Stainless Steel Turned Parts
Stainless Steel Turned Parts
Stainless steel turned parts manufacturer in China.
MOQ Starts from 1pcs.
As a specialized stainless steel turned parts manufacturers,Masion provides high-quality custom different stainless steel turned parts services to customers with outstanding production advantages, advanced technological capabilities, and professional solution offerings.

Masion Capability
High Capacity, Proper Price
10000pcs production capacity per month make the price lower.
Free Samples, Low MOQ
1pcs MOQ make you order flexibly with one free sample for you testing.
Certified Factory, Guaranteed Quality
ISO9001:2008 and strictly 100% inspection guarantee quality and CMM inspection equipment.
High precision, thick gold
With 0.005mm tolerance and with different surface finishing and different materials.
Our Products


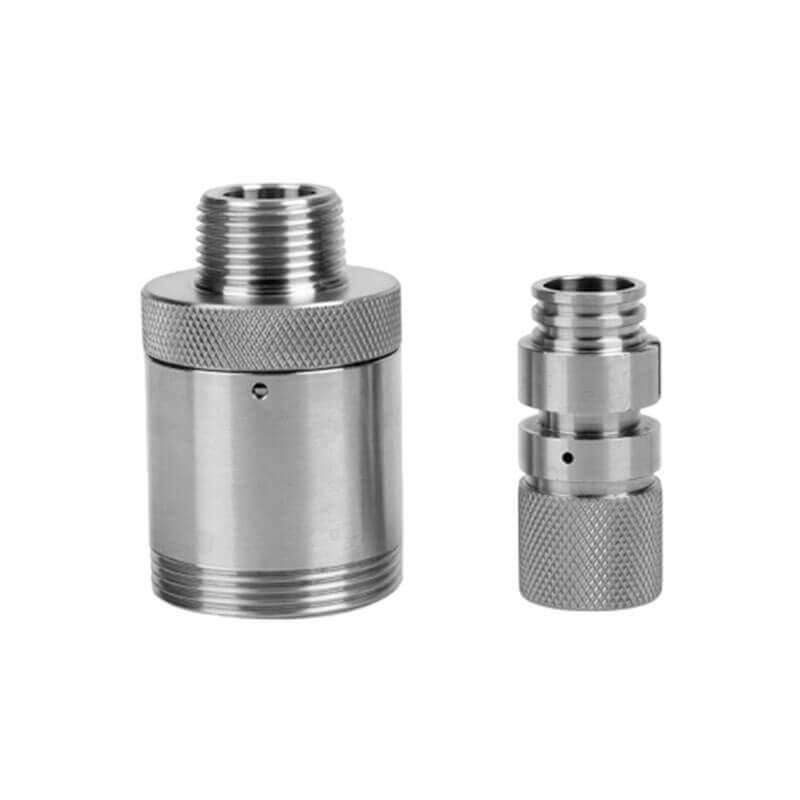



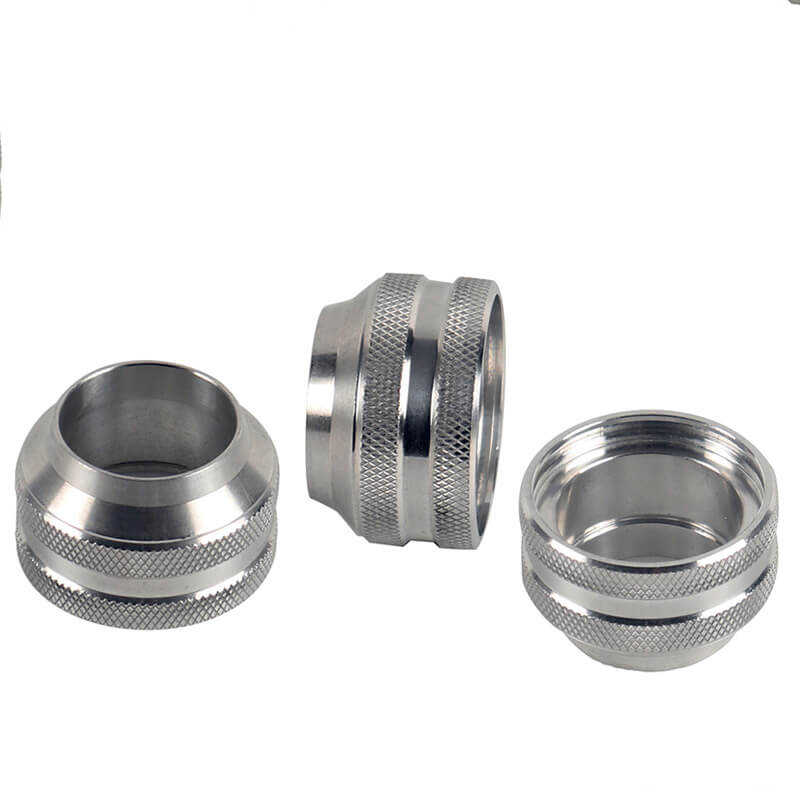



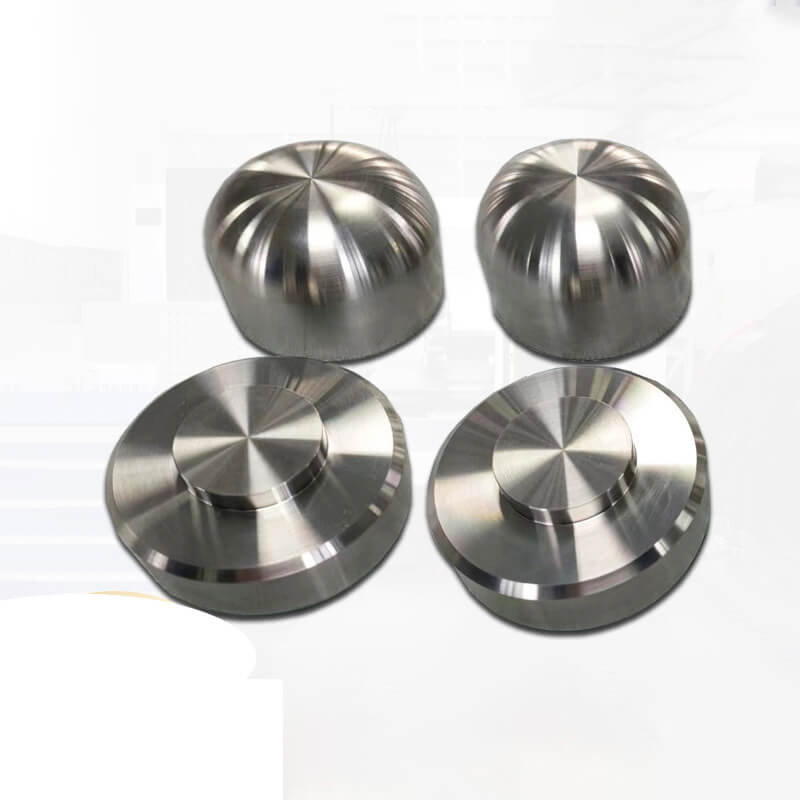

