Chrome Plating
Black Chrome Plating
BriefIntroduction to Black Chrome Plating Process
Black chrome plating refers to coating the surface of a workpiece with a layer of black chrome. The black chrome coating is not pure metallic chrome, but an amorphous oxide crystal. The content of metallic chrome in the coating is only 50%-70%, while the rest is chromium oxide. The black chrome coating has a loose crystalline structure with a branching pattern, which allows it to fully absorb light waves and appear black. It has been proven that black chrome coating is the most excellent selective absorber among all black electroplating and coating as solar energy development continues. The ratio of the absorption rate (a) to the reflection rate (y) of black chrome coating can be greater than 10, making it widely used in solar energy collectors, weapons, optical instruments and cameras. In addition, black is relatively solemn, so it is increasingly used in automotive, daily light industry decorative parts, and other fields.
Common Substrates for Black Chrome Plating
Copper parts
Direct black chrome plating on copper and brass substrates is possible, but it is not reasonable to do so even if avoiding electrochemical corrosion. This is because the difference in thermal expansion coefficient between the black chrome coating and copper or brass is significant. If no underplating is used, the black chrome coating will crack over time and fall off the substrate. Therefore, the corrosion resistance of black chrome mainly depends on the quality of the substrate coating. The more reasonable and commonly used underplating is a nickel plating layer.
Stainless steel
Black chrome plating on stainless steel is also common, but since the surface of stainless steel is in a severely passive state, black chrome plating on stainless steel should first be plated with a flash nickel in a high-chloride nickel plating tank. If the black chrome layer requires a relatively bright appearance, a bright nickel layer should also be plated before the black chrome plating.
Aluminum parts
Aluminum alloys can be chrome plated. Compared with other substrates, the bonding strength between aluminum and the chrome plating layer is weaker. Therefore, chrome plating on aluminum alloys is more challenging and requires specialized plating plants for aluminum alloy chrome plating. For example, many aluminum alloy wheels are now chrome plated.
Thickness and Hardness of Black Chrome Plating
The thickness of black chrome plating is generally around 5μm. For workpieces that require light absorption or energy absorption, the desired thickness can be achieved with a deposition time of 15-20 minutes during actual electroplating. Of course, as the plating time is prolonged, the thickness will increase, but the speed will decrease significantly.
Due to the fact that the black chrome plating is not pure metallic chromium (the content of metallic chromium accounts for only 50%-70% of the plating layer), the wear resistance of black chrome plating is much lower than that of hard chrome plating, with only HV130-350, which is equivalent to HRC0-35.5. The actual wear resistance is similar to that of ordinary chrome plating. In addition, black chrome plating has high thermal stability. When heated to 480℃, there is no obvious change in appearance, and the adhesion between the plating layer and the substrate is good. (Note: The hardness of the hard chrome plating layer on the workpiece will sharply decrease in high-temperature environments above 500℃.)
Color of hard chrome plating
black, divided into bright black (for appearance parts) and matte black (for light absorption).
Difference between black chrome plating and black nickel plating
Whether it is corrosion resistance, wear resistance, or solar energy absorption, black chrome plating performs better than black nickel plating.
Black Chrome Plating Process:
- Hanging
- Chemical degreasing
- Cleaning
- Electrochemical degreasing
- Cleaning
- Acid pickling to remove rust
- Cleaning
- Chloride copper plating
- Cleaning
- Nickel electroplating
- Cleaning
- Black Chrome plating
- Cleaning
- Air drying
- Unhanging
- Polishing (if necessary)
- Oil application (spindle oil)
- Quality inspection
- Packaging
- Shipping.
Pricing for Black Chrome Plating
Price Per Piece
The price per piece depends on the size of the workpiece and the quantity of workpieces in the current batch. The larger the quantity, the lower the unit price. (The range is wide, ranging from a few cents to tens of USD.)
Minimum Charge
Generally around 30 USD;
Price Per Weight
For larger workpieces, the price is generally around 3 USD/kg.
Black Chrome Plating Processing - Production Equipment Showcase.
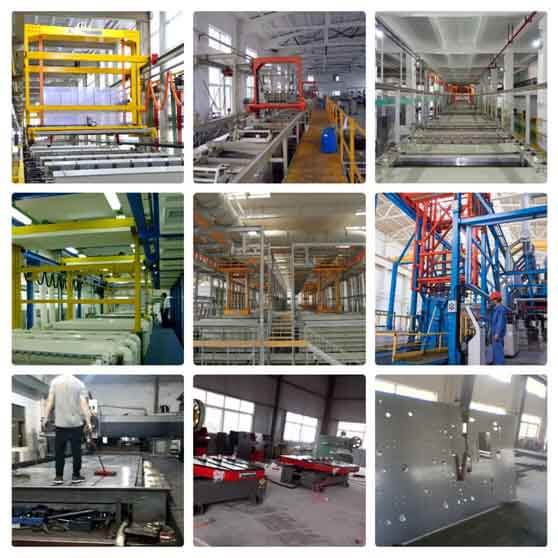
Display of Inspection Equipment for Black Chrome Plating Processing.
