Swiss Lathe Parts
Swiss Lathe Parts
Swiss Lathe Parts manufacturer in China.
MOQ Starts from 1pcs.
As a specialized Swiss Lathe Parts manufacturer, Maison provides high-quality custom Swiss Lathe Parts services to customers with outstanding production advantages, advanced technological capabilities, and professional solution offerings.

Masion Capability
High Capacity, Proper Price
5000pcs production capacity per month make the price lower.
Free Samples, Low MOQ
1pcs MOQ make you order flexibly with one free sample for you testing.
Certified Factory, Guaranteed Quality
ISO9001:2008 and strictly 100% inspection guarantee quality and CMM inspection equipment.
High precision, Good Surface
With 0.05mm tolerance and with different surface finishing.
Our Products
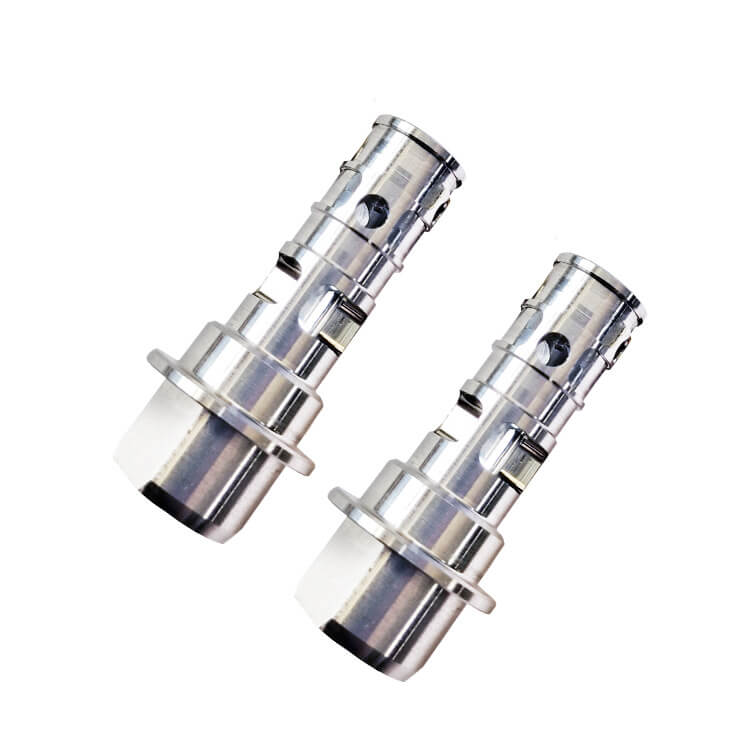


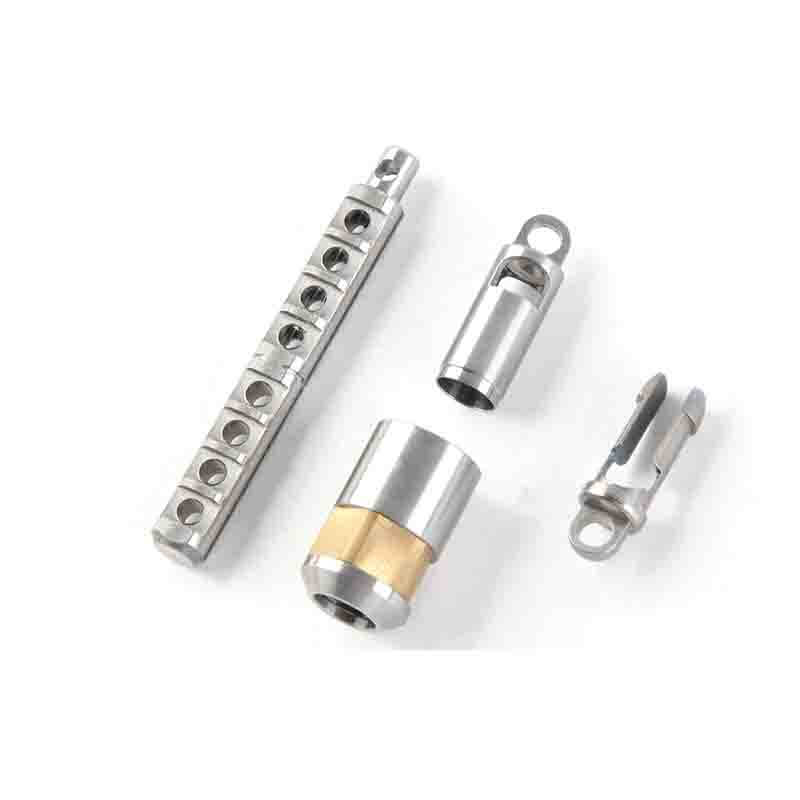
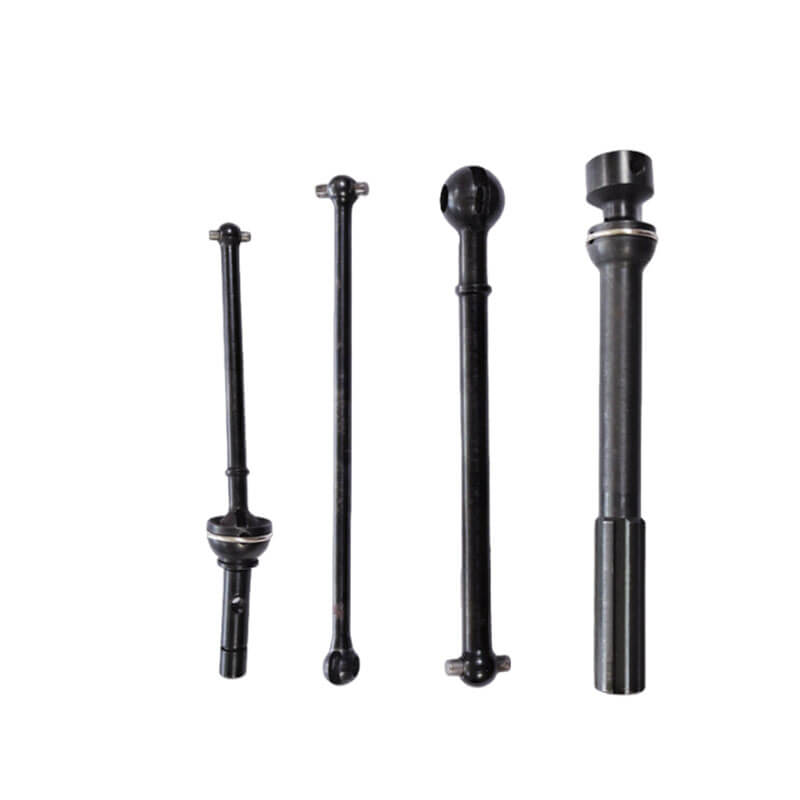

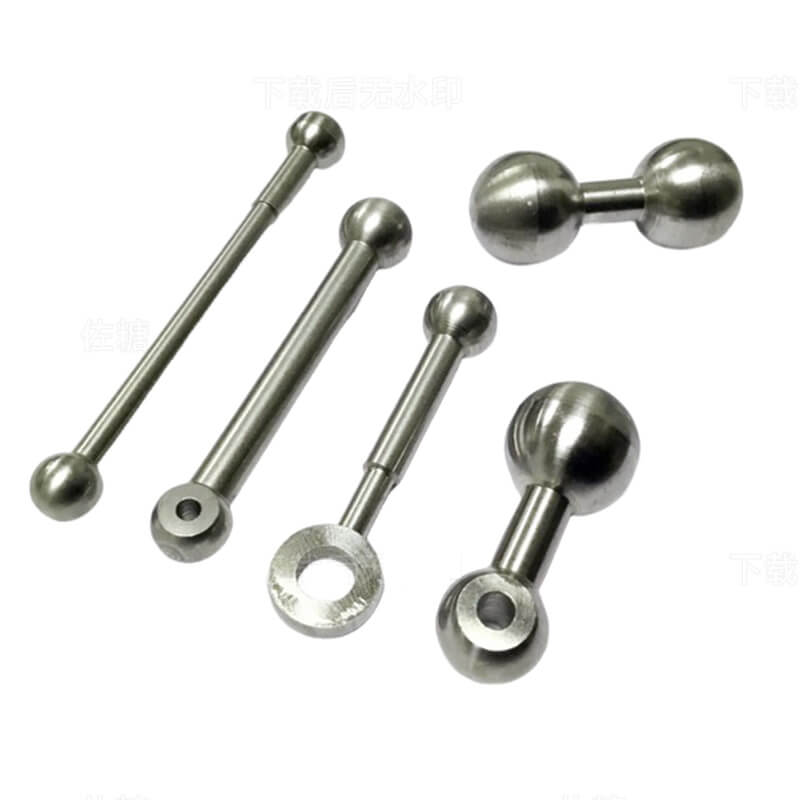

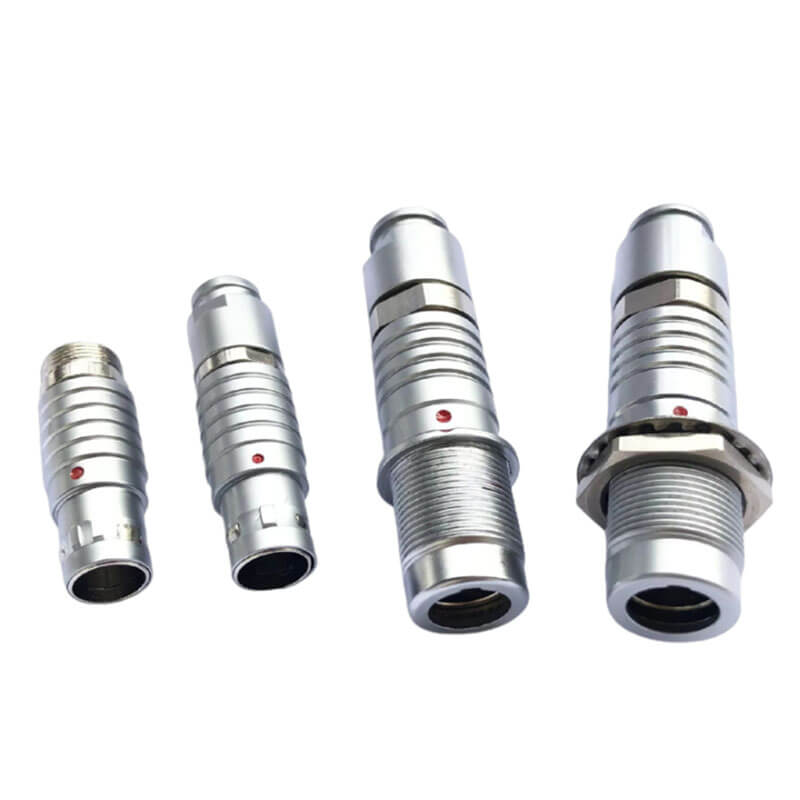
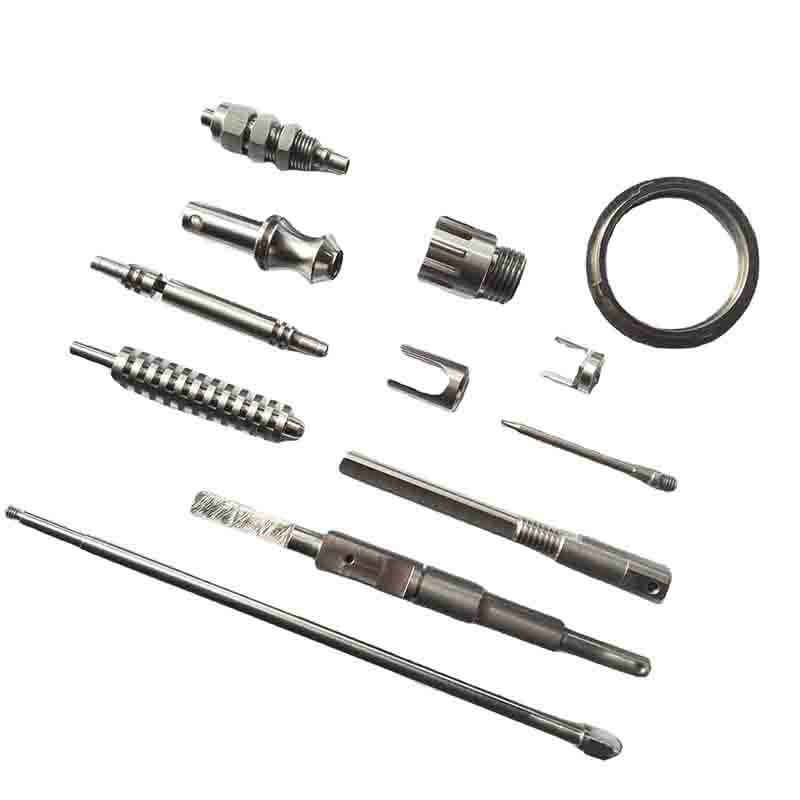

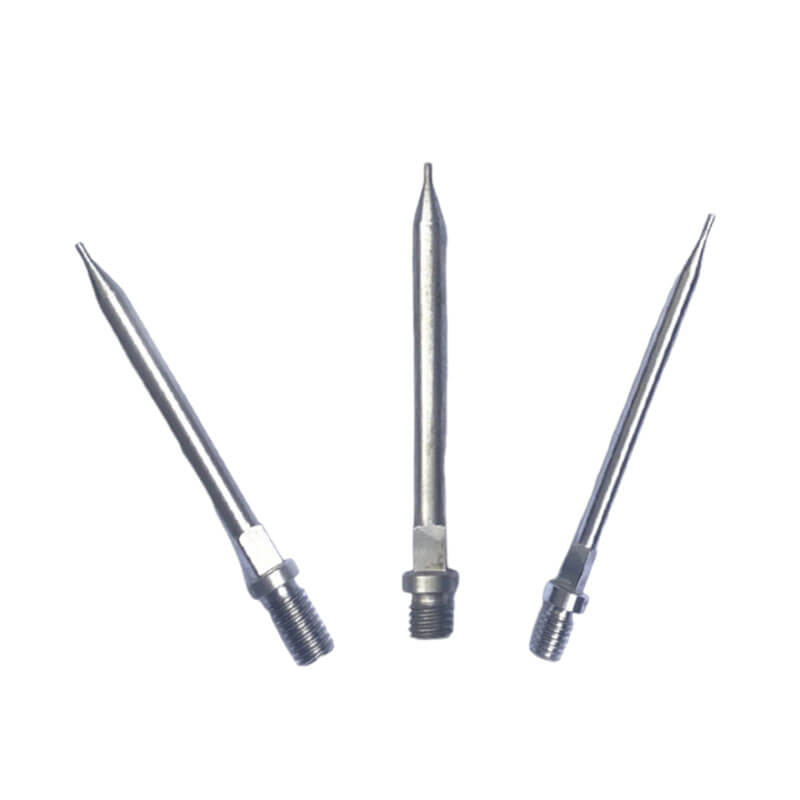
What Sets Us Apart

Strong Experience
With 16 years of Swiss Lathe Parts machining expertise, we focus on high-quality, customized solutions for different Swiss Lathe Parts demands.

Advanced Imported Machine
30 sets precision imported Japanese Citizen Swiss CNC Lathe with mature and stable manufacturing processes with technical machinist and engineer.

Surprised Price
Stockpiling a large amount of conventional materials and having a mature production process can reduce the overall price by 5%.
