Bead Blasting
Bead Blasting processing
Bead Blasting Processing - Introduction to the Process
Bead Blasting, also known as abrasive blasting or sandblasting,typically involves the use of compressed air to propel abrasive particles from a nozzle and direct them onto the surface to be treated. This method can remove old coatings, dirt, and rust, allowing for re-coating while also improving surface quality and appearance.
Sandblasting is commonly used for surface treatment of other materials such as wood, glass, stone, and metal such as aluminum, steel, etc.
Different types of abrasive particles can be used in sandblasting, such as diamond grit, aluminum oxide, glass beads, steel shot, steel grit, alumina, quartz sand, and silicon carbide. Different types of abrasive particles can be used for different types of surface treatment, for example, diamond grit can be used for removing thicker coatings and rust, while fine glass beads can be used for surface polishing and removing fine dirt.
Safety precautions should be taken during sandblasting operations as high-speed abrasive particles can produce dust and noise.
Bead Blasting processing, process flow
Operation Process:
- (Washing)
- Protection
- Sandblasting
- Air Blow
- Removal of Protective Materials
Requirements for Each Operation:
Protection
Protect as required by the drawings. Threaded holes should be protected with corresponding screws, and the end of the protective screw should be flush with the machined surface of the workpiece without any damage. Protective fixtures should be used for protecting surfaces or other holes, and the edges of the protective fixtures should be neat and intact. The effectiveness of the fixtures should be validated before use.
Sandblasting
The air pressure, angle, distance, and sand type used for sandblasting should be in accordance with the process requirements.
Air Blow
After sandblasting is completed, the workpiece surface should be cleaned by blowing compressed air to remove dust and sand.
Removal of Protective Materials
Before entering the next process, protective materials should be removed, and when using electric tools, care should be taken not to damage the threads.
Quality Requirements:
Appearance Requirements for Sandblasting
The surface should have a uniform texture, without large marble patterns, scratches, contamination, corrosion marks, or other obvious visual defects.
The appearance of the sandblasting must be consistent with the customer's standard sample.
Roughness Requirements
The Ra value should be within the range of 1.5~1.8μm (GB10610-89).
Precautions
Compressed air should be free from oil and water contamination. Inspection method: Blow compressed air onto a clean glass mirror for 2-3 minutes, and there should be no traces of oil or water on the mirror.
Check the air pressure to meet the requirements for spraying.
Do not touch the sandblasted surface with bare hands.
Pay attention to protecting the sandblasted surface and avoid causing scratches or impacts.
5 All equipment should be kept in good operating condition.
Bead Blasting Processing - Production Equipment Showcase

Bead BlastingProcess and Production Equipment Display

Bead Blasting Process and Sample Cases

Free Sample
Explore Other Services

QPQ Coating
Phosphating is a process in which a workpiece is treated in a phosphoric acid salt solution containing manganese, iron, and zinc to form a layer of insoluble phosphate film on
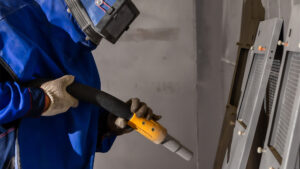
Bead Blasting
Bead Blasting, also known as abrasive blasting or sandblasting,typically involves the use of compressed air to propel abrasive particles from a nozzle and direct them onto the surface to be

Paint Spraying
Spray Painting processing is a method of applying paint or other coatings onto surfaces of various materials, such as wood, metal, plastic, or glass. The purpose of painting can be