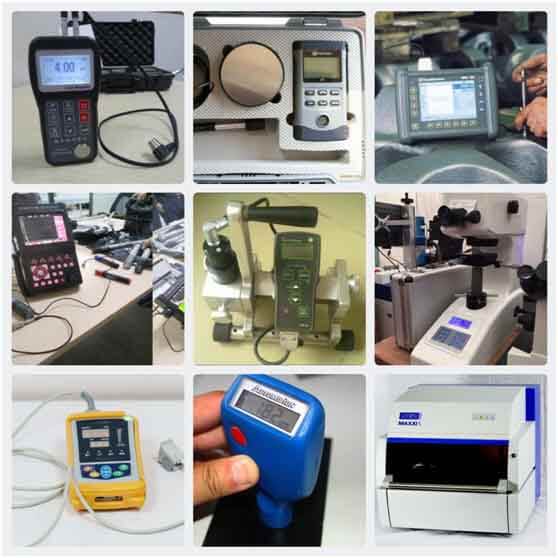
Black Chrome Plating Processing Sample Case
Automotive parts:
Black chrome plating can provide a sleek and modern look to automotive parts such as wheels, grilles, and trim.
Decorative items:
Black chrome plating can be used on a variety of decorative items, such as lighting fixtures, furniture, and household accessories.
Sporting goods:
Black chrome plating can provide a durable and stylish finish for sporting goods, such as golf clubs, fishing reels, and firearms.
Jewelry:
Black chrome plating can give a unique and contemporary look to jewelry, such as rings, necklaces, and bracelets.
Musical instruments:
Black chrome plating can be used on musical instruments, such as guitars and drum hardware, to provide a sleek and modern appearance.
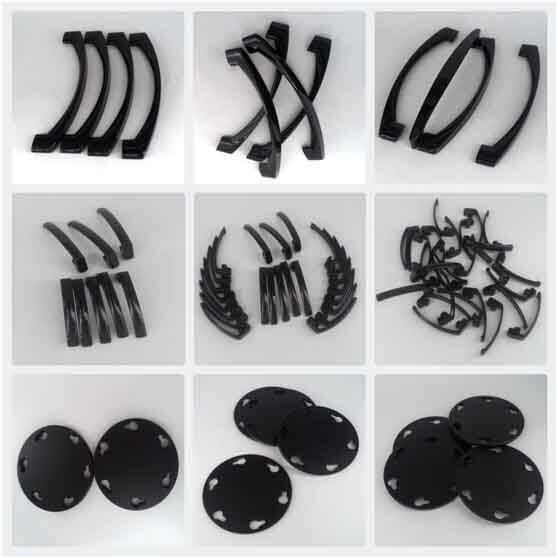
Decorative Chrome Plating
Decorative Chrome Plating - Process Overview
Common substrates for decorative chrome plating:
Copper parts
After polishing, copper and brass substrates can be directly chrome-plated. However, due to the large difference in thermal expansion coefficients between the chrome plating layer and copper parts, if there is no underplating, the chrome plating layer will crack and fall off from the substrate over time. Therefore, in most applications, copper and nickel are plated as an underlayer on copper parts, followed by chrome plating.
Stainless steel
Decorative chrome plating is also common on stainless steel, but since the surface of stainless steel is in a severely passive state, it is necessary to first plate an impact nickel layer in a high chloride nickel plating bath. If the chrome layer still has a requirement for a bright appearance, a bright nickel layer should also be plated, and then chrome plated on the bright nickel layer.
Aluminum parts
It can be confirmed that aluminum alloy can be chrome plated because aluminum is a amphoteric metal that can react with both acids and bases. Therefore, electroplating on aluminum alloy is much more difficult than on other metals (usually requiring an additional process of double zinc plating) and requires a specialized chrome plating factory for aluminum alloy plating. Example: Many aluminum alloy wheels for cars are chrome-plated.
Zinc alloy
Decorative chrome plating on zinc alloys is very common. Most of the bathroom products in our homes are chrome-plated zinc alloys.
