Turning Brass Parts
Turning Brass Parts
Turning brass parts manufacturer in China.
MOQ Starts from 1pcs.
As a specialized turning brass parts manufacturer, Masion provides high-quality custom different turning brass parts services to customers with outstanding production advantages, advanced technological capabilities, and professional solution offerings.

Masion Capability
High Capacity, Proper Price
10000pcs production capacity per month make the price lower.
Free Samples, Low MOQ
1pcs MOQ make you order flexibly with one free sample for you testing.
Certified Factory, Guaranteed Quality
ISO9001:2008 and strictly 100% inspection guarantee quality and CMM inspection equipment.
High precision, Good Surface
With 0.002mm tolerance and with different surface finishing and different materials.
Our Products




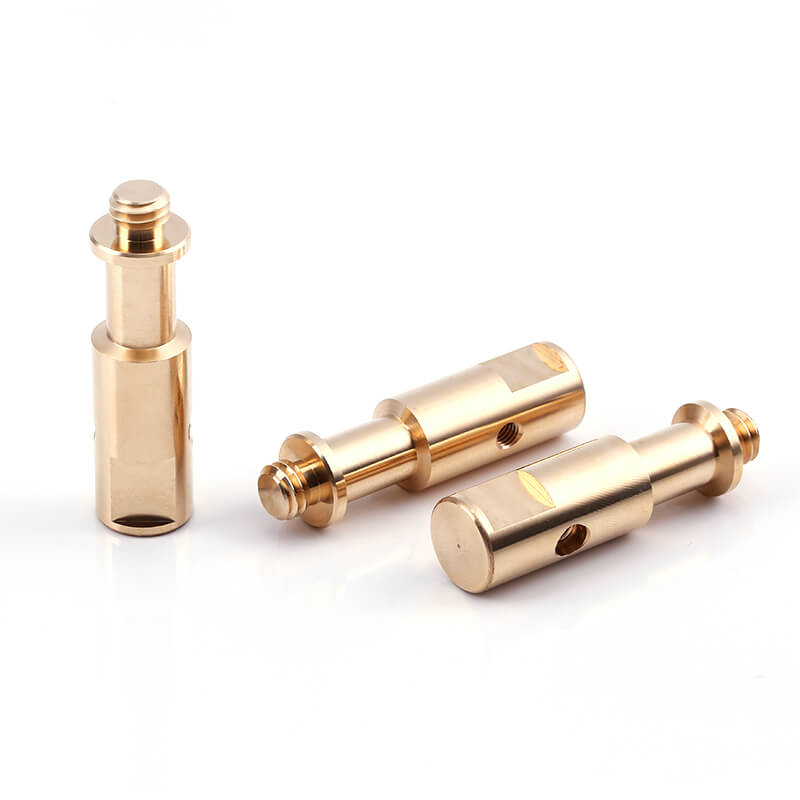
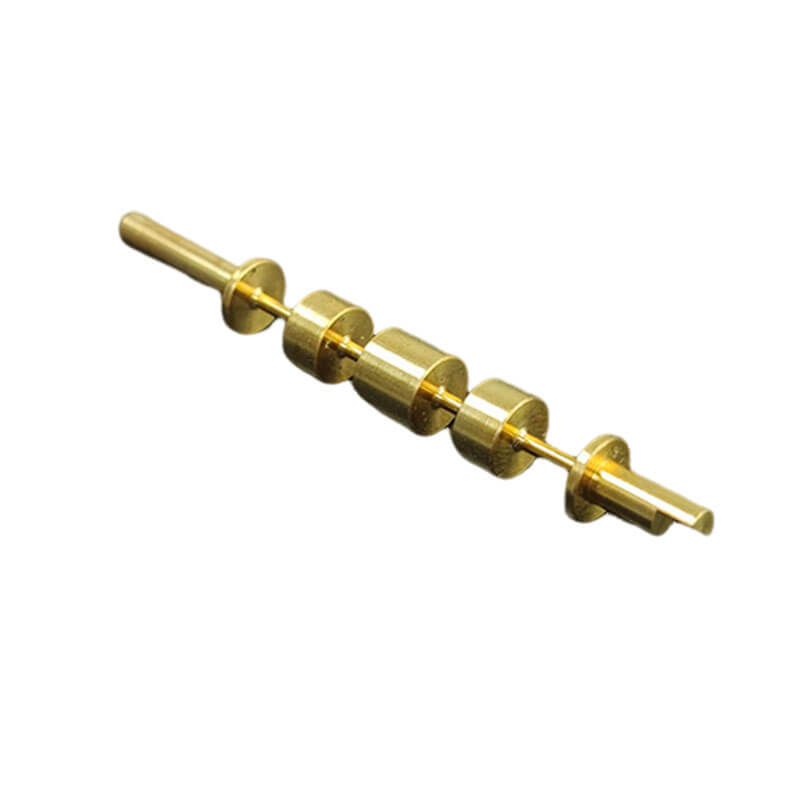

