Precision Screw Machine Products: Top Processes and Industry Leaders
In this age, no one can ignore the position of screw machine production industrial manufacturing because of their incredible accuracy and precision. These remarkable machines churn out components smaller than your fingernail – with tolerances in microns. Derived from the Swiss watch industry during the 19th century, these have been transformed into sophisticated CNC systems that drive the modern manufacture.
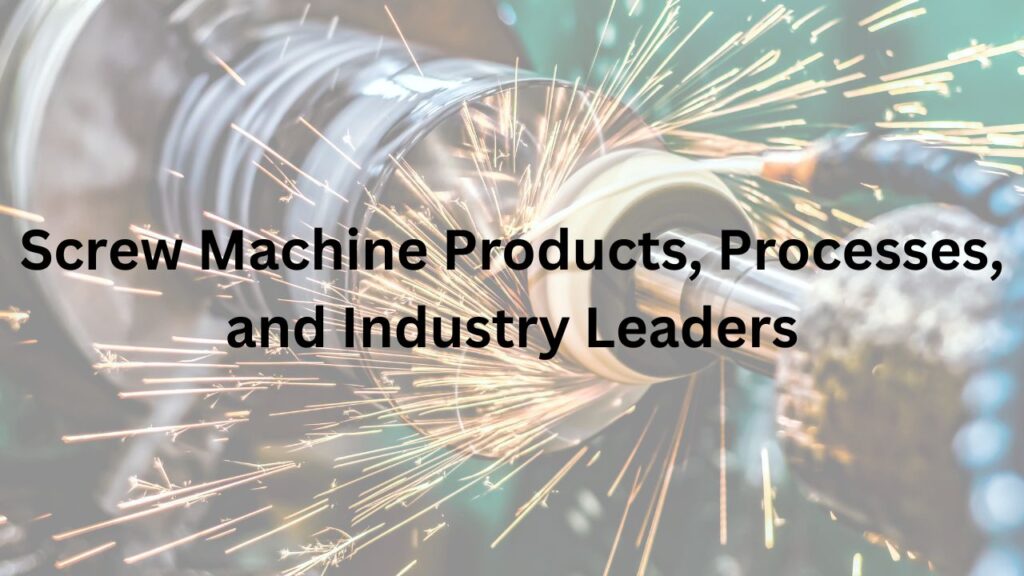
The global swiss screw machining industry has an increasing market value as precision engineered components are being used more than ever, and is expected to continue the steady growth through 2025. Lets’ explore more about screw machine processes, products, leading manufacturers, and more. Keep reading!
Types of Swiss Screw Machines
Basic Definition and Principles
Swiss type lathes, or swiss screw machines, are fundamentally different from regular CNC lathes. The key difference is that their support of the workpiece is different in a unique way. A chuck retains the material when using traditional lathes while swiss machines use a guide bushing which gets the material close to the cutting tool to support the material. With a virtually zero deflection design, this design allows for extreme precision on long, small diameter parts.
Differences from Traditional CNC Machines
Various distinctions lies in between the modern as well as traditional machines. The guide bushing support system provides stability for long and slender parts, which guarantees precision. The multiple tool positions working simultaneously and faster production times make this system a winner. While small parts are often a challenge for traditional CNC machines, Swiss screw machines excel at high-precision turning for long, thin parts.
With swiss screw machining provides super surface finish on screwed components. This is the result of the guide bushing maintaining ground continuously which reduces the tool deflection. By contrast, such tasks can be problematic for traditional CNC machines, particularly with delicate or complex parts. Swiss screw machines are the right choice when you’re looking to raise production rates on small components.
Key Components
Main Spindle: It is important that the main spindle holds and rotates the workpiece. To achieve precise machining, you need to ensure that it becomes smooth. The quality and finish of the final product are largely determined by this component directly.