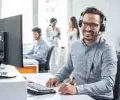
24/7 Engineering Support
Masion is specializing in offering 24/7 engineering support, design services, cost reduction, quality assurance, and smooth product transitionsunparalleled excellence etc.
Brass turning parts Manufacturing Process

Raw Material
At different stages of material preparation, various materials such as aluminum, brass, copper, bronze, stainless steel, titanium, PEEK, POM, etc., can be chosen to manufacture custom Swiss Lathe Parts. Additionally, we offer regular product material inventory to address any issues related to insufficient delivery times.
Swiss lathe parts Machining
- Milling
- Turning
- Drilling
- Threading
- Cutting
- Counter Sinking
- Boring
- Knurling
- Grooving
- Taper
- Turning
- Tapping
- Reaming
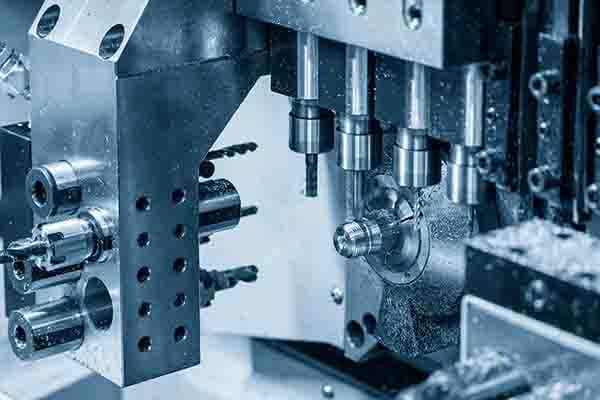
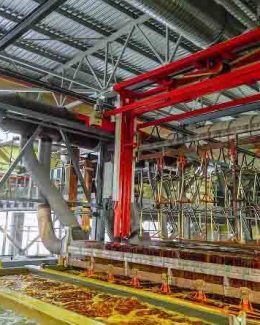
Surface Finish
Aluminum Swiss lathe parts can be anodized for varied colors and appearance options. Stainless steel Swiss lathe parts could use PVD or electroplating for improved wear resistance and aesthetics.Titanium Swiss lathe parts can undergo anodizing or PVD treatment for color variety and enhanced wear resistance. Casting iron Swiss lathe parts can be powder-coated, rust-proofed or black plating for increased rust resistance and durability.
Packing
- For Swiss lathe parts with very high packaging requirements, we will package the products individually, using ziplock bags, or foam bags, or pearl cotton bags, or blister box and then separate with cardboard, and finally use carton packaging.

