Metal Passivation
Metal Passivation
Introduction to Passivation Processing
Passivation refers to the process of treating the metal with a strong oxidant or electrochemical method to oxidize its surface, making it passive, i.e., transforming the metal surface into a state that is not easily oxidized to slow down the metal’s corrosion rate. In addition, there is a phenomenon called passivation, which refers to an active metal or alloy whose chemical activity is greatly reduced and becomes a noble metal state.
If the corrosion product generated by the metal due to the action of the medium has a dense structure, forming a thin film (often invisible) that tightly covers the surface of the metal, the surface state of the metal changes, and the electrode potential of the metal significantly jumps in the positive direction, resulting in a corrosion-resistant passive state. For example, the standard potential of Fe → Fe2+ is -0.44V, but after passivation, it jumps to +0.5~1V, showing the corrosion resistance of noble metals. This thin film is called a passivation film.
Metal passivation can also be a spontaneous process, such as the formation of a layer of insoluble compound, i.e., an oxide film, on the metal surface. In industry, passivation agents (mainly oxidants) are used to passivate metals and form a protective film.
Common examples of passivation include the passivation of iron and aluminum with cold concentrated sulfuric acid and cold concentrated nitric acid.
Passivation is a chemical process that is used to help prevent corrosion and improve the durability of metal parts. The process involves the application of a thin layer of oxide to the surface of the metal, which acts as a protective barrier against corrosion. This oxide layer is created by treating the metal surface with an acid solution, such as nitric acid, which removes any free iron and other contaminants from the surface. The result is a clean, smooth surface that is less susceptible to corrosion and more resistant to wear and tear.
Passivation is commonly used on stainless steel, as well as other metals that are prone to corrosion, such as aluminum and titanium. The process is typically performed after the metal parts have been machined, welded, or otherwise processed, as these processes can introduce contaminants and damage the surface of the metal.
Passivation can be performed using a variety of techniques, including immersion, spraying, and wiping. The choice of technique will depend on the size and shape of the parts being treated, as well as the specific requirements of the application. In some cases, passivation may be followed by additional treatments, such as coating or painting, to further enhance the durability and corrosion resistance of the parts.
Overall, passivation is an important process for ensuring the longevity and reliability of metal parts in a variety of applications, from aerospace and automotive to medical and food processing.
Passivation principle
Passivation advantage
Since the passivation process is carried out in a non-reactive state, the passivation agent can be repeatedly added and used, so its service life is longer and the cost is more economical.
Passivation promotes the formation of an oxygen molecule structure passivation film on the metal surface, the film is dense and its properties are stable. It also has a self-repairing effect in the air. Therefore, compared with the traditional method of coating rust preventive oil, the passivation film formed is more stable and has better corrosion resistance.
In the oxide layer, most of the charge effects are directly or indirectly related to the thermal oxidation process. In the temperature range of 800-1250°C, the thermal oxidation process carried out with dry oxygen, wet oxygen or water vapor has three continuous stages. Firstly, oxygen in the ambient atmosphere enters the already formed oxide layer. Then, oxygen diffuses inward through silica, and when it reaches the SiO2-Si interface, it reacts with silicon to form new silica. This process of oxygen entry-diffusion-reaction continues, and the silica near the interface continuously transforms into silica dioxide, and the oxide layer grows into the silicon wafer at a certain rate.
Passivation process flow
- Degreasing cleaning
- Rinse with water
- Acid pickling activation
- Rinse with water
- Passivation
- Rinse with water
- Pure water rinse
- Dehydration drying
- Package immersion in passivation solution, use the original solution. The soaking time is recommended to be 60 minutes or more.
Operating Procedures
Water Rinse
Use pure water to circulate and rinse the pipeline through the circulation pump, while discharging the water. The time should not be less than 20 minutes.
Alkali Preparation
First, connect the container filled with alkaline solution to the circulation pump and the pipeline system, and connect a hose to the end to the alkaline container, ensuring that the connection and container are tight and leak-free. After confirmation, put the calculated amount of pure water into the container first, and then slowly put in the calculated amount of solid alkali. Stir well with a stirring rod. Turn on the power of the water pump and disconnect the control switch to prepare for alkali washing. The mixing personnel should wear acid-alkali masks to prevent injury to personnel. The container filled with alkali should be intact, without any leakage, and well connected to the pipeline interface.