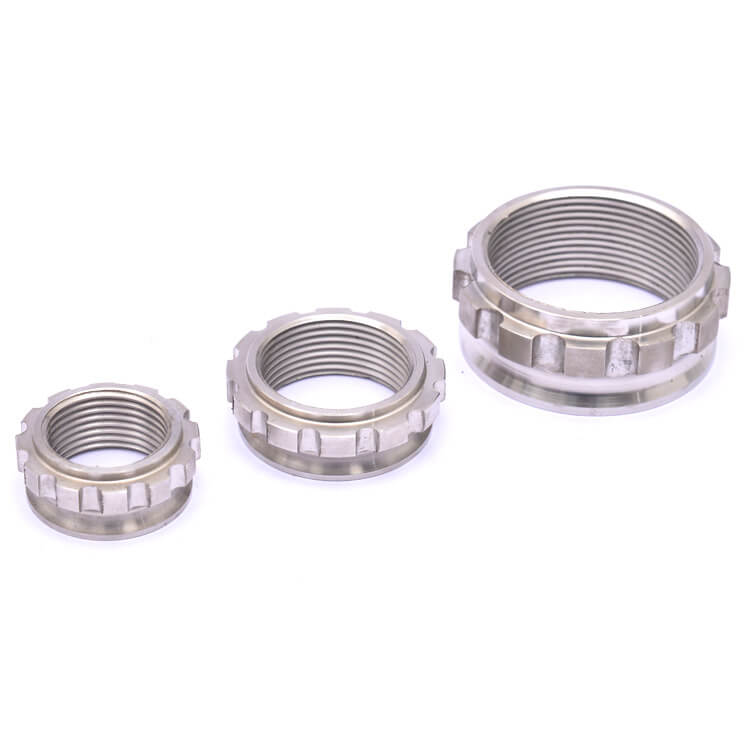

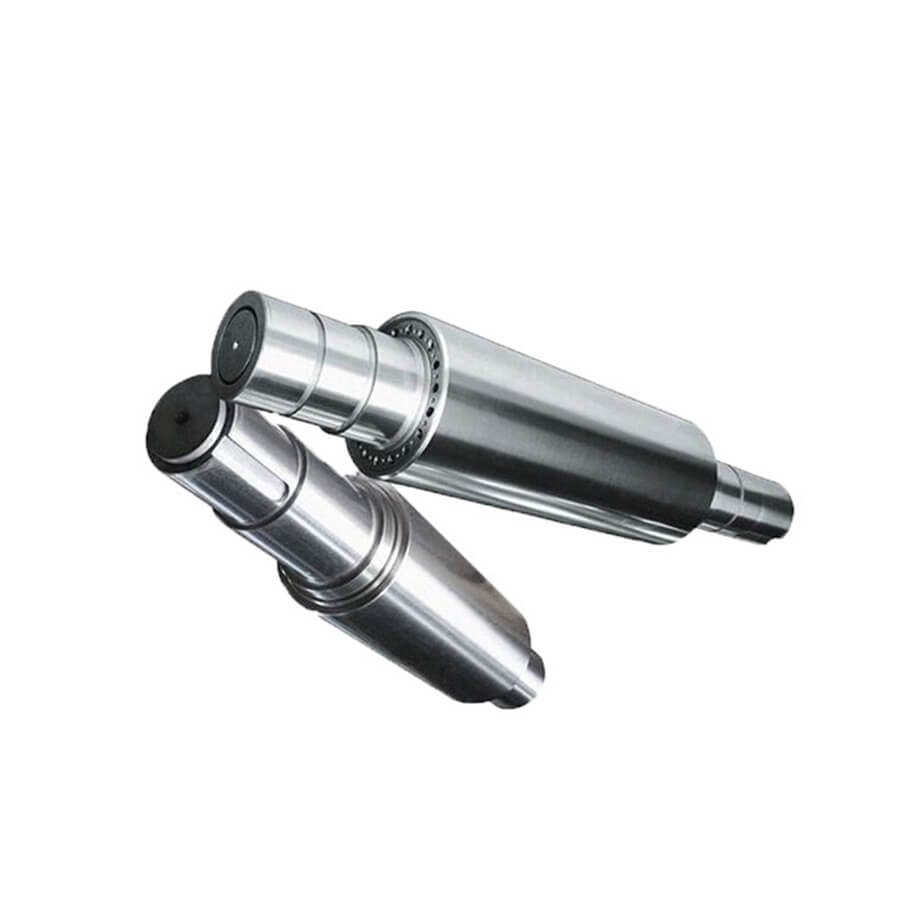

What Sets Us Apart
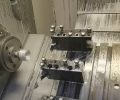
Strong Experience
With 16 years of Turning machining and 5 years stainless steel turned parts machining expertise, we focus on high-quality, customized solutions for different Swiss Lathe Partsdemands.

Advanced Machine
50 sets precision lathe with mature and stable manufacturing processes with technical machinist and engineer. We could manufacture different stainless steel turned parts to meet your need.
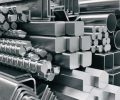
Surprised Price
Stockpiling a large amount of conventional materials and having a mature production process can reduce the overall price by 5%.
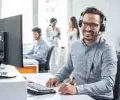
24/7 Engineering Support
Masion is specializing in offering 24/7 engineering support, design services, cost reduction, quality assurance, and smooth product transitionsunparalleled excellence etc.
Stainless Steel Turned Parts Manufacturing Process
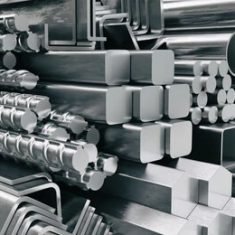
Raw Material
During the Stainless Steel materials preparation stage, it is typically required for the materials to have good smoothness and high concentricity, facilitating smooth usage on the automatic lathe feeding rack. Additionally, we offer a regular product material inventory to address any issues related to insufficient delivery lead times.
Stainless Steel Turned Parts Machining
- Milling
- Turning
- Drilling
- Threading
- Cutting
- Countersinking
- Boring
- Knurling
- Grooving
- Taper
- Tapping
- Reaming

Packing
- For Stainless Steel Turned Parts. with extremely high requirements, we pack the part one by one with PC bag, or blister bag etc.
- For Stainless Steel Turned Parts. with moderate requirements, we also perform packing the bag as clients need.

- For Stainless Steel Turned Parts. with no packaging requirements, we will arrange the products neatly and separate them with cardboard.