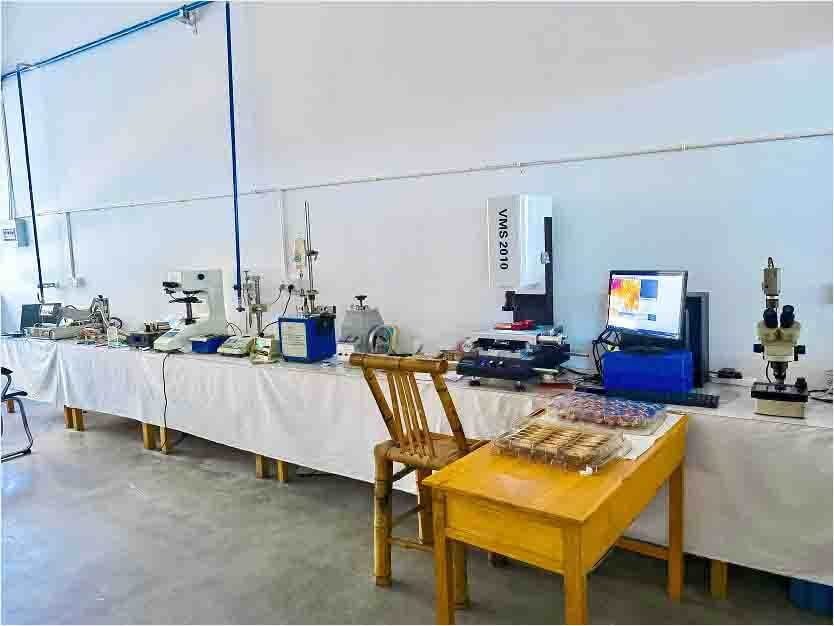
Quality Control (Testing)
- Masion conduct material inspections to ensure the partss correctness.
- Masion perform initial inspections on the first samples; production proceeds only if the dimensional inspection is passed, with adjustments made if necessary for non-compliance.
- Masion conduct sample inspections on the manufactured products to ensure compliance with the dimensional requirements specified in the drawings.
Application Area



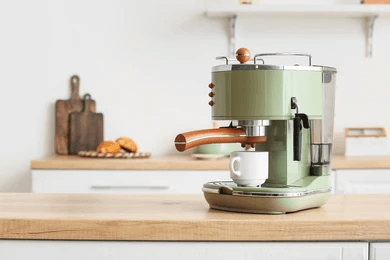

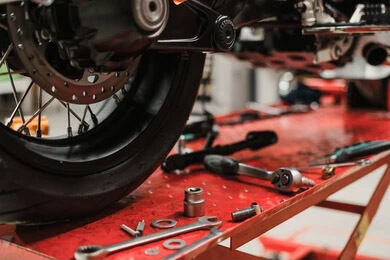



Swiss Lathe Parts FAQs
Swiss lathe parts are products manufactured using Swiss lathes through a series of complex machining processes such as milling, turning, drilling, tapping, knurling, engraving, grooving, and more. The Swiss lathe is a highly precise CNC lathe typically used for machining small, slender, and intricate parts, particularly cylindrical components with an outer diameter of less than 32mm. Notable characteristics of this lathe include its ability to perform cutting operations simultaneously on multiple axes, as well as its high level of automation and precision.
Common Swiss lathe parts include motor shafts, drive shafts, threaded shafts, slender shafts, electric toothbrush shafts, lock cores, slender valves, polyaxial pedicle screws, dental screws, ACL screws, and more.
Swiss lathe parts could be found in various applications industries, primarily where there is a demand for high precision and complexity. Here are some potential application areas:
Medical Industry:
Used in the production of medical equipment and devices that require extremely high precision and complex shapes. Examples include artificial joints, implants, surgical tools, and other medical instruments.
Aerospace Industry:
Employed for machining lightweight and highly precise components for aircraft and spacecraft. Commonly used in the manufacturing of complex aerospace parts like screws, valves, and sensors.
Automotive Industry:
Applied in the manufacturing of precision automotive parts such as engine components, transmission system elements, braking systems, and other crucial automotive components.
Electronics Industry:
Utilized for machining small electronic components such as connectors, switches, sensors, circuit boards, and conductive elements that demand high precision.
Watchmaking and Jewelry:
Originating from watchmaking, Swiss lathes are extensively used in crafting precision watch components and intricate jewelry pieces.
Optical Components:
Employed in the production of high-precision optical elements like lenses and mirrors for optical instruments.
Molds and Models:
Used in the manufacturing of injection molds, die-casting molds, and various types of models requiring intricate details.
Marine Components:
Applied in machining high-precision components for ship engines, hull structures, and marine equipment.
Industrial Valves and Bodies:
Used for machining complex industrial valves and bodies to ensure their sealing and durability in industrial applications.
