Paint Spraying
Spray Painting
Painting Processing - Introduction to the Process
Spray Painting processing is a method of applying paint or other coatings onto surfaces of various materials, such as wood, metal, plastic, or glass. The purpose of painting can be to provide protection, decoration, or functional properties such as anti-corrosion or anti-friction.
The painting process typically involves the following steps
Surface preparation
The surface to be painted must be cleaned and prepared for painting. This may involve removing rust, old paint, or other contaminants, and sanding or priming the surface to improve adhesion.
Mixing the paint
The paint or coating material must be mixed thoroughly to ensure uniform consistency and color.
Application
The paint is applied to the surface using a variety of methods, such as spraying, brushing, rolling, or dipping.
Drying and curing
The paint must be allowed to dry and cure before the object can be used or further processed. The drying time depends on factors such as temperature, humidity, and the type of paint used.
Inspection and finishing
After the paint has dried, the surface is inspected for defects or imperfections, and any necessary touch-ups or corrections are made. Finally, a topcoat or clear coat may be applied for added protection or to achieve a desired finish.
Spray Painting Processing - Process Flow
Each process has its own purpose and requirements
Hanging of Workpiece
Hang the workpiece that needs to be sprayed on the spray hanging line.
Requirements
Before hanging, self-inspect the workpiece to avoid hanging defective workpieces with concave-convex surface, deformation, rust, etc. The workpiece must be hung stably, and rough handling causing deformation and other quality defects is strictly prohibited.
Surface Treatment
Pre-degreasing
Remove oil and debris from the surface of the workpiece.
Requirements
Adjust the alkalinity and spray pressure of the pre-degreasing solution according to the process requirements. Clean the surface oil on the tank liquid regularly and maintain it as required.
Main degreasing
Thoroughly remove oil stains from the surface of the workpiece that was not cleaned during pre-degreasing.
Requirements
Adjust the alkalinity and spray pressure of the degreasing solution according to the process requirements. Clean the surface oil on the tank liquid regularly and maintain it as required.
Water washing 1
Clean the surface alkaline solution, oil stains, and impurities of the workpiece after degreasing.
Requirements
Adjust the pH value (7-9) and spray pressure of the washing solution according to the process requirements. Set up the overflow of the washing tank and maintain it as required.
Water washing 2
Thoroughly clean the surface alkaline solution, oil stains, and impurities of the workpiece after degreasing.
Requirements
Adjust the pH value (7-8) and spray pressure of the washing solution according to the process requirements. Set up the overflow of the washing tank and maintain it as required.
Surface Adjustment
Adjust the surface of the workpiece to promote the growth of the phosphating film.
Requirements
Adjust the pH value (8-9) and spray pressure of the adjustment solution according to the process requirements. Maintain and upkeep as required.
Phosphating
Form a phosphating film on the surface of the workpiece to ensure good adhesion between the coating and the workpiece.
Requirements
Adjust the total acid, free acid, accelerator concentration, and spray pressure of the phosphating solution according to the process requirements. Maintain and upkeep as required.
Water washing 3
Clean the phosphating residue and impurities on the surface of the workpiece after phosphating.
Requirements
Adjust the pH value (6-7) and spray pressure of the washing solution according to the process requirements. Set up the overflow of the washing tank and maintain it as required.
Water washing 4
Thoroughly clean the phosphating residue and impurities on the surface of the workpiece after phosphating.
Requirements
Adjust the pH value (6-7) and spray pressure of the washing solution according to the process requirements. Set up the overflow of the washing tank and maintain it as required.
Water Blowing
Blow dry the water on the surface of the workpiece to ensure that the workpiece is dried before entering the oven.
Requirements
Requirements: Wear latex gloves when blowing water. Blow dry the water droplets on the surface of the workpiece and the water accumulation areas.
Pre-spray Inspection
Inspect the workpiece before spraying.
Powder Spraying
Apply powder coating to the workpiece.
Post-spray Inspection
Inspect the workpiece after spraying.
Curing
Bake the workpiece at a suitable temperature and time to cure the coating.
Finishing
Polish the finished workpiece.
Drying oven
Dry the surface of the cleaned workpiece.
Requirements
Close the drying oven door before heating, ensure that the workpiece is heated to the appropriate temperature within the process range before entering the oven, regularly check whether the drying temperature is within the process range, and ensure that there are no obstructions that may prevent the workpiece from passing through the hanging chain.
Pre-spray inspection
Pre-spray inspection: Perform a full inspection on the workpiece before spraying powder.
Requirements
Perform a visual inspection on the workpiece before spraying powder. Wear CT gloves or canvas gloves when handling phosphatized workpieces. When removing defective workpieces, handle them gently and place them properly. Report any quality problems with batches to the relevant responsible personnel.
Powder coating
Use an electrostatic generator to generate static electricity, which is then amplified by the high voltage pack and discharged by the spray gun electrode to produce an electric field strength that attracts the negatively charged powder particles to the positively charged workpiece, resulting in a powder coating that solidifies into a film.