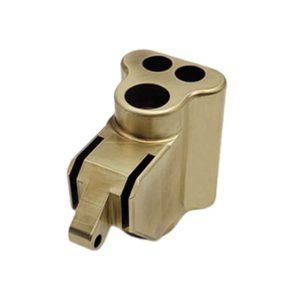
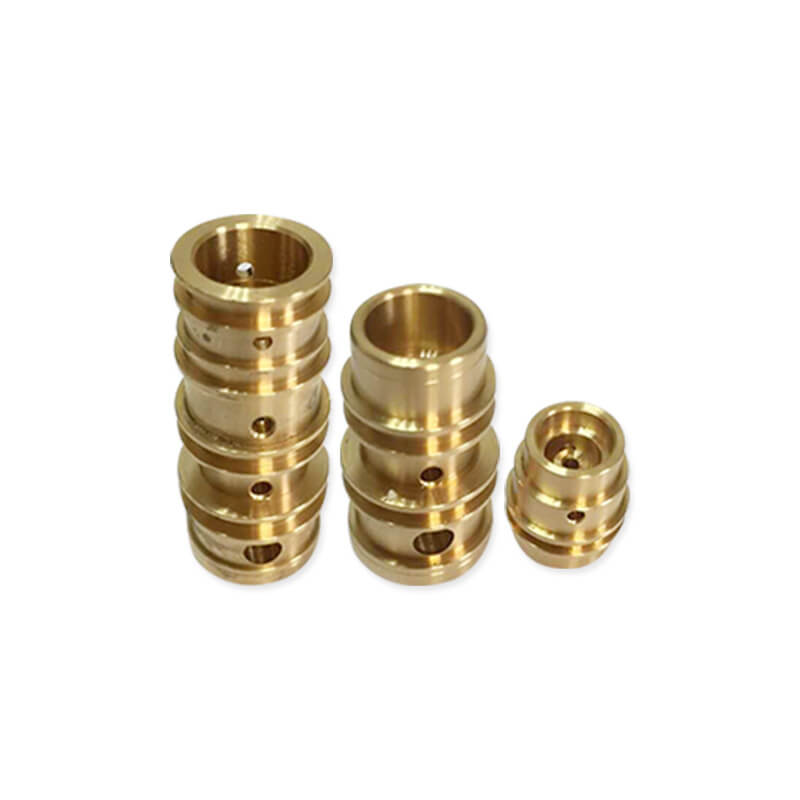
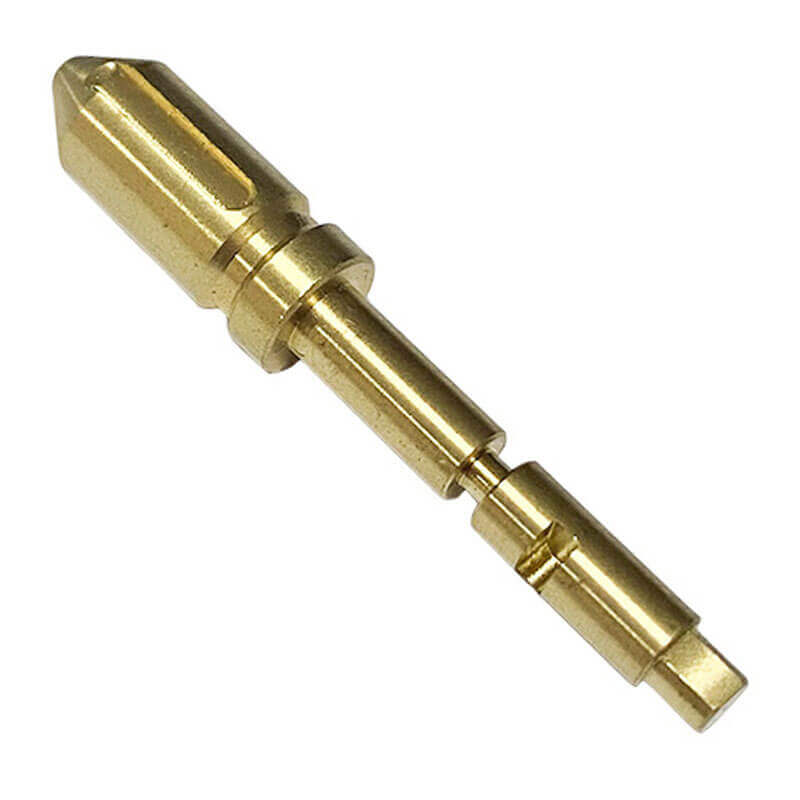