Stage and Stage Equipment:
Utilized in the production of stage equipment, mechanical components, and structures for theatrical and event settings.
Swiss lathes are versatile and capable of machining a variety of materials. The specific type of material that can be machined depends on the design of the lathe, the cutting tools used, and the machining conditions. However, Swiss lathes are commonly used for machining materials such as:
Rare metals:
Tungsten: Military, aerospace industry
Molybdenum: military industry, aerospace industry
Metals:
Steel: Including various grades of stainless steel.
Aluminum: Commonly used in aerospace and automotive applications.
Brass: Often used for precision components and fittings.
Copper: Known for its electrical conductivity.
Nickel:Electronics, military and other industries.
Plastics:
Nylon: Widely used for its low friction and wear resistance.
Acetal (Delrin): Known for its high strength and stiffness.
Polyethylene and Polypropylene: Common thermoplastics used in various applications.
PEEK: Aerospace, electronics and other industries
PVC: Electronics, household appliances and other industries
PS: Electronics, automotive, etc
POM: Electronics, communications and other industries
Alloys:
Titanium: Often used in aerospace and medical applications for its strength-to-weight ratio.
Inconel: A high-temperature alloy used in aerospace and chemical processing.
Hastelloy: Known for its corrosion resistance in harsh environments.
Exotic Materials:
Ceramics: In some cases, Swiss lathes equipped with special tools can machine ceramic materials.
Composites: Some lathes can handle composite materials used in aerospace and other industries.
Swiss lathes are versatile and capable of machining a variety of materials. The specific type of material that can be machined depends on the design of the lathe, the cutting tools used, and the machining conditions. However, Swiss lathes are commonly used for machining materials such as:
Rare metals:
Tungsten: Military, aerospace industry
Molybdenum: military industry, aerospace industry
Metals:
Steel: Including various grades of stainless steel.
Aluminum: Commonly used in aerospace and automotive applications.
Brass: Often used for precision components and fittings.
Copper: Known for its electrical conductivity.
Nickel:Electronics, military and other industries.
Plastics:
Nylon: Widely used for its low friction and wear resistance.
Acetal (Delrin): Known for its high strength and stiffness.
Polyethylene and Polypropylene: Common thermoplastics used in various applications.
PEEK: Aerospace, electronics and other industries
PVC: Electronics, household appliances and other industries
PS: Electronics, automotive, etc
POM: Electronics, communications and other industries
Alloys:
Titanium: Often used in aerospace and medical applications for its strength-to-weight ratio.
Inconel: A high-temperature alloy used in aerospace and chemical processing.
Hastelloy: Known for its corrosion resistance in harsh environments.
Exotic Materials:
Ceramics: In some cases, Swiss lathes equipped with special tools can machine ceramic materials.
Composites: Some lathes can handle composite materials used in aerospace and other industries.
The Swiss lathe combines the characteristics of a lathe and a milling machine, aiming for rapid machining and increased efficiency. Due to its structural design, Swiss lathes are generally suitable for producing small cylindrical parts with dimensions below 32mm, especially those requiring high-precision machining.
Diameter Below 32mm: The primary form of machining for Swiss lathes involves tool layout to enhance processing efficiency and precision, particularly for diameters less than 32mm. However, if the budget allows, tool arrangement might become a limiting factor.
Length Below 50mm: Swiss lathes utilize guide bushing feeding for Z-axis movement, making them suitable for products with lengths below 50mm. Longer products can be inconvenient due to guide bushing feeding limitations and part ejection constraints.
Complex Parts: Swiss lathes are particularly well-suited for products with multiple and intricate machining processes. They can perform complex operations such as turning, milling, boring, and drilling in a single setup, improving overall processing efficiency.
High Volume Production: Swiss lathes excel in high-efficiency machining, making them most suitable for large production quantities. It is recommended to have a substantial volume, with a starting point of at least 100,000 pieces per month. If the quantity is small, frequent tool changes and setup adjustments may negate the advantages of the high efficiency of Swiss lathes, making traditional CNC machining centers a more viable option.
In summary, the versatility of Swiss lathes makes them ideal for small cylindrical parts with dimensions below 32mm, especially when the parts are short in length, have complex machining requirements, and are produced in high volumes.
A Swiss-type lathe is designed for the direct machining of long bar stock, with the workpiece moving along the Z-axis during the machining process. If machining larger components, the bar stock would be substantial, making the cutting process cumbersome. The centrifugal force generated during rotation would also be significant, and the spindle would need to be much larger than the bar stock, resulting in challenging and awkward conditions.