Guide Bushing: The continuous support for the material during machining is provided by the guide bushing. It helps prevent deflection and maintain stability and you benefit from it. It is necessary for keeping your work with tight tolerances.
Multiple Tool Stations: Efficiency is enhanced via multiple tool stations, which facilitate simultaneous operations. That allows you to perform various tasks such as turning, drilling, and milling with little need of changing tools frequently. This greatly cuts down on production time and production productivity.
Sub-Spindle: The sub spindle is used to run back working operations in modern Swiss machines. This feature can be used to machine the back side of parts without moving the part. This further improves accuracy and reduces setup time.
CNC Control System: With the CNC control system, you can program and automate the machine with precision. This allows you to set specific parameters for each operation so it remains consistent and repeatable. High production rates and complex geometries can be achieved using this system.
Swiss Screw Machine Processes
Turning Operations:
OD Turning: This can be done by OD turning the outer diameter from the workpiece. This is a necessary step to realize the ideal dimensions on your cylindrical part. This step is critical for part functionality, so you need precision here.
ID Boring: This technique is called ID boring and involves the formation of internal cavities or holes. This method is how you use this technique to get exact dimensions for fittings and assemblies. If properly executed, it enhances the final product while it eliminates defects and product damages.
Face Turning: Face turning removes material from the face of the part. This technique is used to obtain flat surface or alter thickness. This is a necessary step in order to align correctly in subsequent operations.
Grooving: The part gets grooved cuts to make narrow channels on its surface. This allows you to add features that assist with assembly or improve the part functionality. It also provides better aesthetics in the design.
Drilling and Hole-Making:
Center Drilling: The center drilling creates small holes to guide large drills. The following technique works well for accurate drill placement. This helps to ensure the main drilling operation goes smoothly.
Through-Hole Drilling: Drill through the workpiece completely through hole drilling. For applications that need holes through the entire part, this method is invaluable. You have both precision and depth control at the same time.
Reaming: Reaming finishes holes to exact dimensions. This process is then applied to provide good surface finish and obtain accurate diameters. This is an important step to making sure assemblies fit and function properly.
Boring: Boring enlarges existing holes to polished perfection. This technique is used to fine tune dimensions after the first drilling. It is necessary for achieving precise tolerances.
Please note for all of the above processes the torelance you could add +-0.01mm, machining bigger size is up to 38mm.
Threading Operations:
External Threading: This type of threading cuts the threads on the outer surface of the part. This is the process that you follow for components that need fasteners or fittings. The correct function relies on accuracy in threading.
Internal Threading: Into a drilled hole, internal threading makes threads within the hole. This is crucial in order to ensure screws and bolts can be properly inserted. With precise internal threads, you can enhance the assembly process.
Thread Whirling: For threading long and slender components, thread whirling is ideal. This advanced technique allows you to produce high quality threads efficiently. Suitable for applications requiring strong, reliable fasteners.
Thread Rolling: The thread rolling forms threads without material removal. This method increases material integrity, creating stronger threads. Also, it is a very efficient process and minimizes waste.
Milling Capabilities:
End Milling: In end milling, the cutter is arranged to rotate and the material is removed from the workpiece. This is also how you use this technique to create flat surfaces or complex profiles. End Finishing by milling gives better part quality by increasing precision.
Side Milling: Side milling cuts the side of a workpiece. However, this operation is required to produce flat surfaces or grooves along the part’s length. Its versatility in various machining applications benefits you.
Cross Drilling: Cross Drilling drills perpendicular to main axis of the workpiece. This is a process you use to add functionality where features intersect other operations. Cross drilling accuracy is critical for part assembly.
Polygon Milling: Polygon milling involves forming multi-sided shapes on the workpiece. This technique is applied to create unique geometries for specific applications. It adds to design flexibility and part functionality.
Advanced Processes
Simultaneous 5-Axis Machining: This capability enables you to machine complex geometries in a single setup. This means a more efficient production process with less setup time, and more accurate results.