Alkali Washing
Close the control switch, use the circulation pump to draw the alkaline solution into the pipeline system, and circulate and rinse the pipeline for about 30 minutes. During the alkali washing process, a dedicated person should check (checking method: contact the test paper with the solder joint. If there is no discoloration, there is no leakage). If a leak is found, immediately notify the person in charge of the pump to stop the pump and discharge the alkaline solution at the water outlet near the leak point, and carry out related treatments such as welding at the leak point. After the treatment, the alkali washing can continue. The alkaline solution on the ground and ceiling should be wiped clean with a dry cloth.
Water Rinse
Use pure water to circulate and rinse the pipeline through the circulation pump, while discharging the water, until the discharged water is neutral. For the circulated alkaline solution, use another container to store it temporarily for neutralization and discharge with acid.
Acid Preparation
First, connect the container filled with acid to the circulation pump and the pipeline system, and connect a hose to the end to the acid solution container, ensuring that the connection and container are tight and leak-free. After confirmation, put the calculated amount of pure water into the container first, and then slowly put in the calculated amount of acid. Stir well with a stirring rod. Turn on the power of the water pump and disconnect the control switch to prepare for pressure testing. The mixing personnel should wear acid-alkali masks to prevent injury to personnel. The container filled with acid should be intact, without any leakage, and well connected to the pipeline interface. If possible, the container can also be placed outdoors. If the container leaks, flush it with water at the leaking point until the acid washing is completed.
Pickling
Close the control switch and use the circulation pump to draw the acid solution into the piping system for circulation flushing, which takes about 60 minutes. During the pickling process, someone should inspect each weld joint (inspection method: use test paper to touch the joint, if there is no color change, there is no leakage). If a leak is found, the pump operator should be immediately notified to stop the pump, and water should be emptied at the leak point. The leak point should be wrapped with tape and a water bucket should be placed below it to catch the leaked acid (if unable to use a bucket to catch the acid, a cloth soaked in dilute alkali solution should be placed below the leak point). After all the acid in the piping system is discharged by flushing the system with pure water using the circulation pump, the leak point can be repaired by welding or other relevant treatments. After treatment, pickling can continue. Acid that flows onto the ground or ceiling should be wiped clean with a dry cloth, and acid that flows into gaps should be neutralized with dilute alkali solution before being wiped clean with a dry cloth.
Water flushing
Use pure water to circulate flush the piping system with the circulation pump, while discharging the water until it is neutral.
Passivation preparation
Connect the acid storage container, circulation pump, and piping system together, and connect a hose to the end of the system that leads to the acid solution container, ensuring that the connection and container are tight and leak-free. After confirming the connection, pour the calculated amount of pure water into the container first, and then slowly add the calculated amount of acid. Stir the mixture thoroughly with a stirrer. Turn on the water pump power and disconnect the control switch to prepare for pressure testing.
Passivation
Close the control switch and use the circulation pump to draw the acid solution into the piping system for circulation flushing, which takes about 120 minutes. During the passivation process, someone should inspect each weld joint (inspection method: use test paper to touch the joint, if there is no color change, there is no leakage). If a leak is found, the pump operator should be immediately notified to stop the pump, and water should be emptied at the leak point. The leak point should be wrapped with tape and a water bucket should be placed below it to catch the leaked acid (if unable to use a bucket to catch the acid, a cloth soaked in dilute alkali solution should be placed below the leak point). After all the acid in the piping system is discharged by flushing the system with pure water using the circulation pump, the leak point can be repaired by welding or other relevant treatments. After treatment, passivation can continue. Acid that flows onto the ground or ceiling should be wiped clean with a dry cloth, and acid that flows into gaps should be neutralized with dilute alkali solution before being wiped clean with a dry cloth.
Water flushing
Use pure water to circulate flush the piping system with the circulation pump, while discharging the water until it is neutral.
Discharge of waste liquid
The waste acid and waste alkali should be neutralized to neutral or near neutral before being directly discharged, except for those that require further treatment.