Coating thickness and hardness of decorative chrome plating
Color of Decorative Chrome Plating
Process of Chrome-plating for Decorative Purposes
- Workpiece
- polishing
- wax removal
- Hot immersion degreasing
- Cathode
- Anode
- Cleaning
- Electrolytic degreasing
- Weak acid etching
- Pre-plating alkaline copper
- Acid bright copper (optional)
- Bright nickel
- Chrome plating
- Workpiece
- polishing
- wax removal
- hot immersion degreasing
- cathode
- anode
- Cleaning
- electrolytic degreasing
- weak acid etching
- semi-bright nickel/dull nickel
- high sulfur nickel
- bright nickel
- nickel sealing (optional)
- chrome plating
- Workpiece
- polishing
- wax removal
- hot immersion degreasing
- cathodic electrolytic degreasing
- acid dipping
- alkaline bright copper
- pyrophosphoric acid copper (optional)
- acid bright copper (optional)
- bright nickel
- chrome plating
The process of chrome-plating for aluminum alloys is as follows:
- Workpiece
- polishing
- wax removal
- hot immersion degreasing
- cathode
- anode
- Cleaning
- electrolytic degreasing
- weak acid etching
- first chemical zinc immersion
- zinc removal
- second chemical zinc immersion
- alkaline bright copper
- pyrophosphoric acid copper (optional)
- acid bright copper (optional)
- bright nickel
- chrome plating.
Pricing for Decorative Chrome Plating
Price per piece:
for smaller quantities, the price per piece depends on the size of the workpiece and the quantity of the current batch. The larger the quantity, the lower the unit price.
Minimum consumption:
generally between $10-20;
Weight-based charges:
for larger or heavier workpieces, the charge is generally around $2/kg.
Decorative Chrome Plating Processing - Production Equipment Display
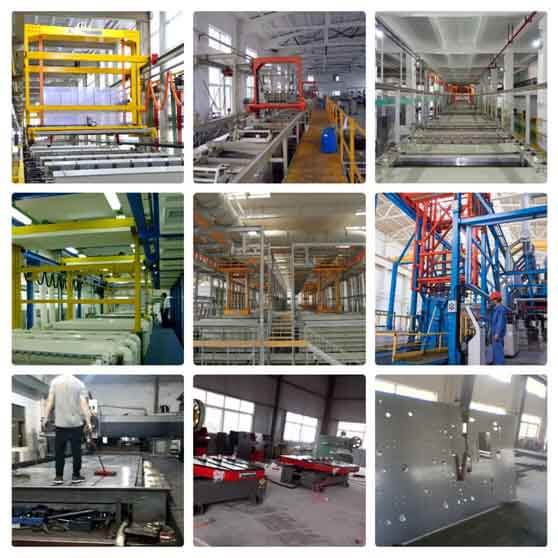
Decorative Chrome Plating Processing | Inspection Equipment Display
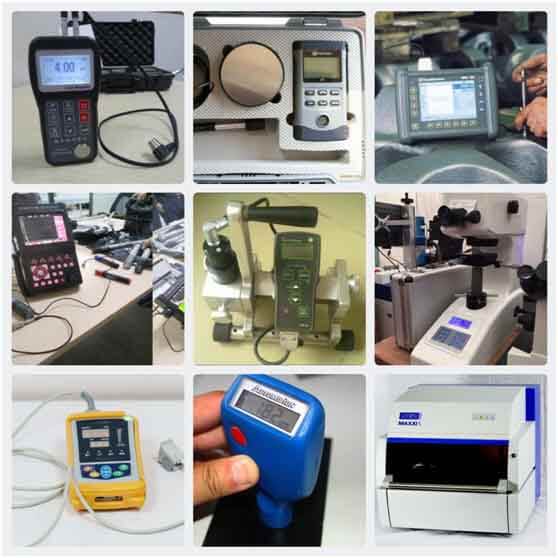
Decorative Chrome Plating Processing Sample Case
Below are some sample cases of decorative chrome plating:
Home accessories:
Decorative chrome plating can provide a noble and elegant appearance for home accessories, such as lamps, door handles, and furniture accessories.
Bathroom accessories:
Decorative chrome plating can provide a high-end and atmospheric appearance for bathroom accessories, such as faucets, shower heads, and bathroom accessories.
Toy models:
Decorative chrome plating can provide exquisite surface treatment for toy models, such as model cars, model airplanes, and figure models.
Jewelry:
Decorative chrome plating can provide a high-end appearance for jewelry, such as bracelets, rings, and necklaces.
Automotive accessories:
Decorative chrome plating can provide a stylish appearance for automotive accessories, such as wheels, grilles, and exhaust pipes.
