Powder Coating
Powder Coating
Introduction to the powder coating process.
Powder coating is a surface treatment method that involves spraying plastic powder onto a part. Powder coating, also known as electrostatic powder coating, uses the electrostatic attraction method to make the powder coating adhere to the metal surface. After high-temperature curing, a protective film is formed on the surface, and the entire set of processes for this technology is called powder coating. Compared with ordinary spray painting surface treatment, the advantages of this technology lie in its advanced process, high energy efficiency, safety and reliability, and bright color. Therefore, it is often applied in the fields of light industry and home decoration. The working principle is to charge the plastic powder through a high-voltage electrostatic device and, under the action of an electric field, spray the coating onto the surface of the workpiece. The powder will be uniformly adsorbed on the surface of the workpiece, forming a powdery coating. The powdery coating will then be baked at high temperature, flattened, and cured, and the plastic particles will melt into a dense final protective coating with varying effects, firmly adhering to the surface of the workpiece. Powder coating products are mainly used for indoor use, and the paint film shows a flat or matte effect. The spray powder mainly includes acrylic powder, polyester powder, etc.
Powder coating processing, process flow
- Polishing
- Alkaline wash 1
- Water wash 1
- Water wash 2
- Acid wash
- Water wash 3
- Phosphating 1
- Surface adjustment
- Phosphating 2
- Water wash 4
- Puttying
- Drying
- Polishing
- Air blowing to remove dust
- Spraying plastic powder
- Small air blowing to remove excess plastic powder
- Drying
- Cooling in the oven environment
- Repairing with putty
- Drying
- Packaging.
Powder coating Process
Preparation
Parts
Equipment
Electrostatic generator
Check whether the power supply of the electrostatic generator is normal and whether the voltage output is normal.
Powder barrel
Check whether the powder is in suspension.
Spray gun, powder tube, and powder pump
Check whether they are cleaned properly and whether there is any remaining powder.
Air compressor
Check whether the compressor is working properly and whether the air pressure meets the requirements.
Compressed air freeze dryer and air path oil-water separation device
Check whether they are working properly and whether the oil and water discharge devices are working properly.
Test spraying
Check whether the powder is applied correctly and whether the voltage, air pressure, and equipment operation are normal.
Process
Electrostatic voltage: 30-70KV
Air pressure: 0.6-0.8MPa
Powder supply: 150-250g/min (adjustable)
PowderCoating Process
Spray gun debugging
Turn on the electrostatic generator, and adjust the powder output through the air intake. Gradually increase the air pressure from zero and observe whether the powder output is uniform. Spraying: The distance between the spray gun and the parts should be 10-20cm. When spraying welding seams or areas that are not easy to powder, the spray gun can be closer to the parts. During spraying, the spray gun should move horizontally or vertically back and forth on the surface of the parts, and the speed should be uniform. The powder thickness in concealed parts or welding seams should be slightly thicker.
Drying tunnel
The drying tunnel should be cleaned regularly, and the temperature should be uniform. Adjust the temperature to 180℃-230℃ according to the requirements of powder solidification. The circulation speed of the parts in the drying tunnel should be adjusted according to the solidification time of the powder.
Inspection
Coating thickness: 60-100um, thickness should be uniform.
Coating hardness: 2H
Coating strength:
a
Fix the test parts so that there is no shaking when they are impacted.
b
The impactor is vertically placed at the test position of the test piece, and a heavy hammer with a steel ball of 12mm in diameter and an outer diameter of 17mm, and a total weight of 100g is dropped freely from a height of lm in the impactor with an inner diameter of 19mm to impact the coating of the test piece.
c
Move away the impactor, and there should be no peeling or cracking in the coated area. Repeat the impact test three times at a position not less than 100mm away from the previous test on the same test piece. If one test fails, the part is considered unqualified.
Adhesion:
a
Use a steel needle to scratch 4-6 parallel lines with a spacing of 1mm on the surface of the coating of the test piece, and the scratches should be deep enough to reach the base metal.
b
Scratch 4-6 parallel lines perpendicular to the previous lines with a spacing of 1mm, and the scratches should be made in the same direction.
c
At the intersection of the straight lines, the coating should not peel or fall off.
d
In case of disputes, a magnifying glass with a magnification of no less than 2 times should be used for re-inspection and judgment. powder coating Process
Principle of Electrostatic powder coating:
The powder coating is sprayed onto the surface of the workpiece using electrostatic spray equipment (electrostatic sprayer). Under the action of electrostatics, the powder will evenly adhere to the surface of the workpiece, forming a powdery coating. The powdery coating is then baked at a high temperature to level and solidify, becoming the final coating with various effects (depending on the type of powder coating). The spraying effect is superior to the paint spraying process in terms of mechanical strength, adhesion, corrosion resistance, and aging resistance, and the cost is also lower than that of paint spraying with the same effect. This process involves the process name, process flow/purpose/task and detailed steps, relevant equipment, relevant materials, and the equipment, materials, and services we provide.
Pretreatment Purpose
Remove oil, dust, and rust, and generate a "phosphating layer" on the surface of the workpiece that is corrosion-resistant and can increase the adhesion of the coating. Main process steps: degreasing, rust removal, phosphating, and passivation. After pretreatment, the surface of the workpiece is not only free of oil, rust, and dust but also a rough and non-rusting gray phosphating film formed on the original shiny silver surface, which can both prevent and increase the adhesion of the powder coating. Relevant equipment: pretreatment tank (concrete tank, the number is equal to the number of pretreatment processes). Relevant materials (chemicals): sulfuric acid (H2SO4), hydrochloric acid (HCl), caustic soda (Na2CO3), acid-based degreaser, phosphating solution, passivation solution.
Electrostatic Spray Purpose
Uniformly spray the powder coating onto the surface of the workpiece. A high-performance electrostatic sprayer should be used to complete the spraying of special workpieces (including locations that are prone to electrostatic shielding). Process steps: Using the principle of electrostatic adsorption, uniformly spray a layer of powder coating on the surface of the workpiece. The fallen powder is recovered by the recovery system and can be reused after sieving. Relevant equipment: 1 electrostatic sprayer (electrostatic powder spraying machine) or multiple machines, 2 spray booths with powder recovery function (single workstation or double workstation), 3 air compressors, and compressed air purifiers (oil-water filter). Relevant materials: powder coating (powder coating raw materials, commonly known as "plastic powder," with different effects and colors such as high gloss, bright gloss, semi-matte, matte, sand texture, hammer texture, and crack texture).
High-Temperature Curing Purpose
Heat the powder coating on the surface of the workpiece to the specified temperature and keep it warm for a corresponding time to melt, level, and solidify it, thereby obtaining the desired surface effect of the workpiece. Process steps: Push the sprayed workpiece into the curing oven, heat it to the predetermined temperature (usually 185 degrees), and keep it warm for a corresponding time (15 minutes). Take out the workpiece after cooling, and it becomes the finished product. Note: Heating and control systems (including various heating methods such as electric heating, fuel oil, gas, and coal)+ insulation box = curing oven. Relevant equipment: curing oven (with automatic control of parameters such as temperature, holding time, and heating method can be electric heating, fuel oil heating, gas heating, coal heating, etc., which can be selected according to your needs).
Decorative treatment purpose
to achieve a specific appearance effect on the workpiece after electrostatic sprayings, such as various wood grain patterns, patterns, and increased brightness. Process steps: transfer printing and other processing techniques.
Powder Coating processing equipment display.

