Wire Edm Machining
What is EDM Machining – Electrical Discharge Machining Definition
Electrical discharge machining or EDM, also known as spark machining or spark eroding, is a metal fabrication process and non-traditional material-removal process to get the desired shape using electrical discharges. EDM machining utilizes quickly recurring current discharges between two electrodes to remove excess material from the workpiece. During the EDM process, the tool and workpiece will not make physical contact. CNC machines and equipment allow the use of some new electrical discharge machining techniques. EDM machining is commonly used in the die and mold-making industry and can be used to machine hard materials and produce precision complex parts.
Why Use EDM Machining?
Advantages of Electrical Discharge Machining
- Not affected by heat during the process.
- The hardness of tools doesn’t need to be higher than that of materials.
- Can be applied to any electrically conductive materials.
- High complexity, high accuracy, and good surface finish can be achieved.
- Reduced machining time compared to traditional machining.
- No contact between the workpiece and tool, it will not cause mechanical stress.
- Extra materials will not be processed into waste, which improves the utilization of materials.
- Vertical angle of the workpiece can be achieved.
- Hard and corrosion-resistant surfaces on the molds can be obtained.

Types of EDM Machining
Wire EDM

Advantages of Die Sinking EDM
- Sinker EDM is able to produce complex shapes and parts that are difficult to produce with conventional tools.
- Delicate details and fragile materials can be machined without distortion, as the tool does not directly contact the workpiece.
- Good surface finish can be achieved using die-sinking EDM as the movements are restricted by axes.
- The operation is protected by the liquids, which prevents the tools and parts from being overheated.
- Excessive diameter of holes caused by grinding of contact surfaces can be avoided, and smaller and deeper holes can be made.
Die Sinking EDM
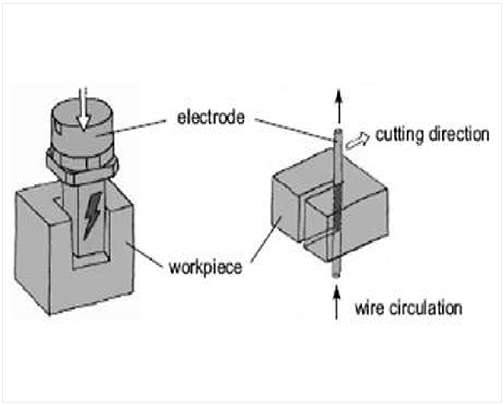
Advantages of Die Sinking EDM
- Since the electrode of wire EDM is 0.03-0.35mm metal wire, there is no need to process a particular electrode, which saves time and considerably improves productivity.
- Wire EDM products are unaffected by the hardness of the material and are capable of processing conductive materials that cannot be created by other methods.
- Materials may be chopped after heat treatment to eliminate deformation issues produced by the post-heat treatment.
- In addition to the influence of wire and gap at the product’s inner corner, WEDM may make virtually any shape of the product.
- WEDM has unrivaled advantages over other forms of machining for milling precious metals. It increases material efficiency and decreases material prices.
- The quick wire is recyclable, and the amount of consumables required is minimal. Although the wire cannot be recycled, it is capable of producing micron-precise parts.
- The cutting fluid is a noncombustible liquid that enables automatic operation.
Hole-Drilling EDM

Advantages of Hole-Drilling EDM
- EDM drilling machines do not rely on physical force to use the tool and can work with various materials no matter how hard it is.
- Some EDM drilling equipment can perform 5-axis machining to create precise holes at different angles.
- It is an optimized technique to manufacture semi-accurate holes in ductile materials at high speed.
- Fast tool wear caused by physical drilling machines can be avoided, especially in rapid drilling.
- The EDM drilling tubes used in hole drilling are typically low-cost and highly-conductive materials.
EDM Services – Top-Notch Electrical Discharge Machining Services
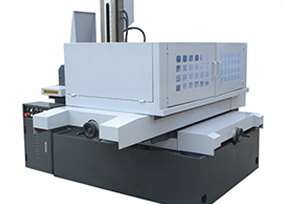
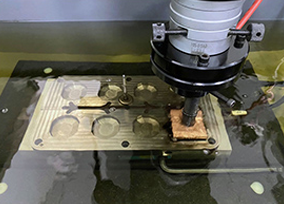
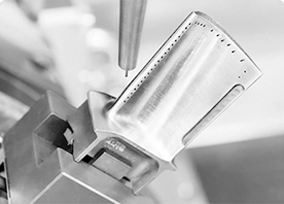
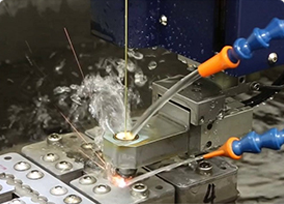
EDM Machining Materials – What Materials Can Be Machined by EDM
Free Sample
Explore Other Services
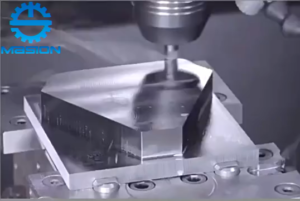
CNC Milling Services
Masion provides CNC Milling Services, specializing in the manufacturing of various CNC Milling parts, ensuring quality and quantity assurance.

CNC Swiss machining
Specialized in CNC Swiss Machining Services –Leading CNC Swiss machining Companies/Manufacturers in China. What is CNC Swiss Machining? CNC Swiss machining is an advanced and rapid CNC machining technique. The

CNC Milling and Turning Services
CNC Milling and Turning Services –China CNC Turning Milling Parts Manufacturer. CNC milling and turning is one of the advanced manufacturing technologies in the international mechanical processing industry. It integrates