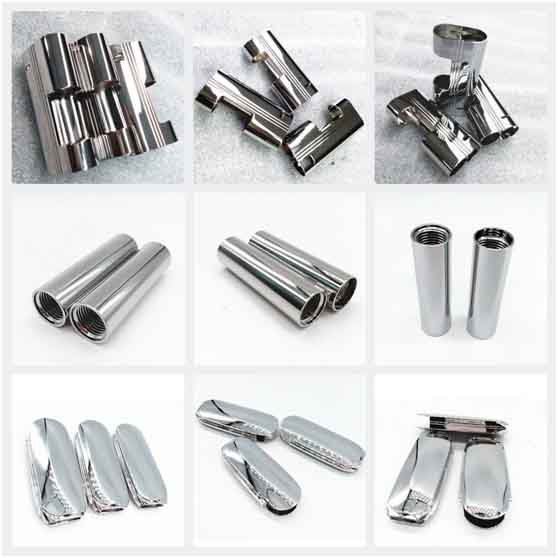
Deep holehard chrome plating
Introduction to the Process of Deep-Holehard Chrome Plating.
Process for Hard Chrome Plating on Deep Hole
- Mechanical pretreatment (polishing)
- Pre-degreasing
- Hanging of parts
- Installation of shielding material (if partial chrome plating is required)
- Degreasing
- Rinsing with water
- Rust removal/activation
- Rinsing with water
- Anodic corrosion
- Rinsing with water
- Blowing with air
- Removal of hanging parts
Degreasing
Chemical degreasing
Use a phosphorus-free degreaser to chemically degrease the deep hole at 60-80°C for 10-15 minutes. The concentration of the phosphorus-free degreaser when mixed should be 3-5%.
Electrolytic degreasing
Place the workpiece to be plated in the electrolyte as the anode or cathode for joint anode-cathode degreasing. The electrolyte includes NaOH, Na2CO3, Na3PO4, and Na2SiO3, with a concentration of 40-80g/L for NaOH, 20-50g/L for Na2CO3, 15-30g/L for Na3PO4, and 2-5g/L for Na2SiO3. The degreasing time includes 4-5 minutes for the cathode and 1-2 minutes for the anode per cycle.
Rinsing
Activation
Hot pure water rinsing
Mounting
Hard chrome plating on an inner hole
Recovery tank
Dismounting
Cleaning
Hard Chrome Plating on Deep Hole Machining Fee Explanation
Equipment Display for Hard Chrome Plating on Deep Hole Machining
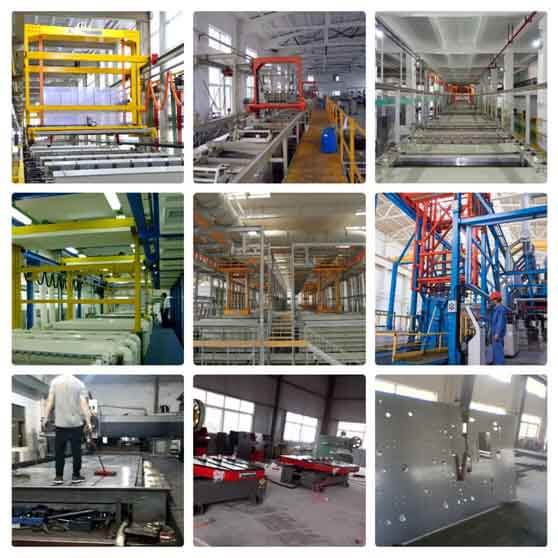
Equipment Display for Inspection of Hard Chrome Plating on Deep Hole Machining
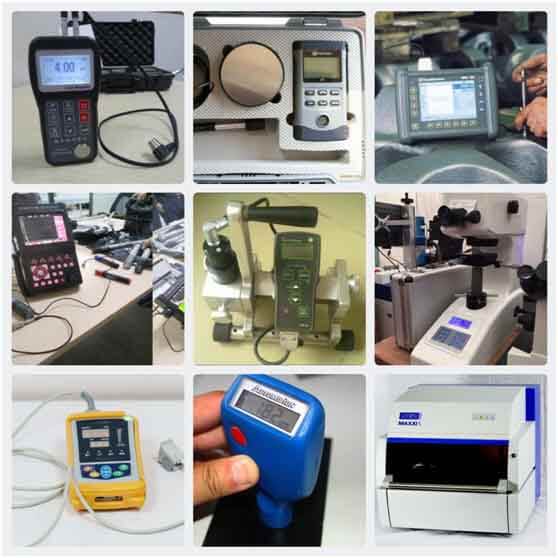
Sample Cases for Hard Chrome Plating on of Deep Hole Machining
Here are some sample cases for hard chrome plating on the deep hole machining
Hydraulic cylinder
Hard chrome plating on the hydraulic cylinders provides wear and corrosion-resistant protection, which prolongs the service life of the cylinder.
Gun barrel
Hard chrome plating on the gun barrels improves the surface hardness and wear resistance, which reduces the erosion of the barrel and extends its life.
Oil drilling equipment
Hard chrome plating on the oil drilling equipment improves the surface hardness and wear resistance, which enhances the performance and longevity of the equipment.
Printing rollers
Hard chrome plating on the printing rollers can enhance the hardness and wear resistance, resulting in longer service life and improved printing quality.