B-Axis Tool Positioning: The B axis tool positioning gives the flexibility of movement of the tool. Multi directional operations allow for enhanced machining capabilities. It also lets for more complex designs and precision.
Multiple Tool Synchronization: This process increases productivity by allowing two or more tools doing work at the same time on a part. It is ideal for high-volume production and you maximize efficiency and reduce cycle times.
Back Working Operations: The sub spindle allows you to complete additional operations on the backside of the part. This capability provides you with the option of saving time and convenient setup which lead to improved productivity and accuracy in your machining processes.
Quality Control Measures
In Swiss machining, quality control is key for getting consistent and high-precision parts. To ensure the highest standards, you can implement several methods:
In-process Gauging: Part dimensions are continuously monitored during machining. This real time tracking is able to identify deviations in real time so that you can make quick corrections.
Statistical Process Control (SPC): This entails monitoring and controlling production processes using statistical methods. It allows you to analyze variations and keep performance levels at an optimum level.
First Article Inspection: Inspect the first part produced thoroughly. It allows you to confirm quality and move to larger production runs.
Continuous Monitoring Systems: Use systems that track machine performance. By alerting the operators to what might go wrong before it affects production, it minimizes downtime and defects.
Swiss Screw Machine Tools
The Swiss machining operations depend on your choice of tooling. Here are the essential tools you should consider:
Guide Bushings: Standard steel bushings are used in general applications to reduce the cost and provide durability. Carbide lined bushings extend tool life for demanding jobs. Long life bushings are even more durable for long production runs, and rotating guide bushings provides less friction resulting in increased precision.
Cutting Tools: Hardness and wear resistance make them good candidates for high-speed machining with select carbide inserts. These high speed steel tools are versatile and they are comparatively inexpensive. For example, diamond coated tools for non-ferrous materials and ceramic inserts for high temperature applications where the tool may fail.
Tool Holders: Minimize downtime by implementing quick-change systems. Setup is flexible with modular tooling. Different holders required for specialized uses increase accuracy and adjustable tools permit extremely precise placement of tool positions for fine machining.
Modern Tool Technologies
Advancements in tooling technology enable Swiss machining advances. Here are some innovations you can incorporate:
Through-Tool Coolant Delivery: Coolant reaches the cutting edge, increasing tool life and improving part quality. This in turn maintains the optimal temperature setting during the machining process.
Smart Tooling with Embedded Sensors: Receive real time feedback on performance and condition using tools equipped with sensors. This information allows you to optimize your machining process.
Additive Manufactured Custom Holders: Use 3D printing technology to produce custom tooling solutions. The ability to rapidly prototype and produce specialized tools at low cost makes this method very advantageous.
High-Pressure Coolant Systems: The way to maintain the optimal cutting temperatures and prevent wear on the tools is to implement these systems. It improves overall machining process efficiency.
Applications and Products
Here are some common sectors where you can find their applications:
Medical Devices: Precise components like bone screws for orthopedic procedures, dental implants for restorations, and surgical instruments for delicate surgeries are produced using Swiss machining. Medical tubing components are also intricately machined.
Aerospace Components: When you’re looking for fluid control parts used in aircraft hydraulic systems, you can count on Swiss machining. It also manufactures electrical connectors for aircraft systems, precision fasteners used for assembling, and housings to protect sensitive electronics.
Automotive Parts: Fuel injection components that deliver fuel accurately into engines are manufactured by Swiss screw machines. Anti-lock brakes systems require ABS sensor parts, while components for transmission make for more efficient gear shifting. They also support the burgeoning electric vehicle sector.
Electronics: Swiss machining is used in electronics to create intricate connector pins that are needed for connectivity. Additionally, it manufactures heat sink components, helping to dissipate heat from devices, PCB standoffs for holding circuit boards and RF connectors for use in radio frequency applications.
