation of complex and custom manifold block designs.
Chemical Resistance: Stainless steel is resistant to a wide range of chemicals and is not easily damaged by exposure to acids, alkalis, and other harsh substances. This makes it suitable for use in chemical processing and similar industries.
Non-magnetic Property: Certain grades of stainless steel are non-magnetic, which can be important in applications where magnetic interference needs to be avoided, such as in medical or electronic equipment.
Recyclability: Stainless steel is 100% recyclable, which is beneficial from an environmental sustainability perspective.
Cost-Effectiveness Over Long Term: While the initial cost of stainless steel manifold blocks might be higher compared to other materials, their durability, low maintenance, and long life often make them a cost-effective choice over the long term.
In summary, stainless steel’s corrosion resistance, strength, durability, and hygienic properties make it an excellent material choice for hydraulic manifold blocks, especially in applications where these attributes are critical. The selection of a specific grade of stainless steel will depend on the exact requirements of the application, including environmental conditions, pressure levels, and budget constraints.
Stainless steel manifold blocks are used in a wide range of applications due to their durability, high strength, and excellent resistance to corrosion. The specific properties of stainless steel make it an ideal material for environments where the manifold block is exposed to harsh conditions or corrosive substances. Here are some of the key application areas:
Marine and Offshore Applications: The corrosion-resistant nature of stainless steel is particularly beneficial in marine environments, where exposure to saltwater and harsh weather conditions is common. They are used in ships, offshore oil rigs, and other marine equipment.
Chemical Processing Industries: In industries where corrosive chemicals are handled or processed, stainless steel manifold blocks are used due to their ability to withstand these harsh substances.
Food and Beverage Processing: Stainless steel is food-grade and does not contaminate products, making it suitable for use in food and beverage processing equipment.
Pharmaceutical and Biotech Industries: Similar to the food industry, the non-reactive and easily sanitized nature of stainless steel makes it ideal for pharmaceutical and biotechnological applications where cleanliness and contamination prevention are critical.
Industrial Hydraulics: In various industrial settings, especially where high-pressure systems are involved, stainless steel manifold blocks are used for their strength and durability.
Medical Equipment: Due to its hygienic properties and resistance to sterilization processes, stainless steel is used in medical equipment, including those with hydraulic components.
Aerospace and Defense: In aerospace and defense applications, the strength and corrosion resistance of stainless steel manifold blocks make them suitable for hydraulic systems in aircraft and military equipment.
High-Pressure and High-Temperature Applications: Stainless steel can withstand higher temperatures and pressures compared to many other materials, making it suitable for high-performance hydraulic systems.
Automotive Industry: High-end automotive hydraulic systems, such as those in performance or luxury vehicles, may use stainless steel manifolds for their durability and performance.
Clean Energy Systems: In renewable energy sectors, such as solar or wind power, stainless steel manifold blocks are used in hydraulic systems due to their longevity and minimal maintenance needs.
Water Treatment and Distribution: Stainless steel’s resistance to corrosion and ability to handle various water types make it suitable for use in water treatment plants and systems.
To ensure the quality of hydraulic manifold blocks, implement the following measures:
Strict Quality Control Processes:
Establish and enforce rigorous quality control processes, including inspections and tests at each production stage.
Qualified Suppliers and Material Selection:
Choose reliable suppliers and ensure purchased materials meet quality standards through regular supplier evaluations.
Precise Dimensions and Geometry:
Ensure accurate dimensions and geometry during the design phase and use precision machining and measurement tools in production.
Appropriate Material Selection:
Choose materials based on hydraulic system conditions, ensuring sufficient strength, corrosion resistance, and wear resistance.
Comprehensive Testing and Inspection:
Conduct thorough testing, including pressure, leakage, and temperature tests, to verify product performance and reliability.
Document Records and Traceability:
Establish a comprehensive document recording system to track production history and quality control information.
Employee Training:
Ensure proper training for production staff on quality standards, operating procedures, and equipment monitoring.
Improvement and Feedback Mechanism:
Implement a quality improvement and feedback mechanism, encouraging employees to propose enhancements, promptly addressing quality issues, and continuously improving production processes.
What are the different between stainless steel manifold blocks and aluminum manifold blocks ?
Stainless steel and aluminum manifold blocks are both used in hydraulic systems, but they have distinct differences that make each suitable for specific applications. Here’s a comparison of their key characteristics:
Material Strength and Durability:
Stainless Steel: Known for its high strength and durability, stainless steel can withstand higher pressures and harsher conditions. It’s more resistant to wear and deformation over time.
Aluminum: While aluminum is strong enough for many applications, it’s generally less durable than stainless steel under high stress or extreme conditions.
Corrosion Resistance:
Stainless Steel: Offers excellent corrosion resistance, making it ideal for harsh environments or applications where the fluid might be corrosive.
Aluminum: Also has good corrosion resistance, but it can be more susceptible to certain types of corrosion, such as galvanic corrosion, especially when in contact with other metals.
Weight:
Stainless Steel: Heavier, which might be a consideration in applications where weight is a critical factor.
Aluminum: Significantly lighter than stainless steel, advantageous in applications like aerospace or mobile equipment where weight reduction is beneficial.
Thermal Conductivity:
Stainless Steel: Has lower thermal conductivity compared to aluminum, which means it dissipates heat more slowly.
Aluminum: High thermal conductivity, making it efficient in dissipating heat. This can be an advantage in systems where maintaining a lower operating temperature is important.
Machinability:
Stainless Steel: Generally harder to machine than aluminum, requiring more robust tools and slower machining speeds. This can affect manufacturing costs.
Aluminum: Easier to machine, allowing for more intricate designs and potentially lower manufacturing costs.
Cost:
Stainless Steel: Typically more expensive than aluminum, both in terms of raw material costs and manufacturing.
Aluminum: More cost-effective, which can be a crucial factor in budget-sensitive projects.
Applications:
Stainless Steel Manifolds: Often used in industrial settings, marine applications, and environments where high pressure, temperature extremes, or corrosive substances are present.
Aluminum Manifolds: Commonly found in mobile hydraulics, aerospace, and automotive applications where weight and ease of machining are significant considerations.
Free Sample
Explore Other Products
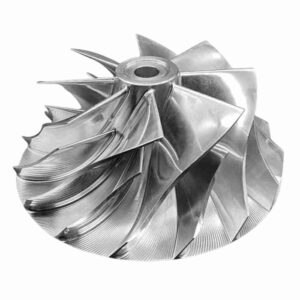
Aluminum Boat Impeller
Five-axis simultaneous complex parts machining, aluminum boat impeller, watercraft impeller, compressor impeller, turbocharger impeller,and another different 5-axis CNC parts etc.

3D pringting
Masionprovides a wide range of 3D printing services, including SLA 3D printing (Stereolithography), SLS 3D printing (Selective Laser Sintering), MJF (Multi Jet Fusion), and DLMS (Direct Metal Laser Sintering).

CNC Milling
CNC Milling Aluminum different automobile hub, and different 3-axis, 4-axis,5 axis CNC machining parts.