Bright Tin Plating
Bead Blasting processing
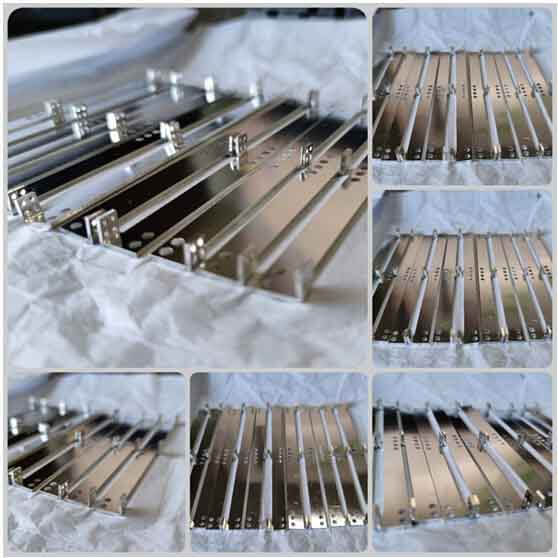
English Translation: Bright Tin Plating Process by Rack Plating
Substrate: Brass H62
Plating Type: Electroplated Tin/Bright Tin
Process: Rack Plating
Auxiliary Process: Mechanical Polishing
Film Thickness: 8μm on one side
Plating Cost: $30 per rack.
Tin Plating Process Introduction
Types of Bright Tin Plating:
Immersion Bright Tin Plating
Chemical Tin Plating
Acid Tin Plating
Advantages
Tin is reduced to divalent, which saves electricity.
The plating solution has high conductivity, low bath voltage, and high current efficiency.
The operating temperature is close to room temperature, and no heating equipment is required.
Glossy coatings can be obtained with appropriate additives.
It causes less damage to the substrate.
Disadvantages
The operation and plating bath management require great care to obtain good coatings.
Additives are required, otherwise, dendritic or nodular coatings are prone to form.
Insoluble anodes cannot be used.
It is corrosive, and the plating tank must be lined with rubber.
Divalent tin may oxidize to tetravalent tin and become passive.
Alkaline Tin Plating
Advantages
Good uniformity.
Tolerant of impurities.
Glossy coatings can be obtained without additives.
Insoluble anodes can be used.
Wide operating range.
Simple formulation.
Low pre-treatment requirements.
Disadvantages
Low cathode efficiency, thin coating.
The electrochemical equivalent is only half of that of the acid bath, high power consumption.
Glossy coatings can only be obtained with molten technology.
High operating temperature requires heating equipment.
High bath pressure is needed.
Soluble anodes must be used.
Careful operation is required in soluble anode plating, otherwise, poor coatings may be obtained.
Continuous High-Speed Tin Plating
It is used exclusively for continuous electroplating of parts.
Tin plating on brass
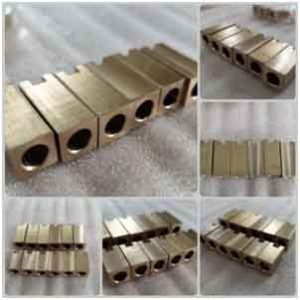
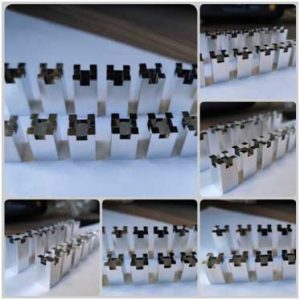
Base Material: Brass H59
Plating Type: Bright Tin Plating/ Electroplated Tin
Process: Rack Plating
Auxiliary Process: Mechanical Polishing / Chemical Polishing
Thickness: 8μm
Electroplating Cost: As this workpiece is small, the electroplating cost is calculated per piece and depends mainly on the quantity per batch. For larger quantities (such as over 1000 pieces per batch), the cost of tin plating on brass is approximately 0.3 USD per piece.
Introduction to Tin Plating on Brass Process:
The Tin plating on brass has the following characteristics and uses:
High chemical stability and resistance to oxidation in air, making it less likely to discolor.
Under general conditions, the tin plating layer is a cathodic coating for steel. Therefore, effective protection of the steel substrate can only be achieved when the coating has no pores. However, in a closed organic acid medium (such as the inside of a can), tin is an anodic coating, and even with pores, it still has electrochemical protection. Moreover, dissolved tin is harmless to human health, so it is often used as a protective layer for food containers.
Tin has good electrical conductivity and is easy to solder, making it commonly used for tin plating on brass electronic component leads, printed circuit boards, and low-voltage devices.