Service and Leading manufacturers
Sheet Metal Maison stands among the best companies in Swiss screw machining services. Located in China, their massive facility covers 30,000 m², and is staffed by over 400 skilled workers. You can trust their commitment to quality as they are ISO 9001 and ISO 16949 certified. Their offerings include:
Design for Manufacturing (DFM) Support: They provide optimized designs that are manufacturable.
24/7 Technical Support: This also helps your issues get dealt with as quickly as possible.
Material Traceability Systems: They guarantee complete tracking of materials used in production.
Rapid Prototyping: However, you get your designs approved quickly before a project, cutting your project timelines.
Industry Standards and Certification
There are several standards that have to be met to be able actively to provide for the reliability of the parts that are manufactured according to the principles of Swiss screw machining. Familiarize yourself with these common certifications:
ISO 9001:2015: This general quality management standard assists in maintaining high standards of quality of your processes.
AS9100D: This accreditation is critical for aerospace industries as it encompasses the quality area, safety in particular.
ISO 13485: This standard covers quality aspects to do with medical devices and aims at meeting the regulatory need.
IATF 16949: This is mandatory for auto part makers, which stress on enhancing performance and preventing defects.
Process Selection and Optimization
When designing parts for operation in Swiss screw machines, they have to be designed in that way that enhances the machining aspect. Consider the following:
Maintain Length-to-Diameter Ratios Below 20:1: This minimizes the possibility of some material being translated or deflected to another location during the process of machining hence increased accuracy.
Tool Approach Angles: Make sure that your tools are well positioned to access the part to enable easy machining of the corners.
Plan for Chip Evacuation: There must be proper removal of chips to reduce on the chances of causing tool damage and to enhance surface finishing.
Design for Simultaneous Operations: Service multiple tool stations to improve the productivity of machining operations with less cycle time.
Material Selection
Swiss screw machines are versatile when it comes to what material they can work with. Common choices include:
Stainless Steel (303, 304, 316): You derive high corrosion resistance and strength for hardness so that it can serve a long-lasting purpose.
Titanium Alloys: These materials are particularly light and at the same time are rather sturdy, thus making their application in aerospace and medicine possible.
Brass and Bronze: Usable in electronics, they offer the ease of machining that makes plumbing fixtures favorable.
Engineering Plastics: These materials are suitable for parts that need low coefficients of friction and low areal densities.
Materials with desirable mechanical properties should be chosen based on machinability, surface finish, cost and dimensional accuracy of the project.
Cost Optimization Strategies
To keep your production costs manageable, implement the following strategies:
Optimized Cycle Times: Aims to shorten cycle times without sacrificing quality to make it more efficient.
Tool Life Management: They can monitor tool wear and replace them at the right times to reduce costs.
Material Waste Reduction: Minimize waste and increase profitability by using efficient cutting techniques.
Process Automation: Find ways to automate repetitive tasks to increase overall operation efficiency.
Future Trends and Innovations
We can state with certainty that the quality of Swiss screw machining will expand with the passage of time. Look out for these emerging trends:
Technological Advancements: Artificial Intelligence will be integrated which will enable predictive maintenance and process optimization, with efficiency being enhanced.
Autonomous Machining: Settings will be adjusted automatically in the future, thereby reducing the number of human interventions.
Advanced Tooling Materials: The key is ongoing development in durable tooling which improves the longevity and performance of your machines.
More Sophisticated CNC Systems: They will give you more control over complex geometries to produce intricate designs more precisely than ever.
Conclusion
These machines are at the heart of modern manufacturing, producing the critical components that help drive innovation in every industry. For those who are considering swiss machining for their production needs or for those who are trying to optimize existing processes, it will be helpful to have a basic understanding of these fundamentals.
Keep pace with technology, and stay focused on quality control to ensure that your swiss machining operations continue to be successful. Especially, remember that it is possible to partner with manufacturers like Sheet Metal Masion for complex projects, but with the necessary expertise and capabilities.