Precision mechanical parts
Hard chrome plating on the precision mechanical parts provides corrosion and wear-resistant protection, which ensures their accuracy and prolongs their life.
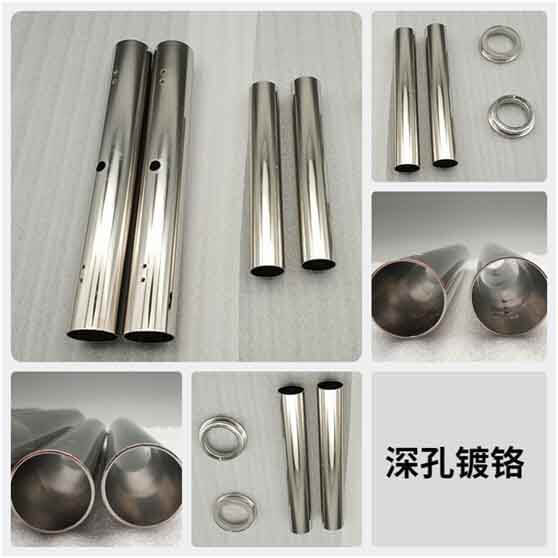
Hard Chrome Plating
Brief Introduction toHard Chrome Plating Process
There are slight differences between the two:
Common substrates for decorative chrome plating:
Common substrates for hard chrome plating
In theory, almost all metal materials can be used for chrome plating. However, the following materials are difficult to plate (not impossible, but require different treatment in the process for different materials): steel with high carbon content (C>0.90%); steel with high silicon content (Si>1.00%); steel with high chromium (Cr) and tungsten (W) content; grey cast iron; ductile iron; magnesium; aluminum alloys containing magnesium; and if the surface of the cast steel parts is free of metal impurities and cracks, they can also be chrome plated.
Common substrates for hard chrome plating include 45 steel, 304 stainless steel, 316 stainless steel, and Cr12 alloy tool steel, etc.
Film thickness and hardness of hard chrome plating
The film thickness of hard chrome plating is usually around 20μm, and the hardness can reach HV800-900. If there are requirements for film thickness accuracy, the film thickness of precision hard chrome plating can be controlled within 10μm. In theory, the most economical thickness for chrome plating is 30μm, at which it can provide good protection against wear and corrosion. When the chrome layer reaches 65μm, increasing the film thickness will not enhance its corrosion resistance.
Hard chrome plating is usually used as a restorative electroplating process for the surface of workpieces. In this case, the thickness of hard chrome plating can reach 200-300μm, and in some special scenarios, the thickness of chrome plating can reach 800μm (this scenario is called "cost is not a concern").
Regarding the hardness of hard chrome plating, the hardness of the chrome layer will decrease with the increase in temperature in different working environments. At room temperature, the hardness of the chrome layer can reach HV900-1000/HRC67 or higher. At a working temperature of 100°C, the hardness will decrease to 830HV/HRC64. At a working temperature of 150°C, the hardness of the chrome layer will decrease to 750HV/HRC62. When the working temperature reaches 250°C, the hardness of the chrome layer will decrease to 700HV/60HRC. When the working temperature reaches 500°C, the hardness of the chrome layer will sharply decrease.
Color of Hard Chrome Plating
Silver White!!!
Hard Chrome Plating Process Flow
- Mechanical pretreatment (polishing)
- Pre-degreasing
- Hanging fixtures
- Installing shielding (if local plating is required)
- Degreasing
- Rinsing
- Rust removal
- Rinsing
- Anodizing
- Hard chrome plating
- Rinsing
- Blowing water
- Removing fixtures
- Removing shielding
Hard Chrome Plating Processing Fee Explanation
Minimum charge:
generally between 10-20 USD;
Charge per item
the price per item still depends on the size of the workpiece and the number of workpieces in the current batch. The larger the quantity, the lower the unit price;
Charge by weight
for larger workpieces, it is generally charged at 2-5 USD per kilogram; some large steel plates, such as the workbench of large equipment, can even achieve a price of 1 USD/kg.