Tin Printing Process
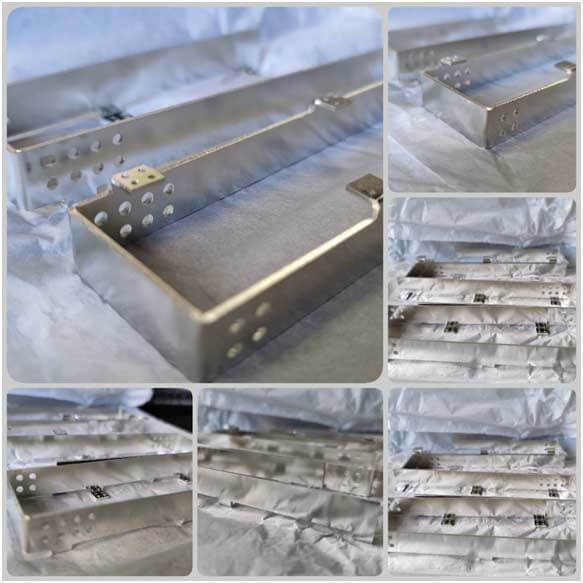
Brass Parts Hanging Plating with Bright Tin Processing
Substrate: Brass H62
Plating Type: Tin Electroplating / Bright Tin Plating
Process: Hanging Plating
Auxiliary Process: Mechanical Polishing
Film Thickness: 8μm on one side
Plating Cost: $30 USD per hanging
Tin Plating Process Flow
- Degreasing
- Cleaning
- Acid Etching
- Cleaning
- Activation
- Cleaning
- Trisodium Phosphate Neutralization
- Cleaning
- Deionized Water Rinse
- Dehydration
- Drying
- Packaging
Poor uniformity of the tin plating layer
Solutions
Control the solution temperature and take cooling measures if necessary.
Use a moving cathode. A moving cathode can improve the ability of uniform plating and adjust the cathode current density to prevent issues like scorching, pinholes, streaks, and a dark gray appearance in the plating layer. It also has a positive effect on improving the brightness of the plating layer.
Slow deposition rate
Main symptoms of excessive tin sulfate concentration: reduced dispersion ability of the plating solution, rough and dull plating layer, and narrower bright area.
Symptoms of insufficient tin sulfate concentration: significantly reduced allowable current density range, the slow deposition rate of the plating layer, decreased production efficiency, and a higher risk of scorching the plating layer. In one specific case, the slow deposition rate was initially suspected to be caused by excessive current density. However, a laboratory analysis was conducted considering that the tin plating layer was not rough and the phenomenon did not improve after reducing the current density. It was found that the tin sulfate concentration was already below 30g/L and the anode was passivated. The decrease in tin concentration in the solution was caused by the passivation of the anode, which resulted from impure tin being used in the anode casting process. Therefore, it is crucial to maintain the purity of the anode in the tin plating process. The purity of the tin anode should not be less than 99.9% to avoid passivation and contamination of the plating solution. Anode bags should also be used to prevent anode sludge from polluting the solution.
Yellow coloration in the solution
The appearance of yellow color in the bright tin plating solution is usually caused by organic contamination, which is often formed by decomposition products (including potential contamination from the workpiece). This contamination increases the viscosity of the solution and leads to rough crystallization, streaks, pinholes, increased brittleness, and reduced adhesion of the plating layer.
To avoid this phenomenon, the solution should undergo purification after a certain period of use to remove excessive organic impurities. The specific procedure involves adsorption with activated carbon, followed by filtration and adjustment of the composition. After a short electrolysis treatment, the solution can be reused.
Accelerated dissolution of the tin anode
Since sulfuric acid has a chemical dissolution effect on the tin, the increased concentration of tin salts in the solution resulted in a waste of materials and increased costs for wastewater treatment.
Sulfuric acid is an essential component in the bright tin plating solution, and its presence has various effects on the plating layer quality. Insufficient or excessive sulfuric acid concentration can affect the plating layer quality in the following ways:
When the sulfuric acid concentration meets the requirements of the process formulation, its presence can inhibit the oxidation of divalent tin ions, stabilize the plating solution, improve its conductivity and ability for uniform plating, enhance cathodic polarization, promote fine crystallization of the plating layer, and accelerate anodic dissolution, thus improving the anodic current efficiency. However, it is necessary to prevent excessive sulfuric acid concentration, as it can negatively affect the cathodic current efficiency and increase the burden of wastewater treatment.
When the sulfuric acid concentration is lower than the requirements of the process formulation, the most noticeable issue is the formation of insoluble precipitates in the plating solution, leading to rough crystallization of the plating layer. In such cases, an appropriate amount of coagulant can be added to the solution, followed by stirring and filtration. Adjustments with sulfuric acid should also be made as needed.
Therefore, controlling the sulfuric acid concentration in the bright tin plating solution is crucial for maintaining the quality of the plating process.
Rough Coating Appearance
Tetravalent tin is formed when divalent tin reacts with oxygen in the air. To prevent excessive tetravalent tin formation, it is necessary to avoid excessive suction by the exhaust fan or air agitation in the solution. Additionally, the solution temperature should not be too high.
This fault can be addressed by adsorption treatment with activated carbon, followed by filtration and readjustment of other components.
Poor Coating Brightness
The tin layer and the underlying copper at the interface penetrate each other, forming a diffusion layer of alloy with a melting point higher than that of tin. If the coating outside this diffusion layer is too thin, especially below 3-4μm, it becomes difficult to solder. Increasing the coating thickness significantly improved the brightness of the coating and completely improved the welding performance.
Hence, it can be seen that the causes of coating failures are diverse. When solving such issues, it is important to think broadly, search for clues, and avoid limiting oneself.