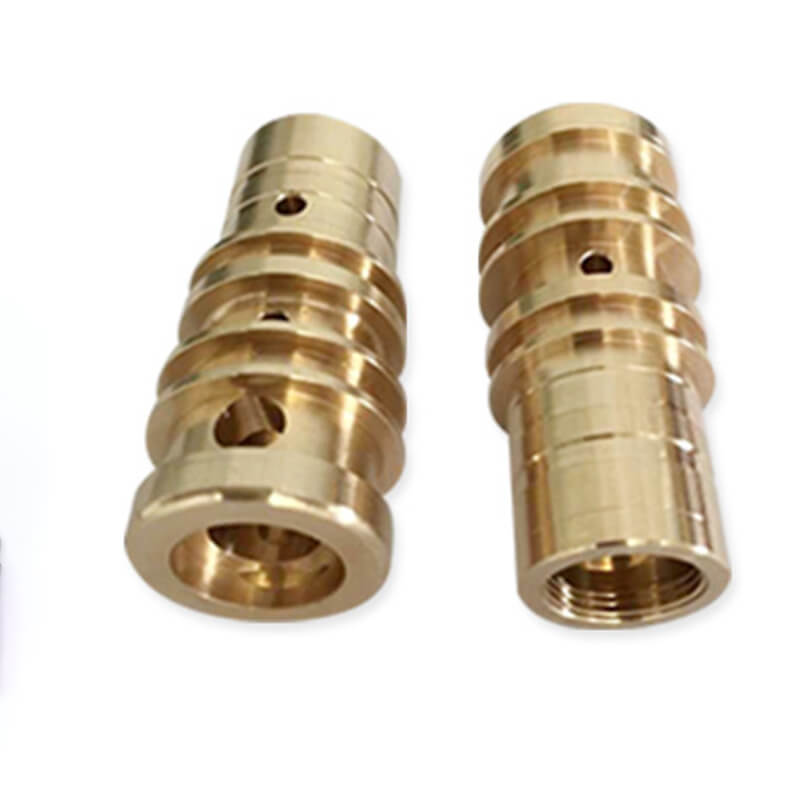
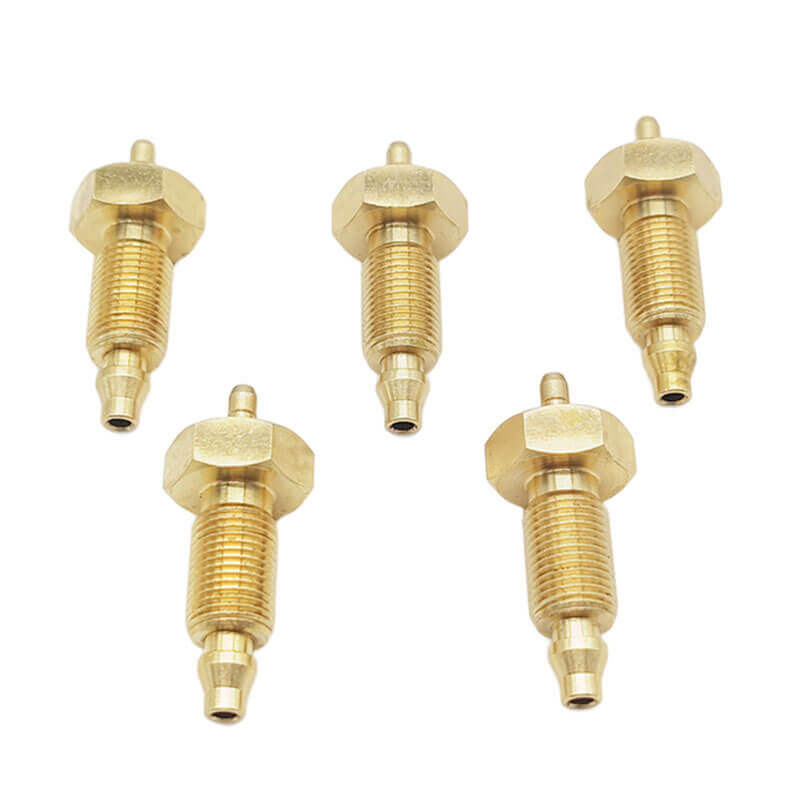