If pickling and passivation are carried out in one treatment, prepare the solution according to the recipe requirements, and then carry out the passivation process as described above. After treatment, the system should be flushed clean with pure water.
Testing Methods
Appearance Inspection
The pickling and passivation surface should be uniform silver-white. There should be no obvious corrosion marks, and there should be no oxidation color or uneven spots on the surface of welds and heat-affected zones.
Residual Solution Test
Use phenolphthalein paper to check the degree of surface residual solution washing. The pH value should be neutral to be qualified.
Blue Spot Test
The quality of pickling and passivation treatment can also be checked by blue spot test as needed. The solution is made by adding 1g of potassium ferricyanide K3[Fe(CN6)], 3ml of (65%-85%) nitric acid and 100ml of water. Then soak the solution in filter paper and stick it on the tested surface, or directly drop the solution on the tested surface. Observe the blue spot on the surface within 30 seconds. If there is a blue spot, it is unqualified. It should be noted that the test should be carried out after the pickling and passivation surface is basically dry, and the test solution should be washed clean after the test.
The basic principle of the blue spot test is: if the passivation film on the surface is incomplete or contaminated by iron ions, free iron ions will be present. Therefore, the following reaction will occur: fe2k3[Fe(CN)6]=KFE[Fe(CN)6] (dark blue) 2K.
The blue spot test method is generally used in the manufacture of stainless steel chemical containers and is a very strict inspection method. In order to pass the inspection, the process specifications must be strictly followed.
Suggestions