The Swiss-type lathe is particularly well-suited for processing small components due to several distinctive features and advantages:
Multi-Axis Control: Swiss-type lathes typically feature a multi-axis control system, including the main spindle, main eccentric, auxiliary axes, etc. This enables simultaneous cutting in multiple directions, facilitating the efficient processing of complex geometries in small parts.
Concentric Design of Main Spindle and Main Eccentric: The Swiss-type lathe employs a concentric design, allowing the material to rotate along the main spindle while the cutting tool moves along the main eccentric. This structural design contributes to stable and precise cutting, meeting the high precision requirements of small-sized components.
Automatic Loading System: Swiss-type lathes are often equipped with automatic loading systems, efficiently handling small-sized raw materials. This reduces manual intervention, enhancing production efficiency.
Tool Configuration: The tool configuration of Swiss-type lathes is designed to be more compact, accommodating multiple tools in limited space. This is advantageous for the fine cutting and multi-process machining of small parts.
High-Speed Machining: Swiss-type lathes typically have high-speed machining capabilities, crucial for the rapid production of small components. High-speed machining helps reduce production cycles, improving processing efficiency.
Bed Rigidity: Swiss-type lathes are constructed with a robust bed, reducing vibrations and ensuring high-precision cutting. This is particularly important for small parts as they are more susceptible to the effects of vibration.
Compact Workspace: The compact design of Swiss-type lathes allows them to adapt to small workspaces, making them easier to deploy in limited manufacturing environments.
In summary, the superior characteristics of Swiss-type lathes in terms of structure, control, automation, and cutting capabilities make them an ideal choice for processing small components, meeting the demands of high precision and efficient production.
Yes, Swiss-type lathes are typically capable of handling highly complex geometries. The design of these lathes aims to achieve high precision and multi-axis control, enabling them to perform various cutting operations on a single machine. Here are some features that make Swiss-type lathes suitable for processing complex geometries:
Multi-Axis Control: Swiss-type lathes are usually equipped with multiple control axes, including the main spindle, main eccentric, auxiliary axes, etc. These axes can move independently, providing flexibility in multiple directions and aiding in the machining of complex geometries.
Concentric Design: Swiss-type lathes employ a concentric design, allowing the workpiece to rotate along the main spindle while the cutting tool moves along the main eccentric. This design helps maintain concentricity of the workpiece, accommodating the cutting needs of complex shapes.
Fine Cutting Tools: Swiss-type lathes typically come with very fine and flexible cutting tools capable of accurately handling small sizes and intricate shapes of components.
Main Eccentric Control: Control over the main eccentric enables the tool to move in various directions, including radial and axial movements, facilitating the machining of more complex cutting profiles.
Automatic Tool Changing System: Swiss-type lathes are often equipped with an automatic tool changing system that can rapidly swap different shapes and sizes of cutting tools to meet the requirements of different machining processes.
High Automation: Highly automated control systems allow Swiss-type lathes to perform multiple operations on a single machine, including turning, milling, drilling, etc., enabling comprehensive processing of complex components.
In summary, with these features, Swiss-type lathes excel in handling complex geometries, small-sized parts, and high precision requirements. As a result, they find widespread application in industries such as watchmaking, medical devices, aerospace, and others.
Swiss lathe parts offer several advantages when it comes to high-volume production, especially for small and precision components. Here are some key advantages:
High Precision and Accuracy:
Swiss lathes are renowned for their exceptional precision. The machine’s design and multiple axes allow for simultaneous machining from multiple angles, ensuring high accuracy in the production of intricate and small parts.
Reduced Material Waste:
The design of Swiss lathes allows for the efficient use of raw materials. The machines are capable of machining close to the material guide bushing, minimizing the amount of wasted material, which is crucial for cost-effectiveness in high-volume production.
Complex Geometries and Tight Tolerances:
Swiss lathes excel in handling complex geometries and tight tolerances. This makes them suitable for the production of intricate components that require high precision, such as those found in the medical, aerospace, and electronics industries.
Simultaneous Machining Operations:
Swiss lathes can perform multiple machining operations simultaneously. This reduces cycle times and increases productivity, making them well-suited for high-volume production where efficiency is crucial.
High Speeds and Feeds:
Swiss lathes are capable of high-speed machining, allowing for faster production rates. The combination of rapid cutting speeds and feeds contributes to shorter cycle times, making them efficient for large-scale manufacturing.
Automatic Bar Feeding:
Swiss lathes often come equipped with automatic bar feeding systems. This allows for continuous and uninterrupted production by automatically feeding new material into the machine, reducing downtime and increasing overall efficiency.
Consistent Quality:
The automated nature of Swiss lathe machining, along with advanced control systems, contributes to consistent part quality. This is crucial for meeting stringent quality standards in high-volume production.