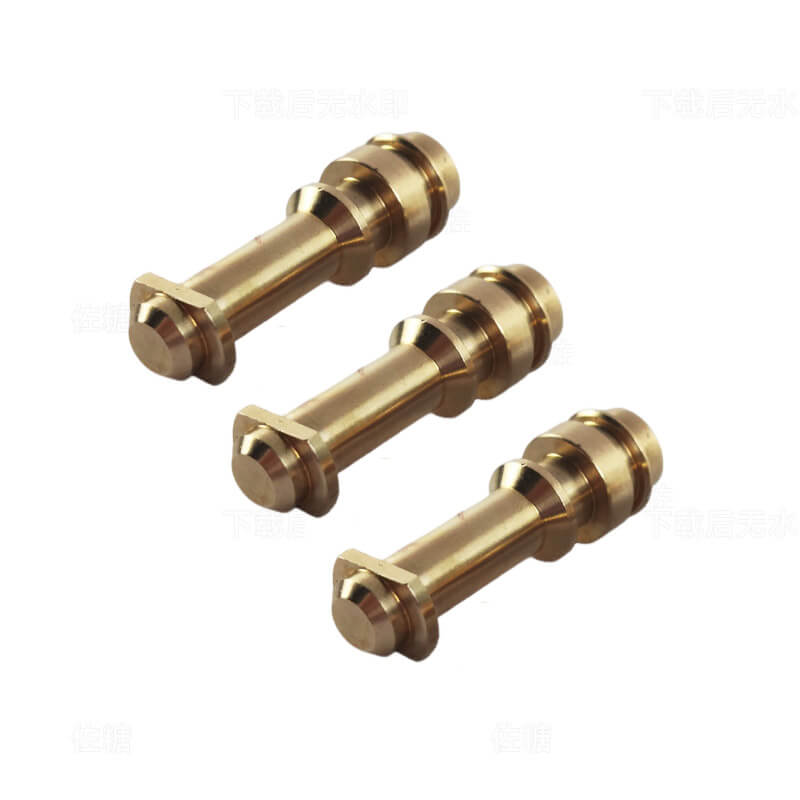


What Sets Us Apart

Strong Experience
With 16 years of turning brass parts machining expertise, we focus on high-quality, customized solutions for different turning brass parts demands.

Advanced Imported Machine
30 sets precision imported Japanese Citizen Swiss CNC Lathe with mature and stable manufacturing processes with technical machinist and engineer.