Requirements
Wear necessary protective equipment (such as dust masks and anti-static work clothes) before entering the powder room. Close doors and windows, adjust the humidity (40-60%) and temperature (23-25 degrees) of the powder room, and adjust the powder coating process parameters according to the requirements before spraying. Follow the responsibilities of the powder coating position and strengthen the monitoring of the powder coating process.
Post-spray inspection
Improve the surface quality defects of the workpiece after powder coating and provide feedback on any abnormal quality information.
Requirements
Blow off any impurities and orange peel on the surface of the workpiece after powder coating and provide feedback on the quality information. When blowing off the surface of the workpiece, the nozzle should be held at a 60-degree angle to the surface of the workpiece and the blowing force should not be too strong.
Curing oven
After powder coating, the workpiece enters the curing oven to melt, level, and solidify the powder coating into a film.
Requirements
Close the curing oven door before heating, ensure that the workpiece is heated to the appropriate temperature within the process range before entering the oven, and strictly prohibit any hanging from stopping without special circumstances.
Degreasing
Cleaning
After degreasing, wash with water.
Rust removal
Use acid rust removal to remove rust on the surface of steel using an immersion tank. The acid rust removal solution formula consists of 31% industrial hydrochloric acid and 3% corrosion inhibitor, at room temperature. The treatment time is 3-8 minutes. After treatment, visually check if rust exists after washing with water.
Cleaning
After rust removal, wash with water.
Surface conditioning
Used for surface treatment before phosphating, using an immersion tank (surface conditioning agent is a white powder). When preparing the tank solution, slowly add 1-3 kg per ton of the conditioning agent, stir to dissolve. The working conditions for the conditioning agent are pH 7.5-9.5, temperature at room temperature, and time for half a minute.
Phosphating
Use zinc-based phosphating solution to phosphatize the surface of steel using an immersion tank. The WF phosphating agent is divided into A agent-tank preparation agent, B agent-supplementary agent, and C agent-promoter.
1. Tank solution preparation
