Swiss Turn Machining
Something we share with you about CNC Swiss Turn machining.
Swiss Turn machining is one of the most common modern machining techniques. Its advantages of speed, convenience, and high precision make it highly favored by customers, leading to its widespread application in various material processing fields. The Swiss Lathe is capable of simultaneously performing multiple combined processes such as turning, drilling, boring, tapping, and engraving, primarily used for batch processing of precision hardware, shafts, and other non-standard parts with complex shapes. It is worth noting that the Citizen Swiss Lathe imported from Japan and used by Masion offers higher convenience and efficiency in processing compared to similar products. Its design with a dual-axis layout of cutting tools significantly reduces the processing cycle time by shortening the tool exchange time between the cutting tool and the opposite tool holder, utilizing multiple tool holders with overlapping functionality, effectively moving and overlapping the thread cutting chips, and employing direct spindle indexing during secondary processing, resulting in a substantial reduction in idle time and further enhancing processing efficiency. However, despite these numerous advantages, the Swiss Lathe is generally more suitable for batch processing of long rod materials and is not as suitable for machining large-diameter single pieces like traditional walking tools; it is limited to diameters of 32mm and below. Moreover, the Swiss Lathe places relatively high demands on material roundness and straightness, as it involves precision machining throughout the main spindle, chuck, guide sleeve, and other components, highlighting its precision machining characteristics. In conclusion, Swiss Lathe processing holds a crucial position in modern manufacturing, and its superior features have made it popular across various industries, continuously expanding its application areas through ongoing development and improvement. We will explain Swiss Turn machining as follows.
What is a Swiss lathe and Swiss turn machining?
Swiss lathe originated in Switzerland and are primarily used for machining bar stock with diameters ranging from 1mm to 32mm (though larger sizes exist but are less common). They are widely applied in industries such as instruments, gauges, watches, cameras, home appliances, medical devices, hardware, telecommunications electronics, and automotive, aerospace, and military sectors.
Swiss turn machining is an advanced manufacturing process that can produce high-precision components. It is suitable for machining small parts and cover the shortage of other lathes and milling-turning centers in processing such small parts.
This machining method involves operating a lathe controlled by a CNC unit, where the lathe rotates the part in radial motion while cutting. Swiss turn machiningis the capability to change multiple different milling tools, enabling it to quickly complete the different machining of workpieces.
Masion specializes in Swiss turn machining focused primarily on micro-sized parts with diameters ranging from 1mm to 4mm. It can also handle complex B-axis milling and eccentric applications with diameters up to 26mm. It offers functions such as drilling, boring, knurling, turning, and milling, as well as external thread cutting, tapping, rolling, and single-point threading. Swiss turn machining can process various materials, including stainless steel, titanium alloys, high-temperature alloys, aluminum, and even plastics. Our machines are also equipped with automatic loading capabilities for high-volume production.
Working Principle of Swiss turn machining
The working principle of a Swiss lathe involves the rotation of the main spindle (C-axis) and movement along the Z-axis, as well as the coordinated movement of the tool turret along the Z/X/Y axes for product machining. The cutting tools in a Swiss lathe remain in a fixed position and perform machining operations by the combined movement of the main spindle along the Z-axis and the rotation of the C-axis.The guide bushing is used to securely hold the required bar material and transport it to the tooling area for machining. The sturdy support provided by the guide bushing ensures that the bar material enters the machining area safely and accurately, enabling stable and precise machining. This unique mechanism makes the Swisstype machine play an important role in industrial production.A spring collet inside the main spindle through-hole clamps the bar stock and rotates synchronously with the spindle. In the case of Swiss lathe with a guide bushing, the guide bushing provides support at the front end of the bar stock, allowing for stable longitudinal cutting. Radially distributed tools can move radially (relative to the machine’s X and Y-axis directions) to perform radial cutting. The main spindle box can move longitudinally (i.e., in the Z-axis direction of the machine) to accomplish longitudinal cutting.
In traditional lathes, the workpiece is typically fixed at one or both ends and undergoes cutting operations through rapid rotation. However, Swiss lathes differ in that the workpiece not only rotates but also moves along another Z-axis. Additionally, Swiss lathes feature a tool turret that allows for the interchange of different tools to perform milling operations on the workpiece. Furthermore, Swiss lathes are capable of machining the workpiece at different positions, whereas conventional lathes can only perform single-point machining at one position at a time.
Although Swiss lathes are commonly used for machining high-precision and high-value screws, they are actually more widely employed for machining complex components such as various motor shafts, valve cores, and bone screws.The flexibility of Swiss lathe machinings allows them to meet various machining requirements and play a significant role in precision manufacturing.
Advantages and disadvantages of CNC Swiss turn machining:
Suitable for machining bar materials with a diameter of 1-32mm.
High processing efficiency.
All Swiss lathe machining use bar feeding, with automatic bar feeders and complete machining in one clamping.