Surprised Price
Stockpiling a large amount of conventional materials and having a mature production process can reduce the overall price by 5%.
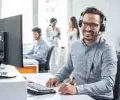
24/7 Engineering Support
Masion is specializing in offering 24/7 engineering support, design services, cost reduction, quality assurance, and smooth product transition sun paralleled excellence etc.
Turning brass parts Manufacturing Process

Raw Material
During the brass materials preparation stage, it is typically required for the materials to have good smoothness and high concentricity, facilitating smooth usage on the automatic lathe feeding rack. Additionally, we offer a regular product material inventory to address any issues related to insufficient delivery lead times.
Swiss lathe turning brass parts Machining
- Milling
- Turning
- Drilling
- Threading
- Cutting
- Counter Sinking
- Boring
- Knurling
- Grooving
- Taper
- Turning
- Tapping
- Reaming
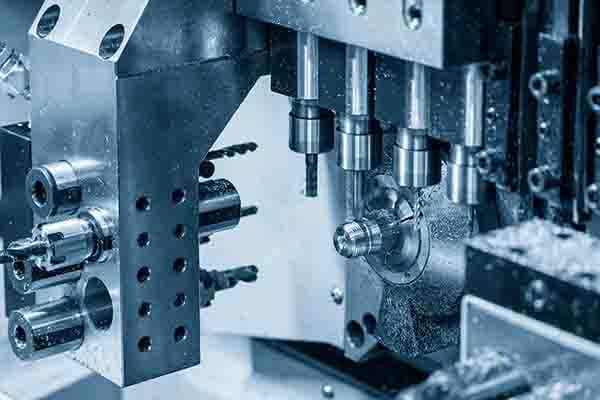
Packing
- For turning brass parts. with extremely high requirements, we pack the part one by one with PC bag, or blister bag etc.
- For turning brass parts. with moderate requirements, we also perform packing the bag as clients need.

- For turning brass parts. with no packaging requirements, we will arrange the products neatly and separate them with cardboard.

Quality Control (Testing)
- Masion conduct material inspections to ensure the partss correctness.
- Masion perform initial inspections on the first samples; production proceeds only if the dimensional inspection is passed, with adjustments made if necessary for non-compliance.
- Masion conduct sample inspections on the manufactured products to ensure compliance with the dimensional requirements specified in the drawings
Application Area