Hard Chrome Plating Processing: Display of Production Equipment
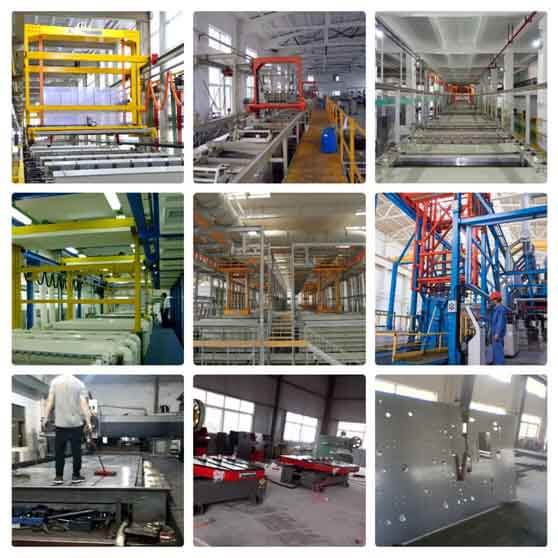
Hard Chrome Plating Processing: Display of Inspection Equipment
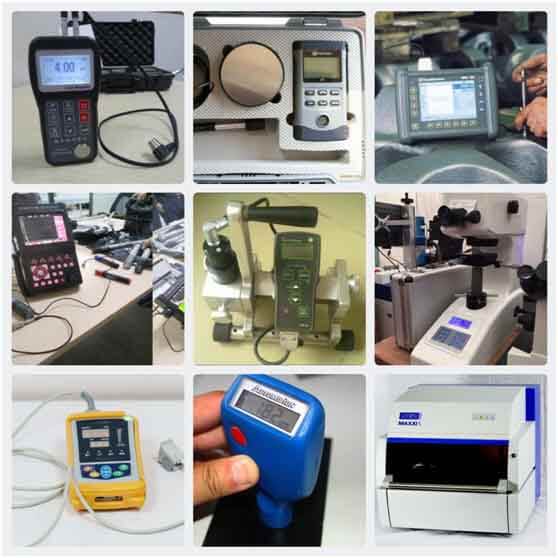
Case of Hard Chrome Plating Processing Samples
Examples of hard chrome plating in various products
Hydraulic Rods
Hard chrome plating can provide hydraulic rods with wear-resistant and corrosion-resistant surface protection, extending their service life.
Printing Rolls
Hard chrome plating can increase the hardness and wear resistance of printing rolls, allowing them to maintain accurate patterns and quality for a longer time.
Mold Components
Hard chrome plating can increase the surface hardness and wear resistance of mold components, increase the service life of the mold, and improve the adhesion of plastic to the mold.
Aerospace Engine Parts
Hard chrome plating can provide high-temperature, high-pressure, and corrosion-resistant surface protection for aerospace engine parts, improving their performance and service life.
Automotive Parts
Commonly chrome-plated automotive parts include intake valves, exhaust valves, piston rings, camshafts, oil seals, engine cylinder blocks, and more.The requirements for these products include high durability, hardness, abrasion resistance, good sealing performance, and corrosion resistance.

Pearl Chrome Plating
Introduction to the Process of Pearl Chrome Plating
There are two methods for achieving pearl chrome plating: electroplating and vacuum plating.
The Difference Between Decorative ChromePlating and Pearl Chrome Plating
Pearl Chrome Plating Process
- Workpiece
- polishing
- wax removal
- Hot immersion degreasing
- Cathode
- Anode
- Electrolytic degreasing
- Weak acid etching
- Pre-plating alkaline copper
- Acid bright copper (optional)
- Bright nickel
- Pearl nickel plating
- Chrome plating
- Workpiece
- polishing
- wax removal
- Hot immersion degreasing
- Cathode
- Anode
- Electrolytic degreasing
- Weak acid etching
- Semi-bright nickel/dull nickel
- High sulfur nickel
- Bright nickel
- Nickel sealing (optional)
- Pearl nickel plating
- Chrome plating
- Workpiece
- polishing
- wax removal
- Hot immersion degreasing
- Cathode electrolytic degreasing
- Acid pickling
- Alkaline bright copper
- Pyrophosphate copper (optional)
- Acidic bright copper (optional)
- Bright nickel
- Pearl nickel plating
- Chrome plating
- Workpiece
- polishing
- wax removal
- Hot immersion degreasing
- Cathode
- Anode
- Electrolytic degreasing
- Weak acid etching
- First chemical zinc immersion
- Zinc removal
- Second chemical zinc immersion
- Alkaline bright copper
- Bright nickel
- Pyrophosphate copper (optional)
- Acidic bright copper (optional)
- Bright nickel
- Pearl nickel plating
- Chrome plating
Pearl Chrome Plating Processing Pricing Information
The price of pearl chrome plating is similar to that of electroplating adom-chrome, as follows
Minimum Charge
Generally between 10-20 USD;
Charge per piece
For small batch sizes, the price per piece depends on the size of the workpiece and the number of workpieces in the current batch. The larger the quantity, the lower the unit price.
Charge by weight
For larger/heavier batches of workpieces, the price is generally around 2-3 USD/kg.