Powder coating Testing Equipment Display
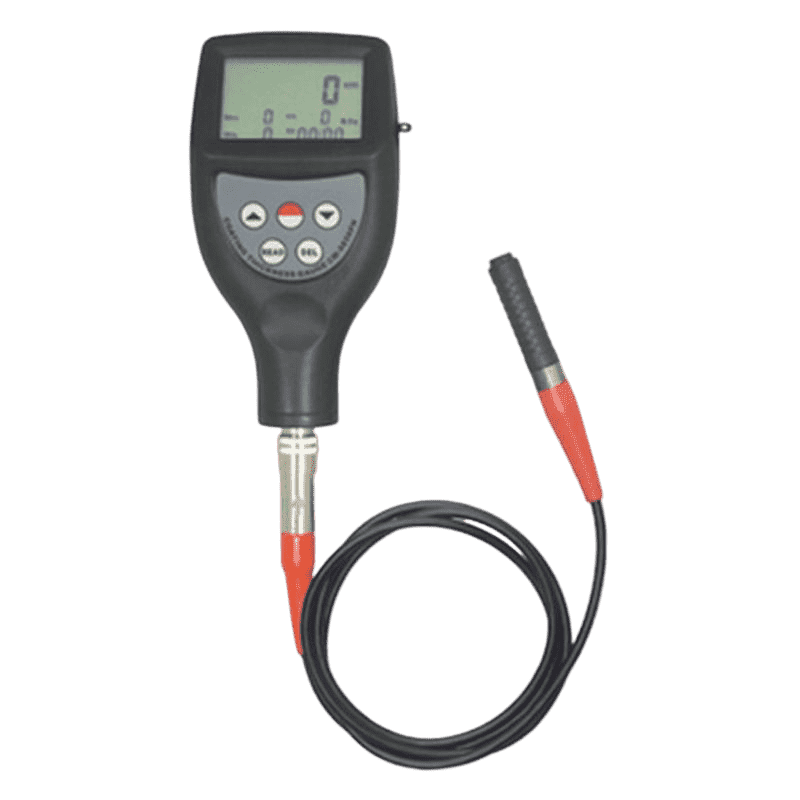
Powder coating Processing Sample Cases

Free Sample
Explore Other Surface Finish

Chemical Nickel Plating
Bead Blasting, also known as abrasive blasting or sandblasting,typically involves the use of compressed air to propel abrasive particles from a nozzle and direct them onto the surface to be

Anodizing
Aluminum Anodized Finish (Aluminum Anodizing) Brief introduction to the aluminum anodizing process Anodic oxidation, also known as aluminum anodizing, refers to the electrochemical oxidation of metals or alloys. It is

Paint Spraying
Spray Painting processing is a method of applying paint or other coatings onto surfaces of various materials, such as wood, metal, plastic, or glass. The purpose of painting can be