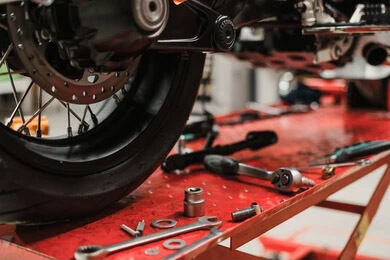

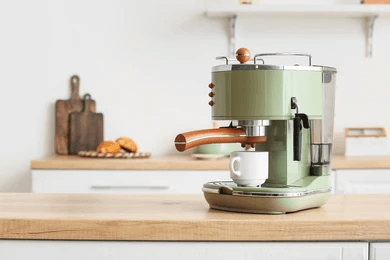
Turning brass parts FAQs
Swiss lathe CNC turning brass parts is a highly precise CNC turning method, where “Swiss-type” refers to Swiss CNC lathes, also known as Swiss-type turning centers. These lathes were initially invented by the Swiss, hence the name.
The Swiss CNC lathe differs significantly from traditional lathes in its unique working principle. On a Swiss-type lathe, the workpiece is fed through the spindle, while the cutting tool rotates around the workpiece. This design makes Swiss-type lathes particularly suitable for machining small-diameter, elongated workpieces, as it allows multiple operations to be performed on a single machine, reducing tool change and setup times.
Due to its high level of automation and precision control, Swiss lathe CNC turning brass parts is commonly applied in fields that require high precision and efficiency, such as medical device manufacturing, electronic components production, watchmaking, and precision instrument manufacturing.
High Precision: Swiss CNC lathes are equipped with high-precision CNC systems, enabling extremely accurate turning of brass materials to meet the requirements of complex components.
High Efficiency: Swiss-type lathes are highly efficient, especially for small-diameter, elongated workpieces. The multi-station design allows multiple operations to be completed in a single clamping, improving production efficiency, especially in large-volume production.
Multifunctional Operations: Swiss-type lathes typically have multiple workstations, allowing simultaneous turning, drilling, cutting, and other operations, achieving multifunctional machining.
Suitability for Small Diameter Workpieces: Swiss-type lathes excel at machining small-diameter workpieces, providing versatility for processing smaller brass materials.
Reduced Scrap: Swiss-type lathes efficiently utilize raw materials, reducing waste production and enhancing resource utilization efficiency.
Reduced Scrap: Swiss-type lathes efficiently utilize raw materials, reducing waste production and enhancing resource utilization efficiency.
Applicability to Complex Parts: The design of Swiss-type lathes allows for the machining of complex part geometries, including internal and external profiles, grooves, threads, and more.
Reduced Manual Intervention: High automation levels reduce the need for manual operations, decreasing the impact of human factors on the production process.
Working Principle:
Conventional Lathe: The workpiece rotates on the spindle, and the cutting tool performs linear cutting operations on the rotating workpiece. This is a common turning method suitable for general machining needs.
Swiss CNC lathe: The workpiece remains stationary relative to the spindle, and the cutting tool rotates around the axis of the workpiece. This design is well-suited for high-precision machining of small-diameter, elongated workpieces.
Application Range:
Conventional Lathe: Suitable for general turning operations, effective for larger diameter workpieces, but may have limitations in high-precision machining of small-diameter workpieces.
Swiss CNC lathe: Mainly used for machining small-diameter, elongated workpieces, particularly effective for high-precision and complex geometries such as threads and grooves.
Automation Level:
Conventional Lathe: Generally has a basic level of automation, requiring operator assistance and monitoring.
Swiss CNC lathe: Features a higher level of automation, capable of automated operations through CNC systems, reducing the need for manual intervention and improving production efficiency.
Production Efficiency:
Conventional Lathe: Suitable for general production requirements, but may be less efficient in handling large quantities of small-diameter parts compared to Swiss-type lathes.
Swiss CNC lathe: Excels in the production of small-diameter parts, efficiently completing multiple operations in a single clamping, reducing setup times.
Tool Change Frequency:
Conventional Lathe: Requires relatively frequent tool changes, especially when performing different types of operations.
Swiss CNC Lathe: Due to its multi-station design, reduces the frequency of tool changes, enhancing machining efficiency.
The processing size range of a Swiss CNC lathe depends on the specific machine model and manufacturer specifications. In general:
Maximum Size: The maximum processing size is typically determined by the machine’s travel (axial movement range), spindle speed, and other design parameters. For brass, the maximum processing size may be in the range of 32mm in diameter.
Minimum Size: The minimum size is often constrained by the precision of the cutting tools and the lathe. For micro-parts machining, Swiss CNC lathes can achieve extremely fine machining, with sizes as small as 0.3mm in diameter.
Ensuring the quality of Swiss CNC lathe turning brass parts involves considerations across various aspects, including appropriate cutting parameters, tool selection, machine maintenance, and quality control. Here are some recommendations:
Choose Suitable Cutting Tools: Select cutting tools based on the machining task, including tool material, cutting edge geometry, and tool coatings. Ensure the quality and condition of the tools.
Control Cutting Parameters: Optimize cutting speed, feed rate, and cutting depth parameters to enhance efficiency while maintaining the surface quality of the parts during the brass parts turning process.
Use Appropriate Coolants: Select coolants compatible with brass to ensure effective cooling, preventing overheating that could damage tools and workpieces.