Quality Control(Testing)
- Masion conduct material inspections to ensure the partss correctness.
- Masion perform initial inspections on the first samples; production proceeds only if the dimensional inspection is passed, with adjustments made if necessary for non-compliance.
- Masion conduct sample inspections on the manufactured products to ensure compliance with the dimensional requirements specified in the drawings.
Application Area



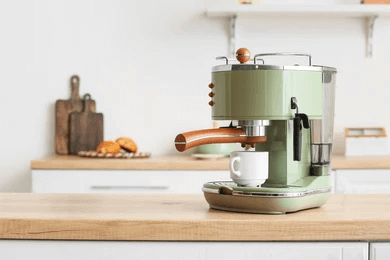


Stainless Steel Turned Parts FAQs
Stainless steel turned parts are components manufactured through the process of turning, a machining process where a cutting tool, typically a lathe, removes material from a rotating workpiece to create cylindrical parts with precise dimensions and finishes. Stainless steel is often chosen for its strength, corrosion resistance, and ability to withstand high temperatures.
Yes, stainless steel turned parts can be extensively customized to meet specific requirements. This customization is one of the key advantages of using turned parts in various applications. Here are several aspects in which these parts can be customized:
Dimensions and Shape: The turning process allows for the creation of parts in a wide range of sizes and shapes. This includes not only basic cylindrical shapes but also more complex geometries with various features such as grooves, threads, and tapers.
Precision and Tolerances: Customization also extends to the level of precision and the tightness of tolerances that can be achieved. This is crucial for applications where parts must fit together with exact precision.
Material Grades: There are different grades of stainless steel available, each with unique properties. Depending on the application, you can choose from austenitic (like 304 and 316), ferritic, or martensitic stainless steels. Each type offers different levels of strength, corrosion resistance, and workability.
Surface Finishes: The surface finish of the part can be customized according to the needs of the application. Options range from matte and brushed finishes to highly polished surfaces. Surface treatments can also be applied to enhance corrosion resistance, wear resistance, or for aesthetic purposes.
Additional Features: Custom features such as threads, knurls, drilled holes, and milled sections can be added to the parts to meet specific functional requirements.
Batch Sizes: Customization is not limited to the parts themselves but also extends to the production volume. Whether you need a single prototype or large production runs, the process can be adapted to suit.
Compliance with Standards: Turned parts can be customized to comply with various industry standards and certifications, ensuring they meet the regulatory requirements specific to different sectors.
They are manufactured using CNC (Computer Numerical Control) lathes or traditional lathes, where the stainless steel material is rotated while a cutting tool shapes it to the desired dimensions and specifications.
Machining stainless steel can be challenging due to its toughness and work hardening properties. This requires appropriate tooling, cutting speeds, and feeds to ensure efficient machining and to avoid excessive wear on the tools.
Ensuring quality in stainless steel turned parts involves several key steps and practices throughout the manufacturing process.We usually ensure the qualityas follows:
Material Selection: Start with high-quality stainless steel. The properties of the final part are largely determined by the quality of the material used. Different grades of stainless steel are available, each suited to different applications.
Precision Machining Equipment: Use advanced, well-maintained machining equipment. Computer Numerical Control (CNC) lathes and turning centers provide high precision and consistency. Regular maintenance of this equipment is crucial to prevent inaccuracies.
Experienced Operators and Engineers: Skilled personnel are essential. Experienced machinists and engineers can optimize the machining process, choose the right tools, and adjust parameters like speed and feed rate to achieve the best results.
Tooling Quality: Use high-quality cutting tools and regularly inspect them for wear and damage. Stainless steel can be tough on tools, so choosing the right type and maintaining them is vital for quality and precision.
Strict Adherence to Tolerances: Follow the specified design tolerances closely. Precise measurements and adjustments are necessary to ensure that each part meets the required specifications.
Quality Control Processes: Implement rigorous quality control measures. This includes regular inspections at various stages of the manufacturing process using tools like calipers, micrometers, and Coordinate Measuring Machines (CMMs).
Surface Finish Inspection: Ensure that the surface finish meets the required specifications. This can involve visual inspections as well as measurements using surface roughness testers.
Batch Testing and Sampling: For large production runs, use batch testing and statistical sampling methods to ensure consistent quality across all parts.
Traceability and Documentation: Maintain thorough documentation and traceability of materials, processes, and inspections. This is important for quality assurance and for meeting regulatory requirements in certain industries.
Continuous Improvement: Adopt a continuous improvement mindset. Regularly review and refine manufacturing processes to enhance quality, reduce waste, and increase efficiency.