Stainless steel should be placed in a special place and must be covered with wooden boards or rubber. Mixing with carbon steel is strictly prohibited.
Various processing equipment, such as roll bending machines and shearing machines, should be cleaned and the rollers and pressure angles should be coated with paint to ensure that stainless steel does not come into direct contact with carbon steel.
The fixtures should be made of stainless steel or stainless steel washers.
Stainless steel wire brushes should be used for pickling steel wire brushes.
Through the above process of pickling and passivation of stainless steel, everyone has a rough understanding of pickling and passivation of stainless steel. The actual operation may be adjusted slightly due to different materials, temperatures, and concentrations.
Passivation Processing Production Equipment Exhibition.
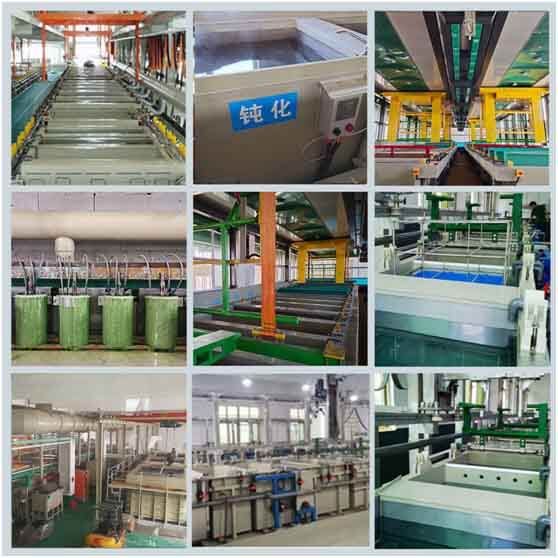
Passivation Processing - Display of Inspection Equipment
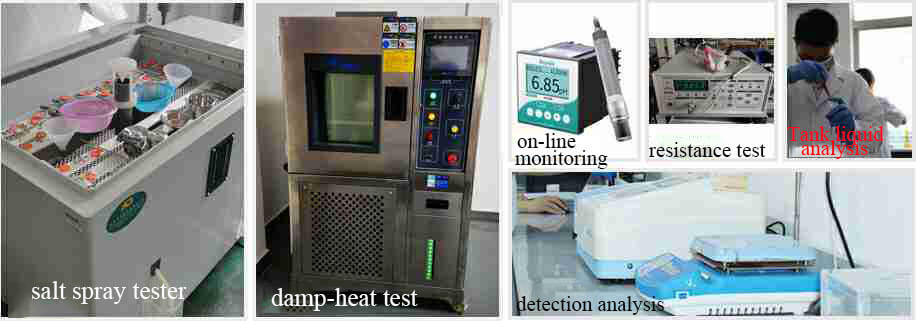
Passivation Processing Sample Cases
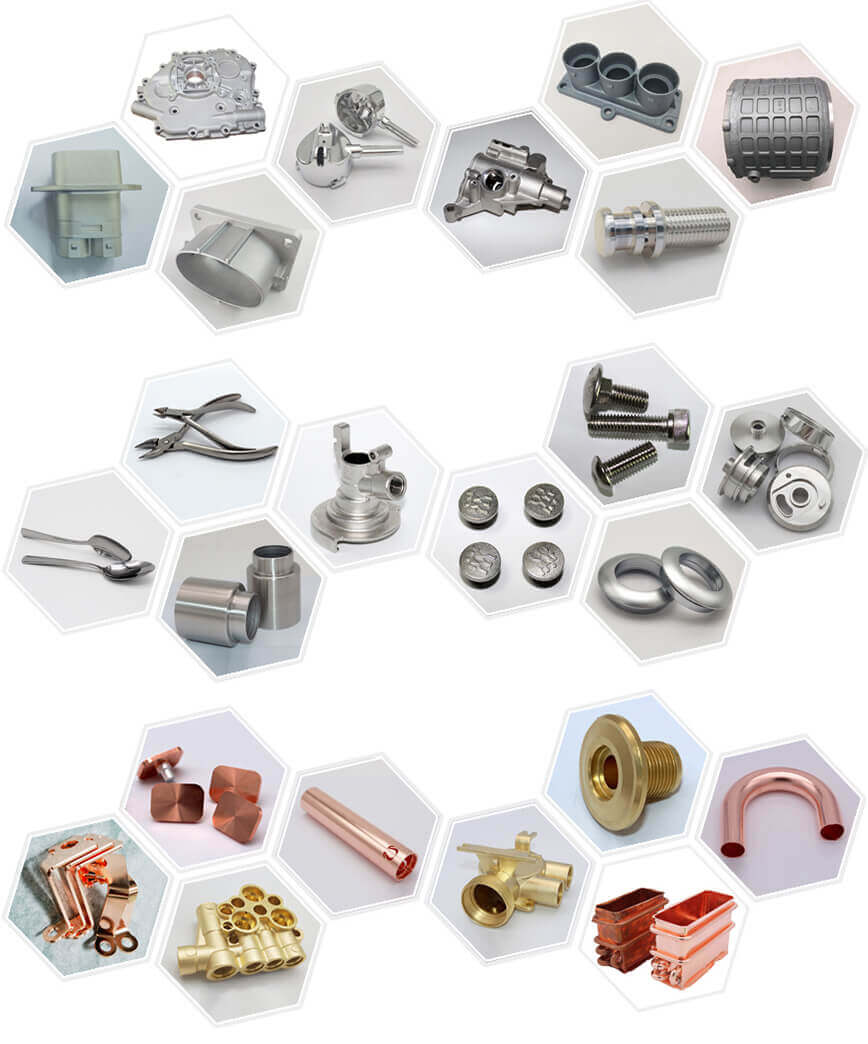
Free Sample
Explore Other Surface Finish
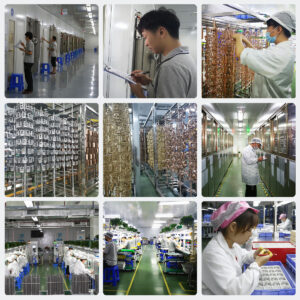
PVD Coating
The vapor phase deposition method can be divided into physical vapor deposition (PVD), chemical vapor deposition, and discharge polymerization. Today, we will mainly introduce the physical vapor deposition method, commonly

Paint Spraying
Spray Painting processing is a method of applying paint or other coatings onto surfaces of various materials, such as wood, metal, plastic, or glass. The purpose of painting can be

Anodizing
Aluminum Anodized Finish (Aluminum Anodizing) Brief introduction to the aluminum anodizing process Anodic oxidation, also known as aluminum anodizing, refers to the electrochemical oxidation of metals or alloys. It is