Pearl Chrome Plating Processing - Production Equipment Showcase
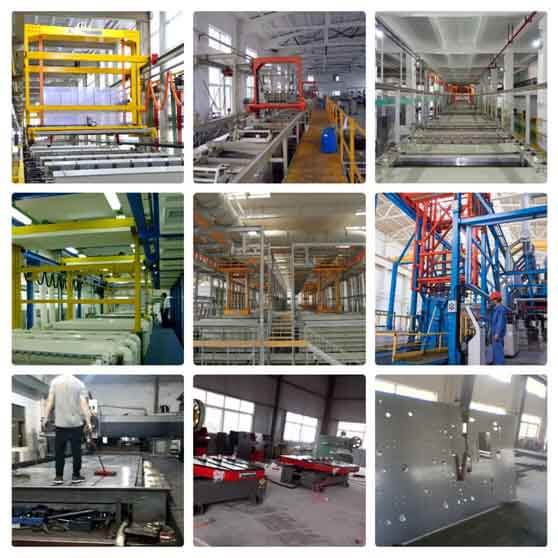
Pearl Chrome Plating Processing - Inspection Equipment Display
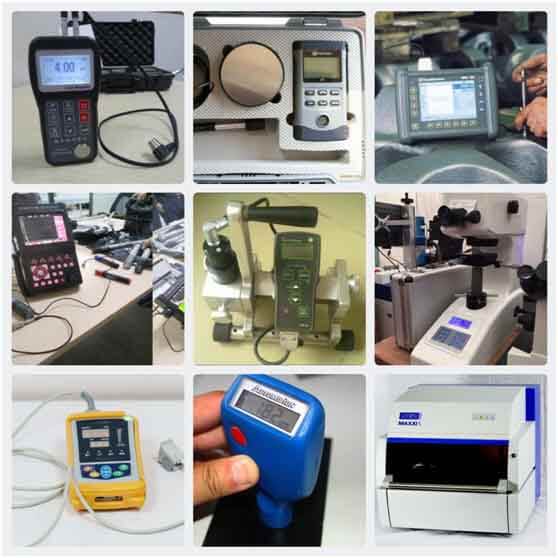
Pearl Chrome Plating Processing Sample Cases
Here are some sample cases for pearl chrome plating
Motorcycle parts
Pearl chrome plating can be used on motorcycle parts to create a unique, iridescent finish that is highly durable and resistant to corrosion. Examples include handlebars, exhaust pipes, and engine covers.
Musical instruments
Pearl chrome plating can be used on brass or other metal musical instruments to create a striking, reflective finish that enhances the instrument's appearance and protects it from wear and tear. Examples include trumpet bells, saxophone bodies, and guitar hardware.
Jewelry
Pearl chrome plating can be used on metal jewelry to create a lustrous, high-shine finish that is resistant to scratches and tarnish. Examples include rings, necklaces, and bracelets.
Decorative accents
Pearl chrome plating can be used on a wide range of decorative accents, such as lamp bases, picture frames, and decorative hardware, to create a unique, eye-catching finish that is both beautiful and durable.
Automotive parts
Pearl chrome plating can also be used on automotive parts, such as rims, grilles, and emblems, to create a distinctive, high-end look that is highly resistant to corrosion and wear.
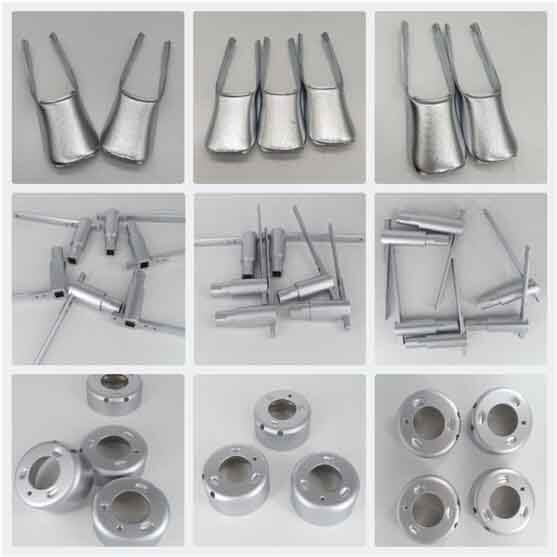
Precision Hard Chrome Plating
Introduction to the Process of Precision Hard Chrome Plating
Special note: Flash chrome plating process
Process for precision hard chrome plating:
- Mechanical pre-treatment (polishing)
- pre-degreasing
- hanging the workpiece
- installing masking materials (if local plating is needed)
- degreasing
- rinsing with water
- Rust removal
- rinsing with water
- Anodic corrosion
- hard chrome plating
- rinsing with water
- blowing with air
- removing masking materials.
Precision Hard Chrome Plating Processing Fee Schedule
Minimum charge:
generally between 10-20 US dollars;
Charge per item
the price per item still depends on the size of the workpiece and the current batch quantity. The larger the quantity, the lower the unit price;
Charge by weight
for larger workpieces, the charge is usually around 2-5 US dollars per kilogram. For some large steel plates, such as the workbench of large equipment, the price can even be as low as 1 US dollar per kilogram.