Minimized Secondary Operations:
Swiss lathes are capable of performing multiple operations in a single setup. This reduces the need for additional secondary operations, such as milling or drilling, streamlining the production process and reducing overall production time.
Scalability:
Swiss lathe setups are scalable, meaning they can be configured to handle varying production volumes. Whether producing small batches or large quantities, the machines can be adapted to meet specific manufacturing requirements.
Cost-Effective for Small Parts:
While Swiss lathe setup costs may be higher, they are often more cost-effective for the production of small, intricate parts over the long run, especially in high volumes. The efficiency gains and reduced material waste contribute to overall cost savings.
Yes, selecting Swiss lathe parts suppliers requires careful consideration to ensure that you are getting high-quality components that meet your specific needs. Here are some specific considerations to keep in mind when choosing Swiss lathe parts suppliers:
Expertise and Experience:
Look for suppliers with a proven track record and extensive experience in manufacturing Swiss lathe parts. An experienced supplier is more likely to understand the complexities of Swiss machining and deliver quality components.
Precision and Quality Standards:
Ensure that the supplier adheres to high precision and quality standards. Swiss machining is known for its accuracy, and your supplier should have quality control measures in place to meet these standards.
Certificate
Before selecting a supplier, it is advisable to check whether the supplier possesses certificates such as the ISO Quality Management Certification. This allows us to quickly assess their level of experience and commitment to quality management.
Certifications can be an assurance of their adherence to industry standards.
Materials Expertise:
Verify that the supplier has expertise in working with a variety of materials. Depending on your specific requirements, the supplier should be capable of machining different metals, alloys, plastics, or other materials commonly used in Swiss lathe parts.
Customization Capability:
Evaluate the supplier’s ability to provide customized solutions. Swiss lathe parts often require precision and customization based on unique specifications, so a supplier that can accommodate these requirements is crucial.
Production Capacity:
Consider the production capacity of the supplier. Ensure they can handle the volume of parts you require within your desired timeframe. A reliable supplier should have the capacity to scale production as needed.
Technology and Equipment:
Check the supplier’s machining technology and equipment. Up-to-date machinery and technology contribute to efficient and accurate manufacturing processes. Ensure that the supplier is using modern Swiss machining equipment.
Quality Control Processes:
Understanding the supplier’s quality management process is crucial, including rigorous quality checks at various stages such as material inspection, initial sample testing, in-process production checks, random sampling inspections, and comprehensive post-processing assessments. It is important to ascertain whether the supplier employs advanced CMM inspection equipment and is equipped with other relevant testing tools to ensure the conformity of product dimensions.
References and Reviews:
Customer or friends recommendations are the best way to go. If you have friends or clients who have collaborated with this supplier, you can inquire about their specific experiences with the supplier.This can provide insights into the supplier’s reliability, communication, and overall satisfaction of their clients.
Logistics and Communication:
Consider the supplier’s location how do they communicate,if they have the sales who could communicate the issues quickly and better. A supplier with clear communication channels and efficient logistics can contribute to a smoother collaboration.
Taking the time to thoroughly evaluate potential Swiss lathe parts suppliers based on these considerations can help you make an informed decision and ensure the success of your manufacturing projects.
Free Sample
Explore Other Products
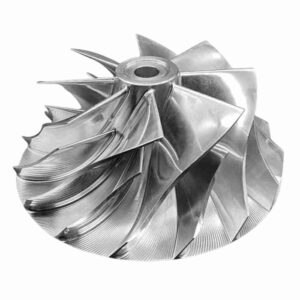
Aluminum Boat Impeller
Five-axis simultaneous complex parts machining, aluminum boat impeller, watercraft impeller, compressor impeller, turbocharger impeller,and another different 5-axis CNC parts etc.
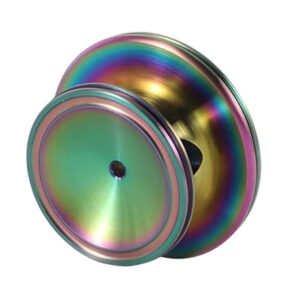
CNC Turning
Stainless Steel stethoscope Chestpiece and another different CNC turning Parts.
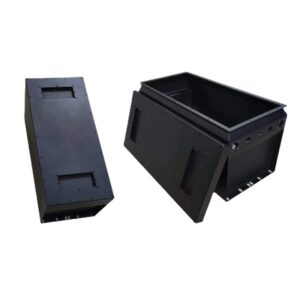
Sheet Metal Fabrication
New Energy Battery Casing and other differentSheet Metal Fabrication parts such as Housing, Case,Enclosure, etc.