Yellow Film on the Coating
The troubleshooting approach for this batch of workpieces involved a brushing method, but it damaged the natural gloss of the tin layer surface. Later, turbulent rinsing was adopted. A self-made nozzle, as shown in Figure 7-9, was connected to a tap water hose. When the valve was opened, turbulent flow was generated to vigorously flush out the residual solution from the cavities and narrow gaps of the workpiece.
Rust Stains on Coating
Poor Weldability of Plating Due to Accumulation of Copper Ions in the Plating Solution
Consequently, the author consciously observed the process of copper green formation. It was later observed that an operator was directly brushing the anode stem in the tank with a copper wire brush, resulting in the formation of copper green deposits. Over time, the copper ions in the solution inevitably increased. The solution may have already been contaminated to the maximum extent. It took a long time of electrolytic treatment to slowly restore the solution.
In addition to the responsibility of the operator for mistreating the solution, production and technical managers also bear the responsibility of supervision and education.
Poor Brightness and Rough Crystal Structure of the Plating Layer
Purity requirement for stannous sulfate: Stannous sulfate must be of analytical purity. Before use, the surface color should be observed. If there is a yellowish tint, it cannot be used as it indicates the oxidation of divalent tin into tetravalent tin. Tetravalent tin is easily hydrolyzed to form metastannic acid, which makes the plating solution turbid. Accumulated sludge will reduce the current efficiency and result in a dull, foggy, rough, and porous plating layer.
Purity requirement for sulfuric acid: Sulfuric acid should also be of analytical purity. Industrial-grade sulfuric acid contains various impurities that are harmful to the plating solution.
Water quality purity requirement: Tap water contains various ions such as chlorine, calcium, and magnesium, which are harmful to the plating solution. These ions, when adsorbed onto the plating layer, will affect the brightness of the plating layer and even its weldability. Therefore, deionized water must be used when preparing the plating solution. In addition to the above possible reasons, regular maintenance of the solution and prevention of harmful impurities from entering the solution through the air and workpieces are also important.
Rapid Failure of Brightening Agent in the Solution
Low solution temperature is also detrimental to the quality of the plating layer. When the plating solution temperature is too low, the current density must be correspondingly reduced; otherwise, the workpiece is prone to scorching, resulting in a slow deposition rate and poor.
Turbidity in Newly Prepared Solution
Trial preparation: Normally, the prepared plating solution should be clear. However, sometimes the solution appears turbid, which may be due to quality issues with the stannous sulfate. It could be a manufacturing process problem or a result of an extended shelf life. Therefore, before preparing the plating solution in the large tank, it is advisable to conduct a trial preparation in a small tank using the normal procedure. If the prepared solution shows no abnormalities, then it can be prepared in the large tank. Otherwise, further examination of the stannous sulfate quality should be conducted based on the possible causes mentioned above.
Add 1/3 to 1/2 deionized water to the tank.
Slowly add the required amount of analytical-grade sulfuric acid while stirring continuously (the addition should be slow to prevent rapid heating and deformation of the plastic tank).
Allow the temperature to cool to around 30°C.
Allow the temperature to cool to room temperature.
Slowly sprinkle stannous sulfate into the tank while stirring continuously. Alternatively, wrap the stannous sulfate in multiple layers of plastic mesh and hang it in the tank, allowing it to dissolve slowly and naturally while stirring continuously (avoid using compressed air agitation to prevent accelerated oxidation of divalent tin ions).
Add the additives dissolved in a small amount of deionized water while stirring.
Add deionized water to the specified level.
Continue stirring for 30 minutes.
Electrolytic treatment: Current density (Dk) = 0.2 A/dm²; treatment time (t) = 12 hours.
Following the above procedure and method of preparing the plating solution can also prevent problems such as the formation of clumps of stannous sulfate at the bottom of the tank, which may hinder dissolution.
Requirements for stirring during the plating solution preparation process:
To ensure uniformity of all components in the plating solution, thorough stirring should be carried out during the preparation process. Superficial stirring should be avoided.
To minimize the exposure of stannous sulfate in the plating solution to air and prevent oxidation, stirring should not be too vigorous. Intermittent stirring can be employed, and the formation of "wave peaks" in the solution should be prevented.
Requirements for electrolytic treatment after plating solution preparation:
After preparing the plating solution, thorough electrolytic treatment should be conducted. The current density used during treatment does not need to be too high; a low current can be used. This not only reduces material consumption in the plating solution but also removes harmful impurities from the solution. It also promotes the "breaking-in" and "coordination" of the plating solution.
Free Sample
Explore Other Services

Paint Spraying
Spray Painting processing is a method of applying paint or other coatings onto surfaces of various materials, such as wood, metal, plastic, or glass. The purpose of painting can be

Electrophoretic Coating
Bead Blasting, also known as abrasive blasting or sandblasting,typically involves the use of compressed air to propel abrasive particles from a nozzle and direct them onto the surface to be

Bright Tin Plating
Bead Blasting, also known as abrasive blasting or sandblasting,typically involves the use of compressed air to propel abrasive particles from a nozzle and direct them onto the surface to be