Customer Feedback: Incorporate feedback from customers to identify areas for improvement and to ensure the parts meet or exceed their expectations.
Quality is ensured through precision machining, adherence to strict tolerances, regular inspections, and using high-grade stainless steel materials. Additionally, surface treatments and finishes can be applied to enhance corrosion resistance and appearance.
Yes, there are several types of stainless steel used for turned parts, each with unique properties that make them suitable for different applications. The choice of stainless steel type depends on factors like the required strength, corrosion resistance, machinability, and the specific environment in which the part will be used. Here are some of the most commonly used types:
Austenitic Stainless Steels:
Examples: 304, 316
Characteristics: These are the most widely used stainless steels. They contain high levels of chromium and nickel, making them highly corrosion-resistant. They are also non-magnetic and have good formability and weldability.
Applications: Often used in food processing equipment, chemical containers, medical devices, and marine environments.
Martensitic Stainless Steels:
Examples: 410, 420
Characteristics: These steels are magnetic and can be hardened by heat treatment. They have moderate corrosion resistance and high strength.
Applications: Common in cutlery, surgical instruments, and other applications where hardness is important.
Ferritic Stainless Steels:
Examples: 430, 446
Characteristics: Ferritic stainless steels have moderate corrosion resistance and are magnetic. They contain higher levels of chromium and lower levels of carbon compared to martensitic stainless steels.
Applications: Used in automotive applications, industrial equipment, and consumer appliances.
Duplex Stainless Steels:
Examples: 2205, 2507
Characteristics: These are a combination of austenitic and ferritic steels. They offer high strength as well as better corrosion resistance compared to single-phase austenitic or ferritic steels.
Applications: Common in the oil and gas industry, chemical processing equipment, and marine applications.
Precipitation Hardening Stainless Steels:
Examples: 17-4, 15-5
Characteristics: These steels can be hardened by a special heat treatment process. They offer a good balance of corrosion resistance and strength.
Applications: Used in aerospace, chemical processing equipment, and high-strength components.
Several factors influence the cost of stainless steel turned parts. Understanding these factors can help in budgeting and decision-making for projects involving these components. Here are the primary factors that affect their cost:
Material Grade and Quality: Different grades of stainless steel have varying prices. Higher grades with better corrosion resistance or specific properties like high temperature or high strength properties can be more expensive.
Complexity of the Part: More complex parts require more intricate machining, which can increase the time and skill needed for production. This includes features like deep holes, tight tolerances, thin walls, or complex geometries.
Tolerances and Precision Requirements: Tighter tolerances and higher precision requirements necessitate more time, better equipment, and often more skilled labor, all of which contribute to higher costs.
Quantity of Parts: The number of parts you need can significantly affect the cost per unit. Larger quantities often reduce the cost per part due to economies of scale, but the initial setup costs can be high.
Machining Time and Labor Costs: The time it takes to machine each part is a significant factor. More complex or larger parts typically take longer to machine, increasing labor costs.
Type of Machining Equipment Used: Advanced machines like CNC (Computer Numerical Control) lathes might produce parts more efficiently and with higher precision than conventional lathes, but they also come with higher operational costs.
Surface Finishing: Additional surface treatments such as polishing, plating, or anodizing add to the overall cost. The type and extent of finishing required will impact the price.
Waste Material and Efficiency of Material Usage: The amount of stainless steel that gets machined away (and therefore wasted) can influence cost, especially with more expensive materials.
Supply Chain Factors: Costs can be affected by the availability of stainless steel, shipping costs, and any tariffs or trade restrictions.
Urgency of the Order: Expedited orders typically cost more due to the need to prioritize production and possibly pay overtime or expedite shipping.
Quality Control and Testing: Additional inspections and testing for ensuring part quality can add to the cost, especially for industries with strict regulatory requirements.
Design Changes and Revisions: If the part design changes during production, this can incur additional costs due to retooling, wasted materials, and additional labor.
Free Sample
Explore Other Products
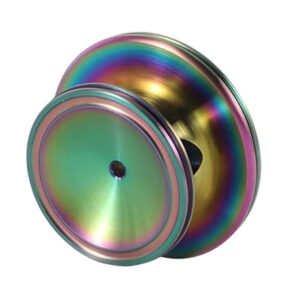
CNC Turning
Stainless Steel stethoscope Chestpiece and another different CNC turning Parts.
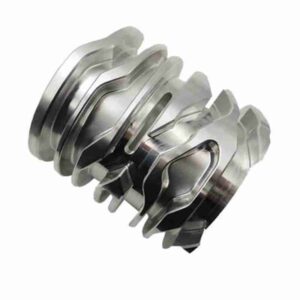
CNC Milling & Turning Combination
Roller shaft,Turn-milling composite processing, 7075 aluminum machining, and another turning and milling CNC machining parts.

Automatic Lathe
Test Pin and other Automatic Lathing Machining Parts such as screws,copper pillar, knob, etc.