Precision Hard Chrome Plating Processing: Production Equipment Showcase.
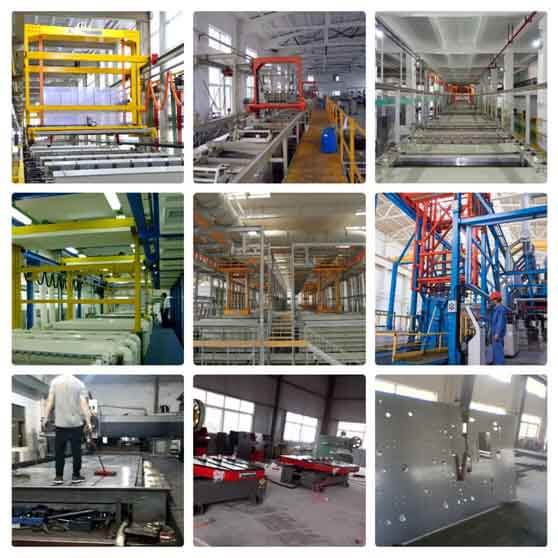
Precision Hard Chrome Plating Processing and Inspection Equipment Display
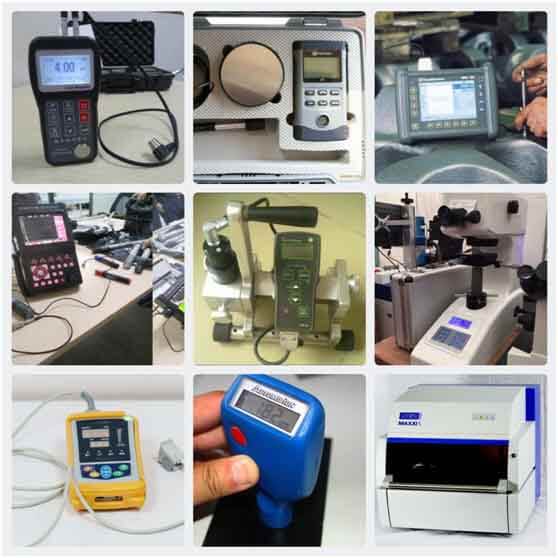
Precision Hard Chrome Plating Processing Sample Cases
Here are some sample cases of precision hard chrome plating
Hydraulic cylinders
Precision hard chrome plating can provide hydraulic cylinders with a wear-resistant, corrosion-resistant surface protection, prolonging their service life.
Aerospace components
Precision hard chrome plating can provide aerospace components with high temperature, high pressure, and corrosion-resistant surface protection, improving their performance and service life.
Printing rollers
Precision hard chrome plating can increase the hardness and wear resistance of printing rollers, allowing them to maintain accurate patterns and quality for longer periods of time.
Injection molding components
Precision hard chrome plating can improve the surface hardness and wear resistance of injection molding components, increasing the service life of the mold and improving its adhesion to plastics.
Diesel engine components
Precision hard chrome plating can provide diesel engine components with wear resistance and corrosion protection, improving their durability and performance.
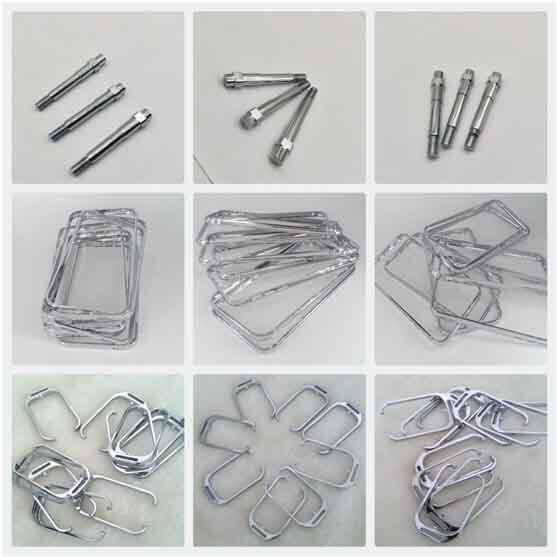
Free Sample
Explore Other Services

Bright Tin Plating
Bead Blasting, also known as abrasive blasting or sandblasting,typically involves the use of compressed air to propel abrasive particles from a nozzle and direct them onto the surface to be

Anodizing
Aluminum Anodized Finish (Aluminum Anodizing) Brief introduction to the aluminum anodizing process Anodic oxidation, also known as aluminum anodizing, refers to the electrochemical oxidation of metals or alloys. It is

Paint Spraying
Spray Painting processing is a method of applying paint or other coatings onto surfaces of various materials, such as wood, metal, plastic, or glass. The purpose of painting can be