PVD Coating
Rose gold PVD plating.
304 stainless steel part (3D printed) with copper-nickel-chromium electroplating base coat and rose gold PVD plating.
304 stainless steel part (3D printed) with copper-nickel-chromium electroplating base coat and rose gold PVD plating.

Plating: Copper-nickel-chromium electroplating, rose gold vacuum plating
Process: Rack plating
Color: Rose gold
Reference price: $0.5 per piece
Difficulties in electroplating this part
Titanium PVD Gold
Yellow Brass Jewelry Components Water Plating

Base Material: Brass H62
Plating: Copper-Nickel-Chromium Undercoat followed by PVD Vacuum Titanium Gold Coating
Process: Hanging Plating
Additional Process: Mechanical Mirror Polishing
Color: Titanium Gold
Film Thickness: 15μm on one side
Electroplating Price: 0.6 USD/piece
What are the advantages of PVD Vacuum Coating?
Uniform and consistent color
Durable surface that maintains a good appearance in various air and direct sunlight conditions
Deep and bright colors
Economical, reducing the time and cost required for cleaning and polishing compared to electroplating brass or gold
Environmentally friendly, avoiding chemical toxicity
Biocompatible
Coating Characteristics:
Resistance of PVD Coatings:
Vacuum Deposition
Introduction to Vacuum Electroplating(PVD) Process
Characteristics of the PVD vacuum electroplating process
Vacuum coating, PVD electroplating, and characteristics of vacuum coating
Characteristics of PVD vacuum coating layer
Resistance of PVD coating
Environmentally friendly process
Vacuum Electroplating(PVD) Process
On the automatic line
Automatic electrostatic dust removal
Automatic surface primer spraying
Infrared (IR) drying
UV surface curing
Down the automatic line
Non-conductive equipment control system
Non-conductive vacuum coating in progress
Non-conductive coating unloading
Automatic spray painting and coloring
Downstream fixture
Vacuum Electroplating(PVD) Equipment Showcase for Production

Vacuum Electroplating(PVD) Inspection Equipment Showcase

Vacuum Electroplating (PVD) Sample Case
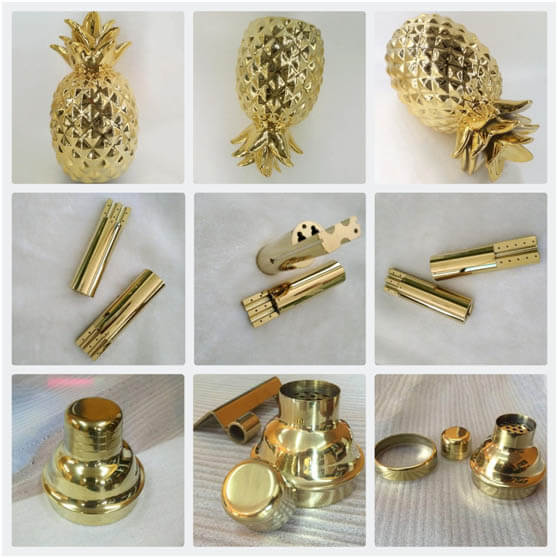
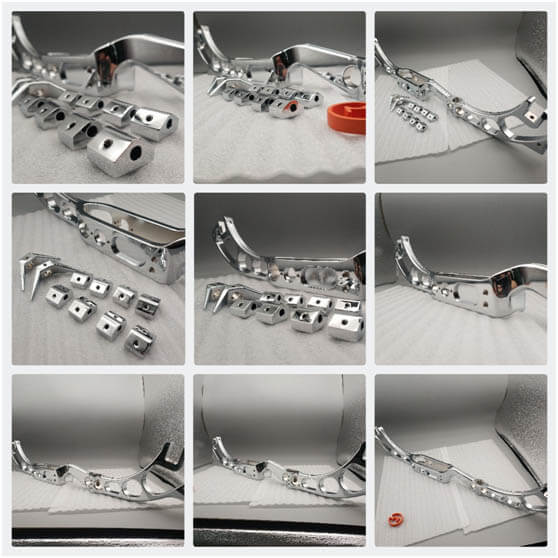

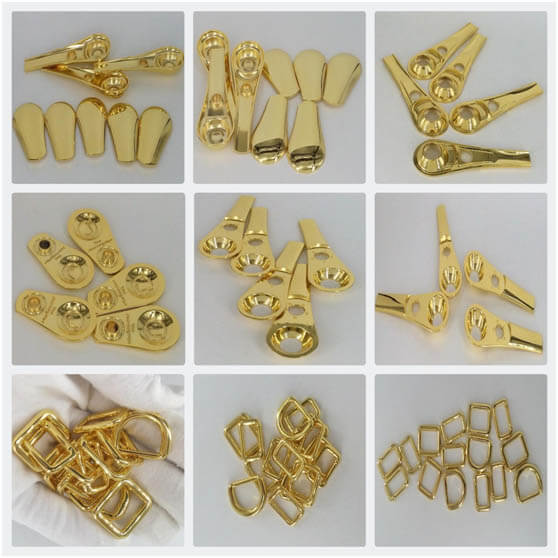


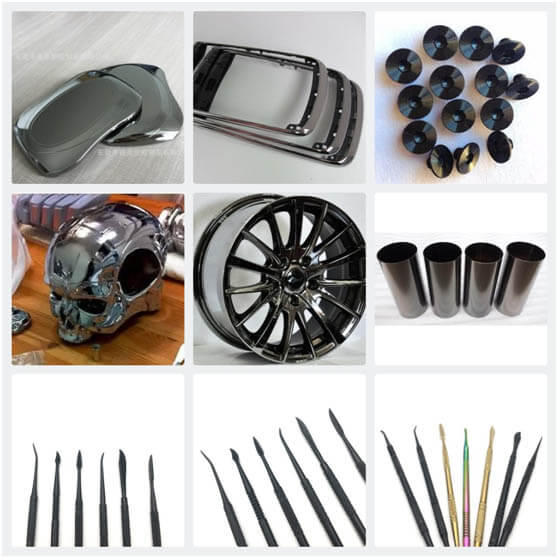
Free Sample
Explore Other Surface Finish

Chemical Nickel Plating
Bead Blasting, also known as abrasive blasting or sandblasting,typically involves the use of compressed air to propel abrasive particles from a nozzle and direct them onto the surface to be
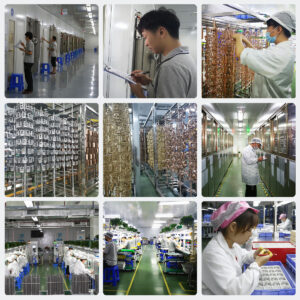
PVD Coating
The vapor phase deposition method can be divided into physical vapor deposition (PVD), chemical vapor deposition, and discharge polymerization. Today, we will mainly introduce the physical vapor deposition method, commonly
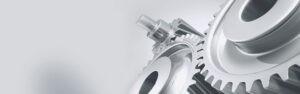
Dacromet Coating
Colorful Dacromet coating processing refers to a special post-treatment process after conventional Dacromet coating processing, which enables the Dacromet coating to exhibit various desired colors such as black, red, blue,