The spindle speed is high (up to 20,000 revolutions per minute or more), resulting in high efficiency when machining small parts.
Complete range of equipment models, suitable for various levels of complexity of small parts.
Particularly skilled at machining long and slender shaft-type parts.
The biggest advantage of Swiss lathe machining is the machining of long and slender shaft-type parts. Compared to conventional machine tools, with guide bushing in Swiss lathes, the bar material is fed through the center guide bushing, and the cutting tool is positioned close to the guide bushing end, ensuring good rigidity and eliminating the deformation of the bar material under cutting pressure, thereby guaranteeing the accuracy of the parts.
Disadvantages
Generally, polished bar materials of 2 to 3 meters in length are required, with a surface roughness not exceeding Ra2.5. The diameter tolerance of the bar material should be within 0.020mm, and the roundness of each bar should be 1/3 to 1/2 of the minimum tolerance size of the product. The taper should vary within 0.020mm. The straightness of the material varies based on the diameter and material grade, as determined in the table below.
Requirement specification for straightness:
Diameter and Straightness Tolerance | Permissible value | |||||
Maximum Bend Tolerance | Minimum Bend Tolerance | |||||
Grade A | Grade B | Grade C | Grade A | Grade B | Grade C | |
Below φ3 | 0.025mm for 300mm length | 0.05mm for 300mm length | ||||
φ3-φ10 | 0.25mm for 1000mm length | 0.5mm for 1000mm length | 1.0mm for 1000mm length | 0.1mm for 300mm length | ||
φ10-φ50 | 0.03mm for 300mm length | 0.06mm for 300mm length | 0.12mm for 300mm length | |||
φ50-φ120 |
There is a leftover material issue:
Swiss turn machining offers the advantages of precision and efficiency. It can achieve a minimum tolerance of approximately 0.003 millimeters, which depends not only on excellent Swiss lathe but also on the expertise of the machinist. Therefore, Swiss turn machining is often the preferred choice for machining small components. Additionally, Swiss turn machining allows for quick turnaround time, typically completing simple parts in just 10 to 15 seconds. With the capability of 4-axis and 5-axis machining, Swiss lathe can approach the workpiece from different angles and perform multi-faced machining.
Maison’s imported Swiss lathes from Japan can make both complex and standard shapes.
Industries and applications:
Application fields:
The materials processed are mostly non-ferrous metals and easily machinable steels, with diameters generally less than 32mm for bar materials and hardness typically less than 30HRC.
Should I choose CNC Swiss turn machining or automatic lathe machining for my product?
The choice between Swiss lathes and automatic lathes for your product depends on your product requirements and manufacturing needs. Here are some factors to consider:
Complexity
Swiss lathes excel in handling complex and precision parts. They are suitable for machining products that require highly accurate internal holes, fine features, or small working surfaces. Especially when dealing with long shafts and complex geometries, Swiss lathes are a better choice.
Swiss lathes have high rigidity and vibration control capabilities, providing a more stable machining process even at high speeds. They typically have the ability to perform simultaneous machining on 4 or 5 axes, enabling complex machining operations in multiple directions. This makes them the ideal choice for products that require multiple operations such as turning, milling, drilling, boring, tapping, and engraving.
Additionally, Swiss lathes offer greater flexibility, being able to accommodate parts of different shapes and sizes, as well as various machining requirements. They perform well in turning and milling operations, allowing for a combination of multiple processes and providing comprehensive machining capabilities.
Therefore, Swiss lathes are the preferred choice when your product requires handling complexity, precision, complex geometries, multi-directional machining, or turning and milling operations. They can meet your high precision and complexity requirements while offering more comprehensive machining capabilities.
Material
On the other hand, Automatic lathes are more commonly used for machining common steel, copper, aluminum, and are widely applied in standard parts such as screws, bolts, and nuts. The automatic lathe can quickly process the desired shape of the workpiece when handling these materials.
Therefore, if your product requires the use of high-hardness materials like stainless steel, titanium alloys, and high-temperature alloys, Swiss lathes may be more suitable as they can provide better machining performance and higher accuracy. For common materials like steel, copper, aluminum, and standard parts like threads, bolts, and nuts, Automatic lathes may be the more commonly used choice due to their efficient production capabilities.
Mass production
Swiss lathes may face some challenges when it comes to production batches. Due to their complex structure and more sophisticated program design, Swiss lathes may have lower efficiency when producing small batches or individual pieces. For smaller batches, the setup and debugging time of Swiss lathes may exceed the actual machining time, leading to decreased production efficiency.
Therefore, if you require large-scale production, especially of identical or similar parts, Automatic lathes may be the more suitable choice as they can provide higher production efficiency and lower costs. However, if your production batch is smaller or you need to handle more complex parts, Swiss lathes may be more suitable as they can provide higher precision and flexibility.