Regularly Check and Replace Tools: Monitor tool wear and replace heavily worn tools promptly to maintain cutting quality and dimensional stability.
Avoid Cutting Vibrations: Employ suitable cutting strategies and tool paths to minimize cutting vibrations, preserving the surface quality of the turning brass parts.
Maintain Machine Stability: Regularly inspect and maintain the Swiss CNC lathe to ensure the stability of the machine structure, minimizing the impact of mechanical vibrations on machining quality.
Implement Quality Control: Introduce quality control procedures, including the use of measuring instruments for part size measurements, surface roughness testing, etc., to ensure turning brass parts meet specifications.
Conduct Initial Sample Testing: Perform initial sample testing before full-scale production to ensure the accuracy of machine settings and cutting parameters, making adjustments as needed.
Train Operators: Ensure operators have sufficient skills and knowledge to correctly set up and operate the Swiss CNC lathe, ensuring consistency and quality in production.
Continuous Improvement: Regularly assess the machining process, collect and analyze data, identify improvement opportunities, and ensure the stability and efficiency of the production process.
By considering these factors comprehensively, the quality of Swiss CNC lathe turning brass parts can be effectively ensured.
The production cycle of Swiss CNC lathe turning brass parts depends on various factors, including the complexity of the parts, size, production quantity, machine performance, cutting parameters, and the degree of automation in the production process. Here are some factors influencing the production cycle:
Part Complexity: Complex parts generally require more processing steps and time, leading to a longer production cycle.
Size and Quantity: Larger parts may require longer processing times. Additionally, producing large quantities of parts is often more efficient than small batches.
Machine Performance: The use of high-performance Swiss CNC lathes can increase production efficiency and shorten the production cycle.
Cutting Parameters: Optimized cutting parameters can increase processing speed, reducing the production cycle while maintaining part quality.
Automation in the Production Process: Higher levels of automation in the production process tend to be more efficient, potentially shortening the production cycle. This may involve automatic tool changes, measurements, and other automation technologies.
Process Preparation Time: Includes the design and manufacturing of part fixtures, tool selection and setup, and initial sample testing.
Quality Control Testing Time: Strict quality control testing during production can increase the production cycle.
Therefore, we would need specific details about the turning brass parts you need, such as drawings, to provide a more accurate estimation of the production cycle. Please provide the drawings, and we can offer you a satisfactory production timeline.
Preventing burrs during Swiss CNC turning brass parts involves several key measures: Tool Wear Inspection: Regularly check the wear of cutting tools on the Swiss-type CNC lathe. Worn tools are more likely to produce burrs, so timely replacement or reconditioning of tools is crucial. Adjustment of Back Rake Angle and Side Rake Angle: Increase the back rake angle and side rake angle appropriately to ensure proper cutting edge transition. Excessive rake angles can lead to cutting edge damage and burr formation. Tool Polishing: Use oilstone to polish cutting tools, maintaining the smoothness of the tool surface, which helps reduce burr formation. Tool Installation Position: Ensure that the cutting tool is installed on the spindle centerline to avoid uneven cutting due to deviation from the centerline, which can lead to burr formation. Comprehensive Chamfering: Perform comprehensive chamfering on the workpiece to avoid sharp edges and corners, reducing the formation of burrs. The combined application of these measures can effectively reduce the likelihood of burr formation during Swiss CNC lathe turning brass parts, ensuring a smoother surface quality of the machined parts.
The feed rate for CNC Swiss lathe turning brass parts is determined based on several factors, and the following guidelines can be considered: Depth of Cut (DOC): Typically, the depth of cut for copper turning is in the range of 3-4 millimeters.Feed Rate (F): A recommended feed rate for copper turning is around 0.25 mm/rev.Spindle Speed (RPM): The spindle speed depends on the diameter of the workpiece, with higher speeds generally resulting in better surface finish. The speed is determined based on the material of the workpiece and the cutting tool. Higher speeds are suitable for better surface finish, but a balance must be maintained to avoid excessive tool wear.Tool Engagement: The amount of tool engagement (cutting depth) affects the cutting speed. Higher tool engagement may lead to higher cutting speeds.It’s important to consider the stiffness of the machine, tool properties, and material characteristics when determining the optimal feed rate. Experimentation and adjustments may be necessary to find the most suitable settings for your specific CNC Swiss lathe turning brass parts.
Free Sample
Explore Other Products

Automatic Lathe
Test Pin and other Automatic Lathing Machining Parts such as screws,copper pillar, knob, etc.

CNC Milling
CNC Milling Aluminum different automobile hub, and different 3-axis, 4-axis,5 axis CNC machining parts.

3D pringting
Masionprovides a wide range of 3D printing services, including SLA 3D printing (Stereolithography), SLS 3D printing (Selective Laser Sintering), MJF (Multi Jet Fusion), and DLMS (Direct Metal Laser Sintering).