add water to the tank to 3/4 of the volume, add A agent at a rate of 25-30 kg per ton, then add sodium hydroxide dissolved in hot water (0.7 kg per ton), and finally add water to the working solution to confirm acidity. When the phosphating is about to start, add C agent at a rate of 0.5-0.7 kg per ton, stir evenly and set aside.
2. Process parameters
total acidity 18-35 points, free acidity 0.5-1.5 points, promoter 2-3 points, temperature 35-45â, immersion time 5-10 minutes. The inspection method is to wash with water and visually check that the phosphating film should be a slate gray color, fine crystals, no spots, and no solid deposits of oxides remaining on the unphosphatized parts. After phosphating, thorough washing and quick drying are necessary.
3. Management of phosphating solution
If the total acidity of the phosphating solution increases after continuous use, it can be diluted with water. If the total acidity decreases, 1 point can be increased by adding 1.6 kg/ton of B agent. If the free acidity increases, 1 point can be reduced by adding 0.4 kg/ton of sodium hydroxide, and 1 point can be increased by adding 6 kg/ton of B agent when the free acidity decreases. If the tank temperature is too low, or too much C agent is added, or insufficient B agent is supplemented, the free acidity may drop to below 0.4 points. In this case, 0.9 kg/ton of B agent should be added to increase the free acidity by 0.1 point. When the C agent is added too much and a colored film is produced, stirring or heating can be used to accelerate its natural volatilization.
Cleaning
After phosphating, rinse with water.
Drying
After phosphating and cleaning, dry the workpiece before painting.
Painting
Drying
Inspection of Spray Film Quality
Painting Processing - Production Equipment Showcase

Spray Painting Process and Production Equipment Display
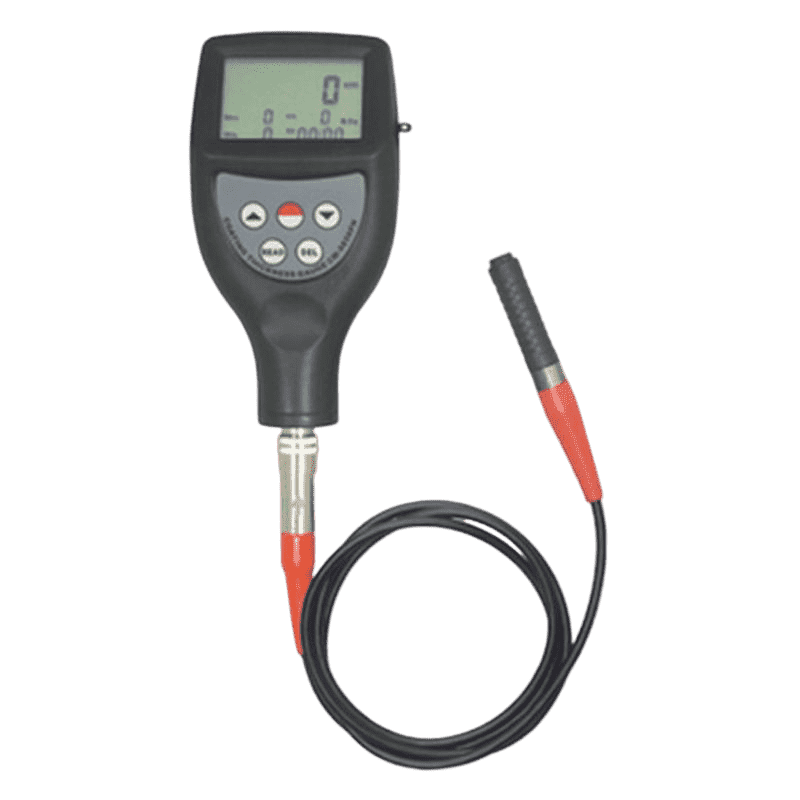
Mirror Polishing Process and Sample Cases
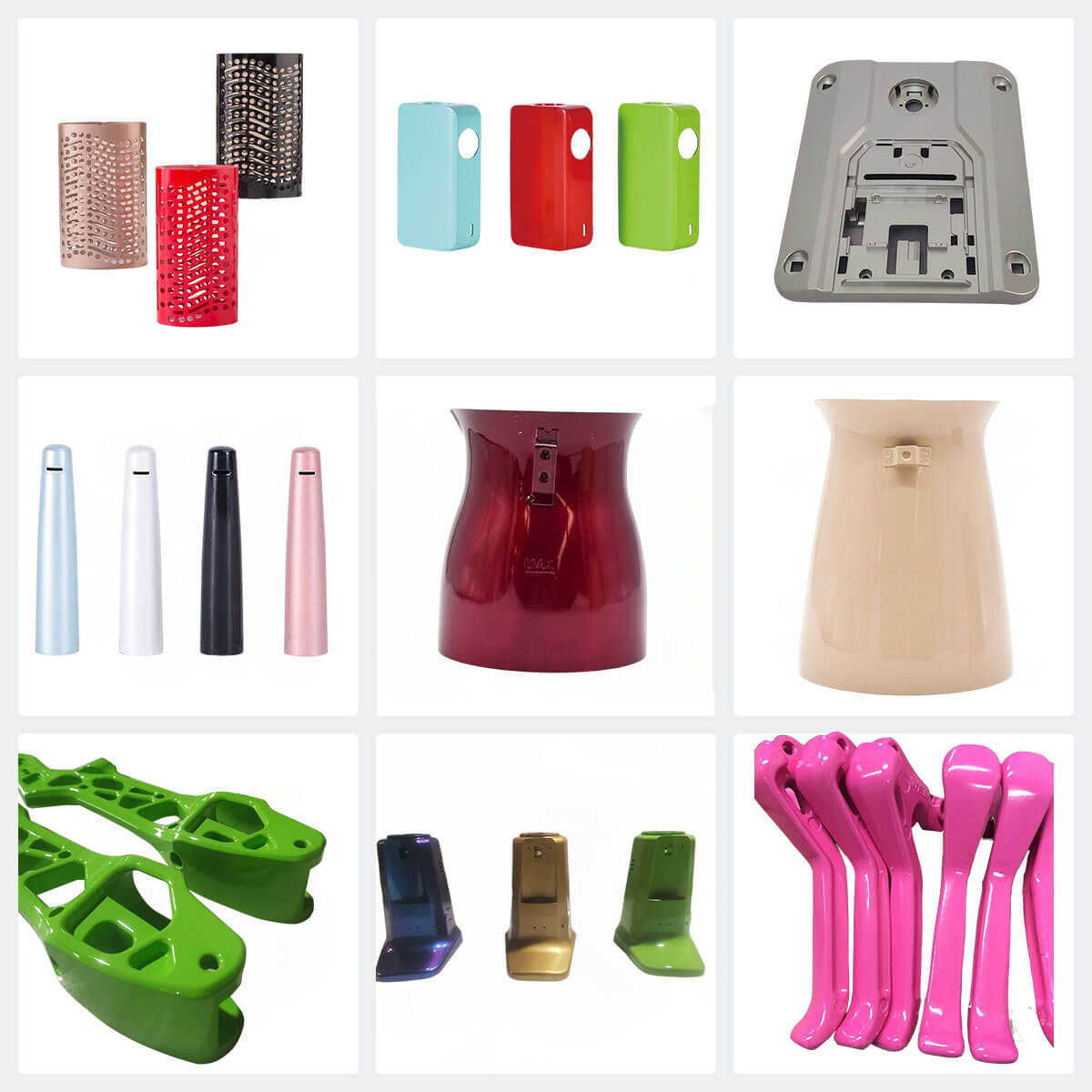
Free Sample
Explore Other Surface Finish

Chrome Plating
Bead Blasting, also known as abrasive blasting or sandblasting,typically involves the use of compressed air to propel abrasive particles from a nozzle and direct them onto the surface to be

Chemical Nickel Plating
Bead Blasting, also known as abrasive blasting or sandblasting,typically involves the use of compressed air to propel abrasive particles from a nozzle and direct them onto the surface to be

QPQ Coating
Phosphating is a process in which a workpiece is treated in a phosphoric acid salt solution containing manganese, iron, and zinc to form a layer of insoluble phosphate film on