Machining Speed
Cost-effectiveness
On the other hand, Swiss lathes may offer better cost-effectiveness in machining complex parts. Due to their higher precision and complex machining capabilities, they can complete multiple machining steps in a single operation, reducing the need for subsequent machining steps. This can reduce overall machining time and decrease the utilization of equipment and human resources, thereby improving production efficiency and lowering costs.
If you are engaged in large-scale production and aim for lower operating costs, Automatic lathes may be the more economical choice. However, if your product complexity is high and reducing subsequent machining steps can enhance cost-effectiveness, Swiss lathes may be more suitable for your needs.
Design Flexibility
Swiss lathes often feature multi-axis control and multi-functional tool systems that can be adjusted and programmed to meet different design needs. This enables them to handle complex geometries, special contours, and intricate details, satisfying personalized and customized product requirements.
In contrast, Automatic lathes have relatively lower design flexibility. They are typically suitable for handling standard shapes and sizes of parts, such as threads, bolts, and nuts. Automatic lathes exhibit high efficiency and stability in these standardized machining tasks but have limited adaptability to complex geometries and non-standard design requirements.
Therefore, if your product requires flexible design requirements, complex geometries, or special machining operations, Swiss lathes may be the more suitable choice. They offer higher design flexibility, catering to personalized and customized product needs. However, if your product has relatively standardized shapes and sizes, Automatic lathes may be a more cost-effective and efficient option.
In summary, you should consider a comprehensive evaluation based on factors such as your product characteristics, material requirements, production batches, machining speed, and cost-effectiveness when choosing between Swiss lathes and Automatic lathes for machining. The optimal choice will depend on your specific needs.
Exhibition Time | Exhibition Name | Exhibition Place |
---|---|---|
9-12 January 2023 | steelfab Sharjah | Sharjah |
4-7 April 2023 | METALWORKING Belarus | Minsk |
April 12-15, 2023 | INTERMOLD Tokyo | Tokyo |
May 16-18, 2023 | FABTECH Mexico | Mexico |
May 10-13, 2023 | LAMIERA Milan | Milan |
May 23-26, 2023 | BUTECH Busan | Busan |
May 9-12, 2023 | NMW Australia | Melbourne |
November 7-10, 2023 | AMB Stuttgart | Stuttgart |
May 30-June 2, 2023 | ITM Poznań | Poznań |
September 11-14, 2023 | FABTECH Chicago | Chicago |
September 10-14, 2024 | AMB Stuttgart | Stuttgart |
October 25-28, 2024 | EUROBLECH Hanover | Hanover |
How do I find the trustful swiss turning part supplier?
Online Research
Start by conducting a comprehensive online search using Google (link: www.google.com) and Alibaba (link: www.alibaba.com). Use keywords such as “Swiss turn machining,””CNC Swiss machining,””Swiss machining,””Swiss lathe machining,””Swiss machining companies,””Swiss machining products,””Swiss turn parts,””Swiss turning,””Swiss turning services,””Swiss machining services,” etc., to find Chinese suppliers specializing in Swiss turning machining. When you choose to use an online search engine to find suppliers, you can simply sit comfortably at home and navigate through the computer mouse to quickly and easily discover the suppliers you need.
Industry Networks and Trade Shows
Supplier Directories
Explore online supplier directories and databases that focus on precision engineering and machining. These directories often include ratings, reviews, and certifications that can help you evaluate the trustworthiness and quality of potential suppliers. Some popular directories include Thomasnet (link: https://www.thomasnet.com/), GlobalSpec (link: https://www.globalspec.com/), and Kompass (link: https://www.kompass.com/). Use keywords like “Chinese Swiss parts suppliers” to search for directories specific to China.
Request for Information (RFI)
Quality Certifications
Customer Recommendation
Visit the Facility
Samples and Prototypes
Continuous Communication
Supplier Assessment
Remember, it’s essential to conduct due diligence and carefully assess potential suppliers to ensure you find a trustworthy Swiss turning part supplier that can meet your quality standards and business objectives.
Free Sample
Explore Other Guide and Resource
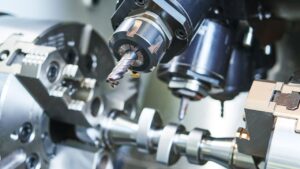
CNC Turning Services 101 – Know the Every Unknown
Get a detailed overview of CNC turning services. Explore the benefits, types, and materials involved in creating high-precision parts for various industries.

Swiss Lathe Manufacturers – Top 10 You Need to Know
Discover the top 10 Swiss lathe manufacturers known for their precision and quality. Learn about industry leaders today!
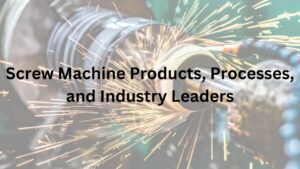
Screw Machine Products, Processes, and Industry Leaders
Explore comprehensive Swiss Machine Products guide covering tools, techniques, and top manufacturers. Master the art of precision